
26 minute read
Product Focus
CONCRETE SAWS & BLADES
Makita XEC01 Cordless Concrete Cutter
The XEC01 cordless 9-in. power cutter features 18V X2 (36V) LXT technology that allows for lower noise, immediate starts and reduced overall maintenance. • Zero emissions enables indoor use • Compact and light weight for reduced strain for wall or above-chest cuts • Integrated water delivery with flow adjustment knob continuously feeds water for OSHA Table 1 compliance
ForConstructionPros.com/21114289
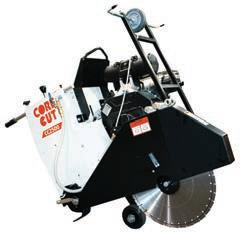
Diamond Products CC2500 Medium Walkbehind Saw
The CC2500 medium walk-behind saw offers 14- to 26-in. blade capacities with a depth of cut ranging from 4 5/8 to 10 3/8 in. • Rigid high-strength 3/16-in. steel box frame with heavy bar reinforcement • Push- or self-propelled drive • Two-position tilt handle bars • Screw feed raise and lower with optional power raise and lower • Cyclone air filter on gas models • Positive gear drive to rear axle via the Eaton hydrostatic transmission
ForConstructionPros.com/21007188

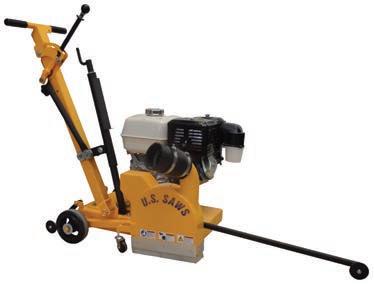
SK-18 Downcut Walk-behind Saw
EDCO's 18-in. SK-18 downcut walk-behind saw is ideal for short-run slab cutting, contraction joints, asphalt patch repairs, and traffic loop installation and trenching. • 18-in. blade capacity • Improved throttle cable • Easy turn crank for lowering and raising blades in and out of cut • Screw boot belt tensioner prevents frame damage • 7-gauge steel blade guard with welded protective segment flap • Heavy-duty lifting bail (optional) • 13-hp gasoline engine • Heavy-duty 7-gauge steel laser cut frame • Large screw-type depth control • Wide-T handles with rubber grips • High quality molded rubber wheels • 3,600 rpm • 6.75-in. cutting depth • 214 lbs.
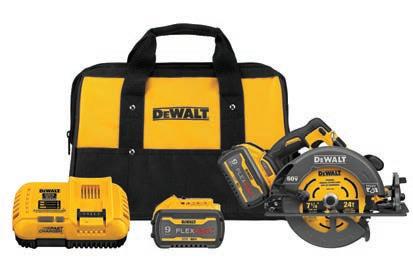
U.S. Saws JS-130 Joint Cleanout Saw
The JS-130 is designed to mill out debris or old joint fill material prior to filling control joints with epoxy or polyurea. • 2 3/4-in. maximum depth of cut with screwdown depth control • Uses an 8- or 10-in. dry diamond blade • Up-cut blade rotation ejects debris into a vacuum port on the blade guard where the dust collector can capture it • Cleans joints at a rate of 20 to 60 fpm • Fully boxed heavy gauge steel frame for extra long life and straight accurate cuts • 13-hp Honda gasoline engine
ForConstructionPros.com/21007218
DeWalt 60V Max Flexvolt Circular Saw
DeWalt upgraded its 60V MAX FLEXVOLT 7-1/4 in. Circular Saw (DCS578) with new motors, software and controls. Other features include: • Available as a kit with a 9.0 Ah battery, compared to the original 6.0 Ah battery • Up to 47% more powerful than its predecessor • Maximum bevel capacity of 57 degrees with bevel stops at 22.5 degrees and 45 degrees • Electric brake stops the blade after the trigger is released • Integrated LED for increased visibility and cut accuracy • Uses a 7-1/4 in. circular saw blade and features a maximum cut depth of 2-9/16 in. at a 90-degree bevel • Integrated rafter hook for quick and easy storage
ForConstructionPros.com/ 21132297
SKILSAW Walk-behind MEDUSAW
The 7-in. model SPT79A-10 MEDUSAW walk-behind saw incorporates a Dual-Field worm drive motor with added overload protection. • Adjustable arm extends to the user’s height and folds and locks into place for transporting and storage • Large handle with a ambidextrous side assist handle and two-fi nger trigger provide greater control when making long cuts • Includes an improved pointer for stronger support and a larger wheel for greater visibility • Features a large foot and oversized wheels for stability • Integrated dust control in both wet and dry operation
ForConstructionPros.com/20986024
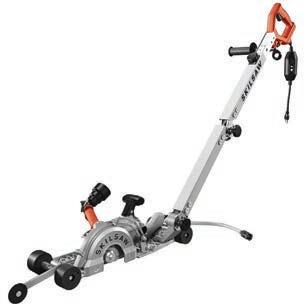
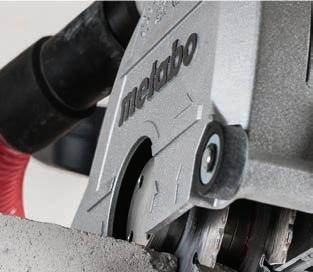
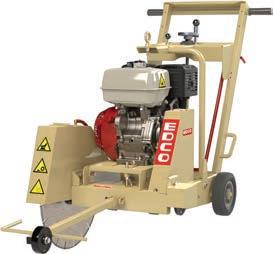
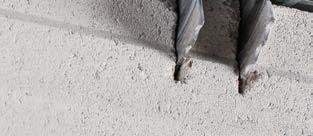
Metabo’s High Powered Masonry Chaser
Metabo’s High Powered Masonry Chaser MFE 40 has a 15 amp motor and a no-load speed of 5,000 rpm derived from its planetary double gear reduction, which makes it easy to cut into concrete, brick, block (up to 1 9/16 in. deep and 3/8 to 1 3/8 in. wide) for the installation of wiring, conduit, or pipe or laying in reinforcing materials. Dust-free work is achieved by the die-cast aluminum cover with 1-1/4-in. vacuum connection. The wall chaser includes the soft start feature, which allows for smooth start-up and restart protection. This prevents the tool from starting on its own in the event of a power interruption. It also includes an LED light that signals if the tool is in danger of overloading. Heavy-duty rollers enable easy guidance, and the rear D-handle and front loop handle are ergonomically designed for best control. The tool includes two 5 by .08 in. diamond cutting wheels, which can be spaced at widths from 3/8 to 1 1/8 in. wide and can be adjusted to cut from 3/8 to 1 9/16 in. deep. The parallel cuts can then be chipped out using a chipping hammer to create a finished slot in concrete for embedment. Metabo has two accessory diamond cutters that slot in one pass, either 3/4 in. wide or 1 3/16 in. wide.
ForConstructionPros.com/21172250
EDCO DS-20 Downcut Walk-behind Saw
In developing the DS-20 concrete/asphalt saw, EDCO took its proven 18-in. walk-behind saw's design and added the ability to use a 20-in. blade, allowing users to cut 7 3/4-in. deep without the need for a larger self-propelled unit. A 13-hp Honda GX390 gasoline engine with heavy-duty anti-vibration mount provides consistent, reliable power. The throttle system features a positive locking mechanism to ensure wide open throttle when engaged during sawing applications. The unit comes with a 7-gauge steel blade guard with welded protective segment flap and an easy turn crank for lowering and raising the blade in and out of cut. It includes a heavy-duty 7-gauge steel laser cut frame, large screw-type depth control, wide-T handles with rubber grips and solid-steel lifting handles. • 13-hp gasoline engine or available as the three-phase, 230V DS-20E with a 7.5-hp electric option • DS-20 generates 3,600 rpm and DS-20E produces 2,880 rpm • Easy turn crank for lowering and raising blades in and out of cut • Large screw-type depth control • Includes an improved throttle cable, heavy-duty anti-Vibration engine mount, screw boot belt tensioner to prevent frame damage and heavy-duty lifting bail for easy loading and unloading • High-quality molded rubber wheels
ForConstructionPros.com/21111934
Milwaukee Tool MX FUEL 14-in. Cut-Off Saw
The lithium ion battery-powered MX Fuel 14-in. cut-off saw (MXF314-1XC) offers fast cuts from start to finish with quick and easy push-button activation.
• Provides the same cut speed as most two-cycle gas saws and a full 14-in. blade capacity to cut more in a single pass • 5-in. cut depth • Up to 50% less noise and reduced vibration for a smoother cut • ONE-KEY compatibility provides ability to track the saw with community tracking and alerts, complete inventory management and smart equipment technology
ForConstructionPros.com/21131552

Husqvarna FS 7000 D Concrete Saw
The FS 7000 D diesel walk-behind flat saw comes with a low-emissions, Tier 4-compliant engine. • Designed for concrete and asphalt cutting up to 17 1/2 in. deep • High output, compact size and good maneuverability provides versatility for mid-sized road work, service work and smaller jobs that require high production rates • Intuitive and ergonomic digital control panel
ForConstructionPros.com/21134492
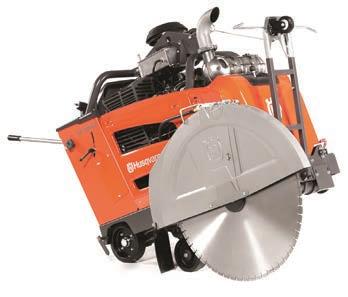
7Questions on COLORS & STAINS
Isat down with John Reynolds, director of technical services at Solomon Colors to talk about the difference between acid- and water-based stains, common problems, and get some advice on applying stains to a slab.
Q. Does one type offer benefits over the other?
A. Water-based stains are nonreactive products. They’re more popular than acid stains in some scenarios and in other scenarios they’re not. They offer some versatility that acid stains can’t achieve like a wider variety of colors. Acid stains are limited to rust and browns (really dark browns) and then blues and greens because of the chemical nature of the stain. Water-based stains, being iron oxide pigment, have a much wider variety of color selection possibilities. Although they’re versatile, [water-based stains] can be finicky, because surface preparation is much more important with them because they have to absorb into a slab.
Acid stains are chemically reactive and basically made of hydrochloric acid, blends of metallic salts, and water. Once the hydrochloric acid breaks through the tight cream at the surface of the concrete, the metallic salts get in and react chemically with the free lime at the surface of the concrete. We’re not depositing pigment, we’re creating a chemical change… so an acid stain is only as effective as the slab’s ability to react. If you have an old slab that has a lot of sand and aggregates exposed through age—your reactivity is minimal. But, because it’s a reactive stain you have a limited selection of colors. There are only so many colors that these metallic salts can create.
That said, you’ve got limitations because greens and blues can’t be used outside. There’s a copper content in them that turn black when they come in contact with moisture.
Q.What’s the most common issue contractors run into?
A. The biggest issues that I've found over the years are surface preparation. Because a power troweled floor that's really tightly troweled is not going to allow an acid stain to get in and chemically react. [The troweling] acts as a sealer. It seals off that slab and doesn't allow the stain to get in to react. It’s the same with a water-based stain. If I have a super slick surface, I've got no way for that pigment to get in and bond. Say I clean a floor really well. I got a floor squeaky clean, but it's super tight and it's slick. I can spray on an acid stain, come back and completely wash it off. It'll look like it was never stained. Because there was no way for those salts to get in and react the way they're supposed to. Same way with a water based.
I've had jobs where the contractor did no surface preparation to open up the slab to be able to get that material to something to bond to. Surface preparation is probably the number one problem. The second biggest problem is with acid stain: neutralization and residue removal. Q. Any advice on application? A. There’s no pigment in [acid stain] at all—it’s totally dependent upon that slab. If you look at any manufacturer’s literature, regarding acid stain, it’s going to tell you to do a mock-up, because we don’t know how that slab is going to react to the metallic salts in the stain.
I’ve done basement floors in acid stains and I always go into the utility room or bedroom where they’re going to put carpet or something like that. I’ll put down samples for the people—that way they can see how their slab is going to react with the color that they like.
There’s surface preparation. There’s staying application. There’s residue removal process. And then there’s a sealer. All four of these things are going to change and alter the way [how the result] looks.
Without getting into a whole dissertation on surface preparation, you have to open up a slab to allow it to stick. So…we open it up with the intention of getting a chemical as well as a mechanical bond on the top of the concrete. I always tell people with acid stains, you have to prepare the surface for the sealer. Whatever sealer you're using, look in their tech data. Look and see what the surface preparation requirements are.
When I teach people about acid stain, I'm always emphasizing prep for your sealer. That said, that preparation for your sealer can alter the way the stain reacts. That's why I always recommend mockups or test samples, so that you can say, “Okay, if I'm going to sand this floor, clean it and scrub it…if I'm going to use an etching product to get a profile on the slab, that's going to alter the way my stain looks as well.” [You] got to figure all that stuff out before [you] cover up 1,000 square feet of a basement floor with acid stain.
It's not rocket science, but there's a degree of being careful. If you follow the rules, acid stains can give you beautiful, long-lasting floors. If you don't follow the rules, you can have trouble.
Generally speaking, we want to spray an acid stain down with an acid-resistant sprayer, so that you get a nice even distribution of the stain and avoid an overlap mark. As soon as that acid stain hits the concrete, it's chemically reacting. So, if I roll across a slab, and then I come back and I start rolling again, I'm going to have a line because it's reacting longer where the overlap mark is. It's doing a more intense reaction in those spots. You'll end up with this slab that
looks like a roller marked mess. That's why we spray and we overlap and create a nice natural modeling with the application to a sprayer. Q. What about clean up? A. Once that stain chemically reacts for a minimum of four to six hours—typically, you'll leave an acid stain overnight—it brings salts to the surface. All of these salts are like a powdery residue. This is where homeowners typically freak out, “What did you do to my concrete slab?” All of this stuff comes up to the surface. Get a scrubber or [my preference] some sort of mechanical agitation of these salts so that they loosen from the surface and rinse them off.
I'll run a floor scrubber if I'm on an exterior slab with a nylon bristle brush attachment. If I'm on an interior slab, it'll be a floor scrubber with a red pad on it. You have to neutralize the slab because you're making it acidic with this muriatic acid that's in there. Neutralize it. Scrub it. Rinse it. Scrub it again and rinse it. I typically do three scrubs. The first one to neutralize and get the bulk of the acid and/or the residue off. Then, I'll do a clean water rinse. And I'll do a final clean water rinse so that I'm sure that I've got all of this residue off because if I don't have the residue off…it's going to force your sealer off the slab. Your surface preparation is important, your application technique is important, your cleaning, neutralizing residue removal process is important. And then allowing everything to dry and getting that sealer on there. All four of these things will contribute to a successful acid stain.
A lot of people will go in and mop a floor or they'll let it sit for a while and they'll just mop it—maybe throw some water on it, mop it up real quick and think they're ready for sealer. You really have to aggressively remove those salts, that residue, that comes up to the surface
Q. Does this process differ with water stain?
A. Over to water-based stain. It's extremely important to have an open slab because we're dealing with micronized iron oxide pigment. That pigment must have a place to go and grab on to. Some water-based stains have an acrylic additive in them, some don't. Either way, you must have a nice open slab for the product to get in there and cling. For example, the windshield of a car. I can spray a water-based stain on a windshield of a car and you're going to be able to wash it off because there's nothing for it to stick to. If we sandblast the windshield, and then apply the water-based stain and let it dry, then it's going to be a real bugger to get off because it's got something to stick to. Cleaning and profiling is very important with water-based stains.
Then it becomes an application technique. Typically you don't want to go over a dry surface with water-based stains because they can flash dry and you'll end up with unsightly overlap marks. By dampening the slab surface saturated-dry, (the surface is saturated with water but there's no ponding) it doesn't flash dry. [The water-based stain] has a chance to slowly penetrate into the pores of the slab.
There are two things we're looking for with water-based stain: profiling for the sealer. Whatever sealer we're putting down we want to read the tech datasheet first and figure out what it requires. The other thing is we need an open slab so that that water stain can get in and cling to the pores of the concrete without putting a layer of pigment or dust. Because once the carrier the water evaporates, you're left with iron oxide pigment, we want a nice even distribution of that pigment. We don't want concentrations of it because that's going to form that dust on the surface and going to cause the sealer to fail.
Once the water-based stain is dry, you're ready for the sealer. You don't have to clean it, you don't have to neutralize it, scrub it, or anything like that. There's advantages: many different colors and no cleaning or washing of the slab compared to acid stain.
Q. Since acid stains are limited in their color pallet, could you accent with a water stain? What if your client wants a black color?
A. You're basically doing everything with the acid stain up until the point that you're going to see. Because you can't get a true black with an acid stain due to the metallic salts, if somebody wants a really dark floor, close to black without being completely black, you can take a black water-based stain. Go through the acidstain prep, apply the stain, let it set, do all the cleaning residue removal. Once you’re basically ready for sealer, then you can take your black stain and apply that and give it the look that you're after by enhancing the color that's down on the floor already. So, whether it's a dye or a water-based stain, it's the last thing that you're going to do to the slab when you're accenting an acid stain.
Typically, what I tell people on acid staining if you're going to do artistic work, get really familiar with how these stains react. Because blues are going to react completely different than a rusty color; it's important to be familiar with that.
I typically don't mix colors together on acid stains. I never mix different colors together. Like I won't take our Mission Brown and mix it with our Mahogany. I just won't do that. But, on the water-based stain, I'll take our Ebony and our Walnut and mix them together to create a really dark brown…it'll work because it's pigment. It's non-reactive.
Q. Will admixtures affect the color at all?
A. With acid stains, yes. With waterbased stains, no - your water-based stain is going to be what it is. Now, if you have a lot of different admixtures in concrete, you can alter the color of an acid stain. Or if you have different cement contents. If I have a 7-sack mix compared to a 5-sack mix, I'm going to have a different color with an acid stain. With a waterbased stain, it might be a little darker because there's more Portland cement in there that will darken when my sealer darkens everything, but you're still going to have that same general color.
Editor’s Note: More from Solomon Colors can be found at ForConstructionPros. com/10074663.
For more information on colors and stains, visit ForConstructionPros.
com/concrete/decorative/ colors-stains.
A Vision of the Long Road Ahead
David Howard takes position as the 2021 Chair of the American Concrete Pavement Association
Following the trend of virtual meetings and Zoom calls, the American Concrete Pavement Association (ACPA) had its 57th Annual Meeting online. Amidst an interchange of mute buttons and cameras, on Dec. 3, a white gavel was passed to David Howard, the president and CEO of Kansas-based Koss Construction Co., to mark the start of his new role as the new ACPA Chair of the Board. Howard took over from the previous Chair, James Mack, P.E, Director of Market Development – Infrastructure with CEMEX.
As a volunteer position, the chair supports and sustains the work of the association and provides governance leadership and strategic support. This is a seat three years in the making; while nominated to the position, one sits as 2nd Vice-Chair and 3rd Vice Chair prior to appointment. This assures a smooth transition each year as the gavel passes from one to the next.
The Board Chair sits as a partner to other board members, the president, and CEO, and communicates with the president and CEO regularly. Responsibilities include presiding over board meetings, leadership on issues, and plans being pursued by the association.
David Howard, CEO of Koss Construction
Images courtesy of Koss Construction
The seat also serves as the ambassador of the association by interacting with members, the network of chapters, research and technology partners, and public officials. Research and technology partners include the National Center for Concrete (National CP Tech Center) at Iowa State University, the International
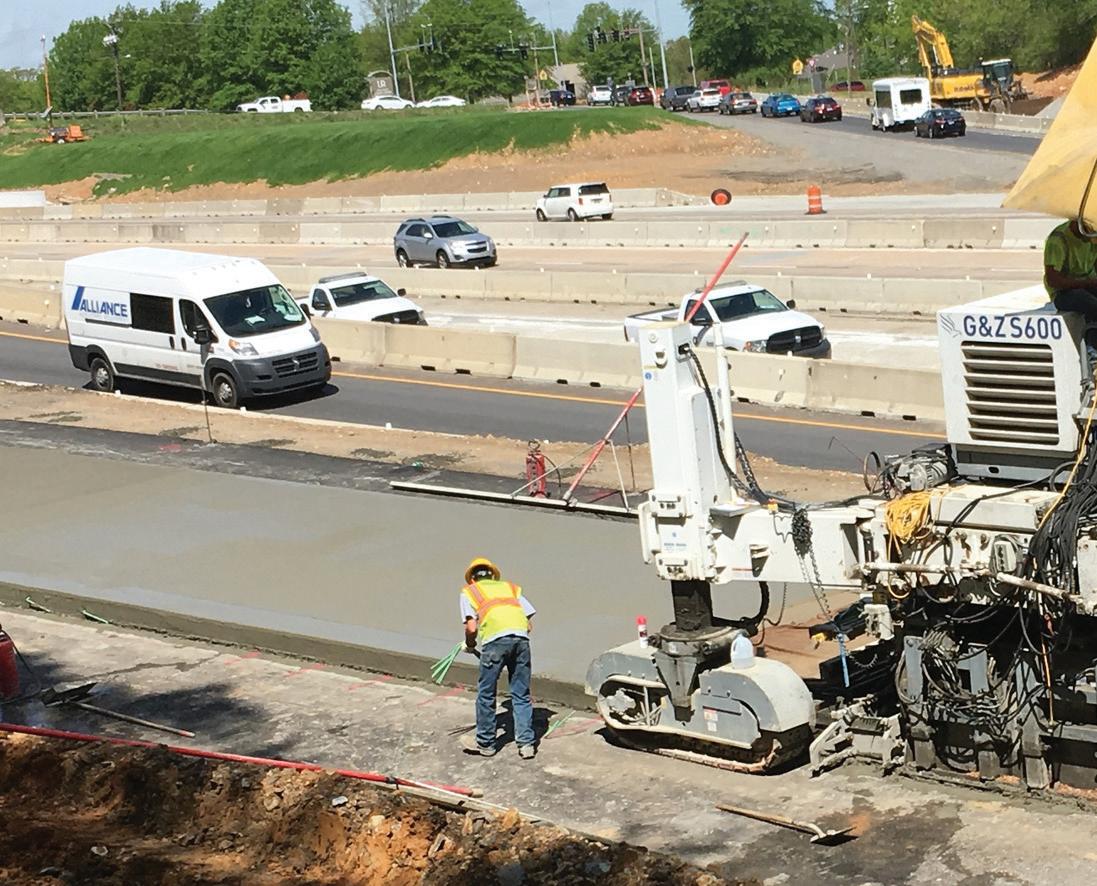

Grooving & Grinding Association, and the Innovative Pavement Research Foundation.
“There’s more”, says Bill Davenport, VP – Communications of ACPA. “Including some strategic oversight, fiduciary responsibilities, but in general, the Chair sets a course of action for our staff, affiliates, and members to follow each year.”
Headquartered in Rosemont, Ill., as well as an office in Washington D.C. supporting its public policy and funding advocacy efforts and federal agency relationships, the ACPA was founded in 1964 with the primary mission to advocate for the use of concrete pavements in surface transportation applications. The association has approximately 400 members with contractors making up about 55% of the membership. Members can range from concrete pavement contractors, cement companies, materials and equipment suppliers, and others.
“On a day-to-day basis we are addressing a wide range of topics, including inter-industry competition, concrete overlay technology,
Construction of the I-630 highway in Little Rock, Ark. performance-engineered mixtures; funding and public policy decisions (notably the support of a robust and adequately funded federal-aid highway bill and federal-aid airport legislation); research, technology and innovation aimed at pavement quality; sustainability and pavement resilience; downfield issues that may impact transportationconstruction 10 to 20 years into the future,” explains Davenport. There’s more, but—put simply—it all comes down to providing the best pavements consistently over time.
Howard has been involved with the ACPA early in his career, since the 1990s, and sees this new role as a way of giving back to the association. As the primary trade association for concrete pavement products, “they’ve been the number one advocate for the company and the products that we sell, both on a technical and a relationship basis— especially the federal and state levels,” says Howard.
He has also had other leadership roles within the ACPA. As the chair of the ACPA Strategic Advisory Committee, a sort of prerequisite to leading the board, he made a significant impact and paved a new path. “He had a vision for taking a different approach with our strategic advisory committee and the task forces that existed at the time,” says Davenport. Howard's vision had taken the existing advisory groups and had them focus on specific areas. The association recast the model of its groups to create a highways market, permit airport market for streets, roads forum, and an industrial forum.
“These firms and committees are… already making a very dramatic difference that, I think, we're going to see that continue,” says Davenport. “[David] has a vision for carrying the association well into the 21st century.”
The goal or function of the Strategic Advisory Committee, explains Howard, is to engage membership and distill what
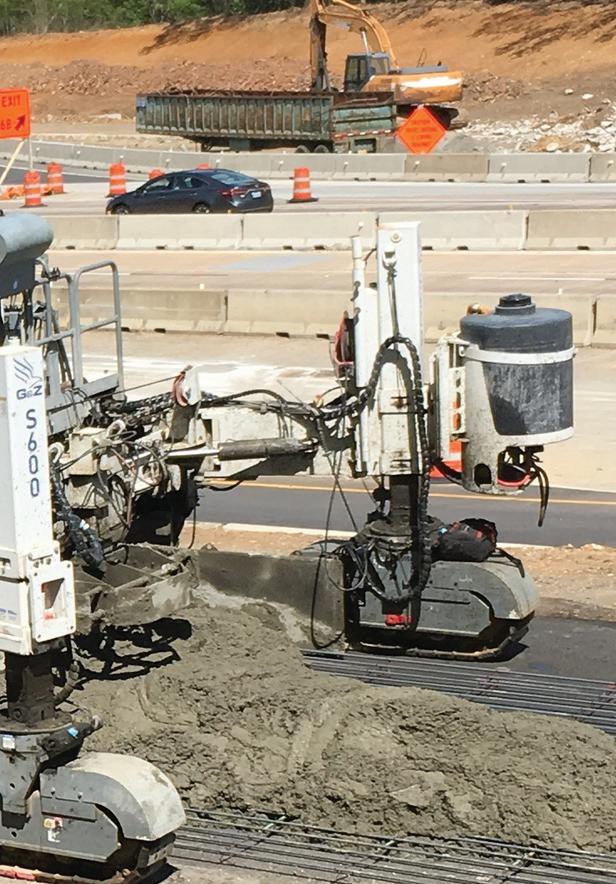
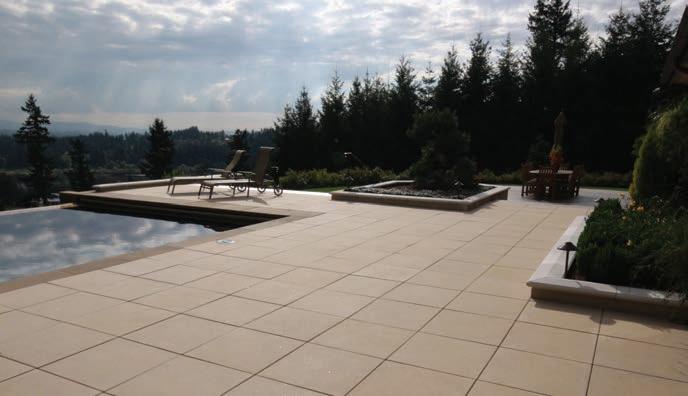
New Colors - New Bag Same Great Results
High quality, non-fading pigment 19 new colors - Easy color dosing Convenient 10# repulpable bags
Powdered Integral Color
1 BAG PER 2 YARDS 1 BAG PER 1 YARD
Different types of finishing techniques and curing methods will alter the finished appearance. A job-site sample or test slab should be done, using the specified materials, as well as the finishing and curing techniques that will be used on the project. Batch-to-batch uniformity must be maintained to produce consistent color.
(PC-6001) EARTHEN
(PC-1001) SLATE
(PC-2017) THISTLE
(PC-3001) BUFF RAWHIDE
SRI 22 LIGHT GRAY
REDBUD
CHAMOIS
2 BAGS PER 1 YARD
SRI 25 BUCKSKIN
SHALE
SRI 40 CURRANT SRI 24
3 BAGS PER 1 YARD
LEATHER
STORM GRAY
RUBY
SRI 41 HARVEST GOLD SRI 41 GOLDENROD
The colors on this color chart are approximate, using laboratory samples of troweled concrete made from a 6-sack mix, using Type II gray portland cement, silica sand, and water to achieve a 4 inch slump. Different colors in cement, as well as some sands and water content will result in different colors.
(PC-4005) SAND DESERT SAND
(PC-5001) CARAMEL TAN
(PC-8001) OATMEAL SRI 37 OAK PINE CONE
SIENNA MOROCCAN TAN
SRI 29 HAZELNUT RUSTIC RED
SRI 29 CARIBOU SRI 48
(PC-8051) BISCUIT SRI 45 FAWN SRI 45 YELLOWSTONE BOURBON
Carbon Black can negate the amount of entrained
*Caution:
air in the concrete mix. Due to the particle size of Carbon, it has the tendency to dissipate out of concrete over time. Seal the concrete with a premium sealer to protect the surface color.
(PC-9001) MUSHROOM SRI 29 UTOPIA SRI 23 SILT SRI 20
(PC-9051) LLAMA
1 BAG PER 2 YARDS
SRI 44 CROISSANT
1 BAG PER 1 YARD
SRI 41 DEER VALLEY
1 BAG PER 1 YARD
SRI 44
(PC-908) SHADOW* RAVEN* (PC-600) FOG SRI 61 MOCHA
HONEYCOMB SRI 16
3 BAGS PER 1 YARD
ALABASTER SRI 71
www.brickform.com • (800) 624-0261 • www.solomoncolors.com
Construction of the I-70 highway in western Kansas.
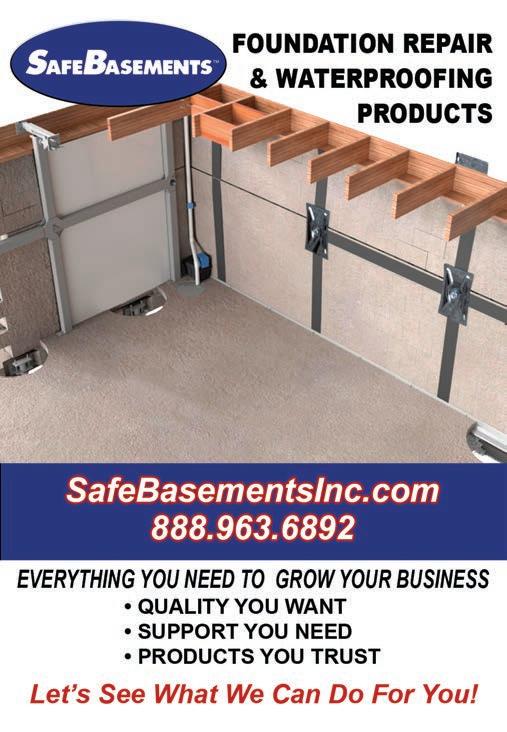
membership sees where the association has blind spots in marketing, technology, legislative, or membership engagement. The committee provides a mechanism to act on what they need to do. Originally, the committee attempted to meet the entire membership once or twice a year—but when new things come up like COVID, Howard found it not the most efficient way to engage.
“The vision was simply to restructure this in kind of a matrix organization chart,” he says. One axis of the matrix being the functional expertise in pavement design, another in communication, in marketing, in legislative affairs, in construction, etc. “Our staff at ACPA, we have all these things—so we split them up in smaller teams.”
He planned a roadmap to create interest-based “focused” forums for members seeking more information on a specific type of project to, hopefully, produce an efficient action out of the experts in the association.
KOSS CONSTRUCTION
Founded in 1912 by George Koss, Koss Construction began working with infrastructure. Then, as many businesses had to adjust in response to the post-World War II world, the company’s focus changed to concrete paving, working on a lot of bridges, as well as asphalt.
Of note, the company received the first highway contract back in 1956 with a stretch of I-44 in Missouri. In 1970, they completed the first interstate contract with the I-70 in Kansas. “The company has paved an awful lot of airfields in the Midwest,” says Howard. Interestingly enough, they also did the airfield in Roswell, New Mexico in the 1950s.
Yes, that Roswell, New Mexico.
“If you drive through the Midwest—Arkansas, Oklahoma, Kansas, Nebraska—you’ll drive through one of our projects,” says Howard.
Employees are proud of their work and many of the companies wear this on their sleeve, literally, along with the title “hard roader.” As explained on their website, “these men and women, laborers and craftspersons, engineers and foremen who are Hard Roaders are all experienced in their trades and take great pride in recognizing high standards.” Employees earn a small red star per five years with the company. The full-time staff runs about 75, but balloons to 200 during the construction season.
Work continues for Koss Construction. Their 2021 includes business as planned with interstate projects through the Midwest: Kansas, Missouri, and Nebraska. They’ve also worked on a number of airfields. At current, they’ve returned to their historic roots; Howard explains that half of the company’s business has been by interstate reconstruction.
With such an area to cover, it’s to their benefit to be as mobile as possible. Shipping heavy materials can be costly so bringing what they need to the site helps them be more effective. “We only work on highways, and for the most part just the larger projects,” says Howard. “We produce our own concrete and have mobile concrete plants. We mobilize to a project with everything that’s required to do the project— the plant to produce the concrete, the equipment to the old roadway. Production is more cost-effective.”
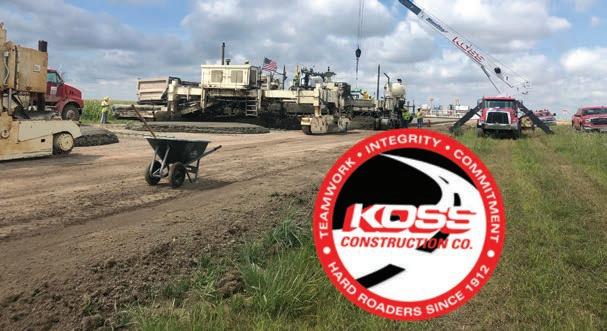
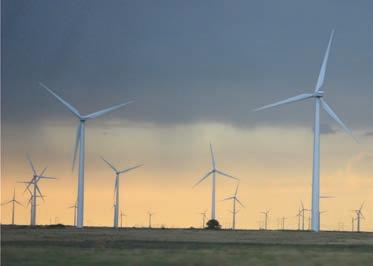

With each state only doing large interstate projects only two, three, or four times per year, Howard finds it necessary to “cast a wide net.”
IN THE SEAT
“The ACPA is very good at what it does,” says Howard. “It has a nice toolbox of resources, both on the technology front…and we have a network of chapter state organizations throughout the country. I think we’re keeping our eyes on the road, looking ahead, and providing stability. Because in a time of change, you don’t want to get caught up in the minutiae—we have things to do, no matter what gets thrown at us.
Howard looks to leverage the decades of his experience for his new role. “I understand how sales opportunities come in—the municipal owners, the state owners—I understand the process, I understand the technical side of concrete pavement. And having been involved in the ACPA for so long, I understand the association well.”
Through hard work and determination, Howard values focus. He imparts this piece of advice, “Somebody once said to me, when you get into executivelevel positions, one of the strongest things you have to lean on is that you have pretty much seen everything before. There may be some nuances and some changes, but it’s the time-tested ability to deal with whatever comes up and maintain focus on the agenda.”
Picturesque windmills tower over the horizon with the 6x6x6 pavement slab of the western Kansas I-70.
For more news and stories from the ACPA, visit ForConstructionPros.
com/10071933.
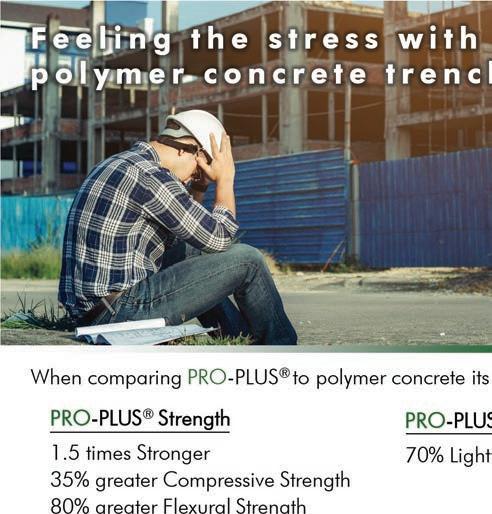
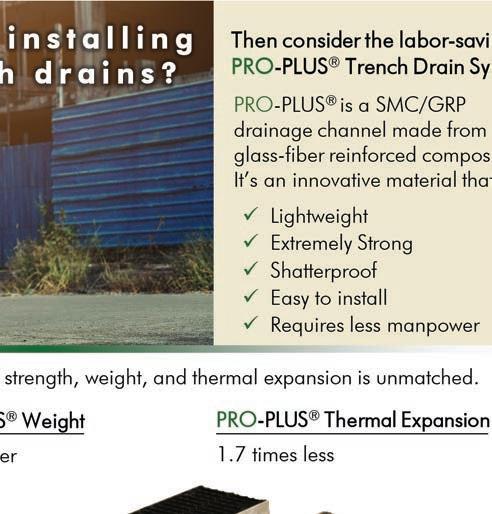
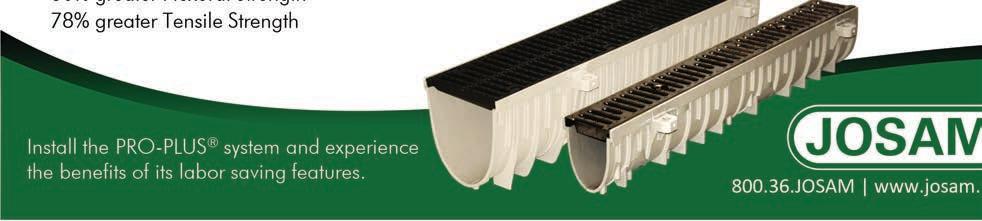