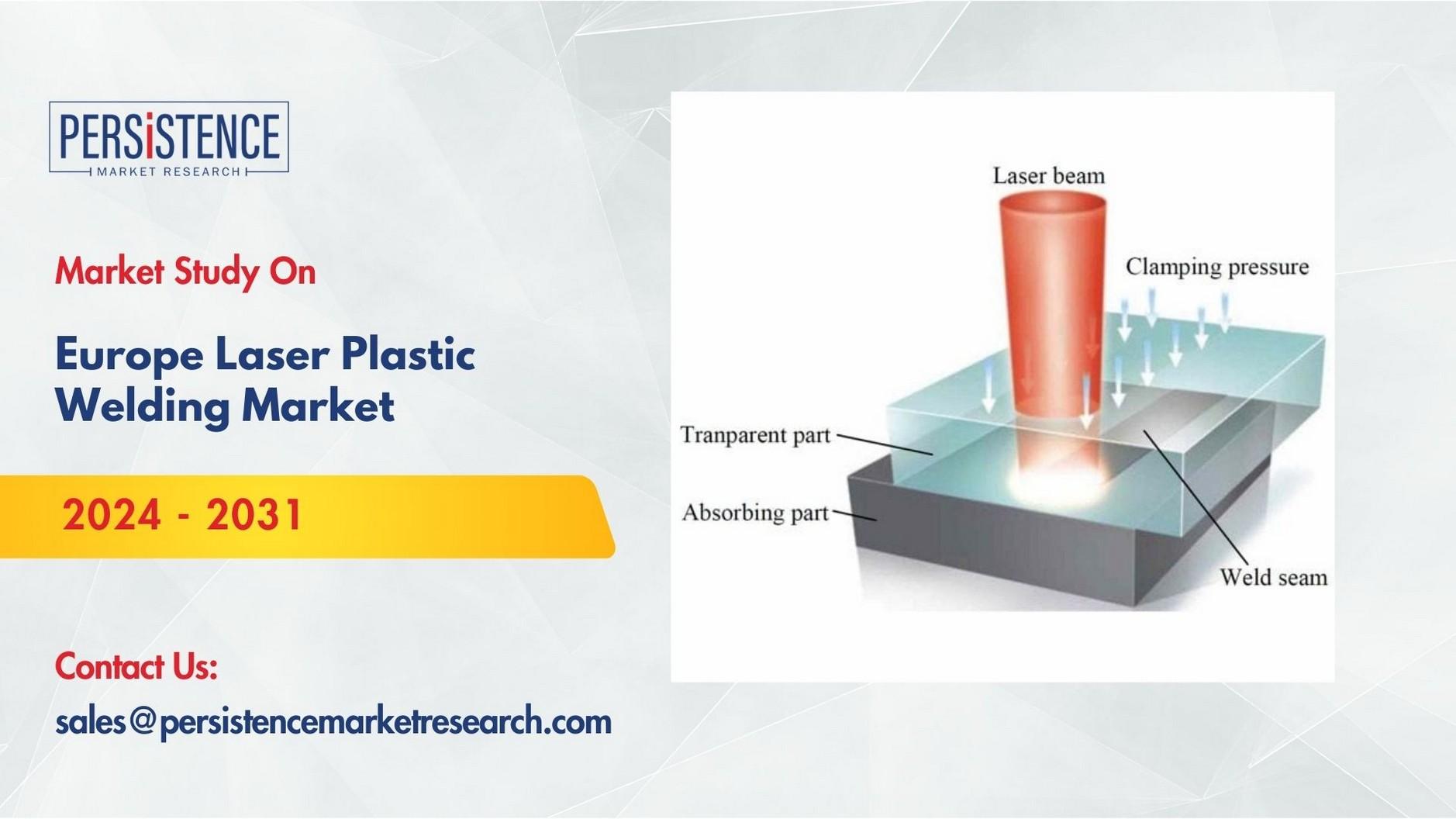
The laser plastic welding market in Europe has witnessed steady growth in recent years, driven by the increasing demand for precision welding solutions across industries such as automotive, healthcare, electronics, and packaging. As industries continue to innovate and prioritize lightweight, durable, and efficient components, laser plastic welding has become a preferred technology for its ability to join complex plastic parts with high precision and minimal defects.
Despite its advantages, the industry faces several challenges that need to be addressed for sustained growth. In this blog, we explore the key challenges faced by the laser plastic welding market in Europe and the innovative solutions being implemented to overcome these obstacles.
The Europe laser plastic welding market is estimated to increase from US$ 418 Mn in 2024 to US$ 760.9 Mn by 2031. The market is projected to record a CAGR of 8.9% during the forecast period from 2024 to 2031. The market is projected to witness significant growth in the coming years, driven by its applications across automotive, electronics, and healthcare industries. Laser plastic welding technology uses focused laser beams to weld thermoplastic materials. It is gaining traction due to its high precision, efficiency, and ability to process intricate components.
Overview of Laser Plastic Welding Technology
Laser plastic welding involves using a focused laser beam to join two plastic components, where at least one part is laser-transparent, and the other is laser-absorbent. The heat generated by the laser melts the absorbent layer, creating a strong bond when cooled. This technology is known for its advantages, including:
High Precision: Ideal for intricate and delicate parts.
Clean Process: No additional adhesives or fillers are required.
Durability: Produces strong and reliable joints.
Flexibility: Suitable for various industries, including automotive and medical devices.
These benefits have made laser plastic welding a popular choice in industries where quality, durability, and precision are critical.
Challenges Facing the Europe Laser Plastic Welding Market
1. High Initial Investment Costs
One of the biggest barriers to adoption is the high cost of laser welding systems compared to traditional welding methods. Laser plastic welding equipment requires advanced technology, including high-powered lasers, precision optics, and automated systems, which significantly increase capital expenses. This makes it less accessible to small and medium-sized enterprises (SMEs) with limited budgets.
Solution:
Rental and Leasing Models: Equipment manufacturers are introducing rental and leasing options to reduce the financial burden on SMEs.
Government Incentives: Providing subsidies and tax benefits for adopting advanced manufacturing technologies can encourage adoption.
2. Limited Material Compatibility
Laser plastic welding relies on the material properties of plastics. At least one component must be laser-transparent, and the other must be laserabsorbent. This limits the range of compatible plastics and poses challenges when dealing with multi-layered or reinforced materials. Additionally, achieving strong bonds between dissimilar plastics can be difficult.
Solution:
Material Innovations: Development of laser-compatible additives and coatings can expand the range of compatible plastics.
Hybrid Welding Techniques: Combining laser welding with other methods, such as ultrasonic or hot plate welding, can address material compatibility issues.
3. Skilled Labor Shortages
Operating laser welding systems requires highly skilled technicians who understand the nuances of laser parameters, material properties, and system maintenance. The lack of trained professionals in some regions poses a challenge for companies looking to adopt this technology.
Solution:
Training Programs: Collaboration between equipment manufacturers, educational institutions, and industry organizations to offer training and certification programs.
Automation: Increasing the automation of laser welding systems can reduce reliance on human expertise.
4. Competition from Alternative Technologies
Although laser plastic welding offers superior precision and quality, traditional methods like ultrasonic welding, vibration welding, and hot plate welding remain competitive due to their lower costs and wider material compatibility.
Solution:
Focus on Niche Applications: Highlighting the unique advantages of laser plastic welding in precision-demanding applications, such as medical devices and microelectronics.
Value Proposition: Educating potential customers about the longterm cost savings and quality improvements offered by laser welding compared to traditional methods.
5. Environmental and Regulatory Challenges
Europe’s stringent environmental regulations and sustainability goals pose challenges for the laser plastic welding industry. The process itself is environmentally friendly, but the use of non-recyclable plastics in welding applications can raise concerns.
Solution:
Eco-Friendly Materials: Encouraging the use of recyclable and biodegradable plastics in laser welding applications.
Compliance Support: Providing tools and resources to help manufacturers meet regulatory requirements, such as lifecycle assessments and sustainability certifications.
6. Market Fragmentation and Standardization Issues
The European laser plastic welding market is fragmented, with multiple players offering varying standards and specifications. This lack of standardization can lead to compatibility issues and inconsistencies in product quality.
Solution:
Industry Standards: Collaborating with industry organizations to establish common standards for laser plastic welding equipment and processes.
Cross-Industry Partnerships: Encouraging partnerships between equipment manufacturers, end-users, and material suppliers to develop standardized solutions.
Opportunities for Growth in the Europe Laser Plastic Welding Market
While the industry faces challenges, it also offers significant growth opportunities:
1. Expanding Applications in the Automotive Industry
Europe’s automotive sector is increasingly adopting laser plastic welding for manufacturing lightweight, durable components. The demand for electric vehicles (EVs) further drives the need for high-precision welding in battery components, sensors, and charging systems.
2. Growing Demand for Medical Devices
The healthcare sector is a key driver of laser plastic welding, as it ensures contamination-free and reliable joints for medical devices such as catheters, surgical tools, and drug delivery systems. The rise in healthcare spending and advancements in medical technology present lucrative opportunities.
3. Surge in Electronics and Consumer Goods
With the miniaturization of electronic devices and increasing demand for wearables, laser plastic welding is becoming essential for joining small, intricate components. The consumer goods sector is also leveraging this technology for durable and aesthetically pleasing packaging solutions.
Future Trends in the Europe Laser Plastic Welding Market
1. Adoption of Advanced
Automation
The integration of automation and robotics with laser welding systems is expected to revolutionize production processes. Automated systems not
only reduce labor dependency but also enhance precision and productivity.
2. Focus on Sustainability
Sustainability is a growing priority for European industries. The laser plastic welding market is likely to see innovations aimed at improving energy efficiency, reducing waste, and supporting the circular economy.
3. Technological Advancements
The development of advanced laser technologies, such as diode lasers and fiber lasers, is improving the efficiency and versatility of plastic welding systems. These advancements enable higher power delivery, faster processing speeds, and improved material compatibility.
Conclusion
The Europe laser plastic welding market is at a pivotal point, with significant opportunities for growth driven by advancements in automation, material science, and industry-specific applications. While challenges such as high costs, material limitations, and skilled labor shortages remain, the industry is addressing these issues through innovative solutions and collaborative efforts.
By focusing on niche applications, sustainability, and technological advancements, the laser plastic welding market in Europe is poised to play a critical role in shaping the future of manufacturing across various sectors. As industries continue to prioritize precision, efficiency, and environmental responsibility, laser plastic welding will remain a key enabler of innovation and progress.
Follow Us: Twitter | YouTube | LinkedIn