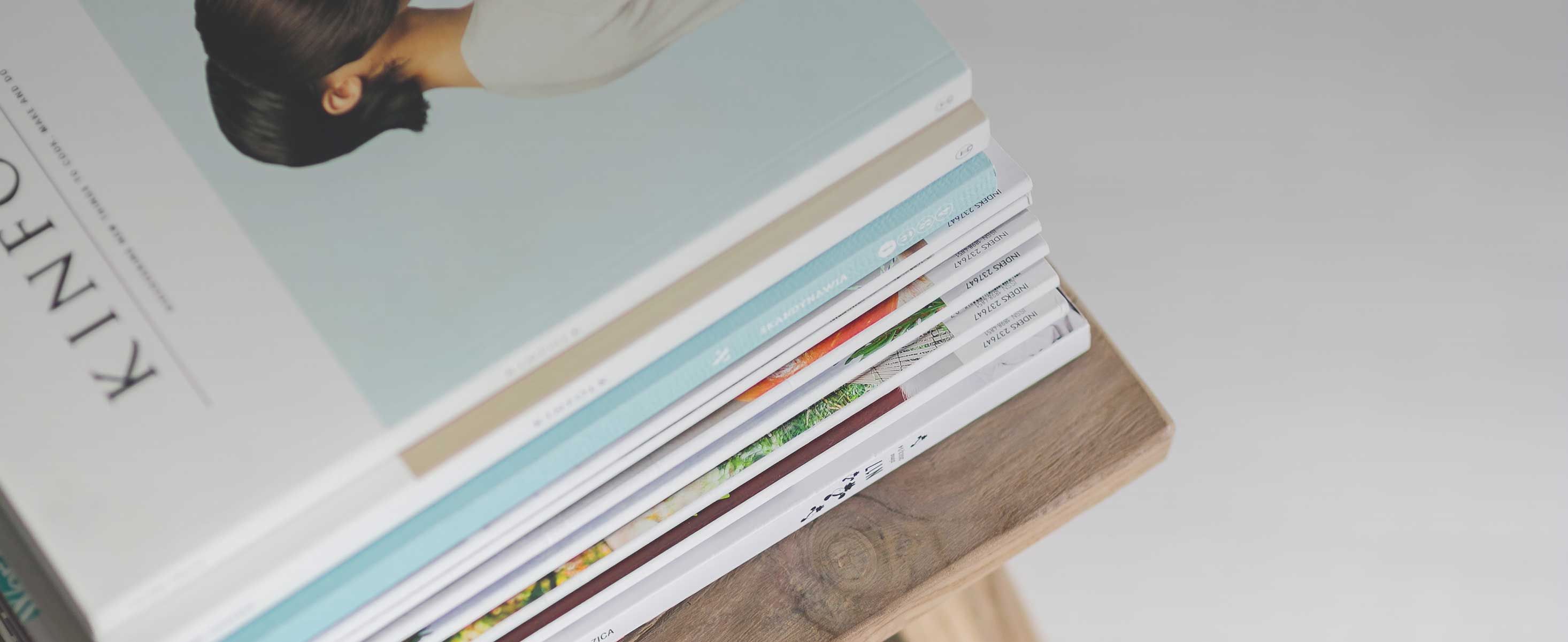
3 minute read
Introduction
Tradi9onal Chinese furniture is made from a variety of hard and soI woods, the most valuable of which are zitan, huanghuali and jichimu, three types of hardwood found on China’s largest island, Hainan and other parts of SE Asia. The furniture market is very material-driven so the price difference between a piece made of one of these woods and a similar piece in a lesser wood can be many thousands of dollars. Genuine huanghuali and zitan have beau9ful, lustrous quali9es. The woods are difficult to harvest and today mostly found outside China, making them even rarer.
Since 2007, the Chinese appe9te for exo9c hardwoods has been rising exponen9ally with dangerous consequences on the supply side. There is con9nued and growing interest in the west for an9que furniture and ar9facts made from wood which can be described with the same exo9c Chinese names. I believe it is 9me to aOempt some unbiased comments related to Chinese exo9c woods in general and these woods in par9cular.
Advertisement
The story begins at least 2,000 years ago in China. Here, we will only men9on that the growth, apprecia9on and use of very slow growing hardwoods in China and surrounding territories has a long history. These trees were considered very special. Nothing like them grew in con9nental Europe or USA. Their outstanding characteris9cs were high density, negligible open capillaries, visual beauty and oIen an appealing fragrance. Figure and color are somewhat secondary characteris9cs to the density which allowed them to take a high polish by careful abrasion alone. ‘Filling’ the grain or covering with paints and varnishes is not necessary. This final polishing is s9ll done in China. It’s a manual process, usually done by women, and making use of horsetail grass (equisetum). It’s laborious and only worth carrying when the quality and rarity of the wood jus9fies it. It is taught in the Imperial workshops and was oIen reserved for wooden furniture des9ned for the Emperor and his family.
The unfortunate truth is that the perfect trees for producing the best results are almost non existent today. It’s not just a maOer of the tree species, it’s also the fact that the tree needed to be undisturbed un9l it had reached a great age. AIer hundreds or thousands of years the tree has reached a great height and girth with the heartwood squeezed to a uniformity such that the cross grain is as smooth as the radial cut. Such trees automa9cally display wonderful figure paOerns when planks are harvested by tangen9al or quarter cuang. This is due to the closeness of the annual rings and a cause for the ‘ghost eyes’ in huanghuali which needn’t rely on the presence of burl growths to account for the effect.
Today, all we can do is aOempt to describe the woods which reached maximum apprecia9on during the Ming period ( 1368- 1644) but which are no longer available in the same quality to cabinet makers and sculptors today. The net has widened in the search for comparably beau9ful woods and that search has had some catastrophic consequences. But just because a tree can be correctly described as e.g. ‘rosewood’ doesn’t mean the wood will present the same quality to the woodworker today as it did to a worker hundreds of years ago. Nowadays, we do the best we can with it including something the Ming craIsmen never did and that is reduce it to the thickness of a veneer to stretch the limited supply. Staining and varnishing are also employed by modern workers in an aOempt to create a similar appearance to that seen on early classic furniture in museums. Not only do those pieces enjoy the incomparable magic that 9me alone has imparted to the the surface but they were created from beOer ingredients in the first place.