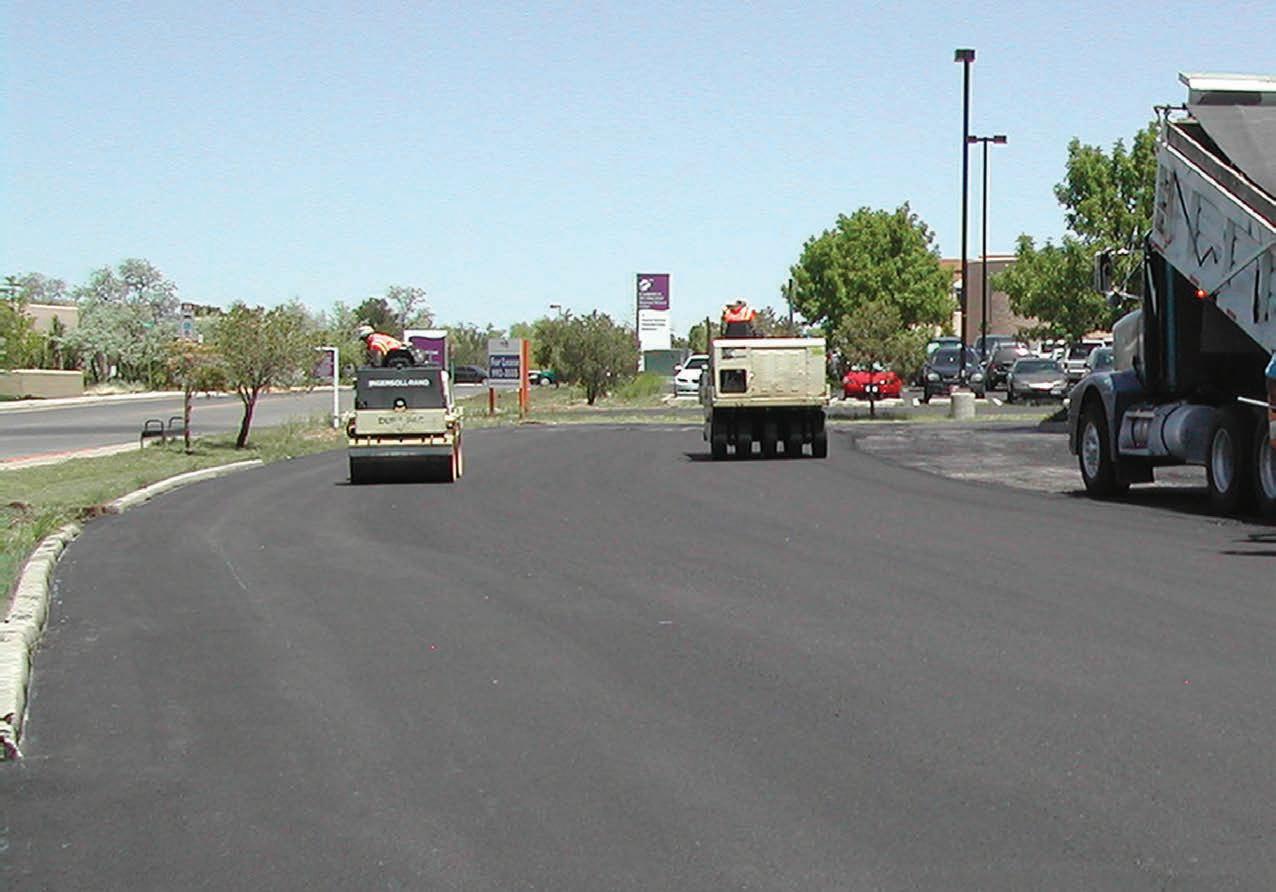
20 minute read
Cracksealing “Best Practices
How to Improve DELIVERY of HMA to the Jobsite
19 tips to help improve the hauling process, from plant to truck to paver hopper
THE HOT MIX ASPHALT that is loaded into a truck at the plant, delivered to the jobsite, then transferred from the truck to the paver is probably the most-important element in a successful paving job. Most paving contractors rely on enddump trucks to get that part of the job done, but the process can be fraught with challenges, which can affect the quality and even profitability of the finished paving job.
After arriving at the jobsite, trucks usually have to wait in line to deliver mix to the paver. Once it’s their turn, they unload the mix by raising the truck bed, and the mix empties into the hopper. It’s this process that can result in pavement defects, stops and starts, and uneven mix distribution if not properly handled.
“Unfortunately, the guy dumping the truck is often the brand-new guy on the crew,” says John Ball, Top Quality Paving. “For some reason crews think that the guy dumping doesn’t have to know a lot about paving, that all they have to do is raise the bed up and take it down. This couldn’t be further from the truth.
“We need to make sure we move the material as a mass, and that means the truck driver needs to be trained in the paving operation,” Ball says. “The driver needs to know how to raise the bed, but not raise it too high or too quickly. The driver has to know how to handle the brakes, how to keep the hopper full without running out, how to keep the tires in contact with the front of the paver, and how to make sure the tires
“When the delivery truck is backing up, it’s important the paver operator focus his attention and not lose concentration,” says John Ball, Top Quality Paving. “He should not be looking at other workers or talking with other workers until the truck gets to the paver.”
aren’t dragging – especially when paving on top of gravel where dragging tires will create a windrow that results in a bump in the paving.”
Here are 19 tips to help make sure the hot mix you’re getting delivered makes it onto the ground so you can construct the best mat possible.
Before the Job
1. Apply a Release Agent. Ball says most contractors know that a release agent prevents the mix from sticking to the truck bed, but many still use diesel fuel instead of any
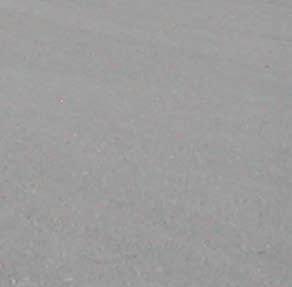
of a number of products designed specifically to be used as a release agent. Not only has use of diesel fuel as a release agent been banned under the Resource Conservation and Recovery Act of 1976, it’s environmentally unacceptable, and its use will compromise the hot mix asphalt, causing it to break down and resulting in a poor-quality mat. Ball says the release agent should be applied evenly on the bottom and inside sides of the truck bed; avoid puddles of the release agent on the floor of the bed. Load the truck correctly. Ball says that improper loading of material at the asphalt plant can result in segregation of the mix and difficulty in dumping the mix into the hopper. Drivers should avoid singledrop loading from the plant, which sets the stage for segregation. He 3. says the best way to prevent segregation and assure an easier transfer of material into the paver hopper is to use multiple-drop loading at the plant. To do this the driver of the truck pulls forward as a pile of mix is dropped into the truck bed. Small trucks might only use two piles where large dump trucks might contain three piles. Tarp the truck bed. Even when travelling short distances from plant to jobsite, it’s important to tarp the load. The tarp should cover the bed and overlap the end and sides and it should be tied down tight. Tarping helps the mix retain heat and protects it from the elements – cool wind or rain. It also helps keep the mix warm if the truck has to sit in line waiting its turn at the site. Tarping the mix also prevents a very thin crust from 4.
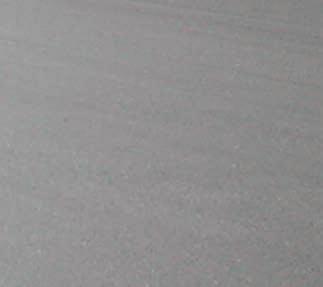

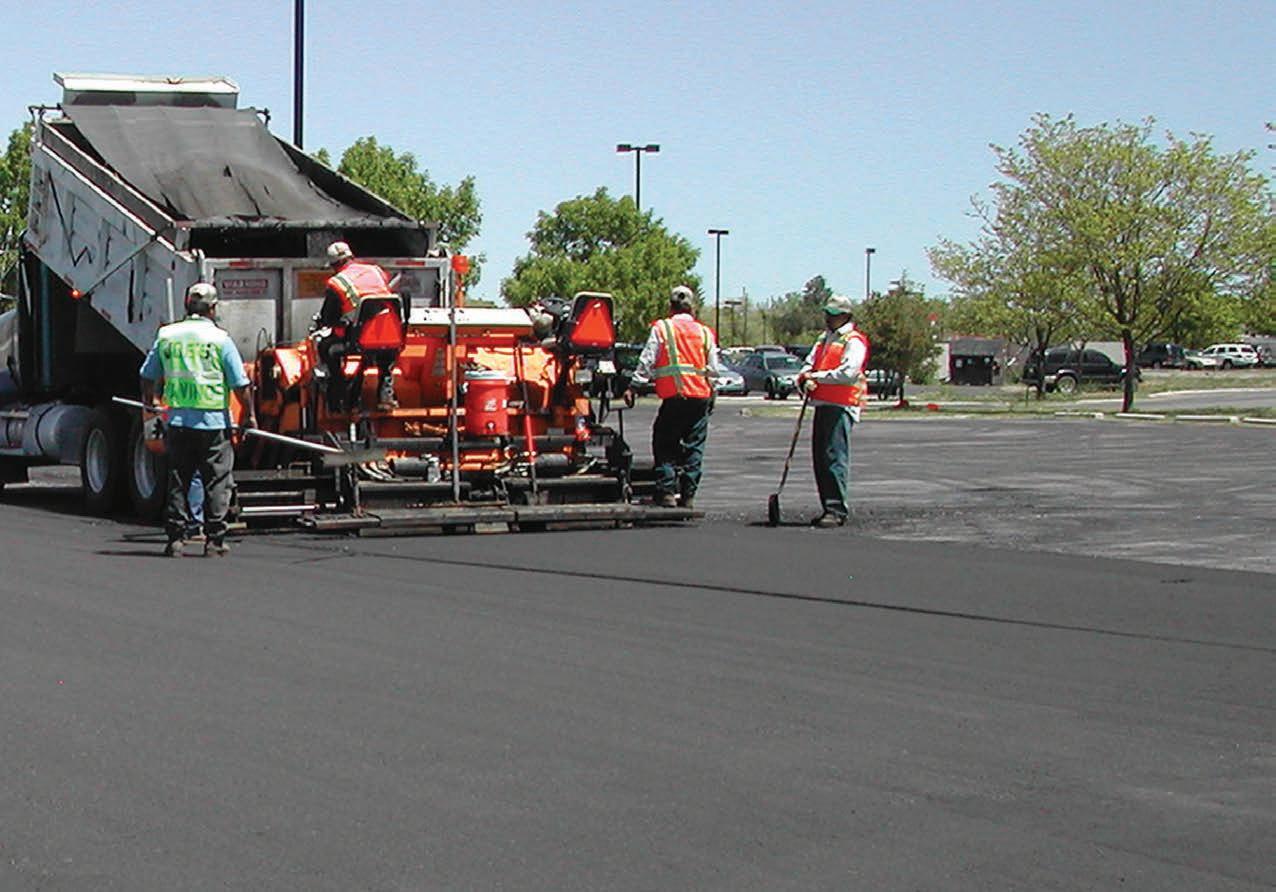
5. developing on the mix surface. This “crusting” can lead to segregation. Review the plant ticket. When drivers pick up the ticket at the plant, make sure to check the time and load order so they know what order they need to line up in at the site. Also check tonnage which tells both their load and provides a running total.
Line up in order – and stay in
order. Trucks need to stay in order in line because that way the timing and temperature is consistent for the paver. “If the trucks are out of order, if truck four goes before truck two, the temperature of the mix in truck two will be significantly cooler by the time it’s placed, meaning it won’t go through the paver as uniformly and it will be more difficult to compact properly,” Ball says.
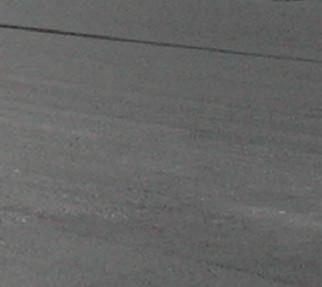
Before Paving Starts
6. Designate responsibility. Ball says a “truck dumper” person should be responsible for the interaction of the haul trucks and the paver. This person needs to make themself visible at all times to the driver of the dump truck, so wearing a safety vest is a must. This is obvious for safety reasons but also makes it easier for the driver to see them. 7. Check for obstacles. This can be the job of the truck dumper or the foreman, but this must be done before the paving starts. Make sure there are no wires or tree branches overhead and along the upcoming paving pass that would prevent the truck bed from being raised as needed. 8. Know each truck that’s dumping the mix. Does the tailgate have a chute or not? Is it a manual, air, or hydraulic gate? The hooks on each are different so make sure you know how to open them.
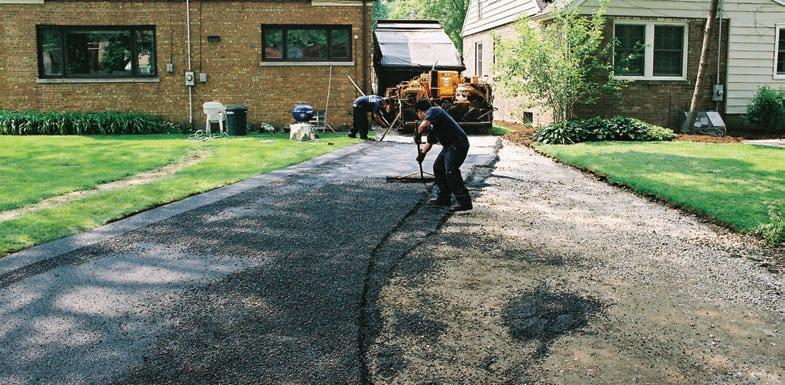
Backing Up the Haul Truck
9. Maintain eye contact with the driver. Ball says the truck dumper always needs to be able to see the eyes of the truck driver. “They need constant eye contact with the driver not only so they can direct the driver when to stop and start but also so that if the truck suddenly accelerates, the truck dumper can move out of the way,” Ball says.
“Eye contact is a safety protection, too.” 10. Don’t bump the paver. Ball says the dump truck should stop about 1 ft. from the paver, then the paver operator should start the machine moving forward, picking up the stopped truck. The key to this process is that the paver picks up the truck instead of the truck backing into and bumping the paver. This approach will reduce mat roughness and screed marks. 11. Center the truck. The truck dumper should step back behind the paver to make sure the truck is centered in the middle of the paver so the mix dumps in evenly across the hopper. “You will only get even distribution on the screed if the material is dumped evenly across the hopper,” Ball says. “If the truck is in the middle of the paver, you’ll have a better chance of getting mix spread evenly across the hopper.
It also helps if the screed is evenly spaced, which will help draw the mix back evenly.” 12. Examine the position of mix in the truck bed. Ball says the truck dumper should look to see how the load is positioned in the truck. He says where the mix is positioned determines how it’s going to flow into the paver and how quickly to raise the truck bed. If the mix is
Raise the bed gradually and at the right time. If the material won’t flow from the truck bed, it’s because the mix is waiting for the pressure to build up and push it out. Raising the bed creates that pressure.
loaded properly – if it’s in two or three piles, centered between the sides -- it’s been loaded properly and it will flow smoothly as the bed is raised slowly (assuming it’s at the correct temperature). But if the mix is all at the end of the truck bed, it will rush out too quickly if the bed is raised too fast.
Raising the Truck Bed
13. “Break” the mix. The hot mix asphalt has been sitting in piles for the trip from the plant to the site – even longer if the truck had to wait in line once arriving at the site. The driver should raise the truck bed just enough so the mix “breaks” and slides against the tailgate. This helps keep the mix together and prevents segregation. Make sure the tailgate is closed! 14. Transfer the mix. Once the mix has gathered against the tailgate, open the gate, and raise the bed as
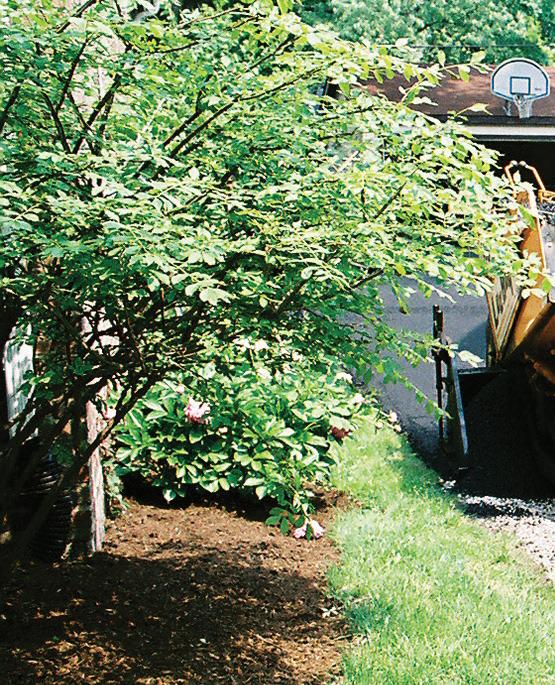
needed to transfer hot mix asphalt to the hopper. Make sure the gate is unlocked before the driver begins raising the bed. “If the gate isn’t open and the driver lifts the bed, the mix will dump out too fast and spill into a pile in front of the paver,”
Ball says. “The weight of the mix will push the truck and paver apart -- and you’ll have a big pile of mix on the ground. Then what usually happens is the paver runs over the pile, creating a bump in the mat.” 15. Make sure the paver stays at the same speed. “The paver needs to maintain a certain speed,” Ball says. “You can’t be going from 25 fpm, to 15 to 40 fpm. The driver of the truck can’t adjust his brakes that quickly so a paver changing speeds means the truck loses contact with the paver. If the paver speeds up the driver has to release the brakes at the right time to prevent mat issues; if the paver slows down it will separate from the truck, resulting in uneven flow of mix, inability to keep the hopper full, or if he slows too much too quickly a pile of asphalt on the
ground in front of the paver.” 16. Don’t allow the paver to “carry” the truck. The raised truck bed
“should not come into contact with the hopper and should not be carried by or ride on any portion of the paver.” If the truck is in contact with any portion of the paver, it can essentially transfer some of the truck weight to the paver, and when that happens, the screed tow-points of the paver can be altered, which can affect the smoothness of the finished pavement. 17. Monitor flow of hot mix. Material self-levels as it flows from the truck.
Once it’s level – once there’s no more pressure on it – that’s when you raise the truck bed. The truck dumper should stand back from the paver so they can see into the truck bed as the driver raises it and mix is released. The driver, directed by the truck dumper and paver operator, needs to get the bed up at the right angle so the mix is flowing. If the hot mix is flowing smoothly and comes out as a line of material across the truck bed, then it’s flowing properly. 18. Raise
the bed gradually – and at the right
time. If the material is not flowing smoothly, the truck dumper or paver operator needs to have the driver make adjustments. If the mix is bunched at the end of the truck bed, don’t raise the bed too high because the mix will just rush out.
If the material won’t flow from the truck bed, it’s because the mix is waiting for the pressure to build up and push it out. Raising the bed creates that pressure. When the mix stops flowing, that’s when you raise the bed another 3-4 ft. When it again stops flowing, raise it another 3-4 ft. Continue this process until almost all the mix has come to the end of the truck, as many as four or five times. Ball says it should take 4-4½ minutes to empty a typical truck and pave 100 ft. 19. Clean-out the Truck Bed. After mix empties out of the truck, the driver puts the body down, closes the tailgate, drives away from the paver, and drives to a dumping area to clean out the rest of the truck bed. Ball says that there’s usually less than a ½ ton of material left in the truck bed, but that material needs to be removed before picking up another load. “Slam the tailgate, clean off the chute, then dump that extra mix off to a designated area where it can later be picked up and thrown away,” Ball says.
“Then make sure the driver lowers the bed, and send the truck back to the plant, completely empty and cleaned of mix.”
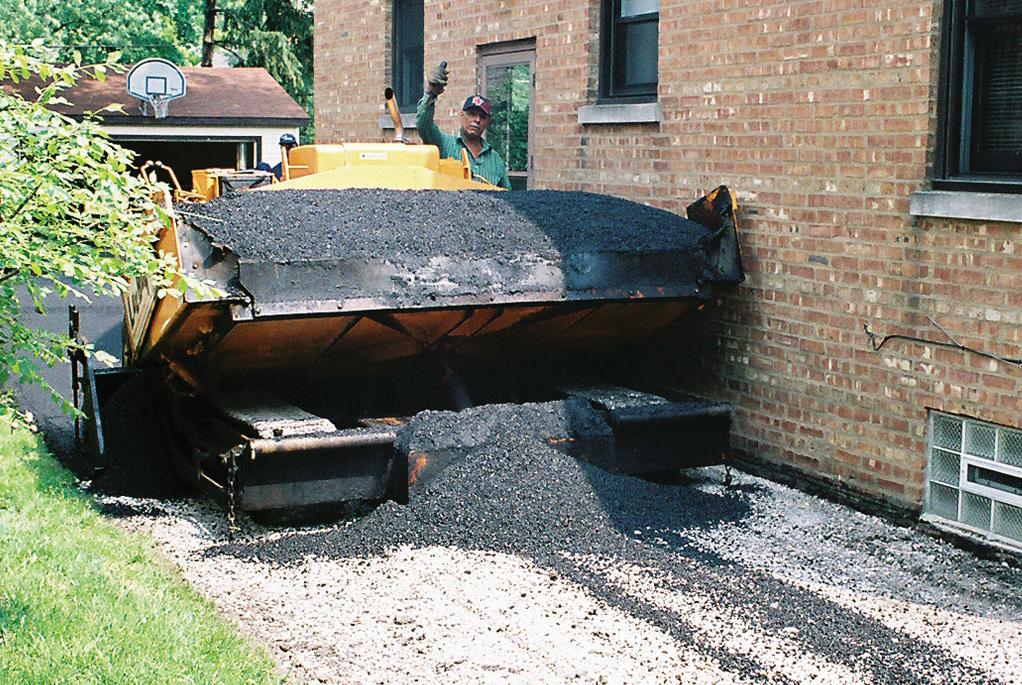

Information for this article was obtained from The Asphalt Handbook, MS-4, Asphalt Institute, and Hot-Mix Asphalt Paving Handbook 2000, Army Corps. Of Engineers.
If mix is left on the ground after the truck pulls away, laborers need to shovel over those piles so you’re not paving over a bump.
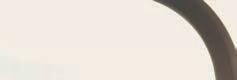


How GPS Tracking Increases Profitability Through Driver Accountability
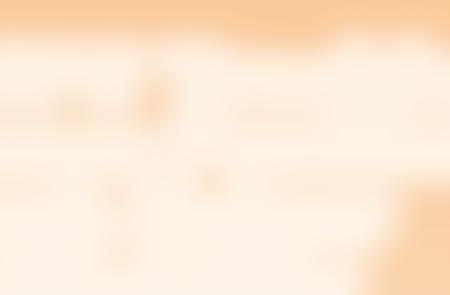
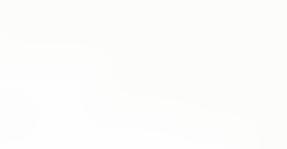

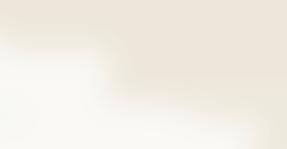
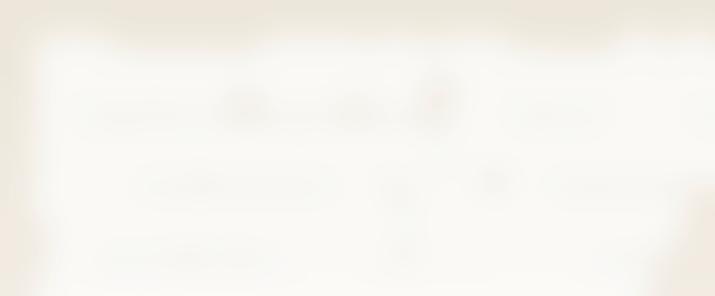
Drivers that are held to a clear, unbiased standard perform better for the company – and themselves
FOR ANY COMPANY with a fleet of light or medium duty vehicles, from service contractors to vendors and those in the transportation industry, increasing profitability often comes down to fostering an environment of greater employee accountability.
The concept of accountability is defined as “the obligation of an individual to account for his/her activities, accept responsibility for them and to disclose the results in a transparent manner.” Implied in this definition is the ability to verify task are completed as expected, on time, efficiently and per company policy. For fleet managers, this can only be accomplished through real-time GPS tracking devices on all vehicles.
After all, it is an established fact that drivers that know they are being monitored by such systems are less likely to make unnecessary detours or stops for personal reasons, may avoid spending unnecessary time at job sites and/or avoid idling the engine while filling out paperwork in the vehicle.
But accountability is not about discovering what a driver is doing “wrong,” it is actually more about what the driver is doing right. Through GPS tracking, drivers can take more ownership for their jobs, have more clarity of tasks and results, can selfcorrect, improve and do not have to be micromanaged. Even well-intentioned micromanaged. Even well-intentioned drivers may discover that there are areas of improvement and efficiencies that could make them more productive. There are also indirect benefits as well. When all drivers are monitored, those not pulling their weight are more easily identified so faster, more productive employees do not have to pick up the slack with extra deliveries or service visits.
Finally, with greater accountability, higher performing employees are more likely to be recognized and rewarded (raises anyone?) based on verifiable performance.
So, with a host of benefits for the employee, fleet managers that have avoided the “leap” to GPS tracking are missing out on a win-win scenario. After all, more accountable drivers lead to greater efficiency overall, which means increased profits. It’s an argument that is hard to deny, particularly as GPS tracking continues to improve while the cost of entry plummets.
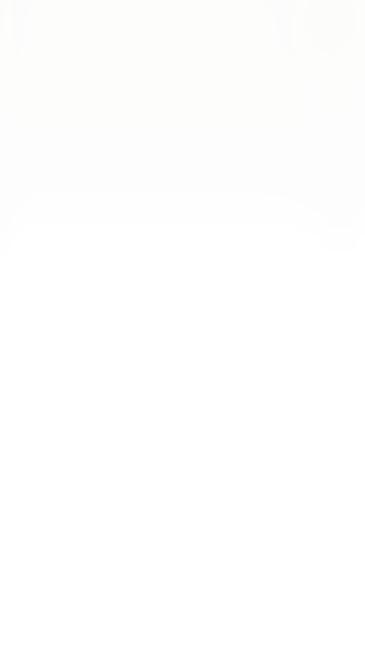
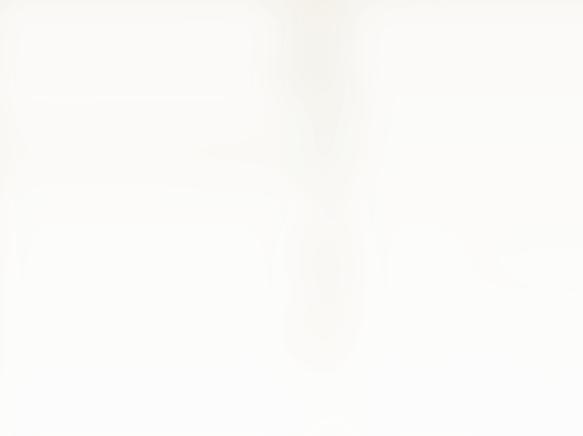
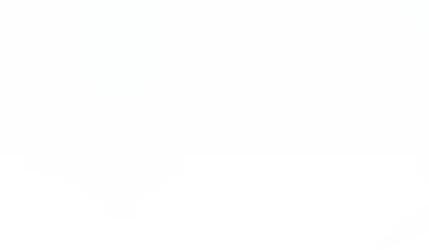
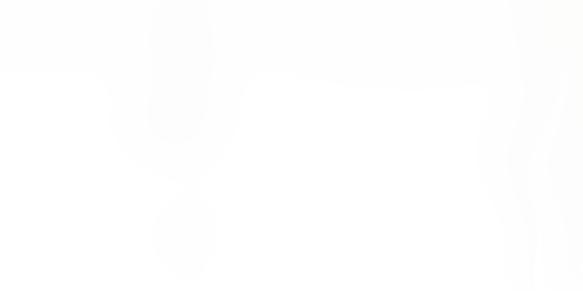
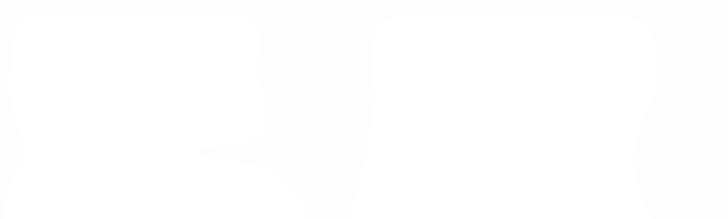
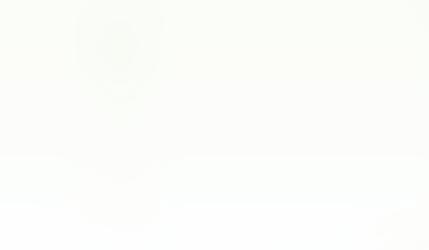
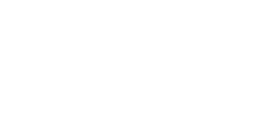
Holding Drivers to a Higher Standard
Although GPS trackers have been around for some time, advances in the technology allows for more realtime tracking and simplified reporting. Fleet managers, after all, don’t want to spend all day on their computers sifting through complex analytical data. Instead, they want simplified, easy to read reports that summarize what they need to know. Fortunately, such systems exist today and at rates less than $20 per vehicle.
The advanced units today allow
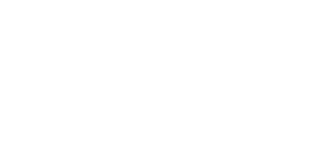
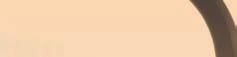
Through GPS tracking, drivers can take more ownership for their jobs, have more clarity of tasks and results.
Photo Credit: Lê Minh/Pexels
real-time and historical tracking of each vehicle in a fleet. This allows dispatchers to assign the closest vehicle to a job, which expedites the service work or delivery and saves gas, labor, and vehicle wearand-tear. It also allows historical routing analysis, which enables even greater routing efficiencies to be determined on an individual or fleet-wide basis.
However, the greatest improvements in fleet management occur when GPS tracking devices are used to hold drivers to a clear, unbiased standard to encourage better performance for the company and themselves.
As an example, when Reilly Construction & Development implemented their first GPS tracking system last year, the Vero Beach,
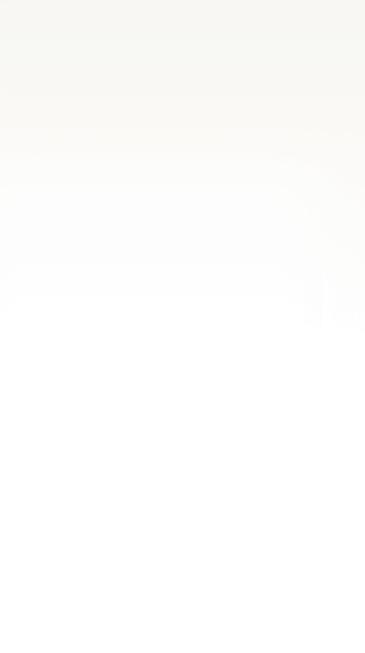
FL.-based residential and commercial construction company benefited from significant productivity gains and operational efficiencies. The construction company has installed company has installed Shadow Tracker Vision Shadow Tracker Vision III GPS tracking III GPS tracking devices from Advanced devices from Advanced Tracking Technologies Tracking Technologies (ATTI), a Houston, (ATTI), a Houston, TX-based designer and TX-based designer and manufacturer of manufacturer of GPS tracking GPS tracking


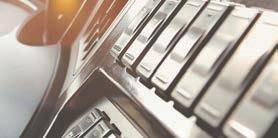
products, on two of their construction trucks.
Compared with typical GPS tracking devices that may only update every few minutes, the device provides real-time location updates every 10-seconds, as well as location, speed and idle time alerts if something is amiss. This data is transmitted via satellite and cellular networks to a smartphone or PC on a 24/7 basis.
With such accountability for how every minute of each day is spent, employees know they are always “on the clock.” This helps to eliminate frivolous or unnecessary stops during the workday, and decreases wasted time during a stop.
“Now we know exactly where our vehicles and drivers are in real time,” Sharon Arnold, office and assistant project manager at Reilly Construction & Development says. “We can spot check our drivers to make sure they are where they are supposed to be and not at unauthorized places because some people will take advantage. That has saved us a few thousand dollars in salary alone. The system more than pays for itself in enhanced productivity.” itself in enhanced productivity.”
On the plus side for employees, On the plus side for employees, the use of such GPS tracking systems the use of such GPS tracking systems helps verify on-time arrival at customer helps verify on-time arrival at customer sites. And automated reporting such as sites. And automated reporting such as that provided by the ATTI system can that provided by the ATTI system can virtually eliminate the reporting virtually eliminate the reporting burden for employee and burden for employee and employer in regard to employer in regard to

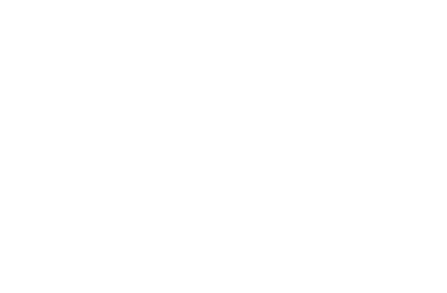
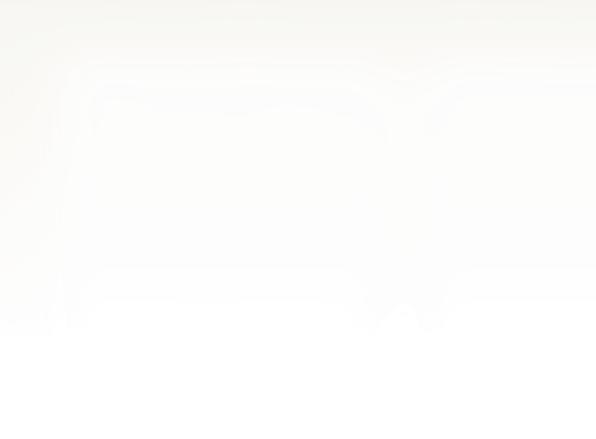










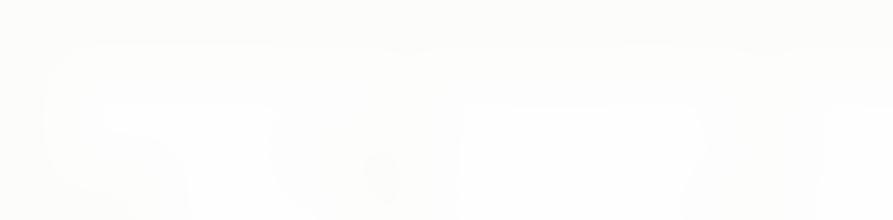


driving logs. Automated exception reporting can also flag potential issues that need to be corrected, such as excess vehicle mileage or idling.
“We are trying to work smarter, not harder,” says Arnold. “We are trying to make things simple and straight forward. With everything out in the open, people know what to expect.”

Boosted Productivity
Once drivers and the work crew know they are accountable for their actions, it is amazing how much more they will accomplish. Using such an approach with advanced GPS tracking commonly improves productivity 10-20 percent while reducing fuel costs 10-15 percent, as drivers start to pay attention to their driving and work habits throughout the day.
Indiana-based Gordon Plumbing Inc., which offers services ranging from small fixes to remodeling and construction, currently uses ATTI’s GPS
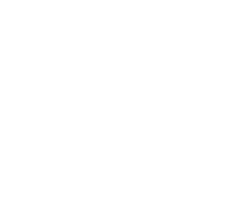
Ihor/AdobeStock
tracking system on 54 vehicles, and has used three different tracking systems over the last decade.
“The [ATTI] system not only expedites job dispatching but also enhances accountability and profitability while reducing costs,” Shannon Allen, Gordon Plumbing service coordinator says.
Allen points out that being able to access a vehicle’s position in real time means “our vehicles can reach customers very quickly when there are emergencies.”
If our drivers on the job need help from a tech specialist, we can immediately find one in their area and dispatch them to that address,” she adds.
According to Allen, the system provides one link for all the covered vehicles.
“The GPS tracking system puts our vehicles on a map, so I can see all of them at once,” she says, noting that the view can be narrowed to any department or [geographic] area, as desired. “It is so accurate that it lets me see exactly where a vehicle is parked.”
Because the GPS system is automated, reports are delivered without anyone having to open software. In addition to the real time views of the activity taking place, next day reports are delivered by email, documenting everything that happened the day before. The reports can be customized, for example, to show how many drivers idled for more than 30 minutes or how many miles were put on a vehicle.
Allen emphasizes that the system can quickly spot driver habits that need correction, such as a driver stopping for 5 or 10 minutes between jobs several times a day.
“With the GPS system, we are able to notice and point out that even five to ten minutes stops between jobs each day adds up to a lot of lost productivity,” she says, concluding however, that her drivers are quite used to the system and even appreciate it when it proves that they are getting to and doing their jobs as required.
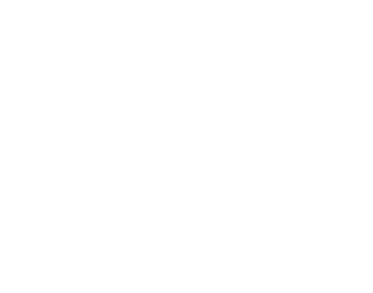

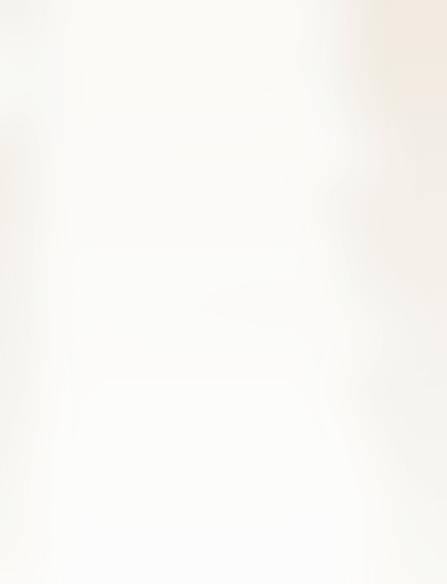