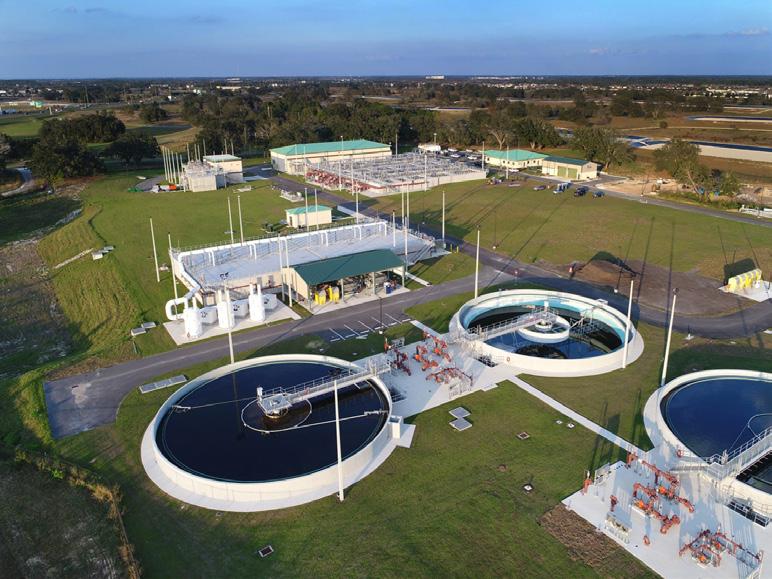
3 minute read
Constructing During a Pandemic
Drew Gumieny
Constructing a multimillion-dollar regional water treatment facility is a challenging venture in and of itself. Imagine complicating the matter with an unprecedented global pandemic, the likes of which most people haven’t witnessed in their lifetime.
Advertisement
In December 2019 Wharton-Smith Inc. received the notice to proceed on the Hamlin Water Reclamation Facility project, which would be a state-of-the-art project budgeted at more than $114,500,000 (inclusive of change requests). The design-bid-build 5-million-gallon-per-day (mgd) water treatment facility would be the next major water treatment facility for Orange County
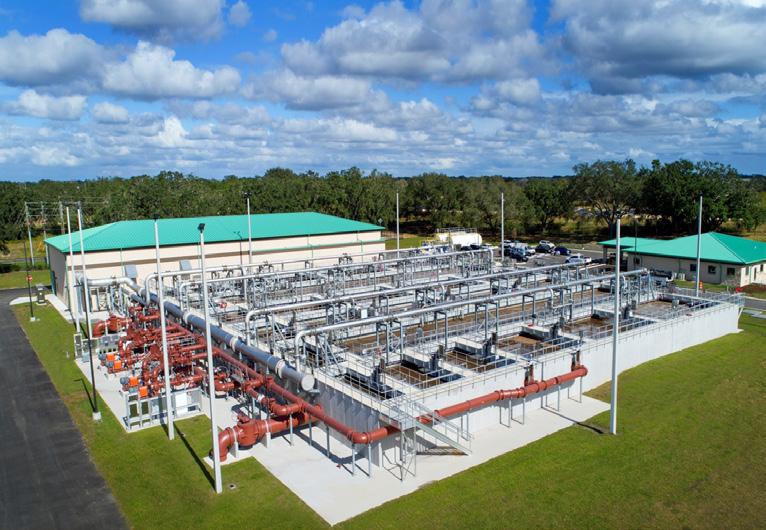
Utilities located in Winter Garden. The lead engineer of record was Arcadis, with contributions from ten subconsultants.
The Pandemic Changes the Workplace
Shortly after mobilization in January 2020, the world was hit with COVID-19 and the new pandemic culture began to change the way our global society lived and worked. March 2020 is when the construction team really began to feel the effects and challenges of the pandemic. Typical project interactions, like progress meetings, were now being hosted digitally via WebEx. In-person meetings were handled with six feet of separation while wearing masks, and construction office trailers started weekly chemical disinfecting protocols. The field office staff had to contend with outbreaks in the quadwide office trailer, causing a chain reaction of testing, isolation, and retesting for all exposed members.
Onsite protocols began to change as well. Daily temperature checks for up to 150 craftspeople became standard operating procedure, sometimes turning those away that had even slightly elevated body temperatures. Despite working outside during most of the project, crews were issued face buffs and encouraged to utilize handwashing stations that Wharton-Smith took extra measures to install.
There were times when whole crews were sick and unable to work, causing multiple delays. This added a whole new level of complexity to an already complex project.
The Challenges of Material Procurement, Pricing, and Supply Chains
As the project entered 2021, the number of those getting sick decreased, but a new set of challenges were presented to the team: the economic and logistical fallout of the pandemic. With factories shutting down in 2020, workers left their current employers in search of viable work. With little factory production and a serious labor shortage, the logistical side of the business began to suffer.
While most of the facility’s buildings and process structures were built, it became extremely difficult to get materials, such as above-grade valves, flanged piping, electrical enclosures, and wire, in a timely manner. Mutually agreed upon lead times and pricing could no longer be honored due to lack of materials, astronomical freight and shipping fees, and inflation driving up the price of goods.
To keep the project moving forward, Wharton-Smith had to find creative ways to source material and prioritize site construction activities. For example, the team had to find a new way to get flanged ductile iron pipe. This pipe required field dimensions in order to be fabricated, but the lead times grew from four weeks to 24 weeks
Utilizing relationships in the industry, the project team was able to quickly get most of the missing pipe from a small outfit in Georgia, albeit at a higher cost. Fiber optic cabling was severely delayed as production stopped in Mexico. The
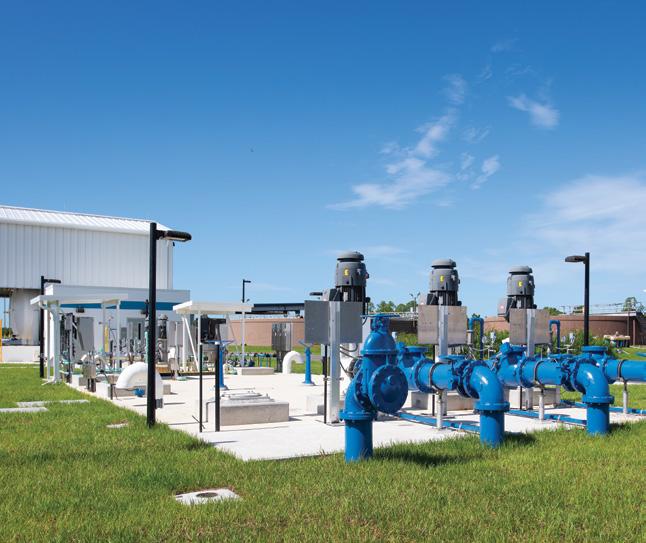
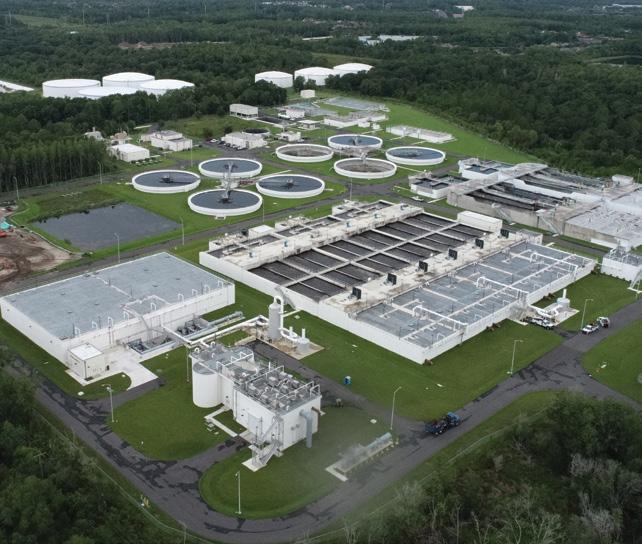
Continued from page 26 team worked closely with the owner and engineer to negotiate an “or equal” product and was able to source a more-readily-available fiber.
The job required several specialty materials, like flanged butterfly valves that take over a year to fabricate in India. With cargo ships being held stationary off the coast of Los Angeles, the actual delivery date of the valves became unknown.

The team elected to airfreight the valves to the job to keep the project moving forward. Now, more than ever before, adaptation and collaboration among contractor, owner, and engineer became the team’s signature strategy to overcome new, and ever-growing, pandemic challenges.
Here’s a glimpse into the amount of material utilized on the project:
S 24,000 cubic yards of concrete
S 2,200 tons of rebar (4.4 million pounds)
S 50,300 masonry blocks
S 5,400 linear feet of encased ductbank
S 8.5 miles of buried process piping, both ductile iron and polyvinyl chloride (PVC)

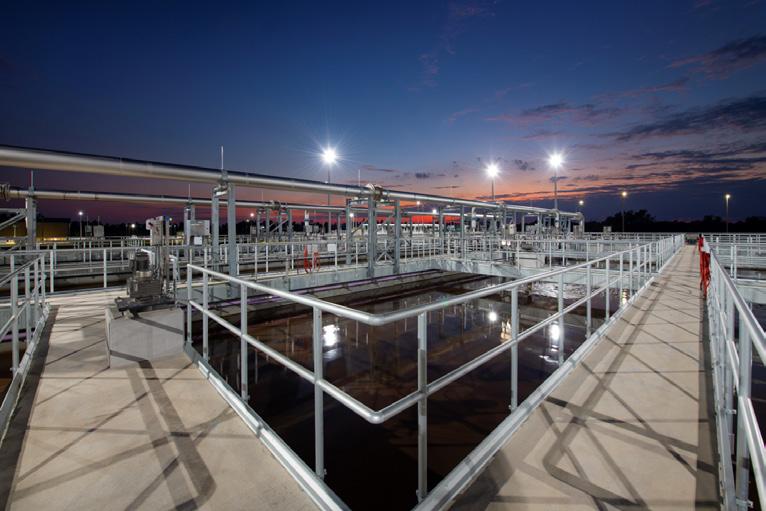
Project Completion
The last of the challenges came as 2021 transitioned to 2022, where the availability of start-up and check-out technicians were limited and backlogged. It was imperative that the owner had beneficial use on time, meaning delays and reschedules weren’t an option. Wharton-Smith worked closely with the owner and engineers to set forth a 16-week lookahead schedule that spanned from Labor Day to Christmas to check out all process systems.
This initiative ensured that the engineers were readily available, going above and beyond to be integral resources to the project. It meant the team worked collectively in “around the clock” shifts during field acceptance, plant start-up, and seeding to get the plant up and running. Perhaps most importantly, it meant that, while this project faced monumental challenges and complexities, the value of strong communication among all parties was a crucial key in achieving beneficial use.
The project achieved substantial completion on Oct. 4, 2022—more than two months ahead of the contractual obligation! Achieving this feat during the COVID-19 pandemic, global supply chain issues, and market volatility is a true testament to the fortitude of many dedicated professionals. Collaboration, adaptation, and creative problem-solving were paramount to the success of this vast undertaking.
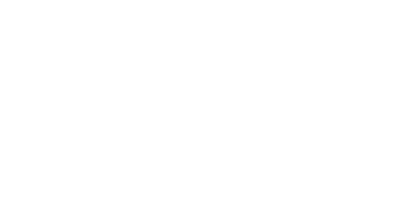
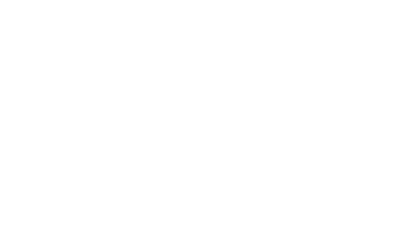