
23 minute read
TELEMATICS GO BEYOND FLEET MANAGEMENT
Danfoss Power Solutions
Continued advancement in telematics enables more data collection and predictive maintenance capabilities.
Telematics systems continue to play a pivotal role in heavy-duty equipment. As use of these systems has increased over the years, so too have their capabilities.
“Telematics as a technology has evolved significantly over the last 10 years,” says Pankaj Sharma, vice president, marketing and product, at NexTraq, a Michelin group company. “It’s no [longer] just a location-based service like it used to be perceived in the past. It has evolved to be all about insights that make an impact on a fleet’s operations, whether it’s productivity, safety, cost efficiency, compliance and a lot more.”
Retrieving data from a piece of equipment and making the most of that data continues to be an area in which telematics technology is evolving. Incorporation of more data analytics as well as artificial intelligence and vision technology, such as dash cams, are some of the ways Sharma says telematics systems are advancing to provide more information for vehicle and equipment owners.
Integration is becoming an important part of the equation, as well. “Understanding that no individual entity can provide all services, it’s very evident we need to be part of a big ecosystem to provide a higher impact for customers,” says Sharma.
Because of this, forming industry partnerships — whether with service providers or OEMs — will be vital to ensuring end-use customers get the features and information they need. While NexTraq currently offers an aftermarket solution, it plans to work with OEMs as they play a critical role in ensuring the right equipment and vehicle insights are provided to end users.
“In addition to having a flexible portal and the ability to configure whatever data you want to collect, it’s also important to realize the level of telematics that every machine needs because not all machines are as complex. Not all of them have complex electronics that need to be monitored and updated,” says Ivan Teplyakov, business development manager for Connected Solutions, Danfoss Power Solutions.
For those wanting software updates, remote diagnostics or monitoring of complex electronics, he says high-level telematics systems with more connectivity are necessary. However, not every machine or customer needs this, which is why Danfoss has made both the software and hardware used for its telematics systems flexible.
“We offer a portfolio of three different devices,” says Teplyakov. “The customer can select the appropriate level of need for their particular machine, as well as the appropriate level of cost.”
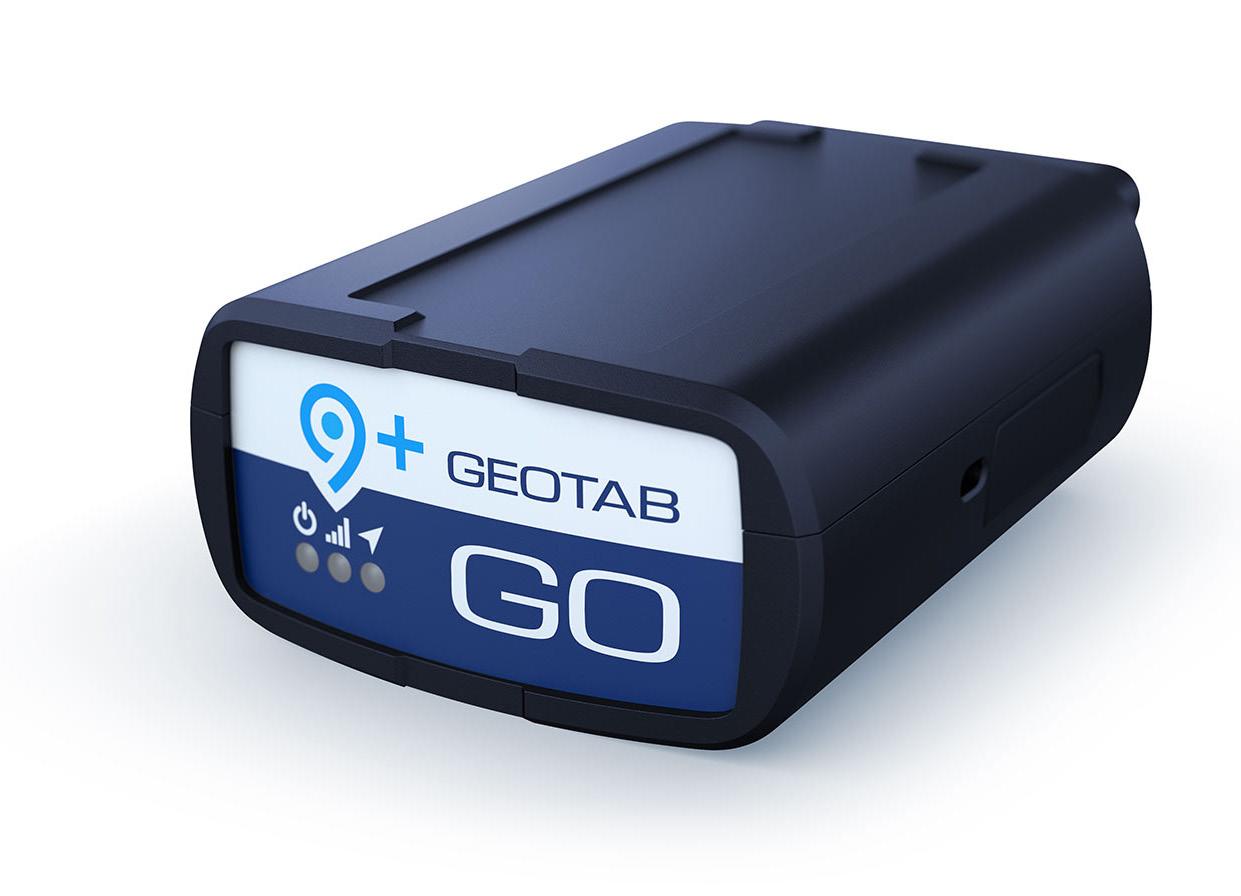
NEW TECHNOLOGY IMPROVES DATA COLLECTION
industries, including the heavy equipment industry. According to Sharma, those services are focused in four main areas: productivity and cost efficiency, safety, compliance and workforce management. “At the end of the day, all of our solutions and services are targeted toward these elements,” he notes.
The heavy equipment industry has a broad range of requirements including tracking assets, projects and workforce. As such, the NexTraq solution brings together various elements into a single solution to help meet the industry’s range of needs. This provides a complete picture of how a business is operating and what changes may need to be made to work safer and more efficiently.
With this solution, users can more easily track where and how their equipment is used. This can benefit rental companies which need to monitor equipment use and plan maintenance. It can also benefit equipment owners who want to ensure their employees are using the equipment in a safe and efficient manner.
Telematics provider Geotab recently introduced its GO9+ solution featuring WiFi connectivity to help make it easier for fleets to track and monitor their equipment. Bluetooth beacons can be placed on tools and equipment that communicate with a WiFi hub, which then communicates with the Geotab technology.
Colin Sutherland, executive vice president, sales & marketing, at Geotab, notes when the company launched the new telematics solution, customers said the biggest value was the amount of data generated to help with business operations. Because the device includes both cellular and WiFi components, customers can potentially reduce their cellular data costs. Many equipment fleets have multiple portable devices and cellular plans, which can become costly. Having a single solution capable of providing all of their data needs can help to reduce these costs.
Sutherland notes customers can set their rate plan to best meet their business needs. “We’re initially launching with a 2-gigabyte rate plan because we expect a lot of users to be dropping their expensive cellular plans and bringing it all through the GO9+ device,” he says.
Customers have told Geotab they will be better able to track data consumption with this new device and operate more cost effectively. “It’s all about operating costs in the field,” says Sutherland. “And in 2021, it’s about staying lean, giving people productive tools and eliminating wasted time. So, you can find a tagged asset and you know where it’s used. Combining connected assets and devices enables an employee to work effectively in a really seamless way. And that’s what excited us when we launched GO9+.”
While tracking a large piece of equipment will be beneficial, so will the ability to track and monitor non-powered assets such as attachments and tools and even cargo in some cases.
Alex Romero, product manager for Software and Connected Solutions, Danfoss Power Solutions, says the telematics portfolio the company is launching keeps in mind the fact heavy equipment also continues evolving. “Not all machines have
Geotab’s new GO9+ includes cellular and WiFi connectivity.
been equipped with enough intelligence to capture how the machine is performing in the field, and some of them are more evolved than others,” he explains. “[Some customers] may need more help from the intelligence that resides within the telematics gateway.”
As such, Danfoss has systems which are programmable and non-programmable.
Reliability and security of the information is integral, as well. Ensuring that is why Danfoss has chosen to engineer its own telematics system from the ground up. Romero says doing so provides more control over the type of protocols used for communicating information. The entire communication chain — other than the cellular network and infrastructure — is owned by Danfoss, enabling it to provide customers with the data they need in a safe and secure manner.
The company is able to do this by ensuring its telematics gateways are compliant with the latest cybersecurity protocols and the right encryption to make sure the data is not exposed.
“A part of this evolving digital environment is data itself. It’s about data ownership, and then data privacy,” says Teplyakov. “By having full control over our system, we can deliver these services to our customers without including, any more than necessary, third parties which could bring an element of risk to the whole environment.”
TELEMATICS AND THE GROWTH OF CONNECTIVITY
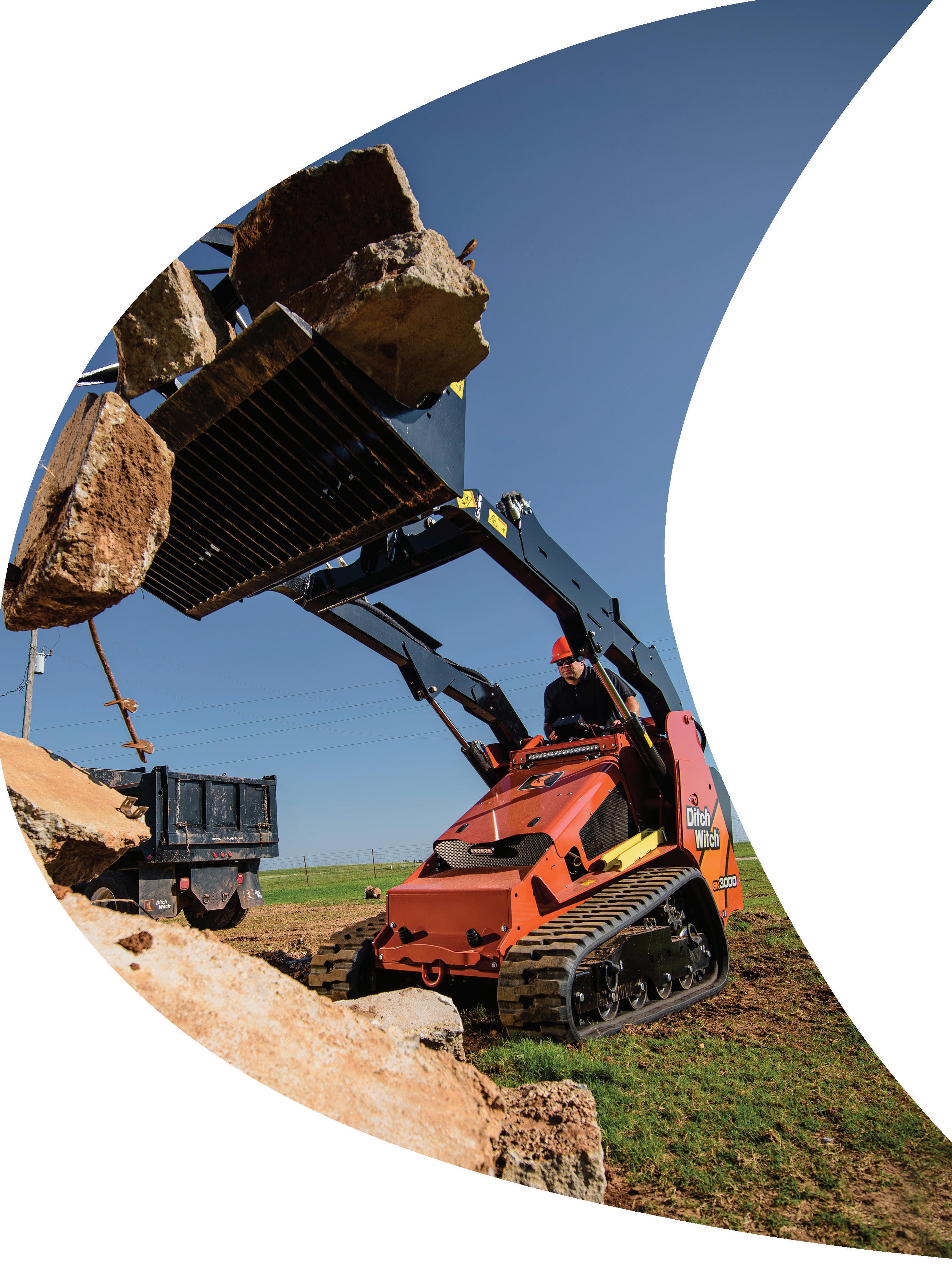
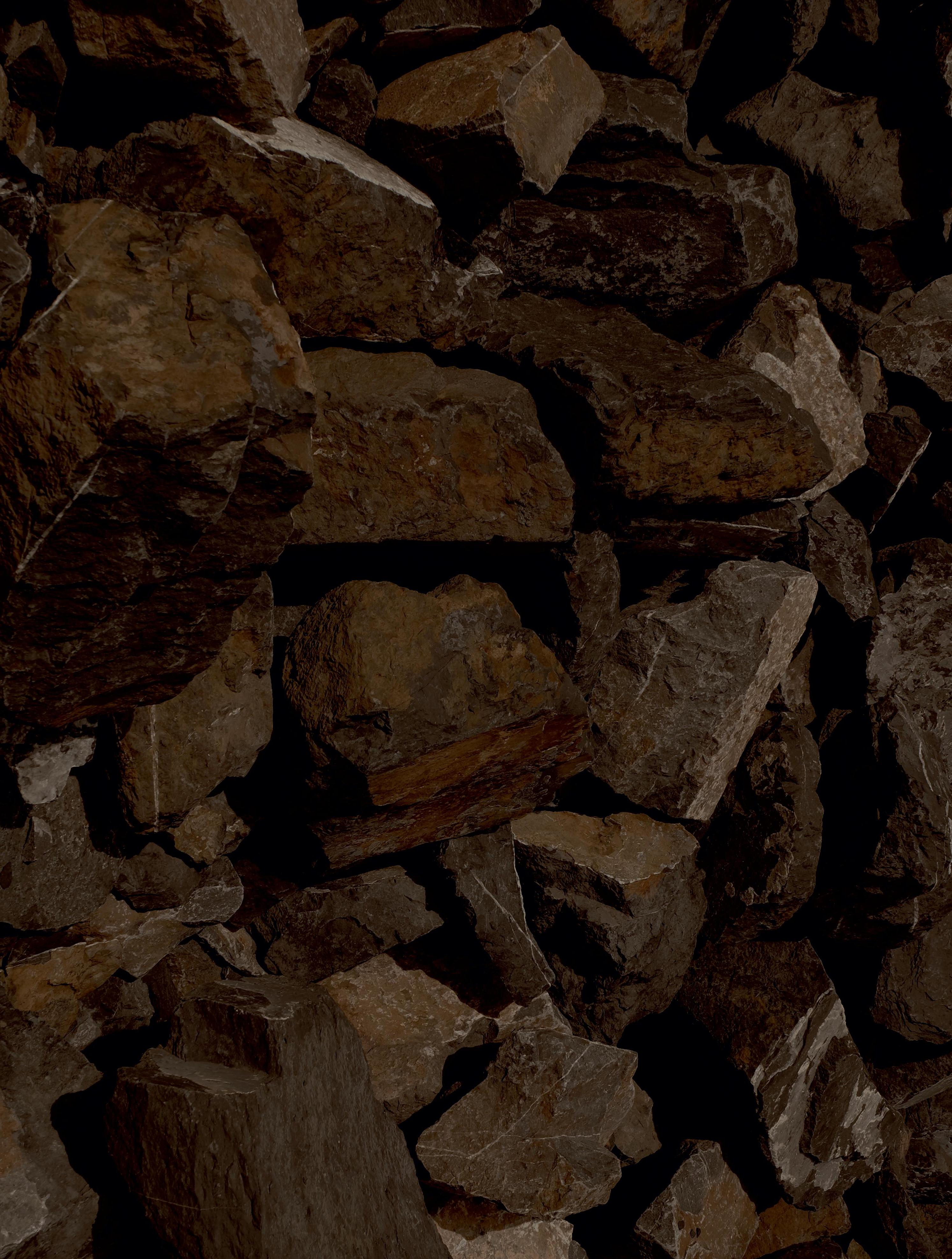
Over the past 20 years, diagnostic trouble codes have moved beyond those which were engine or sometimes drivetrain focused to other components such as PTOs, Sutherland notes. More sensors are also being incorporated into components and systems to make them and the overall piece of equipment smarter. All of this is providing more information to help fleets maintain equipment and maximize uptime.
However, it can be challenging to bring all of this information together, which is where telematics plays a role. Bringing all information and connected devices together to a common upload point, such as a telematics system, makes everything easier to manage.
The never-ending quest for productivity, which all of this information and maintenance planning looks to improve, has been a key driver for the increased use of digital technology in the heavy equipment industry, says Romero.
“We’ve seen a large wave of adoption and willingness to adopt digital technology and specifically connectivity,” adds Teplyakov.
More OEMs are doing so because the cost of entry is lower due to the rate at which technology has evolved. Many see the additional features that can be provided through digitalization as a requirement to compete in the market, as well.
Implementing connectivity and digitalization must be purposeful. Teplyakov says it should either solve a problem or increase reliability and productivity while reducing downtime. What that means for the off-highway equipment market can be very different.
“The large OEMs understand what data needs to be collected and how they can show users the valuable information collected in order to drive these productivity improvements,” he says. “For the majority of the market, what that means could be very different.”
As such, every OEM needs to look at its own machine designs and what constitutes productivity benefits and reduced downtime, Teplyakov states. Based on that, it can then implement the right technology. “Because we cater to this market of small and medium OEMs, we need to have a very flexible platform that can be configured to these different needs,” he adds.
The user interface of Danfoss’ system
UNCAGE THE BEAST.
Bring stand-on convenience to full-size work with the Ditch Witch® SK3000 Stand-On Skid Steer. This beast offers a 3,100-lb operating capacity and the industry’s only easy-on, easy-off platform, so you can work with 360 degrees of visibility. No cage, no obstructions. Just performance.
Ditch Witch. We’re In This Together.
SK3000
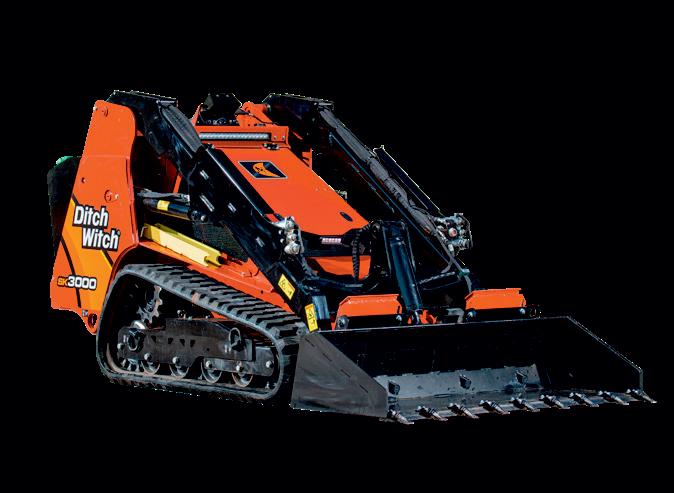
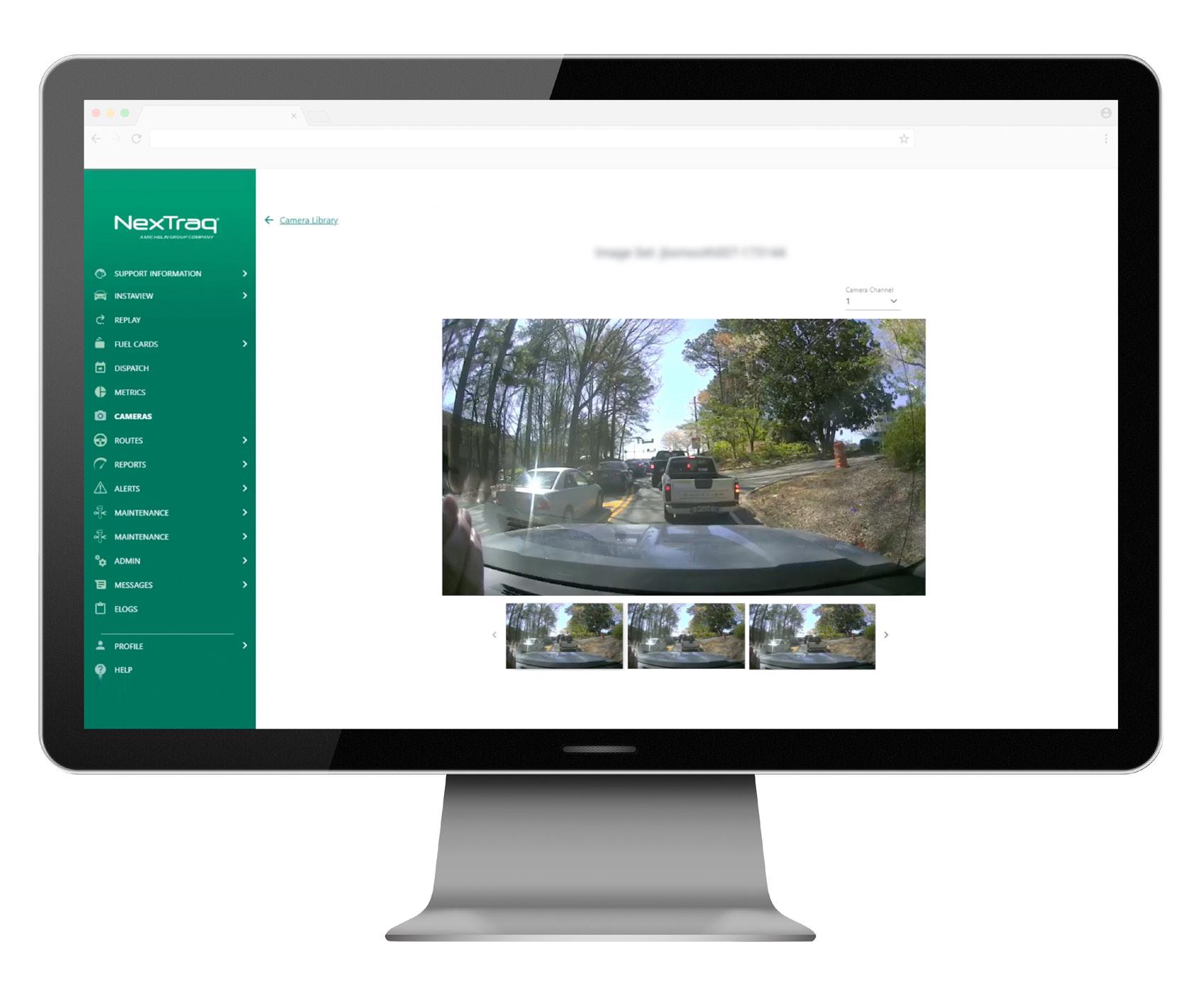
Incorporation of vision technology such as dash cams into telematics systems is helping provide more information for vehicle and equipment owners.
is customizable with various levels of dashboards. Customers can configure which signals they want to monitor and at what frequency. There are also customizable reporting tools through which historical data can be viewed in a way the customer needs.
Danfoss consults with customers to determine what problems they’re looking to solve or where they want to make improvements. “It’s a learning process that we go through together with the customer every time,” says Teplyakov.
It is a growth process, as well. Telematics systems can provide some basic features such as machine monitoring. Adding connectivity can then further expand these features while also making them faster and more automated.
“We always say that changing what you’re already doing to implement connectivity usually will not lead to the kind of success you want. But rather, you should augment the processes that are already in place by adding these data insights into your machine,” says Teplyakov. “Then you can grow from there. As you’re learning more about what the possibilities of connectivity are, then you start looking at more and more advanced features.”
When adding connectivity, he again notes the importance of an OEM understanding its machine and what signals would possibly provide deeper insights to aid end use customers.
Telematics plays an important role in connectivity and the digital transformation of the heavy equipment industry, and is a key enabler component, says Romero. “To create an efficient machine network and deliver the promise of internet of machines, you need to connect them,” he says. “Connectivity technologies [like telematics] and pervasive expansion of wireless infrastructure have been key to this proliferation of connected machines.”
As machines continue to become more connected, it will be critical to also connect all of the different cloud platforms on which they run. Teplyakov says it will be necessary to have the cloud platforms communicate with one another to create machine networks that reach beyond a single IoT (Internet of Things) environment. “That then will lead to connecting not just machines themselves but the actual worksites,” he says.
Doing so would enable not just machines to be monitored but also the flow of various materials and resources. This would benefit a variety of industries including construction, agriculture, mining and others.
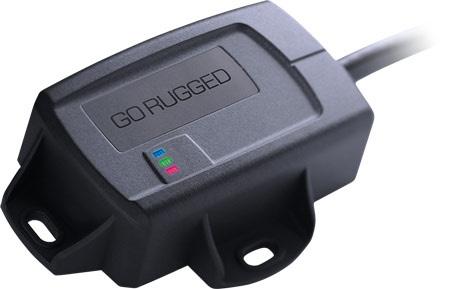
PROVING THE POTENTIAL OF EVS AND ALTERNATIVE FUELS
As alternative fuel and power sources become more prevalent in the heavyduty vehicle and equipment markets, telematics technology will be able to provide insights into how they perform, as well.
Sutherland says there are several alternative fuel vehicles currently in the market which Geotab’s telematics technology supports. It is able to provide not only the day-to-day operational health information but also the potential remarket value of a vehicle.
“We’re proving to some companies who previously thought buying an alternative fuel vehicle was going to be really expensive to maintain in the fifth, sixth or seventh year that actually the vehicle has about double the life of their combustion vehicle,” Sutherland points out.
With electric and alternative fuel vehicles, customers will likely want to hang on to them for 1 million miles, not half a million miles as currently typical with combustion engine-powered vehicles. “It’s pretty impressive to see the distance the alternative fuel vehicles get, and how low a running cost per mile they actually will run,” says Sutherland.
As more alternatively powered vehicles and equipment enter the market, Geotab’s technology can help educate the industry about what is feasible with these new models, says Sutherland. It can help a fleet see what assets could be electrified or operated on an alternative fuel, which he says is key to these new technologies’ uptake in the market. “It’s giving people some benchmarks and trust that when they have to go to an alternative fuel... they will have the confidence to make that decision,” he comments.
The Geotab technology can also be used to provide insights to the manufacturers of these alternatively powered vehicles to help them ensure their designs are meeting the needs of the market.
Sharma believes electrification and automation will provide a big opportunity for telematics and fleet management solutions providers. Vehicles will be more connected and capable of providing more insights into how they are being used. “It enables us to provide a lot more insights to our customers in a very intuitive way,” he says.
There will also be a shift in safety and operations as these vehicles enter a fleet. More operations, such as maintenance, will become automated.
“There’s a big change that is going to happen and I think fleet management services like ours will play a huge role, intermediating the gap between what [fleets] currently have and how they’re shifting,” says Sharma.
Going forward, every component and system is going to be natively connected from the beginning. “As we move forward with the technology, every piece of equipment, every piece of a vehicle will have its own insights,” Sharma predicts. “And the more we learn, the more it will be required for someone to gather those insights and explain or give actionable next steps for a fleet manager or fleet owner to take. That’s the way this evolution is going to take place and it’s more about how you digest the information and present it to the customer so they can take the next steps.” ET
Tenna TennaBLE Beacon Steel Puck
The TennaBLE Beacon Steel Puck is a spin on the company’s Bluetooth Low Energy (BLE) beacon that is encased in steel and welded to the asset.
•Suited for autonomously tracking location of equipment parts and attachments such as buckets and blades •Case design combines an IP67 watertight glass-filled nylon inner casing with a tough steel outer fitting for impact resistance •Welded fitting on asset provides a permanent mounting that can resist extreme forces •Mobile asset tracking app automatically identifies and records asset location when in range and stores the data www.forconstructionpros.com/21354432
Geotab GO RUGGED Fleet Tracking Device
This scalable, flexible and customizable off-road fleet solution can capture rich data on equipment position, fuel use, idling and more.
•Delivers accurate intelligence for real results •MyGeotab fleet management platform integrates with AEMP and third-party devices •IP67-rated device with LTE connectivity lets you monitor assets out on the worksite in real time •Manage both off-road and on-road assets •Open platform and Marketplace offer a variety of third-party solution options www.forconstructionpros.com/21093316
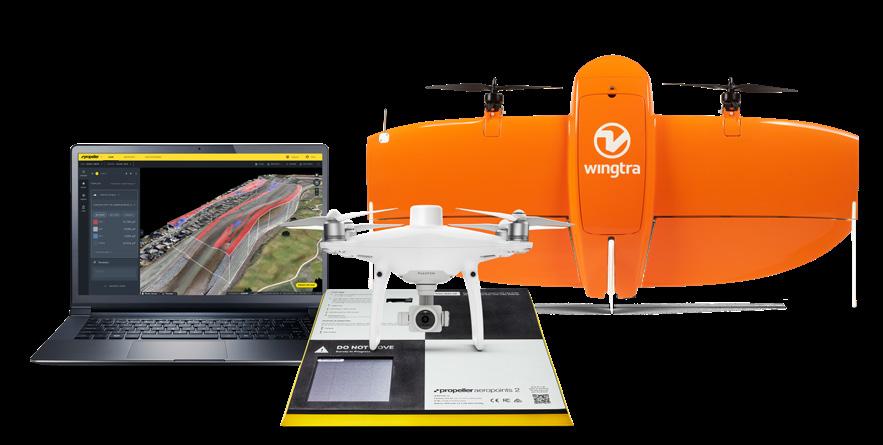
Propeller PPK
This turnkey processing solution harmonizes hardware and software to minimize time in the field for surveyors, reduce drone photogrammetry to drag and drop and make earthworks more accurate.
•AeroPoints eliminate need for complex surveying equipment •Survey using one of the company’s approved drones •Team of GIS experts analyzes captured datasets •Accuracy report for each dataset provides total transparency on survey grade accuracy www.forconstructionpros.com/21485368
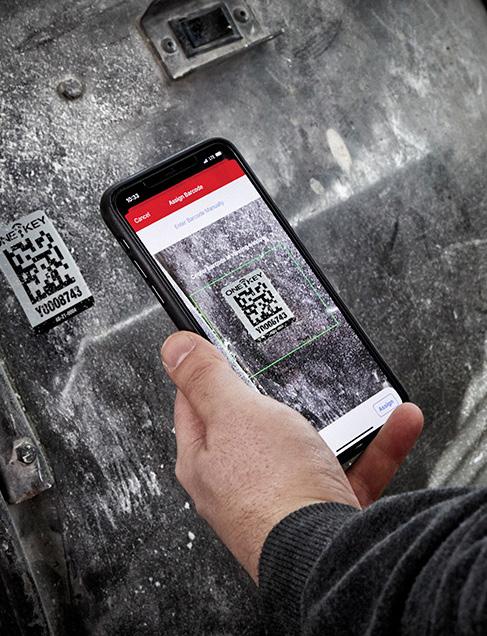
Milwaukee Tool ONE-KEY Asset ID Tags
Durable ONE-KEY Asset ID Tags allow users to easily manage smaller tool and equipment inventories by providing instant documentation as assets are transferred between jobsites and users.
•Users simply scan tags to record time and location data using any smart mobile device with an integrated camera and the ONE-KEY app installed •Available in small (0.69” x 1”) and large (1.5” x 2”) and come in sets of up to 200 designed to adhere to either plastic or metal surfaces •Offer resistance to water and chemical exposure, fade protection from UV light and scratch resistance, plus can maintain adhesion through significant temperature fluctuations www.forconstructionpros.com/21220313
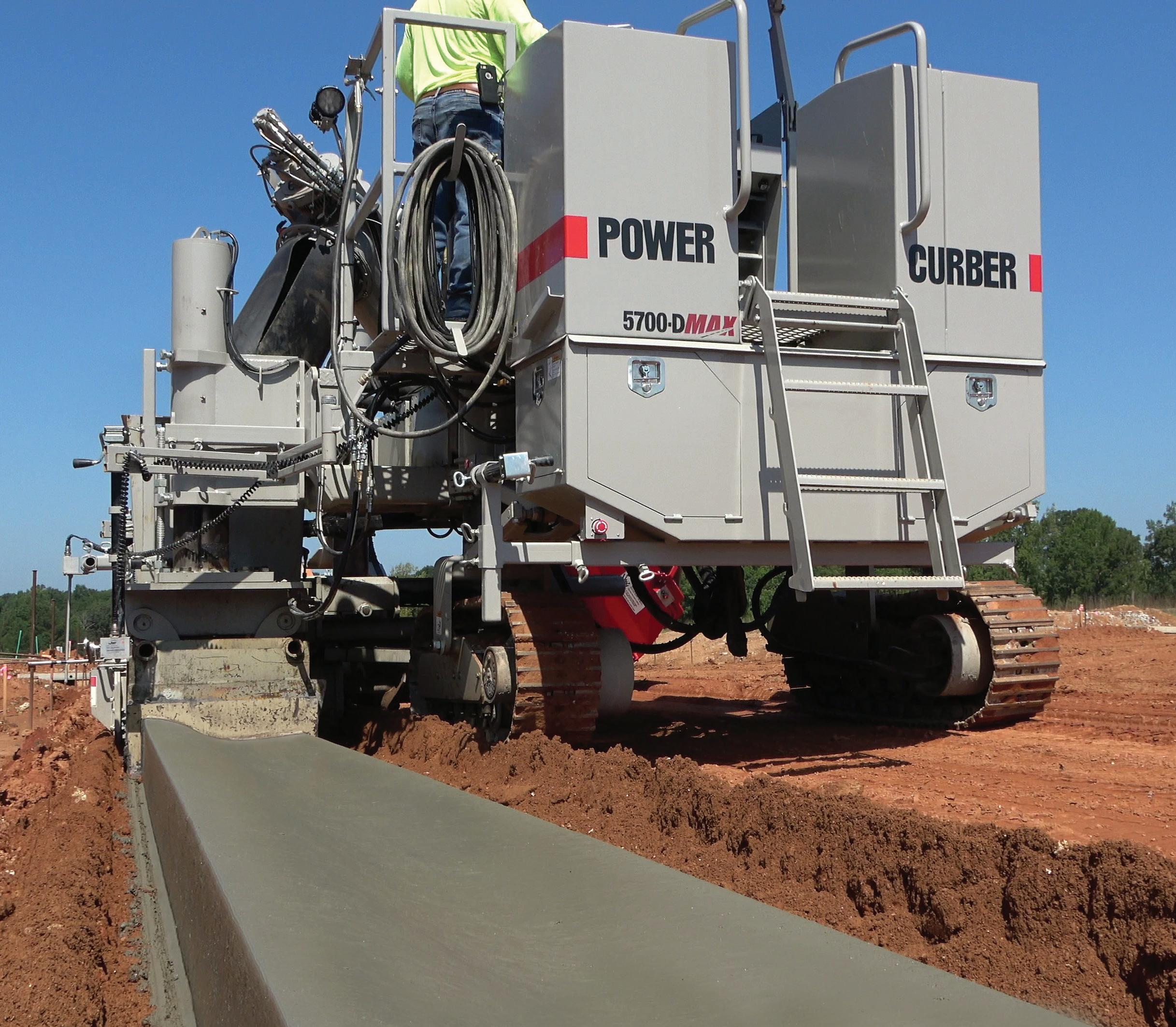
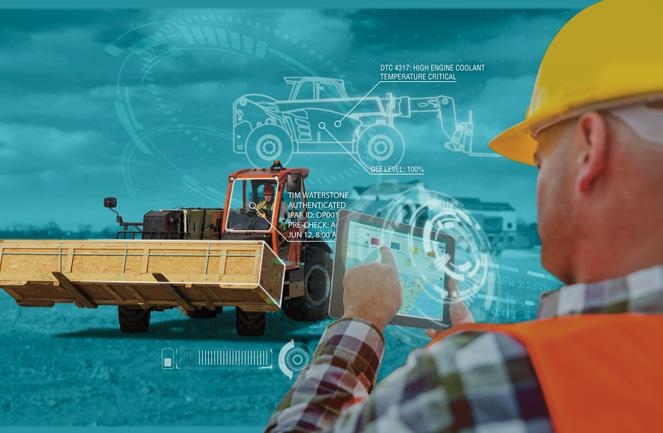
JLG ClearSky Fleet Management Telematics Solution
The ClearSky fleet management telematics solution provides flexible options to access critical engine and equipment operational data.
•Data points include location, engine hours, usage, fuel and battery levels and maintenance schedules and are available in real time for access from desktop or mobile devices •Monitors fault codes and critical alerts can be sent via text and email •Dashboard, settings and widgets are editable and can be prioritized to customer preferences •Available as a factory-installed option for new JLG machines or an aftermarket installation kit to retrofit www.forconstructionpros.com/20867883
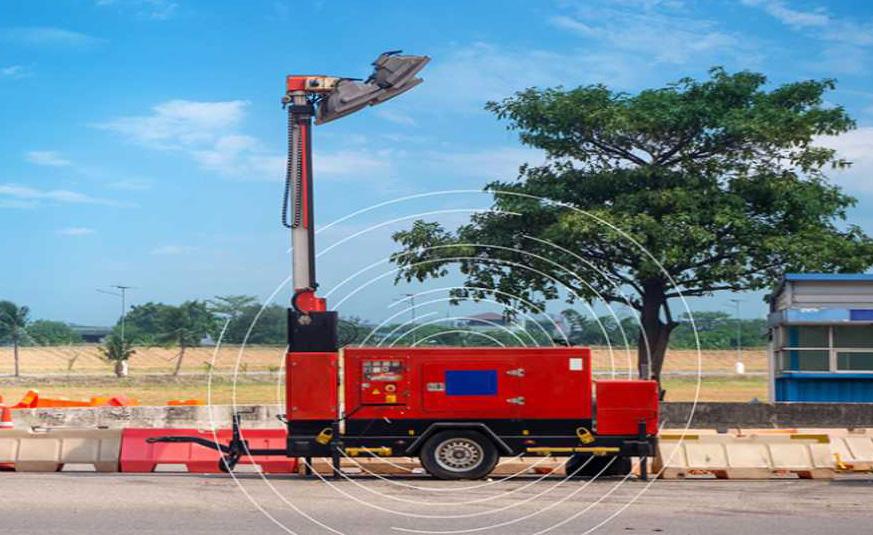
Verizon Connect Asset Tracker for Reveal
Designed for customers running their mobile business on the Verizon Connect Reveal fleet management platform, this asset tracker device offers a compact, discreet solution that is easy to conceal, self-install and self-manage.
•Helps reduce equipment theft, improve utilization and billing and reduce downtime •Replaceable battery extends the life of the device and its value •Enables users to locate and manage equipment as well as vehicles, drivers and jobs online through the Reveal fleet management platform or Spotlight app www.forconstructionpros.com/21497181
Featuring
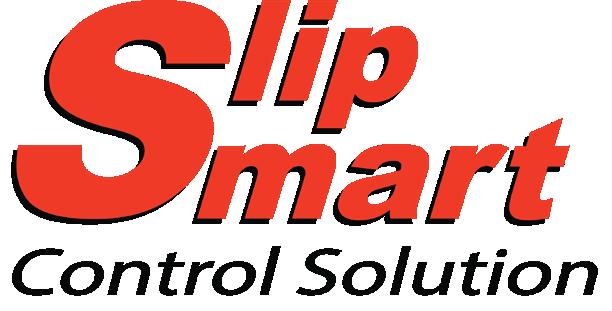
New The Power Curber 5700-D
World’s #1 Selling Curb Machine
The world’s #1 selling curb machine just got better. Power Curbers is excited to introduce the new 5700-D featuring the SlipSmart Control Solution providing operators a new level of precision. Our engineering is dedicated to provide you a reliable and productive machine that is easy to use. We stand behind our equipment with world-class support and unmatched commitment. powercurbers.com
AI Revolutionizes Construction Scheduling and Risk Management
Digital engineering and construction manager Project Controls Cubed offers 4D modeling, virtual and augmented reality services, digital twin technology, virtual planning, scheduling and cost control. The company is contracted for planning, scheduling and cost control on $4 billion-plus West Coast water projects — the EchoWater program, Pure Water program and Sites program in California and the Bull Run Treatment program in Oregon.
Project Controls Cubed is using InEight’s Schedule software to apply artificial intelligence (AI) directly to the construction process at these megaprojects to slash scheduling labor and manage schedule risk. “We understand the power that is behind any schedule, and that’s why we have deployed it,” says Jeff Campbell, director of planning and scheduling at Project Controls Cubed. “We have faith that it is the best solution out there to manage the planning, scheduling and cost control, and it’s predictability certainly has paid off.”
The secret sauce to the program has been AI, which InEight named Iris. “Iris works in the background and starts to predict what our project contributors are going to do with the schedule and the outcome is outstanding,” says Campbell. “The key role in what we do is provide situational awareness to our clients and that situational awareness provides actionable intelligence, which allows the leaders of these big programs to make decisions with confidence.”
SOFTWARE THAT LEARNS AND CREATES
InEight Schedule’s “Knowledge Library” gets populated as you archive or as-build a schedule, cost estimate, etc. “It’s friendly enough where you can use P6 XER files, Microsoft Project files, Excel files. It’s what we call unstructured data,” says Nate St. John, head of product, scheduling and risk at InEight. “Leveraging what we call an inference engine, it will mine this unstructured data and identify matches for recommendations when a planner begins to preplan a new project.”
The machine-learning element built into the software continuously suggests and learns, suggests and learns, says St. John. “It’s a cyclical process. If Jeff or someone on his team declines a suggested match, the computer will remember that, learn it and change the algorithm so that the next time Jeff and his team encounter a scenario with similar attributes, there will be a more accurate suggestion from the inference engine. And it all falls under this AI definition,” he explains.
One big-picture benefit of software that can learn how you think is the way it preserves your experience. Campbell mentions a huge, advanced wastewater treatment program called EchoWater that Project Controls Cubed has been serving since 2012.
“We’ve created and constructed some incredible facilities there. And the people that we work with are probably the most brilliant I’ve ever seen — not just the superintendent, but the program manager and all of his senior people, the project and program managers,” he states. “EchoWater (construction) is coming to an end in 2022-2023, and what happens to all of those incredibly intelligent people? Well, they probably are going to retire; a lot of them already have.
“What we’ve done is captured all of the information [generated over the course of construction] into the Iris AI. So, the next time we build an advanced wastewater treatment program, we can use that knowledge library to create schedule modules that have how much it actually costs to build each component and the actual time — all the actual start and finish dates of all the activities that can go into it,” he points out.
On a program this big, that could include 100,000 activities. “Even with 20 years of experience, I wouldn’t know what to do with 100,000 activities. Well, Iris does. Iris can keep those as schedule modules,” says Campbell.
Project Controls Cubed is also not required to create a whole new schedule when it proposes a different program. “We just go into Iris and say, ‘Hey, we’re creating a new filtration facility.’ And Iris will tell us, ‘Well, you’ve already made a
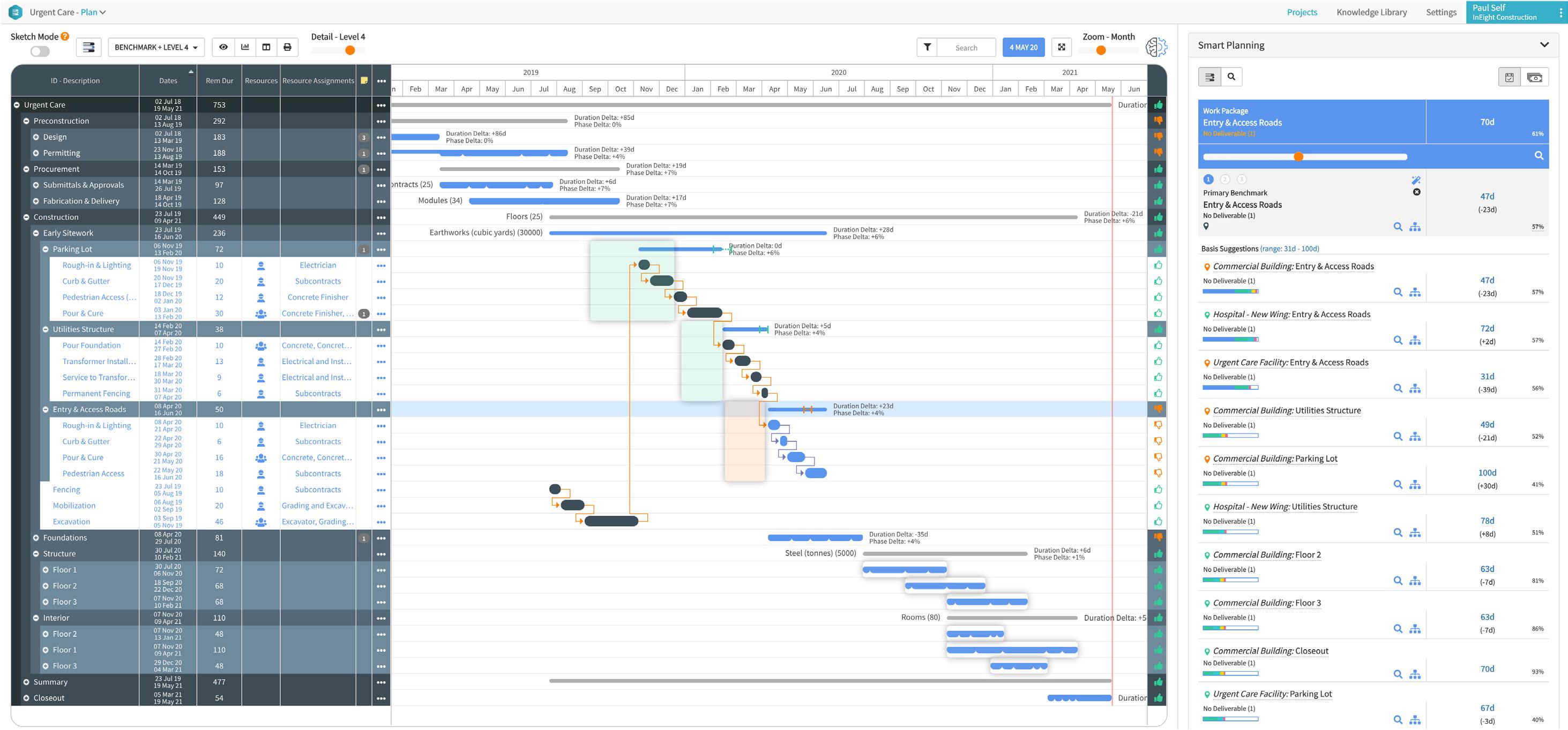
filtration facility before. Here’s what it actually took in time and money to create that.’ And all of a sudden, we have a schedule that would have taken me years to develop,” says Campbell. “So, when we go into proposing a new program, we bring that knowledge to it.”
AUTOMATED RISK-ADJUSTED SCHEDULING
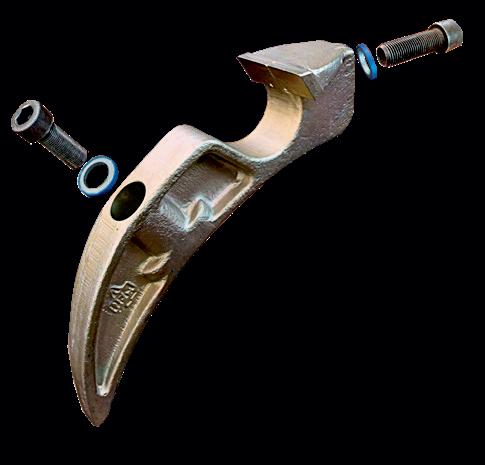
AI also integrates project managers’ ongoing knowledge of job progress with monthly reviews in InEight Schedule to automate risk scheduling. For what Campbell calls “non-scheduling people,” such as program managers and project managers, an email is sent out listing activities for which they are responsible that were active in the just-finished period. The managers update the status of those activities in InEight.
Campbell describes it as a check on the pulse of project progress. “They’re saying, ‘How am I doing with the activities I’m in charge of, according to my deliverables?’ So they take it really seriously,” he notes.
“InEight Schedule allows them to update the schedule and, at the same time, introduce risks. Those risks are kind of like an off-ramp to say, ‘Guess what team, there may be an issue with us making this deliverable, which could impact us getting funding. But it’s not necessarily that I am the cause of that. I am introducing a risk that may be affecting that,” Campbell explains.
“In the past, that would go to a risk manager — someone who’s like a 40-hour a week professional who uses some really expensive software to develop a risk-adjusted schedule that’s actually not a schedule. It’s just kind of a Monte Carlo simulation,” he continues. “We don’t need to have a six-figure income professional risk person on our programs, because Iris and InEight Schedule creates risk-adjusted schedules automatically.”
Project managers introduce risks at project reviews and assign them probabilities — the chance of their occurring as a percentage. Campbell’s scheduling team reviews their updates, assessing risks, and decides whether or not to have Iris create an InEight risk-adjusted schedule. If one is warranted, program and project managers immediately see the risk-adjusted schedule.
“Right away, they’re starting the mitigation planning, which would have taken weeks or months to do on the other side. So, that is another brilliant feature that has really helped us in our programs,” says Campbell.
InEight recently released functionality that allows the cost estimate and schedule to use a unified risk register. The user benefits from work construction planners do up front in developing a risk matrix, import it into InEight Schedule, and now provide a unified point to access the impact of a risk occurring not only measured in days but in dollars.

CRITICAL EVOLUTION IN SCHEDULING QUALITY
Critique that measures schedule quality. “We’re talking about things like constraints, missing logic, missing predecessors, successors, all sorts of great things that we need to make sure are included when we produce the schedule. If you do not have a highquality schedule, then what you’re showing your stakeholders is not very good information,” says Campbell.
“InEight Schedule allows us to be better planners and schedulers because it will automatically identify as you’re building the schedule, ‘Hey, you’re missing predecessors. Hey, you have a constraint. Hey, there’s a gap in your critical path.’ It very nicely and intelligently tells you when you’re not being a very good planner/ scheduler and tells you how to fix it,” he notes. “InEight Schedule keeps us to our high standards.”
Experience using it has convinced Campbell that AI is a linchpin in the chain of events that will take construction performance up to 21st Century standards of business reliability and productivity.
“You have to think about the project superintendent and program manager. They have all the experience, but eventually those great folks are going to retire. Iris and InEight Schedule captures all of their
At Schedule Review, project managers introduce risks to their deliverables and rate their confidence in performance to feed the AI’s ability to automatically generate risk-adjusted schedules and budgets.
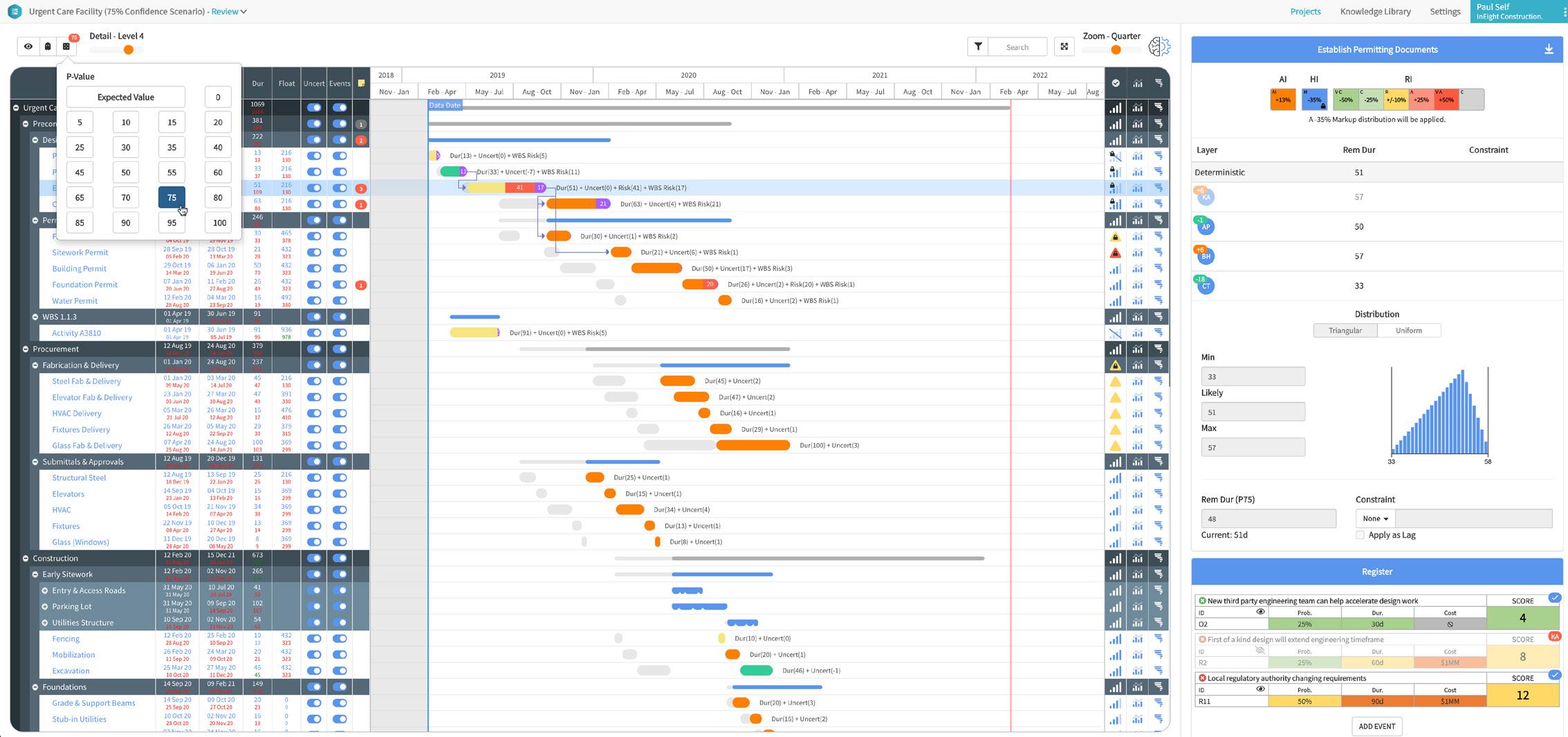
knowledge, and that is how we are going to evolve as an industry,” he states.
“Right now, every single time we have a new project, we start over from scratch, right? But now, the more we learn from past programs and projects, the more we build that Knowledge Library and can apply that knowledge to our new programs and projects, the better we’re going to be,” Campbell adds. “We’re going to have actual cost data, actual start and actual finish dates. So, we will know exactly what it took to build something instead of what it might take to build something in the future.” ET

In-Cab Touchscreen Display
Feed Control Feature
Cabide Cutting Feature
160cc Variable Motor, ECU Torque Control Direct Drive, 2,500rpm Drum, 60” Cutting Width
Patents Pending
Chip Storage Feature
Phone: (405) 542-3520 www.mastodon.com
Mastodon Feed Control Cutting Tooth
Dougherty Forestry Mfg. Hinton, Oklahoma
Bluetooth Shift Ajustment
Bluetooth tuning with a smartphone. Built in GPM tester. Track Operating Hours Track Total Mulcher Hours Track Overtemp Events