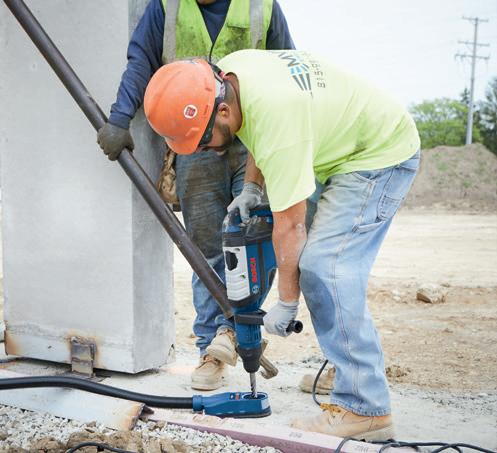
4 minute read
Carbide 101
Bosch Power Tools
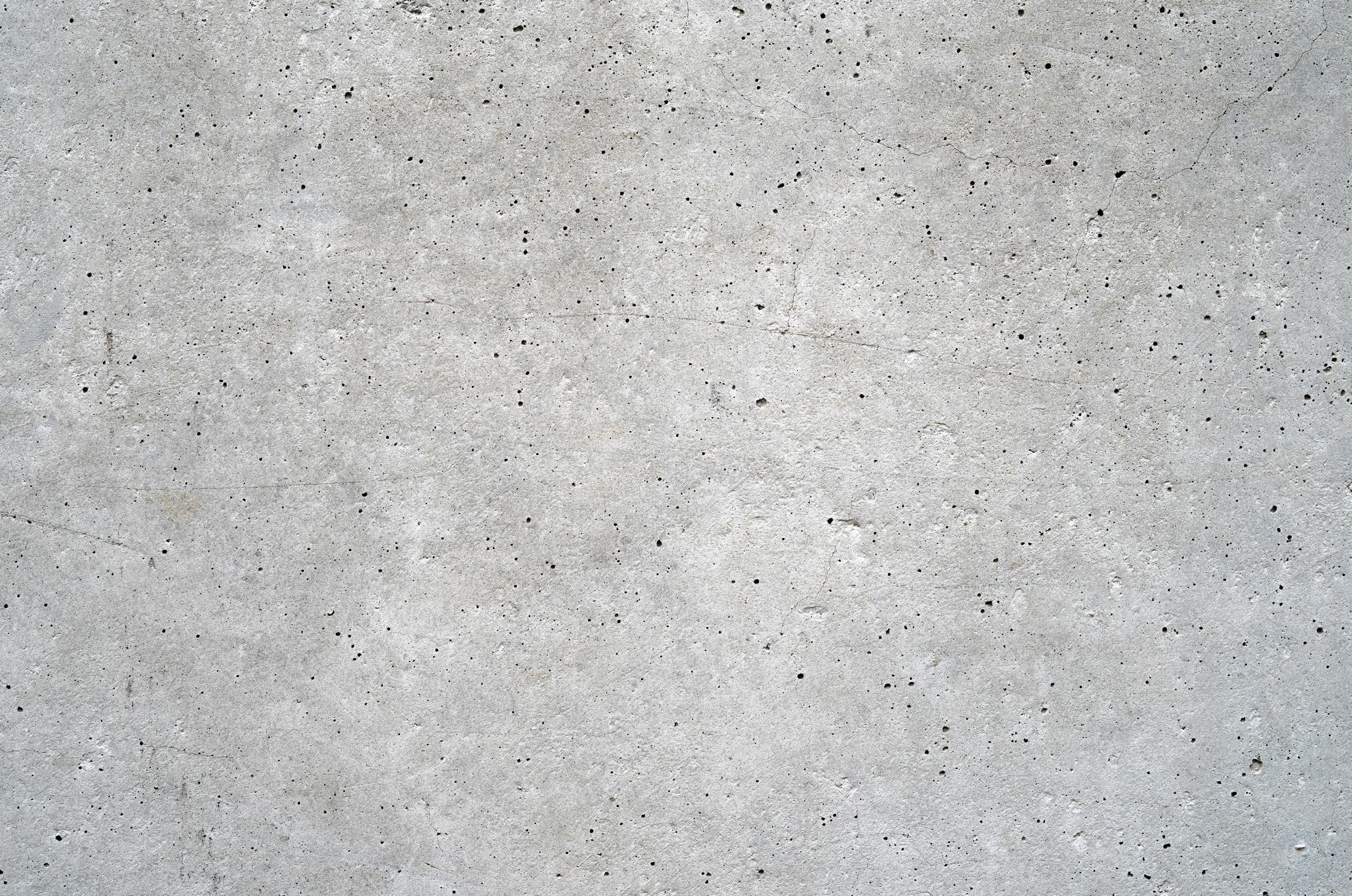
Carbide 101: A Primer
on Tungsten Carbide in Concrete Drilling
Carbide is one of the most important materials in concrete drilling. It’s a tough, long-lasting material that’s well-known as premium for precision drilling. But there’s a little more to employing carbide in concrete applications than placing it on the end of a drill bit. Bosch Group Manager Tom Grego offers his insight into use, application, and best-practice for carbide in drilling applications.
What drives the acceptance of carbide in concrete applications?
“The perception in the industry is that a product with carbide on it is a better-performing product. For example, when you consider a circular saw blade with standard steel teeth versus a blade with carbide teeth, performance goes up dramatically with the carbide blade. The same goes for other cutting accessories: oscillating blades, jig saw blades and reciprocating saw blades.
In the concrete industry, carbide is the standard for drilling holes in concrete and masonry because the material offers the robustness to last for a long period of time. Carbide has become a broad term in the industry, but users know that not all carbide is the same. Users may not know the why of carbide differentiators, but they know the results.
Carbide is different from the steel that makes up the rest of the drill bit. Whether it’s a standard concrete drill bit that goes into a three-jaw chuck tool or an SDS-plus bit or SDS-max bit, the shank is a solid-body piece of steel that’s fluted to ensure material removal. At the tip of that drill bit, the contact point with the work, is some form for carbide.”
What can you say about the various bit designs that incorporate carbide?
“The most common design in concrete drill bits is the two-cutter, although most users wouldn’t refer to it that way. They just know the bit by the two cutting edges on the end of the bit tip. The standard manufacturing process is milling out the steel at the end and attaching a carbide chip, with two edges, using a welding or braising process that connects the carbide to the steel. This is a process known in the concrete industry as embedded carbide.
The next iteration of concrete bit design is the four cutter. In this design, two additional notches are made in the steel on either side of the original carbide chip. New designs have one piece of carbide notched into the steel bit in the shape of the four-cutter. Users may not understand the intricacies of two-cutter versus four-cutter design, but they do know that more carbide at the end of the bit represents a better, longerlasting concrete drill bit.
Full-head carbide is not notched pieces set into the steel shaft, but a 100% carbide tip that’s interwoven with the steel to create a stronger bond. This is the most robust, longest-lasting design when drilling into hard aggregate or concrete with rebar. There’s a visual difference between the three options.”
How does the user know what grade of carbide they’re using?
“Sub-par carbide breaks apart and can be brittle. Poor carbide can chip, or if the welding or braising process is poor, the entire bit head can break, pop or twist off. Users can see the difference in performance.
Also, every design in concrete drilling has its weak points. The two-cutter design is fast in concrete drilling, but it doesn’t withstand hitting rebar well. The four-cutter design withstands rebar hits better, but it doesn’t have the life of full-head carbide. The best concrete drill bits in the world feature full-head carbide in SDS-plus or SDS-max configurations. A two-cutter bit is not intended to drill into rebar.”
How do users justify a more expensive bit?
“The No. 1 cost on any jobsite is labor. When the workers can’t work because of equipment failure and the need to change a bit, that’s downtime. Worse yet, if there’s no replacement available and workers need to walk the site looking for a replacement bit, it’s a waste of money. If there are no replacements, work simply stops.
If the user has a bit with five times longer life and workers can stay at the task longer, that’s a big savings. It’s less downtime. Also, workers sometimes can be placed in difficult and strain-inducing positions to drill holes for anchors in concrete. Rotary hammers used for these tasks are powerful and sometimes heavy, plus there’s extreme heat or cold weather. The sooner the worker can complete the job successfully in these difficult conditions the better off that worker will be and the more exacting the work. Breaking a drill bit when hitting rebar or simply wearing out an inferior drill bit prolongs the task.”
For more information visit