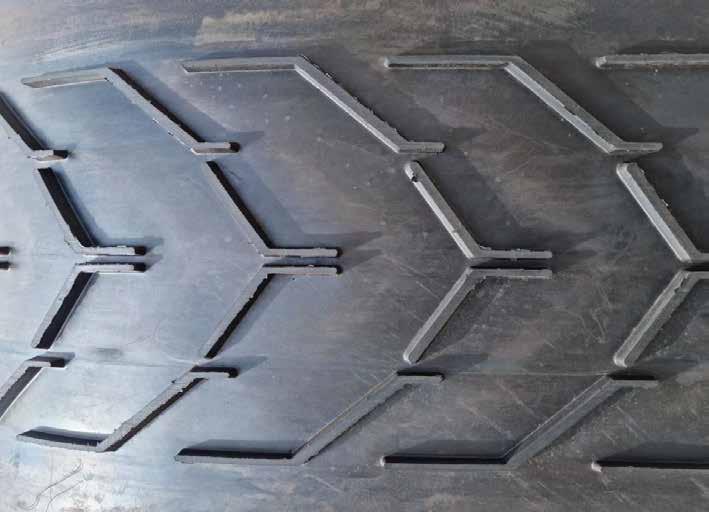
7 minute read
Steed Belting
Steed Belting and Eng. Supplies has collectively more than 50 years of experience in the conveyor belting and production line maintenance supplies industry, with specialised knowledge and experience in PVC, PU, PO, PE, Transmission, Rubber, Conveyor Chain, Elevator Bucket, Treadmill, Agricultural Belting and more.
We are involved in many different industries eg. Tobacco, Food Processing, Citrus, Agricultural, Packaging and with our knowledge and experience we are proud to provide an efficient and effective service to our future and existing valued clients. We are leaders in our field with regards to new technologies, existing standards and excellent quality of product and service. To date we have the 2 x High Frequency Welding Machines, one of them being largest and most versatile in Southern Africa capable of doing cleats to 1350mm wide. with an innovative and experienced team alongside.
Advertisement
Steed believes that a good customer-supplier relationship is vital to providing an efficient service. Through these practices we have built up strong relationships with our suppliers and customers. We provide a wide spectrum of manufacture/maintenance supplies to many industries, allowing a full solution to meet your needs. We are Authorised Distributors for the various market related products, allowing a cost effective and reliable alternative. Steed Belting is a Registered Imports/Exports Trader.
All Industry specific belting is manufactured inhouse to ensure the highest quality and best delivery times. All work done is covered by our product and workmanship quality guarantee standards. With our expertise and experienced team, we provide alternative replacement conveyor belting for a wide variety of OEM equipment that will equal or exceed the original OEM product.
PVC Conveyor Belting is a general and cost effective method of conveying your product, within your production line, to where it is required. Our large variety of belting is manufactured, and designed to work in all general conditions as well as in the most diverse varied applications and conditions.
We stock over 40 different types of PVC and PU belting and we are able to manufacture to your requirements and specifications. All sidewalls and cleated profiles are HF welded ensuring all belting is manufactured to the best quality standards available in the industry.
With the diversity in the many industries, there are different requirements when it comes to joining and splicing conveyor belts. Our workshops and site teams are professional and competent in these different methods, while adhering to your specific site Safety and Health regulations.
Our on-site tooling is well maintained and diverse enough to complete any job on site no matter how big or small. We are currently able to complete hot splicing on site for belting up to 3200mm in width, as well as cold splicing.
Our production team can produce your belting to meet your workshop or maintenance requirements and can supply endless, open ends, splice on site and mechanical fastening. Our experienced splicing teams are able to do many different types of splices best to suit your application requirements (small roller dia. flexible splicing, 24 hour planned maintenance shutdowns and an on call breakdown service).
Steed Belting has an innovative compliment of in field sales and technical personnel that can help advise on any future upgrades or modifications to existing machines or production lines. We are authorised distributors for many of the general maintenance consumable products such as bearings, sprockets and chains, motors, gearboxes, variable speed drives, electrical components such as inverters variable frequency inverters etc. With Steed representing these manufacturers, we are able to provide excellent pricing and delivery times to your demand.
& ENGINEERING SUPPLIES
PRODUCTS:
Conveyor Belting -P.V.C –Standard & FDA Approved -Polyurethane – Standard, FDA Approved, Piled & Solid Extruded -Polyolefin – Tobacco & FDA Approved -Natural Rubber – Standard & Tobacco / FDA Approved -Steel Slat -Agricultural/ Stroper Chain -Baler Belts- Made to size -Webbed Rod Belting New and Recon- Made to size -Felt Bakery Belting -Elevator Belting -Side Wall Steep Incline Belting -Aluminium Piping
DISTRIBUTORS/SUPPLIERS:
-Bonfiglioli: ACTOM, FLEXCO -Challenge: Sprockets, Bearings Chains and other related items
Service:
24 Hours, 7 Days a week, Splicing & Installation For belting up to 3200mm width CONTACT US: 084 430 6308 / 084 858 3585 E-MAIL US: steedsalesext@telkomsa.net / steedmarked1@gmail.com
Oilseed Production: Lower Capital Costs Do Not Always Equal Higher Profit
A review of Anderson’s Dox™ Extruder and Expeller® system for energy consumption and profitable soybean oil production
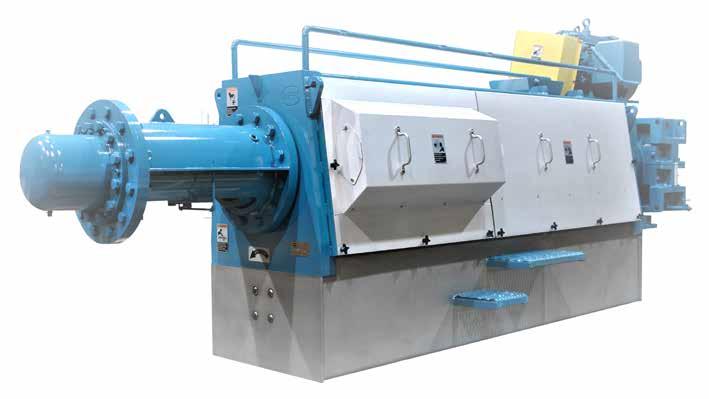
Like any business, oilseed manufacturing requires careful analysis of costs to derive maximum profit. Operators should carefully consider the total cost of both capital and operating expenditures when investing in new machines. The lower-cost option upfront may not prove to be such a bargain throughout a machine’s entire lifecycle. Today, there are compact extruders available on the market that can be purchased and installed at a relatively low cost. While these extruders have proven to be very popular in recent years, a quick analysis shows they can drive up costs over time in several ways. One of the most significant operational cost factors to consider with industrial equipment is energy consumption. It turns out that stand-alone, compact dry extruders lack energy efficiency, particularly when viewed within the context of the entire oil-extraction process.
Energy consumption
A quick examination of the specifications of leading systems demonstrates the energy consumption and subsequent cost savings.
Two compact extruders feeding one standard oil press Six compact extruders feeding three standard oil presses 12-inch Anderson Dox Extruder and 12-inch Oil Expeller press
Soy Processed 2 TPH
Combined horsepower 325 HP 6 TPH
975 HP 6 TPH
700 HP
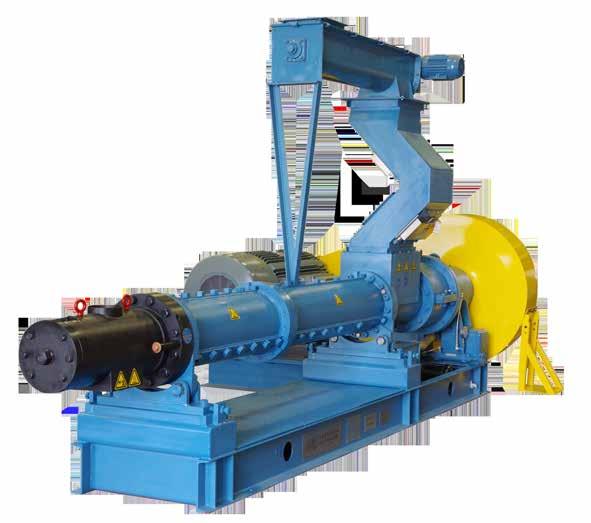
Those who invest in compact extruders will use two, one-ton per hour (TPH) extruders to feed a single, two TPH press. Two extruders with 125 Horse Power (HP) and a press with 75 HP equates to a 325 HP needed to process two TPH of soy. To handle six TPH of soy, these plants would have to run six compact extruders and three presses for a whopping 975 HP.
Why is six TPH important? Because that is the yield available from a single 12-inch Anderson Dox Extruder and 12-inch Oil Expeller press, which run at a combined 700 HP.
So while the Anderson configuration may cost more upfront, it saves more over the system’s lifecycle. And this savings is not insignificant. Going by the average energy cost of seven to nine cents per kWh, a typical producer could shave upwards of $100,000 off their operating budget per year.
Maintenance Costs
Energy consumption is not the only factor when calculating operating costs. Equally important are the repair and maintenance burdens associated with multiple smaller machines. Compact extruders are more likely to require a rebuild every three to four weeks. In contrast, the Anderson Dox Extruder has an average rebuild of 22 to 24 weeks, primarily due to its larger size and more rugged construction.
As operators know, maintenance is not only calculated by direct costs but also by the indirect cost of lost production. Of course, with six smaller machines, maintenance might be able to be scheduled so that only one-sixth of your production capacity is down at any one time.
However, experienced operators find that a longer maintenance cycle on a single machine delivers greater overall productivity than a process running at less than full capacity for extended periods of time
Quality Control
A third factor that is important to keep in mind is production quality. Processors that fail to provide adequate quality control tend to quickly lose business to competitors. By deploying a series of machines across the extraction process, manufacturers run the risk of producing inconsistent results as wear and tear, heat generation, and other performance metrics start to diverge. With a single extruder and a single press, the resulting oil will remain highly consistent.
Anderson’s Unique Dox Extruder
Anderson’s Dox Extruder is unique in that it comes in sizes of up to 6 TPH, it can operate for up to six months without maintenance and can also mount a drainage cage that allows it to process materials with high oil content. It is designed to cook and dry the material before the expelling process. Its high-shear environment ruptures the oil-containing bodies within the oilseed and generates frictional heat. This heat deactivates harmful enzymes within the oilseed.
It cooks the proteins for a more efficient pressing and then flash-dries excess moisture.
The numbers speak volumes.
The Dox is specifically engineered to double the capacity of an oil press, replace expensive steam-heated cooking vessels, double the life of the pressing parts, and reduce meal oil residuals to under 6%. Its size and rugged construction will significantly reduce operating expenses throughout the machine’s lifetime, easily overcoming difference in price compared to compact extruders on the market today.