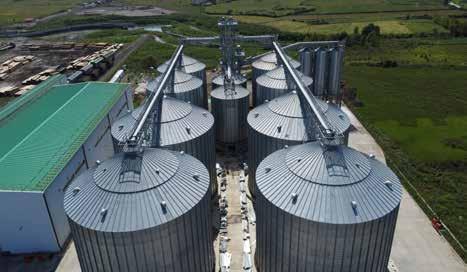
4 minute read
What about Simeza: New trend on all industrial fronts
2015 Simeza was purchased by the German company Petkus Engineering who invested in the steel silo business as the silos are significant components of their industrial and agricultural plants, and with the clear target to introduce the former family company into the international market.
The market is the benchmark of the investor, and the market of the steel silos is always moving to higher technical specification, to bigger dimension, to more reliable performances, to shorter delivery time, to extreme flexibility of the product.
Advertisement
In order to comply with the market requirements, Simeza planed a serial of individual innovative investments on either front of its activity which we are pleased to introduce as follows:
New Design:
• The roof of the silos is the most delicate and sensitive component of the structure of a silo, both from the static point and the corrosion of view.
• The roof was completely redesigned in the main component in order to prevent any welding operation, to allow only bolted assembly, to limit the tolerance, to increase the loading capacity, and to allow any potential finishing.
• The range of alternative solution was extended and is now including the std assembly, the double skin insulated assembly, the fumigation assembly, the color customized shape, the fully stainlesssteel bolting
New Static:
A new static was worked out according to the new design of the roof, by 3D FEM method for all different snow and wind loads, and now a wide data base is available in order to be ready to react in real time to each individual different enquire.
The size and the lay out of the supporting beams of the roof was optimized in order to be adequate for all different snow and wind loads and also to allow easy packing, transport, and assembly also for big size silos.
A new concept of static of the silos under seismic loads was worked out in order to be comply with the significant increase of the seismic coefficient required in many countries.
New Product:
The specification of the storage phase of cereals, oil seed, and paddy/rice in steel silos become every day more sophisticated in order to comply with the specification of the international trading, transport, or later processing of the same, and the silos must be equipped with dedicated additional devices accordingly.
Simeza worked out the industrial design of several accessories of the storage silo which were previously required only in special case, but are now coming usual for many plants, in order be manufactured by automatic lines inside the factory such as:
• various alternative solution of aeration system
• alternative structural and architectural solution of hopper silos
• alternative solution for grain ladder
• much bigger dimension/capacity of hopper silos
• various alternative solution of conveyor bridge and stair, complying with the new static and work safety norms of different countries .
New Clients
• Out of the national market, Simeza is oriented to the investors in large grain terminal required by the international trading
• Grain terminal to be either internal or port terminal, and dedicated to the export and import activities
• The scope and the operation of these terminal and the experience of these investors are requiring silos with much heavier specification than for agricultural plants, and size and lay out concept which allows high performances, high reliability, and easy operation of the plant
• The investors on this front are the new clients for Simeza, and the new property of the company is investing since years in new and additional sales and technical staff in order to satisfy same clients. Simeza already succeeds to get significant order on this front in several countries, such as Eastern Europe, North Africa, Middle East
New manufacturing lines:
• In order to implement the above-mentioned strategy, Simeza performed huge investment in the manufacturing lines, for example:
• Upgrading of the profiling line for corrugated sheet and vertical stiffener of the silos in terms of profiling speed, thickness and tensile of the steel, full automatic operation and control of the dimension of each individual item
• Installation of a new continuous decoiling and cutting line allowing the company to procure all steel only in coil with same zinc finishing and steel quality for all components
• Installation of a full automatic punching and cutting line for bended components coupled and integrated with a robotized bending line
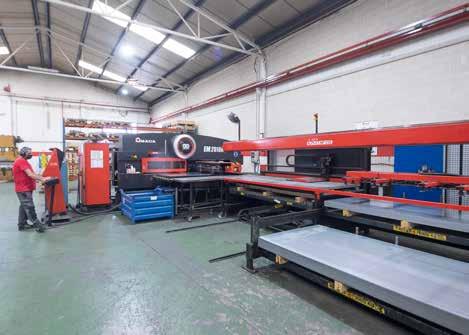
• Full automation of the punching and cutting line for roof panels, integrated with robotized bending line
• The factory is now equipped to manufacture up to 1.500 t of steel components of silo per month
New Factory:
• In order to get the benefit of abovementioned investment the factory was basically doubled by integration of a 3rd adjacent shed
• The rehabilitation and extension of the office is in progress
New Packing And Logistic:
• In order to comply with potential longer storage time of the supplied goods at site before the installation, and to prevent the risk of potential damage of the finishing, the packing method is realized by thin steel sheet without paper or plastic for each individual pallet.
• In order to comply with the shipment by both truck or container the packing concept is revised by using smaller weight and dimension of the individual pallet, allowing loading and unloading operation by front loader or crane.
• For easier loading of containers, the factory is equipped with 2 hydraulic platforms, and for quick loading of trucks the factory is equipped with 2 independent shipping hall, and the company can load simultaneously up to 2 trucks and 2 containers
New ERP
• Simeza has invested a lot of money and efforts in improving the ERP managing system of the company.
• The new system is already in operation for the sales, administration, and technical department, and is in advanced progress of installation for the control of the individual manufacturing cost, of the material stock, and for the continuous control of the manufacture.
• The system requires continuous upgrading and improvement and to this extent the ERP department includes staff of 3 dedicated engineers.