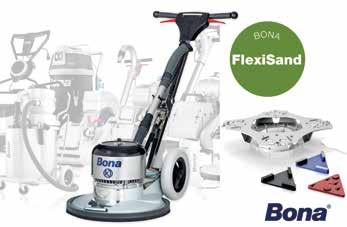
7 minute read
Special Who has walk behind machines for roughening up old tiles, scraping the screed, and removing old carpet, tiles, adhesive residue, etc?
CONCRETE GRINDERS UNDER THE SPOTLIGHT
SIMILAR TO PARQUET SANDERS, YET A COMPLETELY DIFFERENT MACHINE
Advertisement
In this article we consider how to grind concrete. Basically, you have two sorts of concrete grinding machines, one of which is operated manually, whilst you walk behind the other one. Here we only cover the latter one because it is mainly due to this machine that professional floor fitters stand out from better quality odd job workers.
Metal with diamond
If you grind concrete, you should use diamond because that is the ideal material for stripping a floor of elements such as adhesive residue and old coatings and dealing with old marks or scuffed patches. Diamond causes scratches, and that lays a good foundation for the adhesion of a coating or adhesive which is applied later. It’s worth knowing with machines which you have to walk behind that they are usually larger rotary sanders or sanding machines fitted with planetary rotating heads with diamond discs. The diamonds are bound with metal and it is ideal if there is a specially fitted dust suction unit because this job generates lots of dust. A dustless operation might be virtually impossible, but it’s best to keep everything as dust-free as possible.
The machine ‘teeth’
We also need to mention that there are four to six segments under the rotating swivel plate. You can regard these segments as sorts of ‘teeth’ for the machine, where each segment has its own function. We can use a rough comparison to sanding machines which are generally used to sand parquet. The segments are actually comparable to the grain size of sandpaper. The range goes from very rough with a low grain size for the preparation to a very high one for the finish.
If you want to compare the standard parquet sander, the comparison virtually grinds to a halt with the fact that you operate them both manually. With the concrete grinder you only see two wheels which are fitted at the front and help you to move the machine. On the other side there is the rotary sanding disc enclosed in a steel cage. The concrete grinding machine works so effectively because the motor is fitted on top of the grinder so that users can exert plenty of pressure on the concrete. We can also say that it is always possible to add extra weight to increase the grinding pressure.
If we consider the concrete grinders which are available on the market, you will notice that there is a considerable range, but also that there are some really giant-size machines which can easily weigh up to 400kg. It’s important to realise that not every concrete floor requires the same grinding and it all depends on the desired result. For instance, not only is there a difference between ‘normal’ concrete and terrazzo and synthetics, but also you also have to consider the end result. Will you be grinding only once or, on the contrary, are you aiming for a perfectly polished concrete floor? You should be aware that in the latter case you might have to grind up to seven times. Up to seven times
We start with the easiest job, namely removing old coatings. One grinding session with a sanding disc with a grain size of 60 can suffice for that purpose. Indeed, one session may be enough because the floor was already smooth prior to the application of the coating which you want to remove.
The job becomes more complex if you want to remove epoxy layers or level a concrete floor. Generally speaking, two grinding sessions will be necessary for both. Repairing a damaged concrete floor is another job all together, but it is basically feasible in two sanding sessions. This involves recasting the damaged section, but, after that, the floor will no longer form one whole (combination of old and new).
If you want to polish, you have to realise that this is the most labour-intensive of all operations. Indeed, not only do you have to grind the concrete, but also you then have to polish it and that can take a long time. In this case five sessions are often necessary, but even up to seven is not exceptional.
Sources: Various manufacturers, schuurmachineskopen.nl, and profloorcare.nl
What’s on the market ?
Bona
Roughening up old tiles, grinding screeds, and removing old carpet and adhesive residue require hard intensive labour. Bona makes a priority of user comfort and has in its range a single-disc machine, the Bona FlexiSand 1.9, which can be fitted with a drive disc specially for such intensive labour, the Bona Concrete Disc. Various types of grinding segments can be attached magnetically to this base drive disc, depending on the required result.
They include: PCD Maxi Segments: This removes thick adhesive residue, silane adhesive, carpet foam, Paint, and epoxy. PCD Split Segments: This removes polyurethane, thin adhesive residue, jute, and paint. Diamond Segments: This removes sinter layers and epoxy and grinds concrete surfaces and anhydrite.
Lägler
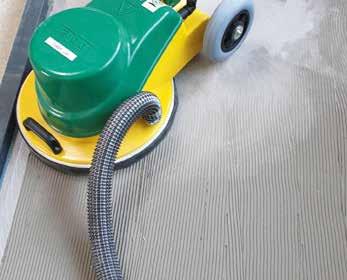
Preparing floors for new installation or renovation - no problem with the extensive range of sanding and milling tools that the Lägler company has developed especially for its machines! The following work can thus be carried out efficiently and in a time-saving manner: RENOVATION OF OLD WOODEN FLOORS with the IGEL milling drum (for HUMMEL and ELF surface sanding machines) and the milling attachment for the edge sander FLIP: Remove: - Paint and carpet adhesive residues - Leveling compound - Carpet and cork back residues - Multiple layers of old varnish - Lubricating parquet varnishes Preprocessing: - Heavily cupped floorboards SUBFLOOR PREPARATION with the tools for the SINGLE single-disc sanding machine: Sanding and leveling: - Screeds - Sintered layers Residue removal: - Felt back - Plaster - Parquet and tile adhesive - Filling compounds - Paints - Thin bitumen layers
New topic: Tools in action!
✔ Effortless and efficient renovation - Milling with the HUMMEL ® and the FLIP ® ✔ New installation and renovation - Subfloor treatment with the
SINGLE
✔ Application possibilities - Using Lägler ® products correctly and successfully ✔ Technical questions - Lägler ® professionals answer your questions.
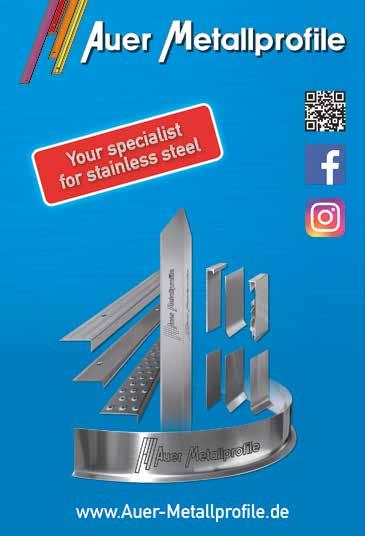
Janser
In addition to an extensive assortment of sanding machines, Janser also offers an impressive range of strippers. The range includes hand machines, walk-behinds and ride-on giants to tackles large surfaces with no problem at all. The COSMO Stripper – a powerful stripper for small and medium-sized areas. Works on wooden or concrete surfaces and will remove virtually any substance adhering to the floor. The handle and wheel adjustments allow different settings of the blade to fit the floor, while keeping the handle in a proper operating position. Also foldable for easy transportation. The machine runs virtually silent with reduced vibrations. The COSMO Stripper has the ideal specifications for rental! The MASTER-MOBIL III is self-propelled (forward and reverse) with unparalleled performance due to its high torque German designed electric motor. The powerful motor combined with the revised HYDRAULIC-DIRECT-DRIVE system ensures high output with an extremely low noise level (105 kg and a maximum speed of 16m/ min). Front weight and center weight can be easily removed for transportation. Wheel hubs with freewheel option for easy handling and easy pushing of the machine without power connection. The STRATO MOBIL IV stands out at once in the upper range of walk-behinds, a heavyweight amongst the hydraulic pusher machines (190kg and a maximum speed of 23m/min). The powerful motor is equipped with the hydraulic-direct-drive system achieving high performance at a low noise level. The machine is self-propelled both forwards and reverse. Weights can be removed for transportation. - Easy operation and low maintenance due to hydraulic technology. - Low noise level without fumes. - Adjustable in height to operator size. - Machines are easy to transport, load, and unload, fit in lifts and go through standard doors. - There are various options for additional weights.
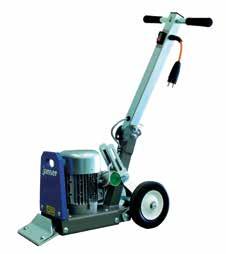
Professional Flooring Technology
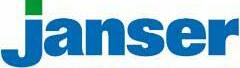
Floor Scrapers in suitable weight classes!
German Quality
Ride-on ADB HS 1180 kg Ride-on ADB 950 kg Ride-on Electro 565 kg
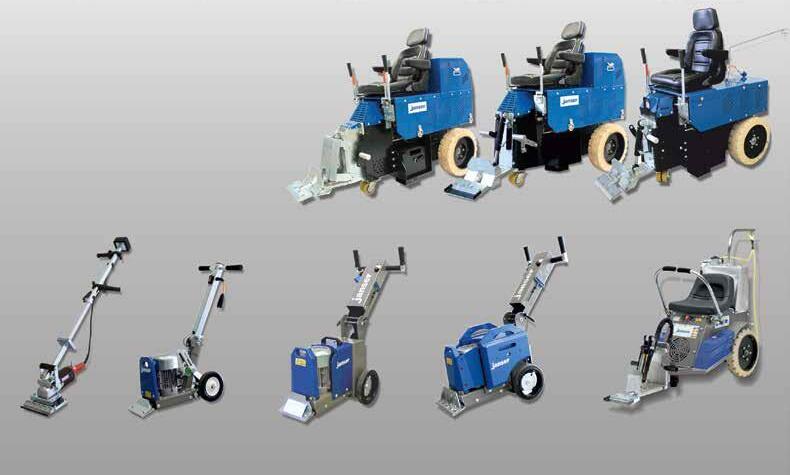
Power-Stripper 14 kg COSMO IV 39 kg MASTER MOBIL III 105 kg STRATO MOBIL IV 190 kg JUNIOR Ride-on 420 kg
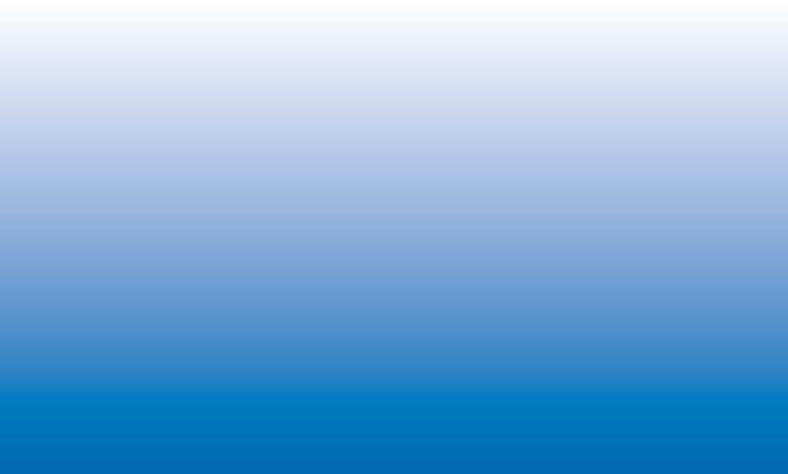