
4 minute read
Fritz Winter integrates sprue cleaning and crushing
Fritz Winter integriert Angussreinigung und Zerkleinerung
Fritz Winter North America commissioned a new iron foundry in 2017 in Franklin, KY to serve US automakers in the Midwest and Southeast. Designing a greenfield foundry allowed the company a clean sheet in foundry flow design to maximize efficiency and production. After four years the company started to look at their sprue and gating and what occurred after the casting process. Results from this study uncovered striking inefficiencies that could lead to a great project for the foundry to further enhance production. While a lot of projects aim to increase casting production efficiency, this particular project boosts production significantly through the energy, safety and labor savings.
Advertisement
During the casting process, the mold is shaken out on a high frequency shakeout resulting in castings, gating, and carryover sand traveling to the casting / sorting conveyor. At this point, the castings are then separated from their gating for the initial shotblast process. The gating and carryover sand would convey directly into a roll-off container to be transported to the scrap yard for sand and metal separation by magnet. This led to excessive sand in the melt yard and on the scrap returns. In addition, the sand waste stream had gating that the magnet couldn’t recover which was estimated at 2-3% of good metal being sent out.
Fritz Winter NA decided to contact DIDION International to learn more about the Rotary Sprue Cleaner / Crusher that is designed to separate the sand from the gating, clean the metal, and provide crushing for a dense melt charge. After taking advantage of the free trial offer at DIDION, the test results were astonishing and the benefits to the foundry were clear.
Working together, Fritz Winter NA and DIDION engineered the best approach to integrate the Rotary Sprue Cleaner / Crusher within the foundry layout. The optimal solution was to install the drum at the end of the existing gating sorting conveyor to process the carryover sand and melt returns. A bi-directional vibratory conveyor from Conveyor Dynamics was then chosen at the drum discharge to fill two totes of melt returns with one conveyor.
2017 errichtete Fritz Winter North America eine neue Eisengießerei in Franklin, KY, um Automobilhersteller im Mittleren Westen und Südosten der USA zu beliefern. Die neue Gießerei ermöglicht es dem Unternehmen, die Arbeitsabläufe so zu gestalten, sodass Effizienz und Produktion maximiert werden. Vier Jahre später begann das Unternehmen, seine Angusssysteme sowie alle Vorgänge nach dem Gießvorgang zu untersuchen. Das Ergebnis dieser Studie enthüllte markante Schwachstellen, die jedoch – wenn sie richtig angegangen werden - zu einem großartigen Projekt für die Gießerei werden könnten, um die Produktion weiter zu verbessern. Während viele Projekte darauf abzielen, die Effizienz der Gießereiproduktion zu verbessern, steigert dieses Projekt die Produktion durch Einsparungen bei Energie, Sicherheit und Personal erheblich.
Während des Gießvorgangs wird die Form mit einer hochfrequenten Ausschlagvorrichtung ausgeschüttelt, wodurch Gussteile, Anschnitte und Restsand zum Gieß-/Sortierband gelangen. An diesem Punkt werden die Gussteile von ihren Anschnitten für das erste Strahlverfahren getrennt. Der Anschnitt und der Restsand werden direkt in einen Abrollcontainer geleitet, der sie zum Schrottplatz transportiert, wo Sand und Metall durch einen Magneten getrennt werden. Dies hatte zur Folge, dass zu viel Sand im Schmelzbetrieb und auf dem Schrottplatz landete. Außerdem enthielt der Entsorgungsstrom Anschnitte, die der Magnet nicht entfernen konnte, was schätzungsweise 2 bis 3 Prozent des ausgeschiedenen Altmetalls ausmacht.
Die Fritz Winter NA setzte sich anschließend mit DIDION International in Verbindung, um mehr über den Rotary Sprue Cleaner / Crusher zu erfahren, der den Sand vom Anschnitt trennt, das Metall reinigt und für eine dichte Schmelze zerkleinert. Nach Nutzung eines kostenlosen Testangebots von DIDION waren die Testergebnisse erstaunlich gut und die Vorteile für die Gießerei klar erkennbar.
Gemeinsam erarbeiteten Fritz Winter NA und DIDION den optimalen Ansatz für die Integration des rotierenden Angussreinigers in der Gießerei. Die ideale Lösung besteht darin, die Trommel am Ende des vorhandenen Anschnittsortierbandes zu installieren, um den Mitnahmesand und die Schmelzrückstände zu verarbeiten. Am Trommelauslauf wird ein bidirektionaler Schwingförderer von Conveyor Dynamics eingebaut, um zwei Behälter mit Schmelzrückständen über einen einzigen Förderer zu befüllen.
Immediate improvements as a result of the installation:
• Labor savings reduced the head count by 1 per shift from less slagging.
• Energy savings of 10-minute reduction in melt time due to charge density.
• Metal disposal savings of 3% from metal that was lost in waste stream now recovered.
“Returns used to be the least favorite material to add to the charge mix. Now the melt department picks this first,” said Erik Storrer, Engineering Manager. “We used to have the drive melt team to maintain the inventory balance and avoid the growing pile of returns: they now prefer this material when building the charge recipe.”
Storrer summarizes, “The benefit is for sure worth it. The energy savings will pay for it, but if you are losing material to your waste stream because of a high frequency shakeout system, you will most definitely benefit from a DIDION.” www.didion.com
Sofortige Verbesserungen infolge der Installation: www.didion.com
• Einsparungen bei den Arbeitskräften: Eine Person weniger pro Schicht, da weniger Schlacke anfällt.
• Energieeinsparungen durch eine 10-minütige Verkürzung der Schmelzzeit aufgrund der Ladungsdichte.
• Einsparungen bei der Metallentsorgung von 3 Prozent, da Metall, das im Ausschussstrom verloren geht, wiedergewonnen wird.
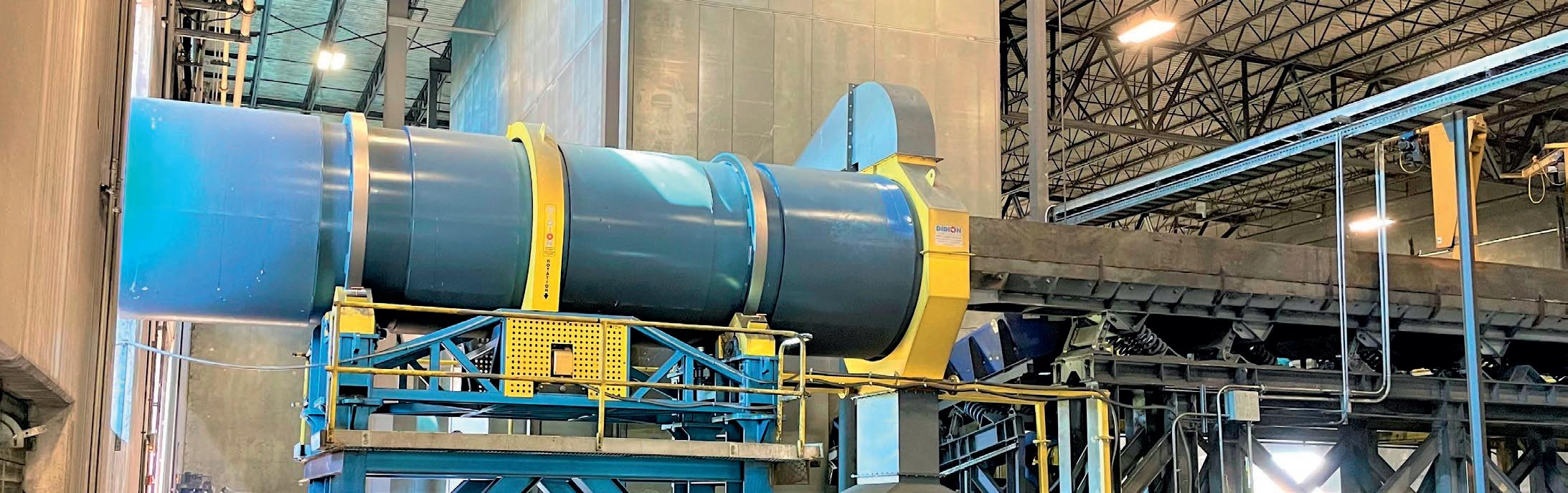
"Rückstände waren in der Vergangenheit das unbeliebteste Material, das dem Gemisch hinzugefügt wurde. Heute wählt die Schmelzabteilung dieses Material vorrangig aus", erzählt Erik Storrer, Engineering Manager. "Früher musste die Schmelzabteilung die Lagerbestände im Gleichgewicht halten und wachsende Rückstände vermeiden: Heute wird dieses Material bei der Rezepturherstellung bevorzugt."

Storrer resümiert: "Es lohnt sich auf jeden Fall, da die Energieeinsparungen sich auszahlen werden. Wenn Sie aufgrund eines hochfrequenten Schüttelsystems Material an den Abfallstrom verlieren, werden Sie ganz sicher von einem DIDION profitieren."