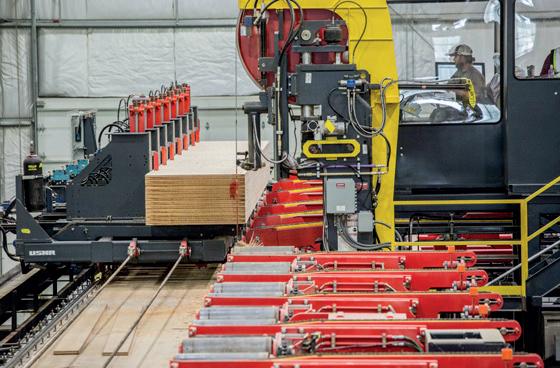
6 minute read
USNR
NEW Products, NEW Processes
Freres Lumber: Carving out a niche
Advertisement
The beam and column line with the new carriage is a way for us to expand on our primary Mass Plywood Panel products. We have the ability to supply a larger percentage of the entire project: beams, columns, and panels
Freres Lumber realized it was missing a portion of its market potential. After researching the mass timber market, the company decided to jump in with its own mass timber offering. With patents in hand, a brand new facility and production process, and very strong markets, the only thing missing was a way to expand the solutions it provided to potential projects. The company turned to USNR to help it realize the full potential of its mass timber appeal
While the wood processing industry is currently enjoying a hot market for lumber, plywood, and panels, a few years ago the markets were struggling. In 2015 Freres Lumber was challenged in the plywood market with competition from OSB and from imported products. That led the management team to look to broaden the company’s product portfolio and expand its market.
Freres Lumber is headquartered at Mill City, OR. Its operation comprises two softwood veneer plants, a plywood plant, a Mass Plywood Panel (MPP) plant, and a cogeneration power plant that produces electricity for the local grid. The plywood plant is in Mill City, while the other operations are down the road in Lyons. The MPP plant employs 20, and the complete contingent of personnel at the Freres company numbers 430.
Freres Lumber is family-owned, with Rob Freres as President and brothers Kyle and Tyler Freres managing the day-today operation. In 2015 market challenges were impacting the company’s operation for its primarily plywood products. At the same time, the Freres team knew their supply of Douglas Fir exhibited superior strength properties for a softwood. Kyle Freres, VP of Operations, explains, “We knew we were not getting full value out of our commodity plywood products, so we started to look into mass timber as a way to fully utilize the strength properties of the wood.” The team traveled to Germany along with a group from Oregon State University (OSU), and toured some Cross Laminated Timber (CLT) facilities. The team thought they could do better than what CLT was offering. “We did some product testing and proof of concept testing that proved out our design, and this resulted in our decision to proceed with the MPP facility.”
To date, Freres Lumber has patented its MPP veneer-based mass timber product and its manufacturing process, in 4 countries.
What is MPP?
MPP is a structural composite lumber-based panel. Freres has engineered MPP to enhance the natural strength of the wood while adding dimensional stability. Panels can be constructed with a combination of cross-grain
Kyle Freres Vice President of Operations at Freres Lumber Co., Inc.
and long-grain components. It can be processed to required specifications; floor, roof and wall panels can be manufactured as large as 11’-10” wide, 48’ long, and 12” thick.
Realizing the goal
MPP panels are marketed world wide, primarily to architects, engineers, and developers. Kyle explained that there has been a lot of interest in mass timber for commercial construction, and as well for mid-to-high rise multi-family apartments. “The commercial and industrial projects we were quoting required more than just panel products; they also utilize a large percentage of glulam material. So the beam and column line with the new carriage is a way for us to expand on our primary MPP products. Now we have the ability to supply a larger percentage of the entire project: beams, columns, and panels.”
Specialty carriage design
This specialty USNR carriage was designed to accommodate panels or billets that are 60’ in length. Dry weight of the carriage is 60,000 lbs. and it can transport 20,000 lb. billets. The carriage drive is engineered to transport that weight at a speed up to 410 ft./min. The single bandmill is USNR’s proven L&B design.
Kyle was happy with the result, “The carriage and bandmill have really expanded the range of products we can produce. Now we can process material that is 24” thick; we can produce columns that are 24” thick and 47-1/2” wide. That is a substantial piece of wood that we would never have been able to process without the new equipment.”
“USNR has been designing and manufacturing carriages for decades for processing hardwood and old growth timber. We thought this capability would be a good fit for designing a carriage that could process our large mass timber beams of the future.”
The project
There were several elements of the carriage that had to be completely designed versus a traditional log carriage. Kyle explained, “Instead of dealing with a round log rolling onto carriage knees and secured with spiked dogs, we had to account for a rectangular piece of wood that is conveyed into the knees, and held down by knurled dogs. Then instead of speed, volume, and grade being the main targets, we know what grade of product we are cutting because we laid it up in an engineered fashion, so we are most concerned with having a precise finish on the final piece.” He continued, “With any large project there are always growing pains, but USNR’s crew is very professional and they did a fantastic job on the installation.”
Kyle described their new process. “We are set up to run in batch operations. We will run that equipment when we have the need, so it’s not impacting the personnel requirements. We move individuals around to produce the product we need to fill the orders.”
Kyle made special note of two individuals who ensured the project’s success. Plant manager Ed Stezer was key to overseeing the project from start to finish, and Zack Holman, millwright and bandmill operator, made sure the carriage installation and start-up hit the mark. Overcoming challenges
Kyle said that with the COVID-19 pandemic, commodity markets were really struggling early on with coming to terms with the new reality. Kyle related, “Some commercial projects were delayed, so projects we hoped to be working on were pushed out to the end of the year. Luckily we had some orders come through our MPP facility that kept us going for a few months while the pandemic was at its worst.”
Riding strong markets
Currently the plywood market is extremely hot, similar to the lumber market. “We are seeing historically unprecedented prices on the plywood products. We try to price our MPP products for the long term in order to build market, and to build confidence in our customers that we can maintain prices.”
For now Freres is focused on sales and marketing efforts to inform the market of what is available, and that they can provide all the raw components from panels to beams and columns. Equipped with the means to add value to its MPP product line, Freres is well positioned to meet future demand.
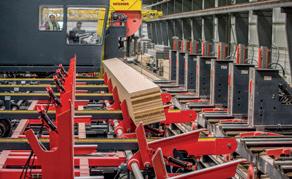
The panel is turned to process products from the opposite side

Beams have been cut and are separated out from the MPP panel
(Photos courtesy of Freres Lumber and Shanna Hall Photography)