
5 minute read
AN OVERLOOKED ROOT CAUSE OF CONSTRUCTION JOBSITE INCIDENTS
AN OVERLOOKED ROOT CAUSE OF CONSTRUCTION JOBSITE INCIDENTS
BY THOMAS J. GREEN, CHST, STS, STSC, SAFETY PROGRAMS INSTRUCTOR/SAFETY PROFESSIONAL MED-TEX SERVICES, INC.
OSHA’s reports and training materials regularly report fall hazards as the number one cause of fatality in construction, but a more wide-reaching cause of injury and fatality is not something that be quantified or photographed by a manager or safety professional. This hazard is not weather-related, or due to an engineering or equipment defect. This hazard is about attitude and is easily boiled down to one word: complacency.
Statements like, “We’ve been doing it this way for years, and no one has gotten hurt,” “I’m a professional! I’m good at my job! Why should I change how I do it?” or “Everyone else is doing it that way,” show both resistance to change and complacency towards reported trends in the industry, as if because incidents are from other jobsites, the hazards are not real. Carter and Smith, in their 2006 study on hazard identification1 found that the only 66.5-89.9% of jobsite hazards were recognized by workers. Incident reports and reports of fatalities available to safety trainers today show that a principal cause of incidents was a lack of hazard recognition.
This does not necessarily mean that we are failing to train workers to recognize hazards. What is more likely is that potential hazards are not recognized and mitigated in the daily routine because they did not previously cause incidents or injuries; workers are conditioned to ignore the hazards that have not caused them injury. If the hazard is pointed out, most workers would concede that they see and should have seen the hazard before being directed to it, yet they still fail to address it.
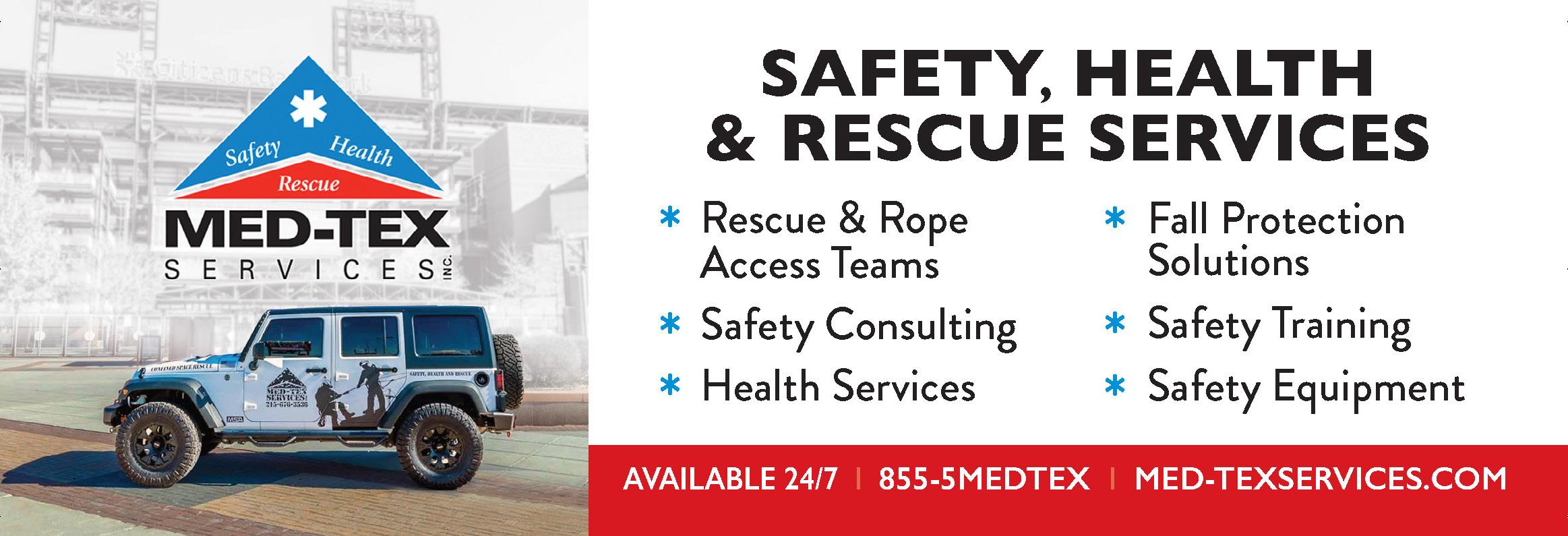
This begs the question: Is the worker the one at fault, or is the responsibility for complacency on the foremen or even more senior supervision?
Do we need new ways to approach hazard recognition and communication, or do we already have the tools to get that job done?
Human performance tools can be an excellent means of combating complacency, at least initially. Tools such as the “Two Minute Drill”, where workers take two minutes to review a hazard recognition checklist before starting a task, usually result in an uptick in hazard recognition and abatement. Eventually, however, these tools often become exercises in going through the motions in order to “check the box” and get to work.

CONDUCT AN EFFECTIVE JOB SAFETY ANALYSIS
Most construction employers require a Job Safety Analysis (JSA) be performed daily by their managers. If JSAs are required daily, then why do workers still fail to recognize hazards?
A Job Safety Analysis, also known as a Job Hazard Analysis (JHA), Daily Hazard Analysis (DHA), or the nuclear industry’s Task-Specific Job Hazard Analysis (TSJHA), is a hazard recognition framework that breaks down the individual steps in a task, identifies the hazards associated with each step, and then details how the hazards will be controlled via the Hierarchy of Controls. Ideally, this is a cooperative effort between the foreman and the work crew so that tasks are examined from multiple perspectives and are specific to the jobsite. The completed cards are kept for reference during the shift and returned to the safety department at the end of shift. Most employers expect the foreman to turn in a JSA card for each job assignment as part of their managerial duties, so that there is pressure to get the card completed and submitted.
The JSA is designed to be a cooperative effort, but oftentimes foremen will complete the JSA prior to examining the jobsite and simply have workers sign the card. Foremen are often rated by their supervision and safety department by how well JSAs are completed. Schedule discipline is often a cause for glossing over the JSA process, as foremen do not want to delay work, or have it appear that the crew is “wasting time” pointing out deficiencies to address. Workers are then inadvertently prompted to think that there are no new hazards to be addressed, often overlooking changes that could present new hazards.
Employers often use the phrase, “schedule never takes precedence over safety,” but how often is this just lip service? If construction employers don’t ensure that employees are encouraged to recognize and correct hazards—even if it impacts schedule—we will likely continue to face fatalities and serious injuries to workers. Here are some suggestions to help correct employee attitudes that may lead to complacency:

1. Refuse to accept “this is how we’ve always done it” as an acceptable defense of an employee’s actions. Any worker who shows resistance to coaching or other corrective measures can become a hazard.
2. Understand that a “culture of safety” means more than having safety meetings that give lip service to safety. Slogans alone do not prompt workers to evaluate their work areas for hazards.
3. Incentivize safety. Most safety professionals understand that recognizing good safety practices with something as small as a $5 gift card can go a long way.
4. Make the JSA process a cooperative effort as was intended. Encourage front line supervisors to assign coordination of this process to individual employees (with supervision) on a rotating basis. Get everyone to take ownership for the crew’s safety.
5. Make PPE a priority. One of the first steps in combating complacency is ensuring that workers realize the importance of properly wearing PPE to avoid preventable injuries, especially while performing repetitive and intermittent hazardous tasks.
Human performance tools help employees to recognize hazards. Yet employees are still unnecessarily injured or killed due far too often to a failure to recognize what are nearly always preventable hazards. Management and safety departments, as a key component of a culture of safety, must take the lead and focus on combating complacency on their jobsites every day.