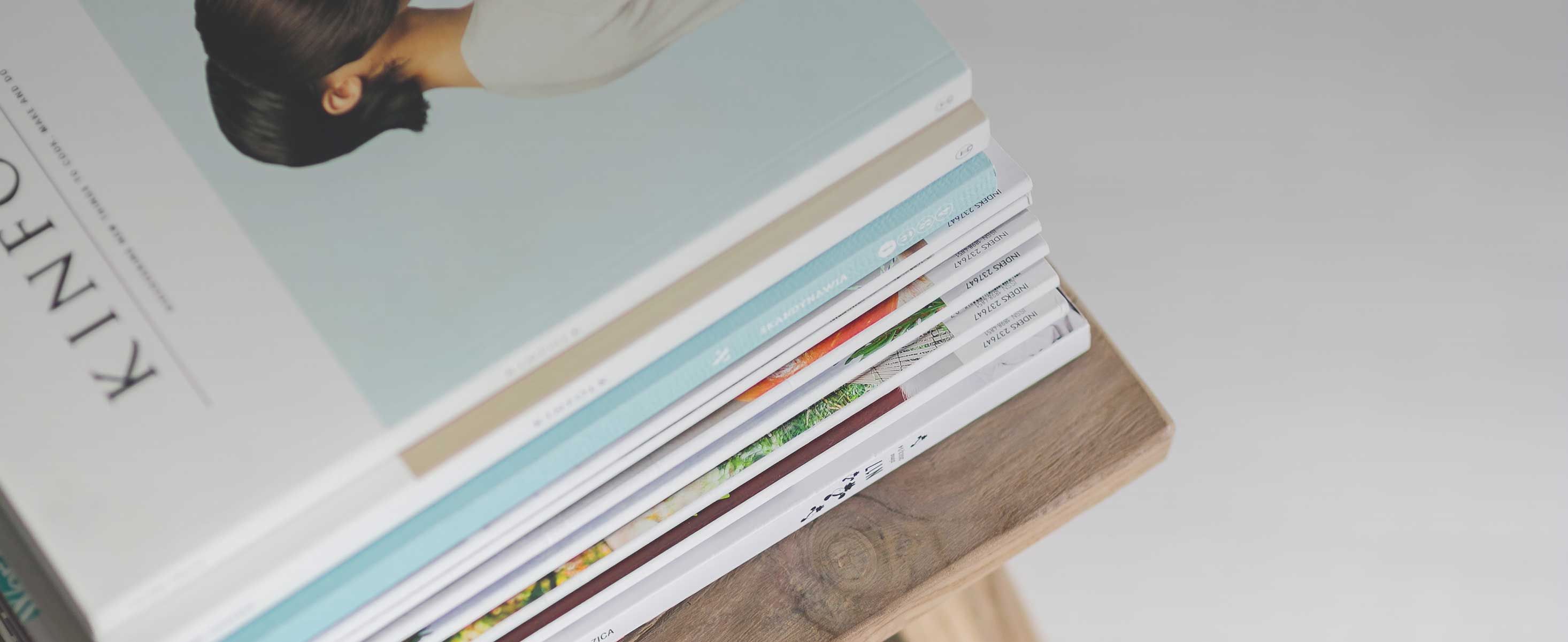
3 minute read
PRODUCT INFORMATION
Sugar
Sugar is one of the company's most important products. To make sugar, the juice recovered from crushed cane is evaporated. This is a widely used sweetener in both food and beverages. Sugar is usually packed and sold loose in India.
Advertisement
Molasses
Molasses, a tasty byproduct, is extracted when sugar cane is refined to make sugar crystals. Machines that use centrifugal force separate the sugar crystals from the liquid. The remaining syrup is converted into molasses.
Bagasse
Bagasse is a byproduct that can be used to generate paper or power in two profitable ways. Making paper from bagasse is an environmentally friendly alternative to the traditional way of collecting pulp from trees. Bagasse accounts for roughly 30% of total sugar production. A 6,000 TCD operation may thus create 1,800 tons of bagasse per day.
Alcohol
Molasses, a byproduct of sugar production, is distilled to produce ethanol, rectified spirit, extra neutral alcohol, denatured spirit, and other products used in the chemical, pharmaceutical, and alcohol industries. Ethanol is another useful alternative fuel.
Energy
Bagasse is utilized to create power due to its high heat factor, which replaces the typical thermal option while lowering greenhouse gas emissions. Sugar mills currently get their energy from boilers driven by bagasse.
Energy Policy Renewal
To function, every sector of the economy, including agriculture, industry, transportation, commercial, and residential use, requires energy inputs.
Since its independence, India has pursued economic growth strategies that have entailed the usage of increasing quantities of energy. As a result, energy consumption in all forms has been steadily increasing across the country. As a result of expanding energy consumption, the country's reliance on fossil fuels such as coal, oil, and gas has grown. Concerns about keeping the energy supply to enable our economic growth are fueled by rising oil and gas prices and the possibility of future shortages. The use of fossil fuels is expanding, which has an influence on the environment both locally and globally.
Technological advancement
Gangakhed has invested in cutting-edge technologies in order to completely automate the factory. More automation has also reduced the requirement for human intervention when creating high-quality goods. The following are some of the advantages of this modern technology for the company:
a. Steam consumption (per tonne of cane)
Compared to the industry average of 45%, the company consumes around 39% less steam per tonne of cane. There are continual efforts to increase electricity savings and reduce them to 36%. Every 1% saved results in a larger surplus for the corporation to export.
b. The moisture content
The moisture content of the crushed cane at Gangakhed is 48%, compared to the industry standard of 50-53%. More efforts are being made to reduce moisture content, which will boost the efficiency of the boilers.
c. Evaluation of quality
The Gangakhed sugar factory can make sugar with an ICCUMSA Color value of up to 50.
d. Captive power use of less than 9% e. cogeneration
For crushing sugarcane, the company is transitioning from a conventional method to a more modern one. This reduces operational expenses while enhancing sugar recovery and lowering bagasse moisture content.
Reduced captive power use indicates that the corporation has more co-generation electricity available for export.
f. variable frequency drives
The company offered conducting variable frequency drive motors to reduce power consumption.
Planetary gears, for example:
In the plant's speed reduction gearboxes, high-efficiency planetary gears are used. Sugar factories' power consumption is reduced to 22 kW/ton of cane using both planetary gears and VFDs, compared to other facilities' normal consumption of 26 kW and higher.
g. planetary gears
High-efficiency planetary gears are used in the plant’s speed reduction gearboxes. Utilizing both planetary gears and VFDs, sugar factories’ power consumption is decreased to 22 kW/ton of cane, compared to other plants’ typical consumption of 26 kW and higher. h. The company constructed a decanter system for the first time in our nation in order to separate muddy juice. This fully eliminates the need for bagacillo in the sugar-making process, saving 0.8% of bagasse, which is then productively used in cogeneration plants to generate additional money. Additionally, the method reduces press mud loss by 0.5% pol. When employing the most recent decanter system, pol loss in press mud is reduced to 0.04% on cane and the quantity of press mud is decreased from 4% on cane to 1.7% on cane. Pol loss in press mud using a conventional vacuum filter is 0.06-0.08% on cane.