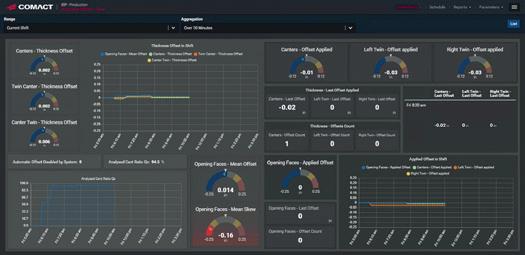
6 minute read
The Primary Breakdown Closed Loop SmartTool, a game-changer!
This cutting-edge technology allows you to break down each log precisely, extracting its full value and maximizing production value. By ensuring optimal recovery, this SmartTool offers significant benefits to sawmills seeking to streamline and optimize their primary breakdown operations.
The Closed Loop SmartTool operates seamlessly, making necessary adjustments automatically in real-time. This relieves the pressure on your team members, freeing them to focus on other crucial tasks. Through the use of data provided by Comact scanners already in place, the SmartTool provides complete information about the log’s shape, guaranteeing unparalleled accuracy.
Advertisement
One notable feature of the Primary Breakdown Closed Loop system is its innovative Multi-offset Adjustment function. This function accelerates the execution of adjustments and corrects offsets swiftly, enabling a more efficient workflow. Moreover, the Pattern Deduction function sets a new standard for closed loop reaction time in defining cutting patterns, providing the fastest response on the market. Additionally, the system automatically corrects offsets to cutting tools and infeed modules. Mechanical breakdowns or problems are instantly identified and displayed on a real-time dashboard, ensuring prompt attention and minimal fiber/ value loss. This comprehensive approach optimizes performance and keeps production running smoothly.
To ensure continuous performance, the Primary Breakdown SmartTool function monitors and makes necessary adjustments, while also monitoring the cleanliness of the scanner. Regular checks of dimension readings further enhance accuracy and performance. By consistently executing optimized cant cutting patterns, each log’s value is maximized.
Installation of the Primary Breakdown Closed Loop system typically requires a short downtime period, usually over a weekend. Once installed, production can resume after calibration, testing, and adjustment of parameter thresholds, alarms, and notifications.
Monitoring the system’s performance and reliability is made easy with real-time dashboards that display primary breakdown operations. Additionally, a comprehensive history of all adjustments performed is available for reference. The technology has been thoroughly tested and improved since its development in 2020, ensuring maturity and reliability. The BID team provides support at every step, offering quick start-up and technical training, backed by the renowned 24/7 service and the reliability program.
Use Case – BID’s Closed Loop SmartTool in Action
More than 10 Closed Loop systems are now up and running in different sawmills across North America and results are witnessed as soon as the “start” button is pressed.
In one particular case, a sawmill had unknowingly been producing off-size boards, in a consistent pattern, for several months. This was caused by cylinders not properly calibrated unable to reach the correct position. Unaware that the output was incorrect and certain that all boards were on target, managers were surprised to conclude the system was right. It was only 15 minutes after turning on the system that the detection occurred, leading to an immediate resolution of the issue.
BID’s Primary Breakdown
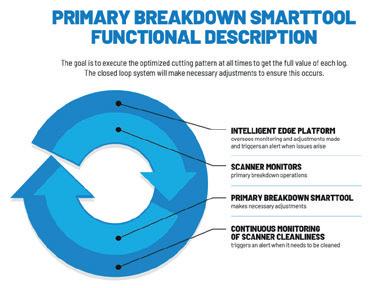
Closed Loop SmartTool offers a holistic view of the production, enabling quick detection of errors in patterns or overall performance. As previously mentioned, alarms can be promptly dispatched, allowing action to be taken rapidly to rectify any issues. Email notifications can also be sent. Let’s talk about numbers
Maximizing material yield is a critical objective for sawmills, as it directly impacts financial performance and sustainability. The process of optimizing material yield involves implementing new technologies to extract the highest value from available resources. Even a small 1% improvement in material yield can result in significant benefits. Studies have shown that in a sawmill with an annual production capacity of 100 MBF, a 1% increase in material yield can translate to cost savings or additional revenue ranging from $250,000 to $300,000 per year. BID’s Closed Loop System enables better control over dimensions and surface adjustments, leading to this outcome. Furthermore, a tighter control of dimensions has been proven to reduce target size by 0.020’’ which equates to a 1% increase in material yield. Additionally, data indicates that optimizing surface adjustments has the potential to save up to 1.6% in yield at a sawmill. By adopting efficient and advanced technologies, sawmills can enhance their profitability, minimize waste, and contribute to a more sustainable operation.
Don’t miss out on the opportunity to maximize your production value. Call now to learn more about the Primary Breakdown Closed Loop system!
450-435-2121 www.bidgroup.ca
MiCROTEC’s sophisticated scanning system significantly increases log yields
Piveteau Bois: The virtual lumber yard
Even though Piveteau Bois still has logs stacked at their log yard, the staff of the large-scale sawmill actually view the woodpiles as a virtual lumber yard already. This approach has changed the entire production process for the French company: Before cutting even starts, they already know exactly which boards they will get out of the logs. This is made possible by means of the CT Log and the one-of-akind fingerprint system provided by MiCROTEC.
The Piveteau Bois sawmill in Sainte-Florence near the French Atlantic coast has several different mainstays. Only a small part of its cutting volume is sold fresh, the rest is dried, planed, glued or otherwise processed. Pine, Douglas fir and spruce wood are used to make wooden floors and facades as well as glulam and CLT elements. In the manufacturing of these products, Piveteau Bois pays particular attention to the optimum utilization of roundwood. “Our sawmill in Sainte-Florence is located in a region with few wood sources. This makes the raw material even more valuable,” R&D Manager Ugo Gerard explains, referring to the unconventional location for a sawmill far from large forest areas
Digital reconstruction
Against this background, the company implemented numerous optimization measures in recent years with the aim of increasing the log yield step by step. The collaboration with MiCROTEC has been particularly close and equally fruitful. In the sawmill alone – from log infeed to lumber sorting – the scanner specialists from South Tyrol implemented three systems that optimally complement each other.
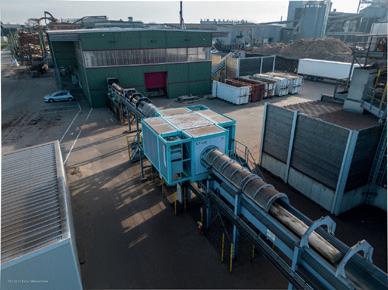
Directly after the log infeed, the long and short logs are brought into the CT Log at feed rates of up to 120 m/min. The computed tomography technology integrated in the machine enables the digital reconstruction of the logs’ complete inner life. Specifically, a comprehensive three-dimensional density profile of each log is created which primarily shows the size, position and condition of knots. Furthermore, the system detects whether there are rotten knots, cracks, resin pockets or spiral grain. “This allows us to precisely predict the quality of the boards and their corresponding location even before cutting, and to adjust the sawing schedule accordingly for each log. Essentially, this means we are no longer accessing the individual logs for cutting but our virtual lumber yard within the logs,” Gerard explains and adds that this has changed the approach to the entire production process. “We now know exactly which logs to use for which products, and what volumes of the various assortments we can produce each year. This not only increases the value of the used wood but also facilitates the logistics for the markets.”
Recognize and rotate
Directly before the sawing line, the logs are passed through the Logeye 302, a multi-sensor quality scanner with fingerprint. Equipped with X-ray technology, multi-sensor cameras and other sensors, the Logeye performs a 3D measurement of the log and again determines its density profile. With the density profiles of the logs – each being as unique as a fingerprint – each log is recognized and rotated according to its optimum value yield before the full traceability from board to log.
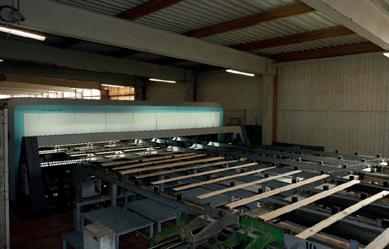
“In the past, when we did not know in advance what we would get out of each log, we had to put some boards to a lower-value use than originally planned. Today, the rate of this unwanted downgrading is effectively zero,” Gerard reports, adding that this has increased the value output of each log by 5%.
A great result, but one that doesn’t lead Piveteau Bois to sit back and relax –quite the opposite, in fact:
The 3D density profile shows the size, position and condition of knots in the log. Cracks, resin pockets and other wood defects are also detected
“To keep getting better, we are continuously working on new projects, and Microtec is a reliable and trusted partner that keeps pushing us forward with new ideas and innovations.” MiCROTEC presented the next evolutionary stage of the fingerprint system at LIGNA 2023 in Hannover. cutting. “We are optimizing the sawing schedule for each individual log,” Gerard emphasizes. In addition to the Microtec scanners, this is made possible with the help of a modernized profiling line from Linck, designed to adjust to every single log which would even allow for a completely unsorted cutting process.
Full traceability of the boards
The third MiCROTEC system is the Goldeneye 900 multisensor quality scanner in transverse transport. It is responsible for quality grading of the fresh boards as well as the definite identification of each lamella. Thus, Piveteau Bois can recognize and allocate each log and each board by means of this digital fingerprint. This results not only in added value, but also