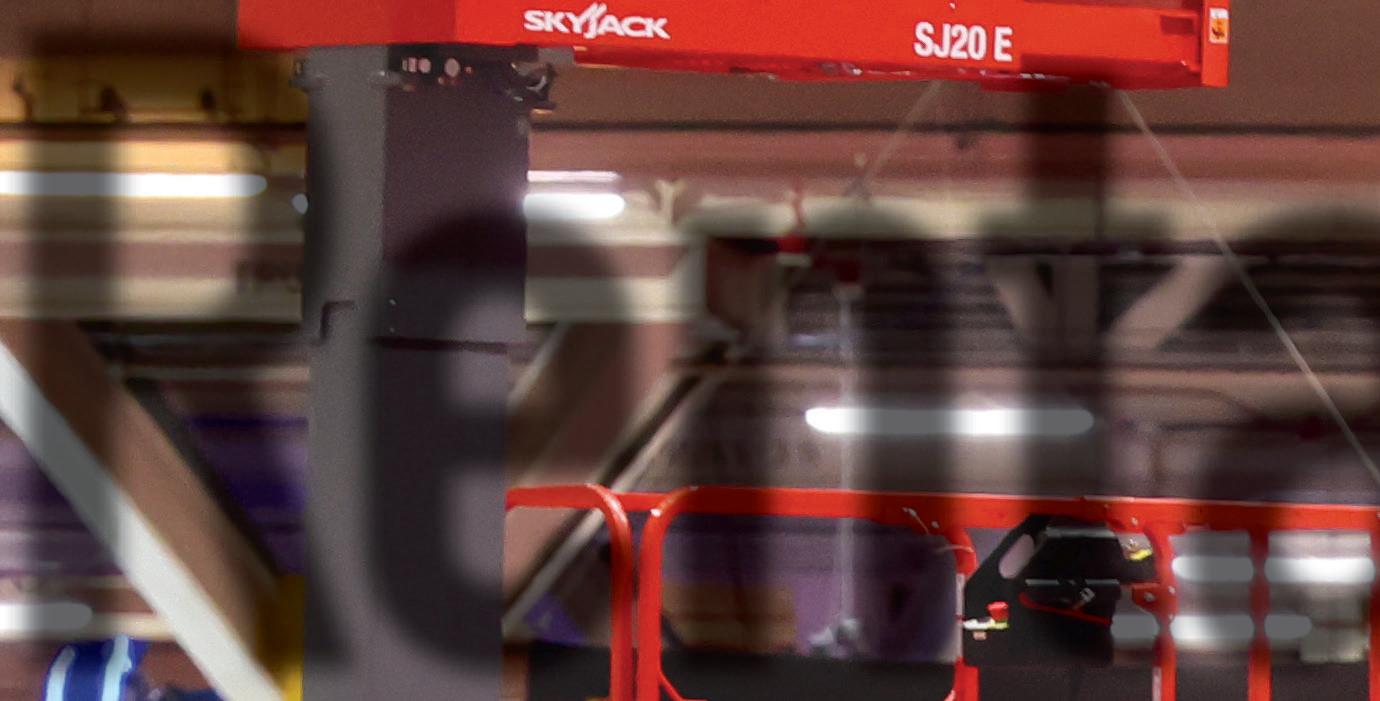


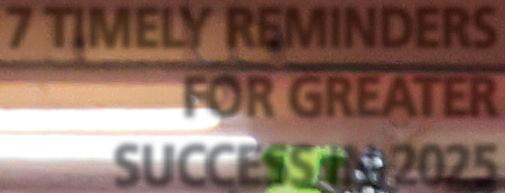

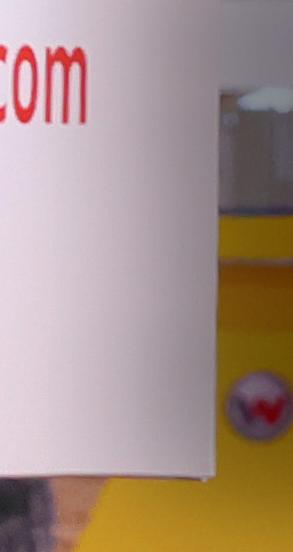
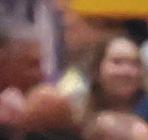


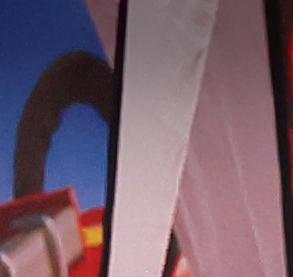

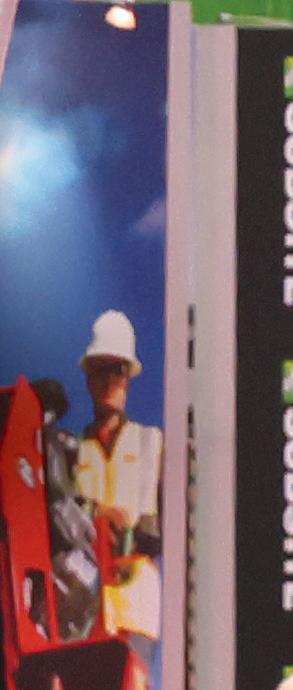


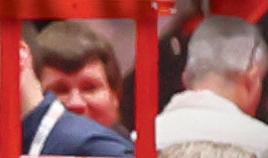
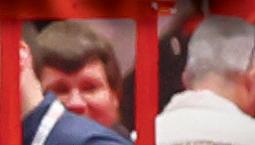
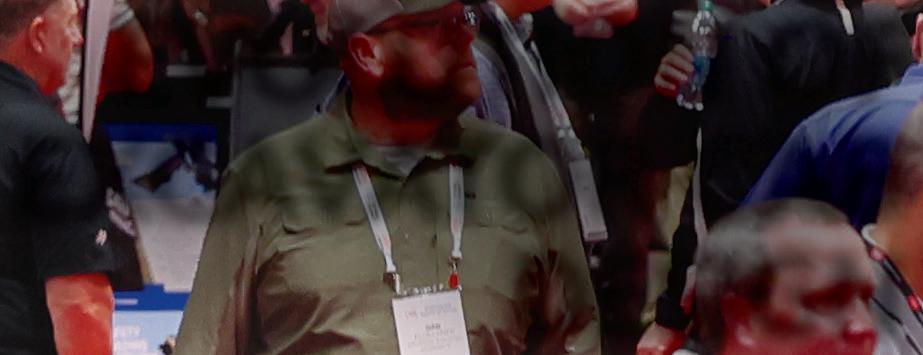
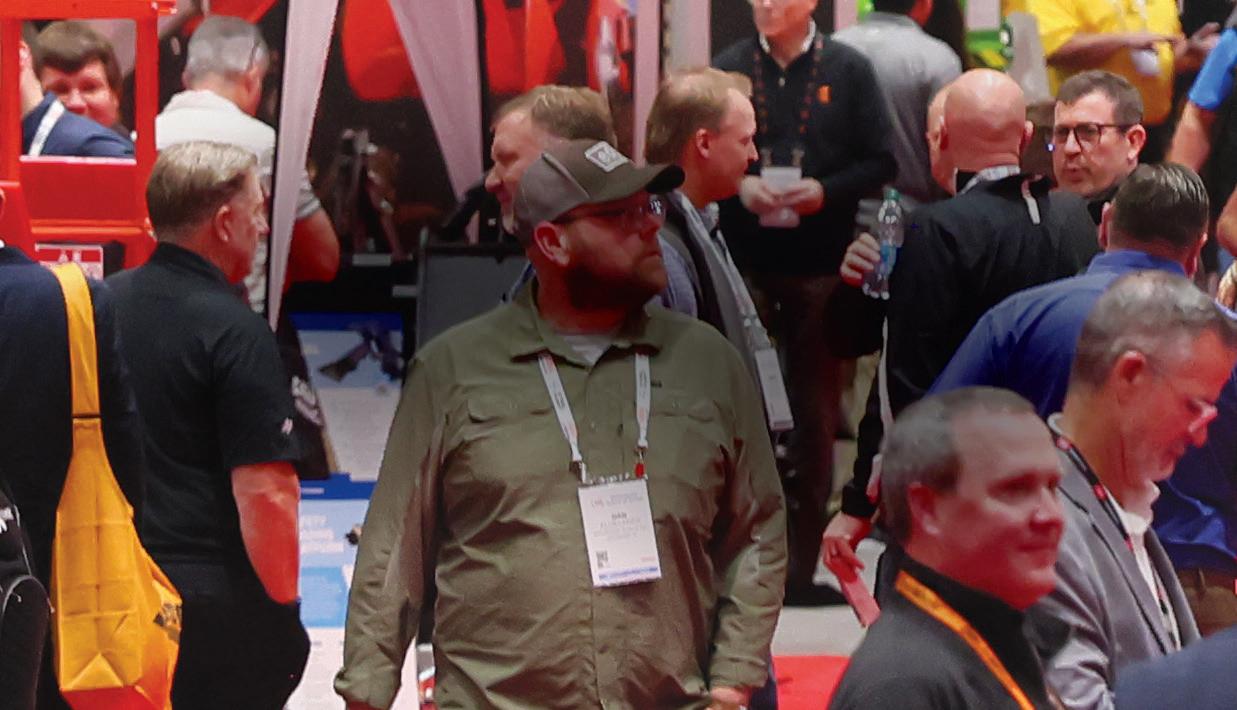




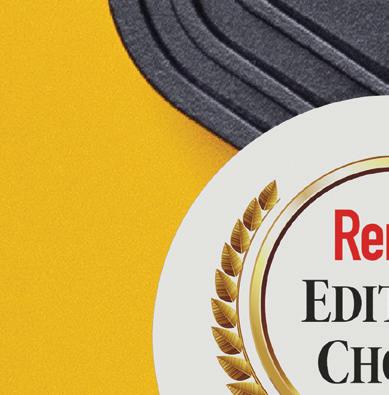



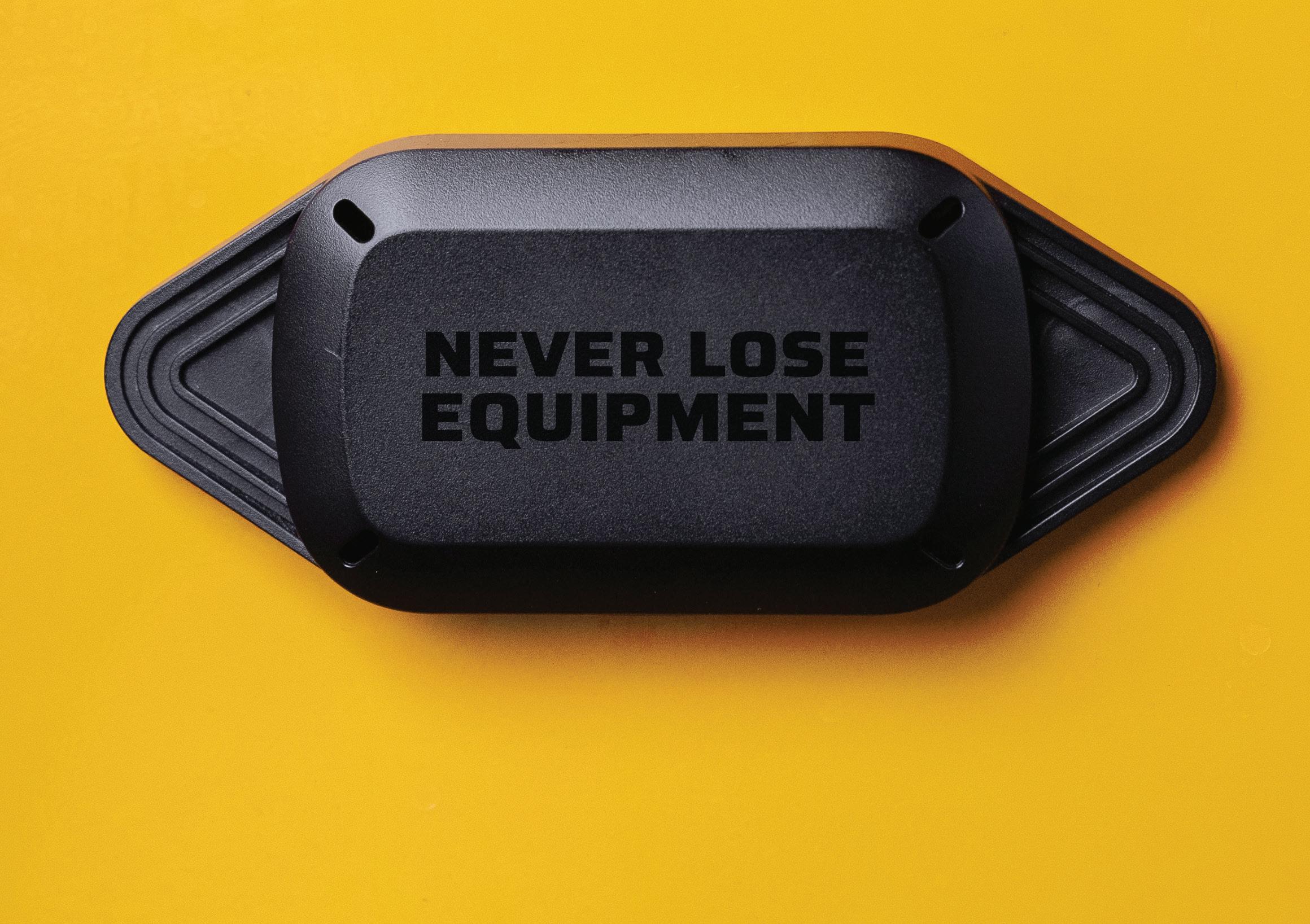
Equip your rental fleet with tools that prevent theft, streamline maintenance, and simplify work orders. Gauge’s Locate Pro ensures peace of mind with 24/7 tracking, while our software integrates seamlessly to optimize every aspect of fleet management. Manage your assets with confidence and efficiency, all from one platform.
Excavator cab design has evolved to incorporate advanced features that enhance the operator experience, improve safety, and streamline efficiency.
Resolutions and the new year go together like jam and toast. You don’t need to add any, but it can be nice when you do. (Points if you see what I did there.)
On page 34 of this issue, our long-running contributor and friend Dick Detmer shares timely some reminders on how to make 2025 a success. Of his thoughts is “planning for the long term.” I think that’s good advice for us all. Planning ahead takes communication, teamwork, compromise but I think there’s a level of ingenuity as well Ingenuity to have direction. A goal to obtain. I think that’s where we can make a new year’s resolution work the best. I think it’s less “start going to the gym” or “eat healthier dinners” but something that can start you up when you remind yourself of what and why you’re doing it. Those are fine resolutions if they work, but I know enough that if I didn’t have something clear, something straight-forward—something big—to get excited about. After-all, I know “run every day” won’t likely motivate many. (Also, running—no thanks. I admire anyone that can knock down a mile or more, but it’s just not for me.)
Ingenuity to create a plan and the fortitude to follow through. It’s one thing to think of an accomplishment to reach, it’s another to figure out the steps to get that done. Especially if its something you and your team have never done before. Want to add to your fleet? Change tactics? Increase profits? You’re going to need more to it than the platitudes one can find on generic posters. You need that ingenuity to develop a plan combined with the bravery to affect your business for the better.
Here’s my suggestion. Think of some general items to change or improve (an exercise you likely already undertake on the regular). Talk to your team and ask for their input. Write everything down. When you have a good list, add bullet points on what needs to happen for each big item to become reality. Then, ignore those general items and use the bullet points are your guide. The TL;DR here, simplify. The world and business is already complicated enough.
I’m no motivational speaker, but let’s take this opportunity to reflect. Check in with the people that support us.
I wrote the following for a separate column but it’s worth sharing here as well: If it sounds like it’s going to be a good year, let’s make it so. Take pride in your work. Appreciate your team. Be safe. Be kind.
Anyways, thank you for reading. Please enjoy this issue.
Stay up to date on the latest happenings across the rental industry. Subscribe to our e-newsletters Rental Watch, Rental Market Watch, Power Rental, and IPAF Elevating Safety. Use the QR code to stay informed on what’s going on around the industry. https://RNT.news/newsletters
EDITORIAL
Editor Jonathan Kozlowski jkozlowski@Iron.Markets
Managing Editor Gigi Wood gwood@Iron.Markets
Junior Editor Merina Shriver mshriver@Iron.Markets
AUDIENCE
Audience Development Manager Angela Franks
PRODUCTION
Senior Production Manager Cindy Rusch crusch@Iron.Markets
Art Director Flatworld Solutions
ADVERTISING/SALES
Brand Director Sean Dunphy sdunphy@Iron.Markets
Brand Manager, OEM & Construction Nikki Lawson nlawson@Iron.Markets
Sales Representative Mike Stack mstack@Iron.Markets
IRONMARKETS
Chief Executive Officer Ron Spink
Chief Revenue Officer Amy Schwandt
VP, Finance Greta Teter
VP, Operations & IT Nick Raether
VP, Demand Generation & Education Jim Bagan
Corporate Director of Sales Jason DeSarle
Brand Director, Construction, OEM & IRONPROS Sean Dunphy
Content Director Marina Mayer
Director, Online & Marketing Services Bethany Chambers
Director, Event Content & Programming Jess Lombardo
CIRCULATION & SUBSCRIPTIONS
201 N. Main St. Ste 350, Fort Atkinson, WI 53538
Phone: (877) 201-3915 | Fax: (847) 291-4816
circ.rpn@omeda.com
LIST RENTAL
Sr. Account Manager Bart Piccirillo | Data Axle (518) 339 4511 | bart.piccirillo@infogroup.com
REPRINTS
Brand Manager, OEM & Construction Nikki Lawson nlawson@Iron.Markets
WINNERS OF FIRST-EVER ‘PACER’ AWARD
ForConstructionPros.com and its affiliate brands announced the winners of this year’s new PACER award, which recognizes construction pros on the jobsite and in the office for their accomplishments. Congratulations to this year’s winners!
EQUIPMENT TODAY
• Women in Construction:
Laurie Bryan, Construction ManagerAllan Myers
• Rising Professionals in Construction: Ryan Bryson, Vice PresidentBryson Grading & Paving
Scan the QR code to learn more.
https://RNT.news/ PACERaward
• Lifetime Achievement: Tim Boulds, Director Construction Equipment Product Marketing - Kubota Tractor Corporation
• Jobsite Excellence: Tom Dusher, Paving SuperintendentHulstein Excavating and Concrete
ASPHALT CONTRACTOR
• Women in Construction:
Beth Conley, Sales Manager - Superior Asphalt Materials
• Rising Professionals in Construction: Kristofer Love, Owner - Love’s Asphalt Solutions LLC
• Lifetime Achievement: James Langley, Executive VP/Co-Owner - CPE Inc.
• Jobsite Excellence: Johnny Coleman, Superintendent - Crown Paving, LLC
CONCRETE CONTRACTOR
• Women in Construction: Lizabeth Howard, Senior Project Manager - Superior Construction
• Rising Professionals: Josh Boswell, President, and Danyelle Boswell, Vice President - Phillips Paving Company, Inc.
• Lifetime Achievement: Ryan Klacking, Founder & CEO - SlurryMonster
• Jobsite Excellence: Marty Small, President - Fairfax Paving & Concrete
PAVEMENT MAINTENANCE & RECONSTRUCTION
• Women in Construction: Jennifer Edgerton, Operations Manager - Driveways By Us Inc.
• Rising Professionals: Eli Stoehr, Director of National Sales - The Pavement Group
• Lifetime Achievement: Mark Carter, President - Peloton Sweeping Service
• Jobsite Excellence: James Leone, Senior Project Manager - EcoSurface
The Associated Builders and Contractors released its annual Merit Shop Scorecard, measuring which states are best for which the construction industry can thrive. Key takeaways include: The 2024 Building America: The Merit Shop Scorecard rates state laws, programs, policies and statistics in seven categories: project labor agreements, prevailing wage laws, right-to-work laws, public-private partnerships, workforce development, CTE and job growth rate.
The top states are:
1. Wisconsin
2. Arkansas
3. Kentucky
4. West Virginia
5. Florida
Scan the QR code to learn more.
https://RNT.news/igc0n09i
In their latest collaboration with Nor-Cal Equipment Rentals (Sacramento, California), Dynapac have delivered a series of custom-painted machines designed specifically to align with Nor-Cal Equipment’s brand and operational needs.
The custom fleet, which includes a utility roller (D.ONE), large soil roller (CA30) and double drum asphalt rollers (CC1200, CC950), represents Dynapac’s continued focus on client collaboration and innovation. By working closely with Nor-Cal Equipment, Dynapac was able to tailor not just the performance features but also the aesthetic of the equipment, offering a unique blend of functionality and branding.
Scan the QR code to learn more.
https://RNT.news/ly0orohn
Sized right for tight spaces. Steel-built for heavy-duty work. With groundbreaking power in a nimble package, Takeuchi Compact Excavators are proof positive that it’s not the size of the machine in the work, it’s the size of the work in the machine.
EXTENSIVE EXCAVATOR LINEUP: INCLUDES CONVENTIONAL TAIL SWING, SHORT TAIL SWING, SIDE-TO-SIDE (STS) OFFSET BOOM, HYBRID AND FULLY ELECTRIC MODELS.
MINI EXCAVATORS (<6 TONS)
MIDI EXCAVATORS (6-10 TONS)
STANDARD EXCAVATORS (10-15 TONS)
The “Li-ion Battery and Manufacturing Equipment – 2024” report from Interact Analysis states that global shipments of Li-ion batteries surged by 38.8% year-on-year in 2023, reaching a new high of >1,100 GWh. In 2024, total shipments are estimated to grow by 21.2% year-on-year to >1,330 GWh, driven up by robust demand in the energy storage market. This growth momentum will continue in the future, with the sector registering a 21.4% compound annual growth rate (CAGR) from 2024 to 2029, rising to >3,515 GWh in 2029.
Compared with a projected 21.9% CAGR (2023 to 2029) for global Li-ion battery shipments in last year’s report, we have revised down the average annual growth rate by 0.5 percentage points over the same period. This is largely due to the slowdown in electric vehicle (EV) production and sales in European and American markets, which resulted in reduced growth for EV batteries, particularly in the short-term..
Scan the QR code to learn more. https://RNT.news/m5szsbv8
The American Rental Association (ARA) has announced its latest inductees for its Hall of Fame. The inductees have provided outstanding service to the association and industry, and are being honored for making a substantial impact to industry growth and success. The inductees will be recognized at The ARA Show 2025 in Las Vegas.
The three inductees this year include: Bick Jones, Peter Lancken AM and David Wilcox II.
Scan the QR code to learn more. https://RNT.news/i355by4u
Equipment and general tool rental companies now have a clear and direct path for valuable insights into their local market to help make critical purchasing, sale, and pricing decisions—further optimizing their operations. Fame Rental and Rouse Services LLC have partnered allowing equipment rental customers on the Fame platform to integrate their Rouse Rental Insights product to access benchmarking data directly within their dashboard.
Scan the QR code to learn more.
https://RNT.news/1qx9kt03
Over the course of his campaign, President Trump’s team has buckled down on its previous position in favor of tariffs. For manufacturers big and small, the proposed tariffs bring about questions surrounding the impacts and how these plans might transpire. Dan Abramson, FourKites SVP of Growth Markets and NAM board member, says these proposed tariffs could bring about a complexity for the manufacturing industry, specifically at a time where companies compete for already-strained logistics
Scan the QR code to learn more.
https://RNT.news/kpgipa9g
Volunteers from around the country came to Renewal House in Nashville, Tennessee, to install a children’s play area with playground equipment, picnic tables, and repair and paint a deck and fences. Fifty volunteers and equipment were provided through the ARA Foundation, the Toro Company Foundation, Ditch Witch of Tennessee, Grand Central Party Rental, Southern Events Party Rentals, MTA Distributors, Taylor Rental of Manchester, All Occasions Party Rental, John Deere, McCoy Construction and Forestry, Coker Rental Company, Sunbelt Rentals and KATO Compact Excavator Sales.
Scan the QR code to learn more.
https://RNT.news/nlzkdh6l
Connecting rental professionals and rental industry leaders, the 2024 Point of Rental International Conference saw over 200 people gathered in Fort Worth to explore new strategies, innovations, and best practices. The event spanned three days with 50+ educational sessions, focus groups, and interactive demos. Highlights included one-on-one consultations and hands-on learning experiences designed to help businesses maximize their rental software investments.
Scan the QR code to learn more.
https://RNT.news/3au7xi4k
The mainstays and changes attendees can expect at the ARA Show 2025.
Of the many tradeshows, conferences, and conventions for the construction industry— one stands out designed for the general equipment and tool rental businesses. The American Rental Association (ARA) calls its annual trade show a “can’t miss event for those looking to discover what’s next in rental.” It’s the world’s largest tradeshow specific to the rental industry.
However, the association has planned a few twists this year. One, they shifted toward a mid-to end of week schedule, placing education on Wednesday and the tradeshow portion Thursday to Saturday. This was to better accommodate current and prospective members as they plan for the year ahead. The ARA Show 2025 will be located in Las Vegas, January 30-February 1, with “The Future of Equipment Rental” educational sessions starting January 28.
The 2025 show will mark its return to Las Vegas since 2021. Mainstays are their educational offerings, networking opportunities, and the tradeshow floor. This year will feature 39 hours of education this year with 19 1/2 hours open for attendees to walk the tradeshow floor. At present, they have 600+ exhibitors with over 50 new companies.
It’s Not Too Late Registration for the ARA Show will remain open throughout the duration of the show—through Saturday, Feb. 1. Attendees can take advantage of advanced pricing through January 26.
Even though they’ve been to the city, new this year is the location. The show is being held within the Las Vegas Convention Center West hall plus exhibits outside in the Diamond lot for demos and stage presentations.
Taking advantage of the space now available to them, the ARA returned a number of features and added a couple of fun moments. The ARA Show will be bringing back town halls—one on events, a second on equipment, both held on the stage outside. You’ll also find cornhole, food trucks, a beer garden, and even pickleball.
“We’re doing everything we can to make an extension of the tradeshow floor,” says Chris Hammes, Vice President of Association Services and Events at the ARA. “To make it fun. A place to rest. Grab some food but also see the exhibits outside. Another big change is what we would call our Tuesday Night event—that’s going to be on Thursday, the first day of the show.” Free for exhibitors and attendees, the Vegasthemed “Thursday” night event will be held onsite in the lobby of the West hall and in the outside lot. Hosting this on the first day opens up a night for exhibitors and members—allowing everyone to enjoy their time and the area how they would like.
“We’ve tried to be very intentional with our planning,” says Hammes. “It’s that blend of trying to keep the things that members like but also trying to understand that they’re taking the time…from the topics we chose and trying to have something to offer everybody at every trajectory in their career—whether you’re starting or you’re new—we’re trying to focus in on that attendee experience so it’s not just coming to another show in Vegas.”
Unique from many other equipment tradeshows, ARA is closed. Everyone inside will be specific to rental. Whether you’re looking for a new asset to add to your fleet, a new supplier, or just looking to network, the show features “like” people. Everybody is within the industry. “Even though buying patterns have changed, it’s still a buying
show,” says Hammes. “We still have over 300 suppliers who are offering a show-only special—I think that still makes the show unique.”
Providing keynote is David Pogue (Jan. 30). A technology expert, Pogue is a New York Times bestselling author of Pogue’s Basics—a series of tips and shortcuts regarding technology in a person’s life. He has also authored several books in the “For Dummies” and “Missing Manual” series of books. He has been at the forefront of new and emerging trends for decades. Attendees should be informed about the state of science and technology today and how it’s shaping the future.
Is it safe to say that construction equipment has changed significantly in the last few decades? As modern challenges push the continued adoption of more technology onto the construction jobsite, equipment responds in kind. These changes also affect the rental industry. Held in the West Hall on the second level will be “The Future of Equipment Rental.”
John Jeanguenat, Vice President for the Equipment Segment at the ARA, considers what the industry might look like five years from now. “It is going to change a lot,” he says. “It needs to evolve to continue to meet the demands of customers that are seeing changes in their business, seeing changes in the construction industry, in the way that we utilize equipment to deal with other challenges that we face as contractors and do-it-yourselfers.”
Jeanguenat has previously served as president at Rental Max in the Chicago area for the general equipment and tool business covering Illinois, Indiana, and Wisconsin. He’s sat on the ARA board of directors for three years and officially joined the ARA in September 2024.
Though things change, what matters now is what you can do today, this year to stay on the right path. The Future of Equipment event for the show focuses on
that directly: what business will look like and what customers are going to demand. “What we see happening five years from now that’s going to influence what action we take and how we invest in new technologies in 2025,” says Jeanguenat. The program includes:
■ Keynote speaker April Rinne, author and leader in having a “flux” mindset. Her book FLUX discusses “essential disciplines and practices” as superpowers to adjust and deal with change
■ Hands-on workshop to help attendees better understand the impact of AI, what it means, and how to take something tangibly away to apply it to the rental business
■ Attend a TEDx-style panel featuring contractors of different sizes to provide different perspectives about their needs, technology investments, perspectives on key issues that impact equipment rental, and more
■ Networking in the cocktail reception to interact with speakers
Workforce development is also another challenge the association has placed effort in addressing. In response, the show includes a student day to share at the highest level what the industry is. The show is planning on bringing in students in the market for jobs and looking to apply to have a hiring event. “For me, when you talk about the future of equipment rental, the people are such a big part of that,” says Jeanguenat.
The ARA Show returns to Orlando in 2026, March 1-4 in the Orange County Convention Center.
• Have a plan in place. Know your priorities of what you want to accomplish. It’s easy to get distracted and lose sense of the day, missing your opportunity to take care of your priority items.
• Download the ARA app to access information.
• Leave time to explore. Don’t miss the 50 new vendors, new equipment, and technology.
• Use the opportunity to network. Make contacts and learn from other attendees.
• Wear comfortable shoes.
• Travel light on the show floor.
• Follow up with the contacts you’ve made, orders, and people you meet. Build from your experiences. There are helpful apps that can scan business cards and import contact information easily.
• Take advantage of the full registration—take advantage of the education as well as networking events.
• Be smart in Las Vegas. Avoid wearing your badge when not at area events.
Let’s take a look at your customer’s role with technology, an equipment management platform, and the availabilty of tools at the jobsite. @Andrii
The construction equipment rental business model can be highly advantageous for all involved. The rental companies themselves stand to make a lot of money in this fast-growing, lucrative industry while the companies renting equipment gain many advantages that can help improve their bottom line. On-site workers also benefit from having ready access to the most modern equipment and latest technologies needed to do their jobs.
When a construction business owner (CBO) rents equipment, they no longer have to worry about issues like repairs and routine maintenance, storage and transportation. The rental company takes care of all of this, freeing up huge amounts of time and resources for the CBO. Even though there’s a big convenience factor with renting, one of the major reasons for choosing to rent is reducing or eliminating CapEx. As an example, excavators, which are often needed only for a short time, can cost between $200,000 and $500,000 to
purchase, compared to a daily rental rate of as little as a few hundred dollars.
However, deciding to rent versus buy equipment does come with some potential disadvantages. First, CBOs must weigh the convenience and short-term efficiencies of renting against the potential loss of valuable investment money in the long run. But even more pressing is the fact that CBOs may be “rolling the dice” in the sense that they cannot know for sure that the equipment and tools they need will be available when they need them. This is a particularly salient issue for construction companies specializing in projects like highways, public works and other structures that are prone to damage from unpredictable natural disasters. For these companies it’s nearly impossible to foresee what equipment will be needed, when and where.
The ability to track rental company equipment availability can vary from CBO to CBO, but generally these systems and processes are not well-automated
and mature. This is because, compared to other industries, construction companies tend to be slow technology adopters. In fact, McKinsey & Company recently ranked the construction sector second to last out of 22 fields surveyed for digital readiness. This is likely due to several factors, including a prevalent attitude in construction of, ‘if it ain’t broke, don’t fix it.’ What’s the point of replacing paper spreadsheets with a more advanced digital system, some companies think, not understanding the greater efficiencies that automated, digitized processes can bring.
Even for a CBO who is modestly advanced technologically, on localized construction sites, equipment and tool tracking is often a struggle and can result in a substantial loss of work time. Incrementally, this downtime can snowball and lead to a big hit on overall project performance. This can be highly detrimental to both the rental company, which may be overseeing the renting of equipment to hundreds or even thousands
of CBOs at once; and the CBO, not to mention on-site workers who depend heavily on having the right equipment and tools in the proper place when they are needed. Moreover, many isolated instances of lost time on projects can accumulate and be a big contributing factor to CBOs’ financial woes and—ultimately—an industry failure rate that exceeds 80%.
In construction, a comprehensive equipment management platform can be the key to ensuring transparency. This platform should be available to all stakeholders (rental company, CBO and on-site workers); integrate with stakeholders’ key platforms like e-commerce and financial management; give total transparency to equipment and tools’ location, usage, expense and
efficiency; and ultimately, unsnarl the entire process for all parties involved.
Automation is also important. CBOs, particularly those that may not be the most fervid technology adopters, need to clarify, simplify and automate the process of making equipment and tools available for their on-site workers. A big part of this can be the ordering of tools and equipment for major construction sites prior to construction starting. For example, the ordering process for on-site workers can be simplified as the equipment that was budgeted can be ordered from the e-commerce system with a few clicks, via automated basket collection. Reducing friction points and eliminating unnecessary steps are critical to a successful digital approach.
Transparency is needed for the success of any rental arrangement, and the construction equipment rental business is no different. While this business model is poised for tremendous growth in the years to come, in a standard arrangement, there is still a lot of room for misunderstandings and for things to go wrong. A shared, comprehensive equipment management platform can serve as the basis for much-needed transparency and automation—fostering shared understanding and communication, and ensuring that all parties realize the maximum benefits.
Excavator cab design has evolved to incorporate advanced features that enhance the operator experience, improve safety, and streamline efficiency.
The design of excavator cabs and the technology inside them are just as important as the power and efficiency of the overall machine. For operators who spend long hours each day on the job, cab comfort and functionality are critical to maintaining their productivity while reducing fatigue. Owners and fleet managers also understand the value of well-designed cabs and advanced technology because they help minimize costs like unnecessary rework, maintenance, and downtime.
As the equipment industry evolves, cab design has moved far beyond basic functionality to incorporate advanced
features that enhance the operator experience, improve safety and streamline overall efficiency. These innovations reflect a growing recognition that operator well-being influences jobsite productivity and profitability.
Excavator operators often face long, physically demanding workdays—their cab serves as their “office” for hours on end. A poorly-designed cab can lead to discomfort and fatigue, negatively impacting productivity and increasing the likelihood of mistakes. Ergonomic designs, improved visibility and intuitive controls help keep them focused
while reducing physical strain, making these features crucial considerations when selecting a machine.
For example, multiple forms of climate control, adjustable seating and logically placed controls are seen as vital to the operator’s ability to work efficiently for extended periods of time.
As cabs become more tech-enabled, machine control systems with real-time data displays contribute to a higher degree of accuracy and a reduction in expensive rework.
With the ongoing skilled labor shortage, managers are looking for ways to keep their current employees happy and returning to work each day.
To be their most productive, an operator should be comfortable and not feel physical strain caused by the layout of the controls and dashboard.
However, modern cabs are expected to do more than provide comfort. Another common challenge is poor visibility, which is a safety hazard. Equipment manufacturers are addressing this concern by integrating camera systems that provide a broader view of the jobsite, allowing operators to better monitor their surroundings to avoid blind spots and reduce accidents.
While staying connected on the job is another necessity, that connectivity should be convenient and distractionfree. For example, some cabs now offer wireless phone charging and Bluetooth capability for hands-free communication. They also integrate additional comforts like built-in hot/cold storage and more compartments for personal items, so operators can access their essentials without unnecessary clutter or distractions.
Temperature control also plays a vital role in keeping operators productive, especially during extreme weather conditions. Cabs should be equipped with features like front and side window shades to help regulate cabin temperature during the hotter summers. Seats also can feature heating and cooling elements — because a long day only feels longer when the temps are tough to handle.
With comfort and safety addressed, owners and fleet managers may wonder how the newest cab technology can contribute to more efficient operations. The top original equipment manufacturers (OEMs) tend to have
assistive software on touchscreen tablets for things like on-board weighing and in-field design. Current models also improve user experience with larger, hi-res screens, as well.
Another feature that is becoming more common on in-cab devices is the ability to automate boom and bucket movements. Combined with real-time data and diagnostics from the cab’s control systems can reduce rework costs and avoid downtime.
A smart hydraulic system that automatically adjusts power based on the task at hand will also go a long way in optimizing fuel efficiency and extending the life of the machine while reducing operating costs.
Another technological perk found in more and more cabs is a selection of work modes. These are predetermined settings that operators can choose based on the task and material at hand. OEMs also are expanding upon these modes in their new excavators. Not only does this help operators find the right power for the job and dig in, but it helps save on fuel and emissions too.
Another addition for excavators is an auto power boost, which
automatically provides more power for additional digging force and lifting capacity. In addition to the ability to adjust this manually, predefined conditions can be set up to allow this function to kick in automatically and turn off after several seconds.
The modern excavator cab has come a long way from being a simple operator station. Today, it serves as a critical component to improve productivity, enhance safety and reduce operating costs. As equipment manufacturers continue innovating, it’s clear a well-designed cab can make all the difference in the operator’s day—and a good day for operators can mean a great day for your bottom line.
The Hatz engines are the perfect solution to power your pump fleet.
Power units built with the durable and fuel efficient, Hatz 4H50TIC and specifically upfit for pump applications, provide all the benefits.
1000-hour service intervals, 1-year unlimited hour warranty, and IoT ready for Hatz performance tracking. This complete Hatz pump power unit is the perfect solution for your pump fleet.
Find your perfect pump solution at hatzamericas.com/pumps
JONATHAN KOZLOWSKI
Why rental companies might want to consider add a water-jet drain cleaning machine to their fleet of assets.
When drains are clogged, life can’t go on as normal. Life is as stuck as the water and building owners are willing to call your customers and pay top dollar to open their drain. Often, the service finds the cause of the blockage: “You have this going on too.”
Punching through the clog and getting that water flowing again isn’t the end of the story. It’s just the beginning. Whether they make that sale or not, water jetter drain cleaning equipment plays a big role in this situation. Sure the drain is open, but discovering the cause can discover any systemic problems. This is when that company calls your rental shop.
While similar to their mechanical snake counterparts, jetters are a different class of pipe-cleaning equipment. We’re not talking about massive 36-in. culverts but in the 3, 4 to 10-in. pipe range connecting a building to a municipal or septic system. Your customers are already coming in renting the equipment needed to work on these smaller to medium drains—there’s a good chance you have a good idea on who in your market would be a good candidate.
It’s recommended to also send a camera into the piping to inspect the drain and get a clear picture of what’s going on. This should allow customers to be able to inform theirs of any issues that may cause problems to reoccur. A snake machine would chop through the obstruction, grab something or push it downstream, but it’s not going to clean the drain—there may be a lot of stuff going on to keep them from seeing the true state of the pipe: cracks, roots, and other points of infiltration.
This leaking adding more water into the draining system than necessary is actually a significant problem in the country.
“We haven’t been spending enough money on our infrastructure,” says Dave Dunbar, Customer Success Specialist at General Pipe Cleaners (General Wire Spring Company).
“We need to spend some money on sewage treatment and the whole system—essentially because it leaks like a sieve and overflows every time it rains. We end up with polluted stuff in our waterways, which isn’t good. What the EPA finds very easy to do is say to plumbers and drain cleanings, ‘if you see a leaky pipe, replace it.’ That’s easier said than done.” There are trillions and trillions of dollars worth of infrastructure repairs that should be done in the next 20 years to alleviate this problem. In order for these drain cleaners to be effective, many situations may very well require a jetter to clean the inside of the pipe to the point where they can get a good inspection.
Water-jet drain cleaning equipment are available in different sizes to match the market, customer, and job. Larger, tow-behind
trailer jetters can run up to $26,000 to $27,000. Depending on maintenance and how it’s treated, the machine should last 10 to 20 years.
Smaller jetters come with two and four wheels for maneuverability to be able to be used almost anywhere. Electric versions draw 13 amps and are not as powerful as their larger counterparts as these were typically not designed to clear the drain. However, about half to 3/4 of clogs blocking up today’s drains are within 10-15 ft. of the kitchen sink, “small is the next big thing in jetting,” says Dunbar. The return on investment, he claims, is similar to post hole diggers.
While a snake can open the drain, (should the owner continue their ways) these drains are likely to “heal” and backup again. When homeowners and restaurants just need to be up and running again, they may not be interested in replacing anything—a small jetter can be effective to blow away the grease and flush the sludge down the system.
Just like every other asset in the fleet, rental shops will need to have a clear idea on how to do preventative maintenance and what can go wrong. Many manufacturers can help with this and even may have videos on fixing issues in a way to help rentals save money.
The pumps used in these drain cleaning machines tend to be triplex, which are plunger style pumps that develop a high pressure from three pistons working in sequence to even the outflow. These pumps have a crank case of ceramic-style cylinders to push the water. Valves and seals around the plungers to keep the oil and water segregated. Check the oil every time the machine is returned. Look for a sight glass, often on the back. If your oil looks milky, water is getting into the
oil—your seals are failing. This process is similar to pressure washers.
“It’s really important to do a physical inspection of the hose,” says Dunbar. He recommends that rental shops do more than
a cursory glance at the hose; make sure the hose is in good shape, especially the front and back parts where it is most vulnerable.
• Keep nozzles clean. These tend to become clogged should impurities get into the water supply. Pressure can skyrocket if the nozzle is clogged and cycle, where its presure will spike, reduce, then return. If its’ cycling, it’s vital to take the nozzle off first to avoid pushing the obstruction further into the hose.
• Should it be needed, remind your customers to remove the nozzle away from the drain to avoid dropping pieces.
• When the camera is run into the drain, remind customers to back the camera out before digging and cutting through the pipe. No one intends to cut off the camera head, but accidents happen.
• Track hours used. Where trailer-mounted jetters may have an integrated hour meter, smaller machines do not. Use this estimation on when to change the oil.
Leonardo HD is not only a platform, it is a revolution in safety and productivity on the jobsite.
92,72% of scissor lifts sold between 2017 and 2023 are used in projects where ceilings are max. Smt (16ft) high.*
·1ntrospective Market Research.
Global Scissor Lift Market Research Report 2024
18,53% of jobsites has ceilings higher than Smt (16ft).
33,40% of jobsites has ceilings with max. height of Smt (16ft), but relateci to residential projects. Not compatible with Leonardo HD.
48,07% of jobsites has ceilings with max. height of Smt (16ft).* Compatible with Leonardo HD.
'lntrospective Market Research.
Global Construction Market Research Report 2024
Equipment manufacturer JLG shares insights from their customer survey.
Every year, JLG customers provide insights into how the latest product launches and current market trends affect the access equipment industry. We are also examining where our customers want to take that technology and where our products are so we’re ready to go. Although most of these are not new, there are some trends in what customers are requesting in MEWPs.
1. Higher Capacities
Customers seek MEWPs that can lift heavier loads. This trend is driven by the need to increase productivity by moving more materials or supporting more workers on a single platform. Higher capacity MEWPs allow for fewer trips and more efficient use of time and resources on jobsites.
2. Compact Sizes
There’s a growing demand for smaller, more maneuverable MEWPs operating in confined spaces. This is particularly important in urban construction, renovation projects and industrial settings where space is at a premium.
Multi-purpose MEWPs are becoming increasingly popular. Customers prefer machines that can perform various tasks, reducing the need for multiple specialized equipment. This versatility can lead to cost savings, improved efficiency, and simplified fleet management.
With growing environmental concerns and stricter regulations, there’s a shift towards MEWPs with low or zero emissions, reduced noise levels and minimal fluid leakage. These eco-friendly features allow operation in sensitive areas like hospitals, schools and indoor spaces,
as well as in jurisdictions with strict environmental regulations.
The demand for and acceptance of electric and hybrid aerial machines are on the rise, and we expect this trend to continue. Four key factors contributing to this growth:
■ Increased model variety: We’re seeing a broader range of electric and hybrid aerial machines become available. These new models offer longer runtimes and quicker charging capabilities, which address some of the previous limitations and make them more practical for various applications.
■ Expansion of bi-energy options: The availability of hybrid and/or bi-energy options is also growing. These machines combine electric power with traditional fuel sources, offering greater flexibility and extending operational hours while still benefiting from the reduced emissions and lower operating costs of electric power.
■ Falling costs for advanced battery technologies: The costs of advanced battery technologies, such as lithium-ion batteries, are decreasing. This reduction in cost makes electric and hybrid machines more financially accessible for both rental companies and end-users, further driving adoption.
■ Growing charging infrastructure: The charging infrastructure is improving, with more portable solutions available to bring power directly to jobsites. This advancement alleviates one of the most significant challenges associated with electric machines and supports increased use in the field.
Given these advancements, we expect that the market for electric and hybrid aerial machines will continue to grow, especially in the rental sector. We also anticipate that rental companies will likely experience greater demand for these eco-friendly and cost-effective solutions as these machines continue to become more efficient and economically viable.
MEWPs are increasingly being integrated into the broader construction ecosystem through IoT (Internet of Things) technologies. This connectivity enables real-time monitoring of machine performance, predictive maintenance, fleet management and data-driven decision-making. It can also enhance safety by providing remote diagnostics and operation oversight.
There’s growing interest in MEWPs with autonomous or semi-autonomous capabilities, particularly for tasks involving heavy, repetitive motion or work in varying conditions. These features can enhance safety by reducing human error, address labor shortages by allowing one operator to manage multiple machines and increase efficiency by optimizing movement and positioning.
A major focus has been on integrating advanced technology to improve safety and efficiency. Autonomous functions can range from simple self-leveling to complex navigation and task execution. For example, one of our focuses in access equipment is to reduce the need for operators to be physically involved in high-risk tasks by leveraging robotics and autonomy. This shift makes strenuous work less taxing and significantly enhances safety by minimizing direct exposure to
hazards.
Overall, integrating these advanced technologies will not only make current construction tasks more efficient but also have the potential to attract a more diverse workforce by making the industry more accessible and less physically demanding. These trends collectively point towards a future of MEWPs that are more capable, efficient, safe and sustainable while also being better integrated with modern construction management practices.
From Incoming Power to Point of Use, Ericson o ers a suite of products to safely power and light your most challenging jobsites
BY JONATHAN KOZLOWSKI
4 quick questions with Tony Leopold, SVP of Strategy and Digital at United Rentals.
United Rentals’ Work United Tour 2024 was host to construction customers across the country. The company took the opportunity to walk attendees through its latest worksite performance solutions, digital tools for productivity, and practical sustainability solutions. The event allowed attendees to experience worksite innovations by touring a demonstration worksite to see how connectivity helps manage site access, equipment access, and inventory management. It also showcased a portfolio of solutions that help contractors maximize every phase of their projects.
While at the event, Rental was able to connect with Tony Leopold - SVP, Chief Technology and Strategy Officer at United Rentals.
Rental: What are the biggest trends in equipment rental right now?
Leopold: I think one of the biggest trends that we’re facing is the increasing value of data one can obtain with telematics. More and more OEMs are
developing their own devices as a way to get better intelligence and data on their machines. From a service perspective, a service technician can diagnose issues remotely, whereas before you had to plug in a diesel laptop to see engine codes and so forth. The ability to access codes remotely and get intelligence about what’s going on—whether it’s around uptime or how the machine is being used—opens up accessibility and a level of intelligence that just wasn’t there before.
I think accessing this kind of data remotely will become standard over time. This creates an opportunity for rental companies to become an aggregator of this data. We have a lot of equipment makes and models, each with their own data protocols. We have to take all this different information, harmonize it in a way that somebody can just see it in a single pane of glass. And we can do this for rental fleet, but also customer fleet, helping customers manage all the equipment on the worksite.
I think these capabilities create a
data services opportunity that benefits everyone. OEMs benefit from it, and we certainly benefit from it and we can provide a better value for our customers.
Rental: Telematics isn’t a new idea, though. Why do you think telematics has risen to such a key issue for construction and equipment rental lately?
Leopold: To your point, telematics has been around for a long time transmitting basic levels of information. What we’re starting to see is more OEMs that are offering their own telematics and providing data through the CAN
bus that are much richer data sets than before. That wasn’t really readily accessible 10 years ago.
Another important factor is the growth of cloud computing and the ability to aggregate and handle the massive amounts of data telematics devices are generating. It’s really incredible how many data records a machine can produce. And with a large fleet, you have to have cloud processing to handle these data volumes. Cloud computing enables companies to create a platform to generate insight and consume that information. That’s why I think it’s becoming more prevalent now, but it’s still in a journey.
Rental: What advice do you have for the independent rental companies? Is
there something they could do in 2025 to stay more competitive?
Leopold: With independents, one of their key strengths is local relationships. Many small rental companies have owners that have been in business for a long time and have deep relationships in the industry. They often have a local customer base that trusts them.
Given how fragmented the contractor base is, locals still have an opportunity to compete effectively. A lot of what I was talking about with the telematics being built into these machines creates an opportunity for data integrators to provide a telematics platforms for smaller players that may not have large IT teams. There are several third parties that can make these tools accessible to local customers so local
players will be able to offer telematics, along with web and digital experiences.
Rental: One of the panelists brought up the skilled labor problems in construction and the rental industry. How is United Rental addressing that situation? (Editor’s note: Prior to this Q&A interview, United Rentals hosted a panel of customers representing their construction base.)
• A comprehensive product lineup that offers the optimal weight, dimensions and engine for your
• A powerful vibratory system that puts any material – from wet clays to dry aggregates – in its place.
• Controls that are intuitive so even inexperienced operators can be productive.
• A robust customer service network that supports the machines – anytime, anywhere.
• Extended service intervals that minimize maintenance costs and maximize uptime. Ammann compaction equipment provides all that – and more. You’ll never a miss round with these lightweight champions.
Ammann America Inc. | 1200 S. Orange Ave, Ste 1050, Orlando, FL 32801, USA Operations / Distribution Center | 680 Clemson Rd Columbia, South Carolina, 29229, USA Phone (954) 493 0010, info.aaa@ammann.com For additional product information and services please visit : www.ammann.com MMP-2488-04-EN | © Ammann Group
Leopold: We certainly see it on our side. We have to hire technicians. They have to learn how to work on our equipment across a variety of makes and models. It’s no different than when you need a skilled trade that can do work—we need a skilled technician to service a machine. To address this we have programs where we train entry-level roles, like equipment associates, to learn how to be a service tech. This gives a meaningful career path and helps someone with no background as a tech start to learn our business and eventually the skills needed to service equipment.
We’re also starting to use augmented reality and other technologies where we have some workers that are nearing retirement or they want to work remotely in hours that are convenient to them.
Through augmented reality, they can partner with a more junior tech see what it is they’re seeing and give them advice and troubleshooting—mentor them on handling certain repairs and so forth. I think this “work from home,” remote connectivity / augmented reality technology enables work to be more flexible and allows experienced technicians to continue to work longer than they were able to do and deliver have value.
We are also exploring how AI can help upskill our employees. With AI you can take an employee that maybe has relatively less training, but if you have the right digital support, you can actually get them to operate at a higher level by showing the step by step instructions. We’re experimenting because we have to find a way to make it more accessible
for new workers to learn how to fix equipment
Technology and AI plays a huge role, but we are still going to need people who want to do the work and learn the skills.
The AKHL1320E features a 2.64-gallon air tank, providing 15% more air volume than its predecessor. The Easy Connect AKTH15 optional accessory integrates an additional three air tanks increasing the total air capacity, while a newly designed handle grip protects the ventilation window with four bolts. The motor operates in temperatures as low as -4° F, includes a circuit inverter that manages electrical current to prevent shutdowns in low voltage supply areas. The new models will replace the AKHL1260E and AKHL1260EX—scheduled to be discontinued.
Scan the QR code for more information. https://RNT.news/10id469s
Cimline has introduced the R3 Asphalt Crack Router, which is designed to support operator safety and sealing operations. Powered by a 27-hp electric start gasoline engine, the machine features a single piece drum design with cutouts on each side of the housing for access. The R3 is equipped with a 6-gal. fuel tank and dual-stage air cleaners.
• Belly-bar hands-free emergency shutdown
• Quick Stop II anti-kickback system
• Integrated depth gauge
• Large tilt-up shroud
• Electronic clutch
Scan the QR code for more information. https://RNT.news/frmb130i
Mi-T-M CTM Series of pressure washers can be mounted to a truck or trailer with a water tank and are designed for custom cleaning setups. The new 3,000- and 3,500psi pressure washers feature a powder coated steel frame and mounting plate, Honda OHV engine, belt drive pump with external bypass and enclosed belt guard. Both units require a 200-gallon or larger water tank and deliver five to eight gallons per minute of cleaning power. Each model is designed with mobile cleaning in mind and is customizable with accessories and options such as an extra fuel tank, 50-ft. hose, 48-in. lance, rotary surface cleaner, rotating nozzle and more.
Hitachi Construction Machinery has announced a new fleet management system, Solution Linkage (SL) CONNECT, to meet the real-world needs of modern worksites. With access using phones, tablets or computers, SL CONNECT users can monitor machines on different worksites in one of various languages. Using technological open-source tools, SL CONNECT allows customers to view information from Hitachi machines from one place and monitor the utilization information from all machines. Users can geofence an area on the map to separate projects and specific worksites, as well as graph and view operating information for each project and worksite.
Scan the QR code for more information.
https://RNT.news/vdo2gugd
Makita has released two new lighting solutions for both the XGT and LXT systems. These Underhood Work Lights provide three modes of operation that deliver 1,700 lumens on High, 800 lumens on Medium and 400 lumens on Low. The lights are foldable and provide three different lighting modes including upper bar only, lower bar only, as well as both the upper and lower bar illuminating for maximum light output. Both lighting options feature a telescopic hook. Users can choose from seven adjustable rotating illumination angles (-90, -45, 0, 45, 90, 135 and 180).
Scan the QR code for more information. https://RNT.news/ykble72m
The DEWALT TOUGHSYSTEM 2.0 DXL 30-in. Modular
The TOUGHSYSTEM 2.0 DXL lineup includes four 30-in. products: a Worktop, Deep Drawer Unit, Two-Drawer Unit, and Dolly. . TOUGHSYSTEM 2.0 modules can be connected and stacked from the top or bottom of TOUGHSYSTEM 2.0 DXL Drawers using auto-connect front latches. The 30-in. Worktop provides a flat, durable, multi-purpose worksurface with five integrated slots for hanging tools and two cup holders. The 30-in. Deep Drawer Unit provides total load capacity of 55 lbs./25 kgs while an integrated metal bar secures tools inside using a padlock-eye.
Scan the QR code for more information. https://RNT.news/ykbqmur1
Scan the QR code for more information. https://RNT.news/btmt8foa
Powered by a turbocharged 3.4L Bobcat engine, the B760 backhoe loader features a 2,200-lb.+ lift capacity at full reach, an 18 ft. 5 in. digging depth, and nearly 180 degrees of backhoe swing for less repositioning. It comes with a standard-equipped extendable arm that provides up to 8 in. of additional dig depth. The B760’s performance and versatility extend throughout the machine, with the front-end loader providing a lift capacity of 7,985 lbs. with its standard, general purpose bucket.
Scan the QR code for more information.
https://RNT.news/pkh0snt3
outstanding duty cycles and increased return on investment through reduced maintenance needs.
The SJ3213 micro and SJ3219 micro combine low cost of ownership with our renowned product support.
✓ 13 ft and 19 ft platform heights
✓ 500 lb platform capacity
✓ AC electric drive performance
✓ 20” rollout extension deck
✓ Low GVW, fits standard elevator
✓ Optional XStep
The Yanmar attachments include a full range of buckets, augers, trenchers, stump grinders, soil conditioners, breakers, sweepers, pallet forks, brush mowers, grapple rakes, grapple buckets and snow and grading blades. The introduction of the new attachments supports fleet owners, contractors and rental centers by allowing Yanmar dealers to act as a one-stop shop for a package of Yanmar equipment and attachments. The attachments, available through Yanmar’s dealer network, allow for compatibility for use with Yanmar-branded compact track loaders.
Scan the QR code for more information.
https://RNT.news/ar0hlso3
Werk-Brau’s Reverse V-Line Bucket allows all teeth to engage the ground simultaneously during application spreading the machine’s digging force across all the teeth. With oversized leading edges and a reinforced plate, the Reverse V-Bucket promotes long service life in severe conditions. Constructed of T-1 steel in critical areas, this bucket features steel walls and reinforced wear areas. Each bucket has tapered sides to reduce wear on bucket sides and to allow for dumping.
Scan the QR code for more information.
https://RNT.
Powered by a 74-hp Tier-4 Final Yanmar engine, the 8,955-lb. VT-80 mid-sized compact track loader provides power and performance and offers a 2,800-lb. rated operating capacity. The machine features ASV’s Posi-Track undercarriage with dual-level suspension for traversal over tough terrain. The 7-in. color touch display supports operation, allowing operators to monitor machine specs, service history, schedules and more. Automated features like the return-to-dig and work tool positioner functions are designed for repetitive tasks.
vhttps://RNT.news/x06ua78a Miller Electric XMT 400 ArcReach Multiprocess Welder
The XMT 400 ArcReach helps fleet managers and operators tackle various jobs with one welder. The XMT 400 ArcReach features ArcReach technology providing remote control of the power source without a control cord. Additionally, dedicated weld processes like gas-shielded flux-cored, TIG, self-shielded flux-cored, stick and gouge allow operators to dial in their requirements for the job. Auto-line technology allows it to be plugged into primary voltage power from 208V to 575V single- or three-phase and enginedriven generators.
Scan the QR code for more information.
https://RNT.news/ gnfaqatz
MGT America offers a line of soil compaction products for site preparation, concrete and construction projects. The series consists of three plate compactors and two rammer compactors, designed for versatility on the jobsite. Accessible features include a self-adjustable clutch, handles designed to allow compacting soil close to walls and more.
Scan the QR code for more information.
https://RNT.news/p6pzsj4q
Mecalac offers a foldablecanopy version of the MCL2, MCL4, MCL6 and MCL8. The quick-folding canopy allows operators to leverage the loaders’ benefits in areas with limited overhead clearance, making a spot once inaccessible to machines now a reality—especially valuable on a farm. The loaders are equipped with hydraulic and maneuverability options, M-Drive and Speed Control. With M-Drive, the engine speed can be controlled independently of travel speed, allowing power and hydraulic flow to be adapted to best suit the job at hand. Speed Control allows operators to set the maximum travel speed from 1-19 mph (MCL6 and MCL8 only). Operators can easily fold down the canopy in seconds by removing a pin on each column and simply pushing the roof back reducing the height by as much as a foot (to less than 6.6 ft.).
Scan the QR code for more information. https://rnt.news/lhhwajnf
The TL623 offers the extended reach and lift capacity of a heavyduty telescoping boom combined with Bobcat’s multi-attachment versatility enabling operators to tackle a wide range of jobs with one machine. The TL623 has a lift capacity of 6,000 lbs. and a lift height of 23 ft. The advanced Tier 4, turbo-charged engine delivers emissions compliance without the use of a diesel particulate filter or selective catalyst reduction. Operators will also appreciate the engine’s reliable cold weather starting, along with a variety of features that make maintenance and service more convenient.
• Four steering modes for application-matched maneuverability
• The Bobcat Smart Handling System for tailored boom movements via controls on the joystick
Scan the QR code for more information. https://RNT.news/0002427f
Blue Diamond Attachments announces its full line of brush cutter attachments to handle site prep and clearing and now provides Heavy, Extreme and Severe Duty models:
• 36-, 42- and 50-in. mini skid steer closed front
• 36-, 42- and 50-in. mini skid steer open front
• 60- and 72-in. heavy duty models
• 60- and 72-in. extreme duty models
• 72-in. severe duty model
• 44-in. swing arm cutter
• 84-in. dual motor brush cutter
• 60-in. extreme duty for excavators
• 60-in. severe duty for excavators
• 36-, 42- and 50-in. heavy duty for mini excavators
• And a 42-in. severe duty for mini excavator
Scan the QR code for more information.
https://RNT.news/56ebfwjc
JLG Industries’ JLG 519 telehandler, a redesign of the G5-18A model, delivers advanced features, greater productivity and enhanced serviceability to improve operator confidence and lower the total cost of ownership.
• Offering a 5,500-lb lift capacity, 18-ft., 7-in. maximum lift height and 10-ft., 10-in. maximum forward reach
• Optimized load chart expands the working zone at maximum lift capacity and forward reach
• New control system enables load stability indication, seatbelt engagement and operator presence, and enhanced diagnostics
• Powered by a Deutz 2.2L 60 hp diesel engine improves fuel efficiency by 10-20%
• The electric-over-hydraulic joystick offers greater versatility
• Redesigned cab is more spacious, includes options like air conditioning and a multifunction display with a backup camera
• Reductions in hydraulic hoses and fittings enhance serviceability— minimizing potential leak points
Scan the QR code for more information.
https://RNT.news/t9z2q5c3
•
•
With the new year underway most rental businesses are in their quieter season now, but that makes this an ideal time to prepare for busier times ahead. Between planning and training this is your opportunity to set the stage for a prosperous year to come.
Here are 7 timely reminders.
1. Be ready to capitalize on what should be a very robust year. Huge opportunities can be missed by procrastination or being overly cautious. Some rental companies are clinging to the old ways and would greatly benefit from fresh equipment, fresh visual image, fresh rental rates, relevant marketing plans and solid employee systems. These companies are not likely to enjoy the growth and prosperity experienced by other rental companies who have invested in these key ingredients.
2. Consider advancements in technology for your rental company. It certainly is a whole new world when it comes to ways to vastly improve a rental company through technology. Most of the ways can be summarized in one word, “efficiency:” efficient use of time, capital, staff, facilities, equipment, marketing, etc. This is certainly an enormous topic but well worth the time and expense to investigate. As I commonly point out, many equipment rental companies are working far too hard for the relatively meager amount left over after their expenses. Greater efficiency should drive your company’s present and future decisions and activities.
3. Be proactive and don’t just react. It is almost normal for rental businesses to be in the “reaction” instead of the “anticipation” mode. One of the defining characteristics of great businesspeople is their ability to anticipate their company’s needs before those needs become obvious to others. In the rental business there are so many sources for quality information to anticipate and plan the best direction for your asset management decisions. (For example, your
computer-generated trend analysis and other analyses help one to make wiser decisions dealing with a wide range of assets.)
4. Establish and/or re-define your company’s culture. For example, supervisors and other team leaders often need more training to anticipate the needs of the business as well. Through specialized training, performance reviews, incentives and implementing properly designed staff “duties and responsibilities” systems, managers will become responsible for making sure that certain controllable problems almost don’t occur. These systems will also assist your team leaders to identify opportunities and act upon them efficiently. Superior anticipation
BE READY TO CAPITALIZE ON WHAT SHOULD BE A VERY ROBUST YEAR.
the best to become even better. It certainly is tempting to coast a bit this year because of the many pro-business signals coming from the Federal government. Some of the proposals will become a reality and some won’t materialize. Some of the business restrictions you face are on a state or local level, so you’ll still have challenges that arise. Changes in competition along with changes in customer preferences also favor rental companies that are nimble and can adapt their company accordingly. So, for all these reasons, it may be wise to avoid having a status quo mind set for this year.
7. Develop and articulate your company’s core values and team members’ core competencies. Core values can help to guide your company’s actions and to help it to stay on course. Core competencies also help to give structure to the team members’ mission and provides greater training emphasis in the all-important fundamentals of success in your rental company. Once developed, these guides must be articulated often to engrain them into fabric of your business.
and planning, along with the principles of preventative maintenance in all aspects of the business, should be made a part of your equipment rental company’s culture.
5. Plan for the long term. Just a few of these far-reaching decisions and related goals include what rental equipment to purchase or dispose of, what should your fleet size be in the months and years to come, what should the company goals be (as well as the goals for key staff members), what will the direct costs be as well as the indirect costs be to work toward these goals; and many more.
6. Avoid becoming overly complacent. Even if your company has done very well for the last few years, it isn’t wise to rest on your laurels. There are always many ways for
And since it’s always good to overdeliver, here’s one more reminder: your team (and you) are the heart and soul of the company. Continue to encourage and invest time and energy in your team. For owners and other team leaders, it certainly is discouraging to have trained, promising staff leave your organization. It’s easy to become cynical especially when there is such extreme competition for employees. It is wise to remember that trying to have a positive attitude about obtaining and developing people still makes the most sense and will serve you well. Don’t give up the quest.
LAYER 1 REMOVAL
Adhesive residue, Sealers, Surface imperfections
SOFT Material - Vinyl/Carpet - TS-8
HARD Material - Ceramic Tile - ALR-E
LAYER 2 REMOVAL
Adhesive, Glues, Thinset, Industrial buildups
SOFT Material - Adhesives - TMC-7, TL-9, SEC
HARD Material - Thinset/Adhesives - TMC-7, TL-9, SEC
LAYER 3 REMOVAL/PREPARATION
Adhesive residue, Sealers, Surface imperfections
Concrete Preparation - TMC-7, TL-9, SEC
In this line of work, you need reliable equipment that can tackle a wide range of tasks. That’s why John Deere offers a variety of rugged machines to help you round out your rental fleet and elevate your operation. And with John Deere dealer support, they come with a team of experts that always has your back.