
6 minute read
Pan tastic forGinG for the future at sB forGe
Pan-tastic
Forging for the Future
by Jeff mIller
Picture three brothers running a blacksmith shop in downtown Santa Barbara . What do you see? Fire? Sparks? Bearded guys pounding red-hot molten steel while heavy metal music booms from the speakers? If so, you got it . That’s Santa Barbara Forge . That’s where you’ll find the Patterson brothers and their crew hard at work on everything from railings to doors to chandeliers to tables and cookware . The brothers are Dan, 43; Joel, 40; and Andy, 38 . Their shop is on Gutierrez in Santa Barbara’s downtown industrial zone, but you can see their work all over town, from the signs at the Museum of Natural History to the exterior lamps at MOXI and beyond . Far beyond . Much of their business comes from their website www .sbforge .com), which is a serious creation in itself .
There you can learn the difference between cast iron and forged steel . (Cast iron involves pouring molten metal into molds . Forged steel involves bending and hammering red-hot metal into shape .)
And the process is beautiful to witness . On their YouTube channel you can watch Andy making that sign hardware for the museum . By the end you might want to become a blacksmith too .
How do three 21st century brothers get into such an 18th century business? Like smithing itself, it was quite a process .
It started with Dan, who was interested in taking some drawing classes at college (Hope College, Holland, MI) but they were full so he took sculpture instead . Turned out to be “one of those great little accidents that turn the course of your life,” he said .
He further followed that course pursing his master of fine art degree at Transart Institute in Berlin, Germany, and then started thinking about “how to commodify” what he’d learned . After several moves (LA, New York City) and jobs (cabinet maker, rock drummer), he finally settled on Carpinteria and metalwork . “There are so many cabinet makers out there, and way fewer metal workers,” he said . “Plus it’s a huge part of the aesthetic here . ”
So he got some tools, including a roofing torch, and built a forge out of an empty propane tank, lined it with brick, and went to work . “It was very, very slow,” he recalled . “I knew a designer who was kind enough to give
me a shot . And I just kept pressing forward . It took a long time, like the Colorado River cutting the Grand Canyon, but eventually things happened .” Even so, there was “no money the first eight years,” Dan said . “We lived off my wife’s [Leanne’s] teaching salary . If anybody deserves credit, it’s her . She’s put up with a tremendous amount of noise . ”
Then brother Andy came on board . “Andy was always really prolific with clay as a kid,” Dan recalled . “Always bending and smooshing . So he brings that natural inclination to this job . ”
After graduating from Westmont College, Andy went to Baltimore to apprentice with blacksmith guru Chris Gavin . “He came back with a lot of skills,” Dan said . All about “treating metal as a moveable medium . ”
And so the stage was set for the brothers’ first big break — fabricating mosaic installations along Cabrillo Blvd . for the city . “That project got us fiscally to where we could get our first studio,” Dan said . The site was the former Craviotto Ironworks building at Anacapa and Ortega, and it was “fantastic,” Dan said . Being downtown “opened so many doors for us . That was really the tipping point .” Then one more move, to Fig and Cota before landing at their present 4,500-squarefoot site on Gutierrez four years ago, formerly home to a VW mechanic and a surfboard maker .
“By then we’d been downtown five or six years,” Dan said, “working jobs all over Montecito and beyond . Mostly this area, but also Tahoe, Mammoth, etc . Once you get your name out there and build a customer base, it tends to roll on its own .” Now the company does hundreds of jobs a year, with wait times as long as six months for major productions .

QUALITY CUSTOM WOODWORK
50 YEAR ANNIVERSARY 1969–2019

Cabinetry • Doors • Windows • Mouldings
RCHITECTURAL
ILLWORK OF SANTA BARBARA, INC.
Showroom located at
8 North Nopal Street Santa Barbara, CA (805) 965-7011 www.archmill.com
Serving Santa BarBara Since 1969
Lic # 261772
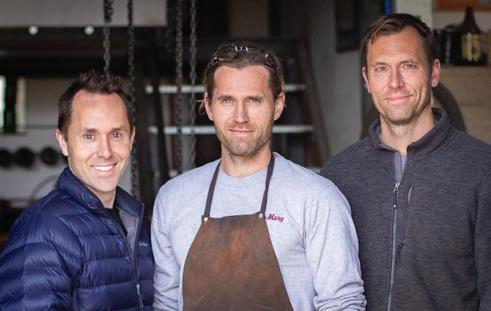
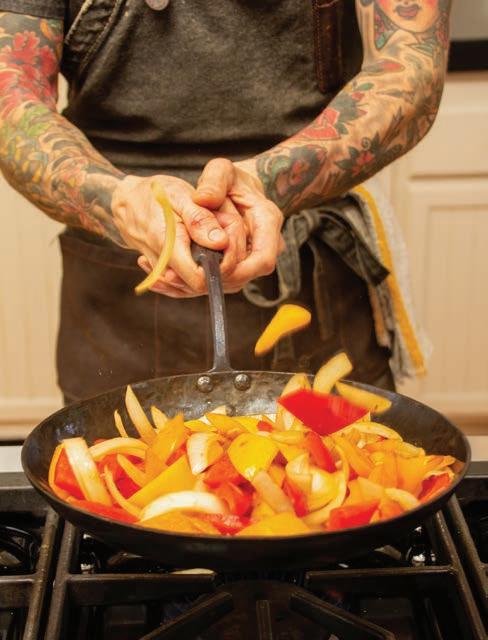
A good bit of that reach has been the work of brother Joel, who was helping out part-time along the way but joined the company full-time in 2018 . While Dan is the CEO and chief designer, and Andy is “definitely one of the finest blacksmiths on the Central Coast,” Joel has built up the website and taken the lead on marketing . As a result, “We’ve worked on some of the finest homes all over town, which would mean some of the finest in the nation,” he said . And the crew has grown to include production associates Ben LaBarge, Ray Martin, Claire Vance, and Jacob Clark .
Recently they’ve added cookware to their product line, to give customers a more intimate point of access to the world of forged steel . Santa Barbara is a foodie town, Joel observed, and the brothers are right in step with that . “We all love to cook and we love kitchen gadgetry, so it didn’t take long to put one and one together,” he said .
Said brother Joel: “We started with a small pan . We wanted something compact that could fit in any kitchen .
—andy Patterson
Also because we love making bacon and eggs .” Then it was the larger pans, then spatulas, ladles, and the Matsu hand-forged cleaver . (What’s the difference between a cast-iron pan and a hand-forged pan? Hand-forged pans are lighter, easier to handle, quicker to season, and less porous, say the pros .)
Joel has also enjoyed describing the line on the website . For example, you can “feed the entire wagon train with the Sonora Homestead collection .” And Dan said it’s been heartening to see all the repeat customers, as well as seeing their company mentioned in cooking blogs . “People are definitely noticing,” he said . (There aren’t too many things in life you can recommend without reservation, Dan observed . One is their skillet . Another is “Rambo III .”)
Andy puts it this way: “Cookware combines the simplicity of function and the beauty of craftsmanship . That, in essence, is what blacksmithing is all about to me . ”
And Joel noted that, like all of their products, the cookware ended up being more than just functional . “These are heirlooms,” Joel said . “The kinds of things that can stay in families and be used and loved for generations . ”