
7 minute read
Get ready for new EPR regulations
Get ready for new regulations
Extended plastic recycling regulations on the horizon will significantly impact garden centre businesses. Jane Lawler explains.
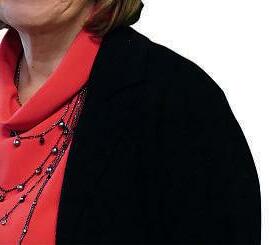

In the garden products supply chain, we think of ourselves as a largely environmentally friendly business sector and we take sustainability pretty seriously. This includes our attitudes to reducing packaging waste and promoting recycling. There’s been a great deal of progress in recent years and some innovative strategies for collecting and recycling compost bags, for example.
All garden businesses turning over more than £2 million and handling 50 tonnes of packaging already fall under the 2007 Producer Responsibility Obligations (Packaging Waste) Regulations. These regulations minimise waste and promote recycling and re-use, and all obligated businesses contribute to the cost of collecting and managing the waste packaging they handle. The bill for recycling packaging is shared out between all the businesses in the supply chain, from the producer right through to the retailer. Most businesses have become used to the arduous task of collecting data every year and the associated levy they have to pay through the Packaging Recovery Note (PRN) scheme.
In the coming years, the regulations will be extended to incentivise even more sustainable product and packaging design, increase re-use and significantly increase collection and recycling rates. There will be four core initiatives:
The Plastic Packaging Tax. Already in force, driving an extra £200 per tonne on any plastic packaging that does not contain 30% recycled content.
The introduction of deposit return schemes designed primarily for food and especially drink packaging – although there could be some interesting opportunities for garden businesses here too. Compost and aggregate sales could possibly be run on a deposit return scheme, using returnable bulk bags.
All local authorities will have to provide the same basic set of collection and recycling, both for households and businesses. Great news for frustrated consumers who struggle with the inconsistencies of kerbside waste collections and recycling.
The full net cost of the recovery of the packaging will be collected from obligated companies.
Jane Lawler, a panel member of the wellattended GIMA conference to introduce and explain the new regulations.
This fourth element will have the most significant impact on manufacturers, importers, wholesalers and retailers of garden products. Estimates of the overall costs of the current scheme range from £230 - £300m, shared across the supply chain. The real cost of recovering all packaging in the UK (currently met from local tax payers and councils) is estimated to be closer to £1.7 billion. The additional costs for collection schemes and administration of the new EPR is estimated to be up to a further £800m so in future, compliance costs for businesses could be between 6x and 10x what they are currently. Additionally, from 2023 the new scheme will make the UK brand owner (or importer) of the packaged product solely responsible for meeting 100% of the cost of collecting, recycling or disposing of the packaging.
It’s early days and the implementation of the new scheme is already running behind schedule. Originally planned for 2023, the most recent consultation response from government lays out a phased introduction beginning in 2024. The bad news is that the levy placed on obligated companies is most likely to be based on the historic sales of product packaging. This means anyone likely to be affected needs to
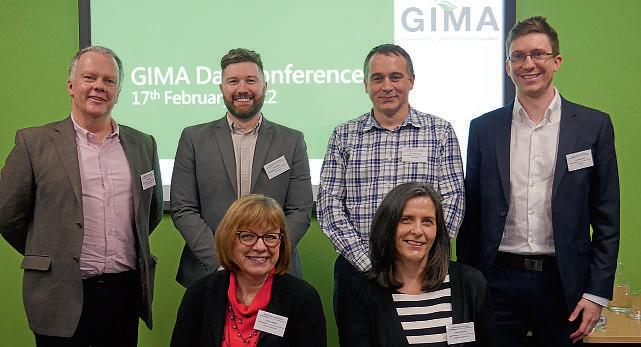
through a process of ‘modulated fees’, set to be introduced in 2025, some packaging materials will be charged less per tonne than others. While the modulated fees have yet to be finalised, it’s clear they will provide strong financial incentives for using packaging that is easy to recycle through domestic kerbside collections. Packaging that is less easy to recycle will be likely to attract much higher fees so, it makes sense to remove the worst offending materials entirely and as soon as possible. Expanded polystyrene, foil laminates, plastic swing tags and carbon black plastics are just a few of materials that could all be very costly under the new scheme.
As well as making plans to reduce overall packaging weight and removing non-recyclable materials from product packaging, businesses also need to begin the process of collecting detailed packaging data. This means understanding and recording the precise weight of different materials in product packaging - primary, secondary and transit packaging, including the pallet!
And small businesses won’t escape. The new scheme aims to fund the recycling of a much
L-R Panel members Tim Hayne, Wessex Packaging; Josh Remi, Ecoveritas; Jane Lawler, Lawler Associates; Sam Marriage, Marriages; Jane Hartley, Evergreen Garden Care; Lee Waring, Valpak.
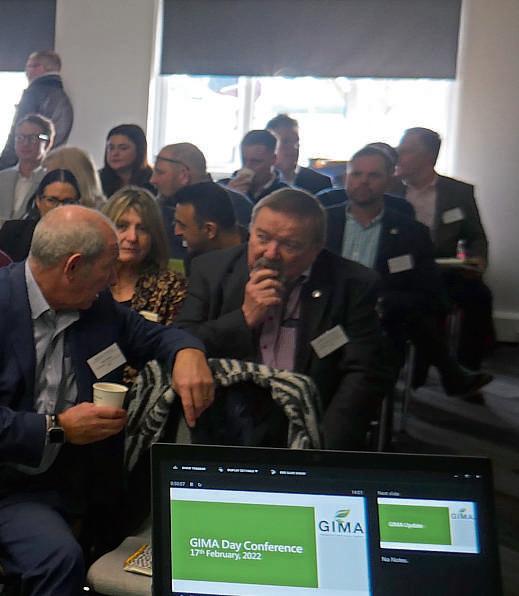
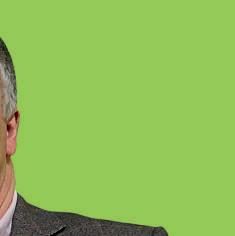
make sure they’re collecting the relevant data from January 2023. Whatever happens, it’s clear that the bill is going to be significant.
So, what can businesses do to try and manage the costs and plan for the future? Firstly, because the levy calculations will be based on tonnage, reducing the overall weight of packaging in the supply chain will ultimately lower a business’s cost. Where practical, this might mean reducing the thickness of board, using a thinner film, or removing secondary packaging entirely. There may be opportunities to minimise transit packaging where materials like stretch pallet wrap can contribute extra weight and therefore push costs up significantly.
As the new scheme is focused on recovering the direct cost of disposal or recycling,g it’s logical that packaging that is easy (and cheaper) to recycle and has a value to the post-consumer waste supply chain will attract a lower levy. This means that
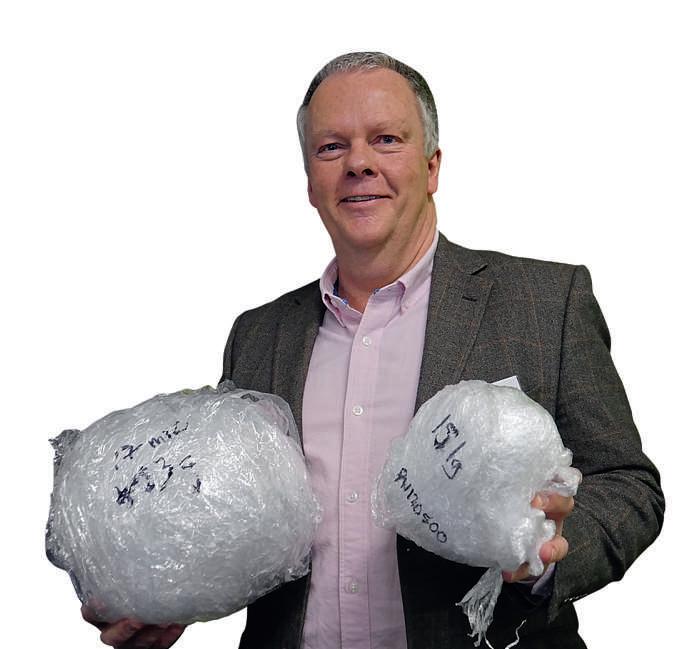
Tim Hayne brings home the impor importance of weight. The plastic on the left weighs 403g, that on the right is just 151g. higher proportion of the UK’s total packaging burden than was funded in the past under the old scheme. The new scheme will continue to obligate all businesses with a turnover of £2 million and 50 tonnes of packaging handled. Even smaller companies with a turnover as low as £1 million and handling just 25 tonnes of packaging will be required to register and report all the packaging they place on the market, although they won’t have a levy bill to pay until they go over the £2 million threshold. No business, however small, escapes the obligation to include appropriate recycling advice on packaging by the deadline of March 2026 (March 2027 in the case of plastic films and flexibles).
In future, unlike under the current system, estimating and rounding of packaging weights will not be allowed. Detailed records of material weights will be required in order to complete packaging returns - a not insubstantial task, especially for businesses importing finished goods - including retailers direct importing and, of course, those selling product under their own brand. Even retailers who only sell UK supplier brands don’t escape completely - while there is no levy to pay on those goods, there is still a reporting obligation. Individual component packaging weights will need to be reported quarterly and, from the end of 2023, separately by the devolved nations (Scotland, Wales, Northern Ireland and England).
There’s also some further ‘devil in the detail’ that could catch companies out who set out to improve their packaging sustainability. Businesses that have moved to compostable or biodegradable packaging will be required to label their product clearly ‘do not recycle’ as there is still uncertainty and inconsistency in how these materials will be managed through the recycling process. We have to assume that if they are not going into the recycling stream, they will not be eligible for modulated fees, so by definition will be a much more costly option.
So, the industry is bracing itself for yet another costly legislative burden and all the extra administration required. At least we can take comfort in the fact that this new system is bound to have a marked impact on the amount of waste packaging going to landfill. Businesses who don’t take heed of the changes and act now will be the ones who pay a much larger proportion of the bill for improving our overall packaging recycling rates.
Further information:
For information on GIMA’s Plastic Packaging Pledge and access to the webinar recordings from the event (members only benefit). www.lawlerassociates.co.uk www.gima.org.uk