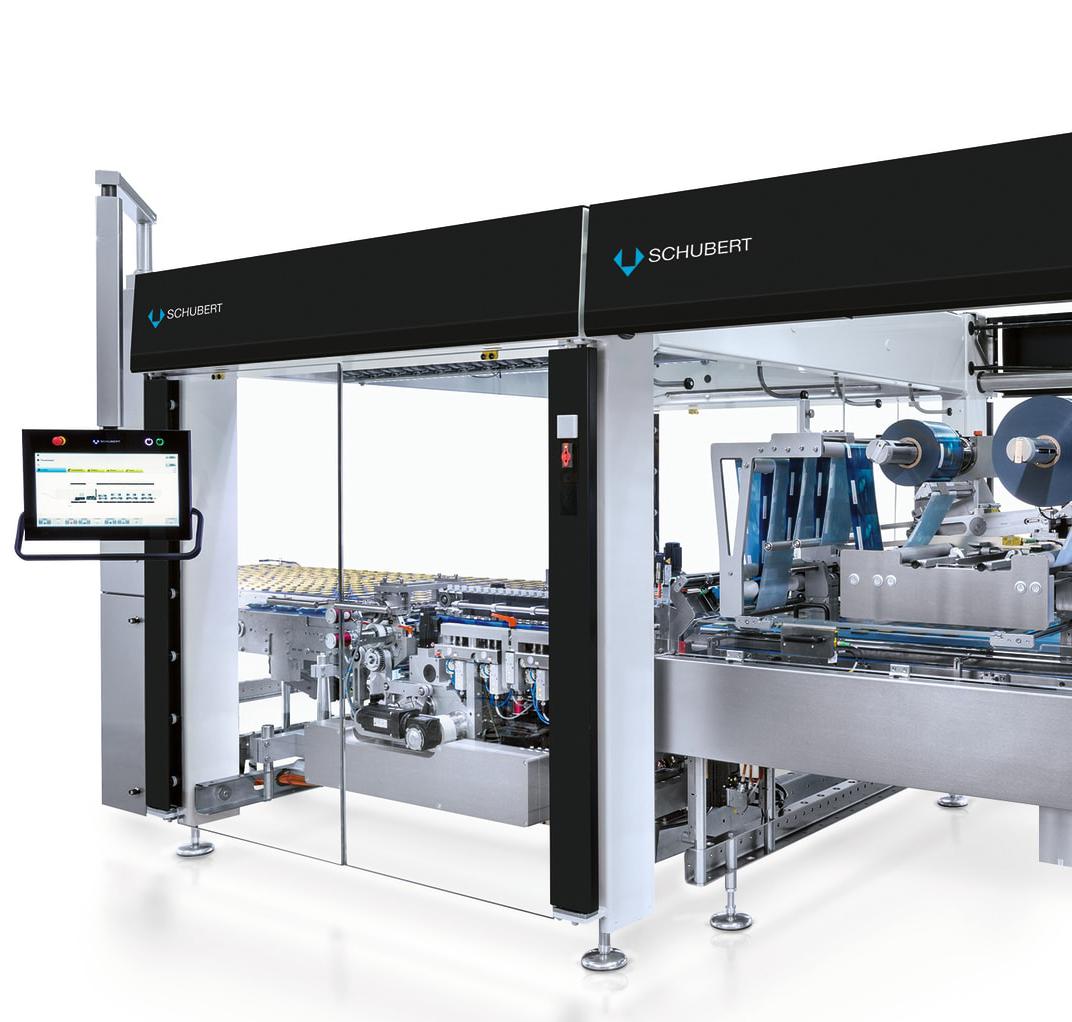
7 minute read
AUTOMATION, ROBOTICS & Sustainability drive PHARMA PACKAGING
By Alphonce Okoth
Pharmaceutical packaging is a critical segment of the healthcare industry as it secures, stores, and protects drugs when transporting and storing drugs. Poor quality packaging can impact a drug’s efficacy, affecting patients’ outcomes in the process. It is for this reason that pharmaceutical packaging is highly regulated over the world to protect medicines from physical damage and external influences that might lead to contamination.
Nevertheless, pharma packaging has been rapidly expanding in the recent past due to the rising demand for pharmaceutical drugs and medicines. Fortune Business Insights estimates that pharma packaging market to be worth US$101.59 billion in 2022 and forecast the market to grow at a compound annual growth rate (CAGR) of 5.8% to reach US$150.78 billion by 2029.
As the market grows, packaging providers are innovating to keep up with new demands in the healthcare industry. From the need for sustainable packaging to the incorporation of artificial intelligence in production processes, a lot is happening in the industry at the moment and is certainly poised to radically change the pharmaceutical packaging landscape.
A SECTOR RELIANT ON ARTIFICIAL INTELLIGENCE (AI)
According to a report by Grand View Research, the global AI healthcare market size will reach a staggering US$31.3 billion by 2025, growing at a Compound Annual Growth Rate (CAGR) of 41.5% in this time. This just shows how AI is becoming increasingly pivotal in healthcare delivery.
When it comes to pharmaceutical packaging, AI pill inspection systems are already being deployed as an effective way to help pharmaceutical companies avoid defects. With AI pill inspection, it is possible to increase the speed at which solid oral doses travel through a packaging line. This could dramatically decrease manufacturing time and the number of pill defects that occur. This technology also helps pharmaceutical companies maintain better quality standards for their pill packaging.
In addition,AI inspection helps manufacturers maintain the correct number of counts in each container by keeping track of pill orientations and pill positions within a package or bottle.This is adding consistency not only across packages but also throughout each container, which leads to more effective pharmaceutical packaging overall.
Robotics Take Over Manufacturing Processes
The adoption of robotics, collaborative robots (cobots) is steadily increasing in pharma packaging. It brings with it the benefits of increased efficiency, boosted productivity, scalability and increased speed.
Previously, robots were often used for lifting heavy items and they used to work in dangerous areas. Nowadays, robots can be found everywhere because of their flexibility for different products and formats. For instance, robots are now being deployed to load products and packaging material on the lines, the picking and placing of products into the packaging as well as labeling and assembling too.
Gerhard Schubert, a developer of modular packaging machines for the pharmaceutical industry has introduced its flexible, robot-based top-loading packaging technology (TLM). Utilizing simple mechanics, intelligent control technology, and high modularity, the technology can also integrate into the packaging machines diverse additional functions such as labeling, inserting instructions for use, or prescribed quality controls. The modular machines by the firm can package pharmaceutical products of all kinds in a wide variety of dosage forms.
Another robot in the market is Marchesini Group’s Integra 720V. The robot is an integrated, robotic line for packaging blisters in cartons, and is characterized by very high speeds. The compact multilane blister line comprises two sections: a blister packaging machine that forms the blisters and places the products for packaging in their cavities, and a cartoning machine that packages the blister in its carton.
The two sections are connected by Robocombi, a three-axis robot fully integrated with the line and created entirely by the firm’s R&D departments. This solution can produce up to 720 blisters and up to 500 cartons/minute, delivering easy cleaning and size change since the product loading area is separated from the electrical and mechanical parts.
ECO-FRIENDLY PACKAGING
A significant portion of pharma packaging is plastic in nature, therefore, making it a problem for the environment. Pharma packaging manufacturers like their peers in food, homecare, and beauty are also on the lookout for alternatives to plastic to cut down on their carbon footprint.
“The market is currently looking for alternatives to plastic," says Francesco Stanzani, Commercial Director, Marchesini Group.
Those that find viable alternatives end up having an edge over their competitors. “We have had great success with our solutions such as the MA 80 cartoner, which is designed to place products in paper trays, as well as the FB220 thermoforming machine with eco-friendly materials such as Polylactide (PLA),” Stanzani confirms.
101.59B
US$ IN NUMBERS PHARMA PACKAGING MARKET SIZE
Packaging equipment supplier Ima is also promoting eco-friendly plastic substitutes for the packages manufactured on its machines. An example of this is Ima Safe’s ‘Paper tray packaging line’ which packages a wide range of parenteral products and medical devices on paper trays inside cartons, creating 100 % paperbased packaging which is easy to recycle, has low energy requirements and is biodegradable.
Sustainability can also be applied to the manufacturing process. Thomas Fricke, Commercial Director of Ima Pharma, Ima Group adds, “There have been significant movements in containment technology for capsule filling which reduces the use of disposables – often in plastic – and of water, thus generating significant energy savings and economic benefits.”
When it comes to producing sustainable packaging materials collaboration is key. For instance, Bosch’s Syntegon, one of the leading global process and packaging technology providers, collaborated with the Finnish packaging material manufacturer Huhtamaki to develop a sustainable paper alternative to plastic blisters for tablets and capsules.
Matthias Klauser, Sustainability Expert at Syntegon states in a release, “Thanks to the combination of our TPU 1000 form, fill and seal machine for paper packaging; the 3D formable Fibreform paper from Billerud Korsnäs; and the sealable barrier coating from Huhtamaki, we have succeeded in forming paper with the geometry required for tablets in cavities of three to four millimeters.”
One emerging trend in pharma is the concept of quality by design (QbD).This initiative ensures that medicine is administered to patients as intended and nothing environmentally harmful escapes the packaging. Antibiotic environmental contamination is and has been a big problem in recent years and QbD can help curb this. In addition, recycling also continues to trend in a positive direction in all packaging formats.

This even includes flexible plastic packaging, which is becoming an easily recyclable packaging format. There is also a push to find solutions for single-use plastic, but in the medical field, that presents a particular challenge. Therefore, singleuse plastic continues to be utilized, while other types of plastic are evaluated for its replacement.
SINGLE-USE PROCESSES
More pharma companies are embracing singleuse technology (SUT) in their manufacturing process. This shift is ongoing as more industry players are becoming aware of the incredible advantages of this technology.
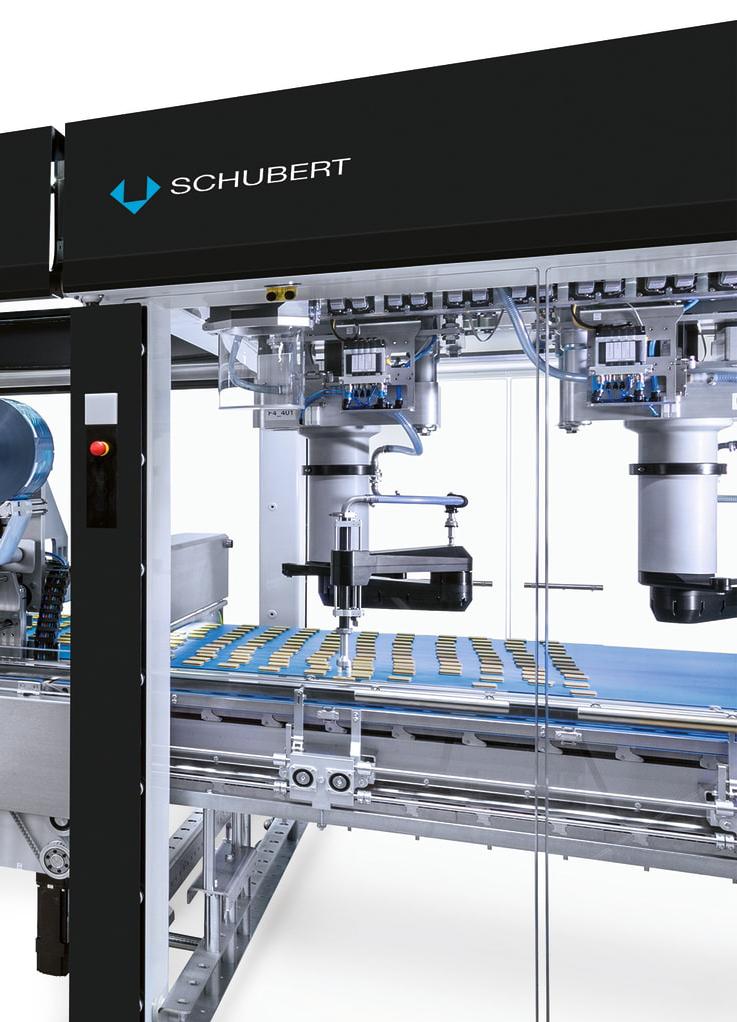
With reduced maintenance processes, pharmaceutical companies already using SUT report quick turnaround and development times and simplified operations. Also, the technology supports the manufacture of more reliable products, eliminating the need to sterilize containers. Equipment running on SUT is easy to set up, taking one or two hours compared to stainless setups which can take a couple of days.
In addition, system maintenance is straightforward, with no need for sterilization validations, annual cleaning, and minimum monitoring. Single-use processes reduce the risk of product cross-contamination, making it easy to maintain a sterilized production environment.
While SUT is a modern technology, its benefits are far-reaching, making it impossible for pharmaceutical companies to ignore.
Automated Shrink Wrapping Provides Precise Outcome
The pharmaceutical industry embraced shrink wrapping to protect drug packaging from tampering. This process was however tedious, particularly when it comes to vertically oriented products which required manual handling to ensure the whole process was effective.
To avoid the added labor and expense from conventional horizontal shrink wrapping systems, manufacturers are now turning to automation.
With automation, multipacks of bottles can be wrapped directly from the fillers with the product standing upright with no need for manual re-orienting of the products before wrapping, which was the case in conventional horizontal wrapping systems. With automation, containers can now go directly from filling to wrapping, and to palletizing and distribution inline, without interruption.
One such system is the 914 Orbital Vertical System (OVS) from Texwrap, which designs and manufactures fully-automatic shrink wrapping systems. The system not only automatically wraps bottles while in vertical positions, but the wrapper trims the film above or underneath the package, where it is hidden from view.
With automation, a multipack of verticallyoriented bottles can be automatically arranged with the labels facing precisely in the same direction while standing upright, before shrink wrapping. Additionally, it has now become possible to cover the barcodes of the individual bottles so that the package can be identified as a multipack and not as individual units.
A Sector On The Rise
Pharma packaging depends primarily on the prevalence of communicable and non- communicable diseases. Although efforts have been made on the disease war front, communicable and non-communicable diseases continue to impact health systems leading to a rise in demand for drugs and extensionappropriate packaging.
The Covid-19 pandemic for instance reminded the globe that we are far away from completely eradicating communicable diseases and put stress on the entire pharma manufacturing industry on a scale never seen before. Non-communicable diseases such as cancer and diabetes also create a huge demand for drugs that need to be packaged in a safe and secure manner.
The global Oncology Cancer Drugs market alone was valued at US$147.2 billion in 2021 and it is expected to hit around US$289.2 billion by 2030 with a CAGR of 8.4% during the forecast period 2022 to 2030. This just shows how much potential lies in the pharma packaging industry and its critical role as an enabler of healthcare delivery.
While the market for pharma packaging is thriving and continues to grow, players in the sector have to continuously adopt new ways of processing to align with the specific needs of the industry while at the same time enhancing the efficiency, safety, and sustainability of their operations
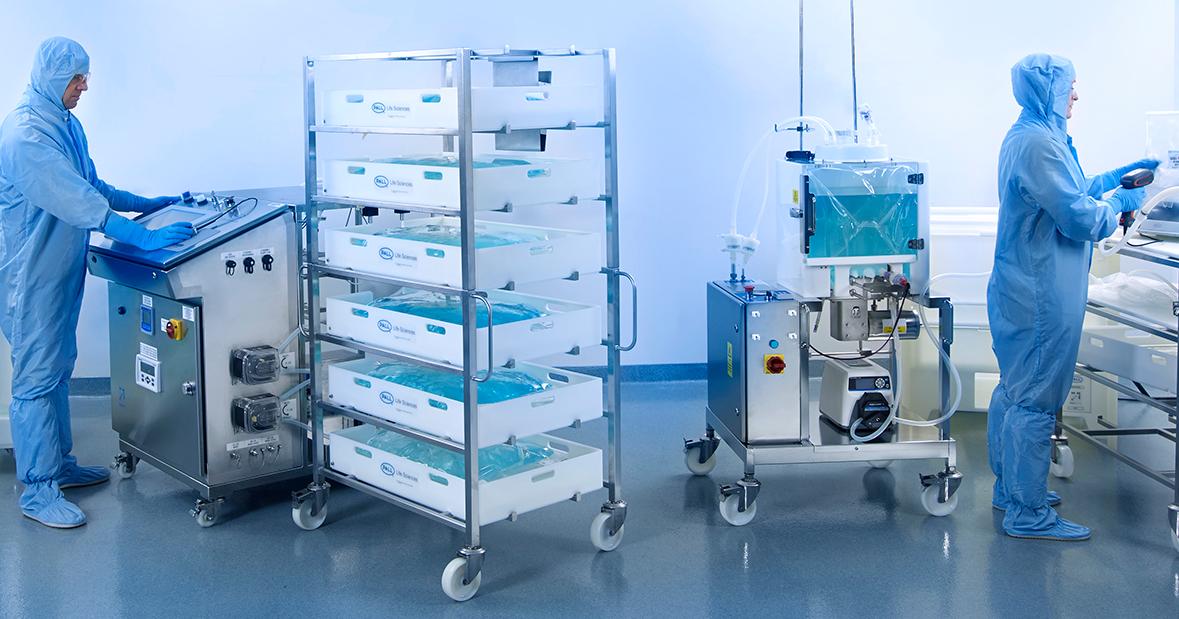