
6 minute read
Special Automation in the parquet industry
Photo CSP Engineering
Advertisement
What’s the best way of packing your products in the parquet industry? We put this question to some market players and in CSP we found the top specialist to explain to us how it all works. Manager Jan Peeters explains how everything revolves around working together with the client to look for the best solution and deciding together which packaging is the most suitable.
According to Mr Peeters, your basic principle has to be that efficient packing means more than just buying a packaging machine. On the contrary, you have to follow a certain plan so that in consultation with the client you arrive at the most suitable packaging line for your client.
Type of products and market
‘In a consultation with a client it’s best to start by considering the client’s type of products and market. You have to know that because it compels you to opt for certain forms of packing,’ Mr Peeters explains. ‘Transport, too, can be a parameter. Suppose you have a parquet manufacturer with limited capacity which has a showroom and a few teams of fitters. In this case the most important consideration for this company is being able to deliver the finished floorboards to the end client easily and without damaging them.’
‘In this example, strapping will usually suffice, so our other solutions from applying shrink film and including packing with cardboard ribbon are not necessary. However, if you hear that the team of fitters is going to store the floorboards at home first before fitting them at the end client later in the week, then you should at least consider packing the floorboards in shrink film, certainly if it are pre-finished floorboards. This shows how various packaging methods are related to both transport and the producer’s market. You see fully fledged packaging with producers who export overseas in containers. Such companies will usually apply both strapping and shrink film and wrap full pallets in plastic, with extra strong straps being applied around the pallets.’ DIY is different to the professional market
Jan Peeters then explains how the professional market and DIY market have different requirements. For instance, for DIY the manufacturer strongly recommends using pre-printed cardboard ribbon around each pack (brand positioning) and bar packs on pallets. ‘random’ lengths per pack are typical for producers in the Benelux and France. The wood is utilised to the full in the length. Floorboards are collected and packed in length groups and then stacked onto one pallet per order. The packs and pallets do not have a perfect ‘bar shape’. However, you need the latter for medium sized and big industrial producers. These firms produce in fix lengths and pack in fix lengths per pack.
‘If the production is in ‘random’ lengths, the packs consists floorboards of ‘similar’ lengths. To that end, we’ve developed the PAR-Scan packaging line controller, which measures the length of individual floorboards very precisely, registers the details in a database, and finally prints a label showing the exact content of that pack, including the wood, quality, and dimensions. If necessary, the label can display the client’s logo and/or a bar code. Since a control has measured the pack, it knows the geometry of the pack and can position each pack ready to be strapped. If you look at such a pack, you notice that the strapping positions are determined by the length of the upper strip, where the upper strip is often somewhat shorter than the lower one. It can apply several straps, if necessary in combination with other forms of packaging such as cardboard ribbon and shrink film. For that matter, PAR-Scan can do a lot. Does the client want to get the average length per pack? Or a list with details of the packs per order? That’s perfectly possible and eliminates discussions between sender and recipient.’
Apart from the random lengths, Jan Peeters refers to both the fix length packs and the so called ‘combination packs’. With the latter, the total length of each layer in the pack is the same (fix), but there are
different lengths combined in a pack. For instance, a package length of 220cm can have layers with two sections of 110cm next to each other and each mix of floorboards will together be 220cm long.
‘The fix length package is a typical way of working for the DIY and professional trade,’ Jan Peeters explains. ‘In those worlds no one works with random lengths, since the main thing is to work efficiently and stack everything optimally. If you print a label, this may include a code in which all the details are processed about the exact identification of the pack.’
Line set-up
With the installation of a packaging line, it is essential to set up and integrate the diverse machines as efficiently as possible. That is certainly one of the great strengths of CSP. They work literally on demand with each client.
‘You always have to work out the best solution. You also consider the client’s various needs and several particularities. An example: The pack has to be stationary in order to apply straps. By contrast, with shrink film the pack goes through the machine in one smooth motion. The art of putting items compact in a line therefore means harmonising the packaging machines with each other.’
‘Furthermore, you also have to maintain perfect tuning to achieve a good capacity on the whole of the line. The specifications, speeds, and such like are harmonised nicely with each other. You also have to take account of the zero lines, which can be different from the machines in line. Moreover, you also have to know which machines you can and cannot integrate. The list goes on. What it boils down to is that you, as a supplier, have to provide as much added value as possible and that you keep all factors in balance. For instance, does someone have some machines which can be integrated? If so, you calculate whether or not you will include them in the new narrative or whether you need to replace them. It is a consideration of many factors which we discuss with the client and we look for the ideal point between the investment sum and the efficiency achieved.’
Photo – PAR-Scan - CSP Engineering Logistical handling
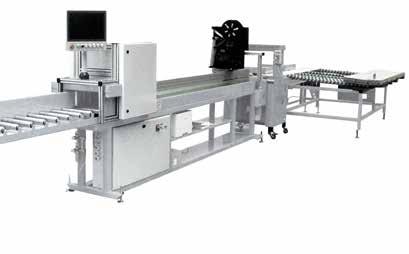
Finally, we should also point out that with a packaging line you have to pay particular attention to the logistical handling.
‘The most simple solution is a so called outflow conveyor belt, where someone always stands nearby to remove packs from the belt. Depending on the line capacity, the next step is to provide a buffer which bundles 10 packs so that the operator can then put them on a pallet. The latter is particularly attractive with short packing lines, such as with strapping. With long packaging lines it is once again advisable to provide a returning system in order to work efficiently and limit the distance covered by the operator as much as possible.’
‘I’d like to refer in this connection to our PAR-Stack, which stacks products automatically. The logistical handling is included in the debate about the quest for the ideal point between investment sum and efficiency.’
Years of experience
Our interview briefly considers a special asset from his own company. CSP has years of experience and that is absolutely essential for defining packing machines.’
‘Having a preliminary history is a big advantage. We’ve been familiar with the parquet market for years and hereby we’ve been able to develop modular blocks with which clients can develop in line with their own needs. This is possible because we know exactly how to intervene.
The main thing is still to work together to look for the right balance between investment and efficiency and thereby look realistically at the near future. This means that you always have to consider what the expected development in capacity is likely to be in the next one to three years.’
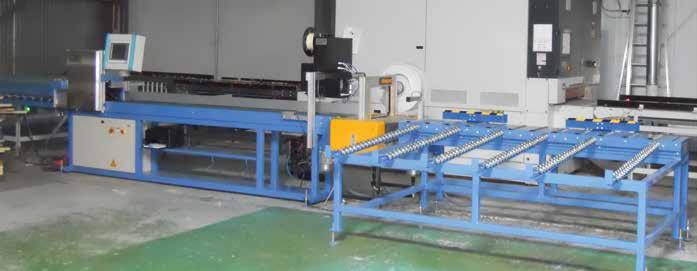
Photo – CSP Engineering