

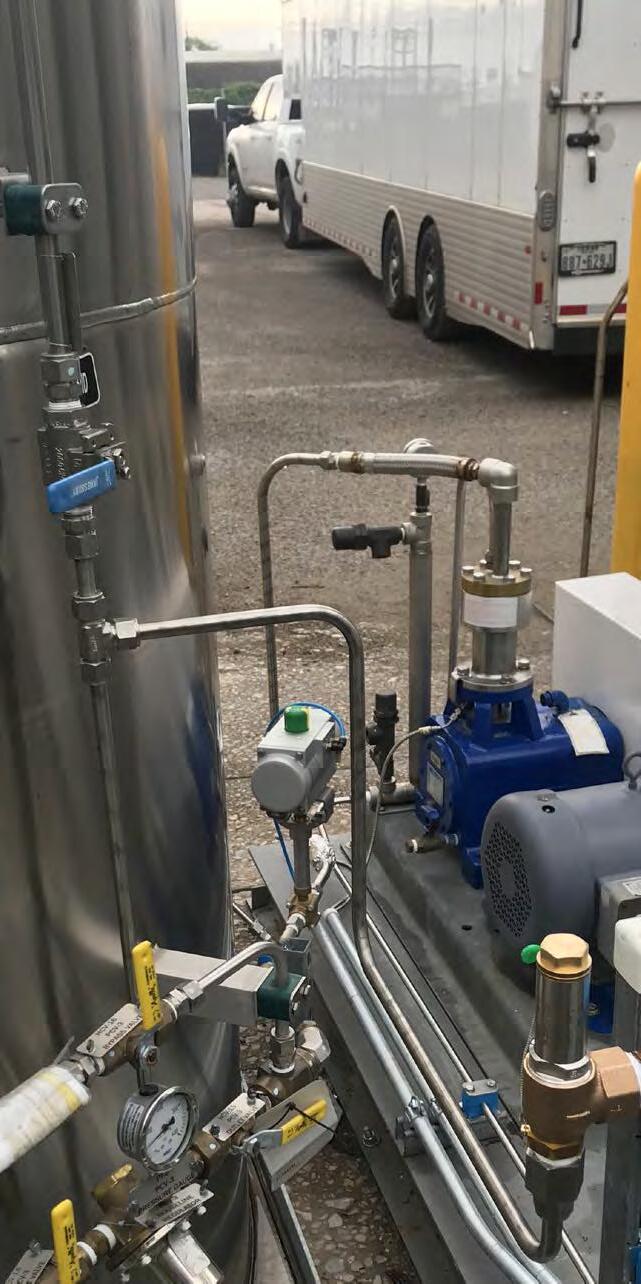


For Gas Extraction Applications
WELDCOA has developed equipment and controls to supply Carbon Dioxide to our customers IN A controlled, safe maNNer that delivers quick roi results.
We meet our customers requirements by determining the best system design using a variety of equipment:
• Bulk Storage Tanks
• Pump/Vaporizer Skid Unit
• Buffer Vessel Stations
• Specially Designed Controls
A bulk CO2 system can feed into your current extraction equipment, drastically improving the volume and condition of the CO2 supply as well as the efficiency in your operation.
The Benefits You Will See:
• Increase the Flow Rate
• Increase in the Extraction Cycles
• Reduce the Charging Time
• Reduce Cylinder Handling and Labor
We’re Focused On Your Success. Weldcoa works because we’re focused on your success. Since 1968 we’ve worked hard to engineer solutions, manufacture equipment, and provide uncompromising service to our customers, who use gases in the production of their products.
Everything we do is driven by our motivation to improve your business. We can help you achieve your goals and maximize your returns.
• Reduce costs
• Improve safety
• Increase productivity
• Maximize uptime
• Minimize waste
• Ensure long-term performance
• Increase value to your customers
If It Involves Gases, We Can Help.
Our history of innovation has always been driven by the needs of our customers. As new applications for high pressure gases, cryogenics, high pressure liquids and supercritical fluid began to emerge, we met the challenge with effective solutions to deliver on the growing demand in emerging markets.
Constant innovation has become our hallmark, one which our customers have grown to depend upon, and so can you.
Our Equipment Does What It’s Designed To Do.
We are a US manufacturer that designs, engineers, manufactures, programs and tests our equipment and automation in-house.
The equipment we built decades ago is still operating today, doing what it was intended to do and more. Clients that made initial investments have continued to engage us in the development of additional solutions to grow their businesses.
Regardless of the scale of the solution we provide, you can expect:
• Quality manufacturing
• Performance testing
• The use of advanced technologies
• Training and Support
We Go The Extra Mile.
It’s in our nature to be curious. We truly enjoy investigating, learning, developing, testing and creating solutions for any application of gas. Our cross-disciplinary team of experts bring an in-depth knowledge of gases to every project. You can count on their passion and commitment to make your project a success.
• Gas Systems Consulting and Engineering
• Equipment Design and Engineering
• Manufacturing in the USA
• Equipment Testing
• Staff Training
• Knowledge Sharing
Bulk Tank or Microbullk Unit:
CO2 is stored in this unit in a Liquid Phase . Weldcoa does not manufacturer bulk tanks or microbulks however we do have a long history of working with tanks and have close relationships with bulk tank suppliers in the gas industry. The components that are needed for this unit, in order to be compatible with our modular skid, are liquid withdrawal and gas/liquid return ports. The tank size will be determined by the extractor size and the number of cycles to be run per day.
This system is best suited for Extraction Equipment of 40 Liters or Larger. The Skid Unit consists of a CO2 pump, automation controls, vaporizer, piping and valve assemblies, all on a steel skid base. This modular unit is provided, tested, and remotely supported by Weldcoa.
1. CO2 product, in a Liquid Phase, is piped from the bulk tank into the Pump (which is on the skid unit) and then piped out of the Pump, in a Liquid Phase, into the Vaporizer (which is also on the skid unit).
2. Once in the Vaporizer, the CO2 product is converted into a Gas Phase and is then piped to the Buffer Vessel Station(s) still in a Gas Phase.
3. This process is managed and controlled by Weldcoa’s automation.
4. From the Buffer Vessel Stations, the CO2 product, still in a Gas Phase, is piped into the Extractor inlet
The number of Buffer Vessel Stations needed depends on your volume and quantity of your extraction equipment. This process is managed and controlled by Weldcoa’s automation, holding the CO2 product in Gas Phase at 750 to 900 PSIG.
• One station is capable of supplying gas to extractor equipment with capacity of 1 to 100 Liters
• Two stations are capable of supplying gas to extractor equipment of 100 to 200 Liters
• Three stations are capable of supplying gas to extractor equipment of 200 to 300 Liters
• Four stations are capable of supplying gas to extractor equipment of 300 to 400 Liters
As the client’s extraction volume increases, they can easily accommodate the demand by adding another Buffer Vessel Station to increase their storage capacity.
Typically, an Extractor consists of a Solvent Chamber(s) ranging from 2 to 400 Liters, an Expansion Chamber(s), an oil collection vessel, a CO2 gas recovery system and automated controls with an operator touchscreen terminal. None of this is provided by Weldcoa.
5. From the inlet, the CO2 product, in Gas Phase is piped into the main Solvent Chambers of the Extraction Machine where the temperature and pressure of the CO2 product is then adjusted, converting the CO2 product from a Gas Phase into a Supercritical Phase. The time it takes to fill up the Solvent Chamber and regulate it to these specific parameters is called the “Charging Time”.
6. Once the correct temperature and pressure are achieved, the system pumps the supercritical CO2 in a loop for a specific amount of time. This is called the “Looping Cycle”. As the material passes through the Expansion Chamber the Supercritical CO2 coverts back into a Gas Phase, allowing the oil to decondense and drop into the oil collection vessel, providing a final product/ yield from the extraction process. When the entire cycle is complete, the CO2 gas is vented into a recovery system for reuse in the next charging cycle.
CO2 Modular Pump/Vaporizer Skid Unit
This system is best suited for Extraction Equipment of 40 Liters or Larger. Every skid unit is specifically designed to be remotely supported for optimum performance, reliablilty and safety.
INTREGRATED AUTOMATION CONTROLS WITH REMOTE SUPPORT
GALVANIZED STEEL SKID FRAME
ELECTRIC CO2 VAPORIZER
INTERCONNECTING PROCESS PIPING
Weldcoa has strict quality control procedures ensuring high quality and consistent performance. Quality control methods and meticulous attention to detail throughout the manufacturing and testing process ensure that our customers will receive a reliable system that will provide years of service.
Every Weldcoa System is:
√ 100% Hydrostatically pressure tested to 1.5 times the MAWP
√ 100% Nitrogen leak tested
√ Inspected and thoroughly tested to the highest safety standards before shipment
√ Inspected again and validated once system is installed and operating
√ Made in the USA
√ A GALVANIZED STEEL SKID FRAME
√ A CO2 PUMP
- 1200 PSI RELIEF VALVE
- 1500 PSI RUPTURE DISC
- BUMP TUBE
√ AN ELECTRIC CO2 VAPORIZER
- HIGH TEMPERATURE LIMIT PROTECTION ON EACH HEATER SEGMENT
- SAFETY LO-TEMP BYPASS VALVE
√ INTREGRATED AUTOMATION CONTROLS
- HOFFMAN TYPE 12 ENCLOSURE WITH LIGHT TOWER
- SDN 10AMP 120VAC TO 24VDC POWER SUPPLY
- MITSUBISHI Q SERIES PLC WITH 5-SLOT RACK, POWER SUPPLY, CPU, CC-LINK MODULE, 16 INPUT MODULE, AND 16 OUTPUT MODULE
- 5-PORT ETHERNET SWITCH
- MITSUBISHI REMOTE ANALOG CARD
- RED LION SIGNAL CONDITIONER
- E-STOP
- LIGHT TOWER STATUS INDICATOR
√ PLC CONTROL UNIT (MOUNTED INSIDE)
- HOFFMAN TYPE 12 ENCLOSURE
- MITSUBISHI “Q” PROCESSER
- POWER SUPPLY
- 12” GRAPHIC OPERATOR INTERFACE SCREEN
√ INTERCONNECTING PROCESS PIPING
- LIQUID SUPPLY “Y” STRAINER
- SUPPLY FLEX LINE
- 3/4” LIQUID SUPPLY EXTENDED STEM VALVE
- 1/4” BLEED EXTENDED STEM VALVE
- 1/2” RECYCLE EXTENDED STEM VALVE
- 1/2” RETURN CHECK VALVE
- GLYCERIN FILLED PRESSURE GAUGE 0-2000 PSI
- RELIEF VALVE SET 1500 PSIG
- ALL MOUNTED, PRE-PIPED, PREWIRED TO STEEL SKID
- 3 RTD’S (PUMP DISCHARGE, SHAFT SEAL, VAPORIZER DISCHARGE)
- PRESSURE TRANSMITTER 0-1500 PSI
- HIGH PRESSURE CUTOUT SWITCH
√ REMOTE SUPPORT
- REMOTE VIEWING
- SYSTEM ALERTS
CO2-1-10-1-24-E1L0V0D1U1B3T1PT1S-75-GALOII
PUMP SKID ASSEMBLY ELECTRIC CO2 VAPORIZER
- RPSA PUMP 3.3 GPM - 75 KW, 180 AMPS - 10 HP MOTOR - 1875 LBS PER HOUR
CO2-1-7.5-1-24-E1L0V0D1U1B3T1PT1S-60-GALOII
PUMP SKID ASSEMBLY ELECTRIC CO2 VAPORIZER
- RPSA PUMP 2.7 GPM - 60 KW, 144 AMPS - 7.5 HP MOTOR - 1500 LBS PER HOUR
PART NO.
CO2-1-5-1-24-E1L0V0D1U1B3T1PT1S-45-GALOII
PUMP SKID ASSEMBLY ELECTRIC CO2 VAPORIZER
- RPSA PUMP 2.1 GPM - 45 KW, 108 AMPS
- 5 HP MOTOR - 1125 LBS PER HOUR
PART NO.
CO2-1-5-1-24-E1L0V0D1U1B3T1PT1S-30-GALOII
PUMP SKID ASSEMBLY ELECTRIC CO2 VAPORIZER
- RPSA PUMP 1.25 GPM - 30 KW, 72 AMPS
- 5 HP MOTOR - 750 LBS PER HOUR PART NO.
PART NO.
CO2-1-5-1-48-E1L0V0D1U1B3T1PT1S-45-GALOII
PUMP SKID ASSEMBLY ELECTRIC CO2 VAPORIZER - RPSA PUMP 3.3 GPM - 75 KW, 90 AMPS - 10 HP MOTOR - 1875 LBS PER HOUR
PART NO.
CO2-1-7.5-1-48-E1L0V0D1U1B3T1PT1S-60-GALOII
PUMP SKID ASSEMBLY ELECTRIC CO2 VAPORIZER
- RPSA PUMP 2.1 GPM - 45 KW, 54AMPS
- 5 HP MOTOR - 1125 LBS PER HOUR
PART NO.
CO2-1-5-1-48-E1L0V0D1U1B3T1PT1S-30-GALOII
PUMP SKID ASSEMBLY ELECTRIC CO2 VAPORIZER
- RPSA PUMP 1.25 GPM - 30 KW, 36 AMPS
- 5 HP MOTOR - 750 LBS PER HOUR
Each Weldcoa Buffer Vessel Station consists of a steel frame, control box, manifold system, piping, gauge and valve assemblies required and four DOT or ASME specification storage vessels with a special heater cover needed for this application. This modular unit is built, tested, and remotely supported by Weldcoa
316L STAINLESS STEEL HEADER 1” TUBE 0.083 WALL
HEATER CONTROL BOX INTEGRATED ONTO CYLINDER STORAGE STAND
125# CO2 CYLINDERS DOT
BLANKETS, 1 PER CYLINDER
BOLT DOWN FRAME
Every CO2 Buffer Vessel Station is:
√ 100% Hydrostatically pressure tested to 1.5 times the MAWP
√ 100% Nitrogen leak tested
√ Inspected and thoroughly tested to the highest safety standards before shipment
√ Inspected again and validated once system is installed and operating
√ Made in the USA
PART NO.
CO2SS1S-BBB-1500-C-BK-H24
- (4) 125# CO2 CYLINDERS DOT (RETEST EVERY 5 YEARS)
- 1000 PSIG MAWP
- 316L STAINLESS STEEL HEADER 1” TUBE 0.083 WALL
- BOLT DOWN FRAME
- BALL VALVE FOR BOTH CHARGING AND DISCHARGING
- 1500 PSIG RELIEF VALVE
- HEATER CONTROLS 240 VOLT
- (4) BLANKETS, 1 PER CYLINDER
- HEATER CONTROL BOX INTEGRATED ONTO CYLINDER
STORAGE STAND
- CARBON STEEL FRAME, POWDER COATED
As the client’s extraction volume increases, they can easily accommodate the demand by adding another Buffer Vessel Station to increase their storage capacity.
The number of Buffer Vessel Stations needed depends on your volume and quantity of your extraction equipment. This process is managed and controlled by Weldcoa’s automation, holding the CO2 product in Gas Phase at 750 to 900 PSIG.
√ One station is capable of supplying gas to extractor equipment with capacity of 1 to 100 Liters
√ Two stations are capable of supplying gas to extractor equipment of 100 to 200 Liters
√ Three stations are capable of supplying gas to extractor equipment of 200 to 300 Liters
√ Four stations are capable of supplying gas to extractor equipment of 300 to 400 Liters
There are a number of factors that affect how to optimally size a system; such as how much recovered CO2 will be reused, pump may be running during the charging cycle, etc. But the below listed steps will be a good starting point of reference.
The first thing we need to do is to determine how much CO2 storage we need to charge your extractors as quickly as possible. This allows us to start a new cycle with less down time in between. Less down time will increase the number of cycles we can run in a given time period. Weldcoa offers Buffer Vessel Stations To determine how many you will need, please see below.
1. Add together the chamber capacities of all of your extractors. (Example: you have 1 – 100 Liter and 2-40 Liter units for a total of 180 Liters)
2. Divide total chamber capacity by 100 (Example: 180 Liters divided by 100 equals 1.8 rounded to 2)
Based on the above example we have determined we will need 2 CO2 Buffer Vessel Stations
You need to determine what pressure range your extractor requires to operate efficiently. You will need to contact the extractor supplier for this information. (Note: 600 PSI Min. to 900 PSI Max. is very common.)
You need to decide what size pump skid is needed. The size of the pump skid is determined by how fast we want to refill the CO2 Buffer Vessel Stations before we can charge an extractor for the next cycle.
If you only have one extractor and a cycle is 60 minutes we do not need a large pump skid. If you have several extractors and will be charging one after the other, a larger pump skid will be required to minimize the refill time.
To pick the correct pump skid please refer to the table “Usage and Recovery Time” to the right.
If you think your business is going to grow you should select a larger pump skid as the flow rates on these cannot be changed economically. As for the CO2 Buffer Vessel Stations, these can be added at any time to accommodate new equipment, faster charge times etc.
CO2-1-5-1-24E1L0V0D1U1B3T1PT1S-30GALOII
CO2-1-5-1-48E1L0V0D1U1B3T1PT1S-30GALOII
CO2-1-5-1-24E1L0V0D1U1B3T1PT1S-45GALOII
CO2-1-5-1-48E1L0V0D1U1B3T1PT1S-45GALOII
CO2-1-7.5-1-24E1L0V0D1U1B3T1PT1S-60GALOII
CO2-1-7.5-1-48E1L0V0D1U1B3T1PT1S-60GALOII
CO2-1-10-1-24E1L0V0D1U1B3T1PT1S-75GALOII
CO2-1-10-1-48E1L0V0D1U1B3T1PT1S-75GALOII
Example:
You have one 200 liter extractor and from step one you have determined you need Qty-2 CO2 Buffer Vessel Stations. You have talked to you supplier and determined the pressure range you need is 600-900PSI. You have an approx. cycle time of 60 minutes. Go to the table and find the 600-900 PSI in the first column which will be the blue rows. Next go the second blue row which is the 2-CO2 Buffer Vessel Stations we determined we needed. Going across you can see four different recharge times. Since we have 60 minutes between charging cycles, we could select the smallest pump skid 1.25GPM/30KW.)
CO2-1-5-1-48-E1L0V0D1U1B3T1PT1S-45-GALOII
CO2-1-5-1-24-E1L0V0D1U1B3T1PT1S-45-GALOII
CO2-1-5-1-48-E1L0V0D1U1B3T1PT1S-60-GALOII
CO2-1-5-1-24-E1L0V0D1U1B3T1PT1S-60-GALOII
CO2 SKID RETURN CONNECTION:
CO2-1-7.5-1-48-E1L0V0D1U1B3T1PT1S-75-GALOII
CO2-1-7.5-1-24-E1L0V0D1U1B3T1PT1S-75-GALOII
CO2-1-10-1-48-E1L0V0D1U1B3T1PT1S-90-GALOII
CO2-1-10-1-24-E1L0V0D1U1B3T1PT1S-90-GALOII
2.7 GPM/75 KW 3.3 GPM/90 KW
Weldcoa CO2 Modular Systems have designed the controls to operate within certain parameters that are specifically configured to assure that your CO2 supply runs at an optimal productivity level. The system is constantly self-monitoring the cryogenic pump and flow. If the system senses an error or becomes aware that it is starting to operate outside of the proper working parameters it will send out alerts. This Self Monitoring process runs 24/7/365.
Remote Viewing gives you the ability to remotely access your new CO2 Modular System on your mobile devices or work stations and view how the system is operating in real time.
√ Your management team can remotely access your system and make limited adjustment to your system in real time.
√ You can assign up to five employees remote access
√ When the “Self Monitoring” featuring sends out an “Alert” this message will go to all five of these employees. They can then remotely access the system to see what it going on or if they are at the facility they can walk up to the system and perform maintenance or adjustments.
Remote Monitoring enables Weldcoa’s in house team to detect any issues that your system may be experiencing. The Weldcoa team receives the same alerts as your companies five designated employees. If required to the Weldcoa remote team can make more technical or complicated changes to your system in order to keep your operation running.
√ Weldcoa team receives alert alarms
√ Weldcoa team maintains client access for its designated employees
√ Weldcoa team can make remote adjustments/changes to client’s system in order to keep them operational
The first year of Remote Support is included in the purchase cost of the system. Thereafter, the service requires an annual service fee. If the service is not renewed, the Remote View and Remote Monitor features will cease to function. If the client later chooses to resume the Remote Support package a Re-Start Fee and the Annual Subscription will have to be paid in full before the service recommences.
“When we looked at Weldcoa’s system and compared it to others in the market, we all found it to be extremely impressive, in particular the ability to provide service using remote diagnostics. Their technicians can receive instant notification of any messages from the equipment and access our control systems to diagnose and address issues. Downtime is practically eliminated, and our customers don’t experience any delays. While these instances are few and far between the ability to address them quickly and flawlessly sets Weldcoa apart from the others.”
Pat Dalton Operations Manager WestAir Gas
& Equipment, Inc.
In the event an onsite visit is required for maintenance or repair to the system, clients will be billed at Weldcoa’s standard time and material fee plus travel and expenses.
All pump related maintenance services and repairs are handled by Nikkiso / Cryogenic Industries Service Company. The Cryogenic Industries Service Company is directly affiliated with cryogenic pump manufacturer ACD, the world’s leader in the design and manufacture of cryogenic reciprocating and centrifugal pumps for over 45 years.
Nikkiso / Cryogenic Industries Service Company repair facilities are strategically located across North America and in strategic off-shore locations to offer customers an unrivaled level of service and expertise. Each location maintains an extensive spare parts inventory to ensure minimal downtime. Nikkiso trains a knowledgeable, friendly staff to answer your questions, and their successful Pump Exchange Program will put your equipment on a cost effective components replacement schedule.
The goal at Cryogenic Industries Service Companies is to produce a quality product and to reach the customer in a helpful and friendly atmosphere. With the expertise of their factory-trained technicians, they are able to service and repair most cryogenic pumps as well as alternator and motor repairs. Their facilities makes use of only genuine OEM parts for our repairs. Every repair completed has met all current factory specifications or it does not go out the door
Service Menu includes:
√ Cryogenic pump repairs
√ Spare parts
√ New equipment sales: pumps and vaporizers in stock and ready for delivery
√ Alternator sales and repair
√ Motor Services
√ Pump Exchange Program
√ Alternator Exchange Program
√ Bellows and ring seal repair
√ Complete pump line spare inventory (ACD, Cosmodyne, Cryo-Chem, etc.)
√ Training Seminars
√ Pump installation and field repairs
√ Knowledgeable staff to answer your questions
√ Warranty information