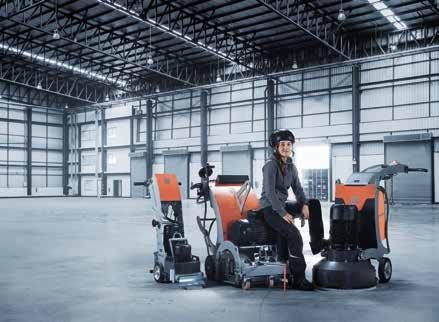
10 minute read
Special How to prepare terrazzo, concrete, natural stone and such like for fitting wooden floors, PVC, vinyl, and laminate
THE WHOLE PICTURE HAS TO BE RIGHT
HOW DO MANUFACTURERS MAKE LIFE AS EASY AS POSSIBLE FOR USERS?
Advertisement
Kris De Rudder and Ad Groenen (Husqvarna Construction surface and floors Benelux )
‘We’re a one-stop partner; we literally have all solutions under our own roof.’
After incorporating businesses such as Blastrac and HTC, Husqvarna Construction can justifiably take pride in the fact that it offers machines and diamond tools for treating all floors, whether concrete, natural stone or terrazzo. The company thereby has all bases covered, from removal work and preparatory work to finishing the floor.
Floor Forum International spoke to two Husqvarna specialists, who immediately made it clear that they offer clients nothing but one-stop solutions. They also stress how the Experience Centre in Ath (B) plays an important part in the corporate philosophy because this is so much more than just yet another showroom. On the contrary, it’s a place where you see and try out all Husqvarna machines in realistic conditions. We spoke to Kris De Rudder, country manager of Husqvarna Construction Belgium and recently appointed as manager for all things related to surface and floor surface and floor treatment in the Benelux, and Ad Groenen. Ad Groenen makes his contribution as a man with over 30 years of specialist experience in the flooring industry. He now combines the know-how which he acquired at Blastrac and integrates this with the products and application options of Husqvarna. On to the machines covered by this subject, we start with the planetary sanding machine.
Planetary sanding machine
Ad Groenen: ‘If you want to remove thin layers, the planetary sander is ideal. You clean and roughen up the substrate so that the next layer adheres well. If you need to remove more, you need a different solution, such as planing or milling. Planing, in particular, is gaining in popularity because you actually plane the floor off, but more about that later.’
Kris De Rudder: ‘The planetary sander comes in a huge range, from smaller tools for residential applications to huge three-headed machines for larger surfaces inclusive.’
Ad Groenen: ‘When we talk to parquet floor fitters, we usually recommend the 230V machine. Obviously, however, there are heavier machines available for bigger projects, even with remote control. The nice thing about the planetary system is that you have one big disc, for instance, of 80cm. That has three or four small heads on it, which rotate left and clockwise. You can sandpaper well to get a very nice scratch pattern which you constantly refine by using other diamonds. That’s how you renovate the floor until you have a polished floor.’
Single-head sanding machines
The next machines in line are the single-head sanding machines with diamond. They also illustrate the Husqvarna one-stop philosophy perfectly.
Ad Groenen: ‘We can best zoom in on the single-head sanding machines, in contrast to planetary sanding machines. These are easy to deploy locally. An example: You want to lower a door opening by a few millimetres. You can do that locally without having to plane or mill. Moreover, they’re ideal for smaller surfaces and some machines can be dismantled.’
Kris De Rudder: ‘The latter is vital. It makes transport and availability easy and more accessible; think here of works on different levels. Husqvarna also makes a priority of ergonomics, and that benefits operators’ health. This also applies to machines like floor strippers, shot blasters, and such like.’
The floor plane machine
The next tool in line is the floor plane machine. Here you put a drum with diamond sheets into a drum casing. Once the machine is switched on, the drum rotates at high speed to saw off the surface.
Kris De Rudder: ‘The aim is to make the floor as flat as possible, hence the drum. What happens is that you literally plane material off.’ Ad Groenen: ‘What’s interesting is that you leave the substrate reasonably intact and get a flat base. And so, you remove concrete without a lot of noise and vibrations. This is completely different to milling, where you demolish the floor and make a lot of noise. A method like this is
Photo – Husqvarna ideal in silent environments, such as in hospitals.’ Kris De Rudder: ‘A powerful vacuum cleaner is important with machines like this which are used on concrete. Moreover, your vacuum cleaner has to have continuous suction force. We can’t stress the importance of this vacuum cleaning enough, not only for the working environment itself, but certainly also for the operator’s health! We have all sorts of vacuum cleaners on offer. We supplement them with air purifiers, which also remove absolutely all very fine dust. At all events, we heartily recommend the combination of vacuum cleaner and air purifier.’
Shot blasters
We had mentioned dust-free work, but dust-free blasting did not come up in the conversation. Both gentlemen talked about shot blasters.
Ad Groenen: ‘This is a unique operation because it really is dust-free in combination with a good vacuum cleaner. This is ideal for roughening up bigger surfaces so the glue sticks better to the base.’ Kris De Rudder: ‘These machines use metal balls which blast against the concrete. They remove all remnants on the floor and roughen up everything. This yields a surface which is totally dust-free and rough. This application is highly profitable because you can treat big surfaces in no time at all.’ Ad Groenen: ‘You have to see shot blasters as a cheap way of roughening up dust-free. After the blasting, you can level any roughness and unevenness with a leveller. You always use shot blasters in combination with a vacuum cleaner with high suction and a high air flow. These vacuum cleaners work with continuous pneumatic filter purification. The filters are cleaned using an air pulse.’ Kris De Rudder: ‘What’s unique about this shot blasting is that you put recycling fully into practice. The blasted metal balls diminish in size after impact on the concrete, but thanks to the vacuum cleaner and a separator in the machine they are continually sucked up again and re-used. This process is repeated until the balls literally become so light that they are discharged together with ordinary dust. This material is used almost exclusively by professionals. Sound training is required in order to obtain the best possible results.’
Striving for a fully electric operation
We’ve discussed the most important machines, but nevertheless it’s interesting to consider briefly Husqvarna’s quest for a fully electric operation in the most popular categories by 2025. The use of petrol needs to be eliminated as soon as possible.
Kris De Rudder: ‘We already have a number of fully battery-powered portable tools and one ride-on carpet stripper and we’re going in that direction with the heavier machines as well. Our strategy is clear: electric and battery-operated. Recently, we’ve launched our K1 Pace cut-off saw, but also, for example, in the floor saws we’ve recently launched a floor saw with a diamond 600mm saw blade.’ ‘I also want to stress once again here how much importance we attach to the ergonomics of the machines and the user’s health. We also have service programmes and I refer once again to our Fleet sensor system which provides good follow-up for all machines and that illustrates how committed Husqvarna is to connectivity.’
New web site launched
We also mention that as of the middle of October Husqvarna has launched a brand new web site: http://www.husqvarnaconstruction.com This new web site also includes a compendium which has a full list of the available range and can be downloaded free.
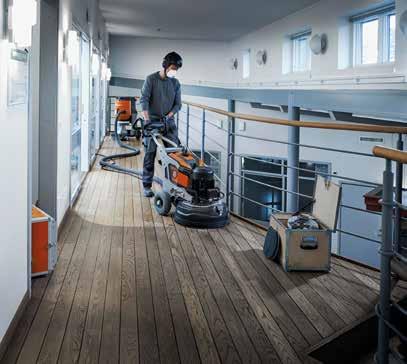
Photo – Husqvarna
The preparation, grinding, and polishing of concrete floors and the repair and polishing of terrazzo and other sorts of natural stone are demanding jobs. They require not only a good dose of strength and skills, but also suitable machines which can cope with this heavy work.
We called on one of the experts in the sector of floor grinding and polishing with the accompanying diamond tools, namely Husqvarna from Sweden. What do they have in their range as stand-out solutions? We consider their system with the licensed Dual Drive technology, examine the remote control machines PG 820 RC and PG 680 RC, and take a look at their approach to dust extraction.
Dual Drive
The most interesting place to start seemed to be their licensed Husqvarna Dual Drive Technology™, which they have designed themselves. This is a design with two separate motors, so the planetary head and grinding heads operate independently of each other. This function ensures an almost infinite number of settings and combinations and excellent process management. What happens is that the planetary head and the grinding heads can be set in the same or the opposite rotation direction thanks to the Dual Drive Technology. What happens if you grind in opposite rotational directions? In that case, when the machine moves forward, the ‘middle’ zone is ground more thoroughly than the ‘outer’ zones. The end result is a deeper cut in the middle zone and a less deep cut in the outer zones. This is a direct result of the greater impact which the diamonds have on the zone where they have worked. If both rotation directions are the same when the machine moves forward, the middle zone is still ground more thoroughly than the outer zones, but there is less difference than if you grind in the opposite direction. This yields somewhat more uniform results.
The important thing to remember is that this technology yields a considerably higher production speed. Users are given the opportunity to optimise the grinding process on the basis of the state of the floor and, if necessary, to use a more aggressive grinding segment to increase the grinding speed. PG 820 RC and PG 680 RC
And so, what about the Husqvarna PG 820 RC and PG 680 RC? The why of this choice will soon become clear from the use: These are the first self-driven floor grinding machines for concrete floors with Dual Drive Technology™ remote control. While the machine is at work, you can do lots of other jobs, and all that yields greater productivity and fewer exertions.
Compared to the standard versions of the PG 820 and the PG 680, the remote control RC versions increase productivity by over 30%. They also ensure a more ergonomic working method and easier transport to and from the site. Moreover, we would like to draw your attention briefly to the oscillation function. This is an innovative and new function which helps to procure an even smoother floor. The PG 820 has a grinding width of 820mm and is designed mainly for industrial applications. With its grinding width of 680mm, the PG 680 RC passes through standard door openings in offices, hotels, and private homes. These machines are used to prepare and repair concrete floors as well as for all polishing and grinding applications and they can also be used both wet and dry.
Dust extraction
With the dust extraction, we peep briefly at the DC 6000 since that machine is equipped with a filter process which comprises three phases. A licensed cyclone filter with double cylinder separates the heavier particles, and then a HEPA 13 filter absorbs the remaining dust particles. Thanks to the self-cleaning function, you can work with no loss of suction power or air flow. All particles are absorbed in a Longopac system, which is easy to empty. Due to its high capacity, the DC 6000 is suitable for use with high-quality concrete grinding machines such as the PG 820, PG 820 RC, PG 680, and PG 680 RC.
Bona
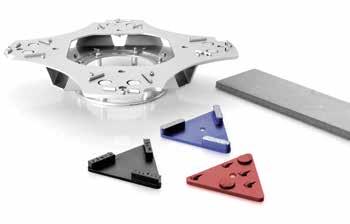
The Bona Flexisand sanding machine has proved itself time and again to be the most versatile machine for preparing substrates. By fitting the ‘concrete disc’ under the machine and selecting the right segments, professionals can level a surface, grind tiles, smooth a screed, and remove adhesive residue and bottom layers and such like before fitting a new floor. With tiles, they advise removing any grease before you use the sanding machine to remove greasy dirt rather than just displacing it. The only limitation of these machines is that they are not suitable for sanding very big surfaces (a few thousand square metres). However, for a private location or for sales areas which are accessible for the public, the combination of the Bona Flexisand sanding machine and the Bona suction unit yields the best possible dust management.