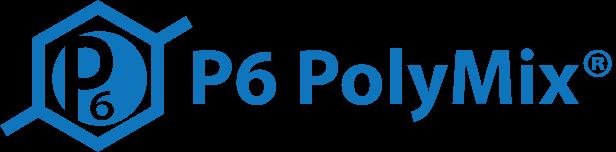
7 minute read
Technology Spotlight: The P6 PolyMix®
The P6 PolyMix® Difference: A Case Study
Advertisement
Biosolids sludge management has become exceptionally challenging for municipalities due to population increases creating greater wastewater treatment demand. This increased demand results in greater amounts of biosolids to process and dispose of, both economically and efficiently. Municipalities are now charged with finding new and creative solutions to handle the growing volume of wastewater biosolids.
The patented P6 PolyMix® system optimizes various sludge thickening processes, specifically the belt filter press (BFP), but also screw presses and centrifuges. Optimization is addressed in the location of polymer introduction into the sludge, the process of how the polymer is mixed with the wastewater sludge, the volume of flow that is fed to the dewatering equipment, and the reliability of the press feed pump.
As a result of these optimizations, the potential for reduced polymer consumption and cost, the potential for drier cake solids, the near elimination of feed pump maintenance, and the ability to process two to three times more volume than that of conventional dewatering systems makes the P6 PolyMix system a powerful addition to a municipality’s sludge handling process
Background
The conventional process for BFP sludge thickening is to pump dilute neat polymer into an injection ring located after the BFP feed pump between the pump and the BFP (Figure 1). Immediately after the polymer injection ring, a highshear mixer is used and is required to properly mix the polymer with the sludge particles so that the BFP can squeeze the water from the solids. The high-shear mixer immediately breaks the long-chain polymer strands into smaller pieces, resulting in increased polymer consumption and blinding off of the BFP belts. This system creates back pressure through the high-shear mixer, resulting in increased pump discharge pressure and horsepower (HP) requirements. Before the advent of the P6 PolyMix system, this was the normal process mode for conditioning sludge prior to delivery onto a BFP.
On the other hand, the P6 PolyMix system optimizes the BFP sludge conditioning and mixing process (Figure 2). The dilute neat polymer is pumped into the P6 InjeX™ chamber ahead of the BFP feed pump. The P6 InjeX chamber receives the dilute neat polymer for initial mixing with the sludge, and then both flow into the P6 PolyMix feed pump, where final mixing and pumping are performed.
The P6 PolyMix feed pump is a boundary layer/viscous drag centrifugal pump that gently “pulls” the sludge and polymer together through the pump. As it passes through the bladeless flat discpac (disc impeller), the sludge particles are gently mixed in a nonmechanical shear manner. The sludge particles and polymer are gently pulled through the discpac in a spiral motion from the discpac eye (center) outward to the pump discharge. The boundary layer/viscous drag pumping action creates a homogeneous slurry of polymer/solids, resulting in large, easily dewatered flocs. This process also has the effect of conditioning the polymer strands by “pulling them through” the pump and unwinding the polymer coils, as opposed to “pushing them through” the pump.
This conditioning of the polymer and sludge allows for more available charged sites on the polymer strands to attract the oppositely charged biological particles in the sludge for greater flocculation with less polymer. The homogeneous sludge/ polymer slurry is transferred without any additional mixing or damage to the floc to the BFP for dewatering/ thickening.
The P6 PolyMix feed pump, with its boundary layer/viscous drag pumping principle, is illustrated in Figure 3. The gentle nonmechanical shear pumping action protects the pump from wear, and the product, which, in this case, is the delicate biological floc, from damage or degradation. Since the flocs, after forming, are not mechanically sheared and not broken apart with a high-shear mixer valve, less polymer is required to achieve excellent flocculation and better dewatering. Continued on page 10
Figure 1. Conventional High Shear Belt Filter Press Pumping Process Figure 2. P6 PolyMix Belt Filter Press Pumping Process

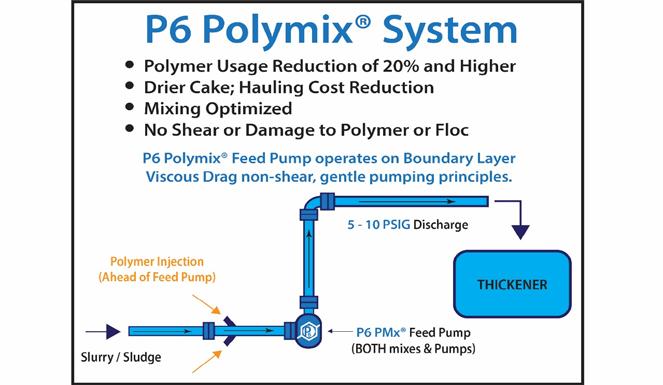
Continued from page 8 Likewise, the longer strands of polymer/sludge particles (floc) tend to allow for greater squeezing out of the water in the BFP and drier cake solids off a BFP. These benefits can also be obtained using the P6 PolyMix system with other dewatering applications, such as a screw press or centrifuge. Regardless of the thickening device, Gerber Pumps International Inc. provides a 10-year, 100 percent nonprorated wear warranty for the P6 PolyMix system, which includes the P6 PolyMix BFP feed pump.
Salisbury-Rowan Utilities Case Study
The Salisbury-Rowan Utilities (SRU) Town Creek Water Reclamation Facility was having problems with its solids thickening system in spring 2019. The BFP was not able to handle the volume desired (averaging only 115 gallons per minute [gpm]) or provide cake as dry as desired at higher flow rates. Stephen Gerber, GPi/P6 PolyMix operations manager, presented the new P6 PolyMix technology to Jason Wilson, P.E., assistant utilities director at SRU. The plant’s positive displacement BFP feed pump’s limited flow capacity to the BFP created challenges with handling the sludge volume of the plant. Additionally, SRU wanted drier cake, if possible, as well as savings in polymer cost.
The plant was typically getting 14 to 16 percent Cw cake solids from its BFP, depending on the flow being pumped to the BFP. The flow ranged from 115 up to 150 gpm, with an absolute max of 220 gpm at minimum acceptable dewatering. The 115-gpm flow produced a higher percentage of cake solids, but also restricted the plant’s solids handling removal capacity. Wilson advised that SRU likes to be innovative and is very open to new technologies that make its operations more efficient and cost-effective.
After initial conversations with Wilson, Gerber visited the SRU plant to review the onsite conditions. After
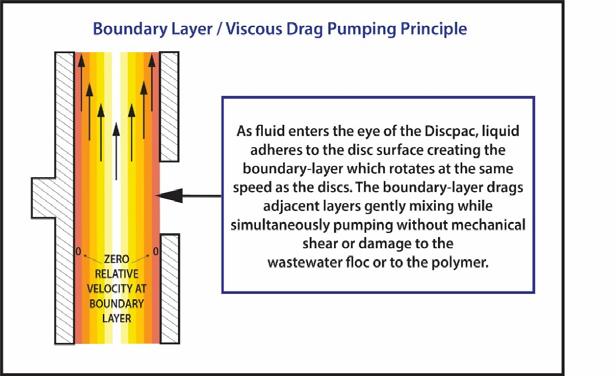
Figure 3. Boundary Layer/Viscous Drag Pumping Principle reviewing SRU’s current dewatering process, he and Wilson discussed the application and confirmed that the SRU Town Creek wastewater treatment site would be a viable location for a P6 PolyMix system (Figure 4). The GPi had a 20-HP P6 PolyMix demonstration.
The wastewater operations/ biosolids supervisor for SRU, Bob Loper, coordinated the installation of the P6 PolyMix system with Gerber and the subsequent testing. A percent solids concentration test for various combinations of flow and sludge types on its OHAUS MB27 moisture analyzer was conducted in June 2019 (Figure 5).
The test was a resounding success. The dry solids cake concentration was increased from an average of 16.67 percent with the existing positive displacement BFP feed pump up to 25.33 percent Cw with the P6 PolyMix system. Polymer consumption was effectively reduced by 47 to 55 percent. The feed to the BFP was increased from the plant’s typical range of 115 to 150 gpm, up to 250 to 390 gpm. This three-fold increase in throughput was significant.
The purchase of another expensive BFP for the plant, with all the associated costs, could be forestalled due to the increased capacity of the existing BFP with the P6 PolyMix system. Ecstatic with the results and, due to the excellent performance of the P6 PolyMix system, SRU purchased a P6 PolyMix system for its Town Creek wastewater treatment plant. Additionally, SRU purchased a P6 PolyMix system for its Grant Creek wastewater treatment plant and two additional P6 PolyMix systems for new centrifuges at its water treatment plant.
Conclusion
The P6 PolyMix technology provided the following benefits to the SRU Town Creek wastewater treatment plant: S 50 percent polymer reduction. S 3 to 4 percent Cw increase in cake solids. S An increase of three times in the
BFP solids removal capacity. S Increased pump performance and pump maintenance elimination.
The director of SRU, Jim Behmer, commented that the utility likes to be on the “cutting edge, but not the bleeding edge” when it comes to new ideas. With this spirit of innovation, the SRU team has embraced the new P6 PolyMix technology, dramatically cutting costs associated with the biosolids handling systems.
The utilization of the P6 PolyMix system has created savings for the citizens and customers of Salisbury, N.C., and the surrounding areas. The P6 PolyMix creative innovation for the dewatering of wastewater sludge (Figure 6) has provided SRU with a solution to the growing challenges associated with the treatment and processing of biosolids.
Jason Wilson, P.E., is assistant utilities director with Salisbury-Rowan Utilities in Salisbury, N.C. Stephen Gerber is GPi/P6 PolyMix operations manager and Bert Gerber, P.E., is GPi/P6 PolyMix chief engineer with Gerber Pumps in Longwood. q
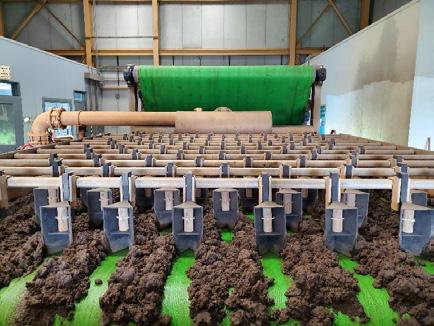
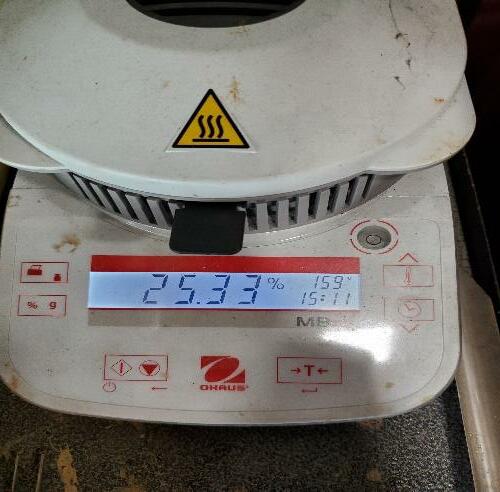
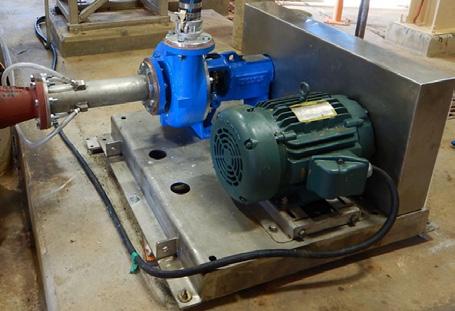
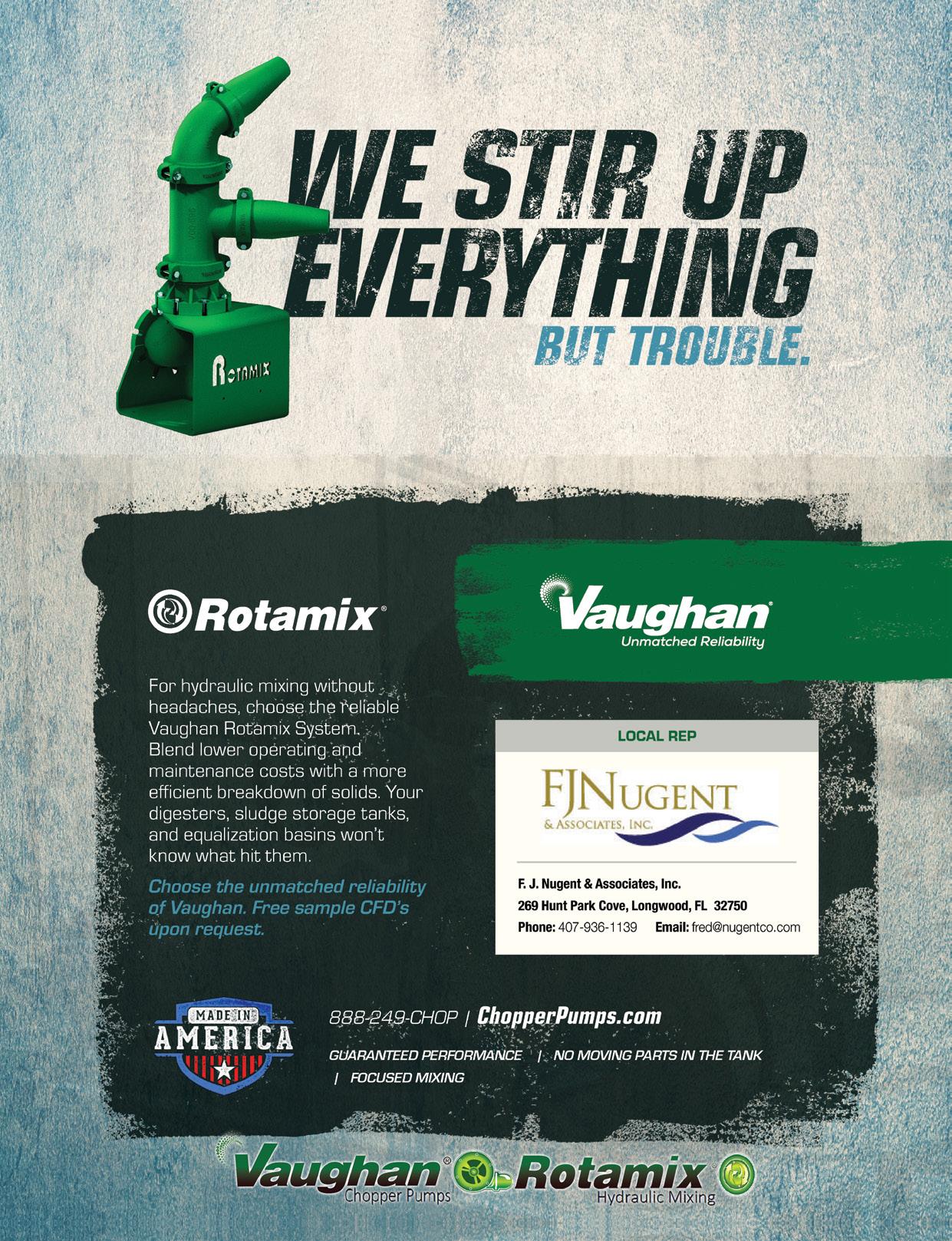