
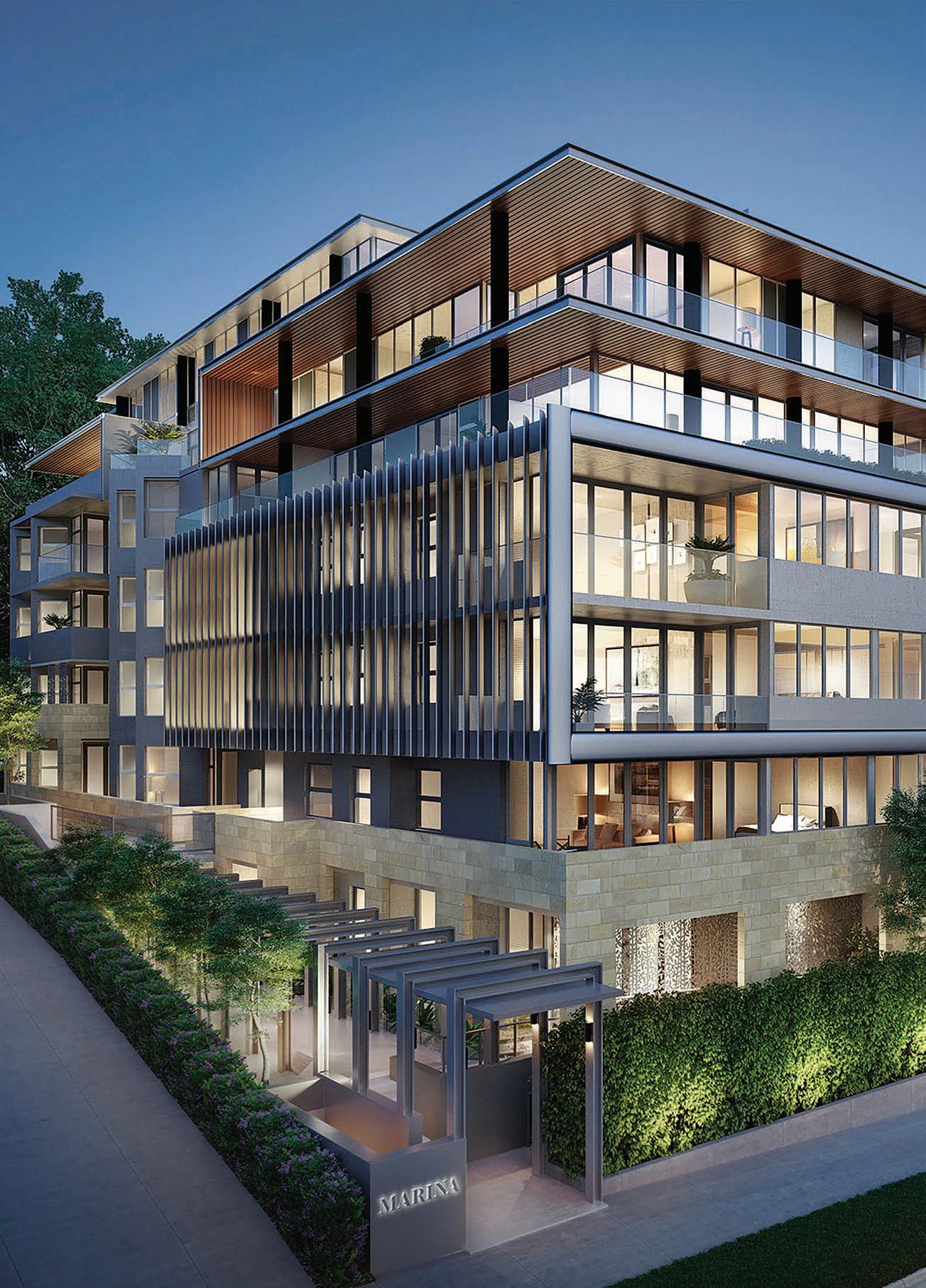
Showcasing Fujitsu’s Commercial Capabilities 2022
Fujitsu General Limited is a leading, global manufacturer of air conditioners and was founded in Japan in 1936 with its original heritage in manufacturing home electrical appliances. The air conditioning division began in 1960 and is the core of the business today. The Fujitsu General Australia (FGA) division was established in 1974 and is now a leading supplier of quality air conditioning products in Australia offering a range of products to suit almost all domestic and commercial requirements and has offices and warehouse facilities in all major capital cities around Australia. Fujitsu General Australia is well known as ‘Australia’s Favourite Air®’.
At Fujitsu, we pride ourselves on providing exceptional customer service. Fujitsu General Assist is our in-house customer care and technical support department which was implemented to deliver a high level of support and accessibility to our customers.
Fujitsu General Assist deploys Fujitsu trained technicians in Sydney, Melbourne, Brisbane, Adelaide and Perth and provides access to dedicated Service Agents in all other parts of Australia. These technicians are well equipped with the necessary tools and spare parts to enable them to resolve issues onsite, promptly, offering customers a high first time fix rate and seamless experience.
Fujitsu General trained technicians attend every commercial VRF installation to assist with the controls commissioning of the VRF units to ensure seamless operation.
Fujitsu believe in the quality and reliability of every air conditioner we sell, providing a 3 years warranty for commercial applications and 5 years warranty for domestic applications.
SITE
THE WINX STAND, ROYAL RANDWICK
RACECOURSE NSW
CLIENT/PROJECT MANAGER
AUSTRALIAN TURF
CLUB/TAYLOR
CONSTRUCTIONS/SEDA SERVICES
PROJECT TIMELINE JULY 2020DECEMBER 2021
The Winx Stand at Sydney’s leading horse racing venue, Royal Randwick Racecourse, is the Australian Turf Club’s (ATC) new large-scale function centre. Named after the legendary mare who captivated the racing world, the two-storey, multipurpose facility is a striking venue with capacity for up to 7,500 patrons in race day mode. With a gross floor area of approximately 5,043 square metres, the new venue features an outdoor terrace, open air roof top, balcony spaces, food and beverage facilities, and numerous light-filled spaces that can accommodate events of all sizes.
With a mix of indoor and outdoor spaces, and the need to accommodate functions of varying sizes, this venue had very diverse air conditioning needs. The project required a customised applied system that could operate at full capacity on race day, or on a scaled down capacity for smaller functions.
The addition of applied products to Fujitsu General’s AIRSTAGE offering provided SEDA Services with an extensive range of customisable commercial solutions for this project.
SEDA Services and Fujitsu General collaborated to design a HVAC solution that: would minimise the maintenance and energy usage costs to the ATC; removed water sourced heat rejection plant, which requires constant water consumption to operate; and would help the venue achieve a future Green Star 4.5 rating.
According to Kyle Rafter, Head of Product ANZ, Fujitsu General, “Originally, two water cooled screw chillers were to be installed in a plant room in the centre of the building however, this space was repurposed for storage. The plans were modified with the two air cooled screw chillers installed on the roof of the stand.
“The use of an inverter on each chiller that produces a capacity of 734kW ensured this change had no negative impact on the benefits of the system and delivered a highly efficient solution. SEDA Services also had to consider the increased loads on the equipment due to high occupancy rates within the conditioned space.”
“To enable us to achieve the loads required while maintaining the allowed space for plant SEDA had to work closely with Fujitsu to design and implement a hybrid solution with a mixture of both VRF and chilled/heating water systems.” Simon Henderson, NSW Senior Project Manager, SEDA Services
The Fujitsu General AIRSTAGE installation in this large, world-class venue is a holistic HVAC solution comprising two air cooled screw chillers, four large air handling units (AHUs), DX split systems and VRF components.
The size of the building required two chillers, designed with screw compressors and inverters to significantly reduce energy consumption. The chillers are air cooled and utilise a shell and tube heat exchanger for the evaporator. Each chiller contains two screw compressors controlled by an inverter achieving an integrated part load value of 4.68. The chiller contains a Danfoss control panel and BACnet interface for simple connection to the building management system.
1 ASTG18LVCC
1 ASTG09LVCC
1 ASTG24LFCC
3 ABTG54LRTA
4 ASTG22LVCC
4 ARXC60GATH
1 ARXC090GTEH
1 ARXC096GTEH
1 ARXC036GTEH
The four AHUs all incorporated EC fan motors for better efficiency. Having two chillers and four AHUs, provides the venue with greater flexibility for indoor comfort management. The system can be used at full capacity if race day operation requires all areas to be air conditioned, or it can be used in a banquet type mode to air condition certain hall spaces only outside of race days.
Inclusion of Fujitsu General DX split systems and VRF in the HVAC design caters for smaller areas to ensure the chillers don’t need to run at extreme loads.
OTHER: 7 UTY-RNRYZ3 WIRED REMOTE CONTROLLER
1 UTY-DCGYZ1 VRF CENTRAL REMOTE CONTROLLER
1 UTY-VBGX BACNET GATEWAY 12 SEPARATION TUBES 2 SINGLE PORT RBS 2 8-PORT RBS
Working with franchisees, suppliers and producers, McDonalds is working to cut greenhouse gas (GHG) emissions associated with its restaurants and offices by 36 per cent by 2030, while also being committed to a net zero emissions target by 2050. Initiatives to achieve this have included refurbishing its restaurants to consume less energy by updating everything from energy management systems for lighting, heating and air conditioning (HVAC), to more efficient kitchen equipment. Since its 2015 base year, the global organisation has reduced absolute emissions from its restaurants and offices by 8.5 per cent.1
Located on the corner of Burwood Highway and Scott Grove, Burwood, Victoria, the 24-hour McDonald’s restaurant was undergoing a refurbishment. This included modifying the interior layout and
replacing the air conditioning with a system that could provide the latest technology and control options to minimise the restaurant’s power usage, while also providing usage reports that arm the franchisee with information to make informed business decisions.
While the interior layout of the restaurant was being modified, the roof would remain the same. The new heating, ventilation, and air conditioning (HVAC) system had to use the existing duct layout and no new penetrations could be made.
Following Fujitsu General’s assessment of the engineering brief, the installation included: two 66kW AIRSTAGE™ Roof Top Packaged Units; (with Economiser; De-Super Heater); anywAiR iO controls; and a variable refrigerant flow (VRF) system.
The two 66kW Roof Top Packaged Units would deliver the indoor comfort the staff was accustomed to, with the latest technology suited for a commercial installation of this size. One Roof Top Packaged Unit was installed for the kitchen area, and another for the dining area.
Regardless of the outdoor temperature, a restaurant kitchen can become unbearable if not managed effectively. The Economiser option enables high energy-saving operation as the outdoor air is used for cooling or warming the internal air. Based on free-cooling technology, the unit features three dampers intelligently managed by an electronic control that constantly monitors the internal and external air temperatures. The Economiser easily integrates with the Danfoss DDC control built into the AIRSTAGE Roof Top Packaged Unit.
The engineering brief specified a De-Super Heater be connected to the hot water system. The De- Super Heater captures and transfers the heat energies from the refrigeration cycle to the hot-water loop via a heat-exchanger rather than rejecting the heat energies through the de-super heating and condensation process on the condenser side into the atmosphere. Incorporating a De-Super Heater in the project would provide the restaurant with an additional smart power saving solution.
For remote control capability, Fujitsu General installed anywAiR iO with wireless sensors. This lets the franchisee: monitor the wattage being consumed; manage the system operation; and remotely change the set temperature. The system also lets the franchisee connect with and manage other restaurant locations from one convenient dashboard, in the office or via mobile phone.
The variable refrigerant flow (VRF) system was installed for a smaller room that had previously been an outdoor space and was being enclosed as an all-weather party room.
OUTDOOR UNITS:
AOTG24LATC 7.1KW INVERTER OUTDOOR SET -ASTG09KMTC 2.5 KW R32 KMTC
SERIES WALL MOUNTED SET
A JT040LCLAH 12.1KW VRF J-IIS
SERIES COMPACT VRF SYSTEM
ROOF TOP PACKAGED UNITS:
RAQ/K/WP/ECO422-DS 66KW
SINGLE SKIN RTPU INCL DE-SUPER HEATER
RA Q/K/WP/ECO0422 66KW SINGLE SKIN RTPU
INDOOR UNITS:
AUTG24LVLC 7.1KW R410A INVERTER CASSETTE INDOOR
A UXK034GLEHVRF CIRCULAR FLOW CASSETTE LARGE TYPE INDOOR
OTHER:
UTY-TWRXZ2 COMMUNICATION KIT
UT G-UFYD-W GRILLE TO SUIT AUTG INVERTER COMPACT CASSETTE UT Y-RNRYZ3 WIRED REMOTE CONTROLLER
UT G-UKYA-B CASSETTE GRILLE BLACK 1 X R UBIX COMPUTE WITH LORA AND RS485 HLI MODBUS C ONNECTION TO 3 X PACKAGE AC UNITS
HLI MODBUS C ONNECTION TO 3 X ELECTRICAL METERS
1 X EDGE IO28 F OR LOW LEVEL
ENABLE OF 3 X PACKAGE AC UNITS
SUPPL Y OF IOT-READY ENCLOSURE WITH DIN RAIL, POWER SUPPLY, CIRCUIT PROTECTION & PLUG BASE
QUANTITY OF OUTDOOR UNITS: 5
QUANTITY OF INDOOR UNITS: 3
SYSTEM CAPACITY: 153.7KW
Offering premium riverside living just a few kilometres from Melbourne’s CBD, Green Square is a $250 million residential apartment development in Victoria Street Abbotsford.
Developed by Salta Properties on a former Metropolitan Fire Brigade site, the first stage features over 400 luxury apartments across four buildings as well as a further 93 serviced apartments managed by Quest.
Designed around a dynamic outdoor recreational hub, Green Square offers residents a host of onsite amenities including indoor/outdoor swimming pool, gymnasium, library, basement car parking and rooftop entertainment zone.
And it’s unique position on Victoria Street also provides direct access to the Yarra River, parks and bushland of nearby Studley and Yarra Bend parks, as well as being within close walking distance to Richmond’s vibrant shops, cafes and restaurants.
Salta Properties engaged Icon Construction as head contractor on the first stage of the Green Square project, and appointed multidisciplinary firm SJB Architects as architect and interior designer. SJB took an innovative approach to the project to successfully integrate higher density living into one of Melbourne’s traditionally low-rise suburbs.
Each building has been designed with its own individual lobby access, gathered around the large central green square, while the apartments feature views across the Yarra, to the city or across the adjoining suburb of Richmond.
A ground floor retail frontage to Victoria Street was also created, as were two distinct street frontages to the apartment buildings.
Consulting engineer Simpson Kotzman was appointed to the project, while local HVAC contractor Rival Air was engaged by Icon Construction to provide a quality, air conditioning and mechanical services solution. Construction commenced on the site in the last quarter of 2012.
According to Rival Air’s Managing Director Andrew Stewart, the project brief demanded a quality air conditioning and heating solution that matched the high end finish of the apartments. This required Rival Air to rework original concept drawings to ensure outdoor condensers were located away from the apartments where they would not be visible and avoid noise issues.
“The client did not want balcony-mounted condensing units with the systems,” Andrew says.“So we worked closely with both the architect and the engineer to understand what was and what wasn’t going to work. This led to relocating around 100 condensing units from the basement car park to a rooftop location to avoid issues around heat rejection.”
With the apartment buildings up to ten storeys high including basement car parks, refrigerant pipe runs became an important consideration. Rival Air began a review of various air conditioning solutions that would provide the flexibility of longer or shorter pipe run lengths, depending on the location of the apartment. Additionally, it was important that the design of the indoor units was also consistent.
“We wanted to avoid the situation where a semicommercial style product would be required in apartments where long refrigerant pipework runs were present, while a domestic type product was used in other areas where refrigerant pipework runs weren’t as long,” says Andrew.
After comparing available systems, Rival Air selected Fujitsu General’s Airstage J-II Series range of heat pump units to provide cooling and heating to the development’s one and two bedroom apartments, as well as the Quest serviced apartments.
“Fujitsu offer a wide range of products with long refrigerant pipe runs, and they also offer a consistent range of indoor units across their domestic and light commercial range and this consistent look was important to the developer.”
Additionally, Andrew says Fujitsu was able to provide the flexibility for apartment buyers to elect to upgrade their system. He says around 70 apartments were upgraded to multi-systems to
provide individual conditioning of living areas and bedrooms.
The HVAC design for the serviced apartments also required multi-systems to be installed. Quest also specified the installation of reed switches on balcony doors, so that air conditioning automatically switches off when doors are opened. “Fujitsu were able to fulfil all of these requirements,” says Andrew.
Rival Air then set about designing a solution that kept refrigerant pipework runs to a minimum. This resulted in a top down, bottom up approach whereby condensing units serving apartments on the bottom four floors were located in the basement car parks, and those serving the levels above were located on the roof.
“Because of the longer pipe runs lengths afforded by the Fujitsu units, we were able to get more units onto the roof and less in the car park. This was advantageous because of the heat rejection available and also allowed for more car parking spaces to be available.”
As well as improving the aesthetics of the development, the basement and rooftop locations also removed any concerns about noise from the condensers.
Considered the best product for this type of application, Fujitsu General’s advanced VRF technology used in the J-II Series allows for a total refrigerant piping length of 180m.
The J-II Series system provides energy efficient cooling and heating via the unit’s DC inverter control, at both full load and low to medium load operation and with any Fujitsu indoor unit. Heat exchanger performance is also substantially improved by the unit’s 3-row large heat exchanger design, while a subcool, dual tube heat exchanger improves cooling performance.
The total combined capacity of the systems installed at Green Square is approximately 3500kW.
According to Andrew, despite the large number of apartments and air conditioning systems across the Green Square project, a central plant was never considered for a number of reasons, including that the provision for individual billing is made difficult.
“The billing associated with central plant and common-type systems have always been an issue in apartment buildings,” he says. “Providing a dedicated condenser for each apartment and individual control is the easiest and most costeffective way of achieving individual billing.”
Construction of Green Square was completed in March 2014 and officially opened by the Victorian Minister for Planning in April 2014. Rival Air provided warranty and maintenance during the obligatory twelve month warranty period, and its service department continues to provide maintenance to the property today. “The systems have performed very well since the project was completed in March 2014 and we’ve been more than happy with the product,” says Andrew.
All areas of the project, from individual apartments and serviced apartments to lobby areas, feature Fujitsu indoor units that add to the luxury interior design created by SJB. “No one sees the condensing units,” says Andrew. “It’s all about the indoors and Fujitsu offered us a very similar look of unit all the way through the project. So whether it required a short refrigerant pipe run or a long one, we knew we had that consistency.”
To this end, he says Fujitsu General’s pre-sales support was vital to the success of the project.
“Fujitsu’s pre-sales support gave us the confidence to use their product. They provided us with the answers and information we needed including the types of controls and multi-systems we could offer as upgrades. I don’t think we would have got a better product for this particular project than Fujitsu.”
Fujitsu’s pre sale support gave us the confidence to use their product.
- Andrew Stewart, Managing Director, Rival Air
PRODUCT OVERVIEW
PRODUCTS:
42 J-II SERIES HEAT PUMP OUTDOOR UNITS
165 INDOOR UNITS
464 SPLIT SYSTEMS
8 DUCTED SYSTEMS
TOTAL SYSTEM CAPACITY: 3,500KW
West Gosford based air conditioning specialist, Air Forced Air, collaborated with builder Central Real, to deliver a premium quality residential project located 100 metres from the shores of Brisbane Waters in the exclusive Central Coast suburb of Point Frederick.
A medium rise building, with six storeys above ground and split-level basement, the complex features 29 luxury units. Given the prestigious location and sale price of each unit, the design brief was to push the boundaries with specification and finishes, to create a first of its’ kind for the area. All units sold off the plan within weeks of the project launch, and, at the time, broke sales records for the Central Coast region.
The tender requirements were air conditioning in all 29 high-end units and basement mechanical services, including all the car park exhaust, lobby fresh air supply, and full mechanical package for air and services. Individual temperature control for each unit was also a requirement.
Due to the premium nature of the project, Air Forced Air specified Fujitsu General’s VRF J-IIS systems. This specification met the premium quality expectations of the build, and would provide unit owners with great operational efficiency.
Each apartment required four to five indoor units; one for each bedroom and one or two in the living area. With limited space above the wardrobes, the Fujitsu slim-line bulkhead (ARXK) units were easier to install. These mini ducts feature drain pumps which made them ideal for this high-spec installation.
The final outdoor configuration featured 15 units on the roof and a further 14 outdoor units in the carpark. In the basement there was a garbage truck turntable, and the units were wallmounted above this, which had no impact on the available floor space. The solution was effective and the outcome positive.
“We had a large ventilated area for the garbage truck to enter, so the units in the car park were able to be hidden,” said Greg Marks from Central Real. “This hasn’t presented any issues with noise, or ventilation. There has been no negative feedback and the installation was defect-free, which is evidence of the quality of the skills provided by Air Forced Air, and the Fujitsu system.”
Fujitsu General’s inhouse project engineers worked with Air Forced Air to provide selection data, system design and efficiency ratings for the Marina Apartments specification.
This was a project that required a system that delivered above and beyond standard performance. The Fujitsu General VRF system enabled these high expectations to be achieved.
OUTDOOR UNITS:
26 AJT040
1 AJT045
2
“…the installation was defect-free, which is evidence of the quality of the skills provided by Air Forced Air, and the Fujitsu system.” - Greg Marks, Central Real
The Yorkshire Brewery’s brew tower stood as one of Melbourne’s tallest and most prominent buildings during the 19th century. And almost 140 years later it continues to survive as a symbol of Victoria’s vibrant brewing history.
Located in the inner northern suburb of Collingwood –the centre of Victoria’s brewery industry for over a century – the Yorkshire Brewery was established by John Wood in 1858 on a two acre site on Wellington Street.
Wood originally operated from a timber building before his son James – an engineer and architect – developed plans for the site, including the brickwork tower in 1875. A year later, the foundation stone was laid and the site soon included the tower, a cellar, stables for over 20 horses, and a 205 foot-high chimney stack.
By 1888 at the Melbourne Exhibition, the brewery was winning awards for its ale and port, and it would become one of Melbourne’s largest brewing enterprises. Its ownership changed over the ensuing years before Carlton & United Breweries (CUB) purchased it in 1909 as a standby plant for the nearby Victoria Brewery.
In 1954, the brewery was adapted to become the Yorkshire Malthouse with large silos erected on the site. Then in the late 1980s the site was recognised for its historical significance leading to it a National Trust classification in 1990.
After the site was sold by CUB, it remained unoccupied and derelict until it was finally redeveloped in 2014 to create 336 apartments and a further 20 townhouses.
SMA Project’s Yorkshire Brewery development has not only renewed the site to make better use of its much sought-after location, but also provided a sensitive restoration of the historic buildings to protect them for decades to come. SITE
YORKSHIRE BREWERY
BUILDER/CONTRACTOR
ICON CONSTRUCTIONS (AUST) PTY LTD
DEVELOPER SMA PROJECTS
PROJECT TIMELINE 2013-2015
“Being a Green Star project, one of the reasons for the selection of the Fujitsu models was their Human Sensor technology.”
– Andrew Stewart, Managing Director, Rival Air
Developed by SMA Projects, the Yorkshire Brewery project was designed by local architectural firm Hayball, with Icon Constructions engaged as head contractor. Hayball’s architectural approach was anchored by historic restoration and adaptive reuse of the site, “coupled with exceptional design quality, residential amenity and public open space.”
Construction on the Yorkshire Brewery site began in 2013, with the development incorporating a mix of residential dwellings.
The historic brew tower, features 5 loft-style apartments across eight levels. Three new apartment buildings were added to the site – The Mill, The Yorkshire and the Silos - with the latter two offering 278 apartments across 17 and 14 levels respectively.
In April 2014, local HVAC contractor Rival Air received a brief from Icon Constructions to design and install a quality air conditioning and mechanical services solutions based on the design by consulting engineer, Lucid Consulting.
“We were engaged to prepare a price based on a D&C (design and construct) contract,” says Rival Air’s Managing Director, Andrew Stewart.
As such, Rival Air reworked the original HVAC design to achieve efficient product sizing and selection.
This led to the selection of split systems from Fujitsu’s popular Inverter range that provides the apartments with energy efficient heating and cooling, whilst meeting the aesthetic ambitions of the development.
Most apartments within the new buildings are conditioned by wall-mounted units served by balcony-mounted condensers. But where owners elected to upgrade to a multi system at the time of purchase, Fujitsu’s range of compact outdoor units also met the exterior aesthetic aspirations of the project.
“Fujitsu’s balcony-mounted condensers offer a very compact multi-system,” says Stewart. “Normally in a multi, they are a double fan and therefore a higher unit. But Fujitsu has developed a low-profile unit specifically for balcony mounting so that it doesn’t protrude above a balcony height.”
“In fact, all of Fujitsu’s balcony-mounted units are very compact and quiet, so for us they were a very easy selection.”
The ground floor of the Brew Tower is conditioned by a Fujitsu J-IIS 12.1kW system. This model was selected for its compact profile, high seasonal efficiency and flexible piping design that allows for a total refrigerant piping length of up to 80m. As a result, the outdoor unit serving the space is located in the basement plant room.
Naturally, the project’s environmental aspirations, including the 5 star Green Star target, was also front-of-mind during Rival Air’s product selection process.
The Fujitsu models used throughout the Yorkshire Brewery project include a number of product features to deliver energy efficient performance including DC twin rotary compressor technology, DC inverter control and DC fan motor technology.
The indoor units also offer “quiet” operation with an air flow mode that can be set in four steps, with more settings possible.
But it was another feature that cemented Rival Air’s selection decision. “Being a Green Star project, one of the reasons for the selection of the Fujitsu models was their Human Sensor technology,” says Stewart. Human Sensor Technology detects movement within the room, reducing energy use by switching to energy saving mode when no movement is detected in the room after 20 minutes.
The decision to select the Fujitsu range was also made easier due to the long pipe runs the products accommodate.
This was particularly important when it came to the design of the heritage Brew Tower and Stables buildings, where outdoor units were required to be located in the basement plant room.
Rival Air’s previous experience using Fujitsu product on other projects was also telling. And despite the heritage aspects of the project – which on the surface would appear to have made installation difficult – Stewart says they did not affect the air conditioning design or installation.
“We were quite lucky. Everything was remotely located and we weren’t required to punch holes or anything like that because you could work within the internal fit outs.”
Given the compact nature of the construction site, the narrow access roads and the ambitious project timeline, the Yorkshire Brewery project encountered a number of scheduling challenges across the construction period.
Normally, this would create a financial and logistical imposition on the mechanical contractor but Stewart says Fujitsu were always very flexible. “The scheduling of this project was demanding, and Fujitsu were very good with stock availability and delivery in this regard.”
To this end, Stewart says it is not uncommon for such developments to encounter scheduling challenges and equipment suppliers need to recognise the flow on effects are often outside the control of their installing contractors.
“Some things experience delays, and some things speed up from original scheduling so it’s important to fit the flexibility of the building industry,” he says. “To have a supplier like Fujitsu able to meet this flexibility gives you great confidence.”
PRODUCT OVERVIEW
PRODUCTS:
391 INDOOR UNITS
358 OUTDOOR UNITS
1 J-IIS SYSTEM
TOTAL SYSTEM CAPACITY: 1,833KW
MECHANICAL SERVICES
CONSULTANT
PEAK CONSULTANTS
PTY LTD
MECHANICAL SERVICES
CONTRACTOR
HALLINAN REFRIGERATION
BUILDING DESIGN
TEAKLE & LALOR PROJECT
“Particularly emphasis was placed on locating equipment within the ceiling space so that it could be easily serviced from ground level through access panels in the grid ceiling.” - Kim Cramer, Peak Consultants
In 1998, the Combined Universities Centre for Rural Health (CUCRH) was established as one of eleven University Departments of Rural Health (UDRH) across Australia and is supported by the University of Western Australia.
As the state’s only UDRH, the centre – now known as the WA Centre for Rural Health or WACRH – continues to actively improve rural, remote and Aboriginal health by promoting rural health careers, creating rural-based placements for undergraduate and higher degree students and providing education, training and support relevant to rural and remote practice.
Additionally, it undertakes collaborative research and knowledge translation with a particular focus on Aboriginal, public and population health and service delivery.
Based in the coastal town of Geraldton, the WACRH building has become locally known as the “A-frame on the hill” since it was built in 2000.
While it served the centre well for over a decade, a combination of Commonwealth and State government funding allowed for a multi-million dollar redevelopment in 2013, which saw the addition of a two-storey extension to its eastern wing to accommodate a new education and simulation centre.
The EdSim Centre is a purpose-built facility that provides students and professionals with clinical education and training in a simulated environment.
The extension included five customisable consulting rooms and two clinical demonstration Emergency Department bays, as well as education staff offices and student desks.
Local Geraldton-based engineering consultant, Peak Consultants was approached by the project’s design drafting consultants Teakle & Lalor to design the mechanical services systems for the new facility. Local HVAC contractor Hallinan Refrigeration and Airconditioning was subsequently engaged to supply and install the air conditioning systems.
As well as achieve a comfortable indoor environment within the centre, Peak Consultants’ brief was to provide an energy efficient mechanical services system that allowed for flexibility in operation due to the varying occupancy levels in the facility.
“Fujitsu VRF heat recovery systems were specified because they offer the capacity flexibility to deal with variances in load brought about by varying occupancy levels” said Peak Consultants’ Kim Cramer.
“Due to the rural nature of the facility, staff are often away for extended periods. With Fujitsu VRF systems, unoccupied rooms are not conditioned, saving on running costs”.
Additionally, intuitive end-user control that gave occupants of individual offices control of their own comfort levels without affecting the comfort of other occupants was desired. As it is a mixed use building combining offices, consulting rooms, meeting rooms and a practical lecture area, it was important to provide adequate temperature control as required for each area depending on individual requirements and room occupancy.
The multi-use nature of the facility combined with the building fabric presented a number of design and installation challenges.
For instance, the existing ceiling grids placed restrictions on the system layout and design. This required a careful approach to equipment selection and installation due to a lack of adequate ceiling space and complex timber truss layouts.
“The project footprint included an existing singlestorey building which was significantly renovated, and a second storey fitted,” said Cramer. “The lower storey had very tight ceiling spaces utilising the existing truss structure, and this did not allow space for ducted fan coil units and air distribution”.
Another challenge that impacted on system design and equipment selection was Geraldton’s climate. In summer, temperatures have been known to reach 47°C with the average number of days above 30°C exceeding 80 across the year. Conversely, winter temperatures can occasionally fall to around 0°C.
To overcome these challenges, Peak Consultants sought technical and product assistance from Fujitsu General’s technical team during the design phase.
“The local commercial team at the Fujitsu WA office worked with the Peak design team to optimise the equipment selection for the design” said Cramer. “This was particularly important in determining what diversity factor to allow for.”
Cramer says that diversity is the difference in the capacity of the condensing units in a VRF system compared to the total connected fan coil unit capacity. Diversity is applied in the condensing unit selection on the basis that not all connected fan coil units require 100% capacity all of the time.
An advantage of Fujitsu VRF systems is that they can be selected with connected fan coil unit capacities of up to 130% of condensing unit capacity.
Based on the Peak Consultants design of a 101kW system, Hallinan Refrigeration and Airconditioning selected two Fujitsu VRF heat recovery systems and a number of cassette-type fan coil units (FCUs) which met the brief of cost-effectiveness,timely delivery, performance and functionality.
Fujitsu’s VR-II heat recovery systems were ideal for the multi-use nature of the EdSim Centre as they are able to provide simultaneous cooling and heating operation in multiple rooms or spaces fitted with individual indoor units.
For example, while heating might be required in staff offices and students desk areas, cooling might at the same time be required in the practical simulation spaces where occupancy rates are higher and students are engaged in physical activity.
This functionality also delivers high levels of energy efficiency, as the VR-II heat recovery systems are able to draw heat from the room to be cooled and transfer it as energy for rooms that are to be heated.
When multiple outdoor units are connected, as was the case at the WACRH, a sophisticated operation is performed by each compressor so that all compressors operate at part load and
“Due to the rural nature of the facility, staff are often away for extended periods. With Fujitsu VRF systems, unoccupied rooms are not conditioned, saving on running costs.” - Kim Cramer, Peak Consultants
distribute refrigerant to all of the heat exchangers, improving overall system efficiency.
The restrictions created by the ceiling grids, and available ceiling space and truss position, dictated the of the use of twelve Fujitsu compact cassette and mini cassette units with outside air provision for offices, consulting rooms, meeting and training rooms.
These units feature a high efficiency design with a two-stage turbo fan and spread air distribution across the heat exchanger evenly to produce two separate and quiet airflow streams. This made them ideal for the office and lecture spaces within the EdSim Centre.
“Particularly emphasis was placed on locating equipment within the ceiling space so that it could be easily serviced from ground level through access panels in the grid ceiling,” said Cramer.
A further nine standard cassette units were also deployed where space constraints did not exist.
According to Hallinan Refrigeration and Airconditioning, Fujitsu VR-II and cassette units were also selected based on the simple process for interlocking the indoor units with outside air fans and motion sensors to provide a high level of user control and greater energy efficiency.
Due to the facility’s coastal location, Peak Consultants specified that the condensing units be positioned on the protected side of the building. Anti-corrosion coil treatments were also specified.
System control is provided to WACRH staff members via an intuitive touch-screen central control unit. With easy finger touch operation via high resolution TFT-LCD panel, it allows users to easily manage the temperature of specific rooms and spaces, as well as distribute heating and cooling to different rooms simultaneously via individual control of the indoor units that can each be named.
This system can be accessed remotely or over a network via the VRF Explorer PC interface which provides a wide range of controls including energy saving management, indoor and outdoor unit control and peak cut operation.
According to both the consultant and contractor, the support provided by the Fujitsu technical department throughout the design and commissioning phases of the project had a major influence on the selection of Fujitsu products for the WACRH project.
Additionally, the extended warranty terms offered by Fujitsu General on its commercial range was considered important, particularly since not all manufacturers offer such terms.
Construction of the Western Australia Centre of Rural Health’s EdSim facility was completed early 2014, and was officially opened by dignitaries in April 2014.
According to Cramer, the building has since performed as designed in both summer and winter.
“The last two summers have been unseasonably hot and the equipment has proved to be reliable and energy efficient in operation,” Cramer said.
PRODUCTS:
2 VR-II HEAT RECOVERY SYSTEMS
9 CASSETTE UNITS
12 COMPACT CASSETTE UNITS
1 TOUCH PANEL CONTROLLER
2 NETWORK CONVERTORS
21 WIRED RC TOUCH CONTROLLERS
21 GRILLE KITS
19 SEPARATION TUBES
4 OUTDOOR UNIT BRANCH KITS
21 RB UNITS
QUANTITY OF OUTDOOR UNITS: 8
QUANTITY OF INDOOR UNITS: 25
TOTAL SYSTEM CAPACITY: 101KW
The air conditioning systems have since operated as designed to optimum levels, and will continue to contribute to a modern learning environment that is sure to benefit students for many years to come.
With Sydney’s population set to hit 6 million by 2036, the population growth in the western and south-western suburbs of Sydney is amongst the highest in Australia.
This continued high growth naturally places pressure on existing infrastructure, including schools. For example, a high school in this region that originally opened in 1958 now receives an average of 1400 enrolments annually.
However this growth in student enrolments had outstripped the development of the school’s facilities until a multi-million dollar upgrade program began in 2010.
This program has since seen the construction of a new building including 10 classrooms, the refurbishment of classrooms for science, visual arts and intensive English, and a new school administration block.
This new administration block replaces the previous outdated administration building that lacked modern facilities such as air conditioning. The new building features dedicated offices for senior staff, interview meeting rooms and a general reception area for students.
Charged with the task of delivering a comfortable indoor environment in the new building, Donnelley Constructions and HVAC Systems were engaged to design and install an air conditioning system for the
building, as well as install new wall-mounted split systems in another building.
Research has shown that the indoor environmental quality of an educational facility plays an important role in the productivity and learning ability of students.
Higher airflow rates and cooler temperatures have been shown to improve learning and information
Fujitsu’s ability to provide a product solution that met the key requirements of easy control, performance and affordability was an important factor in their selection by HVAC systems.
retention, and this is particularly important through the summer and early autumn months in western Sydney when temperatures are at their highest. During summer, temperatures in this region average around 28°C with the average minimum temperature around 18°C.
Without an effective air conditioning system for classrooms and learning spaces, high internal temperatures can have a negative effect on a student’s ability to focus and retain information. Educational facilities also require HVAC systems that are simple to operate, and in this case it was also imperative that the controller be centrally located to effectively manage temperature control and distribution of conditioned air to spaces as required.
This energy efficiency measure also ensures that air conditioning is switched off when rooms are not in use, which in turn reduces system load and energy costs.
To meet these requirements, HVAC Systems selected three Fujitsu General Airstage V-II Series variable refrigerant flow (VRF) systems with a combined capacity of 89.8kW.
These were teamed with seven indoor cassettes, three high-static and three medium-static pressure duct units, and two slim duct units.
Fujitsu’s ability to provide a product solution that met the key requirements of easy control, performance and affordability was an important factor in their selection by HVAC Systems.
The Airstage V-II Series system features a smart, cutting-edge design that offers excellent energy savings via its heat pump type inverter control. A high Energy Efficiency Ratio (EER) is realised due to the unique, 4-face heat exchanger structure and a highly efficient DC twin compressor that substantially increases refrigerant intake while delivering compression efficiency.
The high static pressure design flexibility offered by this system also allows the three outdoor units to comfortably service fifteen indoor units across the building.
Although a number of these were located on the furthest side of the building from the outdoor heat pumps, Donnelley Constructions was able to overcome this challenge due to the system’s ability to accommodate long pipe runs.
In addition to the system serving the new administration building, two Fujitsu 5kW wallmounted split system units were selected and installed to provide air conditioning in a separate building.
While these systems were able to fully satisfy the requirements of the brief, HVAC Systems said this project was made easy by the on-time delivery of equipment in good condition, and the technical support offered by Fujitsu to ensure the solution operates at optimum levels.
In selecting a reputable brand that offered a strong service solution, the end-to-end customer service experience was valued by both HVAC Systems and Donnelley Constructions on this project.
Construction of the new administration building completed in early 2015 ahead of the start of the school year, and was officially opened by government dignitaries in June 2015.
The air conditioning systems have since operated as designed to optimum levels, and will continue to contribute to a modern learning environment that is sure to benefit students for many years to come.
PRODUCT OVERVIEW
PRODUCTS:
8 INDOOR CASSETTES
3 HIGH STATIC DUCTED UNITS
3 MID STATIC DUCTED UNITS
1 SLIM DUCT UNITS
2 WALL MOUNTED SPLIT SYSTEMS
3 V-II SERIES HEAT PUMPS
16 CONTROLLERS
QUANTITY OF OUTDOOR UNITS: 3
QUANTITY OF INDOOR UNITS: 17
TOTAL SYSTEM CAPACITY:
89.8KW VRF AND 10KW SPLIT SYSTEMS
“Service is the most important element for us in this industry, which is why it was important to leverage our good relationship with Fujitsu General to ensure this project would receive the best products and services for the best value."
– Leon Li, Mechanical Engineer atEpic Air
Community provider Anglicare had plans to develop a residential aged care facility in Dapto to help meet the need for seniors’ accommodation in the Illawarra region of NSW.
The proposed development would be delivered in two stages. The first stage included a residential care home, while the second stage included community and recreational facilities.
This two-storey building includes a 111-bed residential aged care facility, 23 additional serviced self-care dwellings and several community/ancillary spaces comprising a care centre, activities room, café, and kitchen facilities with a cool room.
Epic Air was the air conditioning contractor for the entire development, which included individual heating, cooling and air flow requirements for all residents as well as the community amenities.
Anglicare and the development team wanted to ensure the air conditioning system installed was
not only cost effective but could also be easily maintained with a reliable and effective service program. Fujitsu General was selected through a tender process as it offered a superior solution that met the project’s HVAC priorities.
Every air conditioning unit, from the systems cooling the community spaces to the individual residential units, required a direct power cable connection to ensure efficient operation. However, due to the facility’s size a 2,000 metre cable was required to connect all the units to the centralised controllers. This challenged the system’s ability to operate to optimum capability, as cables longer than 500 metres often struggle to provide strong or reliable energy signals.
The 2,000 metre cable was essential to ensure the entire system was connected, so to overcome this challenge, Fujitsu General’s technical team consulted with Epic Air to install a network amplifier with a 12-port branch box that would maintain strong and even power distribution and prevent overheating and malfunction.
SITE
ANGLICARE, DAPTO, NSW
CLIENT/PROJECT MANAGER
ANGLICARE / EPIC AIR
PROJECT TIMELINE 2021
Across the development 111 ARXK012GLEH VRF compact slim duct bulk heads with drain pumps were installed in the residential rooms, divided across three concealed static ducted systems. To prevent high heat concentration in a single area, 24 VR-II heat recovery units were evenly placed around the site. The main building, which houses a conference room, was fitted with a high static split system that could deliver the high capacity required to cool or heat the entire area.
Epic Air and Fujitsu General successfully installed heating and cooling systems across multiple buildings that needed to cater to multiple needs, from residential home comfort to kitchen cooling and the temperature management for communal recreation spaces. Thanks to the successful installation, Anglicare can provide accommodation, wellbeing, and care services to meet the needs of a rapidly ageing population in and around Dapto.
PRODUCT OVERVIEW
PRODUCTS:
AJTA90GALH 28.0KW VRF VR-II SERIES HEAT RECOVERY OUTDOOR
AJT306GBLH 95KW VRF VR-II SERIES SPACE SAVING
AJT288GBLH 90KW VRF VR-II SERIES SPACE SAVING
AJT198GALH 62KW VRF VR-II SERIES HEAT RECOVERY SPACE SAVING
AJT108GALH 33.5KW VRF VR-II SERIES HEAT RECOVERY OUTDOOR
AJT324GBLH 100.5KW VRF VR-II SERIES SPACE SAVING
AOTG18LVCC 5.0KW INVERTER WALL HUNG OUTDOOR
ARXA030GLEH VRF MEDIUM STATIC PRESSURE DUCT INDOOR
ARXK012GLEH VRF COMPACT SLIM DUCT WITH DRAIN PUMP INDOOR
ARXC60GATH 18KW VRF VR-II SERIES HIGH ESP DUCTED INDOOR
ARXA036GLEH VRF MEDIUM STATIC PRESSURE DUCT INDOOR
ARXA024GLEH VRF MEDIUM STATIC PRESSURE DUCT INDOOR
ARXA045GLEH VRF MEDIUM STATIC PRESSURE DUCT INDOOR
ARXC096GTEH VRF HIGH STATIC PRESSURE DUCT INDOOR
ASTG18LVCC 5.0KW INVERTER WALL HUNG INDOOR
QUANTITY OF OUTDOOR UNITS: 24 VRF HEAT RECOVERY
QUANTITY OF INDOOR UNITS: 159
TOTAL SYSTEM CAPACITY: 772KW
Applied Air Services, an air conditioning specialist based in the Brisbane suburb of Geebung, commenced work on Lotus Tower in March 2019. A luxury villas apartment and penthouse development, Lotus Tower is located in the highly sought-after suburb of Kangaroo Point.
The complex features an extensive range of residential amenities including a rooftop sun deck and spa, swimming pool, dedicated yoga space, a golf simulator and children’s play areas, as well as high-end residential villa-style apartments, penthouses and townhouses.
The 24 storey Lotus Tower complex consists of four levels of basement and 19 levels of apartments, with level 20 the penthouse floor. There are an additional 12 townhouses detached from the main tower. Common areas within the precinct include a gym, golf simulator, reception and private dining area.
Applied Air Services was required to meet the individual heating, cooling and air flow requirements of all residential and commercial tenancy, as well as the building’s shared amenities.
Managing power allocation for each tenancy was a requirement of the chosen HVAC system. The Fujitsu General VRF solution enabled this to be implemented due to its power apportioning feature. All the Lotus Tower indoor units are powered from a local distribution point from the apartment, and the building has watt hour meters, monitoring the power used for all the outdoor units. Software converts power meter usage into a percentage for each tenant.
The Lotus Tower project required the installation of 54 outdoor units and 533 indoor units. During installation not one of them had a fault, error or gas leak which is a testament to the quality of the product and the installation quality.
With power apportioning managing the systems energy usage, the building management can extract reports regarding the allocation of energy usage to understand where there is wastage, and where savings can be made.
A Fujitsu General ducted air conditioning system was installed in each townhouse, providing zone control and individual system management.
A Fujitsu General VRF heat recovery system was installed in the main tower. Applied Air used bulkhead fan coil units connected to multiple RB units located in the corridor. The bulkhead fan coil units were chosen for the compact size and internal drain pumps.
The basement received CO (carbon monoxide) controlled ventilation which allows system sensors to level the CO produced by vehicles in the basement and operates ventilation fans to reduce the amount of CO, a new standard practice in the industry.
“Fujitsu was the preferred choice over competitors with its five-year warranty as standard. I also have peace of mind with securing manufacturer parts and labour warranty.” Jeff Mann, Applied Air Services.
TUBES:
TUBES
APPLICATION
STUDENT APARTMENT
ACCOMMODATION
SITE
UNILODGE CITY
GARDENS
ADELAIDE SA
CLIENT/PROJECT
MANAGER
SYNERGY CONSTRUCT
O.P. INDUSTRIES (SA)
PROJECT
Adelaide based air conditioning specialist, O.P. Industries, worked with commercial property developer Synergy Construct, to deliver a modern and sustainable student accommodation project. UniLodge is located on the west side of the Adelaide CBD, next to the University of South Australia’s City West campus and within walking distance from the University of Adelaide.
A high-rise student accommodation building, with 16 floors above ground, it features 772 apartments with shared kitchen, dining and games spaces on the ground floor. The building makes a design impact with a 1,764 square metre living green wall, the largest of its kind in Adelaide.
The tender required air conditioning in all 772 units as well as large common areas, and a full mechanical package for air and services. Originally, the brief was to provide a VRF Heat Recovery system for the whole building, however this was later found to be outside the budget.
According to Wayne Russell, Project Manager at O.P. Industries, “The developer tasked the build team with sourcing an economically efficient system that conformed to the performance and warranty requirements of the project. We recommended the VRF Heat Pump system for the apartments which provided significant value for money benefit. The performance of both systems is identical, the heating and cooling temperature set points are exactly the same, the difference lies in the way you work the units themselves.”
In a heat recovery system, individual fan coils can heat or cool simultaneously. With a heat pump system, all air conditioners in this system either heat or cool only. This is determined by one unit which has a master control, likely to be controlled by the building manager.
A VRF Heat Recovery system was still utilised for the ground floor, as larger units were needed to control the temperature of the spacious common areas.
The main challenge of this project was limited space. The unprecedented number of units in the building meant there was restricted roof space to fit the condensers.
According to the installer, in comparison to a standard residential apartment building, the UniLodge project was considerably large, with more than 800 individual units installed across the entire building.
O.P. Industries and Fujitsu General were also faced with tight delivery schedules.
“We had a very tight schedule for commissioning equipment and were concerned we would not be able to meet the four to six week turn-around. The standard time allowance for a project this size is normally eight to ten weeks. Luckily, Fujitsu’s commissioning team had the manpower to commission and deliver the products in the limited time frame without any delays,” said Wayne.
Managing the heat load of the building also posed a challenge to O.P. Industries and Fujitsu General. As a high-rise structure, certain sides of the building were impacted more by direct heat from the sun, so they required larger units in these areas for more efficient cooling.
Installing a heat pump system rather than a heat recovery system reduced the number of condensers, allowing more room on the roof.
“We were one of the first companies in Adelaide to use the J-IIIL unit to meet the refrigerant charge. This required fewer condensers, making it easier for us to space them out. The Fujitsu General engineering team helped considerably with the design. They worked with refrigerant volumes and condenser locations to try to minimise the amount of pipe and labour used on the project.” commented Wayne.
Fujitsu General’s VRF Heat Pump and Heat Recovery systems went above and beyond the client’s requirements to provide efficiency and cost saving. These products helped to improve the sustainability of the building, as the internal settings and compressors of Fujitsu General’s new J-IIIL condenser use less power, making it more energy efficient.
Fujitsu General’s inhouse project engineers worked with O.P. Industries to provide selection data, system design and efficiency ratings for the Unilodge specification. This project required a costeffective solution that could deliver exceptional performance across the entire apartment block. The Fujitsu General VRF Heat Pump system and VRF Heat Recovery system were able to meet the requirements for efficient heating and cooling in both common areas and the large number of individual apartments.
OUTDOOR UNITS:
4 J-IIS, 31 J-III, 54 J-IIIL, 2 V3, 5 VR-II, 3 LFCC WALL MOUNTED, 1 LHTA HIGH STATIC DUCTED
INDOOR UNITS: 823 ASYA, 3 AUXA, 3 AUXD, 3 AUXB, 5 ARXC, 1 ARXA, 3 ASTG, 1 ARTG
QTY OF OUTDOOR UNITS: 100
QTY OF INDOOR UNITS: 842
TOTAL SYSTEM CAPACITY: 2,069.8KW
After 10 years in Eastern Creek, Fujitsu General Australia had outgrown its head office premises. Landlord Jacfin Pty Ltd offered to develop a bespoke building and separate distribution centre. The new design set out to be a 5-star Green Star energy building in the commercial precinct of Eastern Creek, offering employees and visitors a unique experience, and demonstrating sustainable building and interior fit-out practices.
It was also an opportunity for Fujitsu General to be part of the entire design process, including the specification of the HVAC solution, which it had been unable to do with the previous location.
Working in close consultation with Fujitsu General, the new headquarters was designed from the ground up to deliver a work environment that would meet the needs of the organisation for the next 20 years, both functionally and culturally.
Prior to construction, employee feedback on the new design was encouraged. The result was an 11,093 sqm state-of-art, open plan office with collaborative working spaces, the latest sit/stand desks, natural light throughout, wellbeing spaces, and fun zone.
Officially opened in May 2019, the new headquarters also includes an on-site gymnasium, auditorium, outside green areas, covered carpark, modern indoor kitchen facilities, and outdoor lunch and barbeque facilities, as well as an 8,500 sqm distribution centre.
A Fujitsu General VRF Heat Recovery system was installed, including a combination of ducted indoor units for meeting rooms and offices where individual comfort and control was required. The open plan office is serviced by high static ducted indoor units which are concealed and allow for flexible installation when ducts are installed.
The system has a focus on higher capacities and airflows to meet the requirements of the building with quiet operation designed to use electricity efficiently and effectively.
To minimise human involvement and optimise office space comfort, VRF Heat Recovery outdoor units were installed which are ideal for large facilities such as commercial offices.
The heat recovery operation allows for simultaneous cooling and heating for individual indoor units in rooms with large temperature variances. With remote temperature sensors giving feedback to the indoor units, the Single Port and 4 Port Refrigerant Branch units provide comfort in each zone all day long.
Central control systems were also installed to provide smart energy management across the premises. Energy saving technology helped achieve the building’s green credentials, with the use of operation timers for set times and seasons.
On top of individual control, all meeting room units have an Auto Off timer feature activated on the controller. This means when a unit is turned on, it will run for a set period of time before turning off automatically. This feature ensures that the units are not left running in unoccupied areas of the building unnecessarily during work hours.
A BACnet Gateway has allowed the units to be connected to the buildings BACnet Building Management System allowing high level control of the units along with the other items on the site under the control of the BACnet BMS.
Fujitsu’s UTY-DTGYZ1 Touch Panel Controller allows control of the units from a central location on site with the unit’s individual controllers available for day to day adjustment in line with limitations which has been set from the High-Level Building Controls.
In partnership with Jacfin Pty Ltd, Fujitsu General Australia facilitated the development of a worldclass working environment. The building design enables the business to be energy efficient and help minimise its environmental footprint through the inclusion of timber and modern materials, as well as plants with a reticulating irrigation system. Solar energy is captured via 365 roof panels, and rainwater is recycled for toilets, and irrigation of green walls.
The new headquarters and distribution centre received the 2019 NSW Master Builders Association award for ‘Excellence in Construction of Industrial Buildings $10 million – $25 million’.
Successfully stepping from couture to accommodation, Australian designer Alex Perry has leant both his name and style to a hotel and residential apartment complex in Brisbane’s fashionable Fortitude Valley.
As Creative Director of the Alex Perry Hotel and Apartments, the acclaimed designer’s style is evident in the classic yet edgy design that blends modern technology with friendly service only 1.5km from Brisbane’s CBD.
The complex offers a total of 143 apartments across 11 levels, including studio hotel rooms and one and two bedroom apartments suited to both the corporate and leisure traveler.
Studio rooms, providing approximately 47m² of space, are located on levels one to five of the complex and offer the convenience of a hotel room with the in-room services of an apartment.
The light-filled one and two bedroom executive apartments, offering approximately 57m² and 72m² of space respectively, each feature a self-catering kitchen with European appliances, laundry, separate bedroom/s with opening windows, and balcony.
Other amenities include the Manhattan-style lobby, gymnasium, outdoor heated swimming pool, rooftop recreation area, sundeck and BBQ area for guests.
Given the high-end accommodation on offer at the Alex Perry Hotel and Apartments, a quality air conditioning and ventilation solution was sought by both the developer and designer.
Following full documentation of the mechanical services design by the project’s consulting engineer, Brisbane-based Energy Air were engaged on the project as mechanical services contractor on a design and construct basis in 2014.
According to Energy Air’s Mechanical Engineer, Kim Stephens, the original mechanical services design was completed in 2010 to meet the requirements of the 2009 version of the Building Code of Australia (BCA).
For the 44 two-bedroom apartments, Fujitsu’s J-II Series VRF (variable refrigerant flow) units were ideal. These systems provide individually zoned and controlled air conditioning between living areas and bedrooms.
This led to an alternative design solution being developed during tender negotiations, in collaboration with the construction team, to meet the updated building code. This also provided an opportunity to redesign the basement car park ventilation to meet AS 1668.2 2012 requirements.
“Our brief was to use the same design intent prepared by the original consultant, but also provide value-engineered solutions to improve the constructability of the project,” says Stephens.
With the original design well documented, Stephens said items like riser sizes for ducts and piped required efficient solutions.
But the real challenges were around coordination with other trades, whilst maintaining an efficient design approach.
After The original design documentation specified a range of Fujitsu units to be used, but like every good contractor Energy Air went to the market once design checks had been confirmed.
Ultimately, they returned to the Fujitsu product.
“One of the reasons was that Fujitsu were the best priced, partly because of the rated capacity of their 8kW slim-line ducted inverter,” says Stephens. “Competitors had to use 10kW units which were more expensive.”
Another important factor in selecting Fujitsu equipment was the length of pipe run desired – a common requirement in multi-rise residential and hotel developments.
“Some competitors could not do the 50m pipe run that Fujitsu offered,” says Stephens.
Fujitsu’s renowned pre-sales support was also an important factor to the success of the project, particularly during the design phase.
“Throughout the design stage I sent drawing files to Fujitsu for comment and approval, and at all times they offered the necessary advice and changes or approvals as required to comply with Fujitsu specifications.”
Although the original design intent was to locate as many condenser units as possible on the roof, some of the pipe runs required exceeded even those offered by the Fujitsu equipment, and required additional design work.
The result was the creation of two plant rooms to house the remaining units – one at ground level and another on the mezzanine level.
“To use another equipment supplier would have meant fewer units on the roof, and more units on the ground and mezzanine floor plant rooms which would have required additional platforms to be built,” says Stephens. “Plus the additional plant would have generated more noise.”
As well as maintaining conditions within the rooms, other important mechanical services design criteria that led to the selection of Fujitsu products included
a requirement to maximise the height of the apartment ceilings.
Individual control (including zone control in the apartments), and billing was also a prerequisite.
To meet these objectives, Fujitsu’s ART Series slimline ducted inverter units were selected for the studio and one bedroom apartments.
“These are great units for apartments as they are only 270mm high and have four 200mm spigots at the front of the indoor unit for running flexible duct to reticulate the air to the registers,” Stephens says.
“In the past, we have tried putting hard duct on the front of the units but with all the other services competing for ceiling space, hard duct was too restrictive. If this didn’t fit, nothing would.”
For the 44 two bedroom apartments, Fujitsu’s J-II Series VRF (variable refrigerant flow) units were ideal. As well as the indoor unit offering an unobtrusive low profile, these systems provide individually zoned and controlled air conditioning between living areas and bedrooms.
The J-II Series offer high seasonal efficiency thanks to the large capacity DC Scroll compressor and 3-row heat exchanger. The units’ advanced refrigerant control technology also allows the longer total refrigerant pipe lengths required on this project.
The total combined capacity of the Fujitsu systems installed at Alex Perry Hotel and Apartments is approximately 1428kW.
Construction of the Alex Perry Hotel and Apartments was completed in mid-2015 and officially opened to guests in October 2015.
According to Energy Air, the Fujitsu equipment used here has performed without issue since commissioning.
“Alex Perry Hotel and Apartments was a job that perfectly suited the Fujitsu equipment,” says Stephens.
PRODUCTS:
44 J-II SERIES HEAT PUMP OUTDOOR UNITS
132 INDOOR UNITS
106 STANDARD PRODUCT SYSTEMS
TOTAL SYSTEM CAPACITY: 1,439KW
Given the high-end accommodation on offer at the Alex Perry Hotel and Apartments, a quality air conditioning and ventilation solution was sought by both the developer and designer.
Fujitsu’s extensive range of products adapted to the project and it’s limitations with ease.
The $14.5 million redevelopment of Newcastle Airport’s terminal has been enhanced by the addition of the new Mercure Williamtown hotel within walking distance of the airport.
Offering 95 guest rooms as well as restaurant, bars, gymnasium and four conference rooms that cater up to 120 people, the 4-star hotel has proved popular to both business and leisure travelers alike since it opened in mid-2015.
Located just 300m from the Newcastle Airport’s domestic terminal, the hotel complements the new airport facility which includes new departure and arrivals lounges and dedicated facilities to accommodate direct international services in the future.
Local construction company GWH Build acted as the developer of the project, and was responsible for the design and construction of the four-storey, 4-star hotel.
It assembled a group of key local investors to develop the property via the Newcastle Airport Unit Trust, with a view to operating the hotel under the Mercure franchise with the support of the Accor Group.
Construction commenced in mid-June 2014, with an ambitious 12 month construction timeframe set.
Providing quality air conditioning and mechanical services to the hotel, NSW (M&H) Air Conditioning was engaged by GWH Build under a design and construct (D&C) contract in October 2014.
The HVAC installation commenced in December 2014.
According to NSW (M&H) Air Conditioning’s Martin Swift, the project brief was to provide appropriate air conditioning and ventilation to the hotel’s 95 guest rooms, commercial kitchen, restaurant and two bars, as well as conference facilities. He said while the design of the hotel meant that the installation
“These units met the brief of cost effectiveness, timely delivery, performance and functionality.”
- Martin Swift, NSW (M&H) Air Conditioning
was relatively straight forward, the time constraints placed on the entire project team created obvious challenges.
“The main consideration around the mechanical design was to ensure the equipment selected was appropriate to the area it was serving, so as to provide accurate temperature control,” Martin said.
Being a new build, few obstacles to achieving these objectives were encountered other than some limited ceiling spaces through the hotel room corridors.
Naturally, an energy efficient design was sought and equipment selection played an important role in meeting such targets.
In seeking to provide accurate temperature control across the different spaces of the hotel, NSW (M&H)
Air Conditioning sought product assistance at the initial design phase from Fujitsu General’s technical team.
This led to a system design that incorporated six Fujitsu VRF (variable refrigerant flow) VR-II Series units with heat recovery, as well as Fujitsu’s J-IIS heat pump system. Total system capacity at the hotel is 237kW.
Considered as the best products for this type of application, the VR-II Series provide simultaneous cooling and heating and are particularly suited to the lengthy pipe runs that resulted from the hotel’s low-rise design.
Fujitsu’s advanced refrigerant control technology allows for a total refrigerant piping length of up to 150m to be achieved. The VR-II Series system provides economic cooling via the system’s heat pump type inverter. A high EER (energy efficiency ratio) is realised due to the unique 4-face heat
exchanger structure and the use of a highly efficient DC twin compressor that substantially increases refrigerant intake while delivering compression efficiency.
Martin says that available space for condenser units was also a determining factor in the selection of these units. The space saving design and high seasonal efficiency of the J-Series made this unit particularly suitable on the Mercure Williamtown project. The seven outdoor units service a total of 102 individual indoor units deployed across the interior spaces of the hotel, including guest rooms.
To provide accurate temperature control in the 95 guest rooms, NSW (M&H) Air Conditioning selected Fujitsu’s ARXD bulkhead units. Their compact design made for easy installation where the space above the ceiling is narrow, while air intake direction was able to be selected to match the installation location – taken either at the bottom side or back side of the unit.
“An advantage of the Fujitsu equipment was the smaller bulkhead units serving the bedroom areas,” says Martin. “This allowed us to maintain higher ceiling heights in all areas.”
These units also provide for low noise operation, making them ideal for use in bedrooms.
To enhance the energy efficient operation of the system, all guest rooms have been fitted with room entry cards that automatically turn the system off when the card is removed and the room is left vacant.
In the hotel’s conference areas and public spaces, including restaurant, bars, gymnasium and lobby, a combination of split ducted and cassette-type fan coil units (FCUs) have been used to provide comfortable indoor conditions.
These units met the brief of cost-effectiveness, timely delivery, performance and functionality.
According to Martin, the installation process was made easy due to the support provided to NSW (M&H) Air Conditioning by the Fujitsu technical department.
“Fujitsu’s extensive range of products adapted to the project and its limitations with ease,” he says.
“The after sales service was also fantastic with the commissioning team more than helpful in the closing stages of the project.”
Fujitsu’s advanced refrigerant control technology allows for a total refrigerant piping length of up to 150m to be achieved.
Construction of the Mercure Williamtown hotel reached completion in June 2015, with the hotel open for guest bookings from August 1.
The HVAC system has performed well since the hotel’s opening.
COMPLETION DATE: JUNE 2015
APPLICATION: HOTELS
INSTALLER/CONTRACTOR: NSW (M&H) AIR CONDITIONING
PRODUCTS
6 VR-11 HEAT RECOVERY
1 J-IIS HEAT PUMP 95 SLIM DUCT
4 COMPACT CASSETTE
1 TOUCH PANEL CONTROLLER
1 WALL MOUNTED UNIT
3 DUCT - HIGH STATIC
6 CASSETTES
QUANTITY OF OUTDOOR UNITS: 7
QUANTITY OF INDOOR UNITS: 102
TOTAL SYSTEM CAPACITY: 237KW
Launched in Australia in 2002, the Fujitsu General AIRSTAGE™ Series continues to provide commercial projects with complete air conditioning solutions that deliver design and installation flexibility, optimal comfort, high energy efficiency and consistent reliability. Continually evolving to meet market requirements, the AIRSTAGE™ Series offers VRF heat pump and heat recovery systems. It is also the hero brand of our new portfolio of Applied Products.
Using the latest Japanese technology, the AIRSTAGE™ Series of VRF heat pump and heat recovery systems are developed and performance tested in Fujitsu General’s state-of-the-art facilities to ensure maximum reliability. The AIRSTAGE Series has been designed to effectively provide indoor temperature control solutions for a wide range of commercial projects including high-rise office buildings, retail outlets, hotels, public facilities, schools and hospitals.
Almost any air conditioning system design can be achieved with more than 70 outdoor model combinations and an extensive range of indoor units. The AIRSTAGE range of indoor units includes a variety of different unit types to suit most building applications, operated with a wide variety of controllers, including centralised control systems for building-wide management.
The AIRSTAGE Series is further supported with tools that allow professionals to easily design, install, maintain and service AIRSTAGE VRF solutions. This support includes a remote monitoring tool which means support, quick service and maintenance is available any time. The Mobile Technician, Fujitsu’s service support app can be used for error code checking, obtaining service instructions, troubleshooting and sensor checking information. Fujitsu General Australia strives to consistently provide high quality, energy efficient, reliable products. Fujitsu General trained technicians attend every commercial and industrial AIRSTAGE installation to assist with the controls commissioning of the units and ensure seamless operation.
The Fujitsu General AIRSTAGE™ Applied product line up includes a comprehensive range of air cooled and water cooled liquid Chillers, as well as Roof Top Packaged units, and Air Handling Units for residential, commercial, and industrial applications. Offering simple aesthetics and design flexibility, the Fujitsu General AIRSTAGE Applied range provides the latest technology and product solutions to meet the needs of Australia’s weather extremes.
The Fujitsu General AIRSTAGE Applied range of products is manufactured in Italy and Malaysia.
FUJITSU GENERAL AUSTRALIA
ABN 55 001 229 554
A subsidiary fo Fujitsu General Limited
1300 882 201
contact@fujitsugeneral.com.au
fujitsugeneral.com.au
FUJITSU GENERAL
HEAD OFFICE – NSW
1 Telopea Place Eastern Creek 2766 (02) 8822 2500
VIC / TAS
Suite 1, Building 2, Omnico Business Centre 270 Ferntree Gully Road Notting Hill VIC 3168 (03) 9543 5899
QLD
Tenancy 1.02, 371 Macarthur Avenue
Hamilton QLD 4007 (07) 3257 2800
SA / NT
128A Rose Terrace Wayville SA 5034 (08) 8172 1180
WA
Unit 1, 24 Gibberd Road
Balcatta WA 6021 (08) 9240 5877