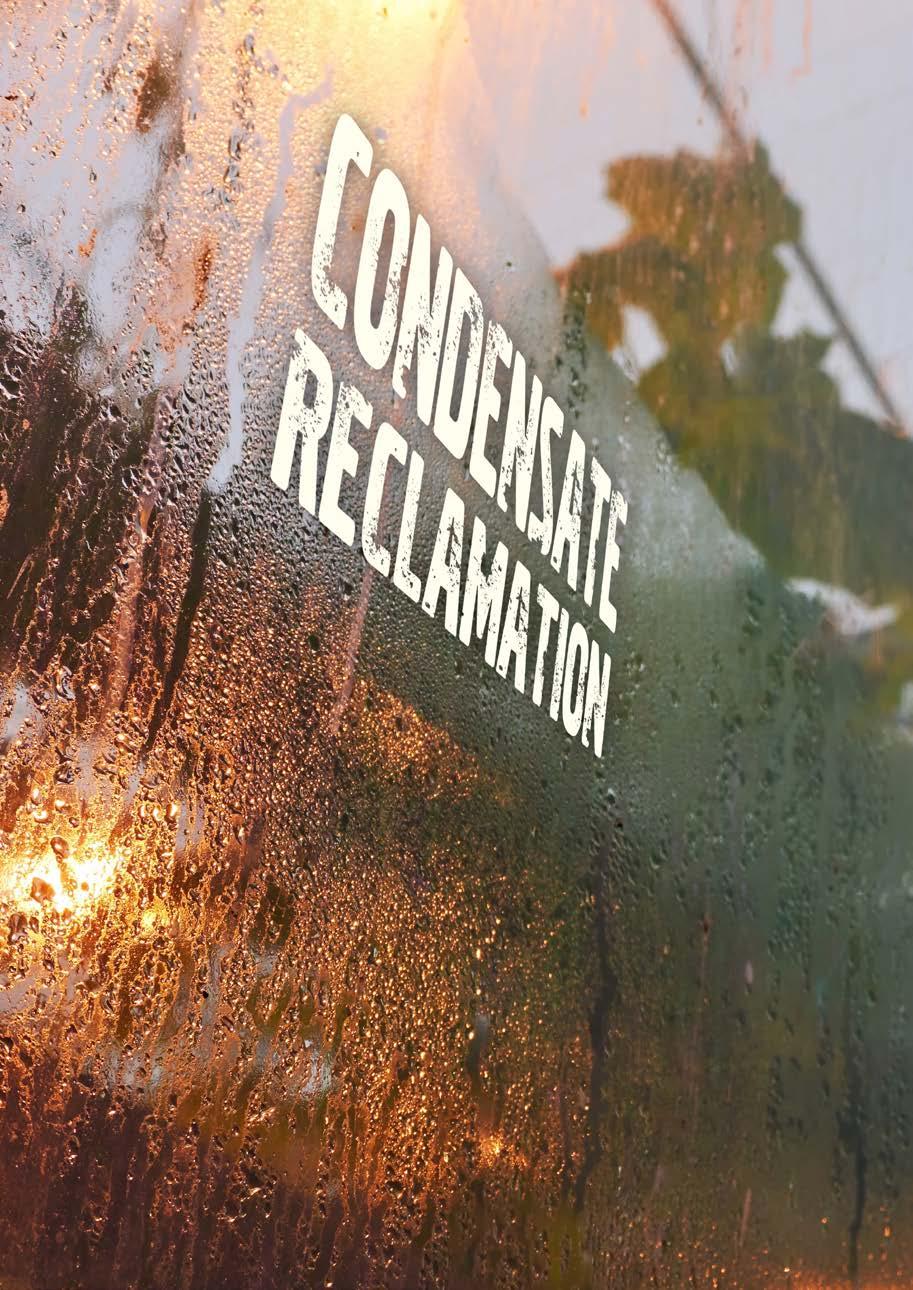
2 minute read
Water Conservation for Sealed Hydroponic Environments
BY RICH GELLERT
Indoor hydroponic farming is quickly becoming the business model of choice, with US revenues projected to reach $3 billion by 2025. The explosive growth of hydroponics can be traced to improvements in technology and efficiencies, as well as ample, decentralised indoor space for year-round harvesting. With this new momentum comes essential questions as to how to reimagine farming from what is currently understood as a resource-heavy, wasteful process, to modern, sustainable, and environmentally-friendly production practices that will last humanity on into the future.
In recent years, water conservation strategies in hydroponic farming have become as important, if not even more important, than any other energy and resource-saving methods taken into consideration when building a new operation. With climate change, drought, and water pollution all becoming increasingly urgent to address, minimising water waste and maximising irrigation efficiency is a top facility-planning priority. Regulatory compliance has also changed the way hydroponic farming approaches water use. In some areas, conservation technologies must be permitted in place and pass inspection before operations can begin.
There are several ways to reduce hydroponic farm water use; the most cost-effective methods involve high-efficiency reverse osmosis systems, as well as nutrient and condensate reclamation filters. Condensate, water vapour accumulated from indoor climate control equipment, is one of the easiest wastewater sources to recycle and reuse in a sealed hydroponic environment. Condensate reclamation technology can be implemented in small farms needing only a couple of hundred gallons a day, to industrial-scale operations requiring massive amounts of high quality, purified water. When properly installed and maintained, condensate can fulfil up to 80% daily water demand, at any scale…water that would typically go down the drain!
Because condensate is the accumulated evaporation of water, it is considered to be pure. Contaminates in the source water are denser than water vapour, so they are separated and left behind. This purified water is a perfect base formula for adding nutrient solutions, which are designed using reverse osmosis water for calibration. This allows the grower to be precise with measurements and control, which can ultimately translate into healthier plants and higher quality, larger yields.
However, in a sealed hydroponic environment, condensate must travel through HVAC equipment, air handlers, dehumidifiers, ducting, or other surfaces that may contain different types of contamination. Surface exposure to rust, oils, metals, biologicals and other types of industrial contaminants can ruin otherwise pure condensate water. Condensate is also naturally acidic and can act as a corrosive on untreated metal, picking up pollutants and destroying the goal of a purified irrigation source. Without proper post-filtration, exposed condensate loses its potential of being a reliably pure source of water ready for nutrient formula mixing, water that would typically be the product of a reverse osmosis filter.