
20 minute read
NPE Buzz
National Pavement Expo Cements 2022 Plans for Charlotte
In-person Expo planned for Feb 23-25, 2022
TO THE CHAGRIN of all who prefer in-person trade shows, the 2021 National Pavement Expo (NPE) switched to a virtual event earlier this year. The successful conference featured 16 timely and relevant sessions plus workshops and live raffles. For those who may have missed it, all sessions are available for ondemand viewing until August 25, 2021.
The global pandemic has taken a vast toll on so many aspects of life, but optimistic NPE organizers have set aside Feb. 23-25, 2022 to get back to business with an in-person Expo in Charlotte, NC. Long-time show attendee and line painter Jim Panzenhagen believes the change of scenery from Nashville will prove to be a positive. “I think a lot more people may attend in Charlotte,” he says, attributing the possible boost to reduced expenses.
“We were pleased with the virtual event earlier this year, but we are really looking forward to getting the industry back together in North Carolina,” Russ Turner, associate show director, NPE says. “You can’t beat the networking aspects of face-to-face interaction. So much information is exchanged in the hallways, on the trade show floors and in the organized networking events.”
Panzenhagen, vice president of JMP Excelsior Services LLC, Oakland, NJ, had planned to be a speaker at the canceled Nashville event. He decided not to speak at the virtual event, instead opting to bide his time and wait for Charlotte. He based the decision on a personal preference toward in-person sessions, particularly the chance to read the room and react to audience interest.
“When I teach my class, I react to what the audience members are doing,” he says. “I can tell if people need more details. Striping is very hands on and question-oriented. In person, you can see attendees perk up and lean forward when they are interested versus having people pull out their phones if they are bored. You can tell if you are going too fast, or if a lot of hands are going up asking questions—that's a good sign.”
As an NPE attendee for the last 20 years, Panzenhagen agrees with Turner when it comes to the crucial networking aspects of in-person shows. Thanks to colleagues all over the country, ideas are shared in all aspects of the business, from the nitty gritty aspects of the job to the front-office tasks of marketing and accounting.
On the Expo floor, attendees can see, touch and even climb on the equipment in some cases—a far cry from mere photos. With a handshake and a smile, Panzenhagen has cemented relationships with equipment manufacturers, many of whom he knows on a first-name basis.
“I run new ideas past them that I would like to see on the machines,” he says. “I discuss problems I have with the machines, and a lot of my suggestions are on the last three or four series of line lasers.”
For those who have never attended or have not been for a while, Panzenhagen believes firmly in the old adage that you will get what you put in. “It's worth every dollar you spend if you go out and talk to people,” he confirms. “You will make more money by learning different things, by networking with people throughout the show. That's the best part. If you network, you will come away with a ton of information and a ton of new contacts, and that's the most valuable part.”
It’s still a ways down the road, but it’s not too early to save the date (Feb. 23-25, 2022) by adding it to Outlook, Google Calendar, Yahoo Calendar, and/ or Hotmail/Live Calendar.
“As in past years, we will eventually roll out SmartSaver rates,” Turner adds. “These are the absolute lowest rates available to attend NPE. Stay on the lookout with the trade publications and at the NPE website. We look forward to seeing you in Charlotte.”

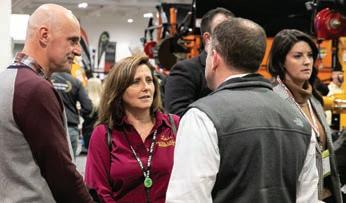
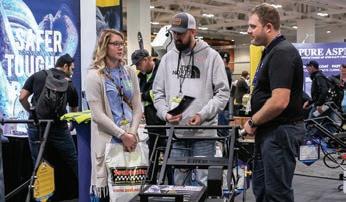
Building relationships with manufacturers and others in the industry is a reason attendees keep coming back to NPE.
PAVEMENT MARKING
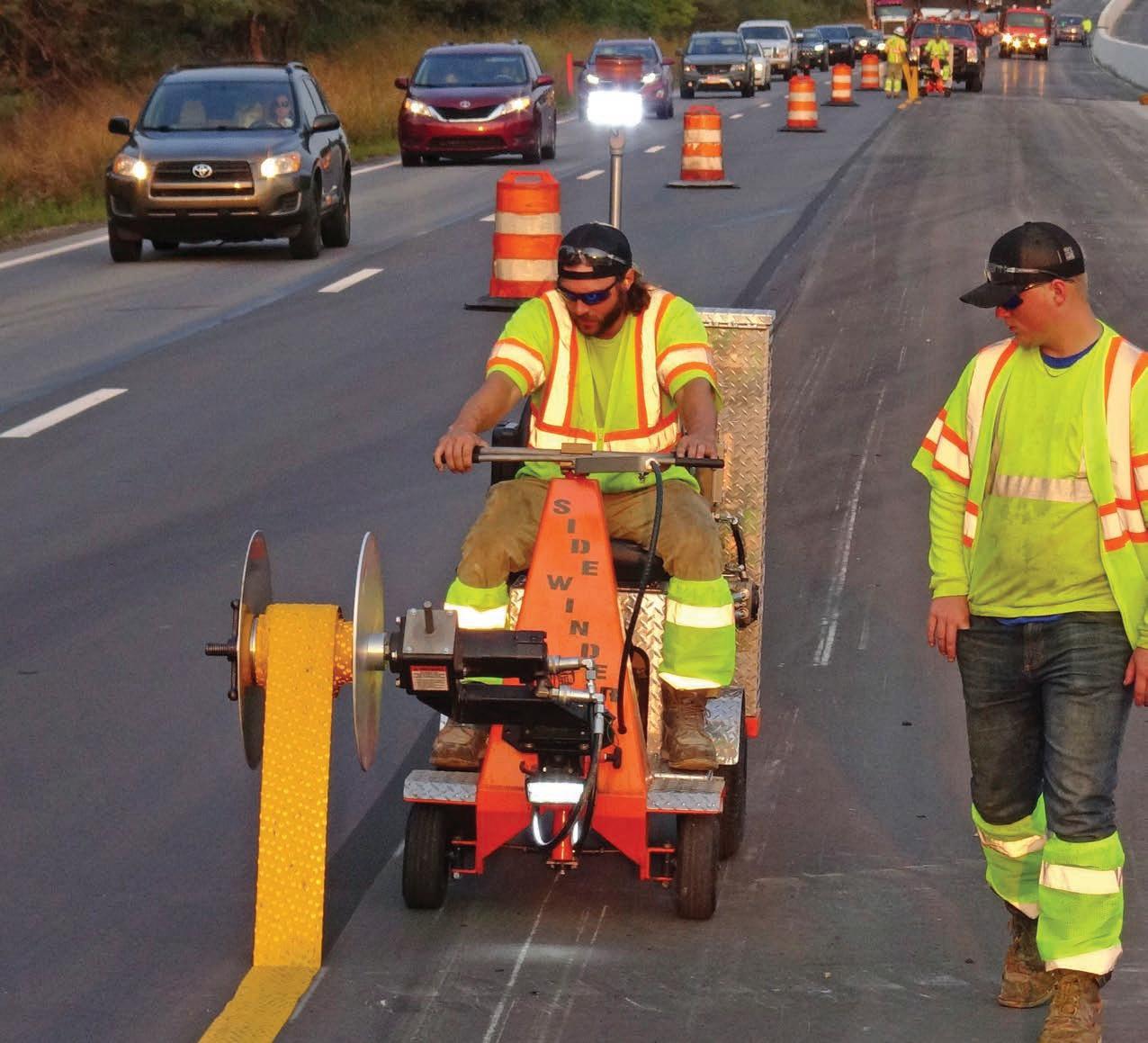
Advancements in the INDUSTRY
New technology helps contractors place and remove temporary road marking tape
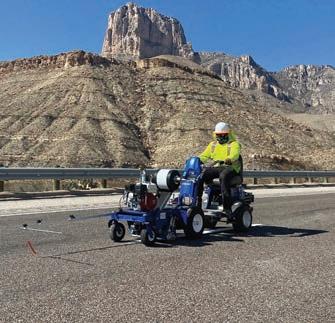
TRAFFIC SAFETY IS a top priority of DOTs and highly visible traffic markings play a key role in ensuring that automobiles stay in their lanes – even during challenging weather conditions. The most common traffic markings include paint and thermoplastic, but permanent traffic is quickly becoming the preferred choice on high-traffic roads because of its high visibility – especially at night and in the rain. Temporary traffic tape is also gaining popularity as it can be easily applied to work zones and removed when the road work is complete. Although tape striping isn’t new to the industry, there has been recent introductions in technology to help contractors place and remove the tape faster and easier.
<<The Side Winder helps transform a difficult, messy task into an easy and efficient process.
Tape Application & Process
There are a variety of machines to apply pavement marking tape, either walkbehind or ride-behind. The type of tape used depends on the project. Temporary tapes can be applied to work zones or other short-term project and then removed when the project is completed. Permanent tape can also be used on roadways and intersections. In cold weather climates, tape can be inlaid into asphalt during paving to reduce wear or can be grooved into pavement to help reduce damage from snow plow operations.
“Before applying tape, contractors should prep the surface,” says Mike Vangstad, global product marketing manager for Graco. “Remove the existing lines and clean the surface with a GrindLazer. Then, use an air compressor to blow all the excess debris out of the area, you want it nice and clean. In most permanent tape applications, contractors will put down a primer and let it set for about 10 minutes. The traffic tape then goes down on top of the primer.”
Graco has an automated tape applicator in the TapeLazer HP Automatic which Vangstad says makes the process as easy as applying paint.
“Finally, tamping of the tape is necessary to ensure proper adhesion,” he adds. “It is important to note that contractors should follow tape manufactures recommendations when applying traffic tape as there are specific requirements such as weather conditions that must be met.”
Tape applicator machines have also been designed to cut the tape without having to stop.
“The Epic Solutions TA5000 tape applicator has been in the market since 2017 with hundreds of thousands of feet applied by applicators,” says Tom Heine, national sales manager with Epic Solutions Inc. “From cutting tape on-the-go to programable patterns which eliminates the need to mark out projects, the TA5000 is an industry proven product which focuses on safety, speed, accuracy and overall improved production.”
The TA5000 operates at 3-4 mph (average) and holds a 12-in. roll of temporary or permanent tape. Heine says the programmable timing system eliminates having to measure out and cut patterns ahead of time. “We developed this machine with the contractor and municipality in mind,” he says. Tape application, similar to paint striping, can happen any time of the day — specifically, at night when traffic is less busy on roadways. However, visibility deteriorates for your crew and the traveling public after the sun goes down. Proper reflective PPE and adequate work zone lighting is imperative.
“A lot of projects happen at night,” says Vangstad. “That is why we can equip the TapeLazer with LED lights

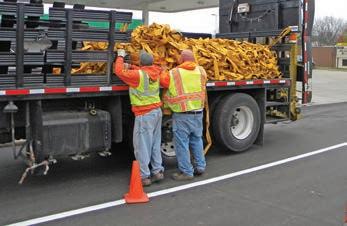
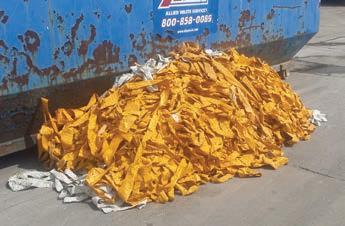
Removing tape by hand can be a messy, time consuming process. The Side Windercan help with the removal process, creating neatly wrapped tape rolls that are more manageable to dispose.
and lasers to help the operator complete the job efficiently and safely.”
Removal of Temporary Tape
While putting down the tape is easy, removing temporary tape can be a physically demanding job. It requires bending over, putting strain on the back while pulling straight up again and again, bunching up the tape in a wad. A contractor came up with a solution, the Side Winder.
“This machine has transformed a difficult, messy manual task into an easy and efficient process,” says Jim Shea, inventor of the Side Winder. “With the introduction of the machine, the task is now less physically demanding than manually
removing temporary tape, with few steps required from tape removal to disposal."
By utilizing this machine, contractors can easily reel the removed tape onto a manageable core and in less time than manually removing tape. Once full, the core can be removed from the machine and disposed on a support vehicle. “Cleanliness of removal is also a major benefit of the Side
Winder -neatly wrapped tape rolls vs. piles of messy tape add tremendous value to the contractor,” says Heine. “The methodically wrapped rolls save much needed space on the support vehicle. Also, the Side Winder utilizes less man hours to complete a temporary tape removal project, resulting in a reduction of traffic accidents and disruptions.”
Ideally, it takes two people to complete a removal job, the operator and a “tendor.” A good tendor will pre-scrape the beginning of each tape start or break point, to ensure a smooth transition between tape breaks or skips. If the tape breaks halfway through: • Peel up tape using scraper or putty knife • Lay the tape around the core then around until it sticks to the backside of the tape • Slowly rotate the spool so it creates enough tension to allow the tape to grab and rollover itself “The structural integrity of tape will always impact the effectiveness of removal,” says Heine. “The Side Winder dramatically increases the overall efficiency/productivity of temporary tape removal and with newer and stronger temporary tapes on the horizon, the Side Winder will continue to add value to the industry.”
Temporary pavement markings such as tape are essential for motorists to guide them through work zones, day or night, through any type of weather. Durability, cost, ease of removal and implementation are all factors that contribute to the decision as to what type of marking to use.
Always consult with equipment manufactures before operating and understand the specifications to ensure success of any job.
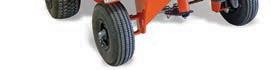
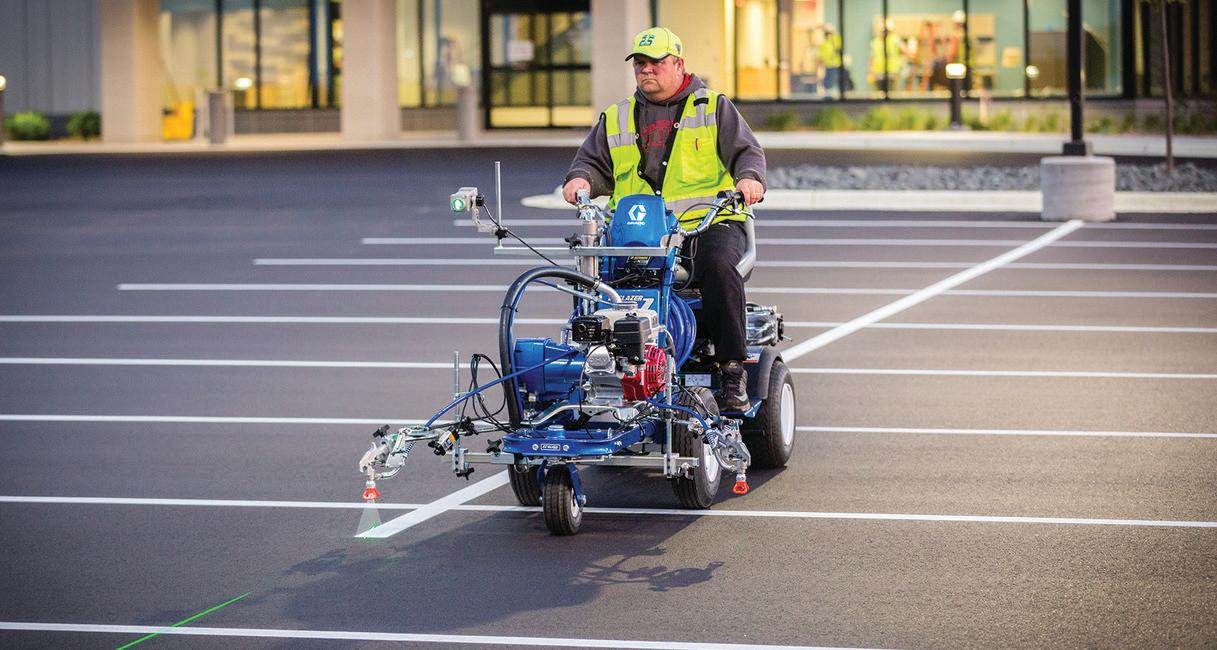

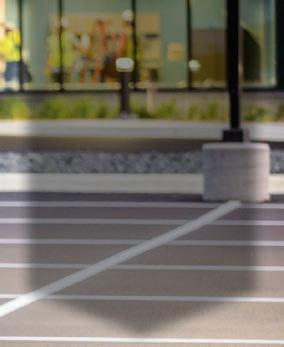
Early Season Striping Best Practices
13 productivity tips to help improve profitability for pavement marking contractors in 2021 and beyond
WHILE THE CORONAVIRUS pandemic may not have shut down your operation, it's sure to have slowed them, creating a backlog of work for 2021. That, combined with a tight labor market, makes productivity key to profitability for pavement marking contractors. The quicker you can get off (or on) a job, the more jobs you can do, the more revenue you can bring in and the more clients you can keep happy.
The important thing to keep in mind when examining productivity is that the changes don’t have to be major. Obviously, a big change – adding a crew, for example – will significantly improve the number of jobs your company is going to complete. But often as important are the small changes that, while possibly insignificant in and of themselves, can make a huge impact when compounded over numerous employees and numerous jobs. Something that can save one worker 10 minutes on a job, multiplied by three people on site, saves 30 minutes per job. If your crews complete three jobs a day, that’s 90 minutes – or 7.5 hours over a five-day work week, adding almost a full workday to your week.
So while looking for ways to improve your production, don’t overlook the tweaks that can really add up over a week, a month, a season and beyond.
Planning & Preparation
1Take advantage of drones to bet-
ter prepare your crew. Drones aren’t only for marketing. While skyhigh photos and before-and-after videos of the great work you’ve done certainly showcases your company, using a drone in advance to walk a crew through a job from start to finish can make the job go quicker once on site. Workers will be familiar with the site, they’ll know where to start and where to end each day (assuming it’s not a one-day job), they can be made aware of troublesome or challenging areas, safety issues for them and for pedestrians and traffic can be highlighted and barrier locations can be shown so crews know exactly what to put where when they pull up on the job. Areas where two-color striping is needed can be highlighted, along with crosswalks, fire lanes and other specialty
Stripers such as this Graco LineLazer 3900 V, feature auto-layout, which eliminates measuring and chalking of a parking lot.
Illustration: graphego/AdobeStock
markings. And when combined with other measuring technology, you can compare actual measurements with blueprints to avoid any last-minute surprises.
2Organize your truck. This might seem like a suggestion that won’t have much impact, but how you organize your tools and equipment in the truck you take to the jobsite can cause downtime – if, for example, you left a tool at the yard, you don’t have enough paint, or everything was thrown in the back and a tool or stencil or part of a machine was broken. Most contractors use their pickup truck to haul a trailer outfitted for striping. Some contractors opt for vans or box trucks, but whichever approach you use, organize the truck so everything – paint, tools, stencils, buckets, cloths, tips, brooms, blowers – has a place and is locked down so it doesn’t slide around during transport. Create racks for stencils, locks for stripers, hangers for blowers. Make sure paint buckets are secure. If you have more than one striping crew it can be helpful if all your trucks are organized and outfitted the same so that a person moving from one crew to another knows where everything is.
3Assign an organizer. Along with organizing your trucks, it’s a good idea to assign someone to make sure each truck is outfitted and ready to go for the next day’s work. This can be someone on the crew that’s using the truck or someone who stays at the yard with other duties but who checks and replenishes the trucks when they come back. Crews need to tell this person if there’s a problem with a piece of equipment, but otherwise the responsibilities should be to make sure stencils are clean and ready to use, tools are clean, paint is mixed, the right colors and correct amounts are in the truck for the next job. While this job could be done prior to heading out, it’s best to do it the day or night before so there’s time to solve any problems that come up.
4Mix paint beforehand. There’s no reason to waste time on a jobsite mixing paint in 5-gal. buckets by hand. Invest in a tumbler or shaker that can handle 5-gal. buckets and assign someone the job of keeping paint mixed for the crews. Paint should last at least a week or two before remixing is needed.
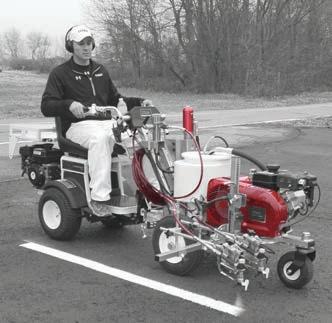
5Take measurements yourself.
Spend some time talking with veteran stripers and just about all of them have a war story about a job where they followed the blueprints – only to find the blueprint measurements and the actual measurements didn’t match. If they were lucky, they discovered the problem before applying paint, but often that’s not the case. Take the extra few minutes to do your own measuring. It might slow productivity on the front end of the job but it can be a huge savings on the back end of the job if you learn to late that the layout you striped and the plans you were given don’t match. There are line stripers on the market today that have "measure mode" which will measure while you push the striper – or better yet ride along on a driver.
6Don’t avoid chalking a layout. Veteran stripers who insist on measuring and snapping chalk lines might have a point, especially on complex or large jobs. While chalking a layout certainly is time consuming, it does enable contractors to step back and view the entire job to see if there are any layout problems or any mistakes – before putting any paint on pavement. Preventing mistakes and reducing call-backs increase productivity, too!
7Buy a premarked tape. Regardless of how you approach layout, a color-coded premarked tape should be a staple of every striping crew.
8Join “the chain gang.” An easyto-make, easy-to-learn chain tool makes laying out parking stalls of any angle a quick and error-free process for three people. Invented by Mick Vinckier, Miktom Parking Lot Maintenance, and introduced in his “How to Stripe the Tough Jobs” seminar in the 1990s at National Pavement Expo, the chains enable laying out of 90º stalls without using the 3-4-5 triangle method and 60º stalls without a tape measure. The chains are particularly valuable when striping inside or outside a curve or laying out stalls on a circle – all with no math. The conventional method of measuring and marking outside stall width and inside stall width is time consuming and math intensive. It’s easy to make a mistake in the calculations or layout. Plus, because curves often aren’t consistent, contractors end up eyeballing, which creates its own problems. The chain tool saves striping contractors countless hours, eliminates layout headaches, and most importantly results in a near-perfect striping job on curves. The tool can be made easily and inexpensively using two chains (18 ft. each is good) with a snap hook on each end. If you’ve never used one, ask a striper who has.
The Right Equipment Speeds Layout & Striping
9Consider auto-layout machines.
Auto-layout devices, which operate similar to a skip-timer, are designed
to eliminate measuring and chalking of a parking lot. Contractors either enter information from blueprints into a calculation system on the striper or walk the lot and let the striper do the measuring. The auto-layout calculates the measurements for the parking lot and determines the number of stalls needed. It then directs the operator to spray dots on the pavement to create the layout. Once all the dots are marked, the striping then becomes a game of “connect the dots.”
10Look into lasers. The mostrecent innovation in pavement marking, lasers can help layout and can also improve accuracy – to say nothing of saving time. Lasers are available to be retrofitted on older stripers and some new stripers are available with lasers already on them or as options. When it comes to lasers you have two options – dot lasers and line generating lasers. The dot lasers are best used to mark your start and stop when placed directly under the spray gun – eliminating the need for shingles. Linegenerating lasers, on the other hand, are best for producing laser-accurate lines on the parking lot – eliminating the need for string lines.
11Pay attention to ergonomics & convenience. Part of productivity is helping your workers maintain their energy and keeping them from getting worn out as the day progresses and as days turn into weeks and hot summer months. Manufacturers are paying closer attention to ergonomic features that make operating a striper easier, including controls within easy reach of the operator’s fingers, handlebars that can be easily adjusted for the comfort of each operator and gun mounts that are easier to change. Just as ergonomics is important, in this day and age comfort is the name of the game, too, and manufacturers are including features such as cup holders, storage trays and phone charging ports. Your operators spend much of their day walking behind (or riding behind) units that weigh up to 300 lbs. when full with paint, so the easier and more comfortable you can make it for them the greater their productivity will be – especially at the end of a long day in the sun.
12A machine for every color. While this does require significant investment, if you’re striping large enough properties and you’re regularly faced with striping two or even three colors, dedicating a machine to each color eliminates cleanout at the site, saving time on the job and avoids the problem of how to dispose of the cleaned out paint. Dual color machines are also available – saving you not only money on equipment but also room in the trailer.
13Get some wheels. Introduced to the industry in 1996, attachments that convert a walkbehind striper to a ride-on striper are probably the most-important productivity development to come along since striping contractors went from hand rollers to spray machines (or from nails and string to chalk lines). Attaching a driver to a walkbehind striper enables you to stripe much faster. You can put down more paint in less time than by walking. Productivity, anyone? They’re also a big advantage on a large parking lot where the staging area (and paint) is at one location and the striping is done clear across the lot. Driving back (they travel up to 12 mph) to get more paint takes less time and is way easier for operators. Contractors who rely on driver attachments get so used to them they rarely get off the unit – even on small lots. Users become adept at maneuvering and striping cleanly and accurately even in tight spaces. Use of a driver attachment reduces the wear and tear on your operators because instead of walking, pushing a striper all day, they’re riding. At day’s end they’re less tired and less tired means they’re likely to more productive. Plus, the accumulated wear and tear on operators is reduced so they’re likely to more productive over the following days. Equipment manufacturers now make their own driver attachments and sell units designed specifically for the attachment and with the attachment already included. The drivers are available either gasoline or battery powered.
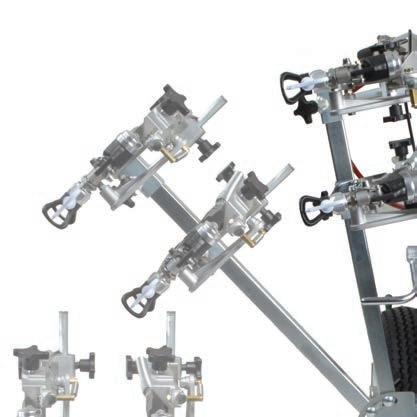
Manufacturers offer features and accessories that make operating a striper much easier, such as Titan's Smartarm assembly that pivots and lifts. This makes line adjustments quick and easy, locks in at any angle for curb striping and offers easy-to-adjust gun height.
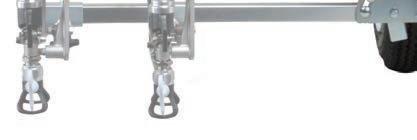
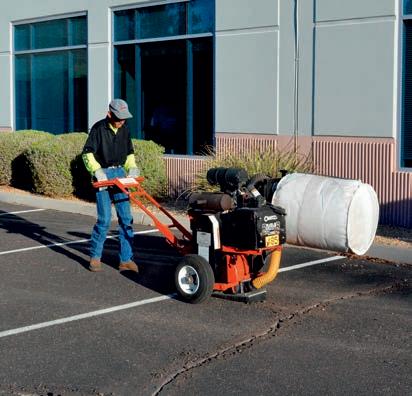

Rout Clean Seal
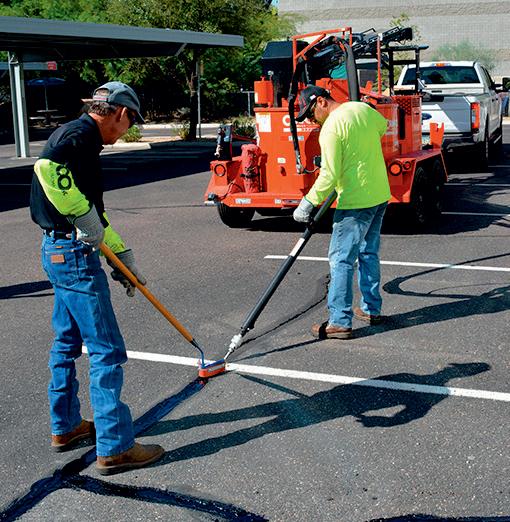
Spring season is an ideal time to crack seal because pavement cracks are at their mid-point and temperatures are moderate. Studies by the National Center for Asphalt Technology found that crack sealing is proven to extend pavement life for good, fair and poor pavement conditions.
1 2 3
Prepare cracks with a Crafco Pavement RouterTM
Placing Crafco high-quality sealant into a routed reservoir provides a solution proven to double sealant service life vs. non-routed and sealed cracks — making the most of your investment. The Crafco SelfPropelled Pavement Router with Dust Control prepares cracks responsibly, keeping respirable dust and silica exposures below Occupational Exposure Limits (OELs).
Clean routed cracks using the Crafco Crack-Vac 2TM
The Crack-Vac 2is uniquely designed to be the most effective at cleaning cracks. It removes dirt and debris from pavement cracks, virtually dust-free, with compressed air, ensuring proper preparation. The Crafco Crack-Vac 2 reduces respirable dust and silica exposure, achieving the industry’s lowest OELs.
Melt and apply sealant with Crafco Melters
Awarded ROADS & BRIDGES magazine’s “Contractor’s Choice” for 7 years running, the Crafco Super ShotTM melter is a model of quality, durability, safety, ease of use and productivity.
NON-ROUTED
Simple Band-Aid Configuration
44.5*
MONTHS
SEALANT SERVICE LIFE ROUTED
Standard Recessed Band-Aid
94.5*
MONTHS
SEALANT SERVICE LIFE
Cracks sealed using Crafco high-quality sealants have been proven to extend sealant service life for more than 7 years in Asphalt Cement (AC) and 21 years in Portland Cement Concrete (PCC) pavements.*
