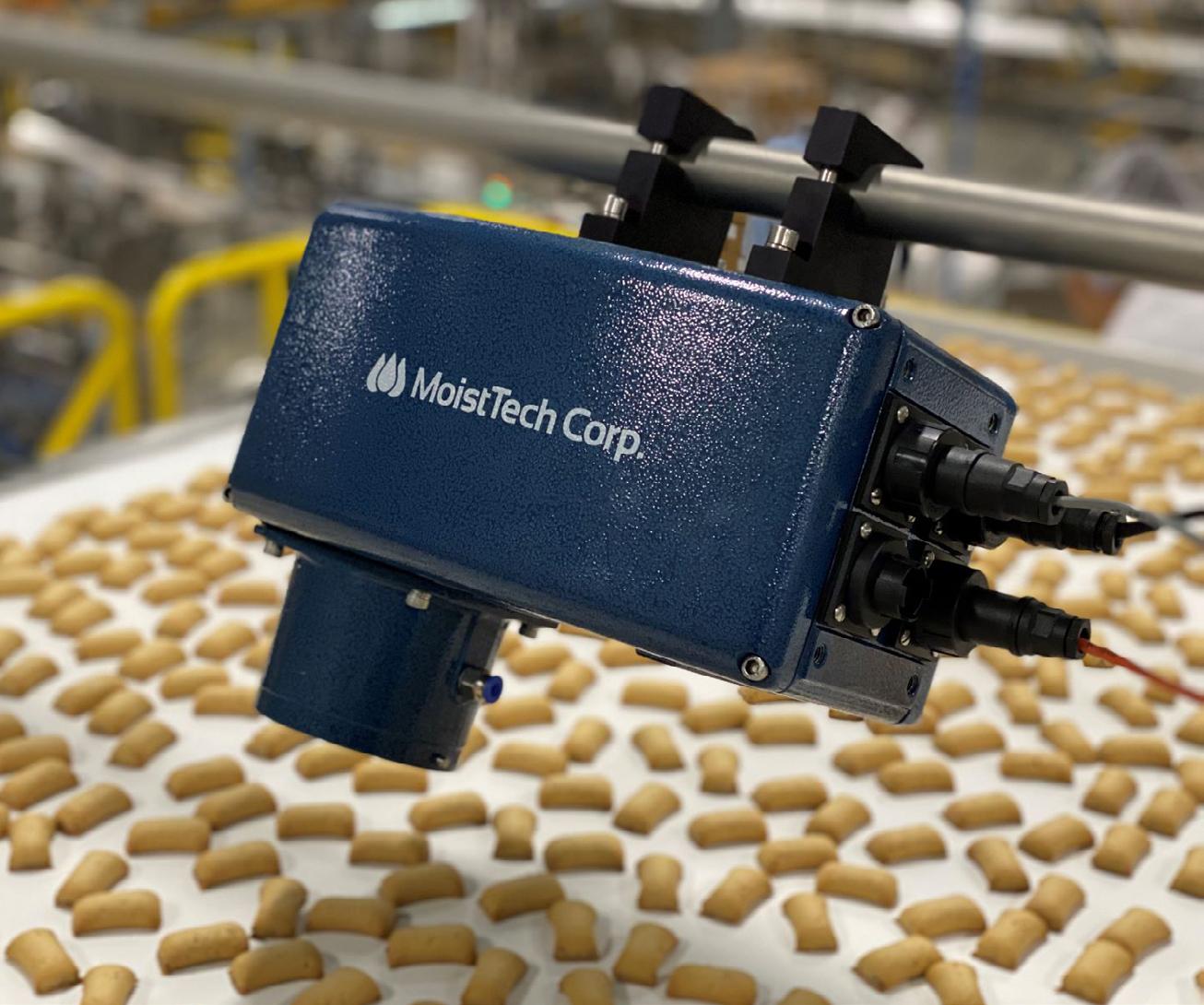
9 minute read
MILLING AUTOMATION made elegant with
A previously labor-intensive industry, milling has embraced automation to drive greater efficiency in operations while at the same time enhancing the safety and quality of milled products
BY MADELEINE ORINA
In the food sector, where sustainability and traceability are two very important factors, process control is increasingly vital to ensure quality and error-free production. This is especially true in flour milling where large quantities of grain are processed in a day. To maintain operations and keep customers serviced, companies have had to embrace technology and automation.
In milling, automation removes variability by continuously monitoring production streams for variances in production rates and quality. Dips in rates and quality can be monitored, and in some cases, corrected upstream automatically.
Automation also offers trending and historical data to help management find the most efficient production methods. Equipment condition monitoring can provide an early indication of imminent machinery failure, providing the opportunity for planned maintenance, and improved uptime.
In the milling industry, new technologies like artificial intelligence (AI), machine learning (ML), and robotic process automation (RPA) are now part of a solid business strategy and have been successfully incorporated in all the stages of the milling process.
Innovative Automation Takes The Uncertainty Out Of Grain Quality Assurance
One critical factor that has a huge impact on grain quality is moisture content. High moisture content leads to storage problems because it encourages fungal and insect problems, respiration, and germination. Storing grains at the desired moisture continent is therefore key to preserving the quality and safety of the grain.
New, innovative grain moisture monitoring methods can vastly improve the accuracy and efficiency of the process, enabling early intervention measures to be taken to ensure grain quality is always at optimum levels. Online near-infrared moisture sensors are one such technology. They provide rapid and real-time analysis of grains and can be mounted above belts and conveyors or installed in silos and storage hoppers.
“NIR moisture meters follow the principle that water absorbs certain wavelengths of light,” says John Bogart, Managing Director of Kett US. “The meter reflects light off the sample, measures how much light has been absorbed, and the result is automatically converted into a moisture content reading.”
Unlike air ovens or even moisture balances, portable NIR equipment is designed for ease of use. For example, with Kett’s KJT130 Handheld Portable Instant Moisture Meter, the user simply points the instrument at the grains, seeds, or agricultural product. The moisture content is instantly shown on a digital display, with results accurate to .01% in a 0-100% measurement range. Technologies such as machine learning, neural networks, and cloud computing have also seen their integration into novel and innovative approaches for measuring grain moisture content.
A revolutionary example is Scottlandbased automation company Crover, which has recently begun commercial trials of its world’s first bulk grain-monitoring robot, aptly titled CROVER. CROVER burrows into stored grain to identify sub-optimal storage conditions, and also physically mixes grains in situ, which helps avoid spoilage.
CROVER is remotely operated, with the ability to reach every corner of the grain bulk, meaning workers can avoid performing the risky operation of sampling themselves. Once commercialized, each one of the new robotic devices is expected to be able to save a total of 380 tonnes of grain every year.
Rapid advances have also been made in recent years in visible spectrum imaging, which uses integrated smart sensor systems. We can see these being implemented in smart granaries which are gaining popularity across China.
As an example, Xinglong Granary has more than 400 sensors installed within the 1800 square meter space. The intelligent platform conducts a comprehensive analysis of grain temperature, atmospheric temperature, and atmospheric humidity, and gives suggestions on how to manage ventilation. Forty-five pest traps are also installed at different layers and locations within the granary. The number of pests collected by the traps will be shown on the platform, telling the granary manager which area requires pest control measures.
NIR moisture sensors provide rapid and realtime analysis of grains
`Buhler's recently unveiled optical sorter reportedly delivers up to 50% higher rejection concentrations
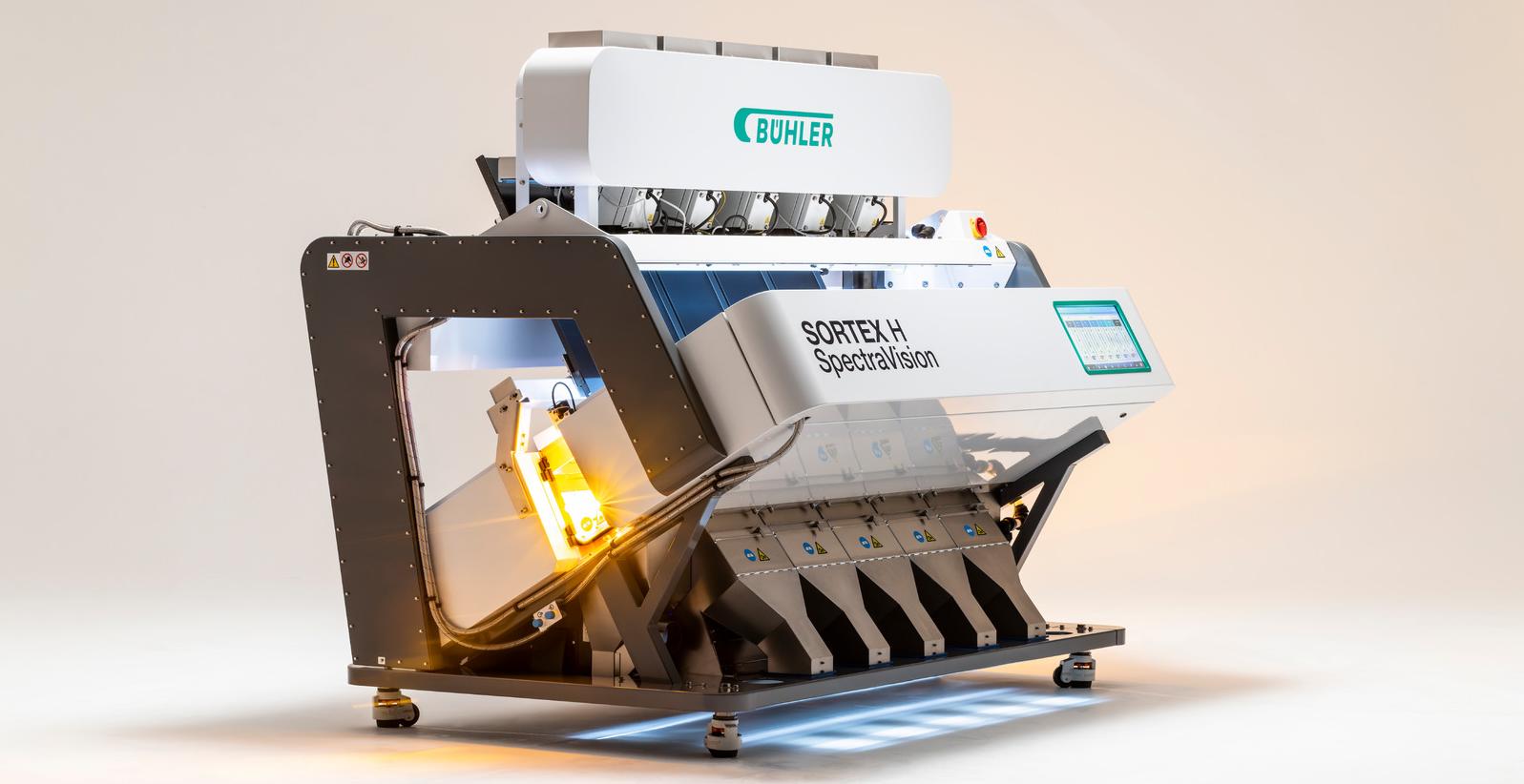
"Through the intelligent platform, data collection can be carried out on the gas content and number of pests. We use the automatic nitrogen filling system, which can reduce oxygen concentration in the grains, and kill pests," said Liang Haoran Manager, Xinglong Granary.
While silo cleaning is an essential task in grain handling facilities, it’s also very dangerous. Because of this, manufacturers are finding new ways to reduce manual interference. Sukup
Manufacturing company introduced its 5K and 10K Zero-Entry Commercial Paddle Sweeps to prevent operators from ever entering the bin.
“Paddle sweeps are designed to greatly reduce or eliminate any manual labor that must be done to clean grain out of a grain bin completely,” says Sukup External Relations Manager Rachel Geilenfeld. “This is especially important in large commercial grain bins.”
In addition to being a highly effective floor cleaner, Sukup's paddle sweeps incorporate several safety features and use the company's advanced zero-entry controls system. The company also integrated a plug switch into the center sump that communicates with their controls. This switch will shut down the sweep if a plugged sump is detected.
Not only do these technologies reduce the difficulty of human monitoring, but they also improve the monitoring speed and accuracy of temperature and humidity, save a lot of manpower and material resources, and improve management efficiency.
Looking Inside Every Single Kernel
The earliest conveyor systems originated in the 18th century when the first conveyor belts were made from leather or canvas and supported by wooden frames. Today a wide range of materials for conveyor belt systems exist and with the increasing popularity of robotics, conveyors have become increasingly computer controlled and automated. Automated conveyor systems are equipped with sensors, bar code readers, weight sensors, RFID tags, camera systems, and other technologies to track materials’ movement and perform tasks such as maintenance and inventory management.
Key Technology’s Iso-Flo vibratory conveyors work in conjunction with different types of sensors and systems, including weighing belts, load cells, and product height sensors, that transmit data to the control system about products flowing through the line.
When it comes to sorting grains on a conveyor line, traditional methods are limited to the removal of odd-looking kernels as observed and judged from the visual inspection of their surface properties i.e., discolored kernels or kernels with abnormal morphological properties. These methods are, however, unable to judge the quality of the most valuable part of the kernel –the inner part.
Digital sorting has enabled the sorting of grains beyond visual surface properties by making it possible to analyze and identify each kernel in a batch and grade them according to their internal qualities.

BoMill's TriQ 30 utilizes a patented grain quality sorting technology, applying the principals of NIR spectroscopy to 'look inside every single kernel' to decide its classification: eg into animal feed or human food, with the capacity of 25,000 kernels-per-second, sorted into three or six quality fractions.
Bühler Group has also launched its latest optical sorter for wheat, rye, oats, grains, coffee, and pulse. Known as the SORTEX H SpectraVision, the new sorter reportedly delivers up to 50% higher reject concentrations. One customer that has been enjoying the benefits of the SORTEX H SpectraVision is Spain's oat milling company Harivenasa. Alberto Loizate, Managing Director, Harivenasa – Alea said: “We’re extremely happy with the SORTEX H because it’s very efficient, boosts our productivity, and we get much better quality now than we previously did in terms of unhusked grains, defects, black spots and so on.” Since installing the machine, Harivenasa says it has seen improved quality in its oats and is now looking to enter new markets in new countries.
Grain sorting has also gone beyond optical sensors. The Metra Group Inc. recently unveiled a new generation grain cleaning machine, METRA, which uses a revolutionary jet stream of air and aerodynamic principles to precisely separate source material into independent fractions based on relative density. Metra’s unique technology with precise quality cleaning ability and high production volume allows the replacement of 3-4 grain cleaning machines within one technological line.
“An intelligent system is built into each model with the help of which we can connect to the machine at any time, help you adjust your required settings, or make diagnostics before the cleaning season, as well as after it,” the company said in a press release.
These advanced cleaning technologies capture the hidden value in every grain batch, allowing the industry to optimize yield and revenue from every harvest and, thus, directly contributing to UN Sustainability Goals for 2030.
There are also safety upgrades in products tasked with monitoring conveyor belt cleaning. Martin engineering’s new N2 Twist Tensioner is an autonomous tensioning system that continuously monitors and delivers proper conveyor belt cleaner tension, replacing a job that, until recently, was done by hand.
"Prior to this new design, belt tensioners had to be manually monitored and adjusted in some applications on a daily basis," says Andrew Timmerman, P.E. and product development engineer at Martin Engineering. "The N2 Twist Tensioner automatically maintains precise cleaning pressure, without maintenance, and data is available remotely."
In Numbers
25,000
Arrius is a radical step change in how millers are able to control the quality and consistency of their product
Thanks to the agile design and automated features that reduce or eliminate the need for manual maintenance, maximize productivity and reduce downtime, today’s conveyors run more smoothly, both operationally and in terms of maintenance. And a smooth-running conveyor system is vital to a smooth-running plant.
Traditional grinding methods have fallen short in a highly price-sensitive and competitive market where even the smallest deviation in production parameters goes straight to a miller’s bottom line.
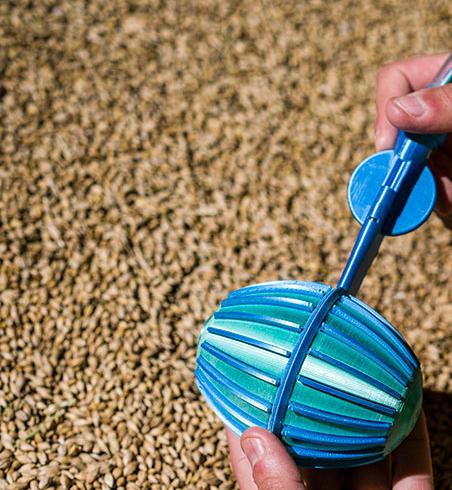
Buhler's integrated grinding system Arrius is a radical step change in how millers are able to control the quality and consistency of their product. The technology features sensors in the feeding module and the roller pack that enable it to automatically adjust to the characteristics of the raw material.
The intuitive touch-screen operating unit allows easy monitoring and control of the grinding system. Thanks to the integrated web server, Arrius can be operated via smartphone, tablet, or PC within the mill. The user interface is extremely intuitive and can be understood within a very short time by personnel with milling experience.
Robots Grace The End Of The Line
In the final step of a flour mill, the flour is either packed in paper or polypropylene bags in a broad range from 1 to 50 kg., or leaves the mill on trucks and trailers after a bulk loading operation.
Henry Simon has a wide variety of automatic and manual packing systems, which can be designed with different levels of automation solutions upon request. The scaling and packaging machines are controlled by PLC to ensure high efficiency and operational safety.
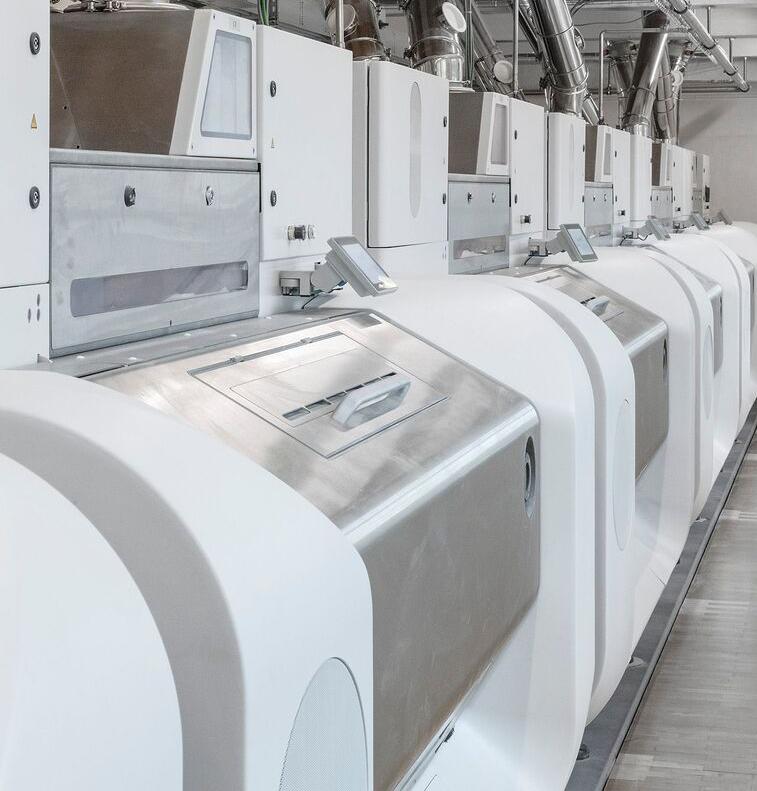
Milling plant manufacturer Ocrim recently completed successful testing of its branded handling system at wheat flour-producing company, Mills of Costa Rica S.A. The new packaging line, completely automated, is a completion of the existing system for small-cut flour packets intended for the convenience goods sector.
Specifically, the line supplied includes the primary packaging in bags, automatic package quality and quantity control systems, conveyors lines, secondary packaging in a shrink-wrapped bundle and in pre-cut cardboard boxes, and finally the double robotic automatic palletizing station and wrapping of pallets with stretch-film.
At the end of the line, bagged grain is moved to the pallet. Traditionally palletizing of bags and sacks was done by hand. However, this has many drawbacks including production downtime due to staff breaks, and the high risk of repetitive strain injuries occurring.
Okura Flexible Automation Systems Pte Ltd (OFAS), a Singapore subsidiary of Okura Yusoki Co., Ltd., a Japanese industrial automation system manufacturer & integrator proposed an automated palletizing system.
A conveyor transports filled flour bags from the production line to the palletizing station, while the Okura A1600 robot palletizer does the rigorous work of palletizing filled flour bags accurately onto automatically-deployed pallets. These collaborative robots (cobots), are equipped with artificial intelligence-based technologies and are distinguished from traditional industrial robots by their ability to work with people safely in a shared work environment.
Robotic palletizers have come a long way in the world of bag palletizing. Once thought of as a “gimmicky” way to palletize bags has become a mainstream and reliable way to do the monotonous and dangerous chore of palletizing bags. These robotics also help increase production and revenue, especially now with labor shortages and supply chain kinks.
The Future Of Milling
According to research firm Allied Market Research, the global flour market is expected to exceed US$ 270 billion by 2022 with a CAGR of approximately 4.4%.
Flour Mills wanting to corner a significant share in this market will not only need to automate their operations but will also have to enable their
IT Systems to cater to this type of growth in the flour industry.
When it comes to implementing an automation solution, purchasers should consider hardware and software that will allow them to “future-proof” their systems, meaning a design that supports future upgrades and keeps knowledgeable support close at hand. As with many products today, there’s no need to hang onto rigid legacy systems when newer, webbased solutions may come with support and a lower cost to implement.
Going ahead, mills have to figure out what data are important for their grind and how to apply it toward improving the process. That typically means using data to improve mill yield, keep flour products within specifications, and run in the most energy-efficient way possible.
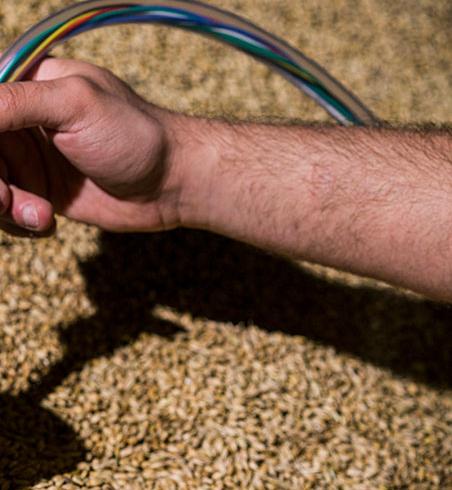
Finally, while the rapid uptake of automation is reducing the need for manual labor, which is a growing concern among the working population, it is best to look at it as a give-andtake. Automation often creates as many jobs as it makes redundant over time.
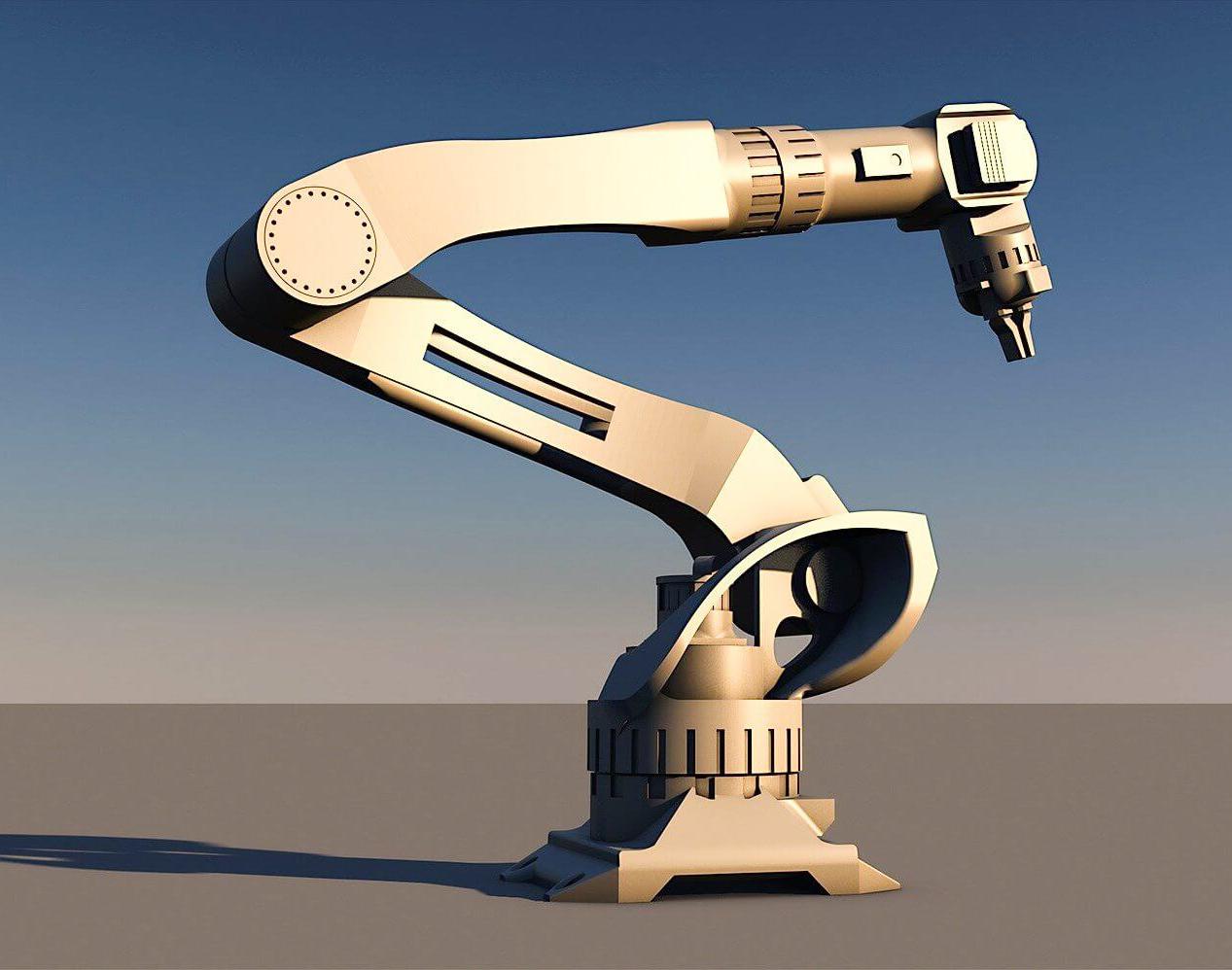
Furthermore, workers who can work with machines are more productive than those without them; this reduces both the costs and prices of goods and services. As a result, consumers spend more, which leads to the creation of new jobs. Ultimately, technology-driven change is inevitable. And considering the end goal, in this case, is the production of greater quality flour at a reduced cost, the change is undeniably for the better.
MMEA