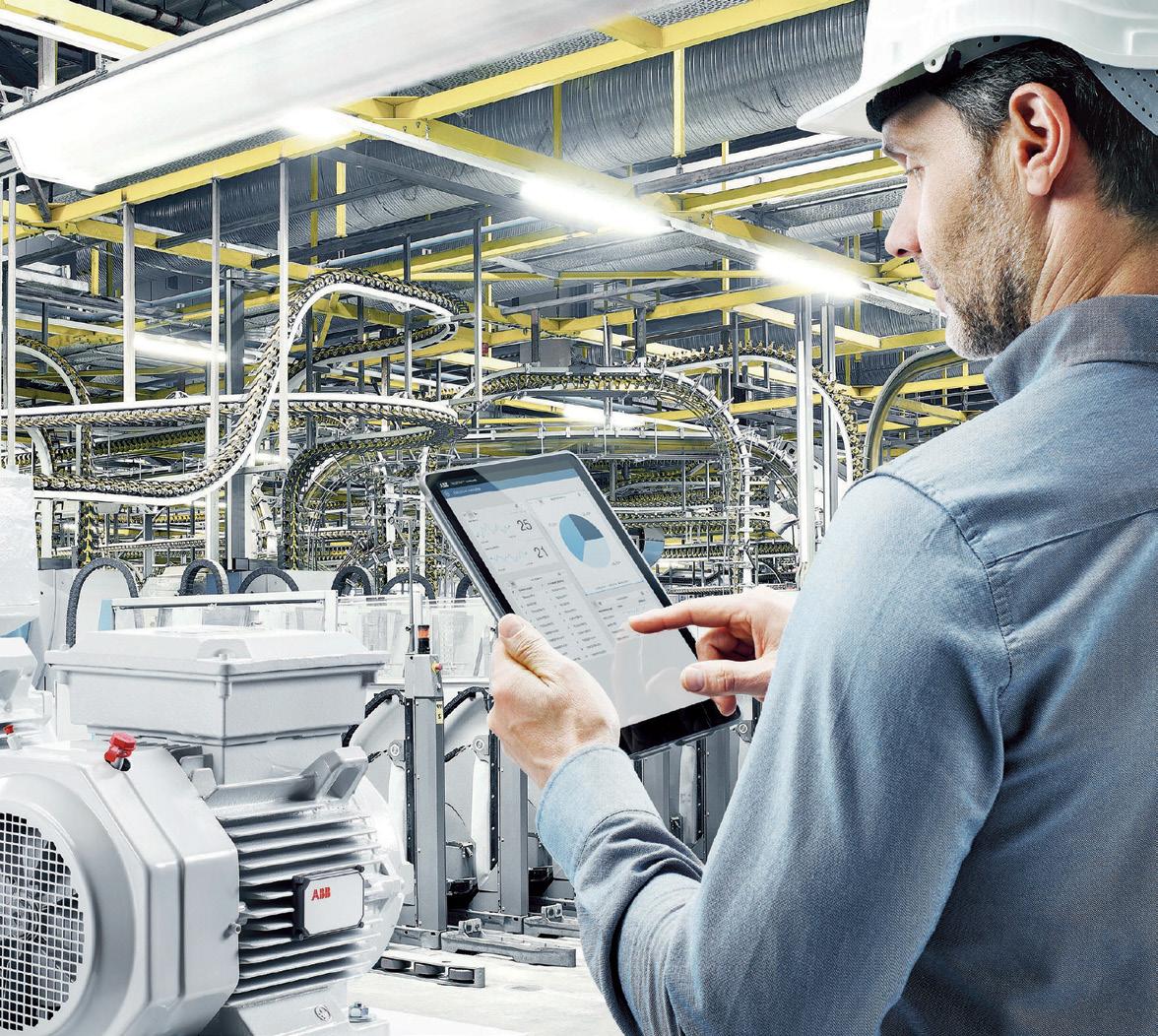
3 minute read
Energy Efficiency
REPAIR OR REPLACE: COST CONSIDERATIONS
Choosing whether to repair or replace an old motor is not always a straightforward decision. Rob Wood explores some of the factors that can determine which of the two options is the right one for your motor.
Advertisement
In general, a well-maintained electric motor is extremely reliable and can give you many years of service. However, motors are not indestructible, and poor maintenance or misuse can see them break down.
When this happens, you have two options: either repair the old motor or replace it with a new one. It is a tricky decision at the best of times, and if getting people and equipment on-site is a challenge in the current circumstances, then you need to know that you’re spending wisely. Upgrading a motor to a new high-efficiency model can pay off in additional energy savings; however, repairing the old one could still be the best decision depending on the circumstances.
Thankfully this decision can be made easier by making some simple calculations, considering your motor’s operating hours and costs. Bear in mind that no two applications are the same, so any decision for a given motor should be taken on its own merits.
RUNNING HOURS
Firstly, consider the motor’s running hours. If a motor runs for less than 2,000 hours per year, then the energy savings gained from installing a new motor are unlikely to justify its purchase cost. In this case, such a motor could be a good candidate for a high-quality repair or rewind. However, if the motor runs for more than 2,000 hours a year, then this introduces upgrading as a potential option.
UPFRONT COST
Secondly, compare the cost of repair against that of replacement. Typically, if the option to repair is around 60% or more of a replacement motor, then this makes the replacement a more viable option. If a replacement motor will be difficult to source or has high installation costs, then clearly this will need to be factored in as well.
TOTAL COST OF OWNERSHIP
Finally, calculate the motor’s total overall running costs. This looks at the costs of purchasing, plus running (i.e., energy use), plus not running in terms of annual maintenance.
The cost of not running is based upon process downtime and can be significant. For example, if we assume that a motor is offline for 30 minutes in a given year and that application downtime costs £150,000 per hour, and then apply this over a 20-year lifetime, this gives you a total cost of not running of £1,500,000.
As this example illustrates, the initial purchase cost is but a fraction of the overall lifetime cost of running or not running a motor, which is why it’s important to consider the lifetime costs carefully, and not just the upfront costs of a replacement or rewind.
In addition, a new motor may have a higher purchase cost than a repair, but the running costs will be lower due to its superior energy efficiency, and it should be less likely to break down, meaning a lower cost of not running.

REDUCING YOUR TOTAL COST OF OWNERSHIP
One way to significantly drive down both the cost of running and of not running is to digitalise your motor. Smart sensors are devices which attach, without hard wiring, to the motor’s frame and measure parameters such as temperature, vibration and energy consumption straight from the motor, providing near real-time feedback on operation and condition.
Data is transmitted via the cloud to a dashboard or can be viewed locally on a smart device such as a mobile phone or tablet from which it can be analysed, providing a window through which your motor can be monitored and optimised. This opens vast new possibilities for remote monitoring and predictive maintenance, allowing potential faults to be identified and mitigated long before they develop into failures, while parameters can be tweaked to improve efficiency. This can significantly reduce both the cost of running and the cost of not running over the motor’s lifetime. Moreover, by using smart sensors to prevent your motor from failing in the first place, you can sidestep the repair or replacement debate altogether. TIMES-CI