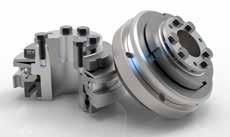
25 minute read
Congo government seeks audit of mining registry
“The government of Democratic Republic of Congo (DRC) has ordered the country’s mining registry to be audited. President Felix Tshisekedi gave the orders and issued a ban on issuing and trading mining permit until the process is done, a measure aimed at combating fraud within the sector.
Tshisekedi told ministers he wanted to end the squandering of mining assets by unnamed political actors and officials involved in the administration of the mining register, which records mining concessions.
Advertisement
“This recommended cleanup will increase the contribution of the mining sector to the state’s budget and help, as a priority, the people benefit from the mineral wealth of our country,” Tshisekedi told ministers.
The move is an escalation of Tshisekedi’s ongoing review of deals struck by his predecessor Joseph Kabila, which includes a US $6bn “infrastructure-forminerals” deal with Chinese investors. The DRC is the world’s top producer of cobalt and Africa’s biggest copper producer, but more than 70% of its roughly 100-million people live on less than $1.90 per day, according to the World Bank.
Transparency activists have estimated the DRC has lost out on billions of dollars of revenue from mining deals over the past two decades. Tshisekedi gained the presidency through a powersharing settlement with Kabila, following the disputed 2018 election, but he has gradually taken almost all the levers of government, political analysts say, and been increasingly outspoken about Kabila’s mining deals.
Mining companies who fail to comply with their administrative and social obligations should have their licences revoked, Tshisekedi told mines minister Antoinette N’Samba. He asked N’Samba to identify mining companies where the state had not gained 10% of shares when the permit flipped from exploration to exploitation, as required by the mining code.
Meanwhile, gunmen killed a policeman and kidnapped five Chinese nationals near a mine in southeast DRC overnight. It was not clear who carried out the attack near the village of Mukera in South Kivu province.
Papua New Guinea mining industry eyed by Jaxin Group
The government of Guinea inked a memorandum of understanding with Jaxin Group to expedite the process of identifying the opportunities and move into making investment decision over the Papua New Guinea mining industry. Mining Minister Johnson Tuke said the memorandum of understanding was witnessed by representatives of China Energy, in Port Moresby. “We are creating an understanding so that we can invite this company to conduct business in the mining sector, so as in the oil and petroleum sector because they have a known history back in their country. We’ve got a process at the Mineral Resources Authority (MRA).
This doesn’t mean we’ll give them first preference or priority. They have to fully comply with processes down at MRA, meaning they have to take part in the application processes,” Tuke said.
Jaxin PNG chairman Kennedy Penial said the company had the financial capacity and human resources to invest in PNG. Simons Energy, an upstream oil and gas subsidiary of Jaxin, is 51% owned by China Offshore Point Corporation. “Since Prime Minister (James Marape) opened up to bring in investors from China through the Embassy of China in PNG, they (Jaxin) are the first ones who have taken up the initiative. Our interest is more in the mining and petroleum sector,” Penial said.
Initial investment anticipated in this arrangement is about US$10 billion (K34 billion) in the first three years, and a further US$30 billion (K103 billion) thereafter.
Compact overload limiter
The safety coupling of the SKY series for indirect drives from JAKOB Antriebstechnik is designed as overload limiter or collision protection for the most modern requirements. With a compact design, it can still offer high release torques of up to 9000 Nm. The conical clamping bushing enables simple assembly, large shaft or bore diameters, the high possible bearing load and the excellent concentricity round off the safety coupling. By using high-strength quenched and tempered steel with surface hardening or plasma coating of the relevant functional surfaces, particularly high release torques could be achieved. It is also available in a rustproof version on request.
Jan Möller Marketing
JAKOB Antriebstechnik GmbH
Daimler Ring 42 D - 63839 Kleinwallstadt Tel. : +49 (0) 6022 12208-55 e-mail: moeller@jakobantriebstechnik.de www.jakobantriebstechnik.de Registergericht Aschaffenburg HRB 797 Geschäftsführer: Ludwig Jakob
WORLD CLASS LAY-FLAT HOSES
SUPERMAN HVT
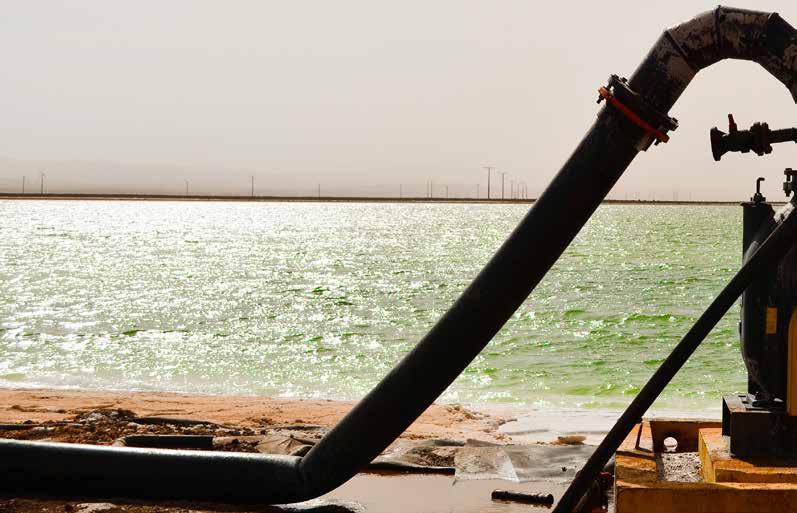
Mandals lay-flat hoses are an important part of an optimal water management system. Effective mine de-watering and slope depressurization systems are important components of many surface and underground mining operations.
In high flow and deep well de-watering systems for mines, layflat hoses are used to deliver or remove the many thousand gallons of water needed per minute. In mines where pit slope depressurization is essential to maintain stable slopes, lay-flat hoses offer ease of handling, deployment and retrieval. And if the mining operation is to be taken to a deeper level, bore hoses are used to remove ground water.
SUPERMAN HVT
MANTEX HP WELLMAN

Designed for long life and maintenance-free service in the harshest environments. This world class leading hose is tough and durable with exceptional resistance to abrasion and cutting.
World class lay-flat hose designed for compressed air at high working pressures, while still offering a light-weight solution easy to deploy and store Lay-flat hoses are ideal for rapid large volume de-watering due to less pressure drop over large distances. Not to forget the rapid and flexible deployment compared to other types of rigid hoses or steel pipes.
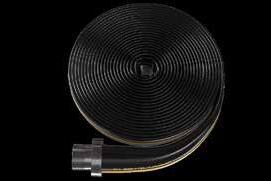
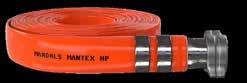
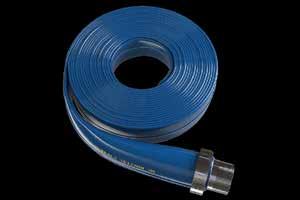
Mine de-watering takes place in the harshest of environments. This requires extremely abrasion resistant hoses to withstand being deployed down steep, rocky mountain sides, lowered into deep wells and to carry the weight of a full set of submersible pumping equipment.
www.mandals.com/industries/mining
Flexible rising main
Wellman 300 flexible rising main is designed as a permanent alternative to traditional materials such as steel, fibreglass, PVC and polyethylene in water wells with electric submersible pumps.
WE ARE LOOKING FOR NEW DISTRIBUTORS JOIN OUR TEAM
Mandals (a Michelin Group company) is a world leading manufacturer of premium lay-flat hoses. With over 245 years of experience in production and distribution of lay-flat hoses, you can trust us as your next business partner. Mandals has become a well-known brand though our worldwide sales and distribution strategy. We are looking for new partners in various industries, such as agriculture/irrigation, oil and gas, mining and portable water. We are always open to explore new industries as well.
NSK Self-Lube® bearings prove reliable in harsh conditions
NSK Self-Lube® bearing units with triple lip seal and end cap protectors provide an extended service life in harsh operating conditions, such as those prevalent within the quarrying, mining and construction sectors. This proven performance is vital in these industries, where contaminants can easily penetrate poorly specified bearings, bringing machinery and equipment to a halt.
Downtime is the enemy of quarry/ mine operators and construction project managers. Critical plant and equipment must offer reliable performance to meet demanding output targets, project deadlines and budgets. Whether extraction, transportation, preparation, separation or enrichment, these processes are subject to contamination and debris, not to mention heavy loads, shock loads and vibration.
Bearing selection is vital to ensure long service life. Getting it right means that mining and construction sites can maximise their uptime and productivity while simultaneously reducing maintenance costs. Leveraging stateof-the-art design, material, lubricant and seals, NSK Self-Lube® bearings exceed the life of conventional bearings. Furthermore, by selecting Self-Lube® bearings with triple lip seal and shaft end protectors, it is possible to reduce the costs associated with downtime and repairs.
Reliable protection
NSK recommends its specially developed triple-lip seal for applications with a high degree of contamination. Bonded to a protective outer steel pressing (secured in the outer ring), this one-piece moulded nitrile seal with three lips makes for a highly efficient sealing design that protects the bearing in severe operating environments.
Standard Self-Lube® bearing inserts also have a locating groove to allow the easy fitting of an optional end cap protector. The cap helps to protect personnel from rotating components and the bearing from external contamination. NSK SelfLube® bearing units comprise a broad portfolio of reliable inserts and housings. Notably, these cost-effective solutions provide a fast and straightforward solution for mounting bearings without the need for complex housings or special shaft arrangements.
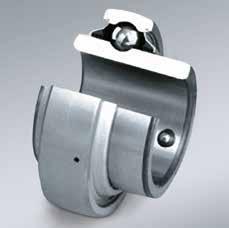
Self-Lube® bearing units with triple-lip sealed inserts are ideal for applications where bearings face exposure to dust and water contamination
Reduce costs
The combination of easy use, selflubrication and long service life mean that increasing numbers of companies in the quarrying, mining and construction sectors are now reducing PR Ref. B192021-N | 1/4 their costs for replacement bearings, maintenance and downtime.
A case in point involves a company that was experiencing frequent reliability problems with the bearing units assembled in a vibrating drum. These bearings work in severe environments, where they suffer exposure to sand that often wholly covers the units. In addition, due to the nature of the application and its difficult access, the regularity and increasing cost of maintenance was proving an issue.
Following a comprehensive failed bearing analysis as part of its AIP Added Value Programme, NSK proposed Self-Lube® bearing units with triple lip seals, which increased the operating life by a factor of 10 against the previous solution. In addition, the three highintegrity nitrile seal lips with lubrication traps have provided an effective way of stopping the ingress of contaminants.
Design innovation
In another customer success story, a company supplying ready-mixed concrete and other construction materials invited NSK to perform an application review of its augur screw pump bearings. The augur pumps transfer ash (an abrasive mixture of ash, sand, glass, fibres and metal grit) into waiting containers. Here, the screws lift the ash at an angle of approximately 40°, where the lower bearing units frequently fail.
Upon examination of the failed bearings, NSK was able to identify several issues. For instance, after removing the flinger seal, it was evident that no contact seal was running against the inner ring of the bearing. It had likely worn away, and there was now a direct contamination path into the bearing. Further problems included heavy cage corrosion and the absence of lubrication. The ingress of fine dust and particulates had probably soaked up any grease and created a grinding paste, eroding the rubber seal.
To rectify the situation, NSK again recommended its Self-Lube® bearing units. In this case, NSK also suggested the inclusion of a small disc plate with an additional seal. This minor redesign would help stop most of the contamination and significantly reduce pressure on the bearing seal as it features a path for the debris to escape. By further improving the sealing, using the triple lip sealing solution on the Self-Lube® insert bearing, it is likely that reliability will significantly improve. In addition, the use of an end cap protector for the bottom bearing could also benefit the company as it will help reduce any dust ingress.
These examples are just two of many successes that NSK is encountering in quarrying, mining and construction applications.
Metso Outotec launches innovative Concorde Cell flotation technology for fine and ultra-fine particle recover
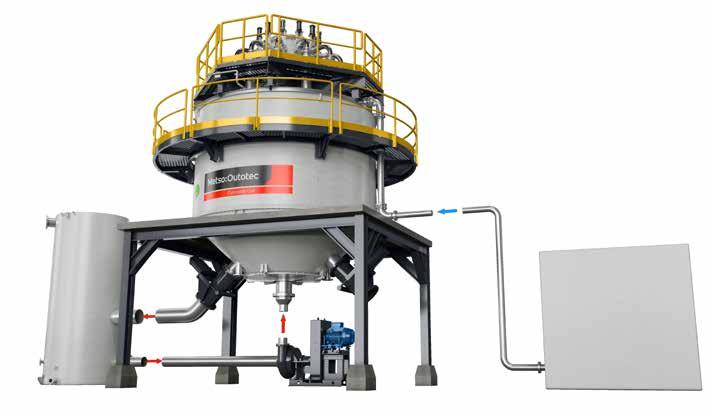
Metso Outotec is launching groundbreaking Concorde Cell™ flotation technology for efficient fine and ultra-fine particle recovery. This innovative Planet Positive technology sets a new benchmark in high-intensity pneumatic flotation, reducing plant operation costs and contributing to sustainability of operations through minimized energy and water consumption per tons of metal produced.
The patented Metso Outotec Concorde Cell™ technology is the first fine and ultra-fine flotation solution for more finely disseminated and complex orebodies that have previously been inaccessible.
“The need to process more finely disseminated and complex ore grades, as well as the declining ore grades and the demand for improved flotation selectivity, all bring new challenges to minerals processing flowsheets. The new Concorde Cell™ technology helps flotation circuits overcome these challenges and recover the previously unachievable ore value,” says Antti Rinne, Vice President, Flotation at Metso Outotec.
The Concorde Cell™ forced-air Blast Tubes treat 100% of fresh feed combined with tailings recycling for improved performance, allowing finer grinding to get extra liberation without the risk of valuable particles lost into tailings.
“Combining the well-proven TankCell® technology with Concorde Cells is a low-risk and high-benefit approach for minerals processing flowsheets. The cell produces very high shear and extremely fine bubbles, which increases recovery in particles under 20 microns,” explains Rinne. Benefits of the Concorde Cell™ flotation technology: • Superior recovery of fine and ultrafine particles • Very high shear environment with increased bubble surface area flux for faster flotation kinetics • Optimized froth recovery and improved selectivity • Forced air allowing wider process control and stability for further flotation optimization
The offering also includes Blast Tube retrofit kits for upgrading the metallurgical performance of self-aspirated pneumatic flotation cells to the Concorde Cell™ technology. In addition, Metso Outotec can provide a complete slurry handling package for the Concorde Cell, including pumps, spare parts, as well as optimization and maintenance services.
USIM PAC, the most well-known mineral processing simulation software, is 35 years old
CASPEO, worldwide provider of process engineering software and consulting services to metals, minerals and mining industries, celebrates the 35th anniversary of its USIM PAC software.
1986 was the year of the Chernobyl nuclear accident… It was also the year BRGM, French national geological survey launched USIM PAC, a powerful process modelling and simulation software dedicated to the design, the monitoring and the optimization of mineral processing and metallurgical plants.
A pioneering software with an already mine-to-mill approach
It’s hard to believe that 35 years ago, BRGM introduced one of the cuttingedge process simulator. Ahead of their time, the experts from the BRGM team –among them Alain Broussaud, Guy Fourniguet, Jean-Claude Guillaneau, Jacques Villeneuve and the CASPEO managing directors Marie-Véronique Durance and Stéphane Brochot– had already understood that they needed to provide an integrated software that would allow mining companies to optimize the whole mining value chain from ores to metal, also called the mine-tomill approach. An approach recently adopted by other software publishers offering a new way of modelling: back to the future?
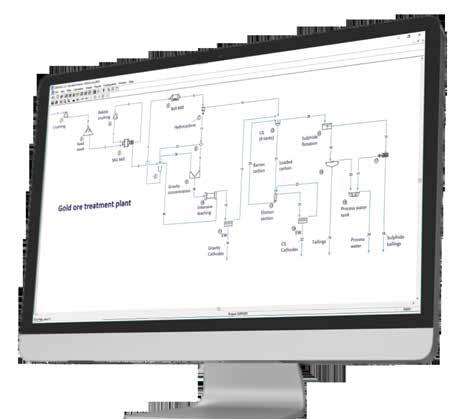
From the beginning, USIM PAC have been specifically developed to meet these requirements allowing engineers to design and optimize each part of a process as well as the overall circuit (and recirculation). In a single interface, USIM PAC performs simulation, data reconciliation, mass balancing, flowsheeting, equipment sizing and sensitivity analysis. “USIM PAC is the only on-premise simulator on the market able to model the entire mineral processing value chain: from crushing to refining, passing through grinding, magnetic and gravity separation, flotation, leaching and concentration. All the models are connected within a single platform. It was, at the time, a real innovation” says Stéphane Brochot.
Separation and physical, chemical or biological transformation: all these kind of processes are simulated in USIM PAC. A library of more than 150 models of unit operations is integrated in the standard tool: extraction, comminution (grinding, crushing…), size classification, concentration (flotation, magnetic and gravity separation…), solid/liquid separation (filtration, decantation…), and hydrometallurgy. USIM PAC offers the possibility to engineers to add their own equipment models.
Modelling the mineral diversity: a challenge for ore processing simulation Another originality of USIM PAC process simulation and optimization software: the possibility to take into account detailed and configurable material description, especially for the mineral phase.
Mineral processing is characterised by the wide variety of raw materials. This diversity appears through the mineralogical and chemical constitution of the ore or through the variability of its properties (mechanical, chemical or physical properties). Consequently, it involves a great diversity in the processes and in the unit operations making ore processing simulation a real challenge.
From the beginning, USIM PAC offers a new approach of modelling to better understand the response of the plant when various variables change at the same time (ore or operation) and automatically test numerous operational strategies. It does not require the use of thermodynamic databases unlike other generic chemical process simulators on the market. The process simulator allows the description of any type of ore with almost no limit in the level of details and associated physical properties that can be met in the mining industry. A feature particularly interesting
in the field of geometallurgy to forecast ores (recovery rates, grades…).
Extract valuable minerals more economically… and with less environmental impact
Processing, refining, recycling… In the 2000s, the development of USIM PAC has been focused on helping mining companies to reduce their environmental impact.
Thus, a multi-criterion design approach has been developed. It includes economic criteria such as capital cost, reagent and power consumption, production quality in terms of valuable mineral grade or undesirable elements level; technical aspects with the evaluation of various configurations and processing technologies, a complete and detailed description of all material streams and their behaviour during process and, environmental factors such as water consumption and recycling, pollutant production or waste treatment. It is also in 2004 that Marie-Véronique Durance and Stéphane Brochot, members of the BRGM mineral processing team (“Département Minéralurgie”), created CASPEO to take over the development and the marketing of USIM PAC as well as BILCO, a data reconciliation by mass balancing software and ECHANT, a sampling error calculator solution.
The path forward
Today, USIM PAC is a decision-making tool that supports industrial R&D departments, technical centres and engineering offices all over the world.
Among mineral process modelling and optimization software, USIM PAC is one of the most well-known application. It helps to better understand and analyse complex processes such as minimizing investment costs, optimizing plant production performance (yield, product quality, etc.) and improving energy efficiency. According to Marie-Véronique Durance, CASPEO Co-Managing Director: “Over the last decade, more than 300 customers spanning 55 countries have leveraged USIM PAC software. Among them the world’s top leading mining companies such as AngloAmerican, Arcelor Mittal, Eramet, Glencore, Vale, etc.”
What’s next? CASPEO team is working to integrate in USIM PAC new models already developed: dissolved air flotation, ion exchange resin, reverse osmosis, to name but a few allowing to manage water quality. Project development will also be based on new services with the launch of self-paced online training courses covering process simulation and metallurgical accounting in 2022. The goal: help the current mineral processing engineers and the next generation to gain skills on these complex areas that bring a lot to mining companies if (well) used. A redesign of the interface is also planned in the middle term.
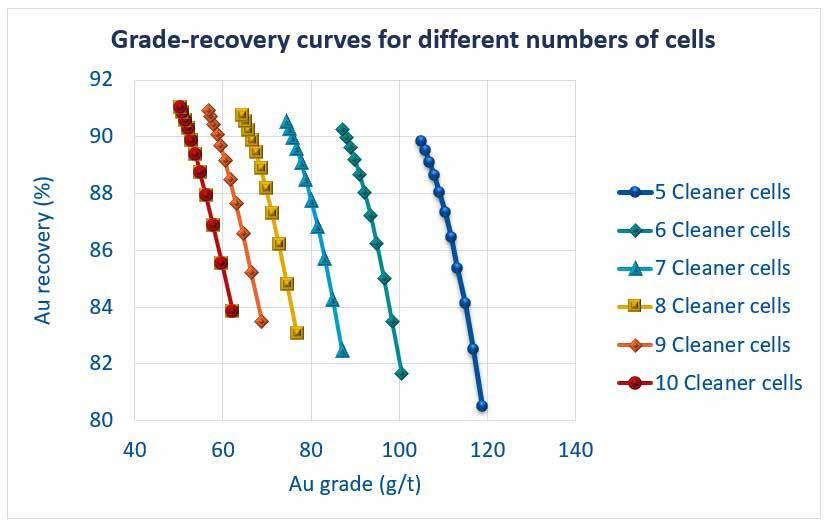
TOMRA Mining holds second successful seminar on sensorbased sorting in Toronto
Experienced industry leaders joined TOMRA Mining’s experts as guest speakers in a seminar designed to provide a solid, pragmatic grounding on sensor-based sorting. The event highlighted the important role of sensor-based sorting technologies in green mining and their potential to unlock significant value in mining projects, as well as the possibilities of digitalization for supporting customers and managing connected equipment.

TOMRA Mining’s seminar on sustainable mining solutions through sensor-based sorting covered a wide range of topics, starting with an introduction to the various sorting technologies, and including different applications, test work, design and economic considerations. Every topic was backed up with practical examples from case studies of ore sorting projects. The presentations gave rise to interesting discussions about the state of the art of sensor-based sorting in mining today and its potential for the future as the industry transitions to green mining.
The seminar highlighted the value of considering these technologies in the first phases of preliminary feasibility. Jordan Rutledge, Area Sales Manager at TOMRA explains: “sensor-based sorting should be considered in the flowsheet from the beginning and evaluated in prefeasibility studies to see if it is suitable for the project and will add value to the plant. In many cases sorting works really well and, as we continue to go towards a green economy, the use of our resources is vitally important. In order to make the best use of them, sorting plays a critical role.”
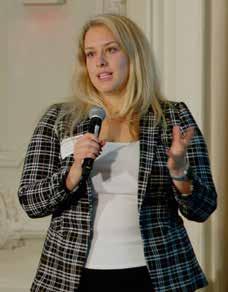
The seminar attracted around 40 participants from across Canada. They included representatives from operator mining companies such as Agnico Eagle, Capstone Mining and Cheetah
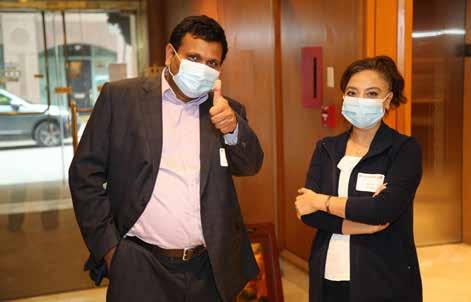
Resources; from laboratories such as testing and certification company SGS and the Saskatchewan Research Council (SRC); from engineering companies such as DRA Global, Primero, CIMA and Halyard; as well as students from the University of Toronto.
This was the first live event in almost two years for many of the participants, who appreciated the opportunity to meet face to face with their peers, as Justin Taylor, President and CEO of Halyard Inc. expressed very well: “I think live events offer a much deeper look and a different dimension into how people can communicate and connect. Part of the experience is learning about things and the other half is interacting with people, building networks and relationships.” us to seek out new solutions and to collaborate, and use the technology in the best way possible.”
Justin Taylor concluded: “Most importantly, I think that the seminar put forward a whole lot of concepts or topics that aren’t usually discussed. Sorting has always been a buzzword, but it’s been spoken about in non-defined terms in previous conferences, and I think this was really focused on the type of technology that TOMRA puts forward. TOMRA being a world leader in this type of technology certainly makes it clear to people what can be done, and I think there is a lot if scope for people to understand what can be done with sensor-based sorting to optimize their sites.”
The breadth and variety of topics covered by the speakers was a key element in the seminar’s success: “It was a good mix of speakers and topics that range from academia to on-site real case studies that were very well presented. The speakers were very knowledgeable and very easy to listen to. The seminar allowed me to gain more understanding of the basics behind the technology, the different applications, in a variety of different parts of the industry,” said Sean Kautzman, Principal Consultant at SRK Consulting.
“It’s good to get all the different perspectives,” added Ryan Cunningham, Process Engineering Director at CIMA+ “We’ve had the innovators, the laboratories, the implementers, different engineering firms. It encourages
The program: a fact-based exploration of sensor-based sorting technology in mining
The wide-ranging program of the seminar benefited from the expertise of TOMRA’s specialists and the intervention of highly qualified guest speakers who gave interesting insights:
Introduction to sensor-based sorting and current technology
• Ines Hartwig, Jordan Rutledge,
Harold Cline – TOMRA Mining • Case study: X-Ray sorting chrome ore – a dry processing alternative to DMS • Helga van Lochem, Gavin
Rech – TOMRA Mining • Introducing final diamond recovery • Harold Cline – TOMRA Mining • Sensor-based ore sorting –
Mining Consortium perspectives • Gillian Holcroft – GLH Strategic
• Victories and lessons learned
at Ma’aden: the largest sensorbased sorting project in the world • Jordan Rutledge – TOMRA Mining
• Setting objectives for
sorting projects: financial and technical aspects • Ryan Cunningham – CIMA+,
Jordan Zampini – DRA
Global, Lina Du – Primero • CanMicro: microwave-assisted comminution and sorting • Erin Bobicki – University of Alberta • Ore characterization for sorting • Jane Danoczi – Saskatchewan
Research Council • Implementing a mobile sorting installation • Justin Taylor – Halyard Inc. • Integration opportunities for particle sorting and bulk sorting • Robert McCarthy –
SRK Consulting • Challenges and opportunities with greenfield ore sorting projects • Marie-Claude Hallé –
PGNAA & Minerals • Case study: Dalradian gold project • Jörn Rohleder – Metso:Outotec • Case study: sensor-based sorting ups ESG/CSR and lowers costs at Nechalacho Rare Earth Mine • David Connelly –
Cheetah Resources
• The future of sensorbased sorting
• Ines Hartwig – TOMRA Mining
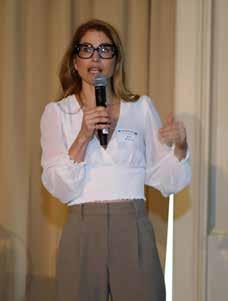
Reap all the benefits of on-site oxygen production with Atlas Copco’s efficient OGP+ oxygen generators
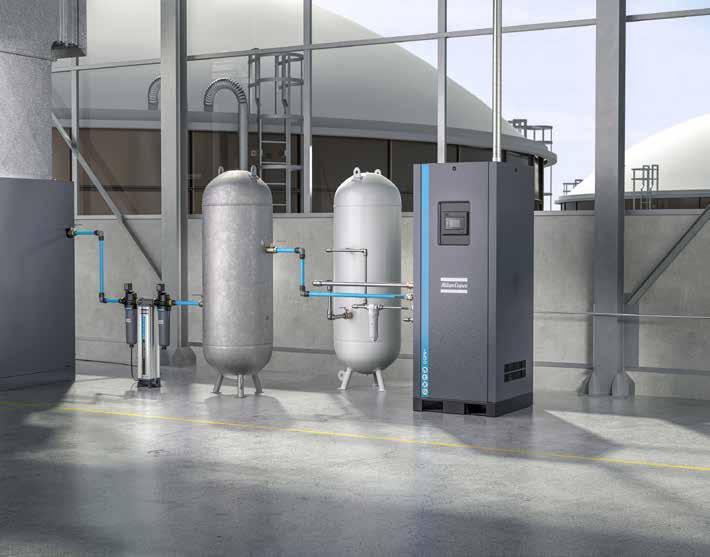
Atlas Copco proudly unveils its latest range of cutting-edge OGP+ Oxygen Generators that seamlessly, efficiently, reliably and cost-effectively produces oxygen (O2) on-site, requiring only a supply of dry compressed air. These environmentallyfriendly machines deliver significant across-the-board savings through lower total cost per cubic meter of oxygen, optimised uptime due to continuous oxygen supply and the delivery of guaranteed gas purity. Oxygen is a critical gas for a vast number of industries including waste water treatment, food & beverage, pulp & paper, steel, medical, pharmaceutical, bioenergy, metallurgical, glass and aquaculture. Oxygen has multiple uses within diverse applications: Oxygen is added to a process for better control of heating patterns, for higher furnace efficiencies (for lower fuel consumption) and for the reduction of particulate and NOx emissions. It can also be used with fuel gases to enhance processes such as gas welding, gas cutting, oxygen scarfing, flame cleaning, flame hardening and flame straightening. Moreover, oxygen is a raw material in many oxidation processes and it is also used to regenerate catalysts.
The on-site production or generation of oxygen as opposed to purchasing this gas from a vendor presents a highly cost-effective, safe, space-saving and convenient solution. Owing to groundbreaking engineering, Atlas Copco’s
new OGP+ 3-30 PSA (Pressure Swing Adsorption) machines deliver best-inclass oxygen generation performance and efficiency. These generators ensure continuous reliable on-site oxygen generation at a significantly lower total cost per unit of oxygen. Furthermore, with the touch of a button, the user is able to choose the correct oxygen purity level for the application.
“With our OGP+ Oxygen Generators, professional oxygen users can become oxygen producers,” states Zandra van der Westhuizen, Business Line Manager at Atlas Copco Compressor Technique. “To switch from sourcing the gas from a vendor to producing oxygen on-site is easy. All that is required is a compressed air system plus a gas generator and the plug-and-play machine is ready to produce oxygen on-site.”
Van der Westhuizen draws attention to the countless benefits that can be gained from on-site oxygen production. “Our Atlas Copco OGP+ generators are 30% more efficient at full load compared to a traditional generator. Moreover, thanks to the machines’ innovative Variable Cycle Saver technology, the OGP+ generators offer up to 70% in additional energy savings when oxygen demand is low. This all adds up to a lower cost per cubic meter of oxygen, delivering unparalleled cost savings.”
Generating oxygen in-house also ensures a dependable and continuous supply source, thus mitigating potential stoppages due to stock shortages. “Reliance on a third-party supplier is eliminated,” adds Van der Westhuizen. “The user is in complete control, generating the exact amount of oxygen when needed at the correct and guaranteed purity required for the particular application. If more oxygen is required, simply run the generator a little longer. Bottom line - users only pay for the gas they need and use.”
Coming back to the topic of purity, Van der Westhuizen points out that the purity of purchased oxygen is usually over-specified for most application requirements. “An on-site generator not only achieves this high purity more costefficiently, but it also offers additional savings. Because generating oxygen of the highest purity uses more energy, the ability of on-site generators to set the correct purity for a particular application will significantly reduce the user’s operational costs.”
Yet another advantage offered by onsite oxygen production is that there is no need for a facility to store oxygen cylinders or to install a large liquid oxygen tank. Owing to an intelligent design, aluminium extrusions and bestin-class usage of zeolite molecular sieve (ZMS) material, the OGP+ generator has a very small footprint and requires only a small space in a production facility.
And finally, producing oxygen on-site with Atlas Copco’s OGP+ generator removes the hassles of long-term contracts, logistics and safety concerns that accompany the ordering and handling of third-party oxygen cylinders. There is no need to move pressurised cylinders around the plant thus avoiding the potential risk of employee injuries. And finally, the elimination of oxygen transport and delivery reduces the user’s carbon footprint.
The generation of oxygen for industrial use is a straightforward process that involves the separation of oxygen molecules from the other molecules within a clean, dry compressed air stream. The OGP+ generator uses and optimises Pressure Swing Adsorption (PSA) technology. This simple, reliable and cost-effective process takes place in two separate pressure vessels (tower A and tower B), each filled with carbon zeolite molecular sieve (ZMS) that separates the oxygen from the incoming air. Adsorption happens when atoms, ions or molecules from a substance (compressed air in this case) adhere to a surface of an adsorbent. PSA technology isolates oxygen molecules from other molecules (nitrogen, CO2, water vapour and trace gases) to leave high purity oxygen at the outlet of the generator.
The ZMS material switches between a separation process and a regeneration process. So, at any time, one of these vessels produces oxygen while the other is regenerating its saturated ZMS. Thus, PSA technology enables continuous, high-capacity oxygen flow at the desired level of purity (90% to 95%).
The Atlas Copco OGP+ generator is supplied standard with an oxygen sensor, a digital flow meter, a pressure regulator and an automatic start-up function. The machine features a new advanced controller with a large HD colour touchscreen that enables easy, user-friendly navigation through options such as oxygen purity selection and purity alerts. The automated 24/7 feed air and oxygen monitoring and interception function safeguards the quality of the OGP+ generator’s performance and output.