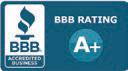
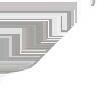






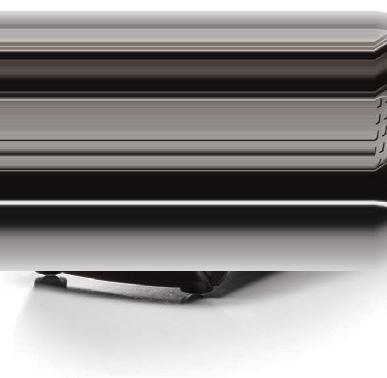
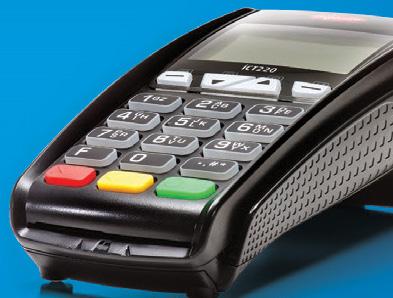



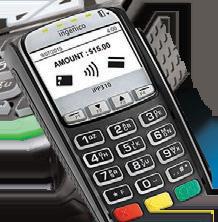
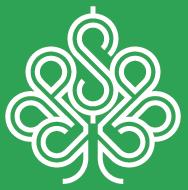


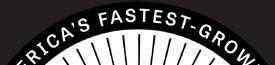
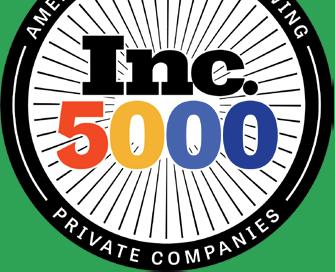
A look at fuel markets in 2023
In the Lead: Fish River Food Mart’s Jigar Patel
HCCI Engines
Advances and trends in an alternative to combustion engines.
Supply
22 Managing Your Fleet: In-House or Outsource? There are advantages and disadvantages with both approaches.
Automated wastewater treatment systems help petroleum terminals and tankers remain in EPA compliance. FUEL
28 Moving Earth, Sustainably Big machines, big power and big ideas dominated the
We once again face challenging times as we move into a new year. Fuel prices are high, and inflation is still high. A deepening global recession looms. Causes include a war in Ukraine, aggressive changes in energy policy both domestically and abroad, lingering supply chain disruption from the pandemic, an OPEC unwilling to increase oil production and U.S. fracking operations similarly unwilling to overproduce as they try to recover from the disastrous pandemic supply glut.
Younger generations likely find our current economic situation a surprising circumstance given their life experiences. Some of us older folks see a potential return to the “stagflation” malaise days of the 1970s. Should that happen, how we handle this as a country will determine just how long the malaise lasts.
Inflation was starting to become a real issue in America as the 1970s began. In a move that White House recordings show was more political than economic in nature, the Nixon Administration responded in 1971 with wage and price controls over a broad swath of the economy. The 1973 OPEC oil embargo added another shock to the economic system, and even when the controls were discontinued for other sectors that year, they continued in the petroleum sector through both the Ford and Carter administrations.
The results were not good for consumers. The price controls caused unexpected disruptions in commodities leading to shortages, and fuel was no exception. There were periods where you had gasoline lines and “even and odd” day sales based on license plate number. Prices stabilized but did not drop. Inflation continued to rise.
The results also were not good for the industry either. Investment naturally
dropped, and production lagged. It eventually became “comfortable” with the system and entered a period of its own stagnation. It faced a rude awakening when the price controls were removed. Many operations, from the refinery down to the station on the corner, had to rediscover how to be competitive and efficient. Many were also ill prepared and found themselves on the wrong side of a consolidating industry.
So far this go-round, there have only been some discussions that lean toward a more direct government control of the economy. Threat of a windfall profits tax in the petroleum sector (another disastrous element of the stagflation era) has so far died down with the end of the U.S. midterm elections. It would be hard to imagine it working any better today than it did in the 1970s when it helped tank industry investment.
We still have a mostly functional, mostly free-market global fueling infrastructure. With enough time, it can be surprisingly resilient to both natural and policy driven disruptions short of those that would be catastrophic in nature. However, there always will be the appeal of feel-good, short-term (and shortsighted) solutions to ease consumer grumblings. Let’s try not to go there again.
Keith Reid Editor-in-Chief (847) 630-4760 kreid@fmnweb.com
Kim Stewart Editorial Director (703) 518-4279 kstewart@convenience.org
Lisa King Managing Editor (703) 518-4281 lking@convenience.org
CONTRIBUTORS
Sal Boutureira, John Eichberger, Bob Ingham, Dr. Vikram Mittal, Clay Moore, Joe O’Brien, Allen Schaeffer, Dr. Raj Shah, Ellen Sowerby, Roy Strasburger, Mike Zahajko, Shi Ying Zheng
DESIGN Imagination www.imaginepub.com
Cover image by RonFullHD/Getty Images
Ted Asprooth (847) 222-3006 tasprooth@convenience.org
PUBLISHING
Stephanie Sikorski Publisher (703) 518-4231 ssikorski@convenience.org
Nancy Pappas Marketing Director (703) 518-4290 npappas@convenience.org
RETAILER/MARKETER MEMBERS
Mark Fitz, president, Star Oilco; Derek Gaskins, chief marketing officer, Yesway; Jeff Reichling, general manager of fuel, Kwik Trip Inc.; Jim Weber, executive vice president of merchandise and marketing, The Spinx Company
VENDOR/SUPPLIER MEMBERS
Regina Balistreri, director of marketing, ADD Systems; Joe O’Brien, vice president of marketing, Source North America Corporation; Kaylie Scoles, marketing director, RDM Industrial Electronics Inc.; Jen Threlkeld, product marketing manager, Dover Fueling Solutions
Fuels Market News Magazine is published quarterly by the National Association of Convenience Stores (NACS), Alexandria, Virginia, USA.
Subscription Requests: circulation@fmnweb.com
Keith Reid is the editor-in-chief of Fuels Market News. He can be reached at kreid@fmnweb.com.
POSTMASTER: Send address changes to Fuels Market News Magazine, 1600 Duke Street, Alexandria, VA, 22314-2792 USA.
Contents © 2023 by the National Association of Convenience Stores. Periodicals postage paid at Alexandria, VA, and additional mailing offices.
1600 Duke Street, Alexandria, VA, 22314-2792
PUBLISHED BY
Modern business presents unlimited opportunities for growth. Let ADD Systems help you realize all those possibilities as we meet today’s challenges of customer experience, speed, accuracy, mobility, and ever more important, scalability.
ADD Systems has been providing solutions to the energy distribution industry –retail and wholesale fuel, propane, convenience stores and more – since 1973.
Fuels Market News welcomes the 2023 Editorial Council, which will provide insights and ideas to the FMN editorial team to help expand the quality of our publications and consider innovative developments for the brand. The council consists of a blend of marketers/retailers and supplier/vendors. Here are the 2023 members:
Mark Fitz, president Star Oilco
Star Oilco is a Portland, Oregonbased petroleum company that was founded in 1936. It is one of the largest distributors of biodiesel to both retail and commercial customers in the Portland area. Every diesel engine in the company’s fleet runs on biodiesel. Star Oilco also provides cardlock fuel services through Pacific Pride, as well as on-site and bulk delivery of motor and heating fuels. With over 40 years of experience in cardlock systems, Star Oilco has been providing fuel cardlock services since before computer-aided cardlock security was even an option. It later pioneered commercial cardlock security via software options. In Oregon and Washington, heating oil is diesel fuel. In these states, the allowance for pollutants in the fuel is more flexible for heating and boiler fuels. Star Oilco is committed to only delivering the cleanest, most advanced fuel possible: ultra-low sulfur diesel.
Derek Gaskins, chief marketing officer, Yesway Yesway, a chain of convenience stores with locations in Iowa, Kansas, Texas, Missouri, Oklahoma,
Wyoming, Nebraska, South Dakota and New Mexico, including the Allsup’s Convenience Stores chain, is known for its world-famous burritos. The Fort Worth, Texas-based company is committed to providing customers with a terrific shopping experience by making their lives easier and the day a bit more pleasant. With its fleet management card program, the customer can control all of the vehicle-related expenses in one convenient and flexible program. The fleet operator decides which purchases to allow and the exceptions reported. The result is a fuel card program that empowers both the fleet operator and the drivers. On the retail side, the Yesway Rewards program rewards its most loyal customers. They can use the Rewards card in stores and at the pump to earn points.
Jeff Reichling, general manager of fuel, Kwik Trip Inc. Kwik Trip was founded by the Hansen and Zietlow families in 1965 when the first store opened in Eau Claire, Wisconsin. In 1993, Kwik Trip became Kwik Star for the sites that operate in Illinois and Iowa. Currently, Kwik Trip | Kwik Star operates over 800 stores in Wisconsin, Minnesota, Iowa and Illinois. In 1997, the company opened its first retail carwash, which is now a core component of the operations. The Zietlow family became the sole owner in 2000. Kwik Trip offers a range of store-branded products including Glasers Donuts, Karuba coffees and Nature’s Touch
branded bottled water, juice and dairy products. As well-known as the company is for its in-store offerings, it has received equal attention for its fuel program. Kwik Trip | Kwik Star goes out of its way to serve both the consumer and commercial customer. It currently offers seven grades of gasoline (including E85 and ethanol free), six grades of diesel and DEF, compressed natural gas, liquefied natural gas, propane and electric vehicle charging.
Jim Weber, executive vice president of merchandise and marketing, The Spinx Company
Stewart Spinks formed Spinx in 1972 with a home heating oil delivery service and one convenience store in Greenville, South Carolina. Today, celebrating its 50 th anniversary, Spinx operates more than 80 convenience stores in South Carolina and employs over 1,400 associates through its stores, food operations and related businesses. Inside the store, the company offers a range of fresh food, beverages and snacks. This includes a variety of fried chicken offerings, a biscuit-centered breakfast program, numerous hot sandwiches, wraps and hot dogs. Spinx has a robust carwash program that includes internal washes and club memberships. With fueling, Spinx offers five grades of gasoline (including E85 and ethanol free), two grades of diesel, kerosene and electric vehicle charging. Fueling
options serve both consumer and fleet operators, as does the carwash operation.
Since 1973, ADD Systems has been a leading provider of back office and mobile software for companies in the commercial bulk fuels, heating oil, propane, HVAC, wholesale petroleum, lubricants distribution and convenience store industries. ADD’s software solutions improve clients’ interactions with their customers and bring efficiency, ease of use and greater profits to their organizations. In addition to its software, ADD offers full-service IT support, including cloud hosting, networking, firewall setup and more, with an overall emphasis on security. ADD’s on-site and remote training is tailored to the specific needs of each individual client. Additionally, ADD clients are welcomed into a strong community of users through its ADD User Group, a self-directed, ADD-supported group of users who assist each other and influence ADD product development. ADD Systems is a family business with family values: be honest, be fair and treat others as you would like to be treated.
Source North America Corporation is one of the largest stocking distributors in the U.S., with 14 facilities that combine to comprise more than 300,000 square feet of warehouse space across the country, anchored by a central warehouse in suburban Chicago. Source specializes in the sale of equipment, parts and materials for the construction and maintenance of gas stations, convenience stores and petroleum and chemical handling facilities. Since its founding in 1979, Source has provided its customers with innovative product solutions that include: POS and fuel management; piping and containment systems; storage tanks and equipment; canopy lighting and submersible pumps.
products, patented to stop a transaction in progress and deactivate a breached fuel dispenser. Retrofit alarm kits are available for new and existing fuel dispensers. The company is also a leading remanufacturer of petroleum electronic equipment. RDM specializes in circuit boards, intercoms, displays, printers, card readers, motors, keypads and overlays, POS systems, consoles, tank monitors and probes with new replacement products available. RDM has five fully stocked locations in Colorado, Florida, Indiana, North Carolina and Texas. RDM employs only degreed technicians and engineers and offers free technical support and training.
Jen Threlkeld, product marketing manager, Dover Fueling Solutions
RDM is a premier U.S. manufacturer of the wired Classic and Performance Series intercoms. RDM also manufactures speakers, call boxes and accessories. RDM additionally manufactures Defender One® pump security
Dover Fueling Solutions, part of Dover Corporation, comprises the product brands of Wayne Fueling Systems, OPW Fuel Management Systems, ClearView, Tokheim, ProGauge and Fairbanks, and delivers advanced fuel dispensing equipment, electronic systems and payment, automatic tank gauging and wetstock management solutions to customers worldwide. Headquartered in Austin, Texas, DFS has a significant manufacturing and technology development presence around the world, including facilities in Brazil, China, India, Italy, Poland, the United Kingdom and the United States.
In November 2022, more than 1,800 merchants from across the U.S. called on lawmakers to pass legislation that would bring long-sought competition to credit card swipe fees that drive up costs for consumers.
“Support for swipe fee competition is quickly building, and this letter from a broad cross section of merchants is proof,” said Doug Kantor, NACS general counsel and Merchants Payments Coalition executive committee member. “Signers range from gas stations and grocery stores to Main Street retailers and local restaurants.”
Both letters cited swipe fees averaging over 2% of the transaction that banks and card networks like Visa and Mastercard charge merchants to process credit card transactions. Credit and debit card swipe fees have more than doubled over the past decade, soaring 25% last year alone to a record $137.8 billion. They are most merchants’ highest operating cost after labor and drove up consumer prices by about $900 a year for the average family last year.
“That number is likely even higher today,” the company letter said, referring to the $900 figure. “Because credit card swipe fees are a percentage of the transaction, they are an inflation multiplier” as prices go up.
Visa and Mastercard, which control more than 80% of the credit card market, centrally set the swipe fees charged by banks that issue cards under their brands rather than the banks competing to offer merchants the best deal. They also restrict processing to their own networks, prohibiting competition from other networks that can offer lower fees and better security.
“This blocking of competition drives up prices for merchants and consumers, harms security and strangles innovation,” the company letter said.
In a letter sent by the Merchants Payments Coalition (MPC) to all members of the House and Senate, merchants asked lawmakers to support the Credit Card Competition Act sponsored by Senators Richard Durbin, D-Ill., and Roger Marshall, R-Kan., and Representatives Peter Welch, D-Vt., and Lance Gooden, R-Texas. NACS is a founding member of the MPC.
“This legislation … will bring much-needed competition into the United States credit card market, which has been dominated by only two players for far too long,” the letter said. “As members of the retail community and champions of the free market, we typically do not support government intervention except in cases where a market is not functioning. That is the case with the credit card marketplace in the United States.”
The letter was signed by 1,802 merchant companies, an increase of 134 over a similar letter sent to lawmakers just months earlier in September 2022. A separate letter sent by 236 state and national trade associations representing merchants emphasized the impact of swipe fees on small businesses.
The legislation would require that credit cards issued by the nation’s largest banks be enabled to be processed over at least two unaffiliated networks—Visa or Mastercard plus a network such as NYCE, Star or Shazam. American Express or Discover could also be the second network, but not networks supported by foreign governments like China’s UnionPay. The banks would decide which two networks to enable on a card and merchants would each then decide which to use when a transaction is made, requiring networks to complete over fees, security and service.
The bill would apply only to financial institutions with at least $100 billion in assets—about 30 of the nation’s largest banks and just one credit union—and would have no impact on community banks or small credit unions.
Convenience store swipe fees were $14 billion in 2021, a 26% increase over the year prior and were about 33% higher than that over the first half of 2022.
NACS is asking its members to contact their members of Congress and ask them to co-sponsor the Credit Card Competition Act, S. 4674 and H.R. 8874, using the NACS Grassroots Portal at www.votervoice.net/NACS/ Campaigns/96609/Respond.
The U.S. transportation sector includes nearly 300 million internal combustion engine (ICE) vehicles, and American consumers were on pace to purchase another 14 million in 2022. Despite the rapid increase in electric vehicle sales, the market will continue to be dominated by ICE vehicles for decades to come. In the pursuit of reducing carbon emissions from the transportation sector, finding solutions for these vehicles must be a priority.
The Fuels Institute report “Future Capabilities of Combustion Engines and Liquid Fuels” presents a highlevel summary of research and development projects focused on improving ICE efficiency and emissions and reducing the carbon intensity of liquid fuels. Understanding the objectives and potential benefits of such initiatives is important to better evaluate the potential emission contributions of the transportation sector.
Despite reports that ICE technology development has ceased and that no additional improvements can be had, this study found thousands of current citations pertaining to research that could yield significant improvements in the performance and environmental footprint of these vehicles.
The report is just a snapshot of what might be possible on the path to decarbonizing transportation. Decisionmakers should seek viable solutions and support further progress in technology and fuel formulations in their effort to achieve a lower carbon future. Download a copy at www.fuelsinstitute.org
2023
FEBRUARY
NACS Leadership Forum
February 08–10 | Eden Roc |
Miami Beach, FL
NACS Convenience Summit Asia
February 28–March 02 |
Waldorf Astoria Bangkok |
Bangkok, Thailand
MARCH
NACS Day on the Hill
March 07–08 |
Washington, D.C.
NACS Human Resources Forum
March 20-22 |The DeSoto | Savannah, GA
APRIL
NACS State of the Industry Summit
April 18-20 | Hyatt Regency
DFW International Airport | Dallas, TX
NACS Leadership for Success
April 30-May 05 | Virginia
Crossings Hotel & Conference Center | Glen Allen (Richmond), VA
With the U.S. government investing $7.5 billion to build out a network of EV charging stations, now is a good time to ask questions about how many chargers we will need, when, where and what type. It is incumbent upon the government and private entities to invest strategically to maximize the utility of the infrastructure that is deployed to best service drivers and to expedite the establishment of a legitimate business case that can sustain market development over the long term. That is why the Fuels Institute Electric Vehicle Council commissioned S&P Global Mobility (formerly IHS Markit) to produce the report “EV Charger Deployment Optimization—An Analysis of U.S. State-level Electric Vehicle Supply Equipment Demand Forecast and Supporting Infrastructure Considerations.”
S&P Global Mobility developed the study in July 2021, and it does not reflect developments over the past year. The rate of development is more conservative than other forecasts being discussed today. However, it is a more realistic forecast than some of the others and serves as a baseline for analyzing demand for chargers. In addition, the methodology of the report can easily be applied to other forecasts.
S&P Global Mobility forecast that by 2030 the U.S. might sell as many as 2.8 million plug-in electric vehicles (battery electric and plug-in hybrid electric). If light-duty sales remain in the range of 16.5 million units per year, this would translate into a market share of about 17%. Meanwhile, the number of plug-in vehicles in operation by 2030 might eclipse 18 million, which would represent a share of 6% of the total projected fleet of about 307 million.
Not all states are developing at the same pace, and this is projected to remain true through 2030. According to S&P Global’s data and forecast, 15 states in July 2021 accounted for 82% of all EVs in operation, and by 2030, 76% of EVs will remain concentrated in just 15 states. This means that charger deployment strategies must be customized to specific market conditions.
Given the insight found in vehicle registrations, S&P Global Mobility then took a census-track analytical approach, leveraging a variety of market-specific attributes and data points, to determine how many chargers
would be needed in each market. By using the international benchmark for the ideal EV-to-charger ratio of 10.4:1. S&P Global analysts determined that the U.S. may require as many as 1.8 million charging stations by 2030— significantly more than the federal government’s goal of 500,000. Yet, based upon mobility assessments and dwell time analysis, researchers project that 90% or more of these stations could be strategically located Level 2 chargers—a discovery that could save billions in capital investment while still effectively serving the needs of drivers.
Rolling the census-track analysis up to the state level, S&P Global Mobility was able to categorize each state into four levels of EV charger demand priority. This prioritization can help direct investments to the markets where the resulting chargers will have the greatest utilization, thereby benefiting drivers as well as those installing and operating the chargers.
To determine the optimal location for charger installation, S&P Global Mobility included within the report three case studies—Detroit, Michigan; Dallas, Texas; and Portland,
Oregon. Each case study looks at EVs in operation, number of chargers, income and housing composition, driver behavior and points of interest with significant dwell time, etc. These examples can help guide a more granular analysis to ensure that charger investments are delivering the greatest value to their markets.
It is easy to talk about future market development and needs using round numbers that are easy to remember, but this expediency does not result in the optimal investment of resources to support the growing market of electric vehicles. It is essential that infrastructure decisions be strategic in nature and based upon real market needs assessments, especially when taxpayer funds are being used.
There is no definitive answer about what the future will be—there are only projections and scenarios of what it might become. The Fuels Institute and the Electric Vehicle Council hopes this evaluation will serve as a valuable resource to help inform investment decisions and to guide charger deployment to deliver value to all stakeholders involved.
Fifteen states in July 2021 accounted for 82% of all EVs in operation, and by 2030, 76% of EVs will remain concentrated in just 15 states.
John Eichberger is executive director of The Fuels Institute. For more information, visit www.fuelsinstitute.org.
Fuel retailers big and small are defining their strategies for serving a new customer base as efforts to establish a national EV charging network accelerate. Companies including Couche-Tard, Phillips 66, Pilot Co. and more have announced plans to expand EV charging within their enterprises. In conjunction with these developments, petroleum equipment suppliers are fielding questions about EV charging. The following Q+A addresses frequently asked questions for fuel sites considering their next EV charging steps.
Q: HOW CAN FUEL SITE OPERATORS GAUGE THE DEMAND FOR EV CHARGING?
A: “EV Charger Deployment Optimization,” a report released by the Fuels Institute in August 2022, estimates that EVs will make up 6% of registered vehicles in the U.S. by 2030. The report states that 1.8 million charging stations will be needed in the U.S. to adequately charge the EV fleet by the end of the
decade. To help planners and investors understand the level of Electric Vehicle Supply Equipment (EVSE) required to support the growth and adoption of EVs, the report ranks which states most urgently need EV charging equipment to support their state’s rate of EV adoption. StreetLight Data is another resource. This provider of mobility insights has created an EV dashboard that shows the gaps in the existing EV charging network.
Q: WHAT ARE SOME OF THE CONSIDERATIONS FOR SELECTING CHARGING STATIONS FOR A RETAIL FUEL SITE?
A: In urban areas, with limited space and generally shorter driving distances, Level 2 charging may make the most sense. Level 2 charging is also a viable option for customers who have a reason to hang around on-site or at a neighboring location for a few hours. Along highways and in suburban and rural locations, where driving distances tend to be longer, Level 3 DC fast chargers (DCFC) can recharge 80% of a battery in 20 to 30 minutes.
In terms of site logistics, proximity to a power supply, existing electrical capacity and parking space size and orientation are among the many considerations when installing EVSE. Power connection occurs in both the public realm—including the public right-of-way—and the private space. This can add layers of complexity to EVSE installations. According to the Fuels Institute report, “regardless of location or charger type, the specific site plan details can actually provide
the biggest impediment toward EVSE deployment, as utilities, landowners, operators and other stakeholders will weigh in on each specific installation.”
Q: WHAT QUALITIES SHOULD FUEL SITE OPERATORS LOOK FOR IN AN EVSE SUPPLIER AND IN THE EQUIPMENT ITSELF?
A: Service and/or solutions providers that provide turnkey project management can be a tremendous asset for EVSE installations. When selecting a supplier, inquire about:
• A market analysis
• A site survey
• Grant money procurement
• Plug-and-play electrical infrastructure
• Charger payment technology options
• Coordination with various stakeholders
• Installation and maintenance
• Monitoring and notification capabilities
Utilities will unquestionably play a role in EVSE development, but they are not the only game in town. In a coordinated effort to promote businesses in the development of EV charging infrastructure, NACS, NATSO, SIGMA, petroleum marketer associations and various companies have joined the Charge Ahead Partnership coalition. Shopping around for service providers may be an opportunity to simultaneously support local business. Learn more about the coalition at www. chargeaheadpartnership.com
Q: WHAT DO FUEL SITE OPERATORS NEED TO KNOW ABOUT EVSE FUNDING AND ROI?
A: With the announcement of the National Electric Vehicle Infrastructure Formula Program (NEVI), the work and proposals for using federal and state funds to build EV alternative fuel corridors is moving forward. Funding opportunities vary widely from state to state and continue to be developed. That notwithstanding, there are
programs with zero out-of-pocket costs available.
AC Level 2 chargers are often advertised in the $5,000 range or lower, and the slower delivery rates usually equate to a less expensive charge for the customer. While the slower rate also provides the site operator an opportunity to maximize other revenue opportunities for the duration of charging, Level 3 DC chargers offer a charging experience that is much more akin to the time customers at retail fueling sites expect to experience. The price range for Level 3 DC fast chargers can vary greatly, ranging from $30,000 to $80,000, and the high-voltage lines needed for DC fast-charging stations are not always easily accessible, which can inflate installation costs. Any investment in DC fast chargers should incorporate obtaining some funding subsidy to produce a return on that investment in a reasonable timeline.
The Fuels Institute report suggests that a “Goldilocks solution” may emerge:
“The 25 to 50 kW DCFCs have a smaller footprint than those 150 and 350 kW chargers, and while they require power transformers, they are still much less expensive to install and operate in the long run. Furthermore, they provide a decent charge time to both mainstream and high-end EVs without costing the end user as much in charge session fees.”
As EV charger funding opportunities begin to take shape, guidelines and standards for installing charging stations will also evolve. And although much is still in flux at these early stages of EVSE expansion, fine-tuning an approach to EV charging absolutely needs to be part of each retail fueling operation’s larger business strategy. Partnering with a total solutions provider that is familiar with all the challenges associated with profitably operating a convenience operation may be a fuel marketer’s leg up to a more stable transition.
In terms of site logistics, proximity to a power supply, existing electrical capacity and parking space size and orientation are among the many considerations when installing EVSE.”
If you weren’t paying attention, you may have missed the fact that one of the great celebrities of the future was born on July 31, 2022. George Jetson, the man who lives in the future with his wife Jane; his daughter, Judy; and his boy, Elroy, came into the world on that day and will be residing in a city in the sky, traveling by jet car within the next 40 years.
“The Jetsons” animated series envisioned a future where technology solves all problems: Robotic
housekeepers take care of your home, children and pets; automated devices dress you in the mornings; you travel by moving sidewalks inside your house and meals are taken in the form of pills.
Many of these things may come to fruition in the next 40 years, but most likely the technology advancements will not be that fast or complete— we haven’t even received the hover boards that we were promised in “Back to the Future II” yet. However,
one thing “The Jetsons” did get right, was predicting the use of video conferencing where poor George is overseen and harassed by his boss, Mr. Spacely, who is constantly checking up on him. Visions of the future always assume that we will use automation to the fullest extent possible—anything that you can think to do, you can make a machine that will do it. There’s no doubt that automated retail ventures such as coffee machines (BaristaBot, for example), salad robots (Spyce) and Mediterranean bowl dispensers (Mezli) exist today. The idea behind these mechanical innovations is to eliminate labor and its associated costs while, at the same time, provide a cost-effective food offer to the consumer 24 hours a day.
However, retail automation, specifically the use of robots, is going to be less extensive than futurists think. Humans by nature want to have some type of social interaction. The automated food purveyors mentioned here are really nothing more than glorified vending machines and, ultimately, that is not enough for the interaction that humans desire.
Technology can play a role in helping retailers lower their operating costs and provide a better customer experience, but it won’t be by using robots. The technology applications that retailers need to look for today are software programs that automate the mundane and repetitive tasks that prevent staff from looking after customers.
Everything from daily paperwork, inventory ordering and checkout can be automated. By doing this you can free up time for staff to stock and clean shelves, brew fresh coffee or interact with customers in order to increase sales.
While automation can help make sure that you have the right inventory in stock, it’s the humans that need to put it on the shelf. Artificial intelligence (AI) can let you know when certain tasks need to be completed in the store, but it will be actual people who do the cleaning or refilling. Automated checkouts can help release a clerk from behind the counter so that they can engage more with the customer, but they will still need to verify the sale of age-restricted products.
The ROI that you receive from automation will depend upon the size of your operation and the number of employees you have. An important
thing to remember is that if you are the store owner, your time is valuable as well. What additional things could you do to increase sales and customer satisfaction if you weren’t spending time doing repetitive tasks?
Areas of automation worthy of further investigation include inventory ordering, labor scheduling, shift duty assignments, HR paperwork, basic employee training, POS price-book accuracy, creating daily and monthly financial statement from POS data, daily shift sales and cash reconciliations, bank deposit calculations, account payables, payroll administration, fuel ordering and permit and license management.
Similar to using robots to save time, outsourcing jobs to part-time contractors can put tasks such as armor-car-delivered bank deposits, cooler stocking, store cleaning, price-book management and store accounting on an automated schedule with the advantage of people handling the more nuanced parts of the task. While you will have to pay for these services, they may cost less in the long run than having someone on your payroll doing the tasks, and it will free up time for more profitable activities.
Every hour of labor you can save per week is either a reduction in your operating cost or should be reinvested in making the store experience better for your customers. Dedicate your and your team’s time to those tasks that add value for the customer and, ultimately, increase your profits.
You may not have Rosie, the robot maid, in the future, but by implementing technology to use time more productively, you may be able to jet your way to more profits.
Roy Strasburger is the CEO of StrasGlobal. For 35 years StrasGlobal has been the choice of global oil brands, distressed assets managers, real-estate lenders and private investors seeking a complete, turnkey retail management solution.
Retail automation, specifically the use of robots, is going to be less extensive than futurists think. Humans by nature want to have some type of social interaction.
Since the first gas station was built in 1905, fuel spills continue to be a common occurrence that causes millions in property damage, injury and deaths each year. Surprisingly, over 100 years later most gas station operators respond to spills with the same technology—ordinary kitty litter.
December 2020 data from the National Fire Protection Association (NFPA) recorded 4,150 fires at gas stations in the United States. These
fires caused 43 injuries, $30 million in direct property damage and three deaths. Unsurprisingly, the item most often first ignited was “flammable or combustible liquids.”
To the untrained eye, most observers would say that spilled gasoline evaporates and goes away by itself. In a study published in the Journal of Contaminant Hydrology by researchers from Johns Hopkins, experiments were conducted to learn just how much gasoline is spilled and where it
goes. The results were surprising. The researchers estimate that 400 gallons of gasoline are spilled at the average gas station each decade.
Markus Hilpert, senior study leader and senior scientist, stated that “gas station owners have worked very hard to prevent gasoline from leaking out of underground storage tanks, but our research shows we should also be paying attention to the small spills that routinely occur when you refill your vehicle’s tank.”
Why is kitty litter or a similar OIL DRI absorbent used? It is cheap, readily available and absorbs spilled petroleum products. Is using kitty litter to treat a gasoline really an inexpensive option? The full cost of responding to a fuel spill must include the absorbent cost, labor and disposal.
• Absorbent Cost: Kitty litter is inexpensive, ranging from 40 cents to 60 cents per pound.
• Labor Cost: Treating a spill with kitty litter takes 20-30 minutes of labor, with another 20 minutes waiting to absorb. Assuming $15 per hour of employee cost, that adds $7.50 to the clean-up cost (more than 10 times the cost of the kitty litter). The time study included the time to cone-off the spill, spread the kitty litter, sweep up and bag the contaminated kitty litter and then dispose it into the hazmat barrel.
• Disposal Cost: Containing and disposing of hazardous waste is expensive, typically ranging from $500-$1,000 for a drum. In some jurisdictions the “waste generator” owns the waste forever.
Retail fueling sites are regulated by multiple environmental programs that vary by state. Typical hazardous wastes generated include waste fuel, clean-up absorbents (like kitty litter), spent filters and catchment basin waste. Out of the 150 different chemicals that make up gasoline, the four most identified as toxic to humans are benzene, toluene, ethyl benzene and xylene.
Benzene content in gasoline is federally regulated. The current national benzene content in gasoline is about 1% as measured by volume. The reason for this strict regulation is that one gallon of gasoline can contaminate up to a million gallons of water, making it undrinkable.
In my 20-year experience, most gas stations do not have the necessary hazardous safety protocols required by state and federal regulations to handle hazardous waste. The absorbents used to respond to fuel spills are swept up and disposed of with all the rest of the trash. While not ideal, store personnel and leaders typically respond that they “double bag” the
hazardous waste before putting it with the other trash. My favorite response when asking what site operators and leaders do with the waste over the years is: “The OIL DRI fairies come and take it.”
While warnings and fines are given by enforcement agencies to prevent the incorrect disposal of hazardous waste, the immediate risk comes from flammability. As the kitty litter absorbs the fuel spill, that kitty litter continues to be flammable for a long time. The “double bagged” waste builds up volatile organic compounds, creating a fire hazard. Of the more than 5,000 retail fueling site fires reported in the United States according to the NFPA, more than 1 in 10 is caused by outside trash fires.
For site employees cleaning up the spill, flammability is a serious safety concern. During the process the kitty litter continues to be highly flammable, endangering the responder and customers in the spill area.
Despite being the most common solution for over 100 years, utilizing kitty litter on spills is expensive, labor intensive, unsafe and fails to correctly treat gasoline left behind in the concrete. Fortunately, new fire suppression technologies are available and are successful in addressing operational, safety and cost-related issues at gas stations around the globe.
The new technology uses microemulsion to suppress vapors to remove fuel flammability in less than three minutes. Additionally, active hydrocarbon-eating microbes can be used to bioremediate and break down remaining hydrocarbons in the surface over time. Bioremediation is an EPA-recommended process for using microbes to break down hazardous chemicals and contaminants.
The full cost of responding to a fuel spill must include the absorbent cost, labor and disposal.
Mike Zahajko is an industry speaker and the executive vice president for CAF, a leader in outdoor cleaning. Learn more about alternative spill solutions at www.mycaf.com/reactfuel-spill-neutralizer.html
Gone are the days where the only way to measure the fuel level in an underground storage tank (UST) was to insert a long stick into it, “read” the height of the fuel and then consult a tank-strapping chart to extrapolate how much more fuel the UST can accommodate or how long it may be until the fuel runs out. Thankfully, there’s been some noteworthy mechanical and digital advancements in automated tank gauging and fuel monitoring since the days of tank sticking.
But the data these next-level systems can gather and monitor is still
disjointed and largely reactive, with each monitoring component its own little ecosystem with no universal connectivity. The next evolutionary step of site monitoring is a system that not only can pull information from an ATG but also collate, centralize and interpret that data on a minute-by-minute basis and intuitively recognize points of failure before an actual failure occurs.
These systems would also parse this breadth of operational data across compliance, alarms, wetstock and fuel inventory, and then proactively suggest ways they could be used to, for instance, identify the best day or time
to order more fuel, improve nozzle flow before customers complain or be alerted to a fuel system component that may be close to breaking down or becoming out of compliance.
At a typical forecourt fueling site, there are three significant pressure points—fuel inventory, compliance and maintenance—that must be monitored constantly. Any slippage in performance in these areas will put the site at risk of incurring excessive downtime, operational disruptions, out-of-compliance fines or even, in the worst-case scenario, a complete site shutdown.
A forecourt that consistently runs out of fuel won’t be in business for very long. Given ever-changing demand and supply conditions, site operators need to have complete visibility into the fuel level in every UST at all times of the day. Often, however, fuel retailers are at the mercy of their carriers, who
Image Caption Goes Herewill schedule deliveries that will make them profitable, not necessarily the site owner. Which is why “stuffing the tank” or runouts are not uncommon.
Another piece of the inventory puzzle is fuel reconciliation. When a delivery occurs, the operator must be confident that the amount of fuel in the UST is the amount that was ordered since everyone wants to get what they pay for. Traditionally, the only way to confirm the delivery amount was trusting a potential erroneous ATG reading and matching it against the BOL or allowing a threshold of variance per delivery.
Staying in compliance is both a necessity and a headache for retail fueling sites. Storing and tracking testing, permits, certifications and inspection information and staying up to date on any changes in requirements is time-consuming, and there are dire consequences if a fueling site falls out of compliance.
To stay in compliance, site operators must identify the cause and effect when an out-of-compliance condition occurs. To do this, they must have an almost supernatural ability to find an issue before it becomes a problem. For example, when frequent outages occur, it often causes air to get into the fuel supply lines, which in effect will put the system out of compliance and create other maintenance costs.
Industry-wide labor shortages continue to plague fuel retailers. So when a line-leak alarm sounds, how can the site operator know when, or even if, a service tech is available to come out and inspect it?
Additionally, by their nature, maintenance routines can be inefficient. After a call is made to the service provider to schedule a site visit, the technician must travel to the location, troubleshoot the situation and identify the best way to fix the problem, which can be challenging if the root cause is unknown.
The most efficient and profitable retail fueling sites are those that create a symbiotic relationship between the fuel inventory, compliance and maintenance areas of their operations. This is only possible if these three departments have the right data and tools to proactively determine an issue long before it affects the customer.
The next evolution of fuel management solutions can collect, centralize and analyze fuel-site data via a single access point, putting actionable operational insights at the user’s fingertips. Utilizing artificial intelligence and advanced data analytics, these solutions enable operators to gain a full picture of real-time events and fuel losses that pose an efficiency, business or compliance risk, with notifications and workflows to manage each issue to resolution.
Instead of logging into multiple systems, the latest software solutions enable fuel managers to manage by exception on a single platform, remotely diagnose key issues and automate traditionally repetitive tasks such as relying on site staff to enter daily variance totals on a spreadsheet, calling sites for inventory levels to order fuel, or running manual weekly reports to review ATG alarms.
Easy to connect and deploy, these tools perform two previously unattainable tasks when it comes to optimized fuel-site management: 1.) They give users access to all key points of fuel inventory, compliance, alarm and wetstock data on one platform. 2.) They take advantage of next-generation AI algorithms and machine learning to compile and analyze historical operational trends to create a proactive system and workflows that alert site operators to an issue before it becomes a costly problem.
So, while technology will continue to evolve, today’s smart fuel retailers are shifting from a reactive to proactive mindset, armed with the tools to run a more efficient, compliant and profitable fueling operation.
Clay Moore is senior director of product for Leighton O’Brien and can be reached at claymoore@ leightonobrien.com. Leighton O’Brien is a leading global fuel-analytics technology provider that enables retail fuel networks to reduce environmental risk, prolong asset lifespan and optimize capital spend. For more information visit www. leightonobrien.com.
The most efficient and profitable retail fueling sites are those that create a symbiotic relationship between the fuel inventory, compliance and maintenance areas of their operations.
Supply chain issues show the benefits of versatile filters.
BY BOB INGHAMThe year 2022 was full of surprises and, for the fueling industry, not least among those was how supply chain issues would transform what previously seemed like an everyday replacement part into a highly coveted piece of equipment. There were several times when fuel dispenser filters were hard to come by, with demand outpacing the supply that was readily available. Fuel-site operators took dispensers out of service. Regulators temporarily excused overdue filter changes. Fueling customers were greeted by out-oforder pumps.
Fuel dispensers require more maintenance than most other equipment on the premises. The supply chain challenges illuminated the benefit of stocking versatile filters
that support numerous dispenser filtration applications.
Here are some important reasons to stock an inventory of fuel dispenser filters with wide-ranging capabilities.
1. FUEL DISPENSER FILTRATION IS NOT A VALUE-ADD; IT’S A NECESSITY. Many states have minimum requirements for fuel dispenser filtration and fuel quality. Nevertheless, all too often, fuel-site operators underestimate the role of fuel dispenser filters in a fueling system. This is not particularly wise because fuel dispenser filters perform an important job.
Contaminants can be introduced to fuel at any point during the supply and distribution process. By the time a consumer pumps fuel from the dispenser, it may have been contaminated three
or four separate times. Fuel dispenser filters are the last chance to capture harmful particles and prevent them from being pumped into a vehicle and damaging it.
2. FUEL DISPENSER FILTERS ARE NOT SIMPLE PIECES OF EQUIPMENT. Fuel dispenser filters may look simple, but they are actually highly engineered components that must reliably provide filtration and contaminant-sensing capabilities for today’s fueling systems.
For example, water-sensing and phase-separation-detecting filters contain special materials that cause a chemical reaction inside the filters in the presence of certain contaminants. This reaction triggers the filter to swell to help prevent passing the contaminated fuel into the vehicle. The slow flow is also a signal to fuel-site operators that a serious problem in the tank needs to be addressed.
Although not regulated by the U.S. Environmental Protection Agency, fuel dispenser filters still need to be constructed in a leak-proof manner. Cover backplate assemblies should be
formed of thick steel for strength and roll-seamed to the shell to prevent leaks. Additionally, the filter materials—including gaskets—need to be compatible with the fuel passing through the filter and be able to withstand the dispenser’s flow rate.
Fuel dispenser filters that are UL-recognized must meet UL’s standards of component service. PetroClear filters, for example, are recognized as safe to use with E0 to E85 (neat gasoline to ethanol blends containing up to 85% ethanol) and for B0 to B100 (standard petroleum-based diesel to pure biodiesel).
3. FUEL DISPENSER FILTERS DO IMPACT CUSTOMER LOYALTY. While advancements in dispenser engineering and monitoring capabilities promise to help make dispenser maintenance more predictive, it is impossible to avoid dispenser downtime altogether. But it is important for fuel retailers to minimize downtime to provide customers a positive experience at the pump. Fuel dispenser filtration plays a large role in that.
Downtime is exacerbated when filter supplies are in high demand or supply chain issues create delays. A limited pool of service technicians can further extend downtime. A dispenser awaiting replacement filters that would have normally been offline for just a few days could be out of service indefinitely. That pump isn’t generating revenue, nor is it enticing customers to go inside and purchase higher-margin items. Having a surplus supply of filters in inventory can minimize such headaches.
4. THE CHOICES FUEL-SITE OPERATORS MAKE WHEN SELECTING FUEL DISPENSER FILTERS CAN HELP OPTIMIZE DISPENSER MAINTENANCE.
On top of needing safe and reliable equipment, fuel sites are usually combatting multiple fuel quality
issues at any given location, on any given day.
Certain fuels are more susceptible to certain types of fuel quality problems than other fuels. And conditions inside an underground storage tank can vary from one tank to another. As a result, having filters on hand that cover the gamut of capabilities to address the scope of possible fuel quality problems is important for keeping the forecourt running smoothly.
To deliver expanded capabilities and provide flexibility with future dispenser maintenance, the filters should be able to:
• Capture particulate;
• Detect dangerous levels of water and help prevent the water from being dispensed into vehicles;
• Detect phase separation and help prevent ethanol blends that have separated into distinct layers from being dispensed into vehicles.
The size of the filter also makes a difference. Standard fuel dispenser filters measure around 5 inches tall. “Extended life” filters range from around 7 inches tall to 10.5 inches tall, with the latter providing twice the filtration media, which allows the filter to capture more contaminants than a smaller filter before requiring a filter change. The 10.5-inch-tall filters have the potential to decrease filter maintenance by nearly 50% in a properly maintained fueling system that experiences relatively consistent throughput.
Value is perceived differently by everyone, including fuel-site operators and their customers. But with most customer experiences starting at the pump, and so much riding on the dispenser to drive sales inside the convenience store, doing whatever is necessary to keep pumps running seems to make sense. Investing in fuel dispenser filters with a wide range of capabilities may be the answer.
Bob Ingham is the business development manager for PetroClear, a manufacturer of fuel-dispensing filters. He has more than 25 years of experience in filtration and automotive component development. Contact him at robert.ingham@ champlabs.com
Fuel dispenser filters are the last chance to capture harmful particles and prevent them from being pumped into a vehicle and damaging it.
Fleets can be managed either in-house or through outsourcing, which appears to be increasing. Here is a look at the benefits and drawbacks of each approach so busy fleet operators can determine which is the best option for their business.
Choosing an approach to fleet management depends on the type of business, the number of vehicles and assets within the fleet, and most importantly, the available skills and workforce within the business.
A fleet manager’s responsibilities can seem overwhelming. Here are just a few things to consider:
• Vehicle sourcing and purchasing
• Maintenance
• Driver requirements such as license checking
• Purchasing and disposal
• Vehicle funding
• Procurement management
• Fleet administration
• Parking and fines administration
• Driver support and training
• Health and safety compliance
• Vehicle tracking and communications
• Vehicle breakdown and recovery
Although managing this workload doesn’t tend to be a problem for larger fleets with tasks carried out across a team, for smaller fleets this could mean some, if not all, of these tasks can’t be done.
Managing and monitoring costs: You and your team know your business better than any external agency–no matter how good the supplier. Familiarity with the vehicles, drivers and resources can help identify areas of concern before they manifest into bigger problems. That can lead to smarter ways of working with the rest of the business that could save money or improve operational efficiency. You can build individual relationships with suppliers and other specialists to deliver on service-level agreements and negotiate rates to save on both fleet costs and additional unplanned vehicle downtime costs just as an outsourced supplier would.
The big picture: Outsourcing can be great for nailing down specific improvements, especially in certain specialist
areas. But, does the outsourced partner have the big picture in mind? Fully understanding your business’s wider plans and goals is key, and an in-house operation will get this. Sometimes, there might be an improvement that could be made to the fleet operation, which has an impact elsewhere on the business. Only an in-house team might be able to see that. That’s because an external service provider won’t have full access to your sensitive business information.
So, while you might be prepared to negotiate for additional budget funding by demonstrating the longer term cost-benefit analysis, an agency will tend to favor achieving only the targets and objectives as pre-agreed in the contract.
Access to new ideas: Bringing an outsourcer in could be the fresh air your business needs. These specialists spend time working with many different companies’ fleet departments, and as a result bring new best-practice concepts and ideas for your fleet processes.
Ability to focus: Is your business focusing on the wrong thing? Outsourcing fleet management could allow you to concentrate on the things that really drive the business forward. It may be easier to outsource the management of vehicles to a specialist organization to remove management strains and manage associated fleet risk.
Reducing risk: Do you find
managing compliance and industry standards a nightmare? There’s ever-changing legislation to keep up with, too, and depending on the size of the operation, this may be less of a problem for larger fleet departments; however, for smaller ones, the risks can be just too great.
Outsourcing can help alleviate some of this worry. Processes and procedures will already be in place to minimize failure to comply, with tools such as fleet management systems creating auditable trails.
It’s worth noting though, that the overall accountability will still rest with you.
Access to resource and knowledge: Outsourcing often means access to a plethora of specialist systems, tools and knowledge that had previously been unavailable. The systems and tools will in turn allow you access to market intelligence, giving you the ability to benchmark your performance.
The costs: Running a fleet in-house comes with a capital cost. You’ll need to spend on providing the suitable facilities and equipment, and that can be a challenge for larger fleets, let alone smaller ones.
As an example, maintenance tasks carried out in-house will require workshops, equipment and trained staff—all of which can be expensive. These costs need to be compared to outsourced work.
Finding staff: Sourcing high-caliber, trained staff can prove troublesome. Can you find enough of the right people to run your operation?
Access to specialist technology: Do you have the tools and systems in place to manage the department efficiently and to improve your operation?
Some fleets rely on outdated practices such as managing and reporting
through spreadsheets and systems with limited integrations and may overlook costly issues.
Contract management: Once costs have been drawn up as per the contract, the potential to find future spending savings could be limited. That’s because these costs tend to be tied into the contract for the agreed period before they can be reviewed and amended. There are often penalty clauses for such amendments before the end of the contract.
In difficult times, when businesses examine where they can make cutbacks, a reduction to fleet operations may not be possible due to contractual obligations.
There’s nothing worse than needing to let go of the workforce and vehicles through redundancy but still paying for a contracted service that is no longer required or only required in part. Similarly, fleets lose bargaining power in areas such as purchasing vehicle parts. Suppliers and prices will remain as set in the contract, which could prove costly in the longer run.
Slower to move: Discussions with your fleet management organization will need to go through the proper channels, which can reduce efficiency itself. That’s because the correct policies and procedures need to be taken to initiate any changes or areas of concern, which can delay operations. This might make you less agile.
How to decide between in-house or outsourcing fleet management? For smaller fleets that want to retain in-house management, there are options available to help, such as fleet management software. Outsourcing part rather than all of an operation is another option. Read more at fuelsmarketnews.com.
Is your business focusing on the wrong thing? Outsourcing fleet management could allow you to concentrate on the things that really drive the business forward.
Terminals which store oil, petroleum and petrochemicals and even the tankers that transport product must meet U.S. Environmental Protection Agency (EPA) and local wastewater requirements for effluent, including those under the Clean Water Act. The EPA
has identified 65 pollutants and classes of pollutants as “toxic pollutants,” of which 126 specific substances have been designated “priority” toxic pollutants. Failing to meet EPA requirements can result in fines that quickly escalate.
Petroleum can enter the wastewater stream at fuel storage depots as well
as rail, barge and road tanker transport hubs. Often the wastewater is discharged into local sewer or trade waste systems and must meet local environmental specifications. Typical contaminants can include solvents, detergents, grit, lubricants and hydrocarbons.
For petroleum terminals and tanker hubs, this means installing a wastewater treatment system that effectively separates the contaminants from the water so it can be legally discharged into sewer systems or even re-used. However, traditional wastewater treatment systems can be complex, often requiring multiple steps, a variety of chemicals and a considerable amount of labor. Even when the process is supposedly automated, too often technicians must still monitor the
Automated wastewater treatment systems help petroleum terminals and tankers remain in EPA compliance.
equipment in person. This usually requires oversight of mixing and separation, adding of chemicals and other tasks required to keep the process moving. Even then, the water produced can still fall below mandated requirements.
Although paying to have petroleum terminal and tanker wastewater hauled away is also an option, it is extraordinarily expensive. In contrast, it is much more cost effective to treat the industrial wastewater at its source, so treated effluent can go into a sewer, and treated sludge passes a TCLP (toxicity characteristics leaching procedure) test and can be disposed of as nonhazardous waste in a local landfill.
Fortunately, complying with EPA and local wastewater regulation has become much easier with more fully automated wastewater treatment systems. Such systems not only reliably meet regulatory wastewater requirements but also significantly reduce the cost of treatment, labor and disposal when the proper separating agents are also used.
In contrast to labor-intensive multiple-step processes, automated wastewater treatment can help to streamline production, usually with a one-step process, while lowering costs at industrial facilities.
An automated wastewater treatment system can eliminate the need to monitor equipment in person while complying with EPA and locally mandated requirements. Such automated systems separate suspended solids, emulsified oil and heavy metals, and encapsulate the contaminants, producing an easily dewaterable sludge in minutes, according to petrochemical industry consultants at Sabo Industrial Corp.
The water is typically then separated using a dewatering table or bag filters before it is discharged into sewer systems or further filtered for reuse as process water. Other options for dewatering include using a filter press or rotary drum vacuum. The resulting solids are non-leachable and are considered non-hazardous and will pass all required testing.
These systems are available as manual, semiautomatic and automatic batch processors and can be designed as a closed loop system for water reuse or provide a legally dischargeable effluent suitable for the sewer system. A new, fully customized system is not always required. In many cases, it can be faster and more cost effective to add to or modify an industrial facility’s current wastewater treatment systems when this is feasible.
However, because every wastewater stream is unique to its industry and application, each wastewater treatment solution must be suited to or specifically tailored to the application.
The first step in evaluating the potential cost savings and effectiveness of a new system is to sample the wastewater to determine its chemical makeup followed by a full review of local water authority requirements.
The volume of wastewater that will be treated is also analyzed to determine if a batch unit or flow-through system is required. Other considerations include the size restrictions, so the system fits within the facility’s available footprint.
Despite all the advances in automating wastewater treatment equipment, any such system requires effective separating agents which agglomerate with the solids in the wastewater so the solids can be safely and effectively separated.
An automated wastewater treatment system can eliminate the need to monitor equipment in person while complying with EPA and locally mandated requirements.
Sal Boutureira is owner of SABO Industrial Corporation, which has been in the wastewater treatment industry since 1992 and has introduced wastewater treatment solutions to companies in the United States and Europe, translating into millions of gallons of wastewater that are now within compliance for discharge or reuse. Learn more at www.saboindustrial.com or email info@saboindustrial.co m.
Bentonite has a large specific surface area with a net negative charge that makes it a particularly effective adsorbent and ion exchange for wastewater treatment applications to remove heavy metals, organic pollutants, nutrients, etc. In contrast, polymer-based products do not encapsulate the toxins, so systems that use that type of separating agent are more prone to having waste products leach back out over time or upon further agitation.
Today’s automated systems along with the most effective separating agents can provide oil terminal and tanker hub operators with an easy, cost-effective alternative so they remain compliant with local ordinances and the EPA. Although there is a cost to these systems, they do not require much attention and can easily be more economical than paying fines or hauling.
The world trade fair for the off-road mining and construction sectors known as bauma took place October 24-28, 2022, in Munich, Germany. On display were the most massive examples of the heavy equipment that powers global energy and transportation, resource mining and construction sectors.
While big machines dominated the floor at the expo hall, it was the big ideas about a reduced-carbon future, sustainability and productivity that drove the conversation at the 33rd gathering of the world’s largest construction trade show.
Customers in these sectors have specialized needs and demands for
their business and equipment that operates in every corner of the globe in demanding conditions, often 24 hours a day. These needs include being successful in a sustainable and reduced-carbon future. Manufacturers at the trade fair showed they are responding to these needs.
AGCO Power debuted a new family of diesel engines called CORE. “Alternative fuels of the future such as hydrogen, ethanol, methanol, biogas as well as electric hybrid applications set new demands for an engine,” AGCO Power noted. “The CORE engine platform is designed to enable the use of alternative fuels with further development.”
Caterpillar’s commitment to a reduced-carbon future was on display, highlighting a diversity of solutions
Big machines, big power and big ideas dominated the 2022 bauma world trade fair.
and options available covering both new products and strategies for reducing carbon intensity in existing products. Cat’s advanced power solutions approach is all about providing options. New fuels and technology like electric battery packs and hydrogen fuel cells, along with gaseous fueled (natural gas, hydrogen) and diesel engines that are capable of using low-carbon intensity fuels provide an array of customer choice. From the largest machines to the smallest all-electric compact excavators, there are solutions for every application.
FPT Industrial showed off new Stage V emissions-level engines, compact hybrid solutions and new battery pack technology.
John Deere focused on its next generation engine range designed to run on renewable fuels. Current engines are compatible with renewable fuels, ethanol, biodiesel and biofuels such as hydrogenated vegetable oil (HVO). Deere also showcased a diesel-electric powertrain and its latest developments in batteries and electric motors. Taking efficiency beyond the engine, Deere also demonstrated how automation technology in motor graders can boost efficiency and productivity on the job site and lower fuel consumption and emissions, as well as the use of remote monitoring of machine conditions. Volvo Penta expanded its electromobility offerings with a cube battery for underground mining loader equipment. This is a step toward helping customers transition to net-zero emissions and achieving the company’s commitment to the Science Based Targets initiative, where it aims to reach net-zero value chain emissions by 2040.
Yanmar introduced a carbonneutral electrification strategy that will establish it as an all-in-one systems integrator for smart electrified power solutions tailored to the application-specific needs of individual OEMs. Yanmar has several new energy
projects in various sectors, including hydrogen-powered cogeneration, research into hydrogen fuel marine engines, biogas cogeneration, dualfuel power solutions with natural gas, fuel-cell marine technology, smart agriculture and resource recycling technologies.
For existing products in these unique sectors, it’s clear that customer demands for sustainable and decarbonization strategies are high. The use of low-carbon intensity fuels like hydrogenated vegetable oil (HVO), also known as renewable diesel fuel, deliver important near-term options for decarbonizing immediately. HVO is a drop-in replacement for petroleum diesel and can be used in blends with regular diesel fuel of up to 100%.
Sustainability and decarbonization take on many forms beyond equipment and fuel technology choice. In these sectors, with slower turnover of equipment, the remanufacturing of existing engines and equipment is one element of a sustainable strategy. It supports a circular economy, one that minimizes waste and energy consumption in making new products and restoring existing products back to original performance that includes lower fuel consumption than aging products.
Looking at these technology developments in very large machines and equipment brings a much greater appreciation for what it takes to tackle the industrial-size work of mining, construction, lifting, digging and moving material. Diesel powers most all of this equipment today, and from the looks of bauma 2022, it will continue that role in the future only to be enhanced by further innovation in engines and use of low-carbon fuels, being paired with electrichybrid technologies. Hydrogen, other gaseous fuels and fuel-cell propulsion systems will undoubtedly earn a place as well. To meet the challenge of climate change, we need all of these solutions.
Allen Schaeffer is the executive director for the Diesel Technology Forum, a nonprofit organization dedicated to raising awareness about the importance of diesel engines, fuel and technology.
The use of lowcarbon intensity fuels like hydrogenated vegetable oil, also known as renewable diesel fuel, deliver important nearterm options for decarbonizing immediately.
High prices for crude oil and fuel continue to be a tremendous issue throughout the world, driving inflation and impacting global markets amid Russia’s continued war in Ukraine and economies that are still trying to recover from the pandemic.
Fuels Market News interviewed three industry-focused oil and fuels analysts to discuss some of the factors that readers should watch for in the coming months. All were quick to point out that we are living in unusual times right now, making traditional forecasts difficult. All indicated little expectation of major changes in the status quo in the first quarter of 2023, barring extraordinary circumstances. However, they did offer some input on the various factors to watch as things develop.
The core component of refined product prices is typically linked to the price of crude oil, which was averaging in the $90 range at press time. This is down considerably from the peaks over $120 per barrel immediately after the Russian invasion of Ukraine. However, prices have stalled due to several supply and demand factors.
On the supply side, the industry was still recovering from the impact of the pandemic-related oil glut that saw prices plummet (even going negative for a short period), severely financially damaging many producers and hurting investors. Demand and supply were recovering, and then the Ukraine disruption occurred.
The resulting sanctions on oil-producing Russia substantially impacted Europe’s natural gas and refined product supply and disrupted global crude supplies. This has been gradually working itself out. Russia has so far been able to find alternative markets for much of its crude though sales to China, India, Turkey and even Saudi Arabia (though at lower volumes and discounted prices). The United States began to adjust its exports to fill European needs, and the Biden Administration began drawing down the Strategic Petroleum Reserve.
However, there was a lack of aggressive, extra production in regions like the United States to quickly ramp up supply. Further, OPEC+ in October 2022, agreed to production cuts of 2 million barrels per day, though that is not always set in stone.
“There’s a lot of difference between what [OPEC+] says and what the realities are,” said Alan Levine, founder and CEO of the hedging advisory firm Powerhouse. “We have a lot of serious uncertainties overseas, obviously, and we’ll see what emerges as the Saudis look for a new position for themselves in the world. There’s even talk that their ability to produce is somewhat strained as well.”
Geopolitical and economic headwinds are likely to persist into the first quarter, industry experts say.
The rationale for the OPEC+ cuts is straightforward.
“OPEC is saying that they made this cut because they see lower demand growth going forward from global economic issues,” said Brian Milne, energy editor and a product manager with DTN. “What they’re really trying to do is support oil at around $90 a barrel. Will they be successful? Demand can come. Or, when you start seeing demand drops and people lose confidence in the market, you could really see prices just plummet despite those cuts if you didn’t make them in time.”
Several of the analysts noted that the administration’s decision to refill the depleted Strategic Petroleum Reserve at $70 per barrel effectively sets a floor on how low prices can go.
U.S. fracking producers have also been hesitant to ramp up significant production to levels demanded by the Biden Administration, despite accusations of price gouging, threats of windfall profit taxes and favorable current oil prices. There are several factors at play.
“In both Europe and the United States, policy has been going against fossil fuels,” said Milne. “The restrictions on investments, the inability to get certain pipelines approved—in recent years that’s been a disincentive. Not to mention a number of the bigger banks have discouraged any sort of investment in oil production—the whole ESG thing.”
The focus on a future green economy and discouraging investment in traditional fuels is not all that’s impacting increased production. Since the beginning, fracking has involved regular cycles of both boom and bust (and, as already noted, the pandemic was a recent, huge bust period), and there finally appears to be some discipline in the industry.
“You’re hearing a lot of drillers have cleaned up their balance sheets,” Milne said. “They got rid of the debt because they’ve followed this process. That’s why if you look at crude production, it really hasn’t grown this year despite the high prices. So, what you’re seeing is more discipline, not just because of the Wall Street demands but also looking out and saying we want to preserve our reserves.”
What would happen if the war in Ukraine was suddenly decided with complete success for the West, causing sanctions to ease?
The bullish possibility is that all’s right with the world, traditional flows could resume, and buyers could seek to reestablish traditional relationships, Levine said. “Short-term demand from Western buyers boosts prices. Generally, good news encourages optimism and boosts prices. The bearish possibility is prices fall because of a reduced fear premium. No Putin, no dirty bomb and the potential for more Russian output. Demand for war goods, including jet and diesel fuel, falls.”
That leaves the demand side, where the “good” news is anything but good. The health of the global economy (and the U.S. economy more domestically) is likely the major issue weighing on where prices go moving forward.
Milne noted that the United States was in a recession in the first half of the year. “We saw some better growth than anticipated in the third quarter, but there are already signs of struggle,” he said. “Do we flip into negative growth in the fourth quarter? Maybe, maybe not.”
The situation is equally grave, if not more so, globally.
“It’s looking like a global recession is coming, and it’s hard to get out of this box now because you’re seeing inflation pressures,” Milne said. “There are some numbers that just came out from Germany and Italy showing high inflation. So, Europe is stuck in there. We know the U.S. still has high inflation, and the response is going to be through interest rates, and that’s going to curb the demand side.”
Milne noted crude price predictions range from Citibank projecting $65 per barrel WTI (based on predictions of a global economic recession), to Goldman Sachs and Bank of America anticipating $135 per barrel. He sees a price from $70-$85 or so a barrel as more likely going into 2023.
Diesel is under significant pressure globally. Europe lost imports from Russia, there have been refinery strikes in France and a number
“OPEC is saying that they made this cut because they see lower demand growth going forward from global economic issues. What they’re really trying to do is support oil at around $90 a barrel.”
—Brian Milne, energy editor and a product manager with DTN
of refiners have converted from conventional to renewable diesel. The United States has fared better, overall, but is facing some significant logistical issues with diesel on the East Coast.
“Inventories are terribly tight, and the mystery in all of this is we’ve got available crude oil to where we are exporting it,” Levine said. “And refinery operations are still in the upper 80s [percent] of capacity, so you’re still getting reasonable runs. But despite all that, we simply have been incapable of building inventories.”
A particular concern involves heating oil, which is essentially ultra-low sulfur diesel and remains a primary heating fuel in the Northeast. A cold winter would strain the market, while a warm winter would ease the situation. The weather is impossible to predict with complete certainty, but forecasts are encouraging so far.
“I think we get through this, because it sounds like the weather forecasts are actually trending a little bit milder than originally anticipated,” said Denton Cinquegrana, chief oil analyst for OPIS (a
because there’s a certain amount of winter turnaround, which is now going on. But nothing to cause a serious concern.”
Levine raised the point that the U.S. still has strong exports of both crude and distillates, and he wonders about the coherence of the policy supporting those exports.
“It’s hard to understand what policy we seem to be pursuing,” he said. “So, we empty out the petroleum reserve and send it overseas—that’s a little bit of a simplification, but still. And last week we exported 1,200,000 barrels [of distillate] a day, and it all detracts from the available pool for the United States.”
While an export ban would likely have an impact on diesel prices, Milne is not sold on the idea. “Short term, it would offer some relief for prices, but we would see Gulf Coast refineries starting to reduce runs. They would bring it in because they’re not going to be able to get the supply out.”
As with diesel, logistics pose challenges in
Dow Jones Company). “So that should help in the long run.”
Diesel prices work as an inflation multiplier since they ultimately impact the price of everything that moves on a truck or train. They are also supported by the state of the general economy.
“If we have a recession, the economic machine runs on diesel, and we’ll lose some of that diesel demand, and it will allow inventories to build up,” said Cinquegrana. “But you don’t want to get to a recession to help supplies and destroy demand. I think that’s going to be a big specter hanging over the market for probably the next six months or until the Federal Reserve really stops or slows down some of the interest rate hikes.”
Gasoline prices are likely to have moderating impacts coming up. Winter will naturally drop demand, and there have been no major hurricane disruptions in the Gulf.
“We don’t anticipate much of a problem with gasoline, at least in the next several months,” noted Levine. “There may be some support
the U.S. in moving product out of the gulf with pipelines at capacity. One logistics cure that is raised regularly when such disruptions occur is a temporary moratorium on the Jones Act. The act, dating to 1920, requires that only U.S. flagged ships carry cargo between ports. Diesel refining capacity is down on the East Coast, and the pipelines carrying refined products to the coast are nearly at capacity. So are the coastal tankers.
“Even if it’s a short-term waiver of a couple months to move diesel and gasoline from PADD3 to PADD1, I think that would really help in the short term,” said Cinquegrana. “I think Valero suggested this in their recent quarterly call, a short-term waiver on the gasoline sulfur specifications. We export a lot of gasoline because there’s a portion of it that doesn’t meet U.S. specifications.”
Backwardation, where the current spot price is higher than prices trading in the futures market, has been excessive. This also impacts building
“Inventories are terribly tight, and the mystery in all of this is we’ve got available crude oil to where we are exporting it.”
—Alan Levine, founder and CEO of the hedging advisory firm Powerhouse
supply. “This strong backwardation, say 50 cents, provides absolutely zero incentive to bring barrels into the terminal, into the storage tanks and hold them in,” said Cinquegrana. “So how do I build up inventory when there’s no incentive to store? You don’t have to reverse to contango [roughly the opposite of backwardation]. You need it to at least normalize to a point where it’s a couple of pennies of backwardation. I think the backwardation theme is going to be a big deal … into the new year, and if it stays like this it’s going to make it very complicated for supplies to normalize.”
With all the current challenges the bad news is that there is not likely any “silver bullet” solution that will solve things overnight. Similarly, there is not likely a super threat that will explode prices.
More of the same seems to be the most expected outlook on fuel prices. And, hopefully, we don’t have to rely on a drastic global recession to see cheap fuel again in 2023. Finally, one significant concern, a potential rail strike which would seriously impact current logistical shortcomings appears to have been negotiated successfully by the Biden Administration.
“This strong backwardation, say 50 cents, provides absolutely zero incentive to bring barrels into the terminal, into the storage tanks and hold them in. So how do I build up inventory when there’s no incentive to store?”
—Denton Cinquegrana, chief oil analyst for OPIS
28 February–2 March 2023
Bangkok, Thailand
Get transported into the epicenter of convenience innovation with the Asian-Pacific iconic retailers, senior-level convenience and fuel executives and speakers, to explore visionary on-the-go growth strategies, transform your specific product offerings and adapt innovation as the norm.
The Summit offers a space to collaborate with other top-level convenience leaders and a window into the future with the latest case studies, digital technologies, experiential store tours, and strategies to stand out and adjust to fast-changing consumer bahaviour.
Reserve your seat today! / convenience.org/CSA
By Keith ReidHow one Alabama retailer supports his business by being politically active.
Jigar Patel is the CEO of Hari 1 LLC, dba Fish River Food Mart, which is based in Fairhope, Alabama. The family-owned and -operated business has three stores. Patel’s uncle, Bharat R. Patel, entered the industry in 1984, and Jigar joined him in 2005. Drawing from his IT background, Patel helped convert what was a manual-process operation to an automated, digital-process business, bringing in back-office systems and scanning and inventory management. He became CEO in 2012. In 2022, Patel created a brand for the stores called FASTTIME. One store has been rebranded, and the leadership team is in the process of rebranding the other two. And the fourth one, when it comes up, will be branded FASTTIME as well.
As one of the legislative leaders at NACS, Patel serves on the political engagement committee to support advocacy efforts as the needs arise. As a small operator, Patel works hard to ensure the industry’s needs are presented to legislators and regulators both in Washington and in his state and county. Here we discuss his motivation for becoming involved, and why his peers should consider their own activism.
WHAT PROMPTED YOU TO BECOME INVOLVED IN POLITICAL ACTIVISM?
I was introduced to it by a friend of mine, and even before that, there was some curiosity in how this political system works and how it affects my business. I would see a law passed or a tax increase or the EPA has a new requirement, and I’ve always wanted to know how all those decisions are made and whether there was a way that I could give my feedback. About six or seven years ago I was introduced to NACS Day on the Hill, where we went to D.C. and met with all these different congressmen and senators and talked to them about the issues that were really bothering us small, independent operators.
I saw that there was an audience in their staffs or the representatives themselves, and they would listen to what I had to say. That’s what got me started and interested in learning more about how a bill goes through the process of becoming law and some of the things you could do to maybe influence the process. I saw that it’s very much important to be active at both the state and national levels. I share this with my peers every chance I get because it really matters. It makes a difference.
WHAT ARE SOME OF THE ACTIVITIES YOU’VE TAKEN PART IN ASIDE FROM DAY ON THE HILL TO KEEP THAT CONNECTION GOING?
We send emails regularly whenever there is a bill or an issue. We connect with congressional
representatives whenever they are in town. We invite them to our stores to see behind the scenes how everything operates. Many times, it’s the education that is missing, and the representatives don’t really know how a problem is coming up or what is driving that problem. When you take them behind the scenes, they can make educated decisions instead of just thinking what is best without that knowledge.
We also support state legislators by donating to their campaigns. And the same things—keeping in touch with them, inviting them to our meetings whenever [my colleagues and I] all get together so they can hear from store owners directly.
WHAT HAS BEEN ONE OF THE MORE SURPRISING THINGS YOU’VE ENCOUNTERED SINCE YOU STARTED THE PROCESS?
The surprising part is that not many people like me know that they need to be active on that lobbying front so that they can make a difference as well. You need someone who’s passionate about their business and who knows its needs in and out—someone who wants to educate the lawmakers and regulators.
WHAT IS THE NATURE OF THE COMMITMENTS INVOLVED?
As a small business owner, when I leave my stores and go to Day on the Hill or other government relations conferences, I have to leave all of that behind. Whereas all these big corporations can just hire somebody to do these things on their behalf.
I also don’t think this is a short-term process. This is something that you need to be active in for the long haul because laws are not made overnight. It’s a long process of understanding, educating and looking to find the best solution.
A LOT OF FOLKS ARE CYNICAL THESE DAYS ABOUT “PAY TO PLAY” IN POLITICS. WHAT IS YOUR PERSPECTIVE ON THAT?
It’s not always about the person with the most money in the PAC influencing it. If you have more people who can go over there and say, ‘We may not have millions of dollars to throw at you, but we have a number of people that will be impacted if you pass this bill.’ I think that’s where the strength is for small people like me and for parties with less financial resources like NACS, compared to lobbying groups like the credit card industry. And yet, that’s also our weakness,
because we need more people to decide that they want to do this.
One of the biggest ones when I had just beome active, and one of the big wins for the industry, was the Durbin Amendment which created competition on debit transaction routing on the network side. And the debit interchange and debit transaction fees came down for businesses across the country.
And now we are fighting to do the same thing on the credit card side. We are asking lawmakers to look at credit card fees that have gone up so much that now they’re acting as an inflation multiplier. So, we are just saying that we don’t want you to cap anything. We don’t want to limit anything. We are just asking to have competition on the credit side so that anybody who’s accepting credit cards or debit cards across the country would be able to see significant savings. Because, if you look at my businesses, just my stores, I’m spending more in credit card fees than I am in my mortgage.
Luckily, in the last few years we haven’t had to worry about much. Nothing like swipe fees. Things like zoning and permitting and things like that. But when you go to [legislators] and you share your side of the story, they are open to listen to it and provide a solution.
Yes, for example, the tobacco taxes in Mobile County have been increasing. And so, what happens there is that when I buy tobacco products, they come prepriced because of the tobacco taxes, and the cost of that product sometimes is higher than the price printed on the product. So that has been one of the issues that we’ve been working on over the past several years.
We’ve collected data from stores and shown what the cost is in the county right next to ours and what the cost is in this county. People are driving over to the next county and buying tobacco from there, and you are losing the tobacco revenue in Mobile County. We haven’t seen a solution to that yet, but we’ve been educating our members, so hopefully sooner or later we’ll see a solution come in our favor.
I’m a big believer in not having to reinvent the wheel. If I go somewhere and I see somebody doing something that is successful, I try to learn from them, and I see how I can replicate that in my life or in my business. So similarly, everybody who is in business does not have to reinvent the wheel by having to figure out how to be active on the political side. They can very easily become a member of NACS at a very minimal cost. They can go to their state associations and become members there and become active on that side.
See what issues that the majority of people in the industry are talking about. Ask yourself, ‘does that pertain to my business?’ Many times, they’ll see that those issues affect their businesses as well, and all they have to do is just become active. Organizations have streamlined ways for people to connect with their legislators where they can educate them on an issue and what it means for their operation. It’s just taking that first step.
Keith Reid is editor-in-chief of Fuels Market News. He can be reached at kreid@fmnweb.com
THIS IS SOMETHING THAT YOU NEED TO BE ACTIVE IN FOR THE LONG HAUL BECAUSE LAWS ARE NOT MADE OVERNIGHT.
omogeneous charge compression ignition (HCCI) engines have better gas mileage and lower nitrogen oxide (NOx) and particulate matter (PM) emissions than traditional diesel or spark-ignition engines, but there are challenges that need to be addressed before potential broad-scale use in commercial vehicles.
A traditional gasoline spark-ignition engine is characterized as a flame propagation mechanism. Variable ignition time from the spark discharge can influence the start of combustion in the engine. In the spark-ignition engine, the electric control unit sets the ignition timing as per the ignition pattern.
Compression-ignition engine combustion is conventional diesel combustion, which occurs at higher compression ratios than spark-ignition engines. Rather than being ignited by a spark plug, the air-fuel mixture in this engine autoignites as a result of piston compression.
The HCCI process is similar to that of a spark-ignition engine, which uses a homogeneous charge for combustion, and to that of a compression-ignition engine, which uses autoignition. As a result, HCCI is a combination of spark-ignition and compression-ignition combustion processes. However, HCCI engines differ from conventional
ICEs in that there are no spark plugs or injectors to assist combustion. The HCCI engine has the high efficiency of compression ignition and the very low emissions of spark ignition with catalytic converters. HCCI is also a single-fueled engine that applies a homogeneous charge to premixed fuel and combusts the mixture.
In an HCCI engine, gasoline is injected into warmed air by port fuel injection or direct injection in the cylinder to establish a homogenous charge. The temperature, pressure and concentration origins of the homogeneous charge, as well as the specific reaction mechanism of the fuel, air and residual gas mixture, all influence the ignition timing of a HCCI engine. First, fuel and air are premixed at the beginning of the combustion process. During the compression stroke, the homogenous charge is heated, hits the autoignition point at the TDC, and then autoignites in many points throughout the cylinder. The mixture also autoignites when the temperature rises in the compression stroke.
HCCI engines could be a new alternative to conventional combustion engines. Compared with diesel combustion, which relies on a fuel/air mixture, HCCI reactions are not always constrained by the
This promising alternative to combustion engines needs more development before mass production.
mixing speed at the fuel jet-oxidizer contact. HCCI engines lack a visible flame front and a confined high-temperature reaction area, compared with conventional spark-ignition combustion, which primarily depends on flame propagation. HCCI combustion is a chemical kinetic reaction regulated by temperature, pressure and in-cylinder charge composition, which reacts faster than both spark ignition and compression ignition. Additionally, HCCI combustion reaction usually happens quickly at low temperatures, and the bulk energy released at high temperatures is controlled by carbon monoxide oxidation. This results in limited combustion reac-
of smoke due to the lack of diffusion-limited combustion and confined fuel-rich zones. However, poor mixture preparation may form liquid fuel deposition during the combustion cylinder and in localized fuel-rich areas as the SAE technical paper notes.
Even though the HCCI engine has better thermal efficiency and emissions than conventional engines, it has various restrictions and technical challenges. Homogenous charge preparation, controlled auto-ignition timing, combustion phase,
tions occurring at high temperatures, which reduces the amount of emitted CO2
HCCI engines have been certified to emit low NOx and particulate matter and produce high thermal efficiency. HCCI combustion can reduce NOx emissions by 90-98% compared to traditional compression-ignition combustion. This is because of the absence of high-temperature regions within the combustion chamber in the mechanism of the HCCI engine, as noted in the SAE International technical paper “Homogeneous Charge Compression Ignition (HCCI): Benefits, Compromises, and Future Engine Applications.”
The global fuel/air ratio in HCCI combustion processes is normally relatively low, and the temperature within the reaction chamber is substantially lower than in compression-ignition or spark-ignition engines. So, the time required for full homogeneous mixing of air and fuel under lowload circumstances is less than the ignition delay period. HCCI combustion also produces low levels
high-pressure rise rate, knocking and noise, operation range limitation over a wide speed and load, high HC and CO, and cold start all must be resolved before mass production and release on the market.
The two main stumbling blocks to adoption are controlling the ignition timing and combustion phase. HCCI combustion has a low processing range and lacks control over the ignition process. Unlike traditional engines, HCCI engines do not have a direct strategy to control the start of combustion. The HCCI combustion process starts when the air-fuel mixture auto-ignites, which the mixture is exposed as fuel burns and timetemperature history reacts. The combustion phasing of HCCI engines is influenced by fuel autoignition qualities, fuel content, residual rate and reactivity, mixture homogeneity, compression ratio, intake temperature, fuel latent heat of vaporization and engine temperature, heat flux to the engine and other engine-dependent factors.
HCCI COMBUSTION CAN REDUCE NOx EMISSIONS BY 90-98% COMPARED TO TRADITIONAL COMPRESSIONIGNITION COMBUSTION.
In addition, during the combustion phase in the cylinder, the combustion rate and combustion pressure heating rate are critical factors. High-pressure increase rates cause severe sonic vibrations in the cylinder, resulting in knocking combustion and risking engine damage. To control HCCI combustion phasing, the most important strategy is to control the timetemperature relation. This leads to changing the behavior of the mixture for autoignition.
Limited operating load range is one of the biggest barriers to successful development. Controlling charge autoignition at greater loads is challenging, and since there is no direct way of controlling combustion at greater engine loads, it is hard to manage the frequency of combustion. To solve these challenges, an engine can be run in several modes: spark-ignition and compression-ignition modes for one-third to one-half of the operating load range and HCCI mode for the balance. Researchers have further discovered that by substantially stratifying the charge (temperature and mixture stratification) under high engine loads to prolong the heat-release process, the operational range may be greatly increased.
There is the potential to use HCCI in hybrid vehicles to limit the operating range of the engine so that autoignition can be controlled. Ignition control challenges stem from the lack of a direct trigger, as well as the narrow working range between the upper “knock” and lower “misfire” limits. To help this, dual-fueled combustion technology was developed as an alternative to better regulate the combustion phase by combining two different reactivity fuels while retaining low NOx and particulate matter emissions. Thus, an HCCI engine with a dual-mode operation (e.g., SI-HCCI) will be essential to cover the entire operating range in an automobile application. The dualmode engine with a hybrid-electric powertrain can extend engine duration when operating in the HCCI mode and reduce transitions between HCCI and spark-ignition modes. (Mazda is already exploring this technology with its Skyactiv-X engines.)
Hybrid electric vehicles (HEVs) improve fuel efficiency without losing vehicle performance or usability. For example, HCCI hybrid spark
ignition can replace the standard spark ignition in a traditional vehicle, which improves the fuel economy by about 17%. In addition, HEVs are available in a wide range of configurations and levels of electrification. Usually, the most fuelefficient choice for a dual-mode system would be a current compression-ignition engine, but combining a highly expensive engine with hybrid results in an unaffordable vehicle price.
HCCI engines normally emit higher HC and CO than traditional diesel engines. As is true with all homogeneous combustion processes, a large percentage of the in-cylinder fuel is retained in fissures during the compression stage and avoids combustion. Also, the temperature is not high enough to burn most of the unreacted gasoline when it flows back to the cylinder during the adiabatic expansion. Therefore, both HC and CO emissions boost massively due to incomplete combustion.
The knock tendency is affected by the two fuels under varying load conditions, as represented by the fuel energy absorbed in the autoignited zone. Knocking occurs when the piston does not reach TDC due to early combustion. Furthermore, the degradation of combustion efficiency along with ignition issues influences the performance of HCCI combustion at the lowest loads. At greater loads, the rate of pressure sharply increases, which causes engine noise to rise dramatically, and if left unchecked, the engine might fail.
Since the exhaust gas includes more CO2 than O2 , engine-out exhaust gas recirculation (EGR) raises the combustion temperature dramatically. As a result, the EGR principle demands combining the remaining gases from the prior period with fresh charge or air in the inlet manifold to reduce NOx emissions. EGR improves the charge’s autoignition capabilities by lowering the maximum pressure during heating.
Internal EGR, which may be adjusted by variable valve timing, improves cold start and warmup times. In a study using a single cylinder spontaneously released HCCI engine with both internal and external EGR, researchers found that when negative valve overlapping increased, NOx emissions rose according to the high temperature of the gases, whereas external EGR had no impact on NOx emissions.
For best outcomes, EGR should be combined with another innovation such as alternative fuel or a chemical method.
Advanced combustion technologies have been studied extensively to replace conventional combustion engines. HCCI engines not only improve effective efficiency and reduce emissions of NOx and particulate matter compared with the internal combustion engine but also display a high level of adaptation and flexibility to many types of fuels. However, the HCCI engine is not perfect; it has challenges affecting its successful operation. Future studies should aim to overcome those difficulties before widescale manufacturing of HCCI engines for commercial use. The main problems are combustion phasing control, high HC and CO emissions, operation range extension, cold start and homogenous mixture preparation.
Dr. Raj Shah is a director at Koehler Instrument Company. He is an elected Fellow by his peers at IChemE, CMI, STLE, AIC, NLGI, INSTMC, Institute of Physics, The Energy Institute and The Royal Society of Chemistry. An ASTM Eagle award recipient, Dr. Shah recently coedited the bestseller “Fuels and Lubricants handbook.”
Dr. Vikram Mittal is an assistant professor at the United States Military Academy in the Department of Systems Engineering. Dr. Mittal’s current research interests include system design, model-based systems engineering and modern engine technologies.
Shi Ying Zheng is a chemical engineer student from SUNY, Stony Brook University, where Drs. Shah and Mittal are on the external advisory board of directors.
“Trinium
Dover Fueling Solutions (DFS), part of Dover Corporation and a global provider of advanced customerfocused technologies, services and solutions in the fuel and convenience retail industry, announced all North American Wayne Ovation fuel dispensers will be supplied as compatible and UL-listed to E40/B20 as a standard feature. The announcement extends DFS’ UL compliance from E25 to E40, with the continued option of up to E85 available across all models and configurations and cements DFS as the first manufacturer of fuel dispensers to offer an E40 UL listing. DFS works in partnership with the National Corn Growers Association to prepare for fueling advancements, enhance dispenser offerings and meet infrastructure needs for future mid-level ethanol blends.
Frank Minnella, CEO of Lock America of Corona, California, announced that Robert Chen was named as national sales manager. “We are pleased to acknowledge Robert’s creativity and performance in helping the company negotiate these challenging economic times. He has spearheaded and supported our efforts to enter new markets and enhance our products for current and new customers.” Chen succeeds Dan Walsh upon Walsh’s retirement.” Lock America develops, manufactures and markets a wide range of security locks and hardware for many markets, including amusement and vending, ATM, information management, municipal government, petroleum and propane distribution and self-storage.
PDI Technologies has expanded its Offer Network by integrating its age and identity verification capabilities. Since acquiring Koupon in 2021, PDI has been innovating more effective ways to optimize loyalty and retail promotions that in turn increase brand visibility and sales. Included with the expansion is the launch of the Deal Hound solution, along with new offers for tobacco and nicotine products from Reynolds Marketing Services Company for age 21+ GasBuddy tobacco consumers. These announcements follow other recent integrations and collaborations, as PDI continues connecting convenience across the industry.
iRely LLC, a partner providing enterprise software for the energy and soft commodities industries, announces Childers Oil has selected iRely as its partner of choice for its wholesale and ERP software solution. Childers Oil Company is a family-operated business based out of Whitesburg, Kentucky. Founded in 1966, the company’s roots are in providing bulk petroleum services to retail and industrial customers. Since the companys inception, it has become a major player in the Kentucky, Tennessee and West Virginia markets, with a mission to provide innovative, firstclass products and services to customers in the Southern Appalachian Region.
Gilbarco Veeder-Root, a Vontier Corporation business in fueling and convenience store technologies, announced the launch of MediaReach, a digital marketing platform that helps retailers deliver unique, site-specific forecourt media experiences that increase in-store foot traffic and sales. One store’s top-selling item may not succeed in another neighborhood across town or in another region. MediaReach solves those complexities with ease, unlocking the full marketing potential of every forecourt. The easy-to-use, rules-based platform customizes dispenser marketing content based on a wide range of factors including time of day, customer demographics, even real-time weather conditions. It uses those factors to create custom ad playlists for each individual station in its network.
TXB (Texas Born), a family of customer service-oriented convenience stores and food market operations, launched a new, custom app in partnership with Paytronix Systems Inc. to provide guests with seamless mobile ordering capabilities. As an industry first, the new app will give customers the opportunity to earn and save on gas purchases—unlike any loyalty and rewards program currently in the market. The new app will provide a streamlined user-friendly experience and offer guests more opportunities to save through TXB’s loyalty program.
When Warren Platt launched National Petroleum News in 1909 it was described as the “voice of the independent oil industry.” At the time, the industry it served was made up of small refiners and drilling operations butting up against Rockefeller’s Standard Oil. The content of the magazine tended to be upstream in nature, and the advertisements were focused on refining, drilling and the rail transport of crude. Gasoline was covered (as was whale oil) but primarily as an industrial solvent. The earliest cars on what passed for roads in 1909 were seen more as novelties and didn’t have the numbers to support a gasoline market. Two pivotal events helped change the industry.
The first event was Henry Ford’s Model T automobile, and more specifically, his method of mass production made the vehicle widely available at an affordable cost. The first Model T rolled off the production line in late 1908. It hadn’t yet made an impact, but year by year the numbers increased, and the era of horse transportation was on its way out.
The second event was World War I (1914 – 1918). This was the first truly
mechanized war. Trucks began to supplant horses for moving troops and supplies. Combat aircraft and zeppelins were powered by gasoline engines. Submarines were powered by gasoline or diesel engines and used batteries and electric propulsion to operate under water. Rudimentary “tanks” powered by gasoline engines were developed to replace the grand European cavalries that were made obsolete overnight by the machine gun.
The war may have ended, but mechanization was here to stay.
Looking back at NPN magazine 100 years ago—January 3, 1923—we can see that transition just getting underway.
Editorially, most of the magazine still focused on exploration and production, including some scientific articles relative to the refining process and cementing oil wells. But shifts were starting to appear. There were several news items describing the opposition to different gasoline taxes. Some of the refining articles were focused on advances in automotive lubricants. Gasoline stocks and prices featured as prominently as similar coverage for crude. The ability of railroads to supply jobbers with products was
covered. The evaporation of gasoline from storage tanks received a look.
And then there was a jobber-focused article by Warren Platt, “Marketers Must Meet Active Competition,” that outlined some of the new approaches to economical drive-in stations that were being deployed. “It is not necessary to put as much money into those stations as has been the practice nor is it necessary to perch them on every street corner. Rather, the wise, small marketers will place the stations at advantageous locations and build them at an absolute minimum expense, figuring on low-cost first and using some taste in the color of the paint for good looks along with a few flowers and shrubs. Then he will put out salesman to drive business into the stations, probably using advertising and coupon books,” Platt states.
From an advertising perspective, most of the products were still focused upstream, but several dispenser companies bought ads, most notably Wayne (which was acquired a few years back by Dover Fueling Solutions), and Heil promoted its multi-compartment truck tank solutions. There were air compressors being sold for automotive service and even an ad for the Eco Air Stations tire inflation solution.
By the end of the 1920s, transitions for both NPN magazine and the industry at large would be complete. Crude still would be critically important, but the real action was centered around gasoline, diesel, heating oil and bunker fuel. Just as important, NPN would be covering retail profit centers such as lubrication service and tires, batteries and accessories as much as, if not more than, the fuel products themselves.
For more than 100 years, from its founding in 1909 to when it went out of business in 2013, National Petroleum News (NPN) documented the rise of petroleum marketing and retailing in the United States. NACS, PEI and The Fuels Institute have catalogued the rich history of NPN in its entirety. Each issue of Fuels Market News will look back at the history of our vibrant industry, through the eyes of NPN, to see how it reflect the issues, challenges and opportunities we face today.
A new year, offering tremendous opportunities.
With a full line-up of programming in 2023, NACS has something for everyone. convenience.org/events
NACS Show
October 3-6, 2023
Atlanta, GA
Global
NACS Convenience
Summit Asia
February 28-March 2, 2023
Bangkok, Thailand
NACS Convenience
Summit Europe
May 30-June 1, 2023
Dublin, Ireland
Government Relations
NACS Day on the Hill
March 7-8, 2023
Washington, DC
NACS In Store
Throughout 2023
Leadership
NACS Leadership Forum
February 8-10, 2023
Miami Beach, FL
NACS Leadership for Success
April 30-May 5, 2023
Richmond, VA
NACS Financial Leadership Program*
July 16-21, 2023
The Wharton School
University of Pennsylvania
Philadelphia, PA
Endowed by: Cash Depot
NACS Marketing Leadership Program*
July 23-28, 2023
Kellogg School of Management
Northwestern University
Evanston, IL
Endowed by: Keurig Dr Pepper, Nielsen
NACS Executive Leadership Program*
July 30-August 3, 2023
Dyson School
Cornell University
Ithaca, NY
Endowed by: Reynolds
NACS Innovation Leadership Program*
November 5-10, 2023
MIT Sloan School of Management
Cambridge, MA
Supported by: Gilbarco, Mondelez, Shell
NACS Women’s Leadership Program*
November 13-18, 2023
Yale School of Management
New Haven, CT
Endowed by: Altria, Frito Lay
NACS Human Resources Forum
March 20-22, 2023
Savannah, GA
NACS State of the Industry Summit
April 18-20, 2023
Dallas, TX
*PLAN NOW! Achieve the Master of Convenience designation by completing 3 of the 5 Executive Education programs.
Protect your station against fuel theft with in-dispenser security and built in siren.
According to a State of Florida Report, 85% of skimmers are found in gas pumps with new locks or security labels. Don’t let your brand get tarnished by compromised fuel dispensers. Build trust and grow customer loyalty by taking the necessary precautions to prevent fraud with Defender One® products.
The Defender One®’s unique patented process can stop a transaction in progress and deactivate a breached dispenser. The Defender One® reduces your risk by disabling a compromised fuel dispenser
Designed to meet the critical safety requirements of a retail fuel station. Underwriters Laboratory certification for use in a Class 1, DIVISION 1, GROUP D hazardous environment. Battery back-up provides protection during power outages.
The Defender One® allows you to customize security to fit your operations and has the capability to interface with existing alarm panels.
• UL listed + certified
• US patented
• Prevent fraud + theft
• Reduce service time
• Boost customer confidence
• No contracts or subscriptions
• AC powered with battery back-up
• Doesn’t cut power to pump
• Customizable security to fit your operations
• Interfaces with existing security and alarm panels