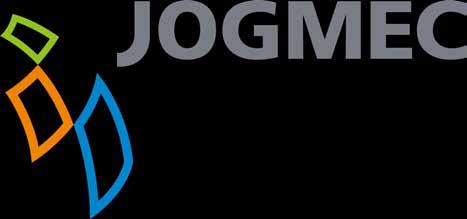
28 minute read
Mining Indaba Focus on African Minerals Critical for a Greener Future
Focusing on the ways Africa can optimise the opportunity to increase the supply of green metals for global energy demands while creating meaningful value for communities will be the emphasis of Investing in African Mining Indaba 2023 (https://www. MiningIndaba.com) which takes place at the CTICC, Cape Town, 6 - 9 February 2023. Green Metals Day, supported by keynote sponsor JOGMEC, will cover the impact of COP27 outcomes on green metal demand and supply; battery metals and carbon neutrality; green metals outlooks; Africa’s hydrogen potential; as well as ways to build domestic manufacturing industries as part of mineral value addition.
Advertisement
African mining and metals are critical to tackling the global climate emergency. Home to 30% of the world’s mineral deposits, including the critical minerals needed in green technologies and renewable energy, the continent is positioning itself to benefit from the green energy transition.
Simon Ford, Portfolio Director for Investing in African Mining Indaba, said “Mining Indaba provides the perfect platform to explore the balance between opportunity and value creation, particularly in the African context where the social licence to operate is as fundamental to success as the commodity being produced.” A Minerals for Climate Action report released by the World Bank in mid2022 estimates that demand for green metals could increase five-fold by 2050 to meet the growing demand for clean energy technologies. This massive boost in demand for minerals and metals will mean that mineral-rich developing countries, like those in Africa, can drive a net-zero future. “Attracting a share of the investment to low and middle-income countries could contribute to economic growth, jobs and local development,” the bank stated.
“Mining Indaba 2023 theme is ‘Unlocking African Mining Investment: Stability, Security, and Supply’, which explores African mining’s opportunities to tap into the global rush for the raw materials needed to ensure a cleaner future, while at the same time considering responsible sourcing and sustained, ethical supplies of these critical minerals.”, adds Ford. This view is supported by the International Council of Metals and Mining (ICMM), a foundational partner to Mining Indaba. ICMM President & CEO, Rohitesh Dhawan notes that “Critical minerals are the backbone of the energy transition, but how we source and produce them is just as important as how much we need,”
Supporting the Paris Peace Forum’s call for responsible sourcing and production of critical minerals, the ICMM warned that we are walking on a tightrope between an exponential increase in demand for these minerals, rising geopolitical tensions and urgent action on global issues such as climate change.
Simply put, the ‘green’ version of almost anything means the use of more metals but the ICMM doesn’t see this as a license for industry to mine them at all costs, added Dhawan.
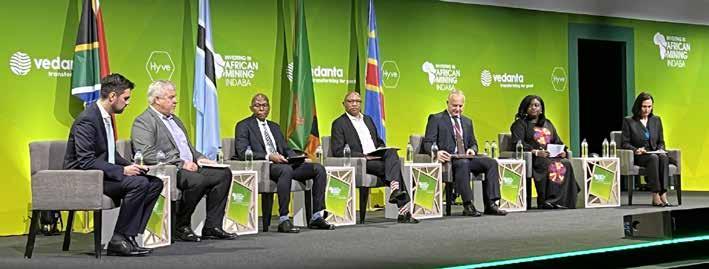
ABCDust decarbonization
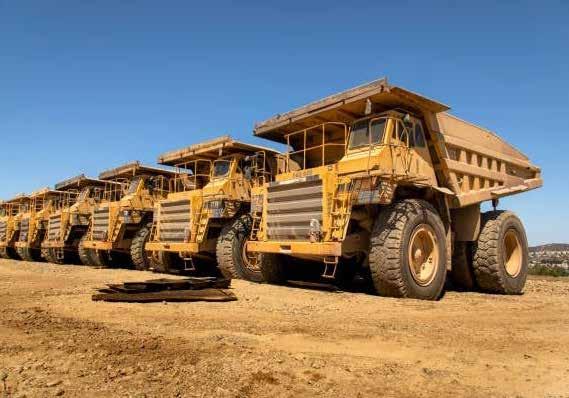
More mining companies are making bold commitments to decarbonize their operations to reduce business risk and help combat climate change.
The International Council on Mining and Metals (ICMM), which represents 28 mining companies and 35 commodity associations worldwide, recently committed to a scope 1 and 2 net greenhouse gas emissions target by 2050 or earlier, in line with the ambitions of the Paris Agreement.
As suppliers of metals and minerals essential to decarbonization and sustainable development, the industry has a responsibility to minimize its environmental footprint - and it is acting. While the speed and depth of decarbonization initiatives vary across the industry, many mining companies are taking immediate action, investing in areas such as renewable energy and electrification, and improving governance to align with global climate risk reporting standards.
Mining companies are under increasing pressure from various stakeholders to reduce emissions and address climate risks, which can have a negative financial impact on the company. Financial risk comes from the physical effects of climate change, such as extreme weather events, and the risks of transitioning to a low-carbon economy.
Challenges of Mining
Decarbonization in mining depends largely on electrification and renewable energy. In some ways, it is easier to imagine how mining can become carbonfree than other sectors. That doesn’t mean it will be easy.
Distinct or disproportionate drivers
Investors are putting strong pressure on large multinational players in the mining sector, particularly in relation to operational emissions. The rapidly declining cost of renewable energy has made it easier for them to respond. For example, BHP has signed a deal to develop new solar and wind farms in the Australian state of Queensland, which will allow them to run their coal operation in the region on solar power. They hope this will help them reduce their indirect emissions in the country by 20% over five years. BHP is also moving toward green copper by signing renewable energy contracts that will allow its Escondida and Spence copper mines in Chile to switch to 100% renewables, replacing imported LNG. It has also committed to eliminate groundwater use in Chile by 2030, invest in desalination plants.
With a patchwork of different national and local policies to navigate, many mining companies are designing their decarbonization strategies based on the strictest common denominator and then applying these tactics globally across their organizations. While mining and metals companies hope to price carbon and increase regulation, these are not the main drivers at the moment. Instead, investors and markets are ahead of where governments are, as evidenced by the growing number of companies signaling their decarbonization ambitions.
The supply chain pull is also generally stronger in mining than in other sectors. For example, battery manufacturers are starting to look for carbon-neutral lithium and nickel, while automakers are starting to ask for green steel and aluminum. Market demands like these could become the biggest driver of all. If customers start demanding green products, mining
companies must offer them to stay in the game.
What are the factors that can provide CO2 reduction in mining?
Cots – energy is a substantial and growing proportion of a miner’s cost, accounting for about one-third of the total cost base of mining companies. Most miners anticipate the introduction of a carbon price, which will increase the cost of diesel power.
Consumers – the COVID-19 pandemic has radically changed the sustainability mindset of consumers, with global markets becoming increasingly consumer-driven, social expectations are rising and participants at all stages of the value chain will have higher expectations of them to reduce carbon emissions. Capital providers – pressure is increasingly being applied by capital providers to meet decarbonization targets in order to access financing for mining projects.
Cots – energy is a substantial and growing proportion of a miner’s cost, accounting for about one-third of the total cost base of mining companies. Most miners anticipate the introduction of a carbon price, which will increase the cost of diesel power.
How mining companies can align their actions to meet the industry’s carbon reduction goals.
Mining companies should ensure that their carbon reduction policies are aligned with industry standards from an ecosystem perspective. This is vital to avoid greenwashing, which occurs when companies claim to be dedicated to carbon reduction for the sake of their reputation, but fail to back up their claims with action.
This alignment is necessary to provide consistent reporting methodologies. Maintaining a social license to operate is crucial for many mining companies. This even affects the company’s employees. As a result, large multinational corporations are increasingly looking to be at the forefront of environmental challenges to recruit the best talent.
In which areas should the company focus its efforts?
The areas that require decarbonization in mining vary among the different elements that contribute to the success of a mining operation from pit to port. Decarbonization in mining is required in the following areas:
• Transport; • Mineral processing; • Diesel Trucks; • Supply chain; • Mineral exploitation; • Electricity supply; • Transportation of goods.
Green technology as a decarbonizing agent
Green technology in mining refers to equipment that reduces carbon emissions and mitigates negative environmental effects. Green mining is now a crosscutting concept for the entire industry, where the global mining scenario is already adapting it to its entire process chain. Green mining alludes to sustainability and the care of each process, such as efficiency in resource extraction, production with less environmental impact, and care for the surrounding communities, among other points. Through this new form of mining, it is expected that the practices within the industries will be optimized and improved to make each process more efficient and conscious.
How can ABC Dust help mines decarbonize their process?
ABCDust is a company focused on developing green technology for smart dust control and soil stabilization. ABCDust’s sustainable solutions help mining companies reduce their C02 emissions: • Reducing the water used for dust control by 90%, which translates into fewer hours of water transport and energy consumption to move and process water; • Improving road rolling resistance with our soil stabilization and dust control solutions. Rolling resistance is the energy lost through drag and friction of a tire rolling over a surface.
A 10% reduction in rolling resistance would improve fuel economy by approximately 3% to 5% for light and heavy-duty vehicles and improve the life cycle of your tires by up to 5%. Open-pit mines use haul trucks that use an average of 50 liters of diesel fuel per hour. Large mines have a fleet of 70 to 150 haul trucks that operate 24/7/365. This can add up to 300,000 liters of C02 diesel consumption reduction per year, plus
the fuel savings alone; • Increasing the life of mining roads by reducing the frequency of grading and maintenance required. Also, reducing the need to use aggregates to improve road properties; • Increasing the life of tires and haul trucks. A better, dust-free road uses fewer tires and extends the life of haul truck suspension systems and filters.
ABCDust - Smart dust control and soil stabilization
Dust suppression
DMS dust suppression solutions and high-performance soil stabilizers are created by the following combination: • DMS® solutions for high performance dust suppression; • Soil stabilizers with electronically controlled wetting equipment; • Georeferenced road dust and friction monitoring systems; • Georeferenced road roughness monitoring systems.
As a result, a completely new dust suppression technology was created and a patent application was generated. Our products are delivered precisely when and where they are needed, resulting in increased productivity, longterm sustainability, and safety. Dust suppression, better soil stabilization, water conservation, shorter braking distances and low maintenance costs are all characteristics of DMS products.
The following DMS® solutions are available for dust reduction: • DMS-DS: Dust control on mining roads. DMS-DS® dust suppressor is suitable for haul roads and high altitudes, and can withstand up to 600 tons of loading; • DMS-EB: DMS-EB® is a clean solution that traps particles and improves road and soil stability; • DMS-DS 80: It is a low-cost dust suppressant and soil stabilizer that is also chloride-free and environmentally harmless. It is successful in a variety of soils, although silty and low water-retention soils produce higher yields; • DMS-TDS: This is a non-ionic dust suppressant designed for continuous lines of conveyor belts on loading fronts, crusher chutes and/ or high frequency material conveying systems. By using ABCDust solutions and
services, you can achieve 95-99% dust reduction, thus saving lives, improving the environment, saving money, and ensuring your operational continuity and social license. Please feel free to contact us for more information.
Soil stabilization
We use soil stabilization solutions to improve many types of roads and sites in different industries such as mining, forestry and construction in Canada, Chile, Peru, Colombia and Brazil. Our solutions strengthen the soil and enable it to withstand more pressure and capacity from heavy vehicles, thus improving the logistics of the sites.
We offer a wide range of products (enzymes, polymers, synthetic oils and asphalt emulsions) that have been formulated to meet different road needs and reduce the need for aggregates and road maintenance. Our selection of products for soil stabilization is very economical, environmentally safe, and non-toxic.
Here are some of our solutions for soil stabilization: • DMS-DS® 100 is specially designed for soil stabilization and dust control of industrial roads, haul roads and tightly compacted surfaces, improving their overall strength and the binding of road materials; • EZISS PRO® is a natural liquid soil stabilization enzyme, which improves the properties of native/ local soils; • CHEM-STAB® is a sulfonated
(ionic) chemical based soil stabilizer, formulated with ionizing complexes associated with ion exchange elements; • SOILCELLS® are high density polyethylene panels used for soil containment. The three-dimensional structure of the cells allows the granular material to be confined and thus avoid any displacement caused by erosion or static or dynamic loads. This versatile material can be used for slope retention, soil reinforcement, road infrastructure and as a retaining wall.
Dust Monitoring
Due to the nature of the comminution and classification processes, the blasting, transporting, crushing and milling of ores makes them major contributors of dust emissions into the air. Workers, the environment and nearby wildlife are all affected.
ABCDust provides a dust monitoring service to its clients that employs the EPA’s PM10-2.5 near reference measurement technology to provide a consistent assessment of dust levels in a variety of environmental circumstances and production levels (Ton/hr). To assess PM10-2.5 dust levels emitted from operations, we employ dust management methods.
Here are some of the features of our dust monitoring solution: • For PM 10, 5, 4, 2.5, and 1 particle, multi-channel dust levels up to 4,000 mg/m3 are continuously monitored; • Gravimetric samples are used to describe and quantify mg/m3 dust emissions; • Modeling of dust emissions using a variety of parameters (winds, humidity, production, material type, etc.); • Solutions for dust control are suggested (maintenance, dry mist, fine mist, dust collectors, additives, etc.); • Before and after implementation, improvement options are reviewed; • Report on emissions both before and after implementation of the measure.
Global decarbonization depends largely on the sustainable mining of minerals and raw materials. A thriving and healthy mining industry is critical to the global economy and supports the innovation needed to mitigate global warming, protect the environment, and develop the circular economy.
Focusing its efforts on the areas of greatest impact by aligning with clean technology and green technology applications is the first major step towards the goal of decarbonization in the industry.
Regardless of the paths taken by mining companies to lower carbon emissions, achieving the reduction targets under the Paris Agreement and meeting the expectations of a more environmentally conscious population are key to the longterm viability of the industry.
The biggest range of OTR tyres for the Mining, Industrial & Construction sectors
OTR supply earthmover, agricultural, truck, bus and light vehicle tyres and rims to blue chip mining, civil contracting, road transport companies agricultural dealerships and end users and can source and ship to anywhere in Africa.
We maintain a healthy inventory of new and used earthmover tyres of critical sizes and have readily available stock of truck, bus, agriculture, industrial and light vehicle tyres for all applications.
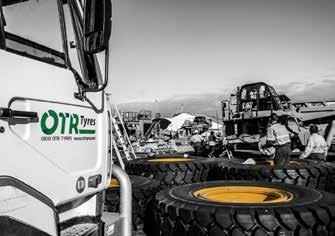
SALES PHONE +618 9250 8949
For any enquiries please visit www.otrtyres.com
Perth | Yatala | Mildura | Muswellbrook | Emerald | Karratha | Port Hedland | Kalgoorlie
ERG and Gécamines restart operations at Boss Mining in the Democratic Republic of Congo
The phased restart of Boss Mining will commence with the processing of the historically mined Kiwana fines at its Luita concession, paving the way for further development
Eurasian Resources Group (ERG) and its joint-venture partner, La Générale des Carrières et des Mines (Gécamines), celebrated the kick-off of the restart of operations at Boss Mining with a ceremony held at its concession on 23 November 2022.
Boss Mining, located in the Lualaba and Haut-Katanga provinces of the Democratic Republic of the Congo (DRC), has a long history of copper and cobalt production from significant openpit resources. Boss Mining was placed into care and maintenance early 2019 to allow for ERG and Gécamines to assess different investments paths and conduct further studies to improve Operations’ economics and sustainability.
Benedikt Sobotka, Chief Executive Officer at ERG, said: “We are not only celebrating the return to production at this time, but also our long-standing partnership with Gécamines and its professional team, without whom this restart would not have been possible. ERG believes that collaboration is the key to building a better future.”
Recognising that mining plays a vital role in the social and economic upliftment of its host communities, ERG aims to develop and scale operations at Boss Mining in a sustainable way to allow for positive, longer-term social, environmental and economic outcomes.
“We are proud that this phase of the restart will create around 750 jobs for DRC citizens, primarily recruited from the surrounding communities, ensuring that direct members of our communities are the primary beneficiaries of Boss Mining’s activities,” added Sobotka.
Provincial Minister of Interior and Security of the Lualaba Province, Mr. Kapenda Wa Kapenda Déodat, commented: “As a government, we can only rejoice once again because the restarting of an operation means not only the creation of jobs for our population, but also that the tax revenue of the province will increase. And every time there is production, we know that there is a small amount that goes into the government’s tax coffer that helps us develop other sectors of our society.”
The phased restart will concentrate on processing historically mined fines over the next 16 months to produce copper cathodes and cobalt hydroxide. The operation will ramp up over the coming months to its full capacity producing, on average, 1,800t of copper cathode and 300t of cobalt hydroxide a month, by March 2023.
“The current restart is only the beginning of our journey, and will provide financing for further potential development, exploration and other mining-related activities at Boss Mining. I am convinced that the revival of Boss Mining’s activities will allow for the creation of important number of new jobs in the future and the union of countless families from the surrounding communities and the four corners of the country,” said Chief Executive Officer of Gécamines, Mr. Ntambwe Ngoy Kabongo.

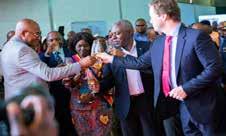
Boss Mining is also currently renewing its five-year ESIA commitments and formalising its Cahier de Charges. Restarting the production will allow Boss Mining to update its commitments and social contribution, in turn supporting the action programme of the DRC President, His Excellency Mr. Félix Antoine Tshisekedi Tshilombo, which aims to improve social conditions through housing, health, education and employment.
“It is important for us to transmit to you the message of encouragement of his Excellency the Governor of Haut Katanga, Mr. Jacques Kyabula Katwe, who sees this restarting of Boss Mining as a vital sign of life returning to the territory of Lubudi and the economic life of our province, Haut Katanga. ERG and Gécamines have our full support for the relaunch of this giant amongst the mines,” assured Provincial Minister of Mines and Hydrocarbons, Mr. Georges Mawine Kaindu.
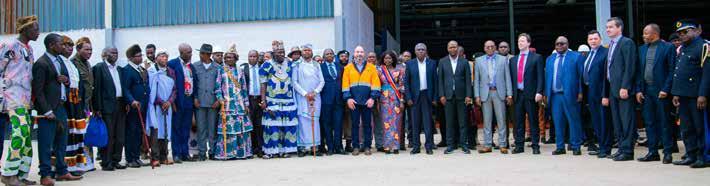
Drilling fluids for mineral exploration
Drilling fluid, also called drilling mud, is used to aid the drilling of boreholes into the earth. Often used while drilling oil and natural gas wells and on exploration drilling rigs. Drilling fluids are also used for much simpler boreholes, such as water wells.
According to the BIS Research analysis, the global drilling fluids market was estimated to be at $6.1 billion in 2021, and it is expected to grow at a CAGR of 7.8% and reach $12.6 billion by 2031. Along with the increasing onshore drilling activities, offshore drilling activities are also expected to increase significantly due to the rise in energy demand, which will lead to further growth in the global drilling fluids market.
The main functions of drilling fluids include providing hydrostatic pressure to prevent formation fluids from entering into the well bore, keeping the drill bit cool and clean during drilling, carrying out drill cuttings, and suspending the drill cuttings while drilling is paused and when the drilling assembly is brought in and out of the hole. The drilling fluid used for a particular job is selected to avoid formation damage and to limit corrosion.
Common drilling fluids are water, bentonite mud, cutting oil, and polymers (both water-based and mud-based).
Water-based drilling fluids are the most commonly used of the mud systems. They are generally less expensive and less difficult to maintain than oil muds, and in some special types of systems, they are almost as shale inhibitive.
Bentonite on the other hand is used in drilling fluids. The bentonite in the flush fluid lubricates and cools the cutting tools whilst protecting against corrosion. As the drilling fluid generates hydrostatic pressure in the borehole, it hinders fluid and gas penetration.
Cutting oil is designed to maximise the life of cutting and drilling equipment; working under extreme pressure, improving performance and extending the life of tools. Cutting oil improves machine finish, lubricates to reduce tip welding and prevents pitting and metal seizures.
Drilling polymers on the other hand have high molecular weight fluid with the ability to control the well’s fluid loss and to increase the viscosity. There are over four variants of this chemical which can include polyacrylate, Snergistic polymer, polyglycol, XCD polymer or partly hydrolyzed polyacrylamide.
When choosing a drilling fluid, several factors are considered. For example temperature, well type, environmental impact and overall Fluids Performance.
When drilling in places with high temperature, the effectiveness of chemical additives is generally reduced and can lead to changes in viscosity and fluid loss. Drilling fluids which can resist to such environment can be used like the oil based mud systems.
Understanding a well type is crucial to determine the drilling fluid to use. In exploratory drilling for instance, the information about the region are not enough to design mud properties. The designed mud system has to contribute in obtaining the geological information easily and safely. The mud composition has to allow for quick change in case of unexpected changes or problems.
Environmental issues are still the important considerations when planning and implementing for the drilling fluid. For example, in offshore operations, synthetic or mineral oil based systems are used rather than diesel oil based system.
Emerging technologies
Drilling fluid technology is constantly evolving because of the escalating demand brought on by more demanding environmental factors such as high temperature and pressure, tight gas and shale gas reservoirs, as well as rising technical standards such as increased lubricity requirements in air drilling and tightening regulations on oilbased systems due to environmental remediation. Researchers at Curtin University in Australia for instance have developed new technology for the rapid cleaning and re-use of drilling fluids, paving the way toward more efficient and environmentallyfriendly mineral exploration.
Supported by the Minerals Research Institute of Western Australia (MRIWA) and the Deep Exploration Technology CRC, Dr Masood Mostofi and his research team at the Western Australian School of Mines: Minerals, Energy and Chemical Engineering (WASM: MECE) at Curtin University developed the new technology as part of their ongoing research toward automating fluid monitoring and handling in the drilling industry.
Drillers exploring deep beneath the surface for mineral deposits need specialised fluids to lubricate and cool the active drill head, and that won’t leak away through cracks and porous rocks around the drill site.
“New Coiled Tubing drilling technology being developed for mineral exploration needs much higher volumes of these special fluids than conventional drilling,” said Dr Mostofi.
“We have developed a system that can meet these fluid needs in remote locations where geologists might explore for new mineral deposits, and reduces the risk of releasing fluids that might affect the local environment.
The drilling fluid eliminates the use of hydrocarbons. Also developed is a method of keeping boreholes stable and rapidly separating rock chips and solid materials from the fluid as it returns to the surface.
And as environmental conservation takes centre stage, such innovation that have minimum negative impact on the environment are likely to become commonplace going into the future.
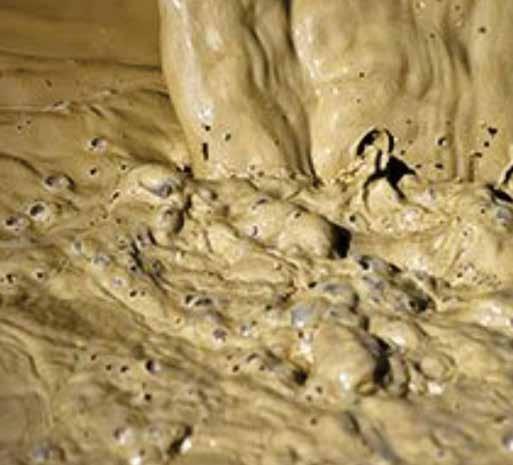
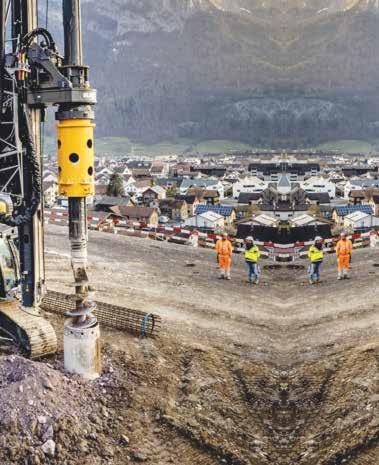
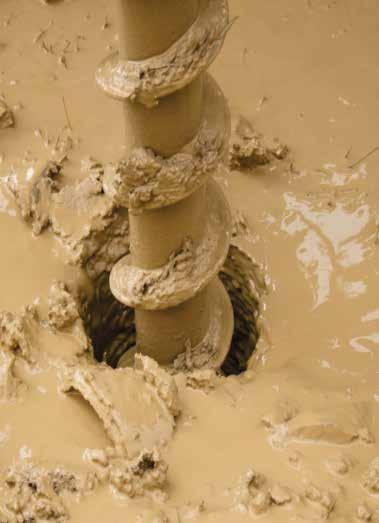

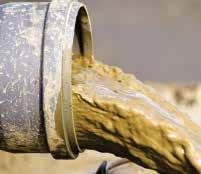
Kamoa Copper’s journey to being one of the world’s lowest greenhouse gas emitters per unit of copper produced
The phased restart of Boss Mining will commence with the processing of the historically mined Kiwana fines at its Luita concession, paving the way for further development

The United Nations’ annual COP27 climate change conference is already well underway in Egypt and the topic of developing and deploying lowcarbon technologies, which are critical for the world to achieve its net-zero targets, is high on the agenda. Because the deployment of low-carbon technologies relies heavily on minerals, the mining sector is critical in the fight against climate change.
Africa, a continent rich in minerals, will play a leading role in the supply of key minerals such as copper, cobalt and platinum group metals. These minerals are critical for renewable energy, hydrogen, and battery energy storage technologies – all of which are required for the clean energy transition. However, this must be addressed against the backdrop of Africa’s climate vulnerability and climate adaptation needs.
By doing its part in prioritising lowcarbon investments and partnerships on the continent and building agency and capability, Kamoa Copper plans to become the first net-zero operational carbon emitter among the world’s top-tier copper producers. We believe that mining companies can be the champions of global decarbonisation, not just in reducing their operational carbon emissions and producing lower carbon minerals and metals, but also in producing the critical raw materials needed to facilitate the global clean energy transition. electric batteries or hydrogen fuel cells, supplied by Swedish original-equipment manufacturer Epiroc. This includes the Minetruck MT65 haulers, the world’s highest payload underground truck in the field, as well as Scooptram ST18 loaders and Boomer 282 face drilling rigs.
In 2021, Kamoa’s Scope 1 emissions were 17,634 tCO2e, while its Scope 2 emissions were zero, thanks to its use of 100% renewable electricity usage. The Company’s Scope 3 emissions (currently calculated on the Company’s land and air travel) totalled 2,091 tCO2e. “Once we achieve net-zero Scope 1 and 2 emissions, we will turn our focus on achieving net-zero total emissions at the Kamoa Copper Mining Complex, which will include Scope 3 emissions and become an industry leader in the fight against climate change,” says Ivanhoe Mines Founder & Co-Chairperson Robert Friedland.
A 2020 independent audit of Kamoa’s greenhouse gas intensity metrics performed by consulting engineering and project implementation firm Hatch, confirmed that the Kamoa will be among the world’s lowest greenhouse gas emitters per unit of copper produced. Copper is an irreplaceable element required in the manufacture of advanced decarbonisation technology including electric vehicles, wind turbines, and solar panels.
emissions at its Kamoa Copper Mining Complex in the Democratic Republic of Congo – a commitment that supports the 2015 Paris Agreement on climate change, which aims to sharply cut carbon emissions to reduce the threat of climate change.
Scope 1 emissions are classified as direct greenhouse gas emissions from company-owned and controlled resources, for example from vehicles, equipment, and machinery, while Scope 2 emissions are indirect greenhouse gas emissions, usually from the generation of purchased energy. The Company’s Scope 3 greenhouse emissions are currently calculated from its land and airrelated travel and cover the travel across the operations as well as from our head offices.
Kamoa is already making progress on achieving its net-zero goals. The Company’s mining operations and its Phase 1 and 2 concentrator plants are currently being powered by clean, renewable hydro-generated electricity from the refurbished Mwadingusha hydropower plant. Following the successful upgrade of Turbine #5 at the Inga II hydropower plant, which is currently under way, these two hydropower plants will provide Kamoa Copper access to a combined estimated 256 MW of clean, renewable electricity for Phase 3, the smelter and future expansions, while also benefitting local communities. Meanwhile, the Company has also recently taken delivery of several key pieces of stateof-the-art mining equipment powered by
Why On-line particle distribution analysers are is increasingly becoming popular
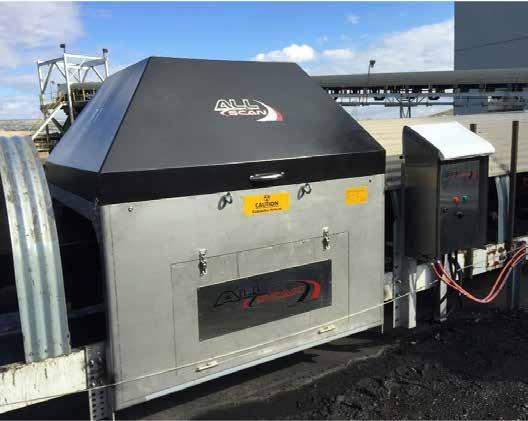
AParticle Size Distribution Analysis helps determine information about the size and range of particles representative of a given material. This analysis can be performed using a variety of techniques; the most suitable will be determined based on the sample properties and question at hand.
Sieve analysis still is the traditional and most commonly used method for particle size determination. A sieve stack consists of several sieves with increasing aperture size stacked upon each other and the sample is placed on the uppermost sieve. The most common sources of errors are overloading of the sieves, old, worn or damaged sieves or errors in data transfer. It should also be taken into account that the aperture sizes of new standard-compliant sieves are also subject to certain tolerances. In modern processes, automated online particle size measurement is being embraced more and more by the mineral processing industry because of the distinct advantages it offers over manual offline measurement and the cost efficiencies it is able to deliver.
One advantage of automated on-line particle size measurement is that it provides a continuous stream of data, which allows for smaller changes to be made more often, thereby reducing wastage during reaction time, allowing problems to be rectified before they can escalate further and optimising operational flow. Where the ore being extracted is of particularly high value such as gold, these cost efficiencies can be significant.
Modern technologies
A laser diffraction particle size analyzer uses multiple light detectors, with more detector elements extending sensitivity and size limits. The time needed to measure particle sizes varies by instrument, ranging from 2 seconds to 10 minutes per sample. The light source used by a laser particle size analyzer also affects particle size measuring limits; shorter wavelength violet and UV lasers are better suited to measure submicronsized particles than red lasers.
Laser diffraction particle size analyzers are used to measure the sizes of particles in a material. Particle size is calculated by measuring the angle of light scattered by the particles as they pass through a laser beam. Laser diffraction analyzers are used in many applications, including manufacturing, quality control and product development. Because this technique can continuously measure particle sizes across a wide range, from 10 nm to 3 mm, laser diffraction particle size analyzers are often used in industrial settings.
Most studies have confirmed that return of investment for on-line laser diffraction occurs anywhere between six months and a year following installation. The biggest reason for this is that there is much less reliance on manpower; manual analysis methods generally necessitate highly-skilled individuals to be working around the clock, while on-line systems only require occasional intervention from a semi-skilled worker, lowering costs in terms of both time and expertise. These lowered man hours have the added benefit of minimising the risk of hazard material exposure.
Image analysis involves processing an image into fundamental components to extract meaningful information. Upon completion of the measurement, results are available on a variety of size, shape, and intensity parameters, such as
Circular Area Diameter, Length/Width, Aspect Ratio, Circularity, Convexity, and Opacity/Transparency along with several others depending on the instrument manufacturer.
Using static imaging, the particulate is dispersed onto a stage where it remains fixed during analysis. Static imaging systems offer versatility in that various sample states can be analyzed: dry powders, liquid suspensions, particulate captured on filters, in addition to creams and lotions. These systems also have the ability to reanalyze the same particles more than once, allowing for more indepth investigation
Ultrasonic attenuation has been applied in wet mineral processes since the 1970s. Because ultrasonic particle size measurement is sensitive to air bubbles, the sample has to be deaerated before measurement. Recently, ultrasonics has been combined with gamma-ray transmission and sound velocity measurement for more accurate solids content compensation (Coghill et al, 2002). The sample volume measured can be relatively large, which is an advantage of this technology. However, the major limitations in mineral processing operations are its sensitivity to air entrainment, flaky particles, solids content and slurry viscosity changes.
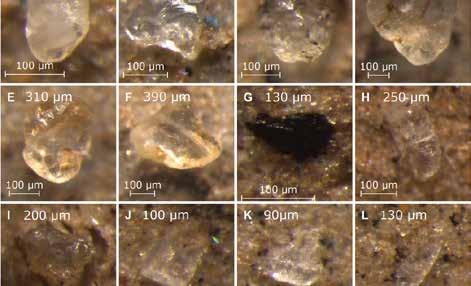
Conclusion
Companies are increasingly adopting on-line methods especially due to their efficiency and ability to detect a problem early enough to act. With off-line particle size measurement, problems can go undetected for hours, but with on-line methods such as laser diffraction, there is constant monitoring of the process and upsets can be detected as they occur. Again, while with off-line particle size analysis requires the analyst to wait until several samples have been taken and analysed before they can see the outcomes of their changes. With an online particle size analyser, however, this process is much quicker. Assessing new operating scenarios requires nothing more than a new steady state to be established, meaning the changes can be evaluated in minutes.
NEXT GENERATION SMART ELEMENTAL ANALYSER
Smart. Accurate. Reliable. Boost productivity. Increase yield.
The AllScan® n-Gen elemental analyser is your high-speed ore sorting solution. AllScan gives you full control over stockpile grade, increasing production and yield and delivering higher grade, cleaner outputs.
Scan this QR code to visit the RTI website and download an AllScan® brochure