
3 minute read
Utilities and wastewater updates
WATER DISTRIBUTION INSIGHTS
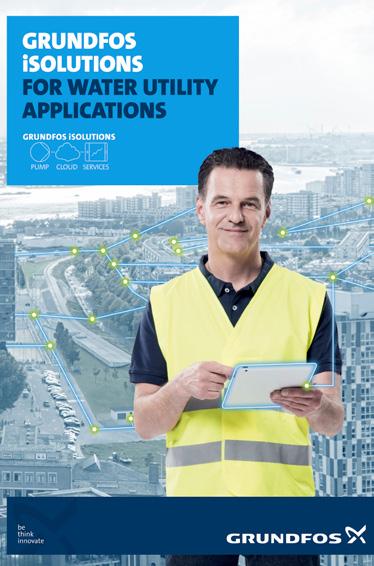
Advertisement
GRUNDFOS’ ISOLUTIONS HUB has been developed to offer water professionals an integrated approach that will allow them to look at the entire system in order to ensure optimised operations. The iSolutions approach integrates intelligent pumps, cloud connectivity and digital services to help users reach a new level of system control, optimisation and predictability.
A dedicated section for water utility applications on the hub includes video content and case studies that demonstrate water saving and energy efficiency, as well as how maintenance costs can be reduced. There is also access to dedicated training content on the Grundfos Ecademy, plus a whitepaper exploring pressure management and a detailed water distribution manual are available for download.
bit.ly/2ZhncfO
MODULE PROTECTS WATER AND WASTEWATER APPLICATIONS
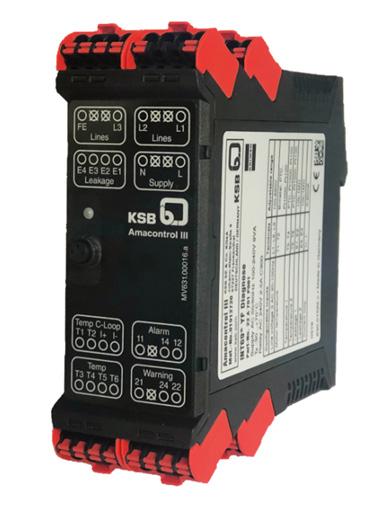
NEW FROM KSB, THE AMACONTROL III offers protection and monitoring functions for pumps and submersible mixers.
The device monitors phase-sequence and detects phase failures; it can also track any overvoltage/undervoltage or voltage asymmetry that may occur. Temperature sensors can also be monitored as can two conductance sensors for leakage monitoring and a 4-20 mA vibration signal. In addition, the frequency of starts and the number of operating hours can be logged while the failure of any connected sensors can also be detected.
A fault relay and a warning relay ensure that attached units are reliably stopped or, if required, a warning can be emitted.
An integrated diagnosis function provides operating data, fault lists, a fault counter, information on operating periods, start/stop cycles, current measurement values and detailed fault analysis for the most recent fault. This makes it possible to control the monitored units via an app on a smartphone or tablet.
www.ksb.com
THE HIDDEN ENERGY COSTS OF MEMBRANE DISC DIFFUSERS
XYLEM IS HIGHLIGHTING THE BENEFITS of fitting new membrane disc diffusers. Installed on the floor of aeration tanks membrane disc diffusers produce air bubbles that allow for the substantial and effective mass transfer of oxygen into the water and are crucial in encouraging the biological treatment process.
Unfortunately, over time the oxygen transfer efficiency of diffusers will slowly deteriorate and the dynamic wet pressure (DWP) rises due to the rubber being ‘fouled’ by organic matter and attacked by chemicals. A combination of declining standard oxygen transfer efficiency (SOTE) and rising DWP means that more air is required to provide the same amount of oxygen, coupled with higher pressure; this results in an increased power draw.
Faced with a need for additional air flow and increased pressure many operators resort to using energy-hungry temporary blowers. However, considering that an aeration system is responsible for between 30 and 70% of a wastewater plant’s overall energy demand, this can impact the plant’s bottom line.
To maximise membrane life while avoiding disruption, Xylem recommends the use of a weekly air bump cycle which involves over-inflating the diffuser membranes for a short period of time to shear off any membrane fouling. This will result in retained SOTE and minimises back pressure increase.
However, at a certain point within the life of the aeration system – typically seven to ten years after installation – the completion of recommended routine maintenance will not provide sufficient performance retention and it becomes cost-effective to replace the membranes. This investment will be recouped through lower power consumption.
CONDITION MONITORING PREVENTS UNPLANNED DOWNTIME AT TREATMENT PLANT
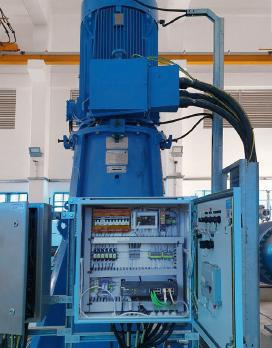
A DRINKING WATER TREATMENT company in Asia is preventing unplanned downtime of critical equipment across its pumping stations following the successful installation of a condition monitoring solution from Schaeffler. The customer operates a drinking water treatment facility where each day, 200 million litres of water can be treated. As the operator is responsible for ensuring a reliable supply of high-quality drinking water for the region, protecting the relevant facilities against failure is a key priority.
The customer was looking for an intelligent condition monitoring (CM) system to reliably prevent failures in its pumping stations. The solution comprises a custom designed CM system based on SmartCheck sensors. In total, 84 SmartChecks are fully integrated into the customer’s infrastructure via a PLC (programmable logic controller), monitoring the critical items of equipment across 15 pumping stations. Equipment monitored includes bearings on pumps and motors, as well as pump vanes/impellers. The SmartChecks monitor vibration, temperature and speed, as well as shaft alignment and balancing.
The data can be viewed individually at each pumping station or centrally in the control room. The system also allows the implementation of automated routines such as the triggering of alarms and the emergency shut-off of equipment.
www.schaeffler.com