
20 minute read
CALDWELL
The rotary leg lumber lifter is in daily use
Freres Lumber Utilizes Caldwell Rotary Leg Lumber Lifter
Advertisement
Freres Lumber Co. Inc. is using a custom below-the-hook attachment, manufactured by Caldwell, to lift long lumber loads at its Mass Ply Panel (MPP) facility in Lyons, Oregon.
The 15-ton capacity, 53 ft.-long, motorized rotary leg lumber lifter handles lamellas (thin layers / plates) of structural composite lumber, used to manufacture MPP products. It is attached to a 20-ton capacity overhead crane with two hoists; the lifting equipment and attachment were provided by U.S. Crane & Hoist, also of Oregon (Wilsonville).
Kyle Freres, VP of operations at Freres Lumber
“I was confident in Caldwell,” said George Beaudoin, general manager at U.S. Crane & Hoist. “Having worked with them for a number of years, I knew that they had a wide range of product solutions as well as the ability to design custom lifting solutions. The Freres team and I discussed a few different options and ideas. Lumber applications can present some challenges due to the length of the loads as well as the width. There are times when the long loads require multiple hoists operating in a tandem-lift scenario and there are other times when a custom lifting device is a better solution. As crane manufacturers, it is extremely helpful for us to be able to work with a company like Caldwell. It gives us the ability to make sure we are providing the best possible solution to the end user.”
The crane, hoists and lifter combine to lift product from a roll case and place it into inventory. The maximum unit dimensions that the motorized lifter picks is 60 ft. long by 30 in. high by 4 ft. wide. This is approximately 600 cubic ft. of material at 37 lbs. per cubic ft., which weighs a little over 11 tons. The lifter itself weighs another 6 tons.
Kyle Freres, vice president of operations at Freres Lumber, said: “We knew we needed to pick extremely long units, and we were aware that lumber lifters had been utilized in the past due to our relationship with LVL [laminated veneer lumber] producers. The lifter was a natural fit for that reason. The 4 ft.-wide units may be made up of 2 ft. by 2 ft. pieces. The lifter is also able to pick a unit from The maximum unit dimensions that the motorized lifter picks is 60 ft. long by 30 in. high by 4 ft. wide
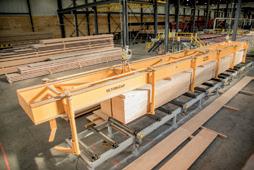
The 15-ton capacity, 53 ft.-long, motorized rotary leg lumber lifter handles lamellas (thin layers / plates) of structural composite lumber
The lifter is attached to a 20-ton capacity overhead crane with two hoists Freres Lumber Co. Inc. is using the attachment to lift long lumber loads at its Mass Ply Panel (MPP) facility in Lyons, Oregon
inventory and place it onto another roll case, which delivers the product to the next manufacturing phase.”
The rotary leg lumber lifter, which is in daily use, can effectively lift two bundles of lumber sideby-side, fully supporting them from underneath. Freres explained that the lifter “forks” or “legs” are rotated out parallel to the length of the machine. This allows the lifter to drop on top of the unit of product that is to be picked. Once the “legs” are under the unit they are rotated 60 degrees so that they are below the unit. When the crane starts lifting it picks the package with it. The aforementioned roll cases have rolls spaced so the lifter can set the unit gently onto the case.
Flexibility & versatility top priorities
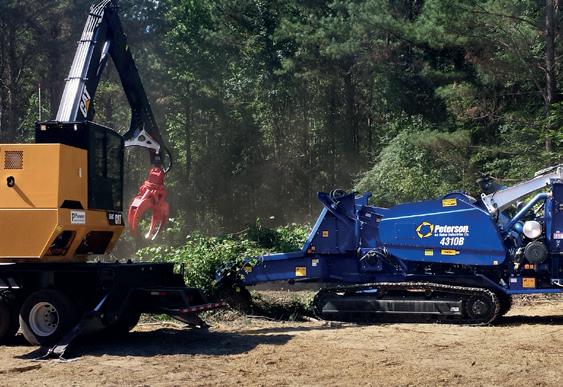
Big brands continue fight for market share in chipper sector
Peterson, Jenz, and Precision Husky – these are three of the biggest and most respected names in the biomass chipper supplier game, and they span the globe in terms of origin and reach.
This year once again sees these key suppliers drift further from their roots as purveyors of raw power and more toward suppliers of multiple business opportunity for the contractors buying these units. These opportunities take the form of a greater range of options in terms of chipping quality, mobility and efficiencies/ serviceability.
That is not to say power isn’t the first consideration for buyers of chipping technology and therefore for the brands supplying that market; it remains the chief requirement for those in the chipping trade. But the race to the top of the raw-power tree is now so tightly fought and the rates
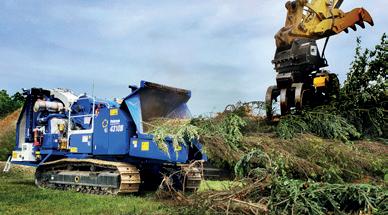
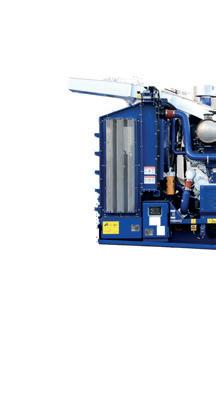
LOAD SPOUTS
All models come standard with an end-load spout, the 4310B, and 4310B Highwalker are available with an optional topload spout.
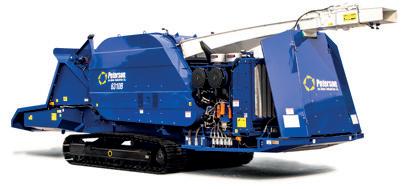
The 4310B Drum Chipper comes equipped with a wireless remote transmitter material, from logs up to 36″ (91 cm) in diameter, to brush and small feed stock.
of processing so impressive that the greatest opportunity to take market share from a rival is around the margins – namely flexibility of a range or of a specific machine.
More Power, More Applications
4300-Series
For applications needing more production, Peterson’s popular 4300-series machines pack a Caterpillar 755hp (563 kW) engine to get the job done. Popular with both biomass and land clearing applications, the Peterson 4300B-series machines are being used in a variety of terrain and feed stock jobsites. “Peterson has had a tremendous amount of success with the 4300B-series for pipe-line right of way contractors who need the extra mobility in tough terrain” said Michael Spreadbury, Director of Marketing for Peterson.
The 4300B-series machine is suited for high volume biomass producers who have a wide variety of feed material from brush and small feed stock to logs up to 24 inches (61 cm) in diameter.
At 58,500 pounds (26 535 kg), the track mounted 4310B Drum Chipper is designed for operations requiring high production and frequent moves between jobs. The 4300B, which comes on wheels, weighs in at 52,000 lbs. (23,586 kg.)
The chipper utilizes a 36 inch diameter by 44¾ inch (91 by 114 cm) wide drum with either 6 or 12 knife pockets. Traditional Babbitt type knife systems are standard equipment. Chip length can be set from 1⁄8 to 1¼ inch (3 to 32 mm) depending on rotor and knife configuration.
Other key features include a hydraulic clutch, sloped feed deck for ease of feeding the chipper, and wear resistant AR 450 wear surfaces on the drum pockets and shell. Optional material sizing grates further reduce oversize twigs and branches in the chips, and an optional chip accelerator helps with loading.
The 4310B Drum Chipper comes
Peterson 4310B Drum Chipper Cutaway The 6300-series drum chippers are suited for high volume biomass producers who have a wide variety of feed
THE POWER YOU NEED
Powered by a Caterpillar engine, Peterson drum chippers boast high torque for high volume production.
CHIP ACCELERATOR
Increases output density and decreases chip truck load times.
SAFE, EASY ACCESS
Knives are easy to access on all drum chipper models with our patented safety latch system and prevents the drum from moving during knife changes.
FEED ROLL
Large, aggressive feed roll smoothly feeds material into the chipper.
FEED CHAIN
Three strands of WHD 120 feed chain, paired with an aggressive feed roll makes loading easy for all types of material.
SLOPED FEED DECK
The sloped feed deck minimizes double handling of feed material by the loader.
GRATE SYSTEM
Provides ultraconsistent chip sizing; twigs and small stems are easily fractured.
BELLY BAND
Helps eject chips, and can include breaker bars to further assist with sizing for microchips.
ANVIL
Peter's anvils are made from AR400, for long life and accurate chip sizing.
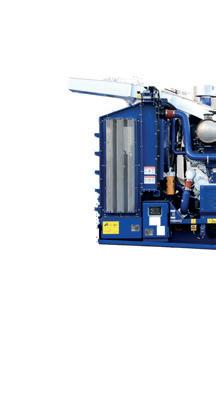
equipped with a wireless remote transmitter, putting control in the palm of your hand.
The end load spout is standard, and an optional top loading spout is available.
6300-Series
For those needing even higher production, or have large diameter feedstock, the C27-powered 6300-series drum chippers are an industry-leading solution. Available in both wheeled and tracked options, the 6300-series drum chippers can get the job done. “The 6300-series machines performance is really inspiring—we have seen these machines utilized on land clearing jobs in orchards, or just making biomass microchips, and their throughput is amazing
We always advise our customers to have plenty of trucking lined up with these machines, as they fill up a traditional chip van fast!” said Spreadbury.
The 6300-series drum chippers are suited for high volume biomass producers who have a wide variety of feed material, from logs up to 36″ (91 cm) in diameter, to brush and small feed stock.
The 6300-series machines are powered by a 1050 HP (772 kW) C27 Caterpillar engine. At 85,000 pounds (38,555 kg), the 6300B was designed for operations requiring high production and frequent moves between jobs. The tracked 6310B weighs in at 86,000 lbs. (39,010 kg).
The 6300-series drum chippers have two drum configurations, an 8-pocket drum to make standard biomass chips, or a 16-pocket drum to make microchips. An optional grate system has been redesigned to allow for adjustment from a microchip to a 1¼” chip with the same grates. Traditional Babbitt type knife systems are standard equipment, or an optional Key Knife system is available. Peterson’s chip accelerator system, adds load density, or throws chips well away from the machine for land clearing operations.
The chipper utilizes a 50″ (127 cm) diameter by 60″ (152 cm) wide drum. Other key features include a sloped feed deck for the ease of feeding and wear resistant AR450 wear surfaces on the drum pockets and shell. The feed chain has been upgraded to WDH120 for improved strength and long life.
In an age where machine owners want real-time data about their machines, Peterson has developed Peterson+ to enhance the customer experience with Peterson products. Peterson+ was designed from the ground up to enable an integrated team to work together by sharing machine data; helping provide customers the information they need to ensure successful grinding and chipping operations.
“Peterson+ is a unique communication network and information system connecting Peterson machines, customers and dealers with Peterson’s cloud-based machine monitoring, diagnostics and information systems,” said Michael Spreadbury, Peterson’s Director of Marketing.
“The system will help improve customer profitability through higher machine utilization, productivity and increased uptime.”
Peterson+ equipped machines, such as Peterson’s 4710D horizontal grinder, provide streaming machine data, including a GPS locator. Customers can have live access to the machine’s on-board display and operating information on their office computer, laptop or mobile phone.
Statistical historical data can also be used to track important information such as fuel consumption; engine rpm’s and oil temperatures giving owners and operators better efficiency, increasing profits through productivity.
The wireless display feature uses a local area network to allow machine operators to use their smart phone as a wireless display mounted in an excavator, loader, or control booth.
Peterson+ also makes a great troubleshooting tool. The operator, dealer, and Peterson technicians can all see what is going on with the machine’s control system – similar to having a technician on-site working through a potential problem.
Machine documentation, parts information, and support services are also made easily accessible through the Peterson+ portal via Peterson’s website.
Michael Spreadbury
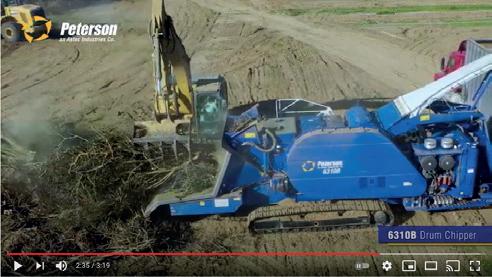
In this application, Peterson 6310B Drum Chippers are making biomass fuel chips from time expired orchards in California. The contractor will clean out the old trees, pull the roots out of the soil and make biomass fuel chips for energy from the wood. The cleaned land will be replanted with new trees so the cycle can start again.
The 460 stationary electric system recognized as the as the toughest and most productive wood hogs available,” the supplier stated.
This machine can handle really tough-to-grind materials like cedar, black spruce, lily pads and log ends. The Rawlings machine has a massive solid steel rotor that supplies more than enough kinetic energy to power through the largest feeding surges.
The hog upper case is clam shell opened hydraulically for quick over the years that did not have the overhead clearance in their existing footprint to allow for a clam shell opening type of machine.”
The VRM hog opens hydraulically from the rear of the machine allowing full access to the hog’s internal wear components and rotor for ease of maintenance.
All models in the Rawlings equipment are equipped with the patented Super Hi-Inertia solid steel rotor that powers through
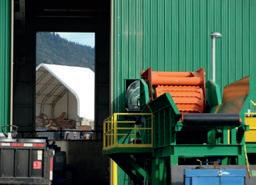
With over 40 years of experience in the forest and sawmill related industries, Rawlings has a proven track record in some of the toughest wood grinding applications that exist.
“We assist our customers with every aspect of designing, manufacturing and supporting a complete materials processing system,” the supplier stated. “We offer a complete line of stationary, portable, diesel or electric powered vertical and horizontal grinders in a full range of sizes and models.
“Each customers operation is unique with its own challenges with this in mind our design team treats each system specific to the customers operation and specifications. Add a wide variety of available options such as work platform decks, choice of belt, chain, vibrating in-feed and outfeed conveyors, metal, or magnet protection, product screening and separation, and you’ve got the flexibility to customize the perfect wood grinding system.
“Our HZX Horizontal model is ideal for processing logs, railroad ties, construction and demolition debris, urban wood waste,” the firm continued.
The Rawlings HZX Horizontal grinders features dual electric drive motors and a fully proportional feed system for efficient processing of diverse feed stocks. Sizing screens insure a consistent sized finished fuel product. Machine capacity ranges from 40-100 t/h, depending on feed stock and finished product size.
The powered feed mechanism insures a metered and controlled feed to the grinder producing a consistent finished product, while Our PXZ Vertical model is the back bone of our company
the slow speed, high torque cutting action means lower hp and lower noise. The horizontal models are available in stationary, portable, diesel or electric-powered units.
“Our PXZ Vertical model is the back bone of our company and is Rawlings Portable Wood Grinders are heavy duty portable grinders that are capable of producing valuable wood fiber products in a single pass
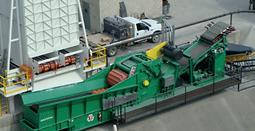
and easy service access. Simple design reduces parts inventory and is easy to maintain, while it operates one third lower RPMs than other types of hogs, reducing both mechanical wear and fines generation.
And, to complete the machine line up, the firm has introduced the VRM Vertical Wood Hog.
“No cookie cutter machine can meet everyone’s space constraints or challenges,” the supplier stated. “We have had several customers feed surges with ease.
“Our machine is tolerant of contaminants, rocks, and metal without catastrophic maintenance costs if metal enters the grinding chamber. Simple design reduces parts inventory and is easy to maintain. Rawlings Super Hi Inertia hogs are the most productive and efficient hogs available with proven track records in some of the toughest applications that exist.”
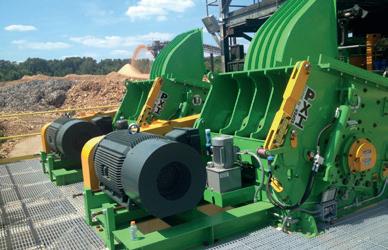
Next-level shredding system complete
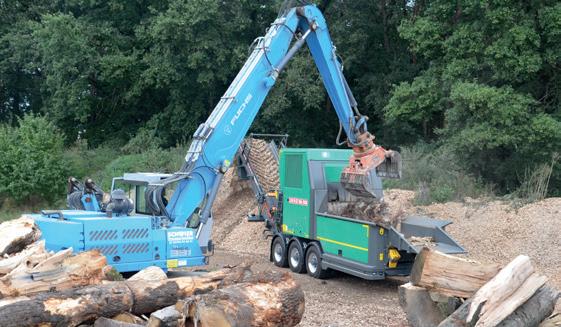
The BA 926 presents itself as a logical evolution of the newcomer BA 916 and sound chipper know-how
Size-reduction specialist Jenz has completed the latest iteration of its shredder generation with the BA 926 becoming the second new biomass processor this year following the release of the BA 916.
The newcomer also builds on the previous market favourite, the all-rounder BA 725, and provides an impressive overall package in addition to a noticeable performance increase of over 30%. The basis for further development was both know-how from the chipper sector, as well as proven success factors from previous shredding technology.
Taken over from predecessor
The foundation for the new development is the TwinGear System, already proven in the predecessor BA 725. The unique system with two working speeds enables application with almost any material – whether green waste, roots, waste or trunk wood.
“It is logical that we didn’t want this significant flexibility to be missing from the new BA 926,” said Product Manager Hans Heinrich Hermeier.
For material with high throughputs such as manure and compost, which tend to bulge at the discharge, it was necessary in the past to dismantle the overbelt magnet. This is no longer necessary because of the magnet can now be moved away from the material flow to a parking position. This and the height are now hydraulically adjusted using the easy2 Control.
The over-belt magnet is height adjustable from 150 mm and a scale with pre-defined steps allows the operator to set the same distance between magnet and conveyor belt again and again, depending on the material.
Copied from little brother
The design of the BA 926 is based on the proven machine base of its ‘brother’, the BA 916.
“This not only provides more freedom of movement at the discharge chute, but above all increases the intake opening to what is now 900 mm,” Hermeier said.
The higher opening in combination with the aggressive high-speed draw-in results in a remarkable increase in throughput – almost 60% more speed at the draw-in belt and almost 90% at the top roller. More power and an electrically adjustable preload pressure ensure rapid material draw-in.
“If more material is drawn in this also means, conversely, that more open area is required for discharge,” Hermeier said.
The unhindered material flow to the rear is ensured by the increased surface area; the gross screen surface increases by some 20%, but net by up to 30% due to optimisation of the screen. The screening surface can be further increased by the standard leakage belt and the installation of a screen floor with screening plates. This massively increases the throughput once again, especially in biomass applications. This allows the chippings to move away from the rotor very quickly.
The BA 926 is also similar to the BA 916 in terms of userfriendliness. In addition to the Operator Info System, consisting of an easy2CONNECT remote control
Hans Heinrich, Hermeier, Jenz
and LED status flashing lights, use of the innovative easy2 controller provides relief during everyday work.
Therefore, the conversion to the easy2 controller includes the mode-selecting system. Up to three programmes can be stored depending on the material to be processed. The programmes can therefore be used to adjust the entire machine at the touch of a button.
Even inexperienced drivers can get the maximum out of the machine, for example by calling up the ‘waste wood programme’. This takes into account the speed of the draw-in, rotor and top roller in addition to their preload pressure. This makes it easy to switch between chipper and shredder mode.
Influences of chipper knowhow
In addition to proven shredder components, the new BA 926 is also influenced by chipper technology. One new feature is the positioning of the lower draw-in roller. The screening technology used in chipper mode also originates from the chipper sector.
Hermeier described the advantage: “Taking the draw-in geometry from the chipper has the decisive advantage that the wood is fed to the rotor in a more controlled manner. The result is even better chipping quality and additional protection of the machine. In this context, slatted screens lead to best chipping results without excess lengths.”
Improved ergonomics and a faster screen basket change were recently in the foreground of further developments in the chipper area. So, it was obvious to do this for the shredders as well.
With additional handles and steps, it is easier to access the rotor and to climb up to the motor. The new machine stands and the greater draw-in height also provide more space for maintenance work on the rotor and also the shredding system.
In addition, the flail bar puller is electro-hydraulically controlled. Valuable time can be saved when converting between chipper and shredder mode. With the screen holder at the rear, the screens are readily available at the machine. It allows the transport of an additional screen set, consisting of two screens, which means it can be handled by only one person.
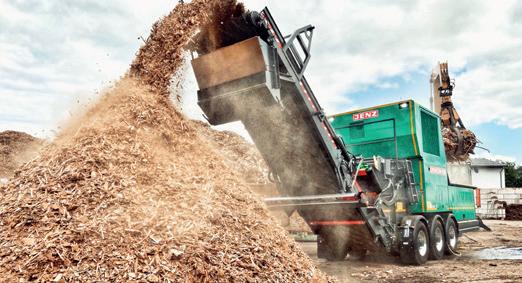
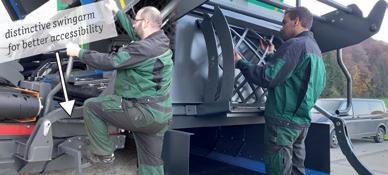
REVERSIBLE FANS FOR AUTOMATIC RADIATOR CLEANING | www.cleanfix.org

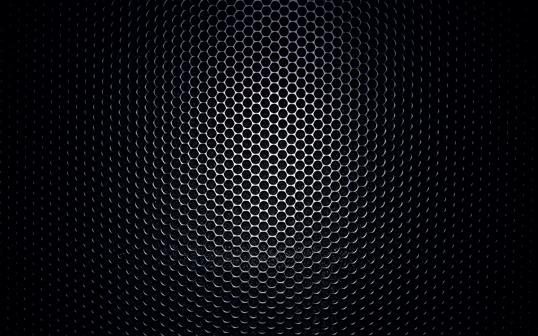
less Downtime
Even after half a century, industry leader Precision Husky never stops innovating its line-up of whole tree chippers, flail debarkers and knuckleboom loaders.
“Most of us came up in the logging industry and we know what it takes to win at this game. Customers all over the world recognize this commitment in the equipment we sell,” Smith said.
The latest achievements in Precision’s quest for forest industry perfection are accomplished with the remarkable design experience and application of ever-changing technology in the digital age.
From the top down, the Precision line is better engineered, built heavier, smarter and stronger for more fruitful logging and less costly downtime than previously.
“Precision is more than our name. It’s our number one goal.”
Precision Husky did not invent the whole tree chipper but it does make one of the best chippers available today as the more than 5,000 crews that use Precision products every day and have access to an unbeatable parts inventory and service technicians would likely attest.
The latest generation of Precision-built chipper pushes the envelope of technology to include a 66 in, five-knife option, which allows the chipper disc to operate at a slower rate. This not only saves wear and tear, it produces the most valuable chip quality available. Year after year, Precision chippers, operating with the 2600-4 flail debarker gives operators the highest production, lowest bark content and cost per tonne in the industry.
Plus, through messagebased CAN bus platform with its easy to use three wire system, a remote operator can monitor infeed through the HD colour control panel. The operator can see production from the top or at insertion in real time and adjust
The new 2366 chipper brings 25% more anvil control accordingly. That’s like having an extra man in the crew. Complete system diagnostics come at the touch of a button, making trouble shooting simple when it used to take hours of downtime.
The new 2366 chipper brings 25% more anvil control to the table to prevent slapping and turning. This results in smoother slicing and more uniform chips, with less horsepower.
The unit comes with a fully adjustable hydraulic system, which provides limitless control of feed rate. The patented PT Tech HPTO Hydraulic Power Take-Off is a totally enclosed wet hydraulic clutch that requires no adjustment through its wear life. During a torque spike, the clutch will act as a torque limiter by slipping to absorb the shock load. A microprocessor controller provides remote operation.
The industry-leading XL-175 knuckleboom loader comes standard in the 2366 Precision chipper. They are professionally engineered to be highly responsive and balanced with a smooth, powerful swing. These workhorse loaders have central hydraulic pressure checks and are the largest available with super heavy-duty sub frames.
“With its 3-axle spring suspension, our Precison chippers are tough to beat,” Smith said. “Choose the engine strength that suits your operation – up to 1,200 hp. We also offer a popular new radio remote controlled trackdriven chipper that goes where the big rigs can’t and are favoured by many of our international recycling operations.
The new FD 2600-4 debarker can easily process logs from 3-26 in (76-660 mm) in diameter with a feed speed of up to 200-plus linear ft (61 m)/minute. An operator can The Precision Husky chipper line generate over 100 t/h of clean chips.
The 2600-4 is also highly flexible. Because it allows for multiple individual solutions, it
Scott Smith,
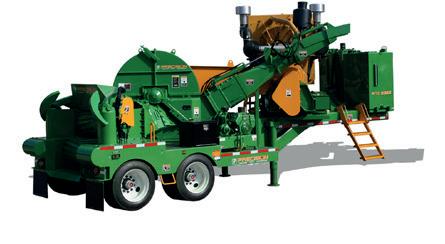
Precision Husky consistently receives the highest efficiency rates in the world. It can operate along with our mobile chipper or as a stand-alone debarker.
Bark and limbs are removed in enclosed housing, protecting the system from damage. The 2600-4 flail removes waste with an oversized hydraulic pusher, keeping the chamber clean.
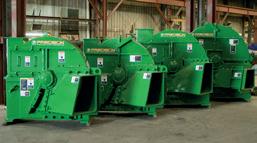
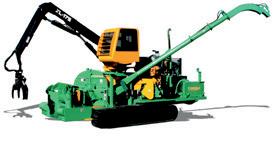