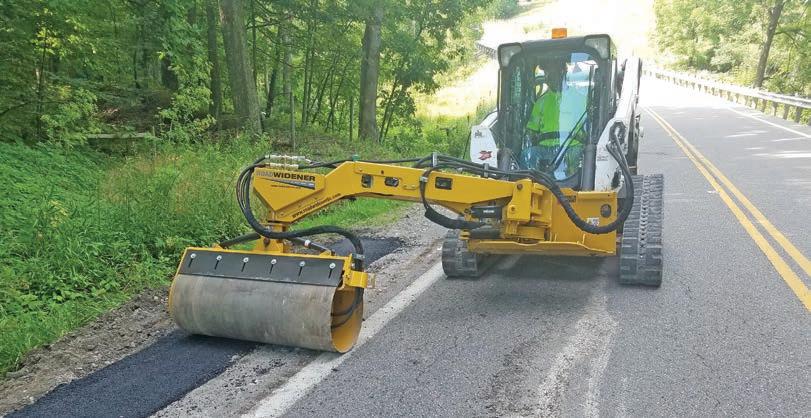
7 minute read
The Safety Benefits of Offset Compaction Rollers
Provided by Road Widener LLC
Improvements to efficiency and safety are worth their weight in gold
There always exists more than one way to get a job done. With so many versatile tools at a contractor's disposal, and more being brought to market every year, it can be daunting just to figure out the best machine for a particular job, and, more importantly, if it will be worth the investment. However, improving jobsite safety is always one of the chief issues worth every dollar spent. Reducing injuries, potential insurance claims, and keeping workers on the job, are paramount.
Offset arm compaction attachments fit neatly into this category of tool. They seem, at first glance, like a niche product, with, perhaps, not enough benefit to justify using them, so we sat down with Lynn Marsh, the president of Road Widener LLC with 20 years of road construction industry experience, to pick their brain, and help draw out what makes these tools so valuable on the jobsite, and primarily, what are ways in which they can offer ben- selim/AdobeStock efits to safety.
From your perspective as a manufacturer in the industry, how would you define some of the most frequent challenges, in terms of safety, when it comes to certain compaction scenarios?
Traditional ride-on compaction equipment is a prime example of a potentially problematic design, especially on uneven or side-sloped surfaces. It is not uncommon for road construction crews to witness a silent rollover, watching their crewmember jump to safety, when the equipment they are operating unexpectedly gives way to gravity while compacting a steep slope. Many ride-on compaction rollers can potentially succumb to rollover accidents due to their rigid design and high center of gravity, which offers little protection or stability for crew members. It's something engineers have taken steps to eliminate.
This far too common jobsite incident is mostly avoidable in the form of an offset compaction attachment that pairs with equipment many contractors already widely own. Offset Vibratory Rollers (OVR) allow crews to safely and effectively compact material from flat ground using the compaction attachment — ensuring a safer work environment at virtually any angle.
What are some other options or features that managers and contractors should take into consideration when looking to improve safety on the job?
Remotecontrolled technology is a newer approach to compaction to offer better safety and efficiency while also reducing labor costs. This is achieved with OVRs by relocating the compaction drum to a remote-controlled offset arm that can be attached to almost any grader, compact track loader, wheel loader or skid steer — immediately solving most operator safety issues. By employing an attachment, the host machine provides a separate source of power for the compaction drum and, thanks to the offset arm, enhances stability and safety.
In its offset position, the drum can pivot up to 30 degrees and reach 30 inches below the mounting point. The host machine can drive safely on flat ground while the attachment arm extends to the furthest, steepest edge of sloping road shoulders and ditches. This allows the roller to easily compact slopes
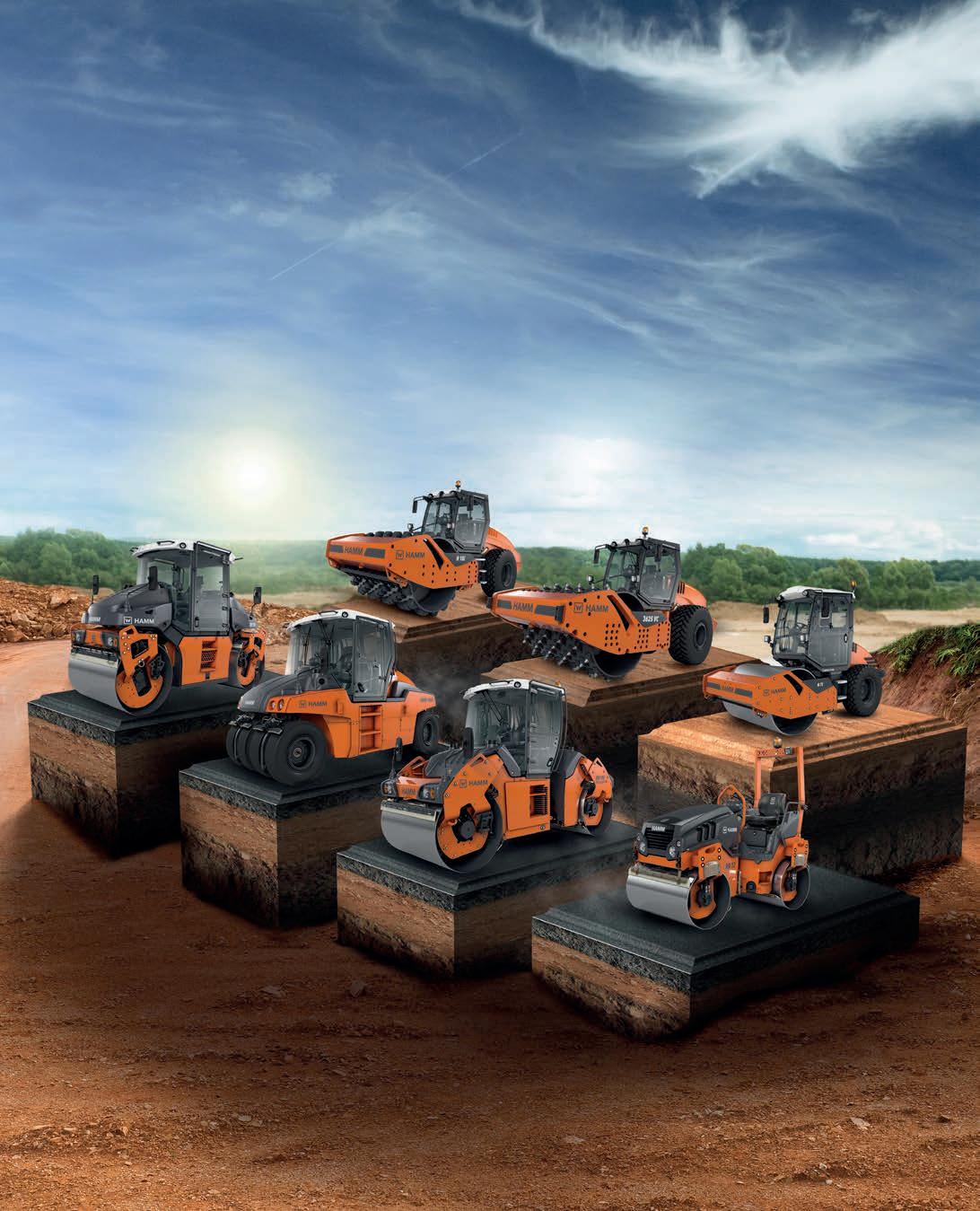
www.wirtgen-group.com
at various angles that would flip a more traditional compaction machine.
The increased safety offered by the offset roller design has other potential benefits like reducing workers comp claims, lowering insurance premiums and enhancing a contractor’s overall safety ratings — all key factors for contractors in a competitive bidding environment where every advantage counts.
What about other uses? In what ways do OVRs or other compaction roller attachments increase general productivity?
Although safety is obviously the top priority on any jobsite, the efficiency and quality of a job, along with equipment versatility, also prove critical. Compaction roller attachments can increase the efficiency and versatility of a contractor’s existing fleet by allowing them to work on a variety of road construction and utility repair projects, all with the equipment they are already familiar with. The attachments effectively compact a range of materials, from gravel, stone, and topsoil — even hot asphalt mix.
With the high infrastructure demand and the current prevalence of a scarce or inexperienced workforce, ease of use — in terms of equipment — is key to a project’s overall efficiency. Some offset compaction attachments incorporate remote controls, combining safety with an intuitive operation that is easy to learn, and allows the operator to adjust the height, angle, extension and compaction adjustments all from the comfort of the host machine’s cab.
Given their obvious differences, is it possible for the offset rollers to provide a comparable level of density to their ride-on counterparts?
Yes, they can. It's situational. While a compaction roller attachment may not achieve density as quickly as a ride-on roller on a flat roadway, it excels in a sloping ditch or trench which places an operator in a hazardous position. Because of the rigid design of traditional compaction rollers, and the stability issues working on a slope, operators tend to drive at a slower rate resulting in a slower compaction times. Alternatively, the offset compaction roller attachment allows an average vibratory density of 106.5 pounds per cubic foot in just one pass on a typical gravel shoulder.
For example, the New Hampshire Department of Transportation (NHDOT) conducted a study to measure the effectiveness of offset compaction roller attachments connected to a wheeled skid steer versus the traditional steel drum and rubber-tired rollers used by NHDOT contractors. The study examined the density of gravel compaction on a road shoulder to determine which method of compaction would yield the most consistent results in terms of gravel density, ensuring a longer wear life of the road shoulder. NHDOT recognized that longer wear life would result in saving thousands of dollars for the state that could be reallocated to other areas to improve infrastructure.
In the past, contractors of the NHDOT primarily used self-propelled rollers in static mode to prevent the risk of rollovers or sliding into ditches. To prove the effectiveness of the study, the self-propelled rollers were utilized in both static and vibratory modes to accurately compare with the offset compaction roller attachment, which was only capable of operating with vibration.
In summary, the offset compaction roller provided a more consistent density of compacted gravel and gave workers added flexibility with its offset arm, eliminating the risk of injury and rollovers compared to other methods. Additionally, the compaction attachment improved efficiency by allowing the operator to remotely control the position of the roller from the host machine, enabling coverage over the entire shoulder as compared to ride-on methods that require straddling the shoulder or not allowing for full compaction coverage.
Besides what we've discussed at-length already, what else would you believe to be important for potential contractors to know about compaction roller attachments in general?
Efficiency is not only seen through the work on the job but also by reduced transportation challenges. The discreet design of compaction attachments allow them to fit on any common trailer along with the host machine — and other primary attachments — and be towed by a standard pickup truck. No heavy-haul trailers or permits are required.
Additionally, compaction roller attachments can be purchased in a variety of interchangeable drum widths, ranging from two to four feet, providing heightened adaptability. To get the same benefit with traditional compaction machines, contractors would have to purchase multiple self-propelled units, all with engines and transmissions that would need to be continuously maintained.
And when it comes to the impact of maintenance, traditional ride-on compaction rollers have several grease fittings that need to be maintained, and they often have a buildup of debris that requires frequent cleaning. Without the need for an engine, powertrain or any associated parts of its own to operate, offset compaction roller attachments require 90% less maintenance than ride-on compaction machines.
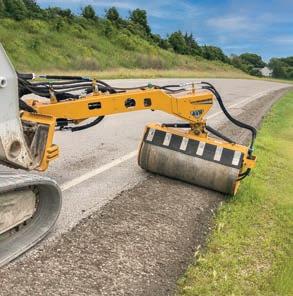
Lynn Marsh who contributed to this article, is the president of Road Widener LLC and has 20 years of experience in the road construction industry.
For more information visit
http://asphalt.com/kk3fi1
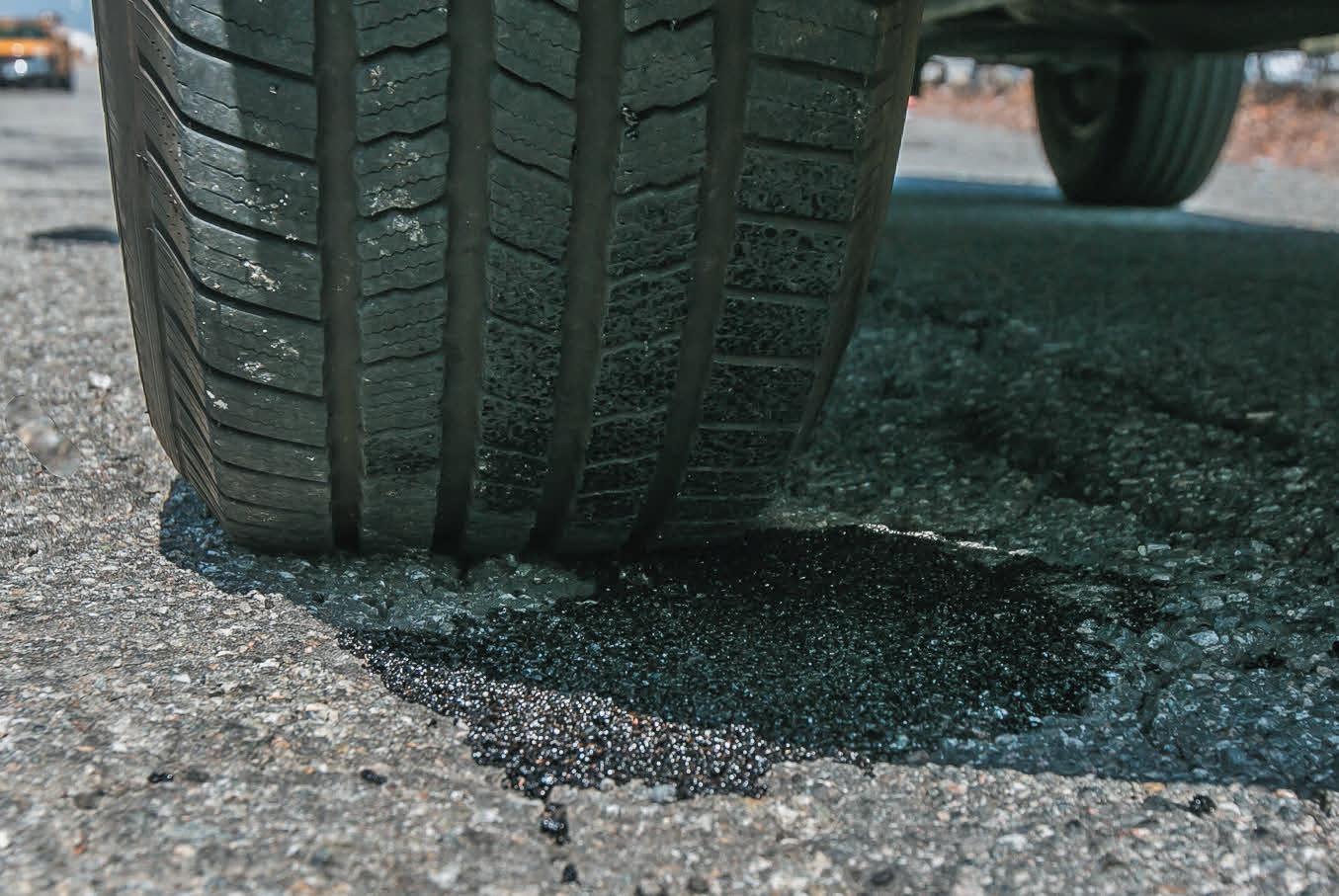
Put An End to Potholes.
Use Crafco HP ER Asphalt Cold Patch and Stop Repairing the same area.
rafco igh erformance sphalt old atch is specially formulated to be e ible, provide a strong bond with the surrounding pavement, and resist raveling and rutting here other cold patch products fail to remain in place, rafco sphalt old atch establishes a rm grip in the repair area n addition to its enduring performance, rafco sphalt old atch is easy to apply o mi ing, heating, or special equipment required and no messy clean-up to deal with when you’re done Crafco HP ER Asphalt Cold Patch can be applied in a wide range of temperatures and climates and opens to traffic immediately