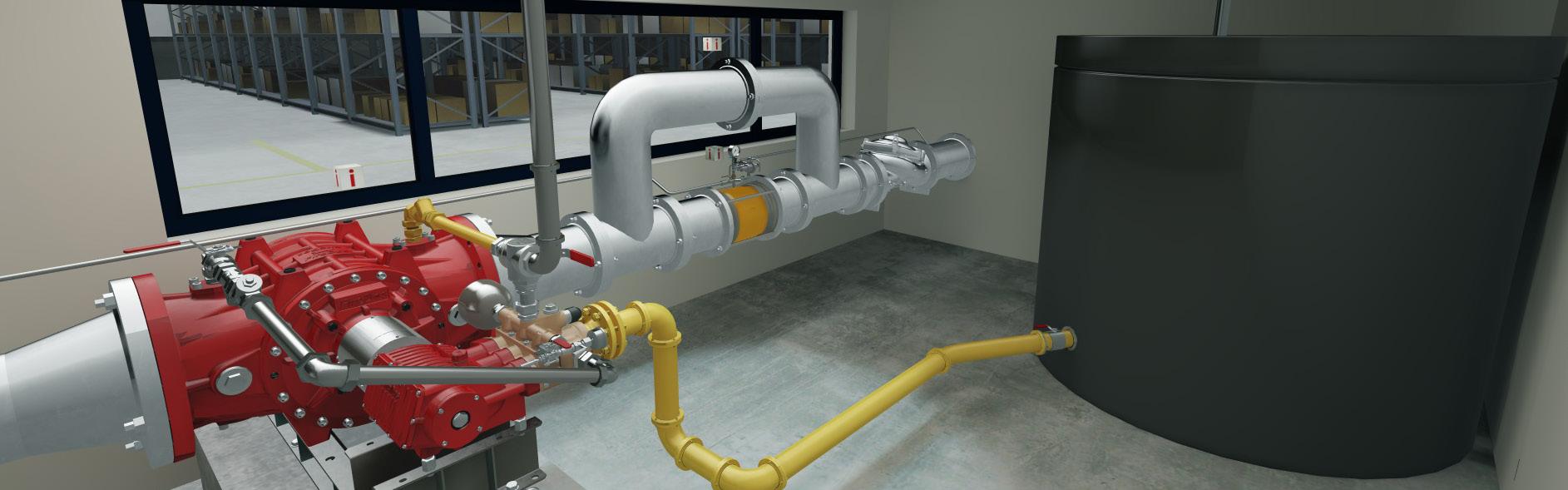
5 minute read
Foam is not the voodoo science of firefighting
Foam firefighting systems are indispensable tools in combating a wide range of fires, including those involving flammable liquids, chemical spills, and industrial incidents, also known as Class B fires. However, the foam firefighting market faces challenges that demand attention from end users, firefighters, contractors and equipment manufacturers. In this article, STUART PHYTHIAN , Oil & Gas Industry Manager at FireDos, delves into the primary issues faced by the industry, shedding light on their complexities and implications and and confirming that using foam as an extinguishing medium need not be regarded as the voodoo science of firefighting. By understanding these challenges in-depth, lay readers can start their research into some areas, enhancing their knowledge.
Environmental Considerations
One of the foremost concerns in the foam firefighting market revolves around the environmental impact of foam agents. Traditional fluorinated foam formulations, such as Aqueous filmforming foam (AFFF), contain persistent chemicals detectable in organisms, including humans, such as perfluoroalkyl substances (PFAS), typically in the form of perfluorinated acids and salt PFOA and PFOS (perfluorooctanoic acid, perfluorooctane sulfonate), which bio-accumulate in the environment and pose severe health risks. The development and widespread adoption of fluorine-free foam agents (per NFPA: Synthetic Fluorine Free Foam (SFFF)) and effective disposal methods represented crucial focus areas to mitigate these environmental concerns.
The method by which any firefighting foam operates is harmful to the environment. Foam is designed to de-oxygenate a fire. Hence, when any runoff meets natural water sources and shorelines, even when an environmentally safe foam is used, due to its ability for de-oxygenation, the short-term risk to plant and aquatic life is still severe.
A common criticism of the move to fluorine-free foam was the hazards to health and the environment associated with any oil, chemical or industrial fire. Any class B fire hazard was better attacked with a proven, albeit persistently toxic, foam as an extinguishing medium. This solution outweighed earlier attempts of using less effective fluorine-free foam. A second-order effect of fluorinated foam usage becomes the better choice when fire extinguishment, regardless of the foam type, is preferable to a prolonged fire releasing toxic gases and chemicals into the environment.
However, the more significant impact of firefighter and enduser training with foam solution represented a hazard to the environment, even when a fire does not exist.
The foam industry has developed and testing by various independent organisations and manufacturers, and in-house tests have proven the improved efficacy of new fluorine-free formulations. The debate has settled on replacing a persistent and harmful compound with a less persistent foam concentrate. Synthetic Fluorine Free Foam (SFFF) has been developed by manufacturers that can replace fluorine-based foam concentrates.
The worldwide adoption of foam concentrate alternatives is ongoing. It has been addressed legislatively by governments, organisations, and end users with the widespread adoption of fluorine-free foam being less damaging to the environment.
Firefighting Foam Replacement Costs
The short-term challenge for many organisations is also of high inventories and the cost. When foam concentrate stocks are purchased and depreciated over a typical three to five years, removing extensive stocks is a significant write-down, impacting company profitability and a concern for organisations.
In addition to the write-down cost of legacy foam concentrates, is the cost of disposal and equipment remediation, with very few cost-effective methods available on the market to dispose of PFAS foam or to reduce the cost of converting a fire truck or system contaminated with long-term exposure to PFAS foam. Washing equipment with hot water does not simply wash away many years of persistent use of PFAS-containing foam.
Replacement costs mean the newer formulations are more expensive than the legacy foam types, and the regulatory compliance costs in reporting, tracking and future potential fines for non-compliance.
Foam firefighting systems
Foam Systems And Operations
Notwithstanding the environmental considerations, a significant consideration is foam performance. Fluorine-free foam is not a drop-in replacement, meaning equipment and foam performance has to be considered. The main foam properties to be considered when using a foam solution are: expansion ratio drainage time burnback or heat resistance fuel compatibility or resistance application method storage and shelf life equipment compatibility training and familiarity regulatory compliance cost-effectiveness stability, retaining performance over time
Replacement foams are not a drop-in replacement to AFFF, and the replacement SFFF will differ in some of these from the legacy foam in use.
Due to new chemical formulations, many foam concentrates are significantly more viscous, pseudoplastic, and non-Newtonian. This non-Newtonian pseudoplasticity property means viscosity reduces as the shear rate increases. This high-viscosity rules out induction methods of proportioning, using a bladder tank system or foam pump skids where a wide range proportioner or eductor is used to mix the foam as the pressure balancing is either limited to a particular and narrow flow rate range or does not meet the required nominal proportioning rate.
At FireDos, as foam proportioner manufacturers, the primary design and installation error we encounter, regardless of foam type, is the design and sizing of the foam concentrate suction line. This is regardless of the proportioning type, such as wide range proportioner, pumped foam skid, stab pipe eductor and water driven foam proportioners. The increased viscosity exacerbates the design and effectiveness of the foam suction line. That is, proper design becomes more critical to the smooth running of the system.
Due to the effect of equipment design, pipe surface friction and pipe bend or elbows, higher viscous foam agents have a significantly higher pressure loss when flowing than low viscosity agents. This means only specific positive displacement pumps can be used for pumping. A high-pressure loss system translates to a very low flow at the discharge device, making the foam firefighting system ineffective. Our water-driven foam pumps are designed to pump all types of firefighting foam. The testament of this design is the FM5130 certification, ensuring proper proportioning with different foam viscosities and varying flow rates and system pressures.
As a service to its clients, we automatically calculate the suitability of an existing suction piping design and can assist with the design and sizing of a new installation. This service makes choosing a water-driven foam proportioner easy, as pressure balancing calculations are unnecessary. Installation and commissioning are easy and remove a significant headache for designers and contractors, ensuring the fire protection system operates effectively.
Training And Education
Effectively utilising foam firefighting systems necessitates specialised knowledge and training. Firefighters, fire protection engineers, and consultants must know the latest techniques and strategies for handling foam agents. Access to comprehensive training programmes in such a specialised area may be limited, particularly for smaller fire departments or personnel in remote areas. Expanding the availability and accessibility of training resources, including online courses, workshops, and simulations, can significantly contribute to the effectiveness of the industry.
To address the ongoing training efforts of a new foam firefighting system, we have a suite of training programmes, webinars and a virtual training area for customers to understand the effect of using different foam types and viscosities on a system.
Summary
When managed effectively, the costs of a properly managed foam solution migration to an environmentally friendly alternative can be seamless within everyday business operations. FireDos, as equipment manufacturers, are here to assist with equipment considerations regardless of the foam type chosen.
More details can be found at https://www.firedos.com/newsoverview/news
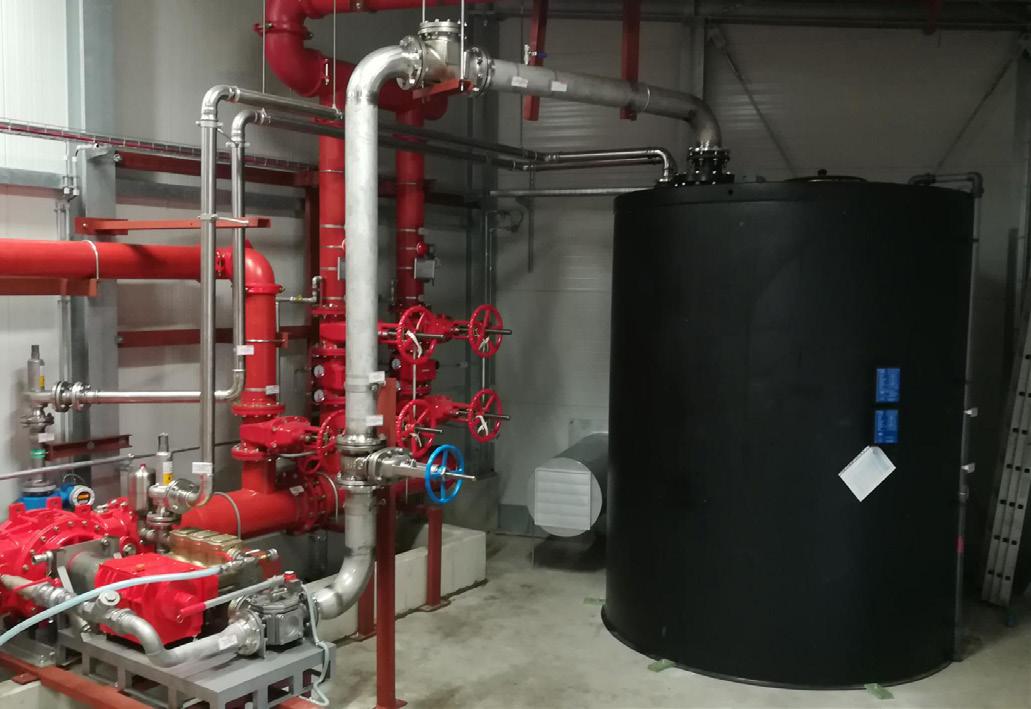
WeightMonitoring System
TLX Fire & Security’s Suspended WeightMonitoring System and Platform WeightMonitoring System monitor cylinder weighs in real time and is accurate within 100 grams. If the weight falls below a designated threshold, an alarm can be sent directly to the fire control panel. Up to 20 weighing units can be connected in series and individually addressed to one central weight control panel, which can display individual cylinder weight and alarm condition.
The Suspended Weight-Monitoring System has a maximum load capacity of 230 kg per weighing unit, and the Platform Weight-Monitoring System has a maximum load capacity of 500 kg per weighing unit. It also features mechanical lockouts on the weighing platform to prevent load cell damage during cylinder loading.
TLX FIRE & SECURITY tlxfire.com