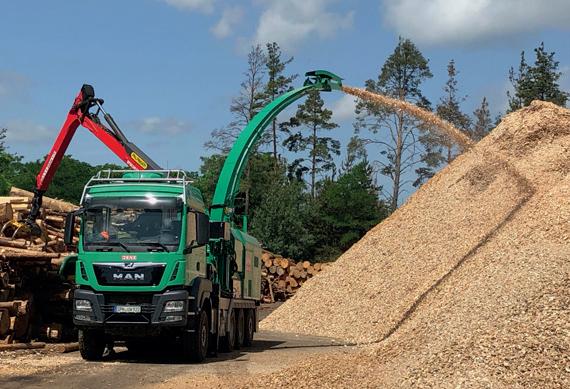
26 minute read
JENZ
Double the impact
JENZ’s new development of the
Advertisement
HEM 922 DQ chipping unit combines the advantages of the previous HEM 821 DQ and HEM 841 DQ in one machine. To simplify matters, the machine will be marketed under the name “Chippertruck hybrid” in future. The range includes the familiar two cab versions with mower glazing and as a Cobra (rotating cab). Sören Stutz, Area Sales Manager for sales region Eastern Germany, has sold two machines of this size in his area in recent months. JENZ wanted to know from him why the power packs are so well received and what experience he has gained with them.
JENZ: Mr. Stutz, two JENZ large chippers in the sales region Eastern Germany within the last few months - a remarkable achievement! It takes quite a bit of material to properly and, above all, permanently exploit such powerhouses. How do you think it is possible to consistently use a hybrid machine economically?
Sören Stutz (SST): Unlike the previous Chippertruck hybrid HEM 821, the new HEM 922 has a genuine 900 mm draw-in height. That alone makes this machine enormously flexible in terms of job handling. And that’s with everything from forest applications in shrub cuttings or soft logs to the processing of dense, heavy hardwood and industrial timber. The latter in particular is either processed for material use (e.g, the paper and pulp industry} or is intended for energy use. And the powerful self-propelled machine scores with its productivity precisely in this segment. After all, throughputs of up to 500 m3 per hour are possible. In general, the motto is: get a lot done in a little time!
JENZ: The high throughput of 500m3 per hour is above average. Critics might claim that further development of the professional chipper was merely about mass instead of class. But what about the quality of the woodchips produced?
SST: In my area in particular the machines are used for the production of coarse woodchips,
Area Sales Manager, Sören Stutz on the most powerful self-propelled JENZ Chippertruck hybrid
and always with the requirement that a low fines content is produced in the process. The D1 rotor, in this case with a size 38 pre-grip, produces high-quality woodchips. Linked to this, a slatted screen basket prevents the formation of excess Lengths and ensures that the material flows off quickly thanks to its large screening surface. The hydraulic blower does the rest.
JENZ: Hybrid machines are faced with the challenge of meeting many different requirements. They are supposed to offer enormous performance potential, be low-maintenance and manoeuvrable at the same time, and all this with low fuel consumption. How does the most powerful self-propelled vehicle manage to combine all this?
SST: The driving force is the add-on motor. We used a Caterpillar C18 with an output of 812 hp with emission level V to power the chipper by itself without AdBlue, by the way. This also means that the motor is spared when it is not chipping. e.g. during transport. In addition, the 32-tonne chipper surprises users with its enormous manoeuvrability thanks to the MAN 8x4-4 carrier vehicle, so that even operations away from the industry are not a problem. Those who need even more flexibility can also switch to AGRO tyres.
Away from industry the fuel tank offers the option for long working days without refuelling with a capacity of about 900 litres. During chipping we are then well below 0.3 litres fuel consumption per cubic metre with both engines. Of course, only if the wood is wellpositioned (laughs).
JENZ: You yourself have been a chipper driver and now view the machines from a completely different angle. What is there to highlight from the operator’s point of view?

SST: Definitely the screen basket and knives change! Unlike other chippers, we can quickly and easily change the screen basket with the machine’s own crane, depending on the application, thanks to the screen basket storage on the engine housing roof. Especially in industrial applications, you notice again and again how important changing the knives quickly and easily is. The steps up to the rotor housing have been optimised and the whole process takes about a quarter of an h0ur thanks to the professional tool system: from carrying up the practical knife pockets, to opening the swivel tool box and replacing the knives.
As a driver, the cabin is also of course crucial. However, subjective feelings also play a major role here because each cabin offers its own advantages. The driver gets more space and storage in the cab with

Flexible and manoeuvrable: The 4-axle chassis in the 8x4-4 version also enables operations away from industry. An optional single agricultural tyre on the drive axles results in even more freedom off-rood. mower glazing. The Cobra cab, on the other hand, provides a different sense of space because the windows are open all around and thus of course offer a better view of the working area. But it is also a little more expensive.
JENZ: Whether Chippertruck hybrid with mowing glass or Cobra cab, impressive and powerful are probably the keywords that characterise both models well. How would you describe the most powerful JENZ self-propelled machines in one sentence?
SST: Both machines are absolutely employer - friendly! (laughs) With the high impact both hybrid machines deliver there is simply no time for a break.
BRIEF FACTS
Performance
Hardwood (in cm)
Softwood (in cm) 60
80
Production up to: 450 m3/h
Draw-in opening
Draw-in width (mm) 1200 Draw-in height (mm) 900
Grinding unit
Drum diameter (in mm) 1.040
Drum construction D1
Type of installed knives 6 knives, regrindable
Pre-grip distance 30 mm (other pre-grip) settings by using wedges)
Material discharge system
Weight
Standard version
Hybrid technology
Truck Hydraulic outfeed incl. Professional package wear plates (armored)
ca. 32.000 kg
Engine
Power
Add-on engine
Engine
Power
Control-function
✓ easy2 ✓ Setup assistant ✓ Draw-in regulating systems CFA & CFA2 ✓ Camera system ✓ Premium light package easyLight
Care and maintenance
✓ Professional tool system ✓ Additional storage ✓ Hose retractor for compressed air ✓ Centralized automatic lubrication system Diesel engine MAN Euro 6d 375 kW (510 HP)
Caterpillar C18 EU stage V 597 kW (812 HP)
Rottne H8D Rottne H11D Rottne H21D
Rottne H8D
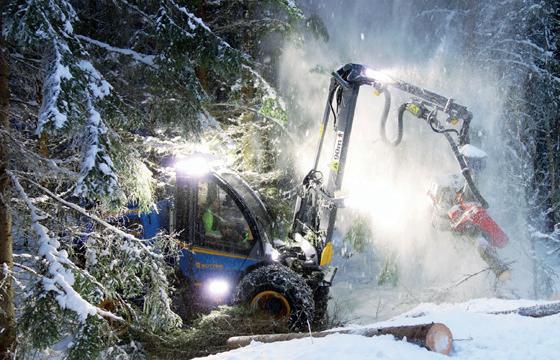
Rottne offers a complete harvester programme, consisting of the stand-operating thinning harvester Rottne H8D, the all-rounder Rottne H11D - as comfortable doing thinning work as it is doing light final felling - and the Rottne H21D for heavy final felling.
✱ New Rottne warranty
Since 2021, the new basic warranty foresees that Rottne replaces for free of charge the machine parts that break down due to manufacturing or material defects up to 3,000 working hours. Rottne is also responsible for the travel cost for the service technician, up to 300 km per warranty case, until the machine has worked for 500 hours. Besides, Rottne also covers the 100 hours service. This allows Rottne to take a leading position in the industry.
✱ Rottne harvester heads can now be fitted to all kinds of harvesters together with a new bucking system.
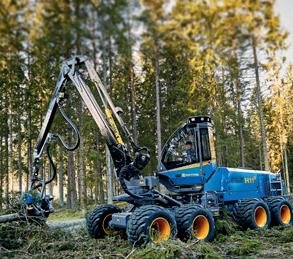
✱ Change to the new generation of ROTTNE
FORESTER system
A powerful and easy-to-use bucking system with many advantages. ✱ Luxury working comfort for operators
All of Rottne’s harvesters are equipped with the same spacious cab, offering excellent visibility providing a fantastic view over work environment. With the cab suspension system Comfort Line you get world-class luxury comfort!
✱ Quieter than in a car
It is also very quiet in the harvester cab (Sound level: 63 dB) – even quieter than in a new road car.
✱ Stage V engines certified for HVO
All of Rottne’s harvesters are equipped with environmentally friendly Stage V engines that are certified to run on both diesel and fully renewable biofuel HVO.
ROTTNE H8D – IDEAL FOR STAND-OPERATING THINNING
Rottne H8D is a compact and versatile harvester with unique characteristics including exact tracking, swing arms on the wheels, variable transmission and automatic anti-spin. This makes it very easy-to-operate with minimum space requirements, providing the conditions for smooth and fluent thinning and an undamaged stand – as well as high productivity. Tests conducted by the company show that the updated version of Rottne H8D offers superb off-road driving performance compared with previous versions and now definitely lives up to demands strengthening its market leading position among stand operating harvesters yet further. NEW for 2022 in Rottne H8 D
New powerful crane RK75 New version of Crane Damping for the lifting arm New Chain Lubrication – Grease New Chain Lubrication – Oil Free Wheel Valve H8D
More comfortable to drive on ROTTNE H11D –the road. AN EFFECTIVE MACHINE FOR BOTH THINNING AND FINAL FELLING

Rottne H11D is an articulatedsteered harvester for thinning and final felling. Powerful engine, hydrostatic transmission and articulated frame joint in the centre ensures excellent off-road performance and precise tracking. The high degree of customisability means that the harvester can be adapted for a range of working conditions. Among other things, the harvester can be equipped with six or eight wheels, a 10 or 11 metre crane, an individual bogie lift, as well as having the option of six different harvester heads to choose between from Rottne, LogMax and SP. Eight wheels and wide tracks spread the weight of the machine well, making Rottne H11D perfect for work on steep terrain or damp ground.
NEW for 2022 in Rottne H11D
Extra Fuel Tank New Crane Damping on the lifting arm New Chain Lubrication – Grease New Level Sensors for Diesel, Hydraulic & Transmission
ROTTNE H21D - A POWERFUL WORKHORSE FOR HEAVY FINAL FELLING
Rottne H21D is the harvester with real reserves of power, its tractive force of all of 230 kN and three-pump hydraulic system make production highly effective. With an extremely strong crane featuring the highest torque of all, effectiveness is guaranteed. Rottne H21D is designed for final felling, and built specifically to overcome difficult and steep terrain – and with eight wheels and broad tracks it can even manoeuvre extremely well on wet ground. The swivel cab follows the crane swing motion (just like the Rottne H11D). Like all Rottne harvesters, Rottne H21D also provides good level of profitability.
ROTTNE H11D: AN EFFECTIVE ALL-ROUND HARVESTER
Optimum trunk diameter: 20–40 cm Number of wheels: 6 or 8
Service weight: from 17 400 kg Sound level inside cab: 63 dBA
Engine: Stage V, 164 kW / 220 hp (at 1800 rpm)
Fuel: Diesel or HVO
Fuel tank:
Tractive force:
Crane reach:
Harvester head: 500 litres
167 kN
10,3 or 11,3 m Rottne EGS596, SP461LF, SP561LF, LogMax 3000T, LogMax 4000T, Log Max 5000D NEW for 2022 in Rottne H21D
New powerful crane RK310 New Chain Lubrication - Grease New Rotator Indexator HX 30 – Heavy Duty for Rottne EGS 706 harvester head Bigger Cooling Capacity on Rottne H21D New Level Sensors for Diesel, Hydraulic & Transmission
ROTTNE H8D: IDEAL FOR STAND-OPERATING THINNING
Optimum trunk diameter: 5–20 cm Number of wheels: 4
Service weight: from 10180 kg Sound level inside cab: 63 dBA
Engine: Stage V, 125 kW / 170 hp (at 2000 rpm)
Fuel: Diesel or HVO
Fuel tank:
Tractive force:
Crane reach:
Harvester head: 268 litres
120 kN
7 m
Rottne EGS 406, LogMax 3000T
ROTTNE H21D: FINAL FELLING IN DENSE FOREST
Optimum trunk diameter: 30-65 cm Number of wheels: 6 or 8
Service weight: from 24,200 kg Sound level inside cab: 63 dBA
Engine: Stage V, 227 kW / 305 hp (at 1800 rpm)
Fuel: Diesel or HVO
Fuel tank:
Tractive force:
Crane reach:
Harvester head: 500+225 litres
230 kN
11,0 m Rottne EGS706, Rottne EGS596, SP661 LF, SP761LF, LogMax 6000D, Log Max 7000D
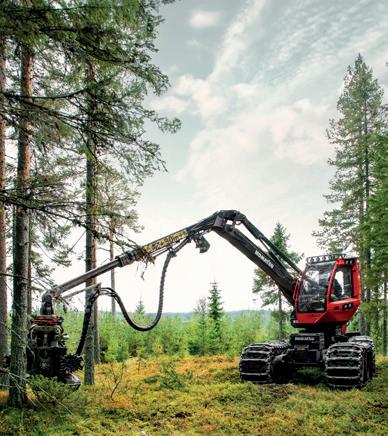
Creating a productive working day
There are some ingredients that are essential for creating a productive working day in the forest
For the forest machine manufacturer Komatsu Forest, taking care of the operator ergonomics and making the machine work as efficiently as possible on every level are two focus areas that are high priorities when developing and refining harvesters.
Smart Crane – a new option for Komatsu harvesters
An easily operated harvester crane is important for ensuring a productive working day. Every movement that can be simplified contributes to increased production and, ultimately, greater profitability.
In November 2021, Komatsu Forest introduced Komatsu Smart Crane for harvester, and with that took crane control to the next level – the crane is controlled with a single lever movement, from the main boom all the way to the tip of the telescopic arm. The result is a faster and more precise crane operation as well as a more relaxed and efficient operator.
Komatsu Forest presented its first parallel crane for harvesters back in 1999. Smart Crane is an extreme extension of this concept, with the crane moving as a single unit.
Precision and responsiveness are two of the greatest advantages of Smart Crane. The operator can easily steer the head where they want it in smooth, precise movements, contributing to a more relaxed way of operating the harvester. A relaxed operator can stay focused for longer and work more productively throughout the entire working day.
Another Smart Crane advantage is the need for fewer lever movements. The automatic control of the telescopic arm makes it even easier to steer the crane exactly where you want it – a single lever movement brings the crane from full reach all the way back to the machine. This provides better ergonomics for the operator and helps to conserve energy level throughout the day.
Another advantage of the simplified crane control is that it is easier for an inexperienced operator to quickly hone their crane operation skills.
One area where Smart Crane is particularly useful is the thinning of dense stands, where the operator often works with the head far from the machine, making extensive use of the telescopic arm. The automatic control of the crane makes work both easier and more efficient. It also simplifies when the operator, for example, wants to quickly raise the crane to move the head over the wheels to the other side of the machine. Faster and more efficient thinning saves on valuable working hours and contributes to greater profitability.
Precision and responsiveness are two of the greatest advantages of Smart Crane. The operator can easily steer the head where they want it in smooth, precise movements, contributing to a more relaxed way of operating the harvester
Proven stability
Komatsu harvester innovations have stood the test of time. In 1984, the Komatsu 901 was launched; the world’s first singlegrip harvester for thinning. And with the 901, Komatsu launched its stable Komatsu concept, which even today remains relevant and industry leading.
Essentially, these machines are based on the well-proven concept of a rigid articulated joint and a swing axle that when combined with the cab’s tilt cylinders provide superior stability, even with the head perpendicular to the machine or while repositioning the machine.
This is a concept that many decades later is still the most effective in terms of stability.
When the centrally mounted crane is working far from the machine, the center of gravity of the area supporting the machine naturally moves away from the
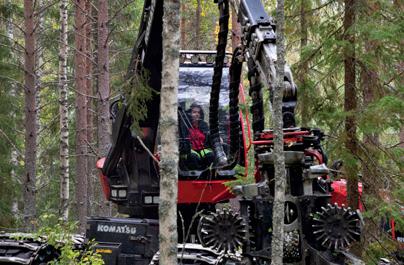
One area where Smart Crane is particularly useful is the thinning of dense stands, where the operator often works with the head far from the machine, making extensive use of the telescopic arm
Cabins are spacious with large windowpanes
machine’s centerline. In order to counteract the instability this would otherwise cause, two stabilizing cylinders on the swing axle act as a counterforce, locking the harvester in a horizontal position.
The force acting on the stabilizing cylinders comes from the pressure in the machine’s tilt cylinders, which are located under the cab. The pressure from each tilt cylinder transfers the force to the corresponding stabilizing cylinder.
Together with the automatic cab leveling, this ensures harvesters with great stability. With the automatic cab leveling the cab always keep horizontal no matter of the terrain. The operator always sits in a comfortable upright position, reducing strain.
Fuel efficiency
An important prerequisite for effective harvester operations is a machine that easily maneuvers all kinds of forest terrain. Komatsu harvesters have high ground clearance thanks to the smart design of the portal bogie, Komatsu Comfort Bogie. That, in combination with good tractive force and an efficient transmission – directing power where it’s needed while at the same time keeping the fuel consumption down – ensures Komatsu harvesters can keep the production at a high level. 3PS stands for three-pump system and ensures that the operator has the capacity to do several operations at the same time, with maximum hydraulic power; for example, slewing the crane, feeding the logs and maneuvering the machine, all while keeping the fuel consumption low. The secret lies in the two-circuit system, where the hydraulics for crane and harvester head can be connected or run separately, depending on what best suits the situation. Simply put, the operators can harvest more in less time, while still reducing energy losses.
Last but not least, the harvester cabins are spacious with large windowpanes that give a good overview over the work area. The whole cabin, together with the crane, can rotate 360° for maximum reach within the work area.
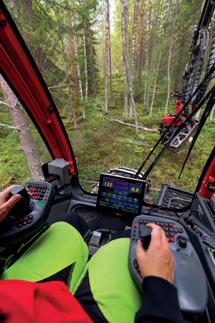
REVERSIBLE FANS FOR AUTOMATIC RADIATOR CLEANING | www.cleanfix.org
more Cooling more Power
more Productivity
less Downtime


Industry heavyweight John Deere has made the latest version of its Intelligent Boom Control technology available for all its CTL forest machines.
IBC is an excellent feature for operators. Instead of controlling the different sections of the boom, the operator can focus on controlling only the forwarder grapple or the harvester head.
The boom’s different sections are controlled automatically, and the electronic end damping softens the movements at maximum reach. This reduces the stress on the boom and on the operator, creating an easy and comfortable work process.
IBC is precise and easy to use. With comfort being critical for operators, the IBC helps to reduce fatigue and stay alert at work. The work performance becomes smooth and error-free. Improved productivity is another benefit and it’s something our customers have noticed: already 90% of the wheeled cut-to-length forest machines manufactured in Finland are equipped with IBC.
John Deere said it would continue to invest in technology and innovations that “support customers’ productivity and profitability throughout the machine life cycle”.
New operator-assist features
The latest version, IBC 3.0, introduces several operator-assist features that guide operators to the correct work methods, increase productivity, and improve the machine’s resale value.
The feeding assistance function significantly slows down the feed when feeding stems towards the machine and stops when encountering a defined safety zone, guiding the operator in the correct work methods. Sawing assistance guides the operator to avoid sawing towards the cabin.
The harvester head’s overrotation prevention protects against hose damage and enables the operator to focus on work planning. The operator-assist features and the functions that guide operators to the correct work methods also protect the machine from external damage and lower maintenance costs.
The continuous product development, new features, and the updating of systems and solutions are an integral part of John Deere’s way of operating. Thousands of hours of uncompromising product development ensure high-quality and reliable machines and products for our customers.
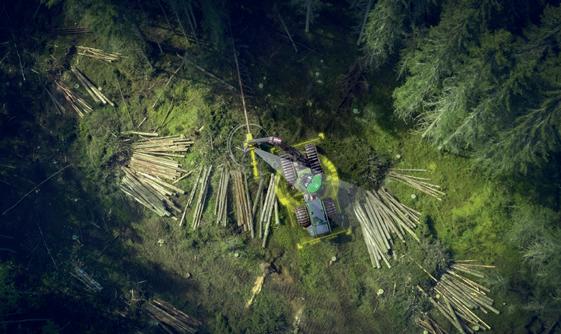
2-4 JUNE 2022
Come to the world’s forestry fair – Elmia Wood 2022
On 2–4 June 2022 the world’s leading forestry fair, Elmia Wood, will be held in Sweden. Elmia Wood is organised in the forests outside the city of Jönköping, welcoming visitors and exhibitors from across Europe to southern Sweden. The 2022 event focuses on innovative, sustainable forestry methods for the future.
Elmia Wood is a meeting-place for forest owners, contractors, forest officials and other forest stakeholders. See the latest new products and innovations, and lay the foundation for new business and commercial relations.
New on this year’s programme is the Wood Square, a forum where guests inform, discuss and debate on interesting topics, as well as the Wood Knowledge LOOP.
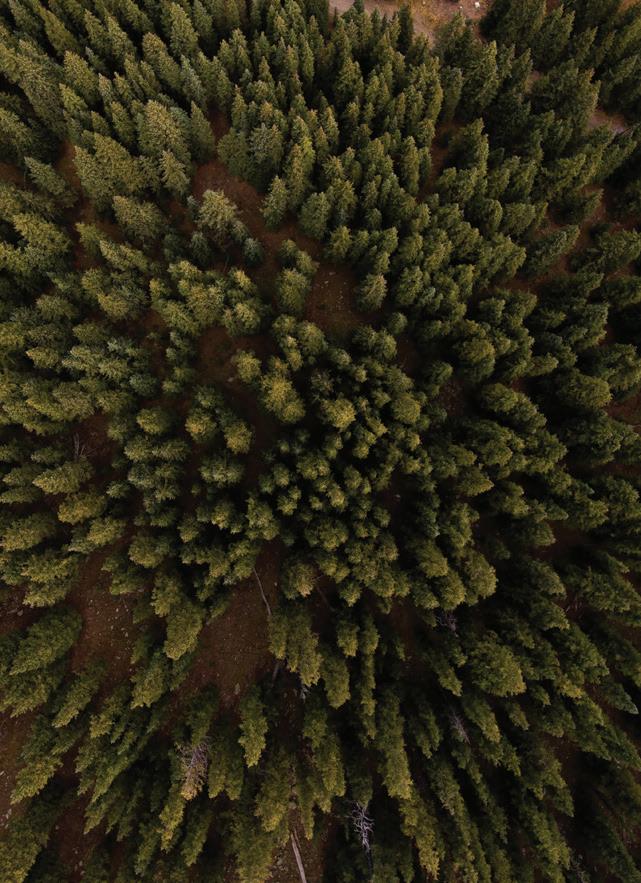
Welcome to Elmia Wood. Secure your place and buy a ticket now!
elmiawood.com
Delivering productivity and precision, the John Deere G-Series Wheeled Harvesters and MHSeries Tracked Harvesters were made to perform in the toughest conditions. The John Deere Harvesters are equipped with the latest technology solutions and support of the John Deere network, providing the reliability and efficiency customers need.
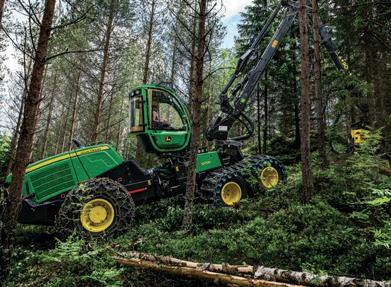
G-Series harvesters
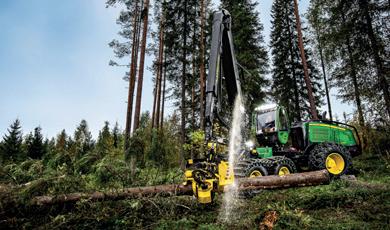
Thoughtful solutions went into the development of G-Series Wheeled Harvesters, including extensive input from customers. Including four power machines, these machines are built to overcome any obstacle. • Offered as a four- and six-wheel configuration, the nimble, productive 1070G is the perfect choice for thinning operations • The versatile six-wheeled 1170G handles everything from thinning to regeneration harvesting. With 26.5 in front tyres, the 1170G can provide a higher ground clearance, ideal for deep snow or rocky environments. The powerful eight-wheeled 1170G provides excellent stability on ordinary logging sites or steeper slopes, as well as the low ground pressure needed for soft-soil applications • With the power to handle large trees, the six-wheeled 1270G
Harvester is an exceptional all-around wheeled harvester.
This model is also available in an eight-wheel-drive option for conditions that call for maximum traction and climbing ability.
“We’re getting into rougher, more uneven ground,” said Doug Sanville, owner of Sanville Logging. “A lot of the easiest wood has been harvested in areas that are not ready for the next harvest cycle. The eight-wheel harvesters provide the flotation and stability we need in tougher, wetter, and frozen ground.” • For ultimate harvesting productivity, the stable, smooth 1470G Harvester is equipped with a CH9 rigid boom and perfect for tackling large timber and extreme conditions.
Available as a levelling or fixed option, the cab on the G-Series Harvesters provides large windows for outstanding visibility, ergonomically-designed seats, and air conditioning and heating. The rotating and smoothlevelling cab turns 290°, allowing 360° visibility of surroundings and boom movements. With the levelling cab option, the operator is guaranteed to remain balanced and comfortable in steep or uneven terrain.
The Processing Power Control (PPC) system provides the operator with energy-saving normal or boost options while it does the remaining work. The applicable processing level is coordinated based on work conditions and tree size, helping to advance fuel efficiency. The Twin Pump Hydraulic System
1070G 1070G 1170G 1270G 1470G
Doug Sanville, Sanville Logging
1470G
1270G
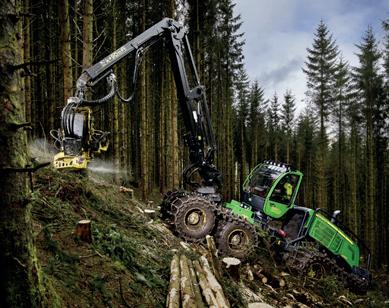
allows operators to have strong and precise control of the boom and harvester head, decreasing operator fatigue and increasing productivity.
The new and improved TimberMatic H-16 user-friendly control system enhances machine performance and precision with its control modules and wiring harnesses. The PowerTech Plus diesel engine delivers high torque at low RPM, providing excellent fuel efficiency and power without compromise.
A key feature of the G-Series Wheeled Harvesters is Intelligent Boom Control (IBC). Available with the 1170G CH6 boom, 1270G CH8 boom and 1470G CH9 boom, IBC makes it easier to manoeuvre the harvesting head. Operators no longer need to control each independent boom joint separately. The operator simply controls the grapple, and IBC does the rest, automatically controlling all boom movements based on the grapple location.
Another key feature, Adaptive Driveline Control, boosts drivability and output by automatically adjusts the engine RPMs to complement the engine load. Operators can select Normal mode for everyday operation or Power mode to get maximum tractive force in high-load situations. For lighter demands, Economy mode reduces engine speed and noise while improving fuel efficiency.
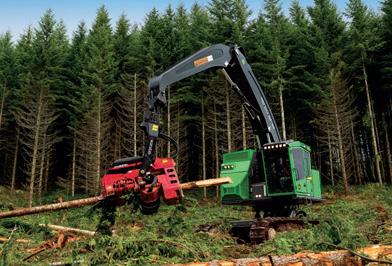
MH-Series tracked harvesters
The 800MH and 900MH-Series Tracked Harvesters are jobproven machines known to outrun expectations and deliver prominent performance. Operators have loweffort control and are comfortable with the spacious station, fullyadjustable armrests, air-cushioned seat, and ergonomically-designed controls. The overhead skylight and floor-to-ceiling front and side windows allow for expansive visibility.
Another key feature is the Rapid Cycle System, which combines the automated felling-head arm cycling with the simple control boom. This dramatically reduces the operator’s fatigue while increasing efficiency and productivity. The Rapid Cycle System tailors the machine for individual skill levels and specific harvesting conditions.
Available on both the wheeled and tracked harvesters, TimberMatic Maps and TimberManager are proven job site-mapping tools designed for full-tree logging operations. TimberMatic Maps enables enhanced visibility, allowing operators to review production values and see and create points of interest that can be shared in real-time with other onsite team members. Staff not on the job site can also access any of this data through TimberManager, to optimize tasks and increase efficiency.
“It’s worth its weight in gold,” said Eric Poehlman, a foreman with Sanville Logging. “I don’t have to physically be at the job to know what is going on or play phone tag with operators. I can see what has been cut, what has been forwarded to the landing, and how much is left to harvest. This makes it simpler for me to line up trucks to move the wood as quickly as possible to the mills. It’s made my job so much – I don’t think I could go back to the old way of doing things.”
859MH
2000T
A small, fast and reliable thinning head
The new Log Max 2000T is a compact harvesting head that offers excellent performance and reliability. Developed for compact harvesters, the 2000T is the latest addition to our thinning heads series, T-series. With these heads specially adapted hydraulics, you get a high-speed head both for feed speed and the saw unit.
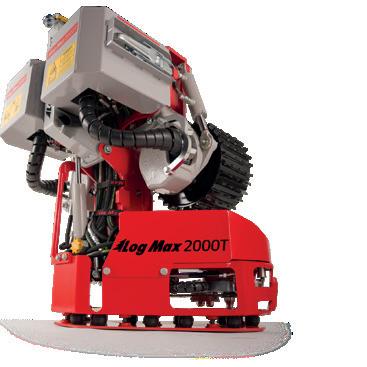
MAXIMUM FEED
You get a quick and powerful head through the improved hydraulics of 2000T.
EASY SERVICE
2000T is built to make maintenance work as smoothly as possible.
STRONG DELIMBING KNIVES
The design and castings of the 2000T are selected to maximize its service life. 30% FASTER
2000T has increased performance and drivability compared to its predecessor 928A. It feeds at 4 m/s, which is an improvement of 30%. The 2000T’s feed roller motors have a power of 280cc, which is less than its predecessor, which had 365cc.
The main pressure is also adjusted, from 210 bar to 280 bar.
The smaller motor improves the feed speed while maintaining traction thanks to the increased pressure. The raised pressure also gives 30% more power to the saw.
NEW HYDRAULIC CYLINDERS
The majority of the hydraulic cylinders are new on the 2000T. These changes provide increased quality and improved function.
The new hydraulic cylinders also have new robust seals to withstand tough working conditions. The saw bar feed cylinder has a locking nut for the adjustable rod end and a stronger attachment.
NEW CONTACTLESS SENSOR
The new sensor for the length measurement is contactless and has no mechanical moving components. That will result in minimal or even non-existent service and maintenance of this sensor.

The length measuring unit now has an easily accessible lubrication nipple to simplify service in your everyday work
NEW MECHANICAL STOP
A mechanical stop has been added to the length measuring arm to avoid using the measuring unit’s cylinder as a brake in its inner position. This modification increases the lifetime of the cylinder.
AVOID MOISTURE IN THE DIAMETER SENSOR
The diameter sensors have been updated with new bushings and seals to avoid moisture ingress.
NEW TENSIONER FOR THE SAW CHAIN
The tensioner for the saw chain has been updated compared to its predecessor 928A to simplify service and maintenance. It was previously tightened with an Allen key but is now redesigned to fit a 7mm flexible screwdriver. Log Max 2000T is equipped with a new saw unit named EasyCut.
NEW MOUNTING OF SAW SENSORS
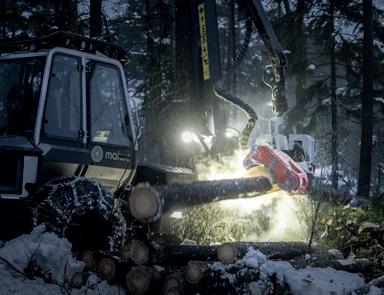
To facilitate the service of the head, you can now change the sensor and cable separately. The attachment has also been redesigned to make it easier to adjust the sensors. • The saw bearing is easier to lubricate via a new lubrication nipple. The new nipple gives the saw bearing an extended service life as you easily can lubricate it at more frequent intervals. • The Easy Greasy cover is easier to attach. The new design makes it possible to mount cable and protection separately, simplifying the service. • The cover of the saw box has been changed.
The new design makes it easier to handle, and less debris accumulates while driving. • The bar feed cylinder is updated with a piston rod that is no longer two-part and a lock nut that locks the adjustable rod end.
NEW CASTING IN THE DELIMBING KNIVES
There are entirely new castings in the delimbing knives at the 2000T, and the change will increase the strength and life span of the delimbing knives
OPTIMAL KNIFE EDGE ANGLE
All movable delimbing knives now have a new edge angle of 35 to improve delimbing
NEW SCREW TO UPPER DELIMBING KNIFE
The screw at the upper delimbing knife has been simplified to increase the service life. The new solution is now like on other Log Max heads.
BETTER HOSE ROUTING IN THE SAW BOX
The pins for the lower delimbing knife and the saw bar feed have been given an updated attachment to the frame. It provides simplified service and at the same time avoids hose rubbing and wearing.
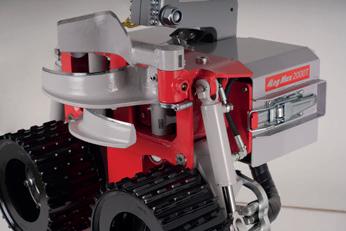
NEW SCREWS FOR RUBBER DAMPERS
The type of screw for the rubber dampers on the damped protection plate has been replaced to increase durability. The change fixes the protective plate to the frame and extends the life of the rubber dampers. Another screw has also been added to the attachment; today, there are six screws.
SOLID PLATE MINIMIZES HOSE WEAR
A new solid plate integrated into the frame has been developed to avoid pinched hoses when tilting the felling link. With the new solution, the durability of both hose and frame increases.
• The head has a new check-valve for saw chain oil to avoid oil spills when the head is in a transport position. • The head now has the same oil cap as Log Max other units. Easy to open and close, which makes the maintenance easier. • Extended filter inside the oil tank to make it easier to refill oil without spillage. • The protective plates around the delimbing knives have new attachments that have been redesigned and reinforced. • To prevent premature wear of the frame, a replaceable wear plate has been added below the measuring wheel hole. • The feed rollers now have large drainage holes to both reduce the head’s weight and avoid debris collecting in them. This modification reduces the weight by about 2 kg/wheel. • Wiring and connectors placed in the saw box have been fitted with Deutsch- and M12 connectors. This change simplifies service, maintenance and troubleshooting.