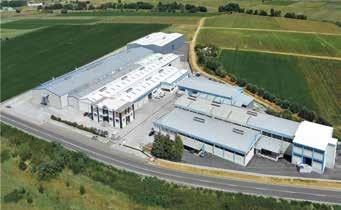
9 minute read
Special Providers of abrasive materials
WHEN GRAIN SIZE IS IMPORTANT
CONSIDERING THE RIGHT SANDPAPER FOR EACH WORK SESSION IS ESSENTIAL
Advertisement
Katerina Topouzoglou (CEO Smirdex - GR) and Klaas Van Dyck (Woodmade - B)
“Our premium quality abrasives are ready to conquer both the Benelux and Europe”
When talking about premium quality abrasives, the name Smirdex is relatively new in the Benelux. However, the coming months and years, we can expect this Greek company to penetrate our – and the European – market a lot more. This should be no surprise, as this company from the north of Greece found a new partner in Belgium, Klaas Van Dyck, who is working the parquet market intensively with these high quality abrasives. What is Smirdex and what can we expect? We interviewed Smirdex CEO Katerina Topouzoglou and her Belgian business partner Klaas Van Dyck.
Katerina Topouzoglou: “My father founded Smirdex in 1981 and meanwhile we have become a leading company in the field of manufacturing premium quality abrasives for a wide range of applications. Ours is a well-structured family business, and, with the continuous efforts of our fully qualified staff, the company has been progressively led to growth, both in production and absolute alignment with top quality standards, through quality European raw materials, a certified production process and development of innovation via a specialised research.”
“We focus our commercial activity on the international market. Smirdex trades 85% of its sales in more than 76 countries worldwide, through its network of dealers and associates, while the remaining 15% is distributed to the internal Greek market. Last year was very good, with a 30% increase in turnover of 30 million euros. This is the result of working with a load of enthusasm and a verh high concern for quality, while keeping our prices normal in comparison to other brands.”
The ceramic evolution
Among other things, Klaas Van Dyck mainly distributes the Smirdex 750 series, a ceramic net abrasive ensuring a revolutionary almost 100% dustfree sanding. Instead of a paper backing, the net fabric structure permits maximum absorption of the sanded particles. Thus, a much healthier environment is created for the user and less effort is needed to clean up the workplace. Smirdex only offers ceramic grained nets, leading to a high cutting performance.
Katerina Topouzoglou: “I was very impressed by pictures i saw from Klaas and his customers. I also saw how good it was brought to market in the stores and we decided to start a cooperation in the high-competitive Benelux market, where there are a lot of high end companies. We are not deterred by this, as we bring products to market that can compete.”
Klaas Van Dyck: “I found Smirdex when I was looking for alternative abrasive products. Most of what came my way was of very poor quality, in total contrast with Smirdex. Katerina and her team sent me samples, I tested these together with a number of parquet installers and was amazed by the quality. Next, I visited the company in Greece and discovered a well-organised, solid company with a very high focus on product quality. As a result, I started to import and sell the 750 ceramic net series a little over 1 year ago, and the product was very well received.”
“What I like especially about Smirdex is how very responsive this company is, it’s about more than ‘only’ quality. I have seldomly seen such a short lead time, together with real support and quick and good answers, combined with stable prices.”
Katarina Topouzoglou: “That is exactly what we want to achieve with Smirdex: offering very good quality, value for money and reasonable prices. This combination makes it easier to penetrate the market, especially with a high-tech product such as our net.”
“Our partnership with Klaas is the same as with all of our partners. We only look for the best partners and do everything we can to support them. This is a benefit of being a relatively small company, people that want a stable business relation with us always come first!”
Growing importance of wooden floors
When we talk further, the same thing always comes back: products such as the 740 and 750 net series are only being put to market when they have been perfected. After their launch, the company keeps looking for further improvement.
Katerina Topouzoglou: “The Benelux market is very interesting for us, as this is a region where wooden floors are important. In a way, we focus now on what my father wanted from the very start: axing on furniture and flooring and perfecting our sanding materials for these.”
“In conclusion, I would like to add that we also have a special way of dealing with raw materials, that we buy in Europe. We always took care of having a very big stock, with almost 6 months stock for production. In these troubled times, this is a big asset and we can assure that we will never be late with deliveries.”
Klaas Van Dyck: “For me, this is an enormous advantage as well. It shows how dedicated this company is and how the central line of thinking is to always be ahead of the needs of the customers. If you ask me, Smirdex is more than ready to conquer the world of abrasives for wood. We are now looking into participating in a number of fairs, to further penetrate the wooden flooring market.”
In a previous edition we considered the fact that in the parquet industry there is a clear and noticeable trend towards raising quality in the direction of zirconium and ceramics, with aluminium oxide and silicon carbide as the most important materials. Each of these materials has specific benefits and drawbacks, so the key is to choose the right material for the right application.
What it comes down to is how you choose the best sandpaper for the specific application you have in mind. To that end, it’s vital to consider a number of basic conditions which we’ll set out. Obviously, all sandpapering requires its own sort of adapted sandpaper. The question here is what to use. The rule is that most sandpaper grains are made synthetically, so that continual high quality is assured.
From coarse to fine
The main thing is the size of the sanding grain. The basic rule is: the more grains applied per square centimetre, the finer the sandpaper. Various things mean, for instance, that fine sandpaper will not suffice to remove old coats of paint. On the contrary, a more coarse grain is needed, and you always work from coarse to fine during the various sessions. To make it easier, we list three groups below. Obviously, there may be a deviation, but the main thing is to work towards fine, medium, and coarse. - Fine: P180, P220, P240, P320, P400, and P600. - Medium: P100, P120, and P150. - Coarse: P60 and P80.
A real illustration: Rough wood or old (poor quality) coats of paints can be sandpapered with a grain between P80 and P120. To get a smoother end result, you sand the primer with finer grit i.e. P150 to P220. For extremely attractive and rigid work, you could use P320-400 for the top coat of paint.
Photo – Smirdex

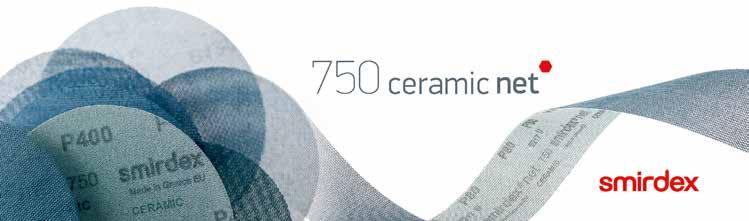
Quality matters
Features of sandpaper
As we’ve said, there are various sorts of sandpaper on the market. To make the right choice, you can apply a number of criteria whereby various features are verified. A list: - Flexibility: To see how flexible the sandpaper is, look at the used bottom layer. Here, amongst other things, you notice paper, polyester, and linen. - The type of adhesive used: If the adhesive is not waterproof, you can only use the material for dry Sandpapering. - Grain size of the abrasive: As you can see in the list above, this is indicated with a number whereby a higher number indicates finer sandpaper. - Sort of grain: Here we identify the four major sorts of grain, namely aluminium oxide, silicon carbide, zirconium oxide, or ceramic. - Shape of the abrasive tool: Obviously, you choose the right sheets with the used material. Everything is adapted, and a sandpapering sole for a machine is not the same as sanding belts for a belt sander. - Thickness of the grains: Remember that the grains should not be too close to each other, certainly with mechanical sandpapering (this soon fills the machine and/or it becomes non-operational).
Guaranteeing good adhesion
We don’t need to convince you of the importance of sandpapering. If you don’t do it, there’s no guarantee of good adhesion between the substrate and the top layer. It’s good to keep in mind that you can remove even surface rust marks and weathered wood with sandpaper. Moreover, you can make welds and rough substrates smooth so that the end result looks much slicker.
Other specialists have their say
Bona
Bona offers its products as a ‘system’. They are designed to be perfectly compatible with each other and combine all their product assets. This is how Bona supports its clients from the fitting of the floor over the protection and up to and including the maintenance. Bona abrasives are therefore developed on the basis of features of the Bona machines. Five years ago, ceramic abrasives came onto the market, something which led to a real revolution. However, you do need to take care with names which can sound attractive and you should remember that it is the concentration and the composition of the material which determine the quality. The sort of abrasive which is used to remove all tiny scratches before the colouring is of crucial importance. Ceramic 8700 is still the market reference.
Devo®
Over the last 40 years, the range of Devo® sandpapering materials has become a regular fixture amongst parquet traders due to innovation and high quality. There has generally been little renewal in terms of basic raw materials. Most ‘new’ materials which enter the parquet sector have existed for a long time, but are now also found on the parquet market due to a growing demand for high-performance materials. In the past, parquet traders used hardly anything except aluminium oxide and silicon grains. Nowadays, they also use zirconium and ceramic materials due to the greater sandpapering grain hardness. The composition of the materials has undergone some change as a result of technical developments. For instance, in 2017, Devo® innovated with the Devo® Fiberpad™. This is a completely new sort of sanding disc which offers scores of benefits for floor fitters.
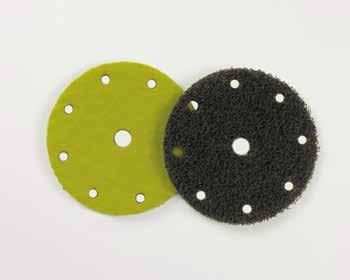
Lägler
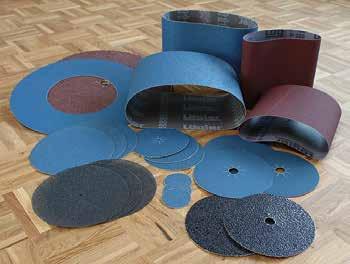
Abrasives have to fit - to man, machine, application and surface! Optimum aggressiveness is required, coupled with a long service life and maximum resistance to mechanical and thermal stresses. The most diverse surfaces are processed with them. A uniform sanding pattern of the highest quality is required as a result. LÄGLER abrasives not only easily meet these requirements, but even exceed them by far. They are efficient, durable and achieve the best sanding results. Perfectly matched to LÄGLER parquet sanding machines, they can be used to effortlessly process a wide variety of wood surfaces, such as softwood, hardwood or tropical wood and coatings with lacquers or oils. Only the highest quality materials are used in the production, sophisticated testing and manufacturing processes are an integral part. LÄGLER abrasives are application-optimised, resource-saving and therefore also future-oriented!