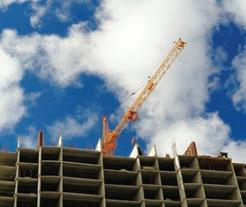
3 minute read
Emerging Concrete Technologies to Reduce Embodied Carbon
Bigstock
Between now and 2050 if construction trends continue, we will likely double the square footage of the built environment. In this short time period, half of the new construction emissions between now and 2050 will be from embodied carbon.
With this, carbon reductions for concrete have become a focal point for the industry. Emitted carbon from the cement production process accounts for 4.4 billion tons of CO2/year and the distinction of being the world’s secondlargest CO2 emitter, as noted in the research Making Concrete Change: Innovation in Low-carbon Cement and Concrete. Many concrete technologies have emerged in recent years to tackle carbon reductions in concrete products.
OPTIMIZING CEMENT Portland Cement Usage
The first step to reducing the carbon impact of concrete is to optimize portland cement usage. Concrete specifications should be performance-based and written to state what strength is needed for each element type, cement may be reduced in some regions by specifying higher quality aggregate or using less water. Mix optimization is key and engineers should ensure their specifications allow mix designers the ability to minimize carbon impact by only specifying the performance requirements necessary for each structural element.
Cement Alternatives
“Project Drawdown” identified using cement alternatives as strategy #36 and estimated a potential carbon savings of 440 million tons of CO2 emissions annually. Maximizing the industry’s use of readily available cement alternatives such as fly ash and slag is one of the most important steps engineers can take to reduce concrete’s carbon impact. Meanwhile, a few cement alternatives are emerging: • Metakaolin is a pozzolan produced from the calcination of kaolin clay at much lower temperatures than portland cement. However, metakaolin is expensive and only used to replace up to 10% of cement and thus has not been widely used, according to Metakaolin and Calcined
Clays as Pozzolans for Concrete: A
Review. • Limestone Calcined Clay (LC3), is a ternary blended cement comprised of portland cement with calcined clay and limestone. Preliminary studies have shown that LC3 is an extremely promising option to achieve lower
CO2 emissions, increase supply capacity, higher return on investment, and potentially lower prices in the construction market, as noted in the research Limestone Calcined Clay
Cement as a Low-Carbon Solution to
Meet Expanding Cement Demand in
Emerging Economies. • Recycled glass and volcanic ash.
Glass pozzolans have been used in concrete mixtures in several projects in the southeastern U.S. because there is a manufacturer located in
Tennessee. • Type 1L cement is essentially a blend of cement and naturally occurring limestone and meets ASTM C595.
Due to the natural limestone component, Type 1L cements have a lower embodied carbon than typical cements yet have very similar performance characteristics. Typical limestone component makeups for Type 1L cements are usually in the range of 10-15%.
CARBON
Another emerging technology in concrete production is to utilize carbon sequestration and injection. Technologies such as CarbonCure, CarbiCrete, and Solidia have been emerging.
Walter P Moore used CarbonCure on a variety of project types and concrete applications. For a commercial office building development in Atlanta, our team was able to work with the concrete supplier for the drilled pier foundations to inject CO2 into the concrete mixture at the batch plant and reduce the cement content by 7% for that application. This technology and technologies similar to it, when used in combination with other cement alternatives such as traditional supplementary cementitious alternatives can help project teams achieve embodied carbon reduction goals on their projects.
Most projects will need to take a multi-faceted approach by incorporating cement reduction, cement replacement, and a variety of new technologies. As concrete designers, producers, and specifiers; we need to be nimble, willing to think outside the box, and consider new technologies as they arise.
Kelly Roberts, PE, SE, LEED AP BD+C, is a principal in Walter P Moore’s Structural Group.
Adapted. Find the full version and references at ForConstructionPros.