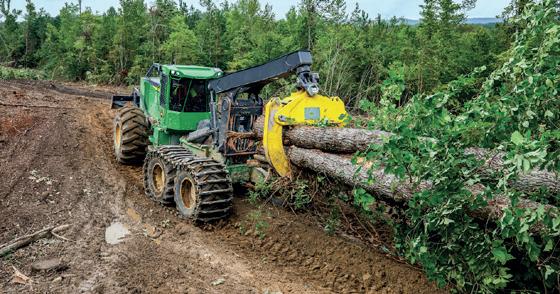
35 minute read
SKIDDERS
John Deere’s powerful purpose-built 768L-II Bogie Skidder
John Deere recently introduced the new six-wheel 768L-II
Advertisement
Bogie Skidder, a true woodland warrior designed to conquer wet conditions and steep slope terrain. Incorporating the proven, durable features found on the John Deere L-II Skidder lineup, the new 768L-II maximizes productivity, performance, and comfort when carrying hefty loads over long distances in challenging conditions.
“Profitability and productivity are critical in the woods, and as loggers take to new areas for jobs, they need dependable machines that are built with these niche applications in mind,” said Matthew Flood, product marketing manager, John Deere. “With our new 768L-II Bogie Skidder, we’re delivering a purpose-built machine that navigates tough terrain, such as swamps or steep slopes. Providing distinct features, the John Deere bogie skidder helps loggers maximize their potential, regardless of the conditions.”
The 281-horsepower 768LII features heavy-duty bogie axles, which incorporate large components to maximize durability and stability for long axle and tire life. The heavy-duty axles are purpose-built for tough applications, effortlessly pulling heavy loads and maneuvering tough terrain. The smooth, stable operation results in reduced machine vibration, ultimately minimizing operator fatigue. Another key feature is the excellent tractive ability and floatation. When combined with the bogie axles, ground pressure is reduced, allowing the 768L-II to work in wet terrain not accessible with a four-wheel skidder. As a result, the harvesting window is extended, adding more working days to the calendar.
MAXIMUM 22.3 -SQ.-FT. GRAPPLE ON THE 768L-II & 948L-II
The new arch design provides the operator with an expansive rearward view of the grapple and work area, providing excellent visibility. Improving maneuverability, the long wheelbase and boom-arch envelope boost reach and lift capability for the boom and grapple, increasing dexterity in the woods. The tight turning radius enhances agility at the landing.
“The John Deere bogie skidder is hands down twice as good as a regular four-tire skidder. It’s just all-around better in my book for productivity and ground disturbance,” said Jason Dawson of Triple J Logging. “With the 768L-II, you can carry twice as much of a load, especially in wet conditions and on the steep terrain, without tearing the ground up.”
The 768L-II retains the other customer-favorite features
Jason Dawson of Triple J Logging
introduced on the L-II product lineup. Streamlined and redesigned electrical and hydraulic systems result in improved uptime and increase guarding and protection of key components. An increased grapple squeeze force and twospeed winch further increase productivity, while articulation steering sensors improve the operator experience.
Highly regarded by customers, all L-Series II models feature a spacious cab, including ample storage space, configurable controls, and an effective HVAC system. Armrest-mounted electrohydraulic controls offer accessible, hand-finger operation of all machine functions, and joystick steering provides smooth control of steer, direction, and ground speed. The industryexclusive Continuously Variable Transmission (CVT) marries the efficiency of a direct-drive transmission with the smoothness of a hydrostatic drive. As a result, CVT provides more power to the ground by sensing the load, increasing torque and tractive effort as needed to maintain the desired speed.
768L-II BOGIE SKIDDER
Gross Power: 210 kW (281 hp) Gross Torque: 1,276 Nm (941 ft. – lb.) Max Grapple Capacity: 2.07 m2 (22.3 sq. ft.) Operating Weight: 23,697 kg (52,245 lb.)
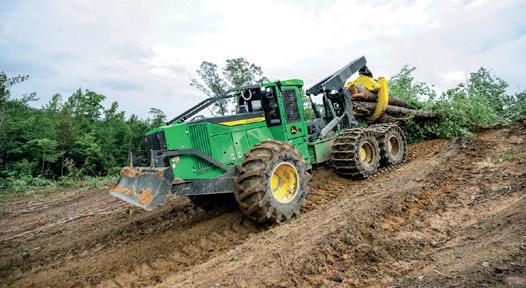
REVERSIBLE FANS FOR AUTOMATIC RADIATOR CLEANING | www.cleanfix.org
more Cooling more Power
more Productivity
less Downtime

Up to now, forestry contractors were primarily interested in powerful machines with all-wheel drive, switchable differential locks and a logging crane. Today the focus is also increasingly on other factors: Drive comfort and ergonomics are becoming more important. Also, efficiency and waste as well as sustainability and environmental compatibility of the machines are playing an even greater role.
Welte has developed the new 6-cylinder machines in the proven tradition of modular construction for forestry contractors with very diverse requirements. In order to meet the particular range of tasks in the best way, all variants of the new generation contain the reliable, compact and proven Welte machine technology. On combi machines the quick-change system also offers the forestry contractors the option to change between clambunk and loading basket, with no problems and in a time-efficient manner. The two-part combi basket patented by Welte is particularly suitable where different product ranges as well as energy wood have to be logged – changing from short to long can be performed during the trip in no time at all, without rebuild time.
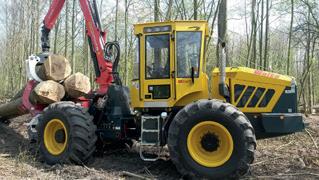
W230 4-wheel forwarder (skidder)
The W230 signals a new era for 6-cylinder skidders. Equipped with a Tier 5 engine, the new, ergonomically optimized panorama cab featuring an unobstructed rear panel gives operators a perfect view of the work area. The W230 redefines the skidder and can be used as a pulley, crane and clam bunk skidder.
The HSM name is synonymous these days not just with outstanding quality and innovation but also with first class service and spare parts service. Competent technical advice and maximum parts availability ensure that their customers remain competitive. This is also backed by their dealers and partners worldwide. During the design stage of the machinery, particular attention is given to accessibility and service friendliness.
HSM 805
The HSM 805 was designed systematically as a cable machine for terrain with extremely steep gradients and for wet ground. The heavy duty frame construction, the height-adjustable rear blade with high cable infeed and good visibility to the skid plate make it the perfect skidder. The low weight with optimal load distribution in conjunction with the powerful hydrostatic drive unit ensure very good gradability. With a wheelbase of 2.95m and a width of 2.4m (with 23.1x26 tyres), the 805 S is compact and agile.*
High productivity at low operating costs make the HSM 805 S the perfect skidder. *To ensure forwarding without damage to the harvested product, the machine can be optionally equipped with radio remote
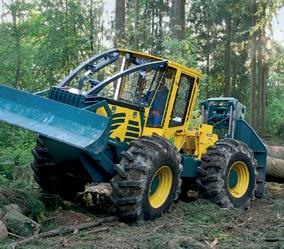
Slow running dual-shaft shredder for wood and green waste
The Crambo is one of the best machines for shredding all types of wood and green cuttings. The e-mobile series adds semi-mobile electric-powered versions to the line-up, featuring maintenance-free electric motors instead of diesel engines. The concept combines the compact design and flexibility of a mobile machine with the energy efficiency of a stationary machine.
Two slow-running drums with shredding tools minimize fine particle and noise/dust emissions, and resist contraries. The particle size is configurable by simply exchanging screen baskets. A modern operating console and convenient access to all maintenance points make everyday work very easy.
• Extremely large shredding compartment with two 2.8 metres long shredding drums • Counter-rotating drums with tools in a spiral arrangement for active material movement • Hydraulic folding hopper for more hopper volume
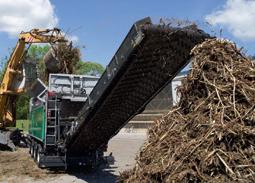
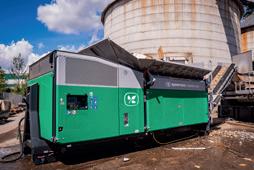
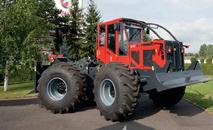
TAF 2012 Powershift 6C
Benefiting from modern technology in accordance with market requirements, the TAF 2012 PowerShift 6C from IRUM is the newest machine designed in their Research and Development Center. It is characterized by performance, efficiency and comfort intended for emerging markets, unregulated from the point of view of emissions.
The high-performance PERKINS engine, the modern power steering system or the PowerShift gearbox are just some of the high-quality components integrated by IRUM in the new TAF 2012 PS 6C machine: all the systems of the 2012 predecessor have been redesigned for more efficiency and comfort , resulting in a truly user-focused machine. What does this mean for you? The numerous technical and ergonomic improvements brought to the machine reduce the physical and mental stress on the operator,
Being perhaps the most important component of the machine, the engine of a TAF must adapt to extreme working conditions, using lower quality fuel, be reliable, easy to maintain and economical at the same time. Precisely for these reasons, THEY opted for the experience and skill of the PERKINS company, a world leader in the field of diesel engines for agricultural and industrial applications. The 1106D-70TA model used in the TAF 2012 PowerShift 6C develops 153hp and is part of the manufacturer’s more permissive range from an emissions point of view. The engine is mated to a 4-speed PowerShift automatic gearbox. Also, the machine has axles with multi-disc brakes in oil bath and lockable differential, 2×14 ton hydraulic winch, air conditioning, as well as mobile shield.
Comfort and exceptional features are also strong points of the machine. From the adjustable driver’s seat with air cushion and seat and backrest heating, to the video camera for monitoring the load, the TAF 2012 PS 6C makes for easu operation. The exceptional sound insulation ensures a wellprotected workplace in any season. The machine’s cabin, in addition to increased robustness and ROPS, FOPS and OPS certification, can be folded 45° to the right to facilitate service and maintenance work in hard-to-reach places, and the location of the controls has been redesigned for more ergonomics and comfort in use . Even the steering column is adjustable.
The new TAF 2012 PowerShift 6C from IRUM is a Romanian forestry machine with Western performance, standing out for cutting-edge technology, efficiency and comfort.

Shredders & Grinders
Size-reduction technology is looking more and more profitable as a secondary revenue stream or primary business
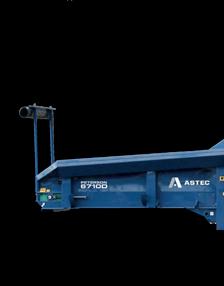
The argument goes that any forms of green product, particularly green and renewable energies, will be favoured as governments use increased stakes in enterprise to force the environment to the front of the business agenda.
This is likely to be a boon for forestry in general, but particularly for biomass production. And while high-level chippers may be the primary recipient of this new favour, all size-reduction technologies could potentially have an angle into new business.
Here, we present some of the leading products in this technology space that could turn forest waste into money for entrepreneurs.
Astec Industries is an industry leader producing a full line of Peterson grinders, disc and drum chippers, flail debarkers, and blower trucks. A history of innovation and reliable manufacturing has established a reputation for equipment of the highest quality. Astec equipment is manufactured in Eugene, Oregon, where each machine is engineered and built to exact standards.
Peterson was one of the first
KEY FEATURES
to develop portable horizontal grinders as wood waste recycling machines. This industry-changing innovation made sustainable forestry practices more attainable. Using horizontal grinders to process bark waste from in-field chipping into a value-added
1
4
2
3
1 Safety Guards
1 Safety Guards
Peterson horizontal grinders are built with safety in mind, including the projectile guard.
2 Sloped Feed Walls
Allow better visibility while loading and smoother feeding for more production in a wide variety of materials.
3 Feed Chain Conveyor
A robust feed chain conveyor efficiently feeds the rotor. A hydraulic drive motor synchronizes with the feed roll for near continuous feeding and massive throughput.
4 Adaptive Feed System
Monitors the grinding load and varies the speed of the feed system to keep the engine working at its optimal power curve.
It accelerates the feed when the engine load is light, slows when the load is high, and reverses feed when the load is excessive.
Peterson horizontal grinders are built with safety in mind, including the projectile guard. 5 Impact Cushion System Absorbs energy shocks and spikes to extend grinding system 2 Sloped Feed Walls component life and helps prevent catastrophic damage from
Allow better visibility while severe impact. loading and smoother feeding for more production 6 Rotor Placement in a wide variety of materials. Optimum rotor placement ensures positive feeding and reduces the potential of thrown material. Pinned or drum 3 Feed Chain Conveyor rotors are available.
A robust feed chain conveyor efficiently feeds the rotor. 7 Mobility Options
A hydraulic drive motor Astec horizontal grinders are available in wheeled, tracked, or stationary electric versions. Larger tracked grinders have synchronizes with the feed an optional tow dolly for easy transport, while the 1700D can roll for near continuous be towed with a dump truck. feeding and massive throughput. 8 Multiple Engine Options Available Depending on emission standards for your region, Astec offers both Tier II, Tier IV, and EU Stage V engine configurations.
4 Adaptive Feed System
Monitors the grinding load and varies the speed of the feed system to keep the engine working at its optimal power curve. It accelerates the feed when the engine load is light, slows when the load is high, and reverses feed when the load is excessive.
5 Impact Cushion System
Absorbs energy shocks and spikes to extend grinding system component life and helps prevent catastrophic damage from severe impact.
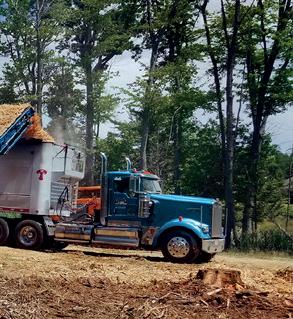
product means leaving less waste and site clean-up. Grinding slash into hog-fuel or nutrient-rich forest bedding can lessen logging impacts to an operation site. Reducing materials before it leaves the job site can increase payload and reduce truck traffic, fuel usage, and road erosion.
Astec’s continued commitment to sustainability and innovation has developed specialized delivery and processing equipment that turns low-grade organic materials into high value products. The company’s strong foundation of innovations, one built upon the next, culminate into a premium product.
5 8 9
11 13
The Astec Industries Peterson 4710D Horizontal Grinder is a track mounted horizontal grinder designed for highvolume producers with very demanding end-product specifications
“Not only are they built to withstand the harsh conditions of forestry operations, but they also offer the lowest operating cost per tonne,” the company said.
Astec’s three-stage grinding process starts with its patented upturn rotor, drawing material into the grinding chamber. The anvil is positioned for optimum sizing and the large grate area offers high-production. The upturn process provides better material fracturing, and Astec’s four-grate sizing system makes it easy to produce the size material customer demands.
This grate system offers unparalleled customization to tool the machine to fit output needs. Grates are removed through an easy-access door on the side wall. Combined with Astec’s heavy-duty bits, and robust anvil, their horizontal grinders have an exceptional wear life and accurate product sizing.
All Astec grinders feature an adaptive feed system. This system monitors the grinding load and varies the speed of the feed system to keep the engine working at the top of its power curve. A patented Impact Release System allows contaminants to be ejected from the grinding chamber to reduce the risk of catastrophic damage from ungrindable objects like rocks and metal, a system unique to Astec.
13 Optional Cross Belt
Magnet
Powerful cross-belt magnets pull tramp metal off of the conveyor, producing cleaner, profitable material. Earn additional income from scrap metal!
14
10 12 15
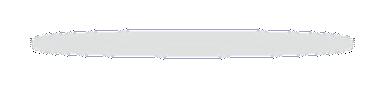
Absorbs energy shocks and spikes to extend grinding system component life and helps prevent catastrophic damage from
Rotor Placement
Optimum rotor placement ensures positive feeding and reduces the potential of thrown material. Pinned or drum
Mobility Options
Astec horizontal grinders are available in wheeled, tracked, or stationary electric versions. Larger tracked grinders have an optional tow dolly for easy transport, while the 1700D can be towed with a dump truck.
Multiple Engine Options Available 9 Telematics gives connectivity
New D-Model grinders feature Remote Monitoring
Analytics, including a wireless display for operators and offsite analytics.
10 Continuous Discharge Conveyor
One continuous discharge conveyor reduces materiel loss, increases uptime, and lowers maintenance.
11 Guard Rails
With safety in mind, guardrails are high-visibility yellow, reducing potential slip & fall hazards when servicing the machine.
12 IQAN Operating System
Fine-tune adjustments for maximum productivity.
13 Optional Cross Belt Magnet
Powerful cross-belt magnets pull tramp metal off of the conveyor, producing cleaner, profitable material. Earn additional income from scrap metal!
10 14 Optional Magnetic Headroll
Peterson grinders feature a magnetic headroll that allows for effective metal separation and high capacity production.
15 Optional Tracked Stacking Conveyor
Add an optional Peterson stacking conveyor to pile material even higher.
12
6 Rotor Placement 13
Optimum rotor placement ensures positive feeding and reduces the potential of thrown material. Pinned or drum rotors are available. 14
7 Mobility Options
Astec horizontal grinders are available in wheeled, 15 tracked, or stationary electric versions. Larger tracked grinders have an optional tow dolly for easy transport, while the 1700D can be towed with a dump truck.
8 Multiple Engine Options Available
Depending on emission standards for your region, Astec offers both Tier II, Tier IV, and EU Stage V engine configurations.
9 Telematics gives connectivity
New D-Model grinders feature Remote Monitoring Analytics, including a wireless display for operators and offsite analytics.
10 Continuous Discharge Conveyor
One continuous discharge conveyor reduces materiel loss, increases uptime, and lowers maintenance.
11 Guard Rails
With safety in mind, guardrails are high-visibility yellow, reducing potential slip & fall hazards when servicing the machine.
12 IQAN Operating System
Fine-tune adjustments for maximum productivity.
14 Optional Magnetic
Headroll
Peterson grinders feature a magnetic headroll that allows for effective metal separation and high capacity production.
15 Optional Tracked Stacking
Conveyor
Add an optional Peterson stacking conveyor to pile material even higher.
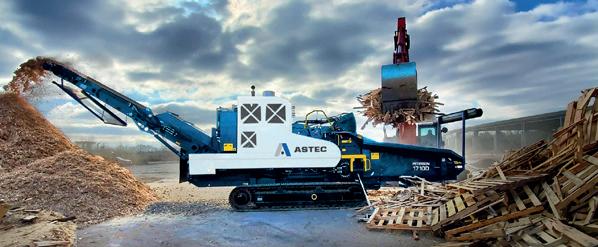
Heavy duty and mobile, the 1710D Horizontal Grinder can readily reduce a wide range of materials
DURABILITY & PERFORMANCE
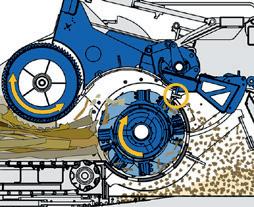
3-STAGE GRINDING PROCESS
The machine uses an upturning rotor in combination with a down-force compression roll to grind the feed material in a three-stage process, resulting in more accurate and consistent finished products.
1 Up Cutting Rotor
Opposing rotational forces create an aggressive shearing action. The upturn rotor draws material into the grinding chamber and minimizes bit wear.
Provides the first stage in material size reduction.
Available with pinned or drum rotors.
2 Anvil
Positioned for optimum sizing and production, the anvil provides the second stage in the sizing process.
3 Grate Area
The last step in the 3-stage sizing process, the large grate area results in high-production of a wide variety of materials and end products.
Peterson+ is a telematics system that is now available on all new Astec grinders. It gives the owner and operator a live view of their equipment performance, and GPS location details. Loading operators can see common machine analytics right from their cab. Peterson+ includes a host of other features, including maintenance log, directions to the machine site, and historical machine data.
Optional features increase the grinders flexibility between jobs. Work lights, cold weather kits, magnetic cross belt conveyor. The company’s liquid injection system is a high-flow water option that’s great for mulch coloring and dust control, and an optional transportation dolly is available on many Astec grinder models.
With an eye on innovation, Astec has added several models to the lineup.
1700 Series Horizontal Grinders
Astec’s most significant addition to the horizontal grinder lineup brings big power in a small package. This compact grinder has a 44 ft 1 in (1,344 cm) operating length but packs an impressive 455 hp (339 kW) Caterpillar C9.3B Tier IV engine and a large feed opening of 54 ft x 27 in (137 x 69 cm).
The 1700D Horizontal Grinder is available with wheels, while the 1710D Horizontal Grinder is a tracked model. The 1700D has a pintle hitch and can be transported between job sites with a dump truck. 4700D Horizontal Grinder
The most recent model release, the 4700D Horizontal Grinder, is designed for high-volume producers with very demanding end-product specifications. The 4700D is powered by a Tier IV Caterpillar C18 engine rated at 755 HP (563 kW).
2750D Horizontal Grinder
Astec’s 2750D Electric Horizontal Grinder is powered by a single 600 HP (450 kW) electric motor. An on-site electric machine may be the answer for grinding mill residuals to increasing profits since electric power costs are typically much lower than diesel fuel costs.
With a feed opening of 60¾ in x 32 in (154 cm x 81 cm) combined with Astec’s high lift feed roll for an optional opening up to 44 in (112 cm) high, the 2750D can reduce a diverse range of raw materials.
While Astec brought the industry-changing horizontal grinder to the marketplace to process wood waste from in-field chipping operations, sustained growth and a focus on customeroriented products continues to keep the manufacturer at the forefront of the market.
Equipment manufacturer Rawlings describes itself as a “proven leader” in size reduction technology that specializes in helping business owners with the design of custom wood-waste recovery systems for specific processing needs and budgets.
Rawlings states it can handle every aspect of configuring, building, installing, and supporting a complete materials processing system. Its electric stationary systems come in all shapes and sizes – indoor/outdoor; from simple stand-alone vertical hogs for saw and paper mills, to complete multi-dimensional systems.
“Add a wide variety of available options, and you’ve got the flexibility to customize the perfect wood waste recovery system,” the company stated.
Each system can be designed with work platform decks, choice of belt, chain or vibrating in-feed and out-feed conveyors, metal or magnet protection, product screening and separation all customizable for specific operations.
Markets for wood waste start with feedstock for engineered woods, landscape mulch, soil conditioner, animal bedding, compost additive, sewage sludge, and boiler fuel. All these end uses have similar processing requirements in that the wood waste has to be separated from other wastes, cleaned by removing contaminants and fasteners, and, in some cases, processed through grinding or chipping. The final use of the wood waste often determines how clean and consistent the feedstock must be (California Integrated Waste Management 2001).
“During our 40 years designing wood waste grinding systems we have found that most of our clients are looking to get the smallest end particle size on a single pass, onestage pass through the grinder,” Rawlings said. “We often suggest that this is not always the most economical option in the long run.
“Running the grinder and related equipment at full surge capacity results in higher consumption of spare parts and maintenance costs. And depending if you’re using electricity or diesel fuel these costs add up over time.”
During the preliminary design there are many factors that should be considered. Such factors include species of wood, moisture content, diameter and length of incoming wood waste, metal contamination and most importantly the required end product size.
For high volume high capacity wood handling operations that typically receive a large variety of contaminated materials such as railroad ties, pallets, construction, demolition and hurricane waste, Rawlings recommends wood waste systems to incorporate a combination of equipment. This could include both horizontal and vertical feed grinders.
Horizontal grinders or slow speed grinders are often utilized as the primary grinder while the vertical grinders are used to produce a smaller more consistent particle size. Using metal protection, product screening and separation allows the customer to protect their investment while producing a high-quality consistent end product.
If the wood handling system is designed to receive a steady stream of bark or sawmill waste a vertical feed hog is the preferred option. Typically in this scenario most of the incoming material is preprocessed further upstream and it already sized to be processed through this type of grinder.
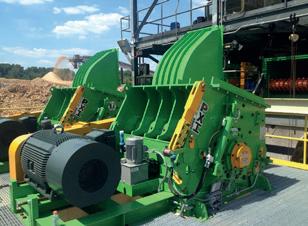
Rawlings Vertical Grinders
Each unit is equipped with the Rawlings Super Hi-Inertia Solid Steel Rotor. With the increased inertia of the solid steel rotor our machine runs at lower RPM’S than many competitors, resulting in overall savings of electricity and maintenance costs.
The Rawlings wood hog is recognized in the industry as a ‘Green monster hog’ and provides the crushing and shearing power needed to handle really tough jobs like green waste, cypress, redwood, cedar, black spruce, poplar and a wide range of other stringy and fibrous material. The machines are also tolerant of contaminants, rocks and metal without catastrophic maintenance costs if metal enters the grinding chamber.
“For over 40 years, we’ve assisted our customers in utilizing renewable resources while reducing and recycling a wide variety of wood waste into valuable wood fiber products,” Rawlings stated. “We offer a complete line up of seven different sizes of both vertical and horizontal hogs to fit any application.”
R
SALES PARTS SERVICE
COMPLETE LINE-UP OF THE MOST PRODUCTIVE AND COST EFFICIENT WOOD GRINDERS
Visit us at the 2022 Timber Processing Expo Booth 237

VERTICAL & HORIZONTAL MODELS AVAILABLE
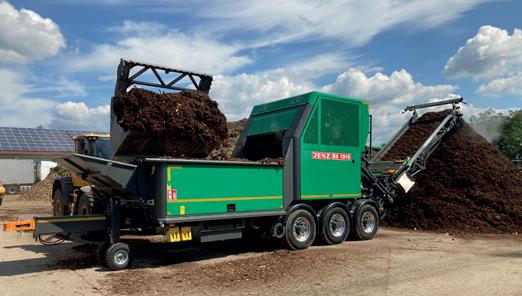
Superlative shredder technology
With the BA 916 and BA 926 series, JENZ successfully introduced its new shredder generation to the market in recent years. Now the largest biomass processor to date, the BA 965, has also been revised. The result is the BA 1016 - a new dimension in the JENZ shredder range.
New introduction of the largest JENZ biomass processor BA 1016
The development work for the BA 1016 is largely based on the experience of our BA 916/926 newcomers, which have been very well received on the market to date,” explains Dominik Meden, JENZ product manager and specialist in the field of shredder technology. “This starts with the optimal intake geometry, followed by the pronounced userfriendliness and ending with the new hydraulic system ‘JENZ Smart Hydraulic’. In addition, there is the screening technology for shredding applications, which is newly developed for the BA 926, which is also not to be missed in the BA 1016. The result is a technically mature and enormously powerful machine that nevertheless stands out clearly from its ‘little brother’ BA 926.”
Powerful engine for extreme throughputs
Equipped with a Caterpillar C18, the BA 1016 has an output of 812 hp. The CAT engine, installed in the largest configuration, makes
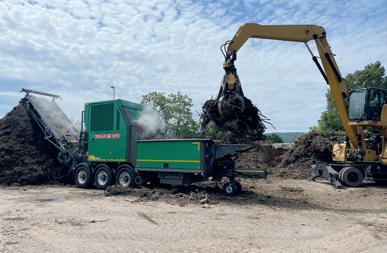
the BA 1016 extremely powerful in terms of throughput. “ We consider the fact that it continues to do just fine without AdBlue and yet also meets the Stage V requirements, as particular advantages of the C18. The distinctive torque curve allows us to operate at wear- and fuelsaving speeds while still increasing throughput. Maximum efficiency and throughputs of over 400 m3 were the goal here,” says Dominik Meden.
Focus on user-friendliness
Similar to the BA 916 and 926 series, the new BA 1016 also focuses on user-friendliness. This includes smartphone-like control via the proven JENZ easy2 machine control system, the Operator Info System with LED status lights and new easy2CONNECT radio remote control, or intelligent assistance systems such as the GFA (Grinder Feed Assistant) infeed control. Ergonomic maintenance has also been taken into account. “The two-part screen basket system in particular makes screen basket changing fast and ergonomic, as it can be done by just one person,” emphasizes Dominik Meden. The operator’s everyday work is made easier by the newly implemented “JENZ Smart Hydraulic” hydraulic system. “In the area of the intake, we have significantly improved control behavior as a result. In short: we can selectively keep the auxiliary engine lugging and thus can use the complete performance spectrum of the engine and bring it selectively to its capacity limit. This results in more throughput, paired with lower fuel consumption. Additional advantage: the machine and the auxiliary engine are protected by the quieter, constant operation.”
New conveyor belt for optimized material flow and easy transport
Due to its inlet width of 1,620 mm and its inlet height of 960 mm, the BA1016 can process large quantities of material. To ensure that the enormous material flow is low in fuel and wear, the JENZ engineers rely on an extra-large screening surface and a specially developed discharge belt. “In total, the conveyor belt has become longer and wider and scores with an increased delivery speed. As a result, even difficult material can now be conveyed onto high transport vehicles with a maximum discharge height of 5.10 m. Due to the increased width and the selected profile, the material layer thickness is lower and the magnets can clean the material optimally. The result: very clean end material,” says the product manager. An additional plus point of the new conveyor belt: a reduced machine length. This is ensured by a different folding technique that enables machine transport without a special permit or special vehicle. “We are proud that we have succeeded in combining 812 hp performance with a compact transport length of 10.55 m. This makes the BA 1016 a mobile but very powerful shredder with technology that is kept simple. This
enables worldwide operations, even in remote regions,” says Meden.
The product manager sees a wide range of applications: “Due to the energy transition, heating material from waste wood and roots is increasingly in demand, so that powerful machines are becoming more and more important. Likewise, the compost market is demanding ever more powerful shredders due to rising fertilizer prices. This is exactly where the BA 1016 comes in with its efficiency and enormous throughput.” Greenwaste
Bark
Waste wood
Roots
Intake
Intake width x Intake height (mm) Free loading length (mm)
Main drive
Standard-Diesel engine CAT C18 (kW / HP) 597/ 812 Shredding unit Rotor diameter (mm) 1.120
Number of fails 430
440
310
190
1.620 x 960
4.500
34
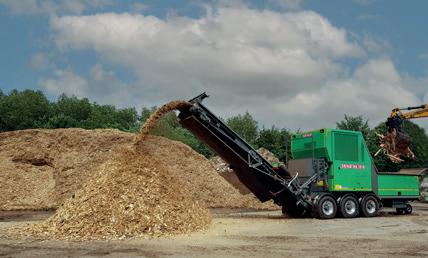
Newcomer BA 1016: The machine has a powerful CAT C18 engine with 812 hp, a large rotor diameter and a large inlet opening – an entirely new dimension in the JENZ shredder program.
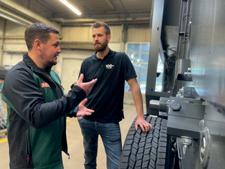
Morbark offers a full line of Wood Hog Horizontal Grinders and specialist Tub Grinders in a range of sizes, on tracks or tires, diesel or electric powered. Add a wide variety of available options, and you’ve got the flexibility to customize the perfect grinder for your particular needs.
The Wood Hog is the best industrial-grade grinder you can get for processing brush, yard waste, clearing debris, storm debris, C&D waste, other mixed woody feedstocks, and asphalt shingles into saleable products. All Wood Hogs come standard with the Morbark Integrated Control System (MICS) to maximize production and engine efficiency; a laser-cut, factory-balanced rotor for unsurpassed durability; and an aggressive feed wheel with an internal poclain drive that has no chains or sprockets for more torque and reduced maintenance. 6400x Wood Hog Horizontal Grinder

6400X WOOD HOG HORIZONTAL GRINDER
Ideal for processing wood waste, land clearing and storm debris into saleable products, the 6400XT Wood Hog weighs in at less than 96,500 lb (43,772 kg) and measures 11’5.5” (3.49 m) wide with the standard Caterpillar 325L undercarriage with 600mm double grousers, allowing the unit to be transported to nearly all domestic and international markets. The infeed bed is 24 inches (60.96 cm) longer than previous Morbark grinders in the 1,000-plus horsepower range and has sloped sides. This configuration improves operator sight lines for more efficient loading of material.
FEATURES AND BENEFITS
• The area between the hood and the engine has been reconfigured to 31.5” (80 cm) of working space, for better access to components for general maintenance or to change screens. • The Morbark Integrated Control Systems (MICS) automatically adjusts feed rates and monitors pressures and feed wheel position to maximize production and engine efficiency. • Standard on the 6400X is a removable infeed chain return floor, which allows excess material to fall away to minimize the wear on the floor, bed chain and inserts, particularly useful in land-clearing or other applications with dirty material. • The hydraulic hinged and locking door allows quick and easy access for changing grates. • A proven external adjustable break-awy torque limiter provides drive line protection against catastrophic damage from contaminants. 3400X WOOD HOG HORIZONTAL GRINDER
Listening closely to customer feedback while developing the design for the 3400XT Wood Hog, Morbark provides the features customers want and the versatility they need, while staying true to our proven technology. One of the most important features of the 3400XT is that it can be made as narrow as 8’6” (2.59 m), making it within the legal transport width in any country, no matter what engine is used.
With 800 horsepower (596 kW), this model is ideal for a broad range of applications in a wide variety of markets worldwide. Like all of Morbark Wood Hog models, the 3400XT also is available with electric power. The size of the 3400XT allows the model to be configured for
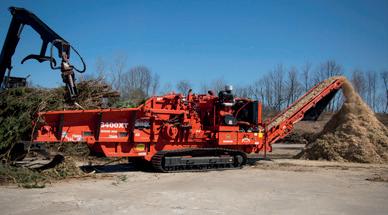
3000X WOOD HOG HORIZONTAL GRINDER
Ideal for niche markets like municipal recycling, pallet recycling, lot clearing, nurseries and tree care debris, the Morbark 3000XT Wood Hog Horizontal Grinder is perfect for processing yard waste, brush and other mixed woody feedstock into saleable product. The size of the 3000XT allows the model to be configured for multiple applications and global markets without additional design considerations.
2400X WOOD HOG HORIZONTAL GRINDER
The compact and configurable Morbark 2400X Wood Hog Horizontal Grinder is perfect for processing yard waste, brush and other mixed woody feedstock into saleable product.
TUB GRINDERS
Morbark introduced the first industrial tub grinders for use in wood waste recycling and land clearing operations in 1990, and has led the industry ever since. We offer the most complete line of tub grinders available, in a range of sizes and in several configurations – with or without cab and loader, on tracks or tires, diesel or electric powered. Add to these choices a wide variety of available options, and you’ve got the flexibility to customize the perfect Morbark Tub Grinder for your particular needs. Morbark Tub Grinders are designed for the most challenging recycling applications. They excel at processing yard waste, pallets and other mixed woody feedstocks into saleable products.
1600 TUB GRINDER
The largest tub grinder on the market, the Morbark 1600 Tub Grinder is able to power through and reduce materials from large land clearing or organic/wood waste programs. With an 11’2” (3.4 m) tub diameter, 15’ (4.57 m) tub opening and a capacity of 20 cubic yards (15.3 cubic meters) and 1,200 horsepower (895 kW), this machine can power through tons of raw materials from large land-clearing projects and organic/ wood waste processing. The Morbark Integrated Control System (MICS) monitors key systems while 3000x Wood Hog Horizontal Grinder
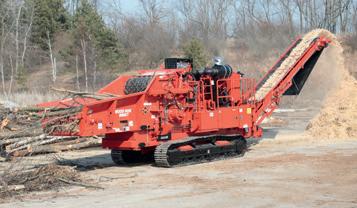

2400x Wood Hog Horizontal Grinder
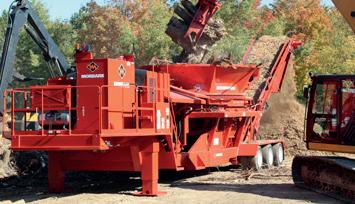
1600 Tub Grinder
maximizing performance, and the remote control allows you to quickly adjust feed systems for top production rates and fuel efficiency. FEATURES AND BENEFITS
• Tub is equipped with hydraulic augers that allow the operator to quickly remove product from beneath the mill. During material surges, pressure sensors automatically slow tub rotation to prevent plugging. • The full breakaway torque limiter system protects the engine and clutch against shock and overload without stalling the engine. • Laser-cut, factory-balanced mill with forged hammers provides optimum grinding power.
XR mobil-e
Single-shaft shredder for efficient coarse, medium and fine shredding of different material flows • Mobile shredding concept • Sturdy design with high resistance to foreign objects • High material quality with high throughput performance • Low maintenance expenditures • Low noise emissions
Advantages:
• high performance • low energy consumption • low noise emission • minimal dust formation • durable Tools Available as: diesel mobile and electrical stationary
Primary shredder VB 450 series
HAMMEL Recyclingtechnik GmbH
Applications: Wood: wood waste, demolition wood, small root stems, green waste, pallets Waste • domestic waste, industrial waste, paper • Scrap: electronic scrap • Functional principle: hydraulically operated slow speed recycling machine with two-shaft-system
Double-shaft shredder IMPAKTOR 250 evo
The mobile double-shaft shredder has gained international recognition since its launch and is now a primary choice for companies within the demolition and processing industry.
The extremely flexible and robust shredder features a unique combination of track system and hook lift version, a revolutionary shaft quick-change system, an innovative SCU control and a shaft design that expands the machine’s range of applications many times over.
In addition to numerous applications for construction and demolition waste, the mobile shredder is also suitable for processing railway sleepers, rootstocks, old and trunk wood, tyres, household and commercial waste and many other applications Double-shaft shredder TITAN 950
In nature, the element TITAN stands for strength, reliability and durability. These characteristics have been and continue to be the key specifications for the development of the double-shaft shredders within the ARJES heavy-duty class. In order to be able to guarantee a wide range of applications with the best results, the mobile shredders are equipped with a track system as standard and are available in two different versions.
TITAN shredders feature a revolutionary shaft quick-change system, an innovative SCU control and a shaft design that even meets the most difficult requirements.
Numerous applications can be found in the construction and demolition industry, for shredding mixed scrap metal*, car bodies, tyres, in the processing of household and commercial waste, as well as in composting and wood processing plants. Double-shaft shredder IMPAKTOR 250 evo
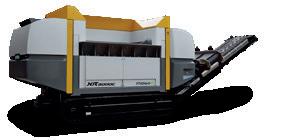
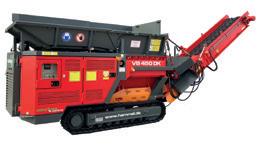
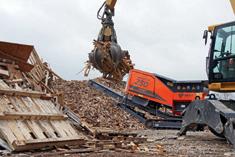
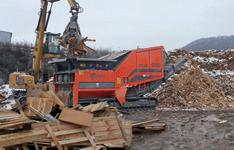
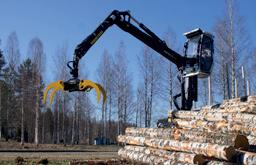
KESLA crane models suitable for bioenergy use, for example for feeding chippers and shredders: 2112T, 2115T, 2117T, 2012T and 1200. The crane range includes Vision XL cabin, proC control system (with either Parker or Olsbergs valve), stabilizer legs beam (width L=4500) and compressor air conditioning.
Kesla timber cranes fit for bioenergy
stress, revealing any weakness in the structure.
A long reach is a feature many wish to have for their bioenergy crane. Kesla cranes offer a maximum reach of up to 12.5 m, with stabilizers ensuring stability. Stabilizers with a width of 3.8 m are typically preferred on forest roads, whereas extra-wide (4.5 m) options can be used for maximum stability at terminals with more space.
Easy serviceability is naturally important both in traditional and bioenergy use to ensure long service life for the crane. Automatic centralized greasing, which carries out the lubrication of the crane, is particularly popular.
Comfortable working in long continuous operations
Ari Pirhonen, Kesla
Political developments show up need for subsistence forestry and facilitating technologies
The need for self-sufficiency in energy production has become more prominent since the start of the war in Ukraine. Wood is an excellent, renewable and carbon-neutral energy source, and residual wood can be chipped for energy. This has seen demand for chippers increase in 2022.
Besides traditional timber handling, Kesla cranes can be used for the efficient feeding of chippers of any make.
Cranes used for feeding chippers must be durable
Chipper feeding includes long continuous operating periods compared to the traditional transport of wood, where the crane is only needed when picking up timber from the site and later at a terminal, for example. It increases the requirements for the durability of cranes in bioenergy use. Kesla cranes are designed with durability in mind.
“Our cranes are mainly made of high-strength steel. Production design has studied the properties of high-strength steel carefully, and the work methods have been selected based on the properties of the material,” says Ari Pirhonen, Business Director of Truck and stationary cranes.
“Welding, of course, is an important work phase, and we have ISO 3834-2 certification as proof of the excellent quality of the welds.”
Surprisingly, the streamlined design of the cranes, especially at the joints, also improves their fatigue durability. All models in the Kesla range have passed a fatigue test before entering the market. The fatigue test exposes the crane to extreme Kesla Vision XL is a slightly more spacious cabin, providing extra comfort in long continuous crane work for larger operators as well. Comfort and ergonomics can be further improved with an optional air seat and armrests.
The temperature can be adjusted as desired by equipping the cabin with heating and air conditioning.
Electric control, which is the preferred choice for chipper feeding, can be had with either mini joysticks or vertical levers. The combination of a control
valve with generous flow capacity and an electric control system adjusted to personal preferences guarantees excellent efficiency and ergonomics.
Good visibility is ensured by the large window area and the positioning of the cabin on either the right or left side of the pillar, as required. Strong polycarbonate windows secure cabin safety. The cabin can be equipped with the Cyclone air cleaner and F9-level fresh air filtering.
“Kesla’s extensive experience with chippers is evident in the design of the cranes,” says Pirhonen.
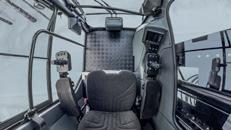
KESLA Vision XL cabin offers comfortable working conditions also when working long hours.
