
6 minute read
Special Providers of abrasives
UNDENIABLE MOVE TOWARDS A LONGER LIFESPAN
SILICON CARBIDE AND ALUMINIUM OXIDE MAKE WAY FOR ZIRCONIUM AND EVEN CERAMICS
Advertisement
There are few materials which require as much professional expertise as wood. Each wood sort has its own characteristics and that means that you have to take that into account, certainly with sanding. If we look at market developments, we see a clear line: abrasive materials with silicon carbide and aluminium oxide have been ousted for some years now by zirconium, ‘the new strong man’. Much more recently, ceramics have started to emerge as an abrasive material.
Whilst aluminium oxide and silicon carbide had the last word until about ten years ago, at present we notice that zirconium and also ceramics have taken the market by storm.
At present, sanding with zirconium (or with a mix in which zirconium is the most prominent element) stands out, and that really is no surprise. The main reason for choosing this material is simply that the bands last up to five or six times longer than aluminium oxide and silicon carbide. Whilst the latter products soon become blunt and jaded, we note that zirconium hardly ever behaves like that, if at all, due to its extra grain hardness. Yet it offers the same grip and sharpness to ensure smooth sanding. The point is that the grain always breaks off a very small piece to retain the same sharpness. This is in contrast to the bluntness of aluminium and silicon.
Moreover, an extra benefit, certainly for parquet floor fitters working with wood, is that zirconium processes very well. The reason for that is quite simple. The grains with this product are further apart, so it is much easier for the dust to escape. The result is that the wood doesn’t get burnt (so there are no characteristic black marks) because the temperature doesn’t build up anything like as quickly. Various things also mean that you always see perfectly what you are sanding, and that can only contribute to a high quality end result. Moreover, there’s one more benefit: Zirconium is also ideal for renovation jobs. After all, it removes extremely hard coating systems much better, such as UV hardened lacquers or DD lacquers.
The ceramic story
Where do ceramics fit into this story? You can say that the basic difference is that ceramics are even harder than zirconium. In practice, this means that ceramic bands are ideal for rough sanding and, after that, you can do the rest with zirconium. Finally, ask yourself: Why doesn’t anyone use glass or diamond? The answer is short and to the point. Glass is certainly not suitable for the parquet industry and diamond even less so because they are considerably more expensive. Scrubbing brushes have their say
Parallel to the main article we want to give separate consideration to scrubbing brushes and we consider scrubbing brushes under stationary and non-stationary machines (or rotary sanding machines). Why and when do we use these scrubbing brushes? If we go back in time, you have to realise that for brushing a wooden floor in situ there has been a change from a sanding drum with sandpaper to a brush which is put under the machine. Such a stationary machine does have a certain drawback: It compels you to stay quite a long way from the side and, after that, you have to finish the job on that side manually. Moreover, the brushing result is also relatively coarse. A good answer to this are the rotary machines with a plate for several discs. If you put brushes onto that plate, it is possible to ‘dive into the sides’ more subtly and easily. What we certainly have noticed on the market is that there is a tendency towards greater use of multi-disc sanding machines. These are very efficient due to their relatively low weight. There is, however, one comment by way of reservation: That lighter weight makes them less suitable for a number of heavy jobs, such as removing old coats of lacquer.
Some specialists
Bona
The key to the best sanding results lies in a perfect combination of machines and the abrasives used. The Bona sanding assortment yields not only excellent results, but also their systems are developed for maximum efficiency, comfort, and safety. A selection from the wide range of Bona abrasives: Bona Ceramic (Series 8700 - Grey) Superior abrasive material made from ceramic quality for the simple removal of hard UV lacquers and adhesive residue and for levelling
very uneven floors. In combination with the Bona 8300 series, an ideal system for high sanding performances for a nice smooth surface. Bona Ceramic Mix (Series 8600 - Green) Abrasive material with a long life and it sands effectively. Yet it prevents unnecessary damage to the wood fibres. The unique mix of ceramic and aluminium oxide offers a 30% faster sanding process and lasts 50% longer than standard abrasive material. Bona Anti-static Zirconium (Series 8300 - Blue) Top class abrasive material with an ideal mix of zirconium and silicon carbide for a perfect balance between aggression and surface-finish. The Bona 8300 abrasives are highly durable and have an anti-static top layer which prevents filling, does not overheat, lasts longer, and discharges dust better. The grain used constantly forms new sharp points during use. Bona Diamond Abrasives Exceptionally durable sanding discs with diamond parts. For polishing ceramically reinforced UV lacquer and other hard lacquers. It reduces the risk of scratches. Covers at least 100m² - Improves the adhesion before applying more lacquer.
Devo
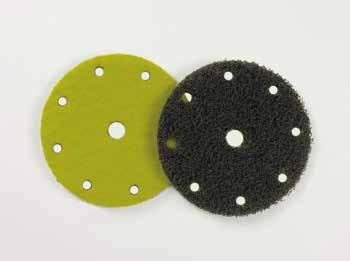
Over the last 40 years, the range of Devo® sandpapering materials has become a regular fixture amongst parquet traders due to innovation and high quality. There has generally been little renewal in terms of basic raw materials. Most ‘new’ materials which enter the parquet sector have existed for a long time, but are now also found on the parquet market due to a growing demand for high-performance materials. In the past, parquet traders used hardly anything except aluminium oxide and silicon grains. Nowadays, they also use zirconium and ceramic materials due to the greater sandpapering grain hardness. The composition of the materials has undergone some change as a result of technical developments. For instance, in 2017, Devo innovated with the Devo® Fiberpad™. This is a completely new sort of sanding disc which offers scores of benefits for floor fitters.
LÄGLER
Nowadays, craftsmen expect high-performance abrasives with long service lives, which have optimum aggressiveness and at the same time, guarantee a uniform sanding pattern. These should withstand the highest mechanical and thermal loads and be able to process the most diverse surfaces. Let it be softwood, hardwood or tropical wood, or coatings with varnish or oil. The appropriate cutting materials, binders and underlays must be used. The development and manufacture of such abrasives requires the use of high-quality materials in combination with sophisticated testing and manufacturing processes. After countless tests, this ultimately resulted in our LÄGLER® abrasives. They have been specially developed for the optimum use of the LÄGLER floor sanding machines, meet the high quality requirements of craftsmen and cover the complete range of applications.
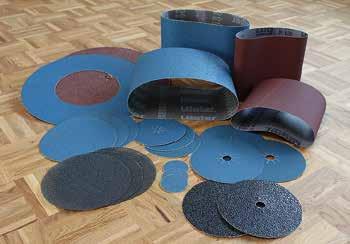
FLIP ® - Corner attachment
Can you build up an emotional attachment to corners? Yes, because now you will love them! With our FLIP® corner attachment you will work corners easier and faster than ever before!