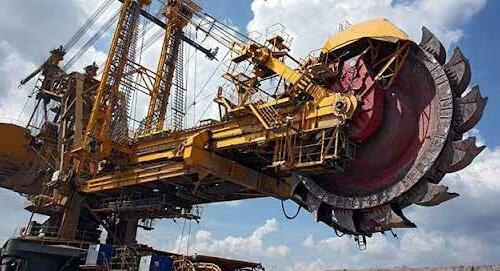
15 minute read
Industrial Shredders in Mining
Industrial shredders are high powered equipment and are often designed as per the needs. The size or composition of the material to be processed determines the type of grinder to be used.
Working of Industrial Shredders:
Advertisement
Industrial shredders operate at a slow speed. The higher torque enables the shredders not to stress the motor much and use up minimal energy. Slower speed and high torque generate enough pressure to pierce through both dry and wet materials.
Shredders cut, grind, hammer, and compress the materials. Some shredders also perform shaking and sorting. Routine monitoring of the equipment is a crucial factor in maintaining its efficiency. It’s critical to make sure there’s enough power and cutting force to reach your final product.
Types of Industrial Shredders Used in Mining
Multiple types of shredders are used in the mining industry. These types are based on their function and application. Following are some types of industrial shredders that are used in mining:
Grinders as Shredders:
Grinders can be high or low speed shredders that use pressure and abrasion to grind materials. Wheels and plates may be used to pulverize matter into granules.
Shredding Through Chippers:
These chip off materials in the form of flakes. Chippers do that with the help of high speed rotating knives. It can be done in single or multiple stages. Materials can be fed either manually or automatically into the chippers.
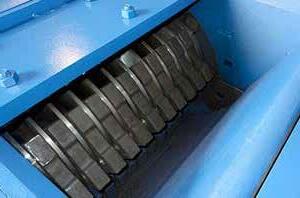
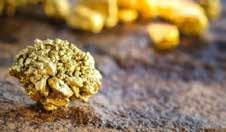
Granulators in Mining:
Granulators are usually used in the mining or fertilizer industry. In mining it is used to recycle the materials extracted.
Hammermills in Mining:
As the name suggests, it uses force to shatter matter in mining. It uses rotating hammers to perform its function. The material, structure, and distribution of hammers control the size of resultant particles.
Shear Shredders:
Shear shredders perform cutting and slicing of materials instead of grinding and crushing. This is done by rotary cutters or specially designed knives. Shear shredders differ in structure and composition depending upon their application.
Special Shredders:
These are manufactured to serve peculiar purposes. Depending upon the terrain or material, specialty shredders can be customized by combining the functionality of any of the above shredders.
All Purpose Shredders:
Large, very minimal speed, hightorque rods with carbide cams or studs, occasionally with hydraulic rams to aid with the intake, make up the machinery. These are majorly used for large scale demolition projects. External systems that remove toxic liquids, gases, or solids, and filter metals from other materials are frequently used in conjunction with them. This functionality comes in very handy, especially in coal mining.
Benefits of Industrial Shredders in Mining:
Industrial shredders have a myriad of applications in the mining industry. These can be used to process materials in the field as well as indoors.
Using industrial shredders in mining has the following benefits: • These consume very little energy as compared to the force they can exert. • These produce high torque to split hard materials. • It decreases human input. Most shredders have an automated feeding mechanism. • These produce increased output as compared to human force. • These can shred diverse terrains and materials during mining. • Shredders have low maintenance costs. • These not only grind and cut materials but are also used to recycle and filter out required objects.
TOMRA Mining delivers sensorbased sorting in extreme conditions at Renison Tin mine in Tasmania
TOMRA Mining provides effective solution for the extreme conditions at the Bluestone Mines Tasmania JV (BMTJV) Renison tin mine in Tasmania, with its XRT sensor-based sorting technology unlocking significant value and delivering environmental benefits.

Bluestone Plant
The Renison mine is 50% owned by Metals X through the Bluestone Mines Tasmania Joint Venture (BMTJV). It is the only major tin project in production in Australia with a mining rate of close to 1Mtpa, although the concentrator is restricted at 750,000tpa. The extreme humidity, with an annual rainfall of over 3,000 mm, and the highly acidic processing water with pH around 4.5, creates unique challenges for the sorting process, the equipment, and waste management, which BMTJV resolved with TOMRA’s help.
A complex flowsheet
The underground mine operates a primary crushing system before the material is transported to the surface through a shaft. Once there, it enters the pre-concentration plant, where it undergoes a 3-stage crushing, screening and cleaning. The particles are split into two fractions – 10 to 25mm and 25 to 60mm – which are fed into two TOMRA X-Ray Transmission (XRT) sorters. The output consists of two streams: the product, which is transferred to the wet plant, and the waste, which is fed into a TOMRA EM sorter to separate acidforming sulphides. In the wet plant, the product goes through primary grinding followed by bulk sulphide flotation.
The tailings are processed downstream to concentrate the cassiterite tin mineral through gravity concentration, gravity tails are further treated via desliming and tin flotation. The combined concentrates are fed to a leaching circuit to remove carbonate minerals, after a final wash stage the concentrate is de-watered and dispatched.
BMTJV approached TOMRA to address two key requirements. The first was the need to upgrade their tin feed to the plant: “The Renison Tin operation wanted to achieve economies of scale, putting more tons through the front end of the plant without upgrading the back end downstream – we wanted to do more with less,” explains Ben Wraith, Principal Project Metallurgist at BMTJV.
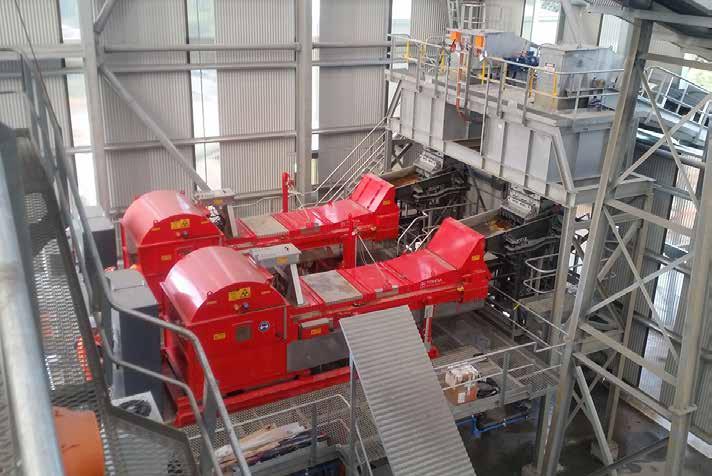
Renison Mine_Ore Sorter
The second requirement was to address the environmental issue of removing acid-forming sulphides from the waste.
Following site visits and extensive discussions with BMTJV’s teams, TOMRA proposed a solution that addressed the tin feed quality with two COM Tertiary XRT 1200 sorters and the waste issue with a COM Tertiary EM 1200 sorter. A team from BMTJV visited the TOMRA Test Center in Sydney, where they observed what the XRT sorter operating at capacity is capable of and experienced first-hand the exceptional accuracy of TOMRA’s XRT sensor. “Our XRT stands out for the high spatial and density resolution and its ability to do contrast sorting, identifying fine high-density tin inclusions in the ore with an accuracy that has no equal on the market,” says Gavin Rech, Technical Manager at TOMRA. “On top of that, it can separate it from the acid-forming sulphides, so that we have the ability of pulling the tin into the first product and sending the rest to the EM sorter.”

Ben Wraith, Ppal Project Metallurgist
TOMRA XRT sorters: the right solution for Renison’s specific conditions
The two COM Tertiary XRT 1200 sorters went into operation in 2018. Initially, BMTJV’s strategy focused on low reject grades, devoting less attention to achieving the mass reject rate and overall process plant throughput. However, the specific conditions at the Renison mine affected the results achieved. The large variance in Run of Mine (ROM) particle size distribution resulted in insufficient stability in the feed to the circuit. In addition, the extremely wet conditions in West Tasmania and consequent high ambient moisture content, combined with the high moisture ore delivered from underground, further affected the sorting process.
In 2019, a new investigation was opened into the ore sorting performance and led to a change of direction: “a paradigm shift away from targeting low reject grades, towards sorting as aggressively as possible, moving from a tin recovery-
based operating strategy to a mass reduction one,” explains Ben Wraith.
“We are getting 20 to 25% mass reduction, so 75 to 80% of the materials are going into the wet plant, and we are still achieving 97 to 98% tin recovery overall across the crushing circuit. Preconcentration didn’t materially impact overall recovery, because the tin in the material that is rejected as waste is extremely fine grained and a proportion is associated with sulphides, so it wouldn’t have been fully recovered in the downstream wet plant and would have been lost to tailings. This approach is best for Bluestone’s application: this configuration gives us the ability to process 15 to 20% more tin units without having to upgrade the downstream concentrator.”
TOMRA’s XRT sorters have proved to be a sound investment that is delivering significant returns: “operating the sorting circuit has slightly increased our overall processing cost, but this is more than offset by the large increase in ROM throughput by 15 to 20%, and thus tin production, so the unit cost per ton of tin produced is reduced by almost 10%,” says Ben Wraith. They have shown to perform consistently, giving BMTJV the confidence in forecasting: “we’ve broken multiple production records in the last year in tin units, and this gives us confidence in what we can achieve, because the machine performs over and over again if you treat it right and if you prepare your feed correctly.”
TOMRA XRT success leads to upgrade decision
In view of the results achieved with the two TOMRA XRT sorters, BMTJV decided to upgrade the ore sorting circuit with two new, recently launched XRT models with stainless steel internal parts, and advanced features such as the TOMRA ACT user interface and the TOMRA Insight cloud-based platform: “the decision to buy new machines was easy,” says Ben Wraith. “The stainless steel will assist prolonging the TOMRA sorter’s life by protecting the unit from our high-moisture and corrosive environment. The more ergonomic design will help our maintenance teams, which is particularly important for machinery operating in these harsh conditions.” Ben Wraith is particularly looking forward to TOMRA Insight: “It will enhance everybody’s understanding and experience of the machines. It will be more of an analytical platform for our metallurgy and maintenance staff, providing ample opportunity to gain valuable information that can be analyzed and optimized over time. The one feature I am personally interested in the particle size monitoring through the machines, which will enhance our overall circuit performance, because we have an integrated circuit with the crushing and screening plant. Feed preparation is key to maintain a consistent performance – knowing how well you’re preparing your feed in a live fashion can only end up with a better result.”
TOMRA will also be able to log into the machine and check the daily reports generated by TOMRA Insight, so that their technical teams will be well prepared ahead of site visits for maintenance or optimization.
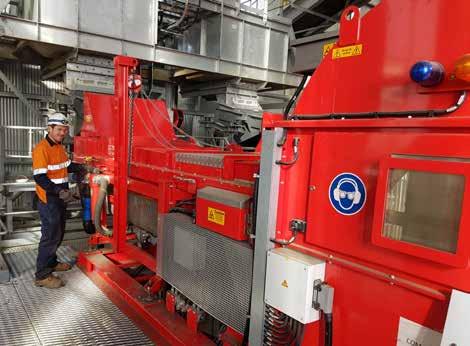
TOMRA-Bluestone
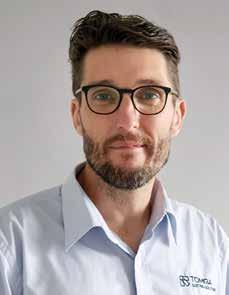
Gavin Rech, Technical Manager at TOMRA
A close collaboration to achieve the best results
Throughout the process, BMTJV worked closely with TOMRA. “TOMRA has been working with the site maintenance team to tailor solutions to our operating environment, which has been invaluable,” says Ben Wraith “TOMRA supported me through site visits, which included equipment inspections, sitebased training of our personnel, and an openness to continually improving the technology and fine tune it to our sitespecific requirements. They assisted the site with troubleshooting, optimization, discussing the nuts and bolts of the issues as they arose and finding a solution that works.”
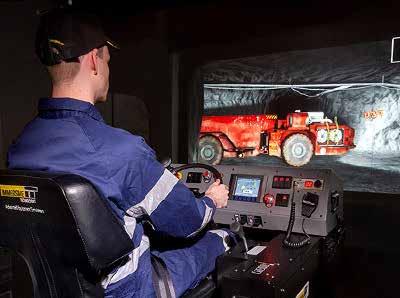
Workforce Training Solutions for Underground Mining in Greece
Hellas Gold S.A. is the first mining company to deploy simulationbased training from Immersive Technologies in Greece, marking the 47th country where Immersive Technologies’ workforce training systems are deployed. Immersive Technologies is known for providing rapid return on investment with a proven formula that combines “People + Process + Technology”.
Olympias mine, located in the Halkidiki Peninsula in northern Greece, an underground mine of gold, silver, lead and zinc, has been modernizing under the management of Eldorado Gold and its subsidiary, Hellas Gold S.A. This strategy and adoption of new technologies improved production rates and efficiency during 2021. The implementation of Two Immersive Technologies’ IM360-B Advanced Equipment Simulators and blended learning products will improve operator performance and safety and enhance workforce development strategies.
In an effort to develop a highly skilled and dedicated workforce for the underground operation, the company has purchased simulator Conversion Kits for Sandvik Underground Loader (LHD), Underground Truck, Drill and Bolter. In addition, Professional Services from Immersive Technologies are in place to support the implementation of simulation products.
“It is an exciting time for mining in Greece. We are proud to support this region in delivering the safest and most experienced operators, resulting in a highly productive mine site,” says Johan Stemmet, Regional Vice President – EMEA & CIS at Immersive Technologies. We continue to support All Makes All Models with new Conversion Kits® and Learning System developments for OEMs such as Caterpillar, Hitachi, Komatsu, Liebherr, Scania, Sandvik, P&H and others.

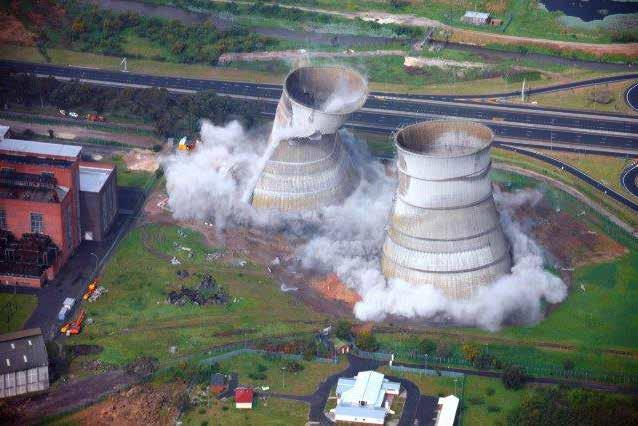
Turnkey solutions for power plant demolition
From the safe and controlled demolition of coal-fired boilers to product conveyors, steam turbines, transformers, silos, cooling towers and associated auxiliary equipment, and the removal of hazardous materials, Jet Demolition has extensive experience in power plant demolition and decontamination. “We offer our clients solutions that are economical, rapid, and risk-averse,” comments Junior Project Engineer Nontobeko Zwane.
Such projects often involve the removal of critically compromised structural steel structures and elements, recovery of undamaged client assets, and demolition of plant buildings and offices. Jet Demolition also conducts cleanup operations that reduce hazardous contaminant levels on the demolished elements to recycle and reuse materials.
The timeframe of such scope of work relates to the project and client requirements. Demolition projects are highly mechanised to ensure the safety of personnel and other persons. The live services that might be compromised within the demolition works area and the associated structural elements that must remain undamaged. “This is where our proven experience in large-scale and technically-challenging projects speaks on our behalf,” highlights Zwane.

From mining facilities to the automotive, chemical, and pharmaceutical, petrochemical, power generation, and steel and glass industries, Jet Demolition has both the expertise and equipment to undertake complex heavy industrial demolition projects. “We provide turnkey value-add solutions to our clients that are not readily provided by any other service provider,” concludes Jet Demolition Director Joe Brinkmann.
main equipment used depends on the site conditions. This ranges from a onetonne skidsteer loader to a 102-tonne high-reach excavator, paired with the ideal demolition shear, grapple, hammer or bucket as required.
The main challenges posed by these type of demolition projects is accommodating
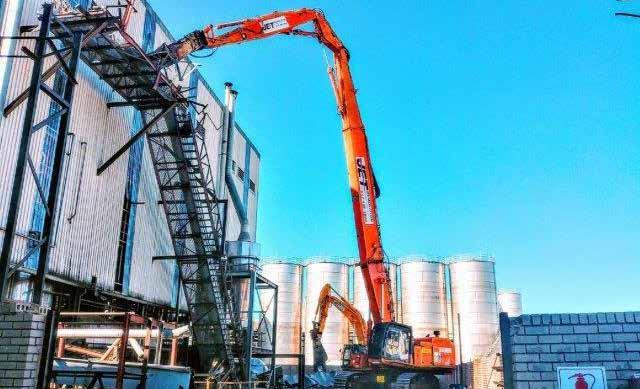

Tire Perfomance Tech
DRIVE, LOAD, MOVE MORE and MOVE FURTHER

At Arsenal Tire Solutions we help our clients in the mining (underground and open pit), transportation, and construction to load more, move more, and move further with less tires. We do this with our Arsenal Cost-Effective Tires, the Tire Sensors by Telemetry , and Arsenal Liquid Powder guaranteeing a reduction in the cost of operation.
MINING. For the mining area, we offer a wide range of patterns for equipment with load capacities from 30 to 400+ metric.
TRANSPORTATION. On the transportation area, we handle tires with real high load capacity in addition to having extraordinary performance in the road, off-road, and mining hauling operations.
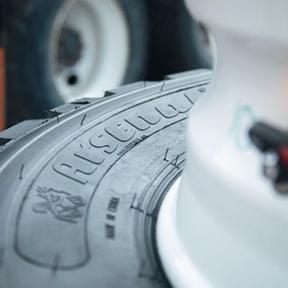
ARSENAL TIRES. Arsenal designs, imports and distributes affordable premium tires under our own brand with an extraordinary competitive quality in areas of underground transportation, construction, and mining sectors with the vision of reducing their total ownership tire cost for our customers.
TELEMETRY TIRE SENSORS. In addition, we have the most advanced fleet solution of telematic & real-time tire sensors where you will be able to monitor, from the operator's cabin as well as the office, the pressure, and temperature. This generates an organizational culture change and gives the power to maintain the right pressures at your convenience and increase mobile vehicle's uptime.
Benefits -More income -More productivity -More Security -More Safety -Less rip-offs -Less dead times -Less premature deaths
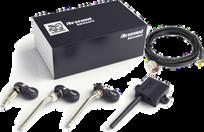
MINING TIMBER (Pty) Ltd
OUR SERVICES
We maintain a consistent and reliable supply of mine support elements to the mines. We do this through having control over all the inputs which makes this possible. Our steel products are manufactured by NHR Manufacturing at our factory in Ga-Rankuwa at the highest quality standard. Our timber products are overseen from plantation, harvesting ,sawmill and transport of the end product to the mines.
At the mines we can provide mine yard management including stock control. We supervise the logistics of the mine support products from surface to underground. This ensures that mines never lose blasts due to a shortage of the support materials that we supply
Our after sales service includes support installation training underground and support effectiveness monitoring. A daily report is generated by each instructor which is circulated to the relevant officials for information and comment.
- Pre-stress pots (with or without hooks) - Chocks, slabs, trims, squares
Research and Development forms part of our strategy. We are committed to continuously improve mine support products and systems striving to improve safety, costs, and productivity.
To summarise:
Ÿ Ÿ Ÿ Ÿ Ÿ Ÿ Mine Yard Management Support Installation Training Support Installation Effectiveness Monitoring and Data reporting Rock Engineering Services Research and Development Quality Assurance and Regular Testing of our products at accredited testing facilities
OUR PRODUCTS
STEEL
- Pre-stress Pack plates - Cluster plates
- Pre-stress pump and hose assembly - Headboards complete with pre-stress units - Split sets – mild steel, galvanised or 3CR12 - Temporary support – Seiza Jacks
TIMBER
- Mats: Solid, end-grain, space etc. - Pencil props, engineered props etc.
- Dunnage, laggings - Gumplanks, Gate stalls, wedges - Hardwood sleepers - Charging sticks
OUR TEAM
Ÿ Raymond Botha – Chief Executive Officer -082 045 2095 Ÿ Correll Kritzinger – Administration – 083 235 5997 Ÿ Eric Scholtz – Rock Engineering - 083 455 9651 Ÿ Tony Davidson – Sales – 072 785 3669 Ÿ Shaun McConnachie – Sales – 082 553 4228 Ÿ Kgomotso Mfulwane – Sales - 082 055 8125
MINING TIMBER (Pty) Ltd
Combi - Plates
Headboard Spiral resin Bolt
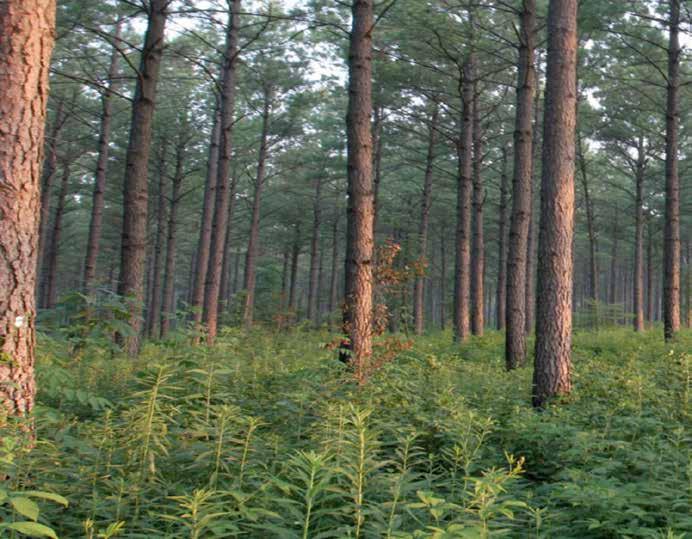
Back Anchor Split Set Sieza Jack Expansion Friction Bolts
Pre-Stressed Pack Plate
Safety Net
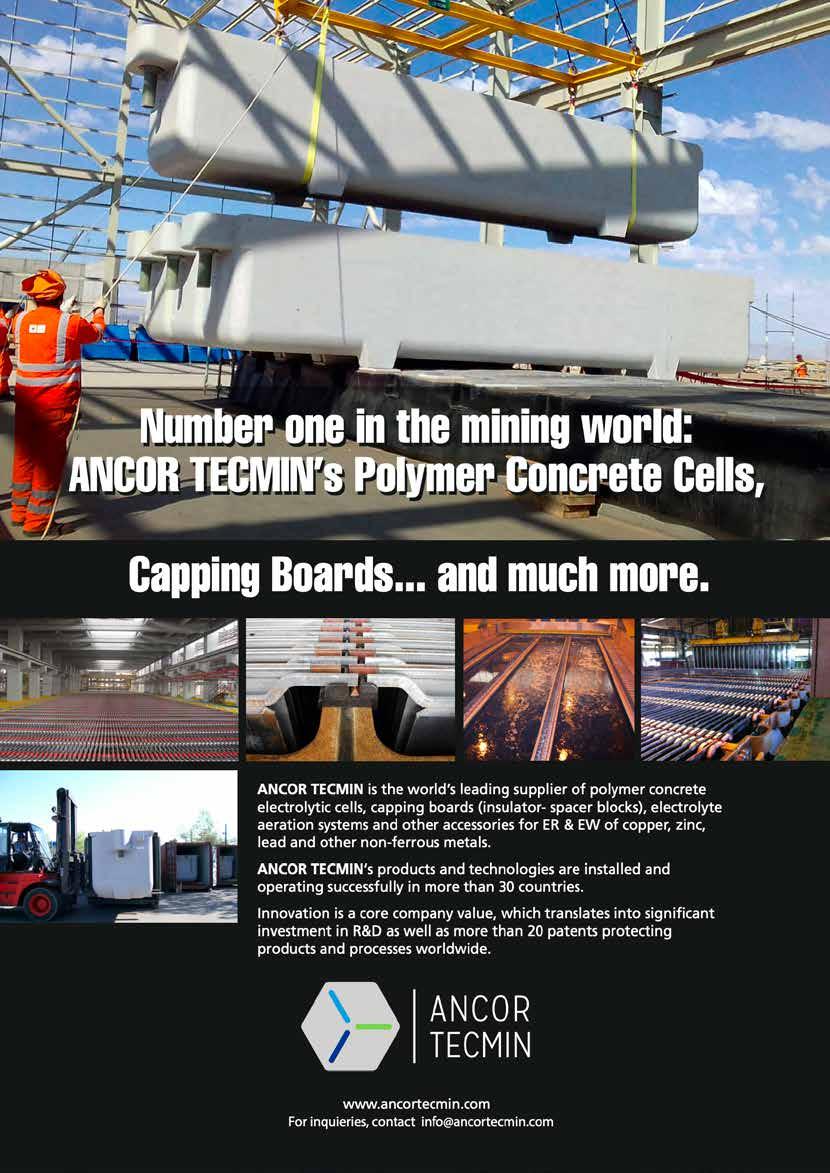