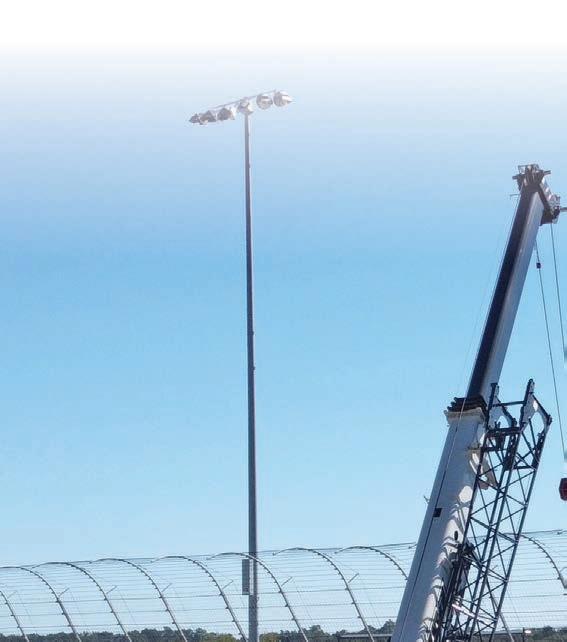
11 minute read
Sunmount Paving customized paving equipment to meet the needs of the new racetrack profile at Atlanta Motor Speedway
Crews Face "Steep" Challenges on AMS REPAVE
Sunmount Paving customized equipment to meet the needs of the new racetrack profile at Atlanta Motor Speedway
Racetrack paving can be some of the most challenging and rewarding projects an asphalt contractor ever works on. Yes, the days are long and the job is tough, but it's worth it to see your hard work on TV as racecars speed around the asphalt you helped put down.
These jobs always come with their own set of tight timelines and tighter tolerances, but Sunmount Paving Company faced an all new level of obstacles on the repave of Atlanta Motor Speedway (AMS) last summer. "The track was last paved in 1997 and the track surface was severely worn and the paving seams were starting to cause large failures prior to events and even during events," Steve Swift, senior vice president of operations and development at Atlanta Motor Speedway says. "The surface was beginning to fail at the paving seams causing large delaminated sections to pull out because of severe wear of the paving seams and water infiltration. We knew it was time for a repave."
Before any work could begin, AMS wanted a clear picture of what their new track
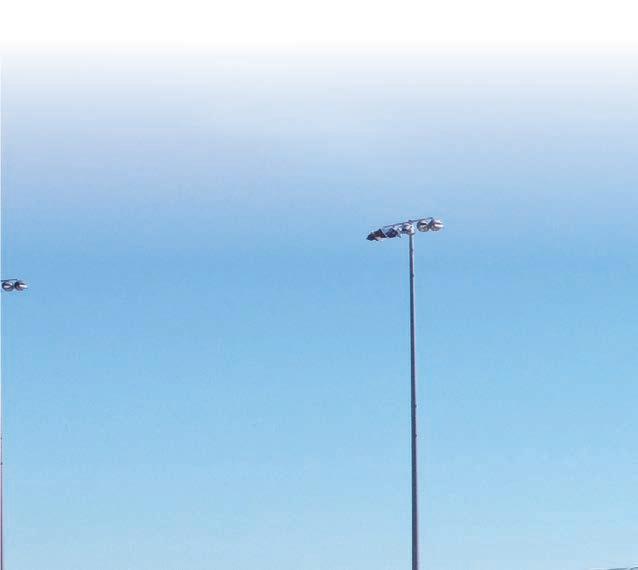
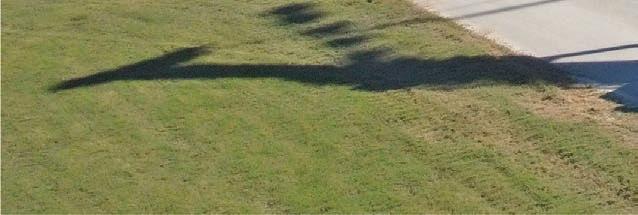
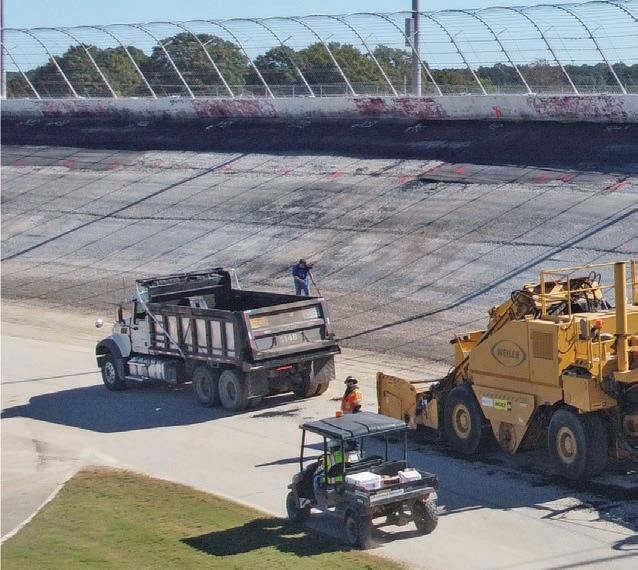
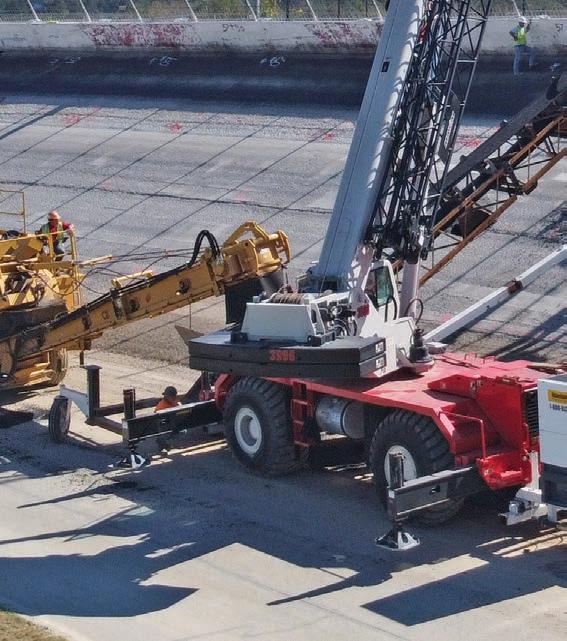
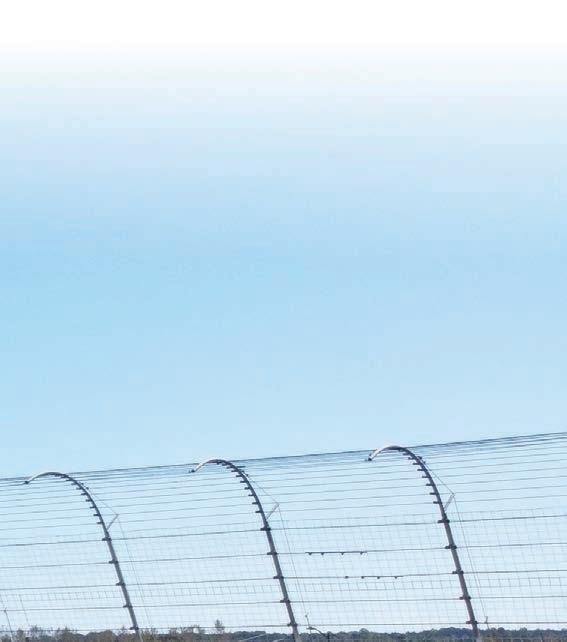
could look like. They worked with a research company, iRacing, for 10 months before deciding on the final profile of the course. "We worked with iRacing to simulate what the new design would produce in racing," Swift says. "In past repaves, we didn’t have the luxury of knowing if the idea we had on track design would produce the racing that we were looking for. Thankfully, in the world today, simulations are as realistic as they have ever been, and iRacing has a huge following and members that race the simulations daily. With their experience and membership, we were able to take advantage of seeing what we were designing prior to the placement of the design. Through the process, we were able to recognize areas that needed to be smoothed out and make for the smoothest ride on the race track. Our initial design did create what we were hoping for in competition on the track and they helped us make some minor changes that took it to the next level."
While the new design, which changed the banking on the turns from 24° to 28°, is sure to thrill racing enthusiasts, it was quite the undertaking for the reconstruction team.
THE RACE IS ON
Sunday, July 11, was the final race on the 24° banked quad-oval configuration of the speedway. Just a few days later, the steel portions of the barriers wrapped around the entire 1.54-mile outer wall had been removed and reconstruction of the track began. Baker’s Construction Services from Bristol, TN was contracted to remove and construct the new profile of the subgrade for the new surface. On Monday, July 19, the first chunks of asphalt were removed from turn 1 of the speedway.
Then they began carving into the embankment in turns 1 and 2 to yield the steeper 28° banking.
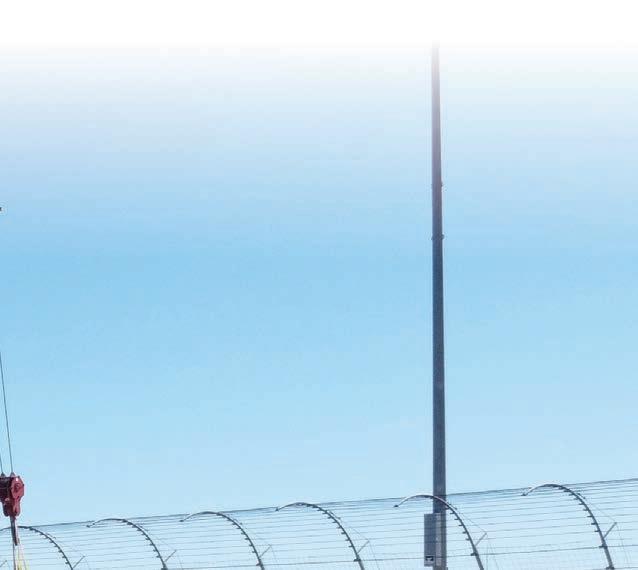
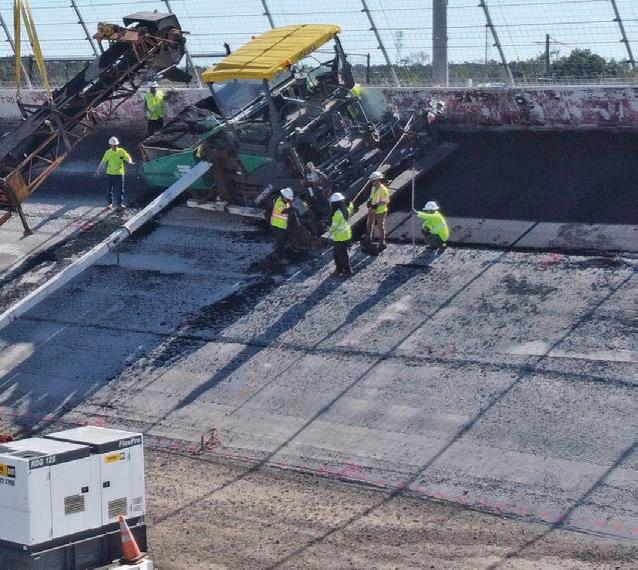
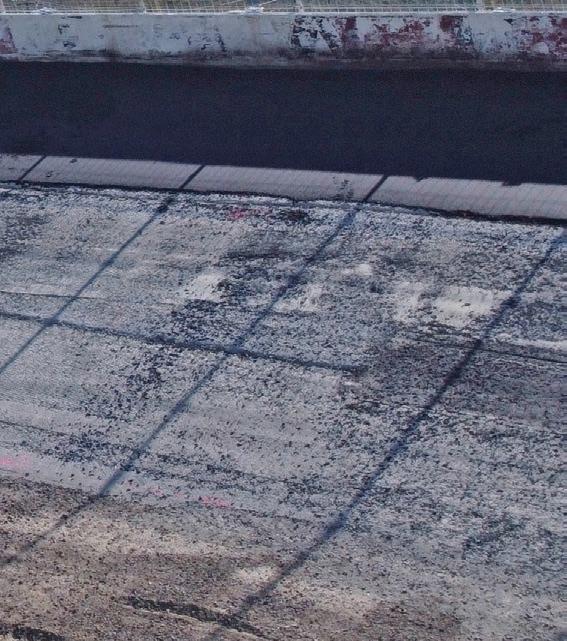
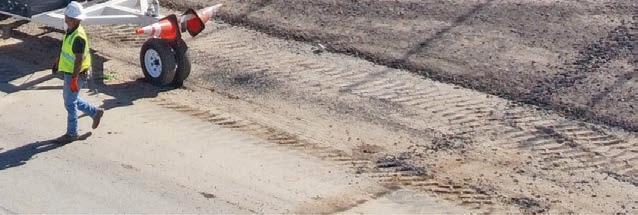
Atlanta Motor Speedway
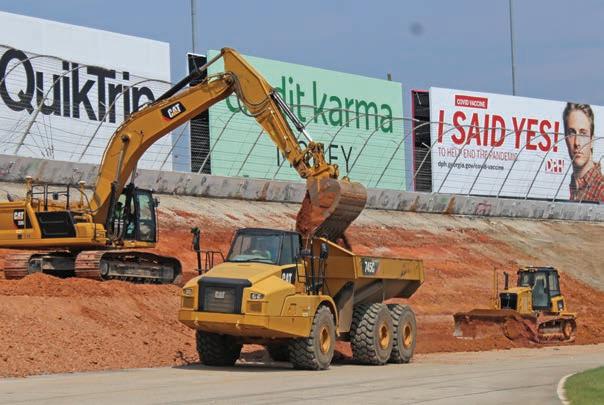
"The new banking on the course will create a more group racing experience for the fans, the cars will not be able to get away from each other and will require drafting to get advantages, thus keeping the cars closer for great competition," Swift says. "This will be the only 28° 1.5 mile race track on the current schedule, or for that matter in the entire United States."
In the process of increasing the banking to 28°, the width of the racing surface in the corners was decreased from 55 feet wide to 40 feet wide.
AMS also took the reconstruction opportunity to improve drainage at the course. To extend the life of Atlanta’s old racing surface, the speedway’s operations department had to work vigorously to limit the amount of moisture below the surface. They installed a new drainage system all around the track and an Open Drainage Layer, or ODL, during the reconstruction. The ODL is a porous layer of asphalt designed to better absorb ground water and lead it to the drainage system, away from the racing surface.
Going forward, AMS has a partner hidden beneath the racing surface removing excess water day after day.
“It’s a large investment for a company to put this (asphalt) in. We want to make sure it lasts as long as it possibly can," Swift says.
PAVING THE BANK
Asphalt paving equipment is designed to be operated on a flat surface. Obviously if you're going to have the equipment work in less than ideal situations, you want to be sure you have experienced partners to help. "Eurovia Atlantic Coast LLC – dba
Crews worked to carve into the embankment in turns 1 and 2 to yield the steeper 28° banking.
Atlanta Motor Speedway
Sunmount Paving Company was, contracted to complete the asphalt paving portion of the project," Swift says. "They were selected to pave the track in February of 2021. There are only two companies in the country that attempt to pave high bank race tracks and Sunmount is the only company that has paved higher than 21°. They are the experts in this difficult paving process and have the want and knowledge to produce a great product and racing surface."


Mix Design Matters
About 20 miles away from Atlanta Motor Speedway, ER Snell’s asphalt plant sits in Stockbridge, GA. After years of prep and tons of material, the company was ready to create the mix for the project.
“Six years ago, we put up some designs for the project, then some of (the speedway’s) engineers came in and pointed out that they wanted a bit of a coarser mix,” Nick Murphy, senior vice president at ER Snell says. “A lot of that stemmed from the desires of the tire manufacturers and there was a lot of talk about the wear on the tires and what they’d expect at race time.”
The mix created was specific to the AMS project. It used a polymer asphalt, 82-22 oil with gradations that are unique to the track.
“This is a high performance paving mix that holds up to the sheer forces exerted by the racing activities that it is subject to,” Steve Swift, senior vice president of operations and development at Atlanta Motor Speedway says. “With the NASCAR cars, you have tires that create a lot of friction on the wearing surface. This product is a little stiffer; it’s going to be little more durable than your typical highway asphalt. There’s a lot behind the scenes research and development that goes into making this product.”
While the stone aggregate for the AMS project comes to ER Snell from a nearby quarry, the liquid asphalt was hauled in from Associated Asphalt’s facility in Savannah, GA. It was all mixed together at the Stockbridge location and transported to AMS.
“They were looking for some things that we don’t encounter on a day-to-day basis so it kind of threw us a curveball, Murphy says. “We were able to make the adjustments they wanted and provide those properties that they were looking for.”
Atlanta Motor Speedway
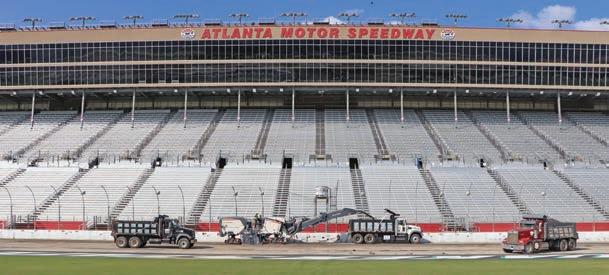
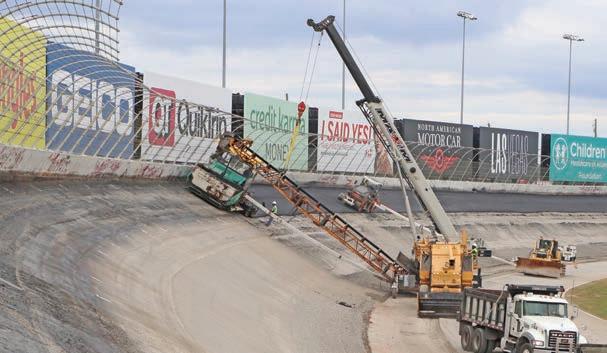
AMS took the reconstruction opportunity to improve drainage at the course. To extend the life of Atlanta’s old racing surface, the speedway’s operations department had to work vigorously to limit the amount of moisture below the surface. They installed a new drainage system all around the track and an Open Drainage Layer, or ODL. The ODL is a porous layer of asphalt is designed to better absorb ground water and lead it to the drainage system, away from the racing surface.
Atlanta Motor Speedway
Paving on the track began in the beginning of October and Sunmount had to custom fabricate solutions that would keep the equipment in place on the high banks. "Typically on this style banking, Sunmount has held the equipment from the top of the race track," Swift says. "Due to the unique structures in the turns of AMS, they were required to hold the machinery from the bottom of the track. With their great engineering and some trial and error, they developed a system to place asphalt on 28° bank."
How do you keep equipment in place when you're at a 28° bank? That required some innovative engineering.
“We fabricated something almost every week to help us and came up with new ways to make it better, make it easier,” John Rauer, division manager for Sunmount Paving Company says.
Over the last 25 years, Rauer has helped pave several racetracks across the country and has experience with the trial and error, quick thinking and adjustments needed on these type of projects.
“For one example, with the hook point on the paver it totally didn’t work,” Rauer says. They used a cranestyle machine with a hook bar to keep the equipment in place and adjustments had to be made for each piece of equipment to keep it steady.
“We had to make some modifications to the equipment because it wasn’t holding the paver up there,” Swift says. “The paver wanted to keep coming down the slope.”
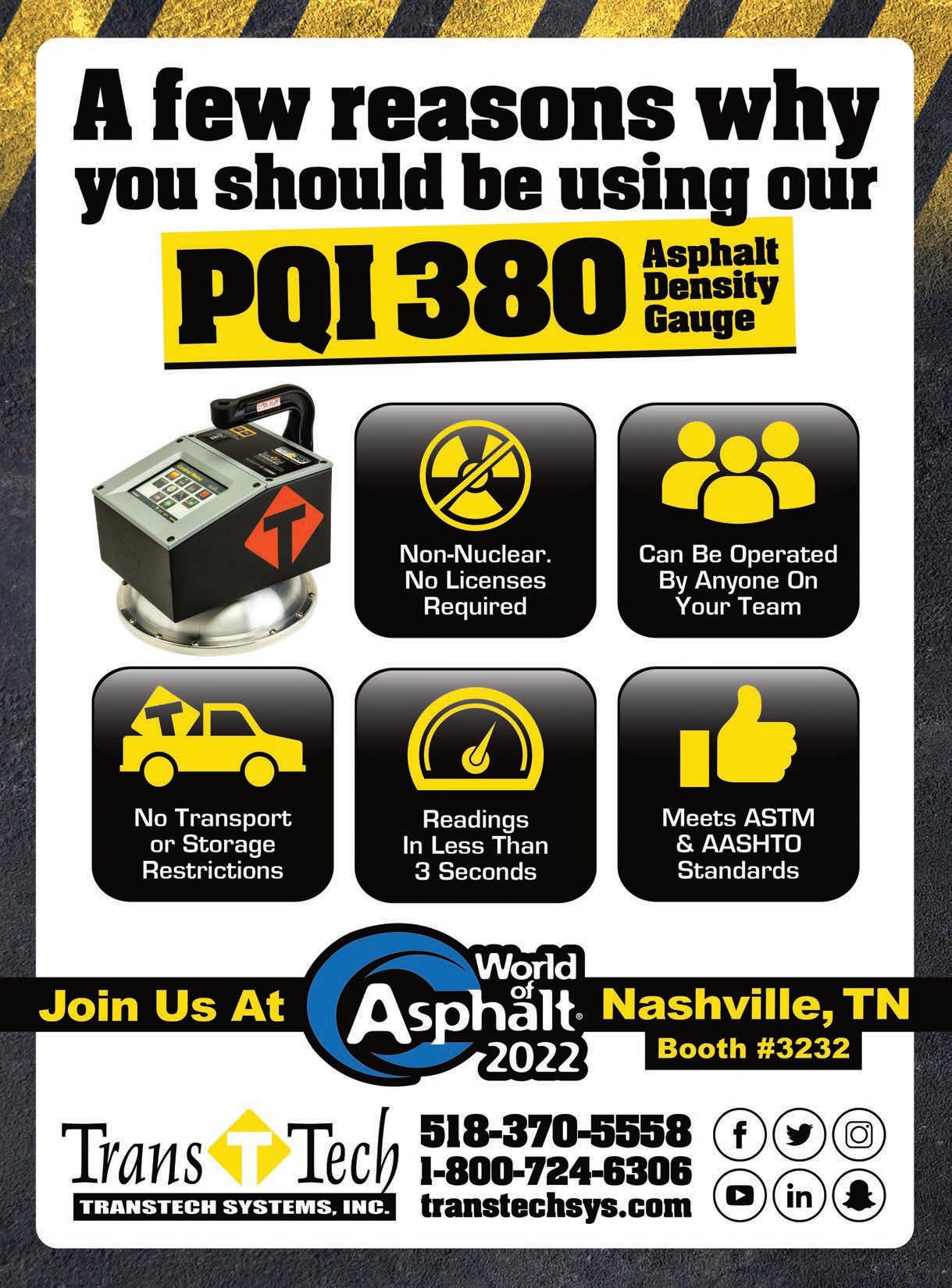
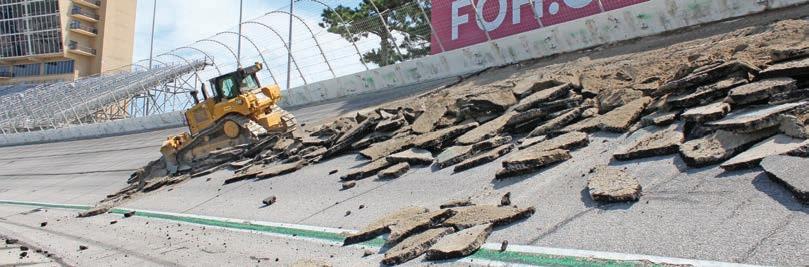
Top photo: Sunday, July 11, was the final race on the 24° banked quad-oval configuration of the speedway. Just a few days later, the steel portions of the barriers wrapped around the entire 1.54-mile outer wall had been removed and reconstruction of the track began. Baker’s Construction Services from Bristol, TN was contracted to remove and construct the new profile of the subgrade for the new surface. On Monday, July 19, the first chunks of asphalt were removed from turn 1 of the speedway.
Bottom photo: In total, about 17,000 tons of material was used to bring the all-new Atlanta Motor Speedway to life. The ODL at 2-in., 1.5-in. leveling course and 2-in. surface mix for a total of 5.5-in. It was a race to the finish to make sure the work was done on time.
Atlanta Motor Speedway

Asphalt Continues to Be Pavement of Choice for Racetracks


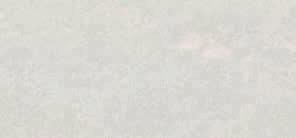
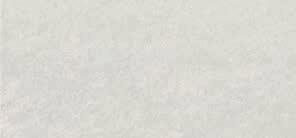
We all know the many advantages of asphalt for our roadways, but racetracks have also historically chosen asphalt over concrete for their surfaces. Of the 88 race tracks listed for the NASCAR Short Track series, 64 are asphalt, 21 are dirt or clay, and only three are concrete.
Atlanta Motor Speedway chose asphalt for their first resurface in almost 25 years for several reasons.
“Asphalt is easier to maintain on a 1.5 mile racing surface,” Steve Swift, senior vice president of operations and development at Atlanta Motor Speedway says. “The track is traditionally asphalt and we didn’t want to change that. The cost difference between asphalt and concrete paving played a key part as well.”
Asphalt pavements provide smooth driving surfaces combined with the excellent traction demanded by professional stock car racing.
“We moved (the hook point) nine inches and that fixed it,” Rauer added. “So it was just a small nine inches that made the difference.”
Segregation on the project was controlled with a feeder belt that kept the paver fed, another proprietary piece of equipment Sunmount developed to pave the high banks.
In total, about 17,000 tons of material was used to bring the all-new Atlanta Motor Speedway to life. The ODL at 2-in., 1.5-in. leveling course and 2-in. surface mix for a total of 5.5in. It was a race to the finish to make sure the work was done on time. "Work had to be completed for a test by end of November 2021," Swift says. "This will allow Goodyear to construct a tire for the Spring 2022 race."
We can't wait to see all the hard work come to life on the course in March,
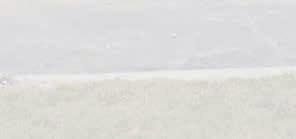
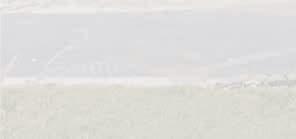
For more information on racetrack paving, visit
ForConstructionPros. com/21119164

