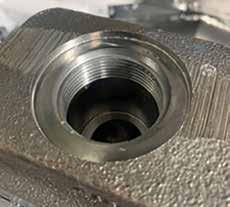
13 minute read
Years Loramendi Germany and New Managing
A machined port. 机加工的端口。
After machining comes assembly and testing, “like breaking an engine in,” says John. 机加工之后是组装和测试,“就像 磨合发动机一样,”约翰说。
Advertisement
tomers. “Through my consultation with the ESPRIT engineers, I’ve learned that these parts are very complex,” says John. “There is no blueprint for this work. I have to reverse engineer each S-cam CAD and CAM to the specs. I never know what kind of order is going to come in or how many will be needed.”
Thanks in part to ESPRIT, John has been able to tackle other challenging projects, too. “We needed to make a hydraulic cap from billet aluminum,” he says. “And we wanted to use one tool for two different operations to complete the project. Although it was one tool, we had to program the software to ‘believe’ that it was two different tools from the same pocket to make the product. [ESPRIT application engineer] Troy Lewis provided input and support, and within two days we had it running.”
John is optimistic about his role in Clutch & Brake Xchange’s future, and he’s excited to have a hand in the shop’s development. “Hydraulic pumps are the future,” he says. “California agriculture runs on fluid power. Recently, we’ve become a Permco West Coast build center. We can port, build, and test in a day. The factory takes six to ten weeks.” Not bad for a classically trained chef!
“I didn’t go to engineering school. I have no machining background, and everything I’ve learned has been with the help of application engineers,” says John. “Thanks to that support and an amazing product, ESPRIT really is the only CAM system you’ll ever need.” ■
For more information about ESPRIT, contact:
ESPRIT CAM, 1150 Avenida Acaso
Camarillo, CA 93012, USA
Tel: +1.805.388.6000, 800.627.8479
Fax: +1.805.388.3085
Email: esprit@dptechnology.com
Website: www.espritcam.com
会收到什么样的订单,或者需要多少 订单。” 部分归功于ESPRIT,约翰也能 够处理其他具有挑战性的项目。他 说:“我们需要用铝坯制作液压 盖,而且我们希望使用一种工具进 行两种不同的操作来完成项目。尽 管它是一种工具,但我们必须对软 件进行编程,以‘相信’它是来自 同一个口袋的两种不同工具来制造产 品。ESPRIT应用工程师Troy Lewis提 供了意见和支持,两天之内我们就让它运行起来。” 约翰对他在Clutch & Brake Xchange的未来中所 扮演的角色持乐观态度,他很高兴能参与该工厂的发 展。“液压泵是未来,”他说,“加州农业依靠流体动 力机械的运行。最近,我们已成为泊姆克西海岸的制造 中心。我们可以在一天内运输、建造和测试。工厂需要 6到10周的时间。” “我没有上工程学院。我没有机械加工背景,我所 学到的一切都是在应用工程师的帮助下完成的,”约翰 说,“多亏了这种支持和出色的产品,ESPRIT 确实是 您唯一需要的 CAM 系统。” ■ 更多信息,请联系我们。 ESPRIT CAM, 1150 Avenida Acaso Camarillo, CA 93012 USA Tel: +1.805.388.6000, 800.627.8479 Fax: +1.805.388.3085
Email: esprit@dptechnology.com
Website: www.espritcam.com

Weijing Degating Hammer Used Worldwide 微晶气冲锤为何值得拥有?

Weijing, established in 2008, is a professional manufacturer of pneumatic hammer which is used to degate iron casting and steel castings.
By end of June 2021, Weijing has delivered 118 sets of degating hammer to foundries worldwide in China, North Korea, Malaysia, India and Finland.
Beginning in 2012, Weijing made the first set pneumatic hammer for the foundry in China, then seven sets in 2013.
Now, 61 sets of Weijing Hammer are used at mining machinery casting makers, 26 sets are used at automotive part foundries, 16 sets are used to degate the engineering machinery castings, six sets to break the honeycomb plate castings, five sets at windmill foundries, and a few sets in some foundries which make other castings. ■
For more details about Weijing Hammer, visit the Weijing website at www.weijingsz.com or email roc.hang@weijingsz.com
微晶,是一家气冲锤专业生产厂家,成立于2008 年。气冲锤,是用来去除铸铁件或铸钢件的冒口。 截止到2021年6月底,微晶已经交付了118台气冲 锤。铸造厂用户覆盖中国、韩国、马来西亚、印度和芬 兰。 始于2012年,微晶为中国铸造厂制作了第一台气冲 锤,2013年制作了7台。感谢第一批选择微晶气冲锤 的客户。现在,微晶有61台气冲锤用在矿机部件铸造 厂,26台用在汽车部件铸造厂,16台用在工程机械部 件铸造厂,6台用在蜂窝盖板铸件厂,5台用在风电部件 铸造厂,及其他铸件厂。 由于微晶气冲锤的质量出色,所以,很多铸造厂多 次选择微晶,而且向朋友铸件厂推荐。 9年,118台成功生产经验,使得微晶非常自信地告 诉全球的铸造人,微晶气冲锤,值得拥有。不仅是因为 出色的品质,更是最高的投资回报比。 你假如有兴趣了解更多微晶气冲锤,请访问微晶官 网或者通过下面方式联系我们。谢谢您的阅读。 ■
网站:www.weijingsz.com 电话:+86 512 6610 2545 手机/微信:+86 153 0612 4775 邮箱:roc.hang@weijingsz.com
Italpresse HPDC TF1850 Exhibited at DIECASTING CHINA 2021 1850吨压铸机惊艳亮相压铸及有色展览会
During METAL CHINA and DIECASTING CHINA, May 26, 2021, Italpresse Gauss diecasting machine with a clamping force of 1,850 tons was unveiled, which once again refreshed the record of physical equipment exhibited at the exhibition.
The TTF two-platen toggle free high pressure diecasting machine is mainly developed for large and complex diecasting parts. It not only incorporates Italpresse’s highperformance injection system, but also uses its leading two-platen design and high-precision hydraulic cylinder drive for mold open and clamping. It provides equipment and solutions for automotive structural parts. The Italpresse Two-platen Die Casting Machine TF1850 is a milestone in Italpresse Gauss’s localization strategy. It is also the first Italpresse equipment manufactured in China. After the successful localization of TF1850, Norican will gradually improve the localized production of Italpresse’s full range of products, and use the Hanjiang factory in Changzhou as the manufacturing and service center of Italpresse Gauss in the Asia-Pacific region, serving local customers. ■ 2021年5月26日,在第十九届中国国际铸造博览 会、第十五届中国国际压铸工业展览会上,意特佩雷斯 高斯旗下锁模力达1850吨压铸机“重磅”亮相,创造 出实体设备展出的最高纪录。 意特TF系列双模板压铸机,主要针对体积较大的 复杂压铸件而开发,不仅融入了意特高性能的压射系 统,更使用了其领先的两模板机构设计,以及高精度液 压油缸驱动开合模,为汽车结构件提供了完美的装备及 解决方案。亮相本届展会的TF1850意特佩雷斯无曲拐 两板压铸机,是意特佩雷斯高斯本地化战略的一个里程 碑,同时也是首台在中国本土制造的意特佩雷斯设备, 继TF1850成功国产化之后,诺瑞肯将逐步完善意特佩 雷斯全系列产品的本土化生产,并以中国常州汉江工厂 为意特佩雷斯高斯在亚太区域的生产制造和服务中心, 更好地服务于本地客户。 ■
Global Foundry Group Grows Business With Sand 3D Printing Innovation 木村铸造集团通过砂型3D打印技术发展业务
With nine decades of experience in sandcasting innovation, Kimura Foundry America places sand binder jetting at the core of its business to deliver top-quality rapid prototypes. 经过9年的砂型铸造创新发展,木村铸造美国公司将 砂型粘结剂喷射作为其业务的核心,以生产出高质量的 快速原型。
挑战
在开始他们的第一次国际扩张时,木村铸造集团寻 求创新解决方案来帮助他们提供高质量的快速原型铸 件。木村铸造美国公司建设了一个完整的工厂,专注于 生产具有快速周转时间的金属铸件,甚至是最复杂的设 计或需要高温浇注。 “我们研究了来自世界各地的3D打印机,并选择了 ExOne打印机,因为其高端技术可提供高质量的打印 产品。”——木村铸造美国公司总裁Yoya Fukuda博 士
解决方案
在日本母公司投资ExOne粘结剂喷射打印设备后的5 年内,收入增长超过5倍,在此基础上,木村铸造美国 公司通过三台3D砂型打印机生产没有传统模具的型芯 和铸型。木村认识到增材制造是下一次工业革命的基 石,围绕ExOne粘结剂喷射工艺,公司在印第安纳州 谢尔比维尔建设了新工厂。“我们的重点关注是质量, 如果我们想保证质量和快速交货,我们需要将设备安
Challenge
When embarking on their first international expansion, the Kimura Foundry Group looked to innovative solutions that help them deliver top-quality rapid casting prototypes. Kimura Foundry America built an entire facility focused on metalcastings with fast turnaround times, even of the most complex designs or for high-temperature pours.
“We researched 3D printers from around the world and chose ExOne printers for their high-end technology that delivered top-quality prints.”
Dr. Yoya Fukuda, President of Kimura Foundry America
Solution
Building on the success of their parent company in Japan that saw revenue increase more than 500% in the five years after investing in ExOne binder jetting, Kimura Foundry America produces core and mold without tradtional patterns or tooling on three sand 3D printers. Recognizing additive manufacturing as the cornerstone of the next industrial revolution, Kimura built their entire greenfield facility in Shelbyville, Indiana around the ExOne binder jetting process. “Our focus is on quality, and if we want to guarantee quality and fast delivery, we need all the facilities in one area,
in one location,“ said Dr. Yoya Fakuda, President of Kimura Foundry America.
HIGHLIGHTS
Embracing the digital metalcasting workflow, Kimura has significantly reduced lead times for customer jobs. Delivering prototypes in less than one week is a gamechanger for metalcasting, opening the door to quicker product development and new freedom of design. By concentrating their sandcasting capabilities under one roof, Kimura can iterate designs quickly based on solidification modeling, casting results, and customer feedback. “It’s easy to communicate with our customers and to give them feedback that supports their needs for unique runner and riser designs or other difficult requirements because we have the engineers in-house,” Dr. Fukuda explained.
ABOUT EXONE
ExOne is the pioneer and global leader in binder jet 3D printing technology. Since 1995, we’ve been on a mission to deliver powerful 3D printers that solve the toughest problems and enable world-changing innovations. Our 3D printing systems quickly transform powder materials – including metals, ceramics, composites, and sand – into precision parts, metalcasting molds and cores, and innovative tooling solutions. Industrial customers use our technology to save time and money, reduce waste, improve their manufacturing flexibility, and deliver designs and products that were once impossible. As home to the world’s leading team of binder jetting experts, ExOne also provides specialized 3D printing services, including on-demand production of mission-critical parts, as well as engineering and design consulting. ■ 装在一个区域、一个地点,”木村铸造美国公司总裁 Yoya Fakuda博士说。
亮点
木村公司拥抱数字化金属铸造工艺流程,从而显著 缩短了交货时间。能够在不到一周的时间内交付原型 是金属铸造领域游戏规则的改革者,为更快的产品开 发和新的设计自由提供了空间。通过集中砂型铸造能 力,木村铸造公司可以根据凝固建模、铸造结果和客 户反馈快速迭代设计。“很容易与我们的客户沟通并 向他们提供反馈,以支持他们对独特的浇道和冒口设 计或其他难题的需求,因为我们有自己的工程师,” 福田博士解释说。
关于EXONE
ExOne是粘结剂喷射3D打印技术的先驱和全球领 导者。自1995年以来,公司一直致力于提供功能强大 的3D打印机,以解决最棘手的问题并实现改变世界的 创新技术。公司的3D打印系统可将粉末材料(包括金 属、陶瓷、复合材料和砂子)快速转化为精密零件、 金属铸造模具和型芯以及创新的工具解决方案。工业 客户使用我们的技术来节省时间和金钱、减少浪费、 提高制造灵活性并交付曾经不可能实现的设计和产 品。作为全球领先的粘合剂喷射专家团队,ExOne还 提供专业的3D打印服务,包括按需生产关键部件以及 工程和设计咨询。 ■
As Early As 2018, Kurtz Ersa Launched The “P01” Project In Order To Derive The Greatest Possible Benefit From Digitization For The Group And To Become Even More Competitive For Its Customers Around The Globe.
In conjunction with the awareness that the Industrial Internet of Things (IIoT) will change all production processes and the entire manufacturing industry in the future–especially those of our customers – we developed a scalable, secure solution: the Kurtz POWerBoard, which was presented very successfully for the first time at GIFA 2019. The visitors were enthusiastic and the reactions were without exception positive.
For further development we then put the Kurtz POWerBoard through its paces under real conditions with our long-standing customer and cooperation partner CSA Herzogenburg GmbH. Our customers can now see the added value of this dynamic 早在2018年,KURTZ ERSA(库尔特埃莎)公司就 启动了P01项目,以便为集团从数字化中获得最大好 处,并使其全球客户更具竞争力。 意识到工业物联网 (IIoT) 将在未来改变所有生产工 艺和整个制造业——尤其是我们客户的行业,公司开发 了一个可扩展的安全解决方案:Kurtz POWerBoard, 并首次在GIFA 2019展会上展示,得到所有参观者的积 极反馈。
为了进一步的开发,我们 随后与我们的长期客户及合 作伙伴CSA Herzogenburg 公司在实际条件下对Kurtz POWerBoard进行了测试。 我们的客户现在可以直接在
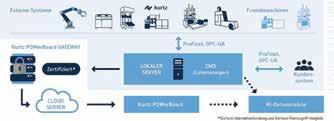
control tool directly on their plants and, for example, their overall equipment effectiveness (OEE) can be permanently and directly viewed on the basis of defined parameters for quality, performance and availability. With the Kurtz POWerBoard, customers now have the opportunity to carry out a detailed, cross-site comparison within the company via a secure and certified cloud solution. On this basis, measures to increase efficiency can be derived, implemented and then the successes determined.
Location-internal system comparison
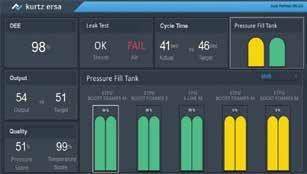

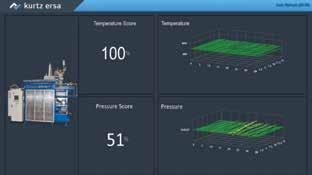
For each user of the Kurtz POWerBoard, a comparison of plants within a production line as well as between different locations is possible, so that foundries of any size can get a clear added value from the Kurtz POWerBoard. In addition to OEE comparisons, digitized downtime tracking, for example, can be used to analyze in real time why a plant has a higher availability than a comparable one. Was there possibly a failure of a cooling system? Did the mould have to be reworked or brought back to temperature first? The Kurtz POWerBoard provides meaningful answers to these and many more questions.
The Kurtz POWerBoard was developed as a tool for all levels of organization. The plant operator, for example, does not have to keep cumbersome paper lists for downtime tracking, but intuitively and quickly selects the downtime reason directly in the machine visualization. In management, it offers the possibility of obtaining an overview of the OEE of individual casting lines, for example, at the click of a mouse. And in the event of a service call, the maintenance department can transmit necessary information such as serial number and message history directly to Kurtz Service via the ticket system at the push of a button and receive immediate support.
With the Kurtz POWerBoard Gateway, an industry 4.0-capable OPC UA server is optionally available, which allows the simple and secure integration of any Kurtz plant as well as third-party machines into the 他们的工厂中看到这种动态控 制工具的附加价值,例如,可 以根据定义的质量、性能和可 用性参数永久和直接查看整体 设备效率(OEE)。借助Kurtz POWerBoard,客户现在有 机会通过安全且经过认证的云 解决方案在公司内部进行详细 的跨站点比较。在此基础上, 可以得出并实施提高效率的措 施,并确保获得成功。
位置-内部系统比较
对于Kurtz POWerBoard 的每个用户,可以对一条生 产线内的工厂以及不同地点 的工厂进行比较,因此,任何 规模的铸造厂都可以从Kurtz POWerBoard获得明显的 附加值。除了设备综合效率 (OEE)比较之外,数字化停 机时间跟踪可用于实时分析为 什么一个工厂具有比同类工 厂更高的可用性。冷却系统是 否可能出现故障?模具是否必 须先返工或恢复温度?Kurtz POWerBoard为这些以及更 多问题提供了答案。 Kurtz POWerBoard被开 发为适用于所有级别的组织。 例如,工厂操作员不必为停机 跟踪保留繁琐的纸质清单, 而是直接在机器可视化中直观、快速地选择停机原因。 在管理方面,通过单击鼠标,可以获得单个铸造生产线 OEE概览。在服务呼叫的情况下,维护部门可以通过按 下工单系统的按钮,将序列号和消息记录等必要信息直 接传输到Kurtz Service平台,并立即获得支持。 使用Kurtz POWerBoard网络平台,可选择支持 工业4.0的OPC UA服务器,它允许将任何Kurtz工厂 以及第三方机器简单安全地集成到客户的本地网络
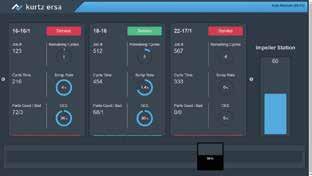
customer´s local network. The development of the Kurtz POWerBoard – like the digitization itself – is far from being finished. Further functions are continuously being developed for all plants listed in the Kurtz portfolio.
Expanding optimization potential with Kurtz Quality Management System
Who would not like to be automatically informed when the same or very similar components are produced in different qualities on the same equipment, regardless of the production location? Where is the optimization potential in the production process? All this can be realized by means of Kurtz POWerBoard in combination with the Kurtz Quality Management System. Industry 4.0 – we are right in the middle of it, are you too? ■ 中。Kurtz POWerBoard的开发就像数字化本身一样, 远未完成。Kurtz产品组合中列出的所有设备的更多功 能正在不断开发中。
使用Kurtz质量管理系统进一步优化潜力
无论生产地点如何,使用同一设备生产出质量相同或 非常相似的组件时,谁不想自动获取通知?优化生产过 程的潜力在哪里?所有这一切都可以通过Kurtz POWerBoard与Kurtz的质量管理体系的结合来实现。我们正 处于工业4.0的时代,您也是吗? ■
Auto Heinen Recommends Latest Dosing Furnace Innovation From Strikowestofen AUTO HEINEN向您推荐来自史杰克西的最新定量炉创新技术
One of Europe’s leading manufacturers of aluminium die-cast components and parts has confirmed it would have “no hesitation in recommending Strikowestofen’s new Westomat Plus+ dosing furnace to other die casting foundries,” based on a product development pilot run in partnership with the furnace solutions specialist.
Auto Heinen GmbH, based in Bad Münstereifel, Germany, has been a StrikoWestofen customer for almost 40 years. The expert in special alloy die-cast parts currently operates 15 Westomat dosing furnaces and 2 StrikoMelter melting furnaces to process around 4 t/hour in peak operation.
Last year StrikoWestofen’s latest innovation, the Westomat Plus+, became a new addition to Auto Heinen’s impressive production set-up as part of a pilot project to experience and feedback on the furnace’s enhanced capabilities in a live customer environment.
The crucible-free Westomat Plus+ holding and dosing furnace has been cleverly designed with a compact footprint that enables foundries to fit a larger holding capacity into a smaller space. In fact, a Westomat 1300 Plus+ easily fits into the footprint of a Westomat 900 Classic. With a smaller bath surface and a large capacity, this means more high-quality melt is available for casting.
Its compact footprint and unique design mean it is ideal for space efficient foundry layouts as the furnace can be positioned 一家欧洲领先的压铸铝合金零件制造商已经确 认,在与熔化炉解决方案专业公司史杰克西合作开展的 产品开发试点的基础上,将“毫不犹豫地将史杰克西公 司新推出的WESTOMAT PLUS+定量炉推荐给其他压铸 企业”。 Auto Heinen公司位于德国巴特明斯特莱费尔, 近40年来一直是史杰克西的客户。Auto Heinen公司 是特殊合金压铸件领域的专家,目前拥有15台史杰克西 Westomat定量炉和2台StrikoMelter熔化炉,在高峰运 行时处理能力约为4吨/小时。 去年,作为试点项目的一部分,史杰克西的创新 产品Westomat Plus+成为Auto Heinen公司令人印象深刻的新设 备,该项目是在现场客户环境中 体验和反馈熔炉增强功能的试点 项目的一部分。 无坩埚Westomat Plus+的 保温和定量炉设计巧妙,占地面 积小,使铸造厂能够在较小的空 间内实现更大的保温产能。事实 上,Westomat 1300 Plus+可轻 松安装在Westomat 900 Classic 的占地面积。有了更小的熔池表 面和大容量,这意味着更多的高 质量熔体可用于铸造。 紧凑的占地面积和独特的设
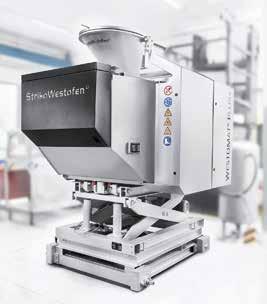
closer to die casting machines without any issue, resulting in shorter cycle times.
Additionally, the furnace’s subframe has been developed to be tilted in any position, allowing cleaning and maintenance to be carried out in a fraction of the time. The furnace’s heating rods are also positioned to ensure that access is only needed from one side in order to replace them.
“We’ve been impressed by the design”, said Dean Wallrath, Director Maintenance HPDC at Auto Heinen, “and not just because it looks so smart. The super flexibility of the subframe coupled with the fact it can be fully enclosed makes cleaning and maintenance easier and safer for our team - that’s a big priority for us. Its distinct oval curves also mean no more tricky corners that can collect deposits.”
Flexibility isn’t the only important benefit for die casters. The Westomat Plus+ consumes less energy thanks to improved design and insulation. This optimized insulation, including high-quality refractory material, is particularly noticeable in the outer wall temperature of the furnace. During the pilot for example, an average wall temperature as low as 55 °C was achieved.
Like all Westomat furnaces, the Plus+ employs a flanged riser tube to take liquid aluminium from below the bath surface to always deliver the right amount of high-quality melt to the casting machine. It also has a dosing accuracy (up to ± 1.5%) in line with the precision performance customers like Auto Heinen have come to expect from StrikoWestofen’s Westomat range.
Dean continued: “To have these trusted benefits but with the added refinements Plus+ offers, is great. As is working with a supplier so keen to have customers involved in product development. Given that our company vision is based on a commitment to ‘continuous improvement and technological development’, piloting new innovations like this is perfect for us.”
Thanks to refinements made possible by working closely with customers such as Auto Heinen, die casting foundries around the world now have access to a unique dosing furnace that convinces with its inner and outer values.
For Dr. Theodoor van der Hoeven, VP Product Development at SWO, the importance of customer involvement in the development of StrikoWestofen’s new dosing furnace solutions cannot be overstated. He commented: “With this furnace, we aimed to offer customers a modern, compact furnace, designed to make die-casting easier, more efficient, cleaner and safer.”
“Having direct customer feedback as part of our development process has been crucial in this mission and we are delighted to now showcase our answer to modern die casting and provide our customers a high-end, premium dosing solution.”
The Westomat Plus+ dosing furnace will be available in Europe in sizes from 1300 to 3100 kg holding capacity. ■
For further information on Westomat Plus+, visit: https://www.strikowestofen.com/ en-us/westomat-plus-dosing-furnace strikowestofen.com/en-us/westomat-plus-dosing-furnace
计意味着这是节省空间的铸造布局的理想选择,因为熔 炉可以毫无疑问地放置在更靠近压铸机的位置,从而缩 短循环时间。 此外,炉子的副框架已开发为可在任何位置倾 斜,从而可以在很短的时间内进行清洁和维护。熔炉的 加热棒的位置也确保只需从一侧进入即可更换。 “我们对这种设计印象深刻,”Auto Heinen公 司压铸业务维护总监Dean Wallrath说,“不仅仅是因 为它看起来很智能,副框架的超级灵活性加上它可以完 全封闭的事实使清洁和维护工作对于我们的团队来说更 容易、更安全——这对我们来说是一个重要的优先事 项。独特的椭圆曲线也意味着不存在难以处理的沉积物 堆积角落。” 灵活性并不是给予压铸企业唯一的好处。由于改 进的设计和绝缘性,Westomat Plus+消耗更少的能 源。这种优化的隔热材料,包括优质耐火材料,在炉子 的外壁温度下优势尤为明显。例如,在试验期间,平均 壁温达到了55℃。 与所有Westomat熔炉一样,Plus+采用法兰提升 管从熔池表面下方抽取液态铝,以始终向铸造设备输送 适量的优质熔体。它还具有计量精度(±1.5%),符合 Auto Heinen公司等客户对史杰克西Westomat系列产 品的期望。 Dean继续说道:“拥有这些值得信赖的好处,加 上Plus+提供的额外改进优势,真是太棒了。与这样热 衷于让客户参与产品开发的供应商合作太棒了。鉴于公 司愿景是基于对‘持续改进和技术发展’的承诺,体验 这样的创新技术对我们来说是完美的。” 得益于与Auto Heinen等客户的密切合作,使改进 成为可能,世界各地的压铸厂现在都可以使用独特的定 量炉,其内外价值都令人信服。 对于SWO产品开发副总裁Theodoor van der Hoeven博士来说,对客户参与史杰克西新型定量炉解决 方案开发的重要性的强调再多都不为过。他评论说:“ 使用这款定量炉,我们的目标是为客户提供一个现代、 紧凑的炉子,从而使压铸生产更容易、更高效、更清洁 和更安全。” “将客户的直接反馈作为我们开发过程的一部分, 对这项任务至关重要,我们很高兴展示我们对现代压铸 的解决方案,并为我们的客户提供高端、优质的定量解 决方案。” ■