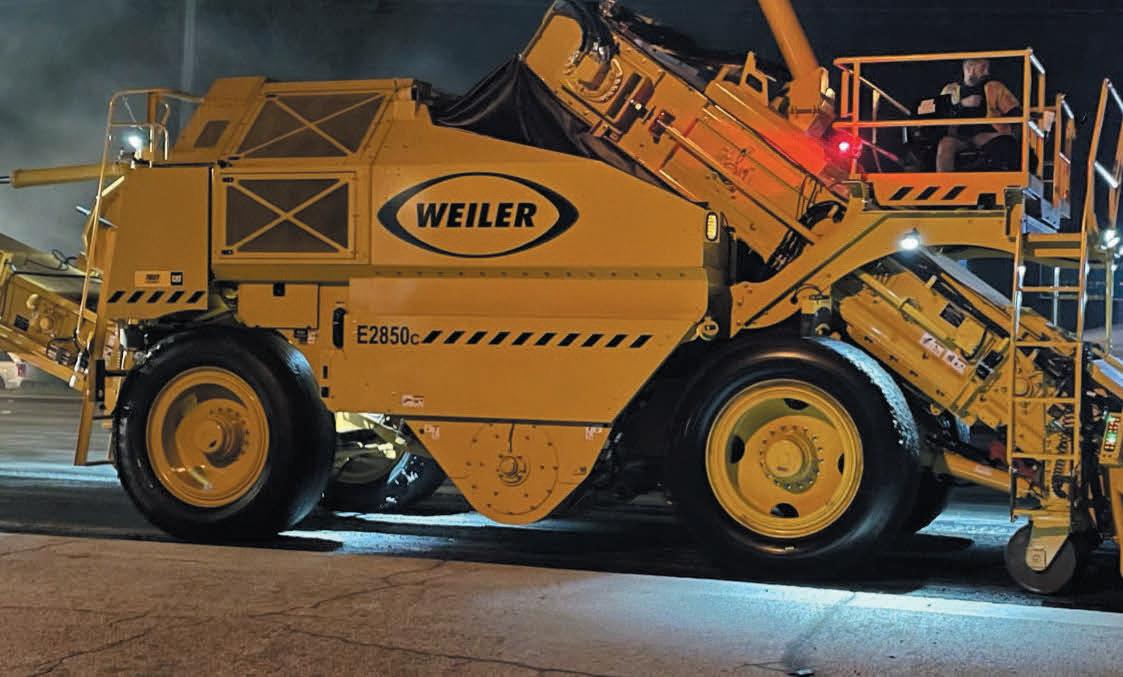
3 minute read
LEADING THE WAY
Weiler Material Transfer Vehicles lead the way with proven innovations to provide the lowest cost per ton of operation.
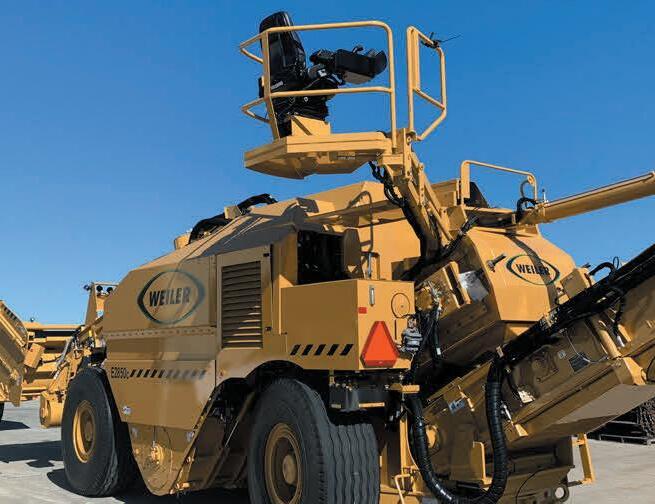
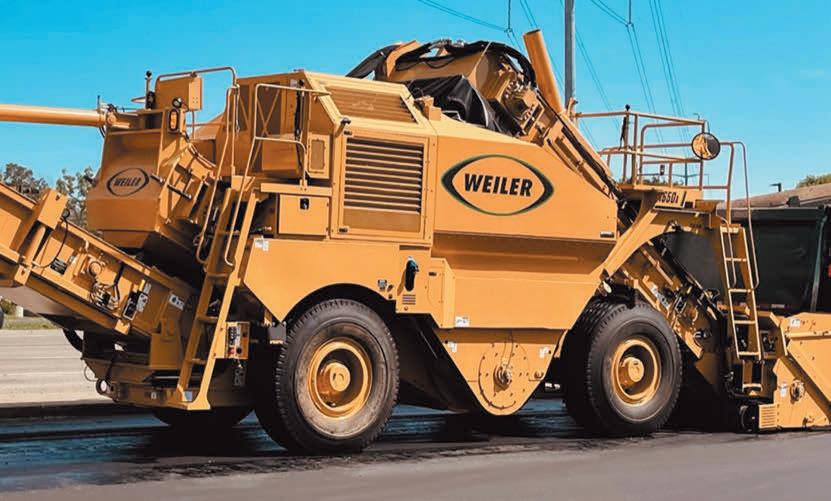
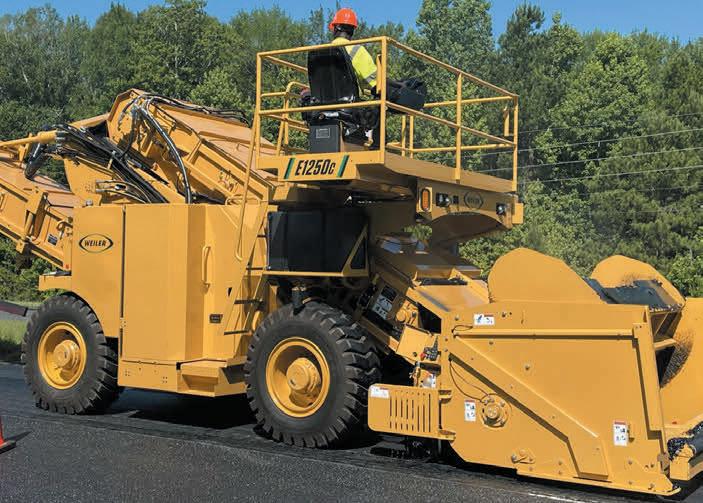
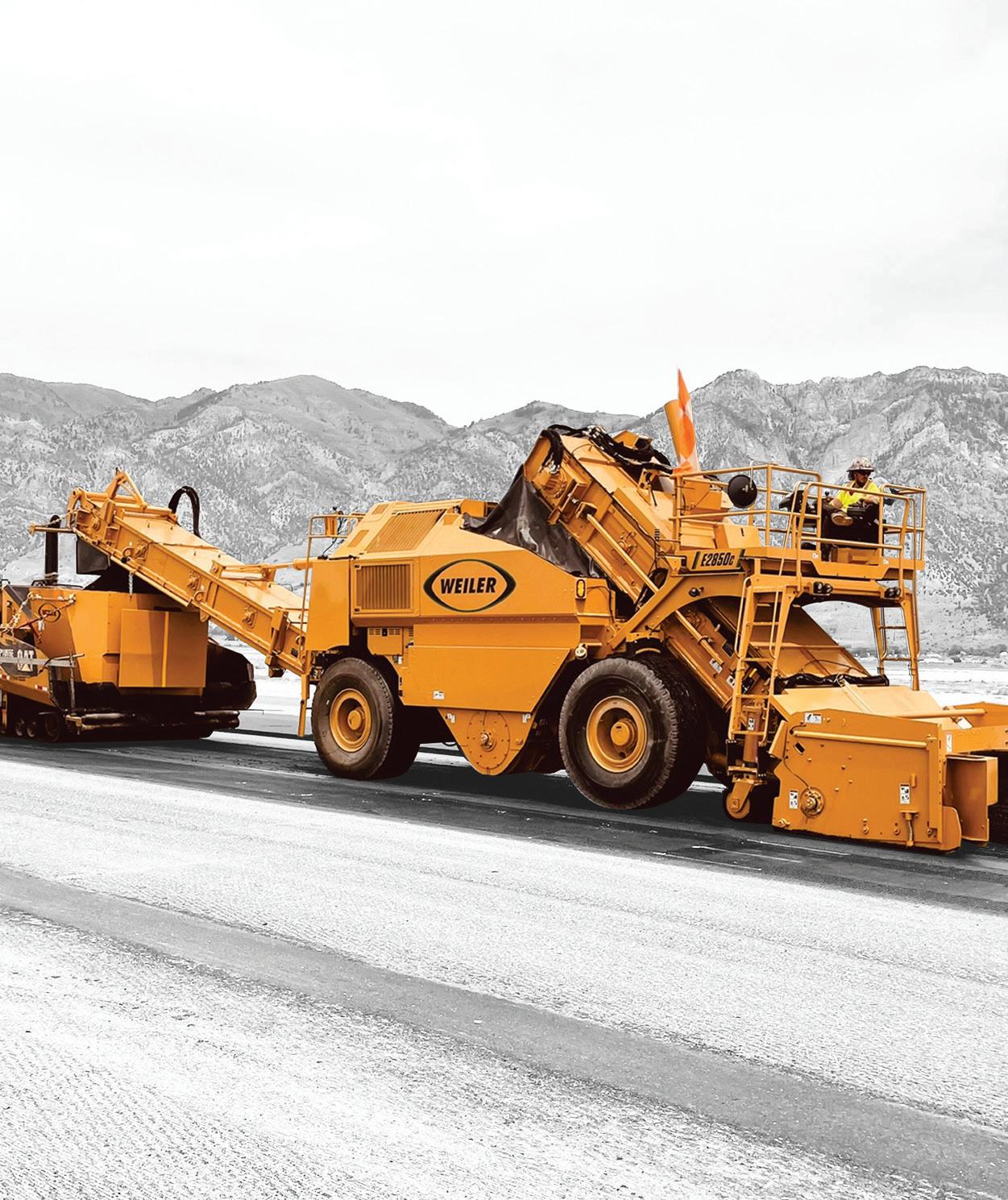
Innovative and reliable operator friendly features such as paver hopper management system with distance to paver, storage hopper management and auto chain tensioning.
Variable speed elevator and conveyors meet production requirements while minimizing wear.
Clam shell doors and full width drop down floors provide unmatched access for cleanout and maintenance.
The multiple, incremental improvements to the 4th generation of chains, sprockets and augers are retrofittable to all machines and provide increased wear life.
“Hydrogen engines solve all of the problems that are associated with battery charging on busy, remote sites, as OEMs work on the internal combustion principle,” said Chris Giorgianni, vice president of government and defense, product and marketing, JCB. “They’ll feel familiar to anyone who is used to diesel or gas engines.” telescopic handlers, to larger, heavier equipment.
Of equal importance, the costs of using hydrogen-powered excavators are roughly the same as utilizing excavators that are powered by traditional engines, which run on fossil fuels. Furthermore, unlike batteries, hydrogen engines aren’t inflationary. And, above all else, hydrogen engines don’t release any carbon dioxide into the atmosphere, as they’re completely carbon neutral.
The company is striving to offer its first hydrogen-powered excavators to customers as soon as possible.
“This commitment reinforces our conviction—as a company—that hydrogen power will be a key part of the solution, in response to climate change’s ongoing threat,” said Giorgianni. “As a result, JCB is looking forward to being firmly at the forefront of the hydrogen revolution.”
MAINTENANCE-FREE ELECTRIC EXCAVATORS QUIETER, CHEAPER
On the other hand, KATO-CES has two models of battery-electric miniexcavators: the 9VXB, which has a 5-foot, 2-inch digging depth, along with a bucket force of 2,360 pounds, and the 17VXB, which has a 7-foot digging depth, as well as a bucket force of 3,687 pounds. Since they each utilize a standard hydraulic system, users can run the same attachments with them as the diesel versions that the company has previously released.
DeHaven added. “This total cost of ownership includes the fuel savings and extended component life of not having an engine, which decreases users’ overall maintenance costs as well.”
ZERO EMISSIONS AND HIGH PERFORMANCE: ELECTRIC EXCAVATORS' SWEET SPOTS
Focused on minimizing its environmental impacts, while also helping its customers achieve the same goals, Bobcat Company is currently leveraging technology to become more productive and utilize resources more efficiently. As an example, the company is now using alternative-energy products that aren’t only environmentally conscious, but also ensure customers can continue their business operations as government mandates are steadily established, regarding zero emissions and clean energy.
“Now that hydrogen-powered excavators are here and proven, global governments need to be encouraged to adopt hydrogen engines and incentivize investment in hydrogen energy infrastructure,” Giorgianni emphasized. “While the benefits of hydrogen power are hopefully clear for everyone to see, it is still a relatively new technology. So, it is crucial that we start to take the lead in getting the message out.”
To help ensure that hydrogen power begins to be viewed as a genuinely viable alternative to electric and battery-powered machinery within the construction industry, JCB is investing $130 million to create super-efficient hydrogen engines for a wide array of machines—from backhoe loaders and
“There is definitely a growing demand and a market for these miniexcavators,” said Bart DeHaven, director of sales, North America, KATO-CES. “The electric units are a little heavier than the diesel units, but they still have the same dig depth. The only drawback is run times, as the diesel miniexcavators can be filled at any time, yet the battery-electric mini-excavators need to be charged for eight to 12 hours to ensure they’ll run for eight hours.”
The battery-electric mini-excavators release fewer emissions, are less noisy and have less vibrations than diesel mini-excavators, thereby improving operators’ comfort, while also reducing their fatigue. Completely maintenancefree, the mini-excavators’ lithium-ion batteries and electric motors have lifespans that are just as long as a diesel engine’s lifetime, if not longer.
“Battery-electric mini-excavators do have higher purchase prices than their diesel equivalents, but the total cost of ownership should be considered when evaluating them too though,”
So far, the company has advanced its commitment to environmental sustainability through the launch of the T7X, which is the world’s first-ever all-electric compact track loader. And it’s also producing a range of battery-electric excavators, as well as a variety of electric products that offer users viable alternatives to diesel-powered equipment.
“While significantly reducing their carbon footprints and producing much less noise than diesel-powered offerings, the battery-electric excavators will also expand users’ jobsite versatility,” said Joel Honeyman, vice president of global innovation, Bobcat Company.
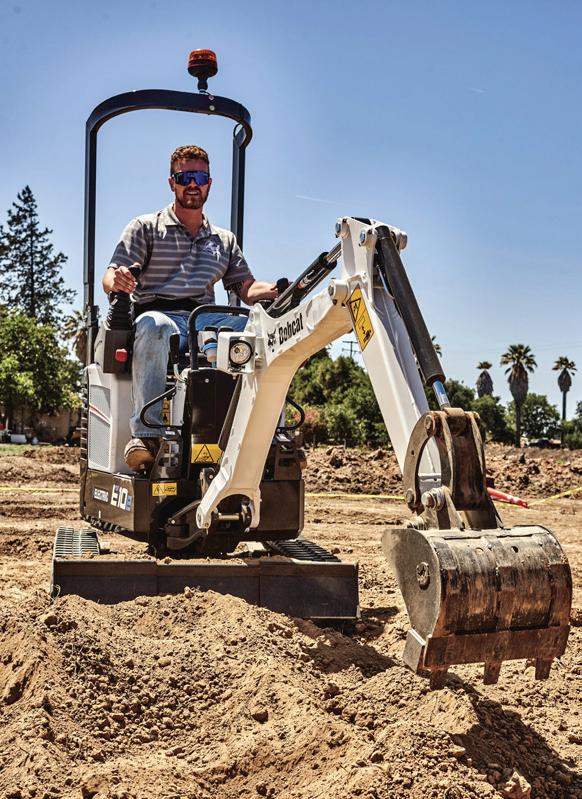
“Producing no emissions, the batteryelectric excavators can tackle tough jobs—outdoors and indoors—as they also require less maintenance than their diesel counterparts.”
The Bobcat Company revealed its latest electric excavator, the E19e compact excavator, which joins the E10e and the E32e as the product lineup’s third member. Each of the battery-electric excavators have compact footprints, quiet operations and zero emissions. Their electrical motors deliver full torque, regardless of rpm, leading to high productivity, on-demand, multifunctioning performance (without any