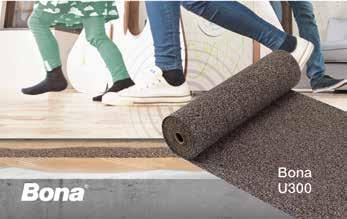
5 minute read
Special Subfloors : part III
ALL POWER TO ECOLOGY
MANUFACTURERS ARE GOING INCREASINGLY FURTHER IN THEIR QUEST FOR SUSTAINABILITY
Advertisement
What makes a subfloor ecologically responsible? More and more people are asking this question in times when care for the environment and sustainability are now key concepts. Prescribers such as architects are now also equally aware of the importance of operations rooted in a mindset with an eye to tomorrow and therefore manufacturers are responding to the wishes of the market.
When we consider the market, we notice how ecology divides into different facets. Obviously, from the start it’s about making elements of the ideal subfloor as ecological as possible. This means that you completely shun once universally accepted modules like softeners, asbestos, formaldehyde, halogen, and heavy metals and look for alternatives. Obviously, you do so without using solvents or other substances which affect the ozone layer. The alternatives take on many forms, but the main theme here is that the players are striving to use naturally occurring raw materials like mineral fillers and polyurethane binding agents, which can be re-used as much as possible after their active life.
Looking for ecological boundaries
By now, this search for naturally occurring and completely re-usable raw materials is now deeply ingrained in the world of architects. Recently, for instance, we discovered a project in Belgium which makes use solely of locally mined loamy soil for an architect’s own home. The soil was excavated on the site where the home was later to be built and that same soil was then used, for example, to make a rammed earth wall in the interior. You can hardly get more ecological than that (although it should be said that a few minimal additives were inserted to facilitate the processing of the loam). Do you want to remove the wall? If so, it will suffice almost literally to throw water at it and the wall ‘melts’ away. This completes the circle fully since the used earth returns to its original state, namely ‘mud’.
Sustainability also includes acoustics
Sustainability in subfloors also takes on other forms. An important aspect here is that the players are looking for ideal acoustics with the most ecological modules. Here we notice that amongst other things manufacturers are turning to polyurethane products in combination with high-quality insulation base layers which consist for 80% and even more of naturally occurring raw materials. Manufacturers are going a long way in their quest, and this means that in their quest for renewable raw materials they avoid going into competition with other economic sectors. No one wants their operations to put pressure on a sector such as food agriculture.
Another point which should be mentioned for sustainability and maximum ecological awareness is that players are keeping the supply chain as short as possible. We note how they are increasingly refusing to source raw materials from other parts of the world. Obviously, sourcing from other lands is still necessary for raw materials for which there is no local alternative (you can hardly produce a lithium battery locally if the raw material lithium isn’t available locally). The reason for this is simple: To reduce your ecological footprint as much as possible, you reduce your transport. If the players can use wood from their own forests, they will consider this alternative (and, if necessary thermo-treatment) rather than ordering the best container of wood in China, as happened in the past.
Recycling and reducing waste
What we’re also seeing specifically as regards substrates is that players are increasingly offering insulation substrates which are made from PE material such as synthetics. They are recycling as much as possible for the production of products, whilst they’re also paying more and more attention to recycling their own waste. At the same time, they are trying to look for ideal dimensions for the substrates to create other benefits during both the transport and the assembly on the site.
What’s on the market ?
BONA
BONA U300 – Sound insulation subfloor
A subfloor of bound cork and rubber granules. To be used as a subfloor for parquet, laminate, and other floor coverings. The material has a sound insulation effect. ∫ easy to fit ∫ improves all-round comfort considerably ∫ low risk of fire ∫ low VOC content Base: fine PU foam and cork granules of recycled rubber, polyurethane binding agent: Colour: brown (cork), black/grey/beige/brown (PU foam). EMICODE : EC1 Plus Density: about 550kg/ m3; Compressive strength: about 0.8 N/mm²; Elongation at fracture: about 30%;
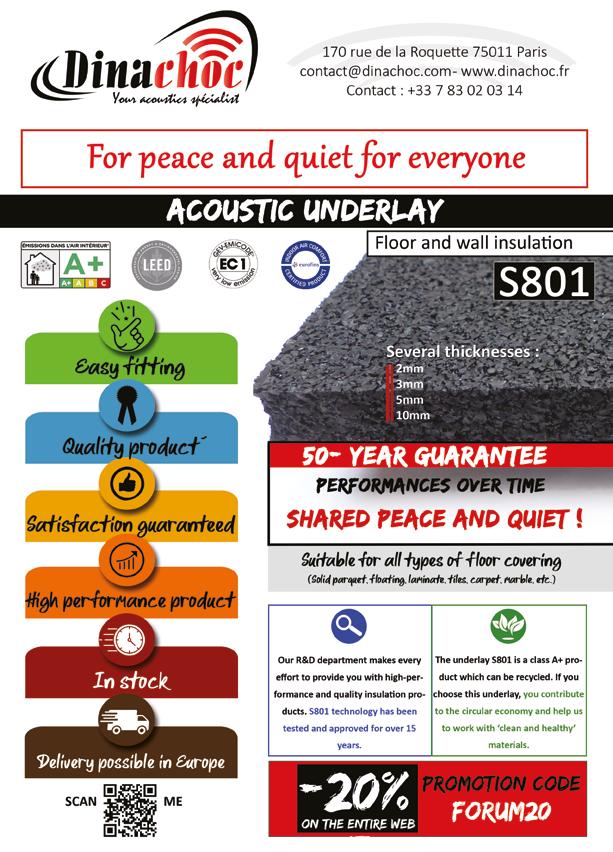
Thickness: 2, 3, and 5mm (± 0.3 mm) Temperature range: -30°C to 80°C Heat transfer coefficient: 0.04m²K/W for 3mm Fire resistance: Efl (EN 13501) Suitable substrates: (also with floor heating, if necessary) ∫ unheated or heated covering floors ∫ covering floor elements, chipboard or multiplex ∫ concrete ∫ mastic asphalt ∫ other expertly prepared substrates.
Design Parquet
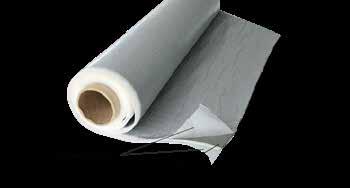
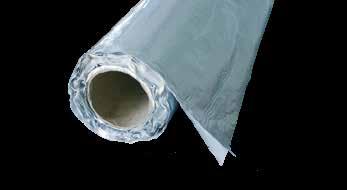
You choice your underlayers according to the use. There are 3 objectives : to sound insulation, to reduce the resonance noise or to create a barrier against moisture backing. Design Parquet offers different underlayers according to your needs. The most popular Design Parquet underlayers for their convenience are : - L’iso dB, patented system, is a ecological system (without CO² emanation), providing both fixing the parquet floor with sound insulation (18dB). This underlays allows fast implementation thanks to 2 adhesives faces. Glue isn’t necessary. - L’iso alu, meanwhile, is a waterproofing underlayer, a real barrier against moisture. We warranty until 10% of humidity in the support.
It’s easy to install with the adhesive face. The wood floor is glued on this underlayer with NAVYCOL PS glue.
Dinachoc
Dinachoc is the top specialist in acoustics. Here you choose efficiency and quality and at the same time you help to protect the environment. Their acoustic solution is universal and is adapted specially to most floor coverings. It protects you from noise, whilst you take care of your loved ones. Dinachoc S801 is an underlay which stems from the circular economy and makes a useful raw material of used tyres. With an A+ assessment, it is one of the healthiest solutions in the field of volatile emissions. The underlay is unchanging and will not shrink or fall apart. This is a comfortable and powerful long-term solution with a 50-year guarantee, and all this for professional insulation up to 22dB! For the completion of your fitting, you use Dinachoc C901, a hybrid and mono-component adhesive which is odourless and contains no solvents, isocyanate, or formaldehyde. Moreover, it has an A+ classification, and this means that the floor covering has a long lifespan and offers 3dB sound insulation. Increase the peace and quiet and freedom of life in your house. Dinachoc - 170 rue de la Roquette, 75011 Paris - 07 83 02 03 14 - contact@dinachoc.com - www.dinachoc.fr
Photo – Dinachoc