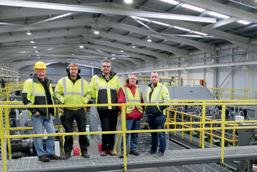
6 minute read
EWD
Good cooperation: Steve Williams (EWD UK), Shane O’Callaghan, EWD Managing Director Herbert Oppenborn, Gerard O’Callaghan, Niall Grainger (from left) At GP Wood in Lissarda, the logs are transferred online on three decks to the new EWD sawmill
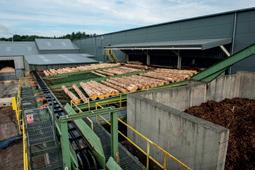
Advertisement
Rebuilt in record time
After a fire at the Lissarda/IE site in 2018, GP Wood immediately decided to rebuild the sawmill. The choice of supplier was made quickly: For those in charge, there was no other option than EWD, due to their previous good cooperation on the profiling line project in Enniskeane
In 2014, the Irish company GP Wood launched an extensive investment programme for its two sawmill sites in Enniskeane and Lissarda.
One of the first steps was the replacement of the saw line in Enniskeane with EWD, Altötting/ DE. The five-year plan included investments in Lissarda at a later date – but everything turned out differently. On Friday the 13th of July 2018, a fire broke out at Lissarda. The sawing line and parts of the sorting system were completely destroyed. “But it was immediately clear to us that we project – as well as the technology won us over,” Grainger explains.
“Thomas Lang from EWD spared no effort. The entire installation was planned and designed by EWD in 3D, which contributed significantly to the rapid assembly.”
With regard to the technology, Grainger and GP Wood project manager Shane O’Callaghan had makes the site slightly larger than Enniskeane.
However, “larger” is not to be taken literally with regard to the area – there are only 3.5 ha available in Lissarda.
“Making the best possible use of this space was a big challenge - especially since the new hall was

were going to rebuild,” says Niall Grainger, one of the managing directors of GP Wood.
Focus on flexibility
The investment package in Lissarda had to be put on the front burner immediately. Due to their very good cooperation in Enniskeane, the choice of supplier once again fell on EWD. “EWD listened to our wishes and designed a very flexible and robust saw line for us. The competence – even in our first not decided – in the end, they opted for a reducer band saw line with three Quadro band saws and two Optidrive Edger optimizer installations.
“We looked at many sawmills throughout Europe, and time and again the band saw stood out. With this equipment, we can respond very flexibly to customer wishes,” clarifies the GP Wood managing director. About half of the production concerns construction timber for building, the other 50 % is divided between garden timber and packaging timber.”
Grainger puts the cutting volume in Lissarda at 300,000 fm/y in an extended shift. This not allowed to be bigger than the previous one,” says EWD project manager, Rolf Rigoni. The new concept was already in place in Lissarda at the end of 2018, and production has been up and running again in January 2020.
“As in Enniskeane, the schedule was very ambitious this time - but we were once again able to implement it as planned,” says Grainger.
Online sawmill
GP Wood does not operate a classic log yard in Lissarda, but feeds the logs – in comparison to Central European sawmills – virtually unsorted at the sawing line. “It’s not as efficient, but it saves us space and costs,” Grainger reasons. One works on the principle of “scan and set”, similar to the American sawmill principle. The logs are fed in
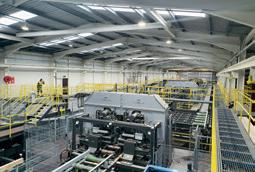
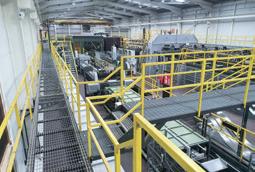
The EWD line with three quadro band saws: for special cutting patterns there is a merry-go-round system, here the view from the finish-cutting quadro (front) onto the line
A
B C
D
View from above on one of the two Optidrive edger optimizer installations: operator’s cabin (A), scanning section (B), TAE circular edging saw (C), edging separator (D)
sorted by length and then roughly pre-sorted on three decks based on diameter ranges. The band saw line is designed for log lengths of 3 to 5.4 m, with diameters ranging from 14 cm (small end) to 65 cm (large end).
In the first step, a 3D scanner determines the log dimension. The cutting pattern is determined on the basis of the scan. In the primary breakdown, the ZE2 infeed unit turns the log into the correct position. This is followed by the PF19 chipper for guiding faces on the left and right. The first quadro band saw of the type EBT4-1800 cuts up to four side boards. After the 90° rotation of the 2-sided cant, it again goes through a 3D scanner, a ZE2 centring unit, a PF19 chipper and the second EBT4-1800 quadro band saw, which also cuts off up to four side boards.
The resulting squared lumber can be cut in line directly with the third quadro band saw of the same type into up to five finished main products. Larger diameters or squared lumber with more than five products are returned to the first band saw via a merry-go-round system and pass through the line again.
“This means that up to three times five main products are then possible,” explains the EWD project manager. The feed rate of the reducing band saw line is up to 120 m/min, depending on the diameter.
High edging performance
The side boards are fed to two high-performance EWD Optidrive edger optimizer installations. They are designed for feed rates of 180420 m/min. “At the moment we are running at around 270 m/min,” O’Callaghan elaborates. With the Optidrive installations, the board is first scanned during lengthwise
A C
B

The side board is transported to two high-performance Optidrive board edgers - the picture shows the cross transfer (A), the infeed (B) and the scanning system (C) The operators of the reducer band saw installation and the Optidrive board edger sit in one operating cabin
transport.
After a scanning and optimisation section of 12 m, the actual edging process takes place with a TAE machine. The special feature of this TAE is the skewing and slewing of the saws of up to 25 mm/m at all cutting heights. This ensures a better quality of the side products and at the same time a higher yield. The board edgers are designed for board widths from 90-550 mm and thicknesses from 16-55 mm.
The band saw line and the Optidrive edger optimizer installation are operated from one cabin. Once all the fine-tuning work has been completed, only one employee is to be responsible for both high-performance board edgers, as one installation is to run in automatic mode. Grainger is very satisfied with how things have gone: “Despite the circumstances - the final steps of
EWD listened to our wishes and designed a very flexible and robust saw line for us. The competence – even in our first project – as well as the technology won us over
Niall Grainger, MD GP Wood
the commissioning fell during the first lockdown – we can already cut at full capacity.”
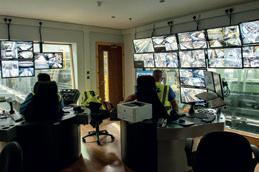