Metal Injection Molding Market to Benefit from Rising Demand in
Auto and Aerospace Sectors
The global metal injection molding (MIM) market is projected to reach USD 4.3 billion by 2025 and grow at a CAGR of 10.5%, reaching USD 8.6 billion by 2032. MIM is widely used in industries like automotive, consumer electronics, and medical devices, thanks to its ability to produce complex, high-strength components. The automotive sector, accounting for 35% of the market in 2025, is a key driver, particularly for lightweight parts in gearboxes, engines, and turbochargers. Stainless steel is a preferred material due to its mechanical properties, while North America's automotive resurgence is expected to fuel MIM growth. Technological advancements and automation further enhance MIM's adoption across sectors.
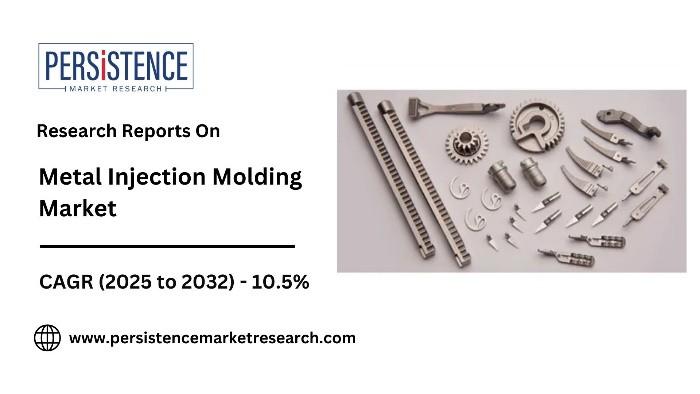
The metal injection molding (MIM) market is experiencing substantial growth driven by the rising demand from the automotive and aerospace industries. As these sectors demand high-performance components, manufacturers are turning to MIM as a cost-effective and efficient method of production. This article explores the growth of the MIM market, its potential applications, and how it is revolutionizing key industries.
What is Metal Injection Molding (MIM)?
Metal Injection Molding (MIM) is a manufacturing process that combines the precision of injection molding with the performance of metal. It involves mixing fine metal powders with a binder material to form a feedstock. This feedstock is then injected into molds to create complex shapes. The component is then subjected to a process of heating and sintering, which removes the binder and solidifies the metal. The result is a high-strength, high-precision metal part, which is ideal for producing complex geometries.
MIM is increasingly popular for producing small to medium-sized components, particularly where high precision and reliability are required. The ability to create intricate designs with less material waste and at a lower cost than traditional metalworking methods makes MIM an attractive option for many industries.
Growing Demand from the Automotive Industry
The automotive industry is one of the primary drivers of the MIM market. With the growing demand for lightweight, durable, and fuel-efficient vehicles, MIM offers significant advantages. Components like engine parts, sensors, transmission gears, and fuel system components, which require both strength and precision, are ideal candidates for MIM production. These parts must meet strict safety and performance standards, and MIM allows for the efficient production of these high-quality parts.
MIM is particularly beneficial for the production of complex automotive components that cannot be easily produced through traditional methods such as casting or machining. For example, MIM is used in the manufacturing of small, intricate parts like brackets, fuel system components, and locking mechanisms. The automotive sector’s push towards electric vehicles (EVs) is further fueling demand for lightweight and durable parts, as EVs require components that help to reduce weight and improve energy efficiency.
Moreover, as vehicles become more connected and automated, the need for high-precision, miniaturized components, such as sensors and actuators, is on the rise. MIM is well-suited to meet these needs due to its ability to create components with intricate shapes and complex designs.
Impact of Aerospace Industry Demand
The aerospace industry is another key contributor to the growth of the MIM market. With an increasing emphasis on high-performance materials, lightweight components, and cost-effective production methods, MIM is gaining traction as a solution for producing parts for both civil and military aviation.
MIM is used to manufacture components such as brackets, fasteners, gears, actuators, and connectors, all of which require high strength-to-weight ratios and the ability to withstand extreme temperatures and stresses. As the aerospace industry pushes for lighter and more fuel-efficient aircraft, the demand for components that meet these stringent requirements is increasing.
The aerospace sector is also seeing greater use of MIM for producing parts for unmanned aerial vehicles (UAVs), which require miniaturized components with high precision. The ability of MIM to produce small, intricate parts in high volumes at a relatively low cost makes it an attractive option for this segment of the market.
Technological Advancements Driving Growth
Advancements in MIM technology are playing a pivotal role in its growing adoption across industries. The ongoing development of new materials, such as high-performance alloys and specialized powders, is enhancing the capabilities of MIM. Additionally, improvements in mold design and process optimization are leading to better-quality parts with fewer defects.
The introduction of new sintering technologies, including high-speed and vacuum sintering, has helped improve the overall efficiency of the MIM process. This not only reduces production times but also makes MIM a more cost-effective option for large-scale manufacturing.
As industries such as automotive and aerospace continue to push the boundaries of performance and precision, MIM technology will evolve to meet these needs. The integration of MIM with other advanced manufacturing techniques, such as 3D printing and additive manufacturing, is also expected to open up new opportunities for innovation and growth in the sector.
Cost Efficiency and Sustainability of MIM
One of the key advantages of Metal Injection Molding is its cost efficiency. Traditional metalworking methods, such as machining or casting, can be expensive and time-consuming, particularly when producing small or complex parts. MIM, on the other hand, allows manufacturers to produce high volumes of intricate parts with minimal material waste, reducing overall production costs.
Additionally, MIM contributes to sustainability efforts within the manufacturing sector. The use of fine metal powders and the precision of the molding process ensure that less material is wasted
compared to traditional methods. This makes MIM an environmentally friendly option for industries looking to reduce their carbon footprint.
With increasing pressure on companies to adopt more sustainable practices, MIM offers a compelling solution that meets both economic and environmental goals. The ability to create highperformance parts while minimizing waste and energy consumption is likely to drive further adoption of MIM in the coming years.
Regional Insights: North America and Asia-Pacific Lead the Charge
The global Metal Injection Molding market is expected to grow rapidly, with significant contributions from regions such as North America and Asia-Pacific. North America, particularly the United States, is witnessing strong growth in MIM due to its well-established automotive and aerospace industries. The need for high-performance components in these sectors is driving demand for MIM technology, and manufacturers are increasingly adopting MIM to meet these demands.
In Asia-Pacific, countries such as China, Japan, and India are also seeing rapid growth in MIM adoption. The region’s booming automotive sector, coupled with increasing demand from the aerospace and electronics industries, is fueling the expansion of MIM in these markets. Additionally, the rise of manufacturing hubs in China and India is making MIM more accessible to a wider range of industries, further boosting its growth prospects.
Future Outlook of the MIM Market
Looking ahead, the Metal Injection Molding market is poised for continued growth. As industries such as automotive, aerospace, and electronics continue to demand high-performance, costeffective components, MIM will play an increasingly important role in meeting these needs. Advancements in MIM technology, along with the growing trend towards sustainability, will further drive the adoption of this manufacturing process.
The development of new materials, improvements in sintering technology, and the increasing use of MIM in combination with other advanced manufacturing techniques are likely to open up new applications and opportunities. As demand for lightweight, durable, and complex parts continues to rise, the MIM market will remain at the forefront of manufacturing innovation.
Conclusion
The Metal Injection Molding market is experiencing significant growth, fueled by rising demand from the automotive and aerospace sectors. With its ability to produce complex, high-precision components at a lower cost, MIM is poised to revolutionize manufacturing across a range of industries. As technology continues to evolve, MIM will become an even more integral part of the production process, helping companies meet the increasing demands for high-performance parts while also addressing the need for cost efficiency and sustainability.