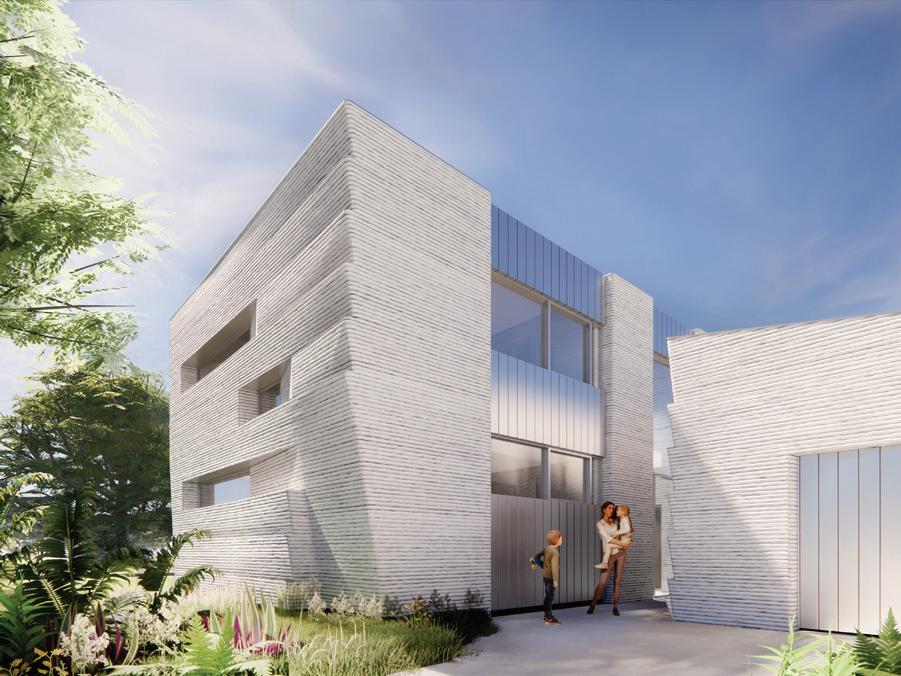
4 minute read
Robotic Brutalism
It took a team of innovative contractors, ingenuity, and a clever architect to finally break the ceiling in the construction of the first multi-story 3D concrete printed home on U.S. soil.
Acorner lot sat dormant in a quiet neighborhood of Houston, Texas. Unknown to the surrounding homeowners, an idea sat on the horizon that would change the look of the block for decades—and possibly the look of the U.S. concrete construction industry forever.
After years of plans, permitting, and communication with the city and community, this lot was reactivated with activity late summer 2022. Construction of a new concrete home would soon begin; a unique concrete home that would break the mold of concrete innovation. Soon enough, a gantry was constructed. Massive bags of locally sourced cement mixes were delivered. Hard hats dotted the scene behind safety fences as a robotic 3D concrete printer started placing the first multistory concrete structure in the U.S. It’s estimated to be completed February 2023.
In a collaboration with building industry partners, design firm HANNAH, PERI 3D Construction, and construction engineering company CIVE, partnered to print a two-story single-family home that integrates customized architectural design and a resilient structural system.
The 4,000-sq.ft. project showcases the possibilities of 3D printing technology, mass customization, and design solutions that integrate conventional construction systems. Utilizing a hybridized construction method, the structure combines 3D printing with wood framing. Its scalable design and construction process is applicable to multifamily housing and mixed-use construction. Using the COBOD BOD2 gantry printer, the project takes advantage of the printer’s modularity for its design layout.
This isn’t the first go-around for the COBOD BOD2. It’s a popular machine deployed around the world for the printing of numerous buildings like schools and tiny homes. The company describes the printer as a “modular truss structure.” The equipment used for the multi-story home in Houston measured 30 ft. by 45 ft. and 30 ft. tall. They recommend a crew of 3 to 4 operators when printing: • a printer operator, • materials operator, • materials operator helper, and • a hands-on helper.
The project is the culmination of a two-year collaborative effort between boundary-pushing design researchers and industry partners. The project is spearheaded by architectural designers and assistant professors at the College of Architecture, Art, and Planning at Cornell University Leslie Lok and Sasa Zivkovic, principals of HANNAH; along with PERI 3D Construction, an internationally leading provider for 3D construction printing, and CIVE, one of the leading engineering and design/ build contractors in Houston.
Lok and Zivkovic explain their hybrid construction approach to couple the innovations in concrete 3D printing with traditional wood framing techniques creating a
HANNAH HANNAH HANNAH

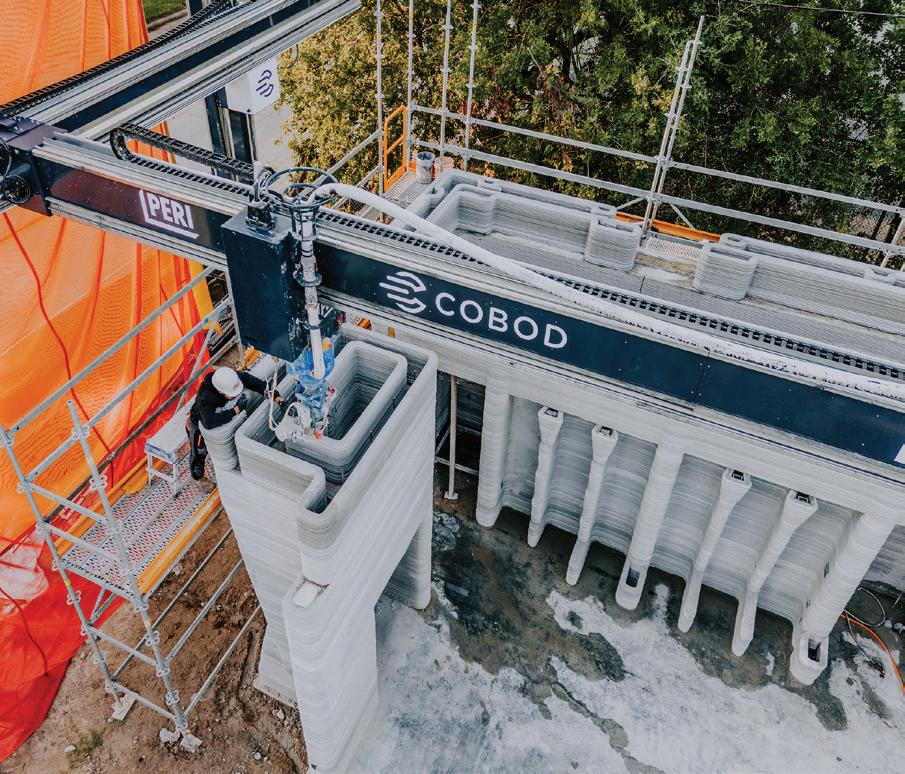
HANNAH HANNAH

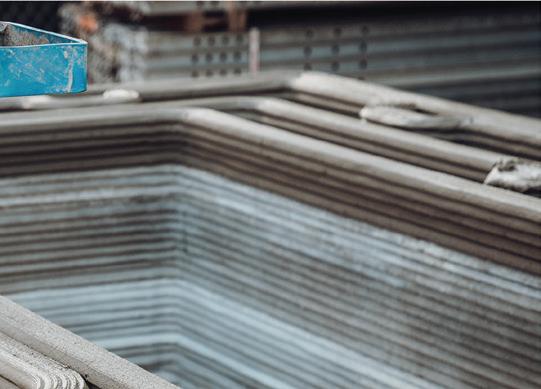
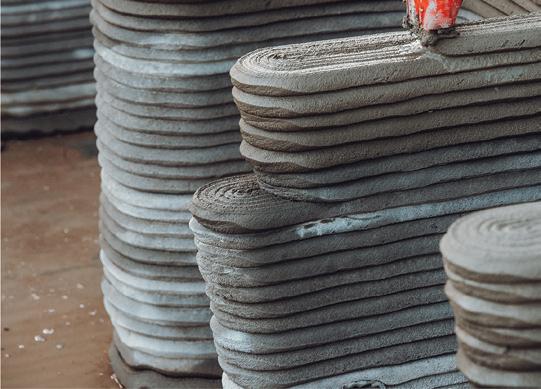
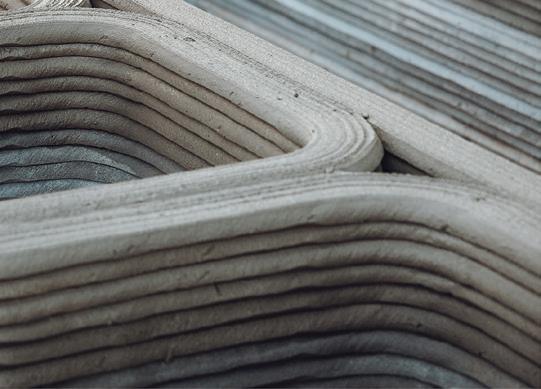
structurally efficient, easily replicable, and materially responsible building system. “The project also highlights the exciting design potential of mass-customized architectural components to meet homeowner’s needs and to simplify building system integration. These design efforts aim to increase the impact, applicability, sustainability, and cost efficiency of 3D printing for future residential and multi-family buildings in the U.S.” they add.
Collectively, the team has extensive experience in 3D printing. HANNAH’s innovative architectural design practice is known for its progressive design solutions, such as upstate New York’s Ashen Cabin project. The Ashen Cabin is a sustainable building that advances the use of 3D printing concrete and robotic timber construction.
During this experience, they’ve come to start calling the style from 3D concrete printers as “robotic brutalism.”
PERI 3D Construction has an extensive record of advancing the implementation of 3D printing. Using COBOD BOD2 printers, PERI has completed six projects in Europe and in the U.S. including the first 3D-printed home in Germany and Europe’s largest 3D-printed apartment building.
CIVE combines structural engineering expertise with bountiful construction experience to create a coordinated workflow.
According to Fabian Meyre-Broetz, CEO of PERI 3D Construction, the Houston home marks the seventh and largest project (at the time) for the team. Adding, “We are incredibly proud to not only showcase the possibilities of the BOD2 3D construction printer but also our extensive know-how in planning, engineering, and printing on this project. We are convinced that it will set new standards from a design as well as printing execution perspective and underlines our role as the forerunner for this new construction technique.”
The project also developed detailed solutions with key building industry partners from construction material to HVAC systems. The team calibrated printing parameters with QUIKRETE’s new generation of printable concrete. Working with Huntsman Building Solutions and their R&D research team, the building integrates a closed-cell foam insulation system. The hybridized construction utilizes Simpson Strong-Tie’s anchoring systems for both 3D printed elements and wood connections.
Eventually, a state-of-the-art variable refrigerant flow technology will be installed for an efficient HVAC system. “Having the opportunity to be the engineers and general contractor for the first multistory 3D printed structure in the U.S. has been an honor,” says Hachem Domloj, CIVE President. “We can see how this technology and our team’s approach is providing the scalability to larger commercial developments. Collectively, we’re changing the way our country builds and paving the way for more affordable housing, higher structural integrity, and faster building capabilities. The possibilities of 3D printing are endless!”
HANNAH AC Business Media | Photo by Jonathan Kozlowski

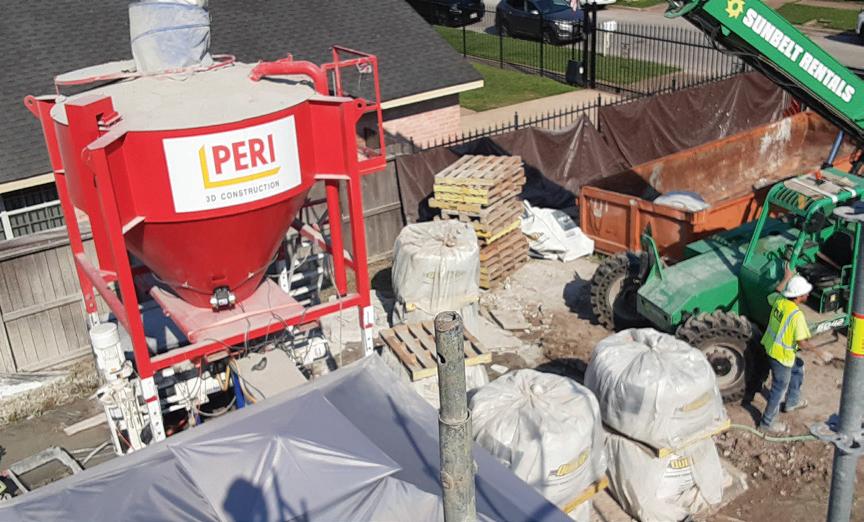
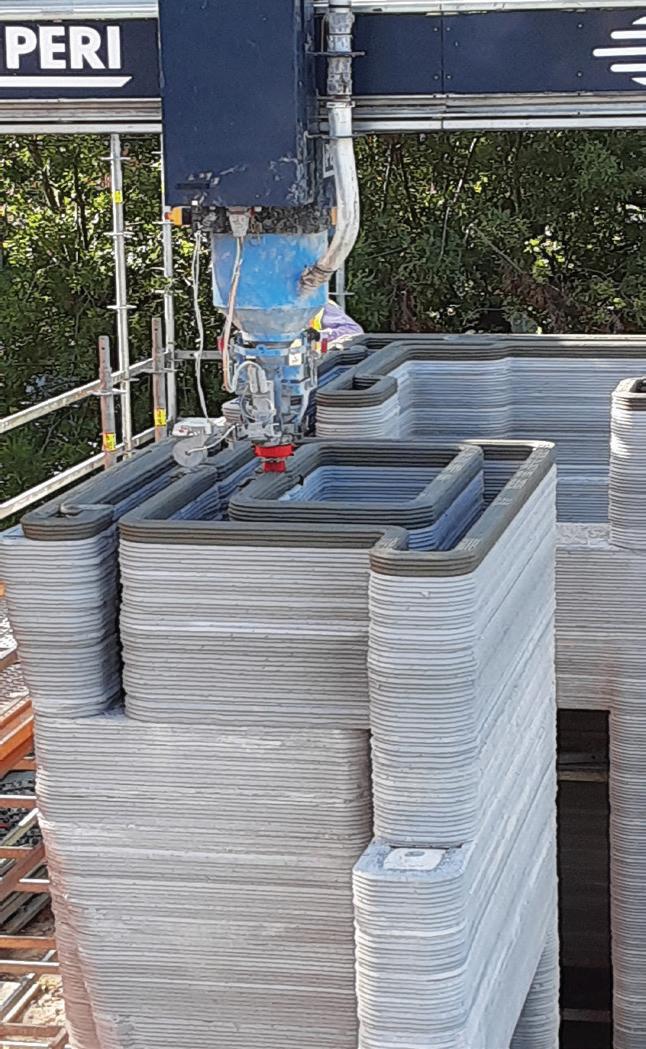
AC Business Media | Photo by Jonathan Kozlowski
For more information visit https://CONC.me/6z53ev