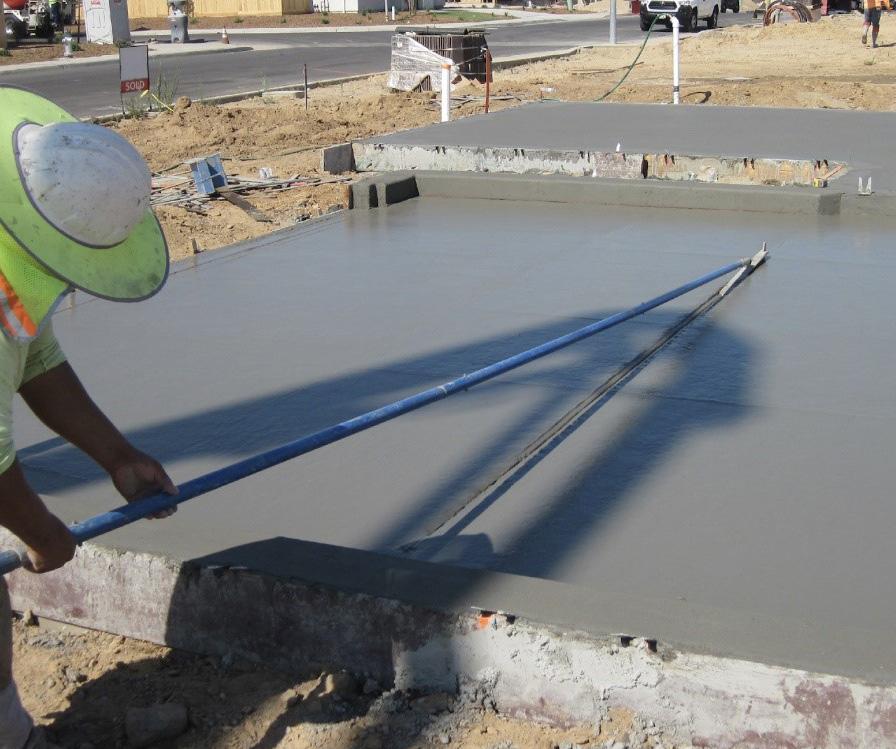
5 minute read
Contraction Joints: New Developments for Slabs-On-Ground
The ACI Committee on Residential Concrete now recognizes early contraction joints, here’s how an early contraction joint method called “Trak Joint” can help reduce random cracks in your concrete slab.
Two new developments have recently occurred regarding the installation of contraction joints in slabs-on-ground. First, the ACI Committee on Residential Concrete now recognizes joints, installed soon after concrete placement, as early contraction joints. The types of joints that meet this category are tooled joints, inserts, and early entry saw-cuts. The depth requirement for these joints is 1/5 the thickness of the slab or a minimum of 1 in.
Second, a “Trak Joint” insert type of contraction joint is now available on the market. This joint is installed at the time of bull floating, which makes it a very early contraction joint, and an effective method to minimize random cracks.
Historically, the joint depth of 1/4 the thickness of the slab applied to all types of contraction joints for slabson-ground. In the 1980’s with the introduction of early-entry sawcuts, a new criterion evolved. Joints could be 1-in. deep for slab thicknesses of up to 9 in. These joints were installed shortly after the slab was strong enough to support foot traffic. The age of the concrete was about one hour in summer and four hours in winter. This was in contrast to conventional wet or dry sawcutting where the concrete needed more strength prior to sawcutting. Conventional sawcuts required the concrete to have an age of about four hours in summer and 12 hours in winter. Many times, the conventional sawcuts were installed the day following concrete placement. This delay often allowed cracks to develop overnight. Field experience showed a significant improvement in reducing random cracks by using earlyentry sawcuts.
Interestingly, the criterion for the reduced sawcut depth, that is 1 in. for slabs up to 9 in. thick, applied only to early-entry sawcuts. Tooled and insert joints were required to meet the joint depth of one-fourth the thickness of the slab. Yet, tooled and insert joints are installed sooner than early-entry sawcuts. This oversight is now corrected in the ACI Code Requirements for Residential Concrete (ACI 332-20), where tooled, inserts, and early-entry sawcut joints are treated equally. The new joint depth is one-fifth the slab thickness, or a minimum of 1 in. Conventional sawcut joints, either wet or dry, remain at the depth of onefourth the slab thickness, or a minimum of 1 in.
There are technical reasons why contraction joints installed earlier are more effective in activating than joints installed after the concrete is hard.
Technical Discussion
Random cracks in slabs are primarily caused by volume decreases to concrete. Three mechanisms exist that cause concrete to decrease in volume. The most well-known mechanism is drying shrinkage. Here, water in the pores of hardened concrete needs to evaporate. As water evaporates, the water remaining in the partially filled pores forms a meniscus. The occurrence of menisci means that the surface tension of the water has increased. The more water evaporates, the greater the surface tension becomes. The surface tension of water pulls on the solid particles. The hydrated cement particles are forced closer together, which results in a volume decrease. Drying shrinkage occurs slowly from days to years.
On the first day of concrete placement, plastic shrinkage of concrete may occur due to water evaporation. Plastic shrinkage is a form of drying shrinkage, only the shrinkage occurs while the concrete is “plastic” or very weak. The formation of menisci in the pores cause volume decreases, which can lead to cracking of the young concrete.
The second mechanism is thermal contraction. On the first day of concrete placement, the internal temperature of concrete can become high at 150º F and greater. Factors influencing the maximum temperature are initial temperature of concrete in the ready-mix truck, ambient air temperature, solar insolation, and amount of portland cement in the mix. As portland cement hydrates, the chemical activity is exothermic. Substantial amounts of heat are generated by cement’s heat of hydration, particularly on the first day. Concrete hardens when its internal temperature is high. The initial volume of concrete is established at a high temperature. When the temperature of concrete decreases, a volume decrease occurs. The coefficient of thermal expansion is the material property that permits calculation of the amount of contraction expected due to temperature change. The first night is a vulnerable time for concrete, where its strength is still low and decreases in volume occur due to cool evening temperatures. Thermal contraction is a major cause of random cracks in slabs-on-ground.
The third mechanism is less well known. It is chemical shrinkage. When portland cement is exposed to water, the cement particles partially dissolve, and the atoms and molecules, now swimming around in solution, combine to form various types of crystals. A rapidly forming crystal, ettringite, is responsible for the setting and stiffening of concrete and are composed of calcium, aluminum, sulfate, and water. The next important crystal to form is responsible for the strength development of concrete. These crystals are called calcium silicate hydrate, and consist of calcium, silicates, and water. The volume of crystals is less than the volume of the individual elements because of attraction forces between the atoms and molecules. As cement hydrates, volume decrease occurs in the concrete by chemical shrinkage. Once a strength-giving structure is developed for the concrete, water continues to be consumed by hydration. Some pores start to become partially filled with water, so menisci form. Cracks can occur in concrete on the first day due to chemical shrinkage. Once concrete is hard and water consumption continues due to hydration, the volume decrease is called autogenous shrinkage.
Normal concrete mixtures are usually not affected by cracks developing due to chemical shrinkage. As a consulting concrete engineer, I have encountered projects where cracks in slabs occurred on the first day, and those cracks could not be explained by drying shrinkage or thermal contraction. For those cases, the concretes contained a high cement content and low water-to-cement ratios, and other factors which resulted in rapid hydration during the first day. In any event, chemical shrinkage can have a contributing effect to the development of cracks because volume changes by chemical shrinkage, thermal contraction, and drying shrinkage are additive.
Effective Contraction Joints
Tooled and insert joints are installed prior to the occurrence of all three volume change mechanisms; hence, these joints are most effective in having cracks develop where desired—in the contraction joint. From an effectiveness standpoint, the best joints are installed in fresh concrete (tooled and inserts), next are those installed in recently stiffened concrete (earlyentry sawcuts), and last are those installed in hardened concrete (conventional sawcuts).
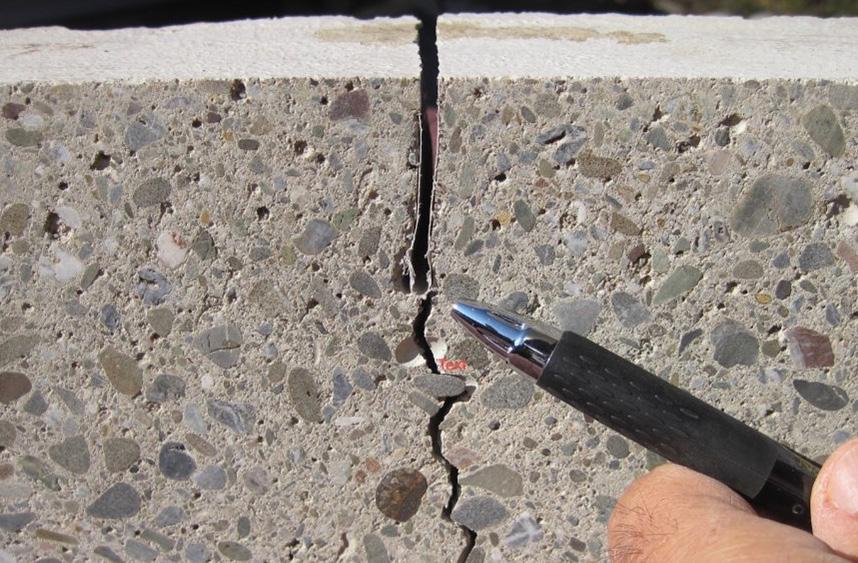
Tooled Joints
Early contraction joints are now recognized as tooled, inserts, and early-entry sawcuts. The depth of joint needs to be 1/5 of the slab thickness, with a minimum depth of 1 in. for each of these methods.
Conventional wet or dry sawcut joints still need to be 1/4 the thickness of the slab.
These joints are also called scored or grooved joints, and the tools used to form the joints are jointers or groovers. The top image of this article shows a deep groover, where the bit is usually about 1.5 in. but tools with bits about 3/4-in. deep are also common.
These tools are used for relatively small jobs, such as, driveways, patios, and sidewalks. In residential work, garages typically show tooled joints. The slab to the residential part of the house may also have tooled joints. Some contractors use the deep groover to push aside the coarse aggregate particles and then fill the groove with cement paste during bull floating. This type of joint is only partially effective as a contraction joint. It is not recognized as an official contraction joint.
Tooled joints have edges that are rounded to various radii. The appearance is neat and clean.