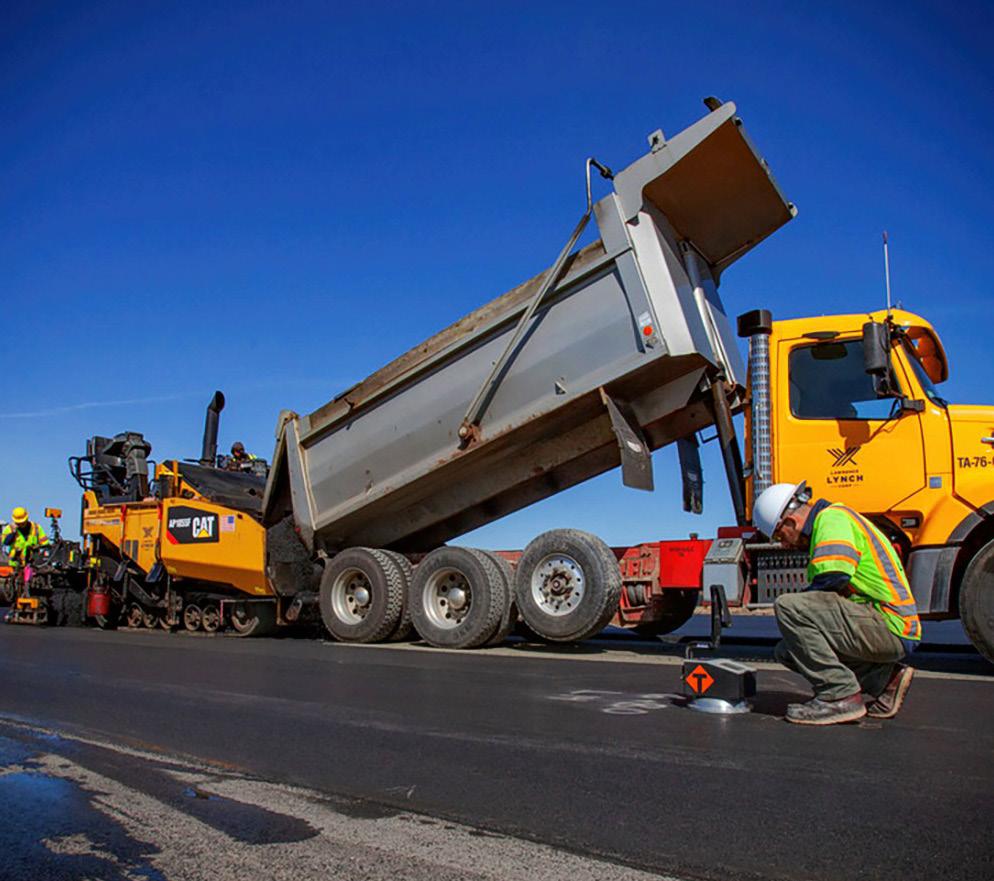
8 minute read
Tech Tools for Measuring Asphalt Density
Non-nuclear asphalt density gauges have many advantages in that they are capable of providing density measurements very quickly and in a completely nondestructive manner, are easy to handle, and are not subject to complicated regulations.
TransTech Systems Inc.
The Tech Tools for Measuring ASPHALT DENSITY
By using the proper equipment to measure asphalt density, contractors can help ensure the success of the roadway and keep record of their efforts
In-place asphalt density is one of the most important measurements used to determine the quality of asphalt when paving a roadway. A small in-place density increase can potentially lead to a significant increase in the service life of asphalt pavements. The industry relies on compaction to increase pavement density and extend pavement life, but what tools are we using to make sure compaction is being done properly?
Quality control on the ground is still paramount to the success of the job. In most states, contractors are paid incentive or disincentive (financial penalties), based on the final, in-place density of asphalt on the roadway. In extreme cases of low density, contractors may be required to remove and replace the new asphalt if it does not meet density specifications. Make sure you're obtaining and tracking these numbers for success with the right tools.
Traditionally, pavement quality was measured by coring the asphalt that is placed and taking those samples back to a lab for evaluation. Not only is that timeconsuming but it also impacts the quality of the pavement. Non-destructive testing (NDT) methods on the other hand offer a good alternative to traditional tests; they reduce coring only for calibration and provide immediate test results.
There are three main types of equipment available to measure density out on the jobsite with a NDT method; nuclear gauges, non-nuclear gauges and ground penetrating radar. There are benefits and limitations to each of these methods and it will be up to your crews comfort level with each technology, and the bid specifications, to determine what you should use.
NUCLEAR ASPHALT DENSITY GAUGES
According to the Environmental Protection Agency (EPA), the use of nuclear gauges is a type of industrial radiography. Radiography is the use of radiation to produce an image on photographic film. This is similar to the way a medical x-ray uses radiation to produce images of bones.
A nuclear density gauge measures the density of in-place hot mix asphalt (HMA) using gamma radiation. Gamma rays are emitted from the source and interact with electrons in the material. By calculating the percentage of gamma rays returned to the source, the gauge can quickly and accurately measure the density and inner structure of the test material.
A nuclear density gauge offers the following key advantages over destructive density measurement (cores): • Portability. One person can easily transport a typical nuclear density gauge. • Quick results. Most nuclear gauges allow both one and four minute readings. These are much quicker than typical densities obtained from cores which could take from several days to several weeks. • Virtually non-destructive. Used in the backscatter mode, the nuclear density gauge is entirely non-destructive. Used in the direct mode, the gauge only requires a small penetration into the finished mat less than 1-in. in diameter and about 2-in. deep.
There are two different modes of testing that a nuclear gauge can perform: Direct Transmission Mode and Backscatter mode.
While in direct transmission mode, the sensor measures the amount of gamma radiation given off by the source rod. The less radiation detected by the sensor the higher the material’s density. This is why it is important to select the correct depth of penetration of the source rod, as a more shallow depth will allow for more radiation to reach the sensor than if it were deeper in the same material.
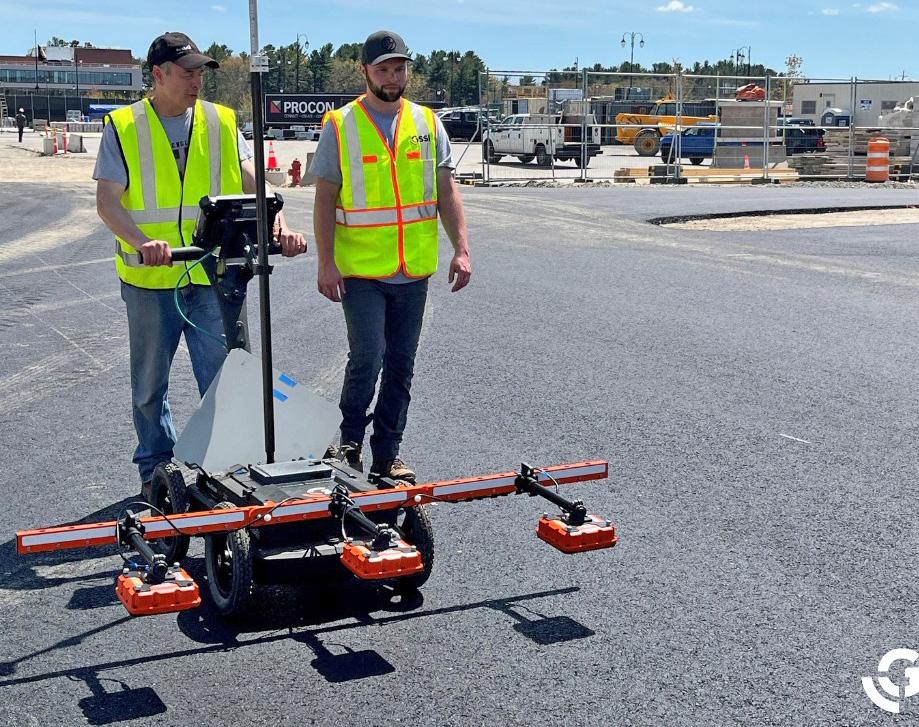
PaveScan RDM is an asphalt density measurement system that provides highly accurate compaction information in real-time. With PaveScan RDM, you can quickly assess the quality of pavement during the paving process, including poor uniformity and significant variations in density. By detecting these problems, PaveScan RDM helps avoid such premature failures as road raveling, cracking and deterioration along joints.
Geophysical Survey Systems, Inc ›
›TECHNOLOGY MATTERS | QUALITY CONTROL SPECIAL REPORT In backscatter mode, the source is in the same plane as the sensor. The shielding within the gauge means that radiation given off the source must first be deflected by the material before reaching the sensor. This means that the more radiation detected by the sensor the higher the material’s density. While these gauges have been widely used in the past, they use radioactive materials that may be hazardous to the health of the user unless proper precautions are taken. Users of this gauge must become familiar with the applicable safety procedures and governmental regulations. Some agencies require the use of personal monitoring devices such as a thermoluminescent dosimeter or film badge. There are also permits and training courses required for operation non-nuclear device is similar or slightly less than a nuclear gauge (depending on the model), but the majority of the savings are generated through the elimination of costs associated with licensing, training and maintenance. Some concerns have been raised around the use of non-nuclear gauges however. Researchers have voiced common themes including 1) insensitivity to actual changes in density, 2) poor correlations with other measures of density, and 3) the need for a better calibration procedure. The current consensus appears to be that while the non-nuclear gauges offer a great number of practical advantages, their results can be affected by a number of factors that may need to be addressed with future models. of this equipment. Effective instructions, together with routine safety procedures such as source leak tests, recording and evaluation of personal monitoring device data, etc., are a recommended part of the operation and storage of this gauge.
NON-NUCLEAR ASPHALT DENSITY GAUGES
Just like nuclear gauges, non-nuclear devices are used in a similar way to measure density - only without the radiation component. With increasing regulations and cost associated with using nuclear source material, non-nuclear density gauges are rising in popularity. Non-nuclear density gauges estimate pavement density by inferring the relative proportion of air-filled voids in the asphalt from a measure of dielectric permittivity. What this means is that these devices operate based on the principles of electrical impedance for a current passing through the HMA material. These devices have many advantages in that they are capable of providing density measurements very quickly and in a completely non-destructive manner, are easy to handle, and are not subject to complicated regulations. In general, the non-nuclear devices have been advertised to provide significant savings as compared to a nuclear gauge. The initial cost of the
GROUND PENETRATING RADAR TO MEASURE ASPHALT DENSITY
Ground penetrating radar (GPR) works by sending a tiny pulse of energy into a material and recording the strength and the time required for the return of any reflected signal. A series of pulses over a single area make up what is called a scan. Reflections are produced whenever the energy pulse enters into a material with different electrical conduction properties or dielectric permittivity from the material it left. The strength, or amplitude, of the reflection is determined by the contrast in the dielectric constants and conductivities of the two materials.
GPR technology has been most successfully used to determine pavement layer thickness, but has also been used to identify subsurface voids, assist with forensic investigations, locate utilities and reinforcement, evaluate degradation of bridge decks and estimate volumetric properties of asphalt pavements.
Recent research has shown that GPR has the capability to conduct a 100% scan of the new pavement and identify density deficiencies. The method also provides significantly more data than traditional density tests and calibrated GPR dielectric values correlate better with core density values than standard nuclear and non-nuclear density gauges.
The collection process can also provide a continuous profile of existing road conditions. GPR can utilize highspeed data collection at speeds up to 50 mph, thus requiring less traffic control and resulting in greater safety when compared to the handheld devices.
Results for these devices have shown a very strong correlation between the GPR-based air void measurements and the laboratory measurements, however there are also limitations with potential interference due to ambient radio noise and antenna variations.
Achieving and measuring asphalt density will continue to be an ongoing quest for perfection. No matter what method of density verification you choose, increased testing of asphalt densities will result in a higher quality pavement, allow the pavement contractors to rapidly verify that the pavement meets the specified density, reduce over-compaction of the pavement and better optimize the paving process.
A nuclear density gauge measures the density of in-place hot mix asphalt (HMA) using gamma radiation. Gamma rays are emitted from the source and interact with electrons in the material. By calculating the percentage of gamma rays returned to the source, the gauge can quickly and accurately measure the density and inner structure of the test material.
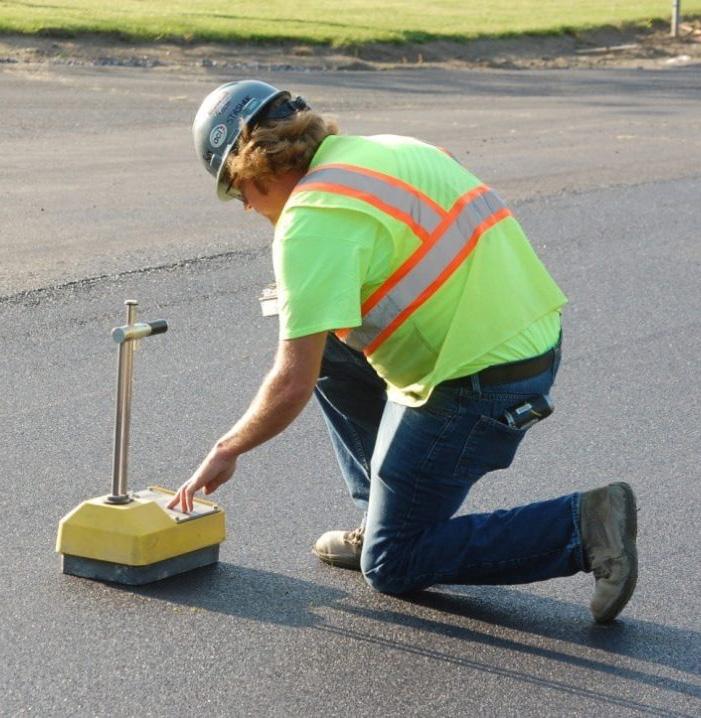
For more information visit
http://asphalt.com/ msfr6p
Engineered Innovation.
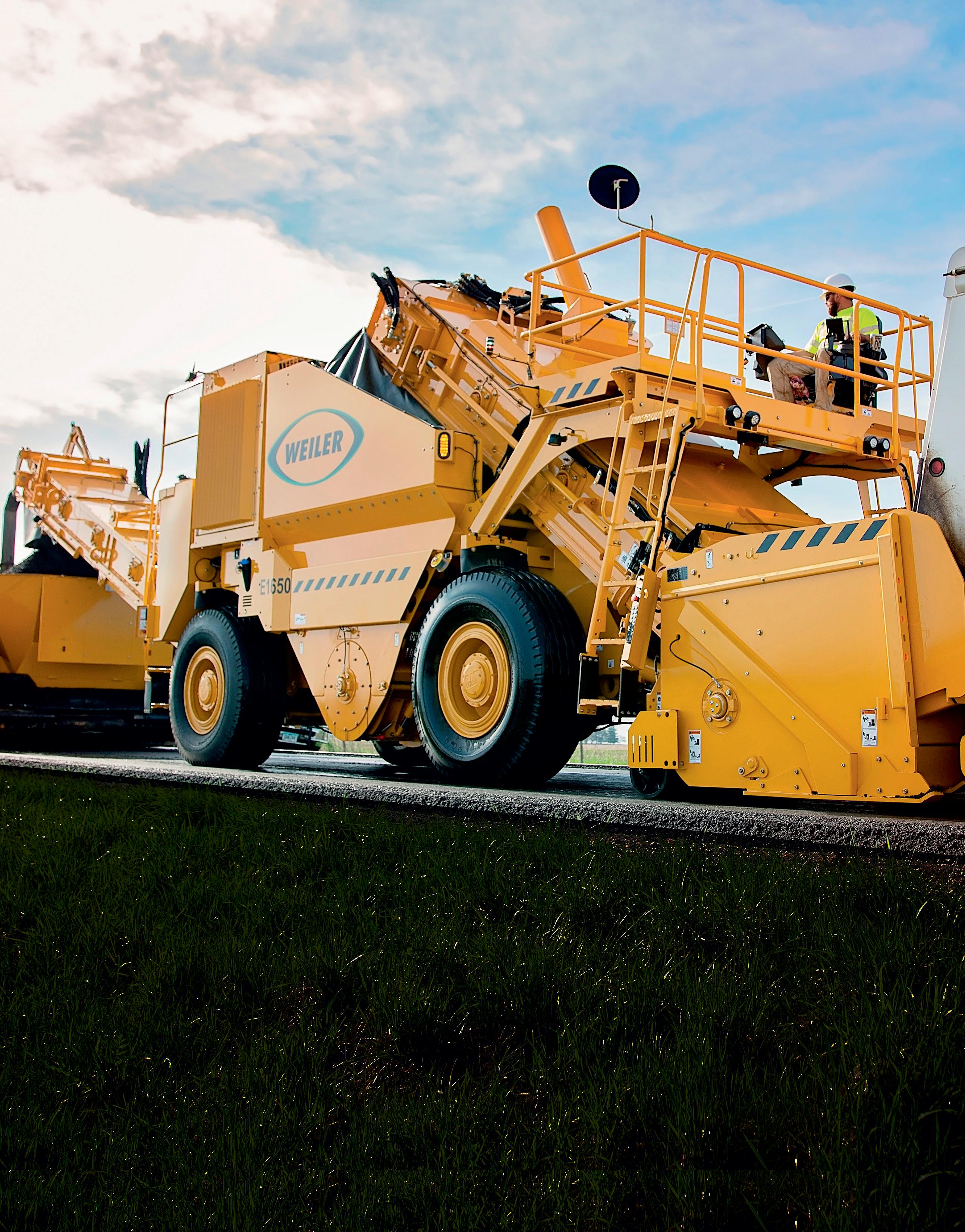
From innovative designs to Caterpillar dealer service and support, Weiler is paving the way to success for contractors across North America. Weiler’s material transfer vehicles, commercial pavers, road wideners, windrow elevators, static split-drum compactors, soil stabilizers, rock drills, tack distributors and front mount screeds are engineered with innovative features to increase productivity while reducing operating costs. Weiler equipment is sold and serviced exclusively at Caterpillar dealers throughout North America.